Abstract
Aiming at analyzing the safety of the dynamic structure involving both input random variables and the interval ones, a new dynamic reliability analysis model is presented by constructing a second level limit state function. Two steps are involved in the construction of the dynamic reliability model. In the first step, the non-probabilistic reliability index is firstly extended to the dynamic structure, in which the uncertainties of interval inputs can be analyzed by fixing random inputs and time parameter. In the second step, the second level limit state function is constructed by considering the fact that the non-probabilistic reliability index larger than one corresponds to the safe state, in which the uncertainties of random inputs are taken into account. Generally, the actual reliability of dynamic structure with both random and interval inputs is an interval variable, and theoretic analysis illustrates that the proposed reliability is equivalent to the lower bound of the actual reliability, which can provide an efficient way for measuring the safety of dynamic structure. For estimating the proposed reliability, a double-loop optimization algorithm combined with Monte Carlo Simulation as well as the active learning Kriging method is established. Several examples involving a cylindrical pressure vessel, an automobile front axle and a planar 10-bar structure are introduced to illustrate the validity and significance of the established reliability model and the efficiency and accuracy of the proposed solving procedure.
Similar content being viewed by others
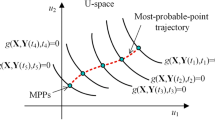
Avoid common mistakes on your manuscript.
1 Introduction
In the engineering application, the uncertainties of structure have crucial effects on the proper functioning of the structure. With the development of technique, more and more attention and discussion are focused on the research of how the uncertainty impacts the mechanical behaviors of structure (Lemaire 2009). Over the past few decades, the reliability analysis based on the classical probabilistic theory has been widely studied and applied by researchers to measure the safety level of the structure (Abdelal et al. 2013; Antonio and Hoffbauer 2010). Many methods have been proposed to analyze the reliability of static (Pang et al. 2016; Abdelal et al. 2008) and dynamic (Jiang et al. 2017; Hu and Du 2013; Shi et al. 2017) structure with random input variables. For applying the probability method, lots of information or experimental data are required to construct precise probability distributions of the random inputs. Unfortunately, in many engineering applications, the experimental data is limited.
In this case, the boundaries of the uncertainty inputs may be easy to be determined and the uncertainty inputs are suitable to be described as non-probabilistic interval variables. For the reliability problem with interval input variables, available non-probabilistic approaches can be employed to measure the reliability. Ben-Haim (1994, 1995) firstly proposed the concept of non-probabilistic reliability in which the interval model was also employed into the calculation of reliability, and the reliability is measured by the maximum extent permissible. Elishakoff (1995) also did some researches on the non-probabilistic reliability. Guo et al. (2001, 2002) proposed a new non-probabilistic reliability index for the structure only with interval input variables, the new non-probabilistic reliability index is defined as the distance measured by the infinite norm from the origin of coordinates to the failure surface of the structure in the expansion space by normalized interval variables. In recent years, researchers (Liu et al. 2016; Balu and Rao 2017; Jiang et al. 2013; Stampouloglou and Theotokoglou 2006) have proposed many non-probabilistic reliability methods based on the non-probabilistic convex model. For the dynamic reliability problem with non-probabilistic input variables, Qiu et al. (2004, 2009) proposed the dynamic non-probabilistic reliability analysis technique based on the convex model and interval analysis. Geng et al. (2016) developed the dynamic non-probabilistic reliability assessment for function generation mechanisms. However, all the non-probabilistic reliability approaches discussed above are suitable for the static or dynamic structure only with single-source uncertainty of the input variables.
In engineering, there may be multi-source uncertainties present in a structural system simultaneously. Therefore, it is necessary to develop efficient approaches for addressing the problems with hybrid uncertainties. At present, how to construct the reliability analysis for structure with both randomness and non-probabilistic but bounded uncertainties has become a significant issue in the field of structural safety (Antonio and Hoffbauer 2010). Du et al. (2005) proposed a hybrid reliability model for the structure with both random input variables and interval ones, in which the reliability is considered under the condition of the worst case combination of interval variables and applied it to reliability-based design optimization. Jiang et al. (2012) developed a new reliability analysis method through transformed optimization model for hybrid uncertainties, and only through computing the equivalent model the original hybrid reliability can be evaluated. Based on the interval analysis of non-probabilistic theory, Guo and Lu (2002) established the hybrid probabilistic and non-probabilistic reliability analysis approach for the structure with both random variables and interval variables. Wu et al. (2015) proposed an uncertain analysis method named polynomial-chaos–chebyshev-interval (PCCI) for vehicle dynamics involving hybrid uncertainty parameters, and this method does not require the amendment of original solver for different dynamics problems thus has high applicability. Huang et al. (2017) established a hybrid reliability design optimization model and corresponding decoupling strategy for structure with random and interval uncertainties, in which the incremental shifting vector algorithm is employed to convert the nested optimization process to a sequential iterative process of deterministic optimization and hybrid reliability analysis. Zheng et al. (2018) presented a robust topology optimization method for cellular composites with random input variables and interval ones, and a new uncertain propagation method named hybrid univariate dimension reduction is proposed to estimate the interval mean and variance. Other researches for calculating the reliability with mixed uncertainties can be found in Refs. (Carneiro and Antonio 2017; Jiang et al. 2018; Chen et al. 2016). These methods are proposed to estimate the reliability of static structure with hybrid uncertainties, however, the dynamic structure may also has hybrid uncertainties.
Up to now, the research about the reliability analysis for the dynamic structure with hybrid uncertainties has been rarely considered, and only a few of scholars have done some researches (Guo et al. 2015; Zou et al. 2015). Therefore, it is particularly necessary to develop effective and validated hybrid reliability analysis techniques for the dynamic structure. Aiming at addressing this issue, this paper focuses on developing a new reliability analysis model for the dynamic structure with hybrid uncertainties, including random variables and interval variables. The proposed dynamic reliability analysis model is constructed by a second level limit state function, where the non-probabilistic reliability index for dynamic structure is firstly established to analyze the uncertainties of the interval input variables, and the second level limit state function is then constructed to analyze the uncertainties of the random input variables. Moreover, a double-loop optimization algorithm combined with Monte Carlo Simulation as well as the active learning Kriging method (Jiang et al. 2012; Echars et al. 2011) is employed to solve the new hybrid dynamic reliability.
This paper is organized as follows: The general dynamic reliability model with hybrid uncertainties is showed in Sect. 2. The proposed dynamic reliability analysis model for structure with hybrid uncertainties is established in Sect. 3. The computational methods for the proposed dynamic reliability model are constructed in Sect. 4. Several examples are introduced in Sect. 5. Conclusions are given in Sect. 6.
2 Definition of general dynamic reliability model with hybrid uncertainties
For dynamic structure with random input variables and interval ones, the limit state function can be expressed as \( G = g({\mathbf{X}},{\mathbf{Y}}\text{,}t) \), where \( {\mathbf{X}} = (X_{1} ,X_{2} , \ldots ,X_{n} ) \) indicates the \( n \)-dimensional vector of the random variables with the probability density function \( f_{{X_{i} }} (x_{i} )(i = 1,2, \ldots ,n) \) for \( X_{i} (i = 1,2, \ldots ,n) \). \( {\mathbf{Y}} = (Y_{1} ,Y_{2} , \ldots ,Y_{m} ) \) denotes the \( m \)-dimensional vector of the interval variables, and the corresponding interval is \( Y_{i} \in [\underset{\raise0.3em\hbox{$\smash{\scriptscriptstyle-}$}}{Y}_{i} ,\bar{Y}_{i} ](i = 1,2, \ldots ,m) \). \( t \in [0,T] \) is the time parameter. Obviously, the interval variables \( {\mathbf{Y}} = (Y_{1} ,Y_{2} , \ldots ,Y_{m} ) \) can be expressed as \( Y_{i} = Y_{i}^{C} + \delta_{i} Y_{i}^{R} (i = 1,2, \ldots ,m) \), where \( Y_{i}^{C} = {{(\underset{\raise0.3em\hbox{$\smash{\scriptscriptstyle-}$}}{Y}_{i} + \bar{Y}_{i} )} \mathord{\left/ {\vphantom {{(\underset{\raise0.3em\hbox{$\smash{\scriptscriptstyle-}$}}{Y}_{i} + \bar{Y}_{i} )} 2}} \right. \kern-0pt} 2} \) and \( Y_{i}^{R} = {{(\bar{Y}_{i} - \underset{\raise0.3em\hbox{$\smash{\scriptscriptstyle-}$}}{Y}_{i} )} \mathord{\left/ {\vphantom {{(\bar{Y}_{i} - \underset{\raise0.3em\hbox{$\smash{\scriptscriptstyle-}$}}{Y}_{i} )} 2}} \right. \kern-0pt} 2} \), and \( {\varvec{\updelta}} = (\delta_{1} ,\delta_{2} , \ldots ,\delta_{m} ) \) indicates the normalized interval variable vector, on which the dynamic limit state function can be rewritten as \( G = g^{{ ( {\text{T)}}}} ({\mathbf{X}},{\varvec{\updelta}}\text{,}t) \). It can been seen that the output \( G = g^{{ ( {\text{T)}}}} ({\mathbf{X}},{\varvec{\updelta}}\text{,}t) \) is interval and varies with the random variables \( {\mathbf{X}} \) and time \( t \). Then the safe domain \( \varOmega_{S} \) and failure domain \( \varOmega_{F} \) for the output \( G = g^{{ ( {\text{T)}}}} ({\mathbf{X}},{\varvec{\updelta}}\text{,}t) \) can be given as follows:
Therefore, when the input variables locate in the failure domain, the structure is failure; else, it is safe. The actual reliability \( P_{r} \) and failure probability \( P_{f} \) are interval variables because of the existing of the interval input vector \( {\varvec{\updelta}} \) in the limit state function. \( P_{r} \) and \( P_{f} \) are defined by
where \( P\{ \cdot \} \) means the probability of the events occurrence. \( P_{r} \in [P_{r}^{l} ,P_{r}^{u} ] \) and \( P_{f} \in [P_{f}^{l} ,P_{f}^{u} ] \), in which \( P_{r}^{l} \) and \( P_{r}^{u} \) are the lower bound and the upper bound of the reliability \( P_{r} \) respectively, \( P_{f}^{l} \) and \( P_{f}^{u} \) are the lower bound and the upper bound of the failure probability \( P_{f} \) respectively.
The lower bound \( P_{r}^{l} \) and upper bound \( P_{r}^{u} \) of the actual reliability \( P_{r} \) can be estimated by
in which \( g_{\hbox{min} L}^{(T)} ({\mathbf{X}},{\varvec{\updelta}}) = \mathop {\hbox{min} }\limits_{t \in [0,T]} g_{L}^{(T)} ({\mathbf{X}},{\varvec{\updelta}}\text{,}t) \) is the minimum output lower bound value with respect to the time parameter, and \( g_{\hbox{min} U}^{(T)} ({\mathbf{X}},{\varvec{\updelta}}) = \mathop {\hbox{min} }\limits_{t \in [0,T]} g_{U}^{(T)} ({\mathbf{X}},{\varvec{\updelta}}\text{,}t) \) is the minimum output upper bound value with respect to the time parameter.
Generally, a complex nesting estimating process will be involved when estimating the lower bound \( P_{r}^{l} \) and upper bound \( P_{r}^{u} \) of the actual reliability \( P_{r} \), which will lead to extremely low efficiency or instable convergence performance. In the next section, a new dynamic reliability analysis model with hybrid uncertainties is proposed to measure the safety of dynamic structure. Furthermore, theoretic analysis illustrates that the proposed reliability is equivalent to the lower bound \( P_{r}^{l} \) of the actual reliability \( P_{r} \), which demonstrates the effectiveness of the proposed reliability model for measuring the safety of dynamic structure. One advantage of the proposed dynamic reliability analysis model is that it can be efficiently solved by our estimated methods.
3 The proposed dynamic reliability model with hybrid uncertainties
When the random variables \( {\mathbf{X}} \) at time \( t \) are fixed at the realization \( \varvec{x} \), the failure domain as showed in Eq. (2) is only the function of the interval variables. The further the distance of the interval variables is away the failure domain, the more robust the structure is to the interval variables, and the safer the structure is. Therefore, the distance between the interval variables and the failure domain has the monopoly on the state of the structure (safe or failure). Refer to the static non-probabilistic reliability index (Guo and Lu 2002), the non-probabilistic reliability index \( \eta (\varvec{x},t) \) with the fixed random input \( \varvec{x} \) and the time \( t \) can be defined as the shortest distance measured by the infinite norm \( ||{\varvec{\updelta}}||_{\infty } \) from the coordinate origin to the failure domain in the expansion space of the normalized interval variables, i.e.,
where \( ||{\varvec{\updelta}}||_{\infty } = \hbox{max} \{ |\delta_{1} |,|\delta_{2} |, \ldots ,|\delta_{m} |\} \). The standardized interval variables belong to the convex region \( \varOmega_{{\varvec{\updelta}}} = \{ {\varvec{\updelta}}:|\delta_{i} | \le 1,i = 1,2, \ldots ,m\} \), and the expansion space indicates the extended infinite spatial domain \( \varOmega_{{\varvec{\updelta}}}^{\infty } = \{ {\varvec{\updelta}}:\delta_{i} \in ( - \,\infty , + \,\infty ),i = 1,2, \ldots ,m\} \). Take two-dimensional interval variables for example which is showed in Fig. 1, where \( g_{1}^{{ ( {\text{T)}}}} (\varvec{x},{\varvec{\updelta}}\text{,}t) = 0 \) and \( g_{2}^{{ ( {\text{T)}}}} (\varvec{x},{\varvec{\updelta}}\text{,}t) = 0 \) represent two limit state surfaces of two performance function \( g_{1}^{{ ( {\text{T)}}}} ({\mathbf{X}},{\varvec{\updelta}}\text{,}t) \) and \( g_{2}^{{ ( {\text{T)}}}} ({\mathbf{X}},{\varvec{\updelta}}\text{,}t) \) respectively, and \( \eta_{1} (\varvec{x},t) \) and \( \eta_{2} (\varvec{x},t) \) are the corresponding non-probabilistic reliability indexes of these two performance functions respectively.
For this two-dimensional interval variables case, the non-probabilistic reliability index is estimated by \( \eta (\varvec{x},t) = \hbox{min} \{ ||{\varvec{\updelta}}||_{\infty } \} = |\delta_{1} | = |\delta_{2} | \). Geometrically, When \( \eta (\varvec{x},t) < 1 \), the structural failure domain intersects with the convex region \( \varOmega_{{\varvec{\updelta}}} \), then the structure is unreliable, such as \( \eta_{2} (\varvec{x},t) \) showed in Fig. 1; else if \( \eta (\varvec{x},t) > 1 \), the structure is safe, such as \( \eta_{1} (\varvec{x},t) \) showed in Fig. 1. Thus when \( \eta (\varvec{x},t) = 1 \), the structure locates the critical state between the reliable one and the unreliable one. It is easy to understand that when \( \eta (\varvec{x},t) > 1 \), the bigger \( \eta (\varvec{x},t) \) is, the safer the structure is. Therefore, it is reasonable to employ the non-probabilistic reliability index \( \eta (\varvec{x},t) \) to measure the reliability of the structure with the interval variable. Above analysis is based on that the random variables \( {\mathbf{X}} \) are fixed at the realization \( \varvec{x} \), thus when the uncertainties of the random variables are considered, the non-probabilistic reliability index becomes the function of random variables \( {\mathbf{X}} \) and time parameter \( t \) and it can be rewritten as \( \eta ({\mathbf{X}},t) \).
In order to further analyze the effect of the uncertainties of the random variables \( {\mathbf{X}} \) in non-probabilistic reliability index \( \eta ({\mathbf{X}},t) \) on the structural safety, we propose to employ the following second level limit state function to measure the safety of dynamic structure with both random input variables and interval ones based on the critical state of the non-probabilistic reliability index \( \eta ({\mathbf{X}},t) \).
Based on above analysis of the non-probabilistic reliability index, it is easy to understand that the structure is safe when \( F({\mathbf{X}},t) > 0 \) and failure when \( F({\mathbf{X}},t) \le 0 \). By Eq. (8), the dynamic reliability model involving both the random variables and the interval variables is transformed as the dynamic reliability model only involving the random variables. Hence, we define a new reliability \( P_{r}^{(\eta )} \) for measuring the safety degree of the dynamic model as follows:
It should be noted that the reliability \( P_{r}^{(\eta )} \) in Eq. (9) is the result based on the non-probabilistic reliability index. The general dynamic reliability model in Sect. 2 shows that the actual reliability \( P_{r} \) of the dynamic model \( G = g({\mathbf{X}},{\mathbf{Y}}\text{,}t) \) is interval variable \( P_{r} \in [P_{r}^{l} ,P_{r}^{u} ] \). Actually, the proposed reliability \( P_{r}^{(\eta )} \) is equivalent to the lower bound \( P_{r}^{l} \) of the actual reliability \( P_{r} \). The proof process is showed below.
By extending characteristic of the non-probabilistic reliability index of static structure (Guo and Lu 2002), the non-probabilistic reliability index \( \eta ({\mathbf{X}},t) \) of linear dynamic structure can be written by
where \( g_{L}^{(T)} ({\mathbf{X}},{\varvec{\updelta}}\text{,}t) \) and \( g_{U}^{(T)} ({\mathbf{X}},{\varvec{\updelta}}\text{,}t) \) are the lower bound and upper bound of the output interval \( g^{{ ( {\text{T)}}}} ({\mathbf{X}},{\varvec{\updelta}}\text{,}t) \). The proposed reliability \( P_{r}^{(\eta )} \) is defined as the probability of \( F({\mathbf{X}},t) > 0 \) for all the time \( t \in [0,T] \). Combining the extreme value theory for estimating the dynamic reliability, the definition of \( P_{r}^{(\eta )} \) corresponds to the probability of that the minimum value of \( F({\mathbf{X}},t) \) with respect to the time \( t \) is larger than zero. Therefore, the reliability \( P_{r}^{(\eta )} \) can be rewritten as follows:
By combining Eq. (8) with Eq. (9), the proposed reliability \( P_{r}^{(\eta )} \) can be estimated by
in which \( g_{\hbox{min} L}^{(T)} ({\mathbf{X}},{\varvec{\updelta}}) = \mathop {\hbox{min} }\limits_{t \in [0,T]} g_{L}^{(T)} ({\mathbf{X}},{\varvec{\updelta}}\text{,}t) \). Generally, the lower bound \( P_{r}^{l} \) of the actual reliability \( P_{r} \) corresponding to the probability of that minimum output lower bound is larger than zero, i.e., \( P_{r}^{l} = P\{ g_{\hbox{min} L}^{(T)} ({\mathbf{X}},{\varvec{\updelta}}) > 0\} \). Therefore, for the linear dynamic structure we have \( P_{r}^{(\eta )} = P_{r}^{l} \). This conclusion can be extended to the non-linear dynamic structure because that the structure will be absolutely safe when \( \eta_{\hbox{min} } ({\mathbf{X}}) > 1 \) as showed in Fig. 1, which illustrates that the output interval will be always larger than zero. Thus, the minimum output lower bound larger than zero is equivalent to \( \eta_{\hbox{min} } ({\mathbf{X}}) > 1 \) which means \( P\{ \eta_{\hbox{min} } ({\mathbf{X}}) > 1\} = P\{ g_{\hbox{min} L}^{(T)} ({\mathbf{X}},{\varvec{\updelta}}) > 0\} \), then \( P_{r}^{(\eta )} = P_{r}^{l} \).
Therefore, the proposed reliability is significant in measuring the safety of dynamic structure with both random and interval variables. Also, it is reasonable to concern the conservative solution in engineering application, i.e., the lower bound of the reliability. Accordingly, the failure probability \( P_{f}^{(\eta )} \) can be estimated as follows:
Based on the discussion above, the failure probability \( P_{f}^{(\eta )} \) corresponds to the upper bound of the actual failure probability solution \( P_{f}^{u} \) with the probabilistic reliability theory.
In the engineering application, lots of information or experimental data are always lacking. In this case where the inputs involve the interval variables, providing the bound of the reliability or the failure probability is more reasonable than giving a value. For the dynamic model \( G = g({\mathbf{X}},{\mathbf{Y}}\text{,}t) \), this section establishes a reliability analysis model to estimate the reliability \( P_{r}^{(\eta )} \) (the lower bound \( P_{r}^{l} \) of the actual reliability \( P_{r} \)) or the failure probability \( P_{f}^{(\eta )} \) (the upper bound \( P_{f}^{u} \) of the actual failure probability \( P_{f} \)). In the next section, the computational issues are established.
4 Estimate procedure
To estimate the reliability \( P_{r}^{(\eta )} \) for the dynamic model \( G = g({\mathbf{X}},{\mathbf{Y}}\text{,}t) \), we need to firstly calculate the non-probabilistic reliability index \( \eta ({\mathbf{X}},t) \). In the Sect. 4.1, the one-dimensional optimization algorithm (Jiang et al. 2007) is extended to estimate the non-probabilistic reliability index \( \eta ({\mathbf{X}},t) \). Then the MCS method and the Kriging surrogate method for the reliability \( P_{r}^{(\eta )} \) are proposed in Sects. 4.2 and 4.3 respectively.
4.1 The non-probabilistic reliability index \( \eta ({\mathbf{X}},t) \)
When the random variables \( {\mathbf{X}} \) and time \( t \) are fixed at the realization \( \varvec{x} \) and \( t^{ * } \) respectively, the non-probability reliability index \( \eta (\varvec{x},t^{ * } ) \) is defined as \( \eta (\varvec{x},t^{ * } ) = \hbox{min} \{ ||{\varvec{\updelta}}||_{\infty } \} = \hbox{min} \{ \hbox{max} \{ |\delta_{1} |,|\delta_{2} |, \ldots ,|\delta_{m} |\} \} \). If we define the \( 2^{m} \) peaks of the symmetric convex domain \( \varOmega_{{\varvec{\updelta}}} = \{ {\varvec{\updelta}}:|\delta_{i} | \le 1,i = 1,2, \ldots ,m\} \) as \( P_{{\varvec{\updelta}}}^{j} = \{ {\varvec{\updelta}}:|\delta_{i} | = 1,i = 1,2, \ldots ,m\} (j = 1,2, \ldots ,2^{m} ) \), then there must be \( 2^{m - 1} \) super rays from the coordinate origin to \( P_{{\varvec{\updelta}}}^{j} (j = 1,2, \ldots ,2^{m} ) \) in the extended infinite spatial domain \( \varOmega_{{\varvec{\updelta}}}^{\infty } = \{ {\varvec{\updelta}}:\delta_{i} \in ( - \,\infty , + \,\infty ),i = 1,2, \ldots ,m\} \). If there exist one or more intersections among these \( 2^{m - 1} \) super rays and the failure surface \( g^{{ ( {\text{T)}}}} (\varvec{x},{\varvec{\updelta}}\text{,}t^{ * } ) = 0 \), then the intersections must satisfy the following equation.
For the static structure with only interval variables, Jiang et al. (2007) proved that the non-probabilistic reliability index must exists in the intersections among the super ray and the failure surface. The conclusion can be easily extended to the dynamic model \( G = g^{{ ( {\text{T)}}}} (\varvec{x},{\varvec{\updelta}}\text{,}t) \). Suppose there are \( l \) intersections denoted as \( {\varvec{\updelta}}^{k} = (\delta_{1}^{k} ,\delta_{2}^{k} , \ldots ,\delta_{m}^{k} )\,(k = 1,2, \ldots ,l) \). The absolute value of the component for these intersections is equivalent, i.e., \( \left| {\delta_{1}^{k} } \right| = \left| {\delta_{2}^{k} } \right| = \cdots = \left| {\delta_{m}^{k} } \right| = \varGamma^{k} (k = 1,2, \ldots ,l) \). Then \( \text{||}{\varvec{\updelta}}^{k} ||_{\infty } = \hbox{max} \{ |\delta_{1}^{k} |,|\delta_{2}^{k} |, \ldots ,|\delta_{m}^{k} |\} = \varGamma^{k} (k = 1,2, \ldots ,l) \). Considering the physical significance of \( \eta (\varvec{x},t) \) is the shortest distance measured by the infinite norm \( ||{\varvec{\updelta}}||_{\infty } \) from the coordinate origin to the failure domain in the expansion space of the normalized interval variables. Therefore, the non-probabilistic dynamic reliability index \( \eta (\varvec{x},t^{ * } ) \) can be estimated as follows:
in which \( \varGamma^{k} = |\delta_{1}^{k} | = |\delta_{2}^{k} | = \cdots = |\delta_{m}^{k} |(k = 1,2, \ldots ,l) \). Above Eq. (15) indicates that the non-probabilistic reliability index \( \eta (\varvec{x},t^{ * } ) \) at time \( t^{ * } \) equals to the minimum absolute value of the components in these \( l \) intersections between the super rays and the failure surface.
The steps for estimating \( \eta (\varvec{x},t^{ * } ) \) can be summarized as follows:
Step 1 Give the random variables \( {\mathbf{X}} \) and the time \( t \) a realization \( \varvec{x} \) and \( t^{ * } \) respectively. Construct the limit state failure surface \( g^{{ ( {\text{T)}}}} (\varvec{x},{\varvec{\updelta}}\text{,}t^{ * } ) = 0 \).
Step 2 Considering the \( 2^{m - 1} \) super rays from the coordinate origin to \( P_{{\varvec{\updelta}}}^{j} (j = 1,2, \ldots ,2^{m} ) \) in the extended infinite spatial domain \( \varOmega_{{\varvec{\updelta}}}^{\infty } = \{ {\varvec{\updelta}}:\delta_{i} \in ( - \,\infty , + \,\infty ),i = 1,2, \ldots ,m\} \), and they satisfy \( \delta_{1} = \pm \delta_{2} = \cdots = \pm \delta_{m} \).
Step 3 Take \( \delta_{1} = \pm \delta_{2} = \cdots = \pm \delta_{m} \) into equation \( g^{{ ( {\text{T)}}}} (\varvec{x},{\varvec{\updelta}}\text{,}t^{ * } ) = 0 \) respectively, then we can get \( 2^{m - 1} \) dollar algebraic equations. Solve these equations and obtain all the roots.
Step 4 Wipe off the complex roots, then the rest of the roots can be expressed as \( {\varvec{\updelta}}^{k} = (\delta_{1}^{k} ,\delta_{2}^{k} , \ldots ,\delta_{m}^{k} )\,(k = 1,2, \ldots ,l) \). Estimate the \( \varGamma^{k} (k = 1,2, \ldots ,l) \), and the non-probabilistic reliability index \( \eta (\varvec{x},t^{ * } ) \) can be obtained by Eq. (15).
By above method, the estimation of the non-probabilistic reliability is transformed by the calculation of \( 2^{m - 1} \) dollar algebraic equations. For the simple equations, e.g., first-order or second-order equation, the analytic method can be used to obtain the roots. For the complex equations, e.g., high-order equation, the numerical method such as the FSOLVE toolbox in MATLAB can be employed.
4.2 MCS for solving the reliability \( P_{r}^{(\eta )} \)
From Eq. (11), one can see that the estimation of the reliability \( P_{r}^{(\eta )} \) can be transformed to the estimation of the probability that the minimum of the non-probabilistic reliability index \( \eta_{\hbox{min} } ({\mathbf{X}}) \) bigger than 1. When the random vector \( {\mathbf{X}} \) is fixed at the realization \( \varvec{x} \), the non-probability reliability index \( \eta (\varvec{x},t) \) can be obtained by solving the multiple monadic equations and it is the function of time \( t \). The minimum value \( \eta_{\hbox{min} } (\varvec{x}) \) of \( \eta (\varvec{x},t) \) can be obtained by the optimization algorithm. In this paper, we use the following double-loop optimization to estimate the \( \eta_{\hbox{min} } (\varvec{x}) \):
For the inner-loop optimization, the proposed method in Sect. 4.1 can be used to estimate the \( \eta (\varvec{x},t) \). As to the outer-loop optimization, the FMINCON toolbox in MATLAB is employed to obtain the \( \eta_{\hbox{min} } (\varvec{x}) \). Compared with the method that disperses the time \( t \) to obtain the \( \eta_{\hbox{min} } (\varvec{x}) \), the double-loop optimization method just need to search a few time instant to obtain the \( \eta_{\hbox{min} } (\varvec{x}) \). Therefore, the proposed double-loop optimization method can decrease the computational cost so as to get the \( \eta_{\hbox{min} } (\varvec{x}) \) efficiently. When all the \( \eta_{\hbox{min} } (\varvec{x}) \) for the random variables are available, the reliability \( P_{r}^{(\eta )} \) can be obtained by Eq. (11).
We briefly summarize the MCS procedure as follows:
Step 1 Generate a sample matrix \( {\mathbf{A}} \) of dimension \( N \times n \) by Sobol’ low-discrepancy sequence (Sobol’ 1998), each column of which contains \( N \)-size uniform sample between 0 and 1. Employ the sample matrix \( {\mathbf{A}} \) to obtain a sample matrix \( {\mathbf{B}} \) which forms the sample of the input random vector \( {\mathbf{X}} \) by the inverse cumulative distribution transformation.
Step 2 Use \( Y_{i} = Y_{i}^{C} + \delta_{i} Y_{i}^{R} (i = 1,2, \ldots ,m) \) to express the interval variables \( {\mathbf{Y}} = (Y_{1} ,Y_{2} , \ldots ,Y_{m} ) \). Substitute it into the original limit state function \( G = g({\mathbf{X}},{\mathbf{Y}}\text{,}t) \) to obtain the form of \( G = g^{{ ( {\text{T)}}}} ({\mathbf{X}},{\varvec{\updelta}}\text{,}t) \), and let \( k = 1 \).
Step 3 Substitute the \( k \)-th row of the sample matrix \( {\mathbf{B}} \) into \( G = g^{{ ( {\text{T)}}}} ({\mathbf{X}},{\varvec{\updelta}}\text{,}t) \) to obtain the \( G = g^{{ ( {\text{T)}}}} (\varvec{x}^{(k)} ,{\varvec{\updelta}}\text{,}t) \), then use the Eq. (16) to estimate the \( \eta_{\hbox{min} } (\varvec{x}^{(k)} ) \).
Step 4 If \( k < N \), then \( k = k + 1 \) and go to step 3; else, go to step 5.
Step 5 Denote the number of the sample points that satisfy \( \eta_{\hbox{min} } (\varvec{x}^{(k)} ) > 1(k = 1,2, \ldots ,N) \) as \( N_{R} \), then the reliability \( P_{r}^{(\eta )} \) can be estimated as follows:
The above MCS process for estimating the reliability \( P_{r}^{(\eta )} \) is commonly computationally expensive, although the double-loop optimization method and the Sobol’ sequence are employed to improve the efficiency. For each sample point of the input random vector \( {\mathbf{X}} \), there always needs some computational cost to obtain \( \eta_{\hbox{min} } (\varvec{x}) \). In the next Sect. 4.3, the Kriging surrogate model method is provided to improve the efficiency.
4.3 The Kriging surrogate for solving the reliability \( P_{r}^{(\eta )} \)
By several training data, the Kriging surrogate method (Lophaven and Nielsen 2002; Echars et al. 2011) can provide a surrogate model for the original structure. In this paper, we use the Kriging method to construct surrogate model for \( \eta_{\hbox{min} } (\varvec{x}) \). Generally, the Kriging method can not only provide the predictions, but also the probabilistic errors. For the objective function \( Z({\mathbf{X}}) \), the Kriging surrogate model \( \hat{Z}({\mathbf{X}}) \) is expressed as follows:
in which \( f({\mathbf{X}}) \) contains polynomial terms with unknown coefficients and \( \varepsilon ({\mathbf{X}}) \) is the error term. Here we focus on the application of the Kriging surrogate method, and details of the Kriging model can be found in Ref. (Lophaven and Nielsen 2002). To improve the accuracy of the surrogate model for \( \eta_{\hbox{min} } (\varvec{x}) \), here we employ an active learning Kriging procedure. The following is the procedure and the flowchart of this procedure is plotted in Fig. 2:
Step 1 Set the acceptable mean square error \( \varepsilon_{0} \). Generate a sample matrix \( {\mathbf{C}} \) with the dimensionality \( N_{K} \times n \) for the input random vector \( {\mathbf{X}} \), where \( N_{K} \) is a large number such as \( 10^{4} \). Select \( N_{0} \)-size sample from the sample matrix \( {\mathbf{C}} \) randomly to construct a sample matrix \( {\mathbf{D}} \), in which \( N_{0} \) is a small number such as 10.
Step 2 For the sample matrix \( {\mathbf{D}} \), employ Eq. (16) and the method in Sect. 3 to obtain the \( \eta_{\hbox{min} } (\varvec{x}^{(k)} )(k = 1,2, \ldots ,N_{0} ) \) (where \( \varvec{x}^{(k)} \) is the \( k \)-th row vector of the matrix \( {\mathbf{D}} \)).
Step 3 Construct the Kriging surrogate model with the sample matrix \( {\mathbf{D}} \) and the corresponding minimum value of non-probabilistic reliability index \( \eta_{\hbox{min} } (\varvec{x}^{(k)} )(k = 1,2, \ldots ,N_{0} ) \).
Stepx 3 Apply the constructed Kriging surrogate model to obtain the Kriging predictions \( \hat{\eta }_{\hbox{min} } (\varvec{x}^{(j)} )\,(j = 1,2, \ldots ,N_{K} ) \) and the corresponding mean square error \( \varepsilon_{{\hat{\eta }_{\hbox{min} } (\varvec{x}^{(j)} )}} (j = 1,2, \ldots ,N_{K} ) \) for each sample in matrix \( {\mathbf{C}} \). Find the maximum mean square error \( \varepsilon_{\hbox{max} } \) from the \( N_{K} \) mean square errors. If \( \varepsilon_{\hbox{max} } < \varepsilon_{0} \), stop the training process and go to step 6; else, add the sample which has the maximum mean square error \( \varepsilon_{\hbox{max} } \) into the last row of sample matrix \( {\mathbf{D}} \) and let \( N_{0} = N_{0} + 1 \).
Step 5 For the last row of sample matrix \( {\mathbf{D}} \), use Eq. (16) and the method in Sect. 4.1 to obtain the \( \eta_{\hbox{min} } (\varvec{x}^{{(N_{0} )}} ) \). Then go to step 3.
Step 6 Denote the number of the sample points that satisfy \( \hat{\eta }_{\hbox{min} } (\varvec{x}^{(j)} ) > 1(j = 1,2, \ldots ,N_{K} ) \) as \( N_{KR} \), then the reliability \( P_{r}^{(\eta )} \) can be estimated as follows:
With above active learning procedure, the Kriging surrogate model between the minimum non-probabilistic reliability index \( \eta_{\hbox{min} } (\varvec{x}) \) and the random vector sample \( \varvec{x} \) can be well constructed. Then the reliability probability \( P_{r}^{(\eta )} \) can be obtained accurately. Comparing with the direct MCS method, the computational cost of this method mainly results from the construction of the surrogate model, which is commonly small. Therefore, the proposed Kriging surrogate procedure for estimating the reliability \( P_{r}^{(\eta )} \) is efficient and accurate.
5 Examples
5.1 Cylindrical pressure vessel
Considering a cylindrical pressure vessel (Guo and Lu 2002), the inner diameter \( D \in [1470,1530]\,{\text{mm}} \) and the wall thickness \( d \in [4.4,5.6]\,{\text{mm}} \). The cross section of this vessel is shown in Fig. 3. The work stress inside the vessel is \( P = P_{0} \left( {\sin \frac{t}{15} + \frac{1}{2}} \right)\,{\text{MPa}} \) (radian), where \( P_{0} \) is normal random variable \( P_{0} \sim N(5.88,1.18^{2} ){\text{MPa}} \), and \( t \) is the time parameter \( t \in [0,T] \). The upper bound of the time interval \( T \) is considered as varying in \( [0,20] \), so we can obtain the curve of the reliability \( P_{r}^{(\eta )} \) varying with the upper bound of the time interval \( T \). The fracture toughness \( K_{IC} \) of the material is a normal random variable, i.e., \( K_{IC} \sim N(124,18.6^{2} )\,{\text{MPa}}\sqrt {\text{m}} \). A surface crack in the axial was found by nondestructive inspection, and the crack depth \( a \in [2.5,3.5]\,{\text{mm}} \). Based on the fracture failure criterion, the dynamic limit state function can be described as \( G = K_{IC} - \frac{0.975PD}{d}\sqrt {\frac{a}{Q}} \), where a constant \( Q = 1.55 \).
In this example, the acceptable mean square error for Kriging surrogate method is set to be \( \varepsilon_{0} = 10^{ - 3} \). When the time interval upper bound \( T \) varies in \( [0,20] \), Fig. 4 shows the minimum value \( \eta_{\hbox{min} } ({\varvec{\upmu}}) \) of the non-probabilistic reliability index varying with the time interval upper bound \( T \) when input random variables \( {\mathbf{X}} \) are fixed at the mean value \( {\varvec{\upmu}} \). The solutions of the reliability \( P_{r}^{(\eta )} \) estimated by the MCS method and the Kriging method are plotted in Fig. 5. The number of the sample of the MCS method for each \( T \) is \( N = 5000 \). The Kriging surrogate model is constructed at each \( T \) respectively, and the number denoted by \( N_{call} \) of the sample of the Kriging method for different \( T \) is listed in Table 1.
The Fig. 4 shows that the \( \eta_{\hbox{min} } ({\varvec{\upmu}}) \) decreases with the time interval upper bound \( T \) increase, which is in accordance with the engineering qualitative analysis. It can be seen in Fig. 5 that the reliability \( P_{r}^{(\eta )} \) estimated by the Kriging surrogate method can match well with the solution by the MCS method, which illustrates the accuracy of the proposed Kriging method. The Fig. 5 also shows that the reliability \( P_{r}^{(\eta )} \) decreases with the time interval upper bound \( T \) increase. The descent velocity of the reliability \( P_{r}^{(\eta )} \) is variant with the interval upper bound \( T \). When the \( T \) is set to be a small or big value, i.e., \( T \in [0,6] \) or \( T \in [16,20] \), the descent velocity is small which illustrates that the reliability \( P_{r}^{(\eta )} \) has a good robust on the time interval upper bound \( T \). But the descent velocity is big when \( T \in [6,16] \), which can be explained as that the reliability \( P_{r}^{(\eta )} \) has a bad robustness within \( T \in [6,16] \).
Compared with the MCS method, the proposed Kriging method has high efficiency. The Table 1 shows that the Kriging method just needs dozens of sample for each \( T \) to construct the surrogate model. When the surrogate model is constructed well, then it will cost no additional evaluation of \( g^{{({\text{T}})}} (\varvec{x},{\varvec{\updelta}},t) \) to obtain the reliability \( P_{r}^{(\eta )} \). The number of the sample for the MCS method for each \( T \) is \( N = 5000 \) which is much more than the sample size of the Kriging method, and the MCS method needs more computational cost such as the cost for the optimization procedure to obtain the reliability \( P_{r}^{(\eta )} \). Therefore, the proposed Kriging method is an accurate and efficient method for the estimation of the reliability \( P_{r}^{(\eta )} \).
For comparing the solution based on the non-probabilistic reliability theory and the complete probabilistic reliability theory respectively, here we suppose all the interval variables are normal random variables where their mean value is regarded as the mid-value of the interval and their standard deviation \( \sigma \) can be determined by regarding the bounds of the interval variables as \( 3\sigma \). Then the reliability \( P_{R} \) based on the complete probabilistic theory can be obtained. From Fig. 6, one can see that the \( P_{R} \) is bigger than the \( P_{r}^{(\eta )} \) for different time interval upper bound \( T \). As discussed in Sect. 2, the \( P_{r}^{(\eta )} \) is the lower bound of the actual reliability, and it is possible that the actual reliability reaches to this value \( P_{r}^{(\eta )} \). Therefore, employing the \( P_{r}^{(\eta )} \) as the reliability measurement is conservative. The solution \( P_{R} \) with the complete probabilistic reliability theory is slightly higher. It may cause some risk when using the \( P_{R} \) to guide the design and the optimization of the structure. Therefore, for the dynamic model with both the random variables and the interval variables, the \( P_{r}^{(\eta )} \) is more reasonable.
5.2 Automobile front axle
The automobile front axle is an important component in the automobile (Shi et al. 2017). Nowadays, the I-beam structure is popular in the design of the front axle due to its high bend strength and light weight. The structure is shown in Fig. 7, the dangerous cross-section is in the I-beam part. The maximum normal stress and shear stress are \( \sigma = \frac{M}{{W_{x} }} \) and \( \tau = \frac{T}{{W_{\rho } }} \) respectively, where \( M \) and \( T \) are bending moment and torque, and they are time-variant, i.e., \( M = M_{0} (\frac{1}{5}\cos \frac{t + 8}{30} + \frac{6}{5})^{2} \), \( T = T_{0} (\sin \frac{t + 8}{20})^{2} \), in which \( M_{0} \) and \( T_{0} \) are basic bending moment and torque, \( t \) is the time parameter and \( t \in [0,T] \) (radian), and \( T \) is considered as in \( [0,1] \). \( W_{x} \) and \( W_{\rho } \) are section factor and polar section factor which are be given respectively as follows:
To check the strength of the front axle, the dynamic limit state function can be represented as:
where \( \sigma_{S} \) is limit stress of yielding and \( \sigma_{S} = 350\,{\text{Mpa}} \). The loads \( M_{0} \) and \( T_{0} \) are independent normal variables, and \( M_{0} \sim N(8 \times 10^{6} ,(5 \times 10^{4} )^{2} )\,{\text{Nmm}} \), \( T_{0} \sim N(7 \times 10^{6} ,(2 \times 10^{4} )^{2} )\,{\text{Nmm}} \). The geometry variables of I-beam \( a \), \( b \), \( c \) and \( h \) are independent interval variables with the distribution parameters listed in Table 2.
To guarantee the accuracy of the results, here the number of the sample for MCS method at each \( T \) is set to be N = 10,000, and the acceptable mean square error for Kriging surrogate method is \( \varepsilon_{0} = 10^{ - 5} \). When the time interval upper bound \( T \) varies in \( [0,1] \), the minimum value of the non-probabilistic reliability index \( \eta_{\hbox{min} } ({\varvec{\upmu}}) \) when the random vector \( {\mathbf{X}} \) is fixed at the mean value \( {\varvec{\upmu}} \) is shown in Fig. 8. The reliability \( P_{r}^{(\eta )} \) estimated by the MCS method and the Kriging surrogate procedure is exhibited in Fig. 9, and the corresponding number of the sample for the Kriging surrogate procedure at each \( T \) is listed in Table 3. Figure 10 shows the comparison of the \( P_{r}^{(\eta )} \) and the \( P_{R} \) which is estimated based on the complete probabilistic reliability theory.
From Fig. 8, we can see that when the random vector is fixed at the mean value, the \( \eta_{\hbox{min} } ({\varvec{\upmu}}) \) is similar linear function of the \( T \), which illustrates that the decreased rate of the \( \eta_{\hbox{min} } ({\varvec{\upmu}}) \) with \( T \) is constant. Figure 9 shows that the reliability \( P_{r}^{(\eta )} \) estimated by the Kriging surrogate method can match well with that by the MCS method, which demonstrates the accuracy of the proposed active learning Kriging surrogate procedure. It can be seen that the reliability \( P_{r}^{(\eta )} \) decreases with the time interval upper bound \( T \) increase, and the \( P_{r}^{(\eta )} \) has a sharp decrease at the interval \( T \in [0.2,0.5] \). This indicates that the reliability \( P_{r}^{(\eta )} \) has a bad robustness on the interval \( T \in [0.2,0.5] \). The number of the sample of the Kriging surrogate method for each \( T \) showed in Table 3 indicates that there just need a dozen samples to obtain the reliability \( P_{r}^{(\eta )} \). But the number of the sample for the MCS method is N= 10,000 and the computational cost is more than this number. Therefore, the proposed Kriging surrogate procedure is an efficient method to estimate of the reliability \( P_{r}^{(\eta )} \).
We suppose all the interval variables are normal random variables where their mean value is regarded as the mid-value of the interval and their standard deviation \( \sigma \) can be determined by regarding the bounds of the interval variables as \( 3\sigma \). Then the reliability \( P_{R} \) based on the complete probabilistic reliability theory can be obtained. It can be found from Fig. 10 that the reliability \( P_{R} \) is always equal to one, which is completely different from the reliability \( P_{r}^{(\eta )} \). However, the actual reliability of the structure can reach to the reliability \( P_{r}^{(\eta )} \). In the engineering application, the conservative estimation of the reliability is more reasonable to guidance the design and the optimization instead of the reliability \( P_{R} \) when the interval inputs are involved.
5.3 A planar 10-bar structure
A planar 10-bar structure which is shown in Fig. 11 is introduced to illustrate the engineering significance of the proposed dynamic reliability analysis model. The length of the horizontal and vertical bars is \( L \). The section area and elastic modulus of each bar are \( A_{i} (i = 1,2, \ldots ,10) \) and \( E \) respectively. \( P_{i} (i = 1,2,3) \) are the point loads. \( P_{2} \) is time varying and \( P_{2} = P_{0} (\frac{1}{5}\sin \frac{1}{3}t + \frac{12}{5}) \), in which \( t \) is time parameter and \( t \in [0,T] \) (radian), and \( T \) is considered as in \( [0,3] \). \( P_{1} \) and \( P_{2} \) are interval variables, i.e., \( P_{1} \in [79,81]\,{\text{kN}} \), \( P_{3} \in [9,11]\,{\text{kN}} \). \( L \), \( A_{i} (i = 1,2, \ldots ,10) \), \( E \) and \( P_{0} \) are normally distributed, and their distribution parameters are listed in Table 4. The dynamic limit state function can be expressed as \( G = 0.0042 - \Delta \), where \( \Delta \) is the displacement of node 3 in vertical direction.
The finite element model of this planar 10-bar structure is built in Analysis 15.0 and it is shown in Fig. 12. In this example, the number of the sample for the MCS method at \( T \) is set to be N = 10,000, and the acceptable mean square error for Kriging surrogate method is \( \varepsilon_{0} = 10^{ - 3} \). The minimum value of the non-probabilistic reliability index \( \eta_{\hbox{min} } ({\varvec{\upmu}}) \) with the random vector \( {\mathbf{X}} \) fixed at the mean value \( {\varvec{\upmu}} \) is shown in Fig. 13. The reliability \( P_{r}^{(\eta )} \) estimated by the MCS method and the Kriging surrogate method is exhibited in Fig. 14, and the corresponding number of the sample for the Kriging surrogate method at each \( T \) is listed in Table 5. Figure 15 shows the comparison of the \( P_{r}^{(\eta )} \) and the \( P_{R} \) which is estimated based on the complete probabilistic reliability theory.
The Fig. 13 shows that the \( \eta_{\hbox{min} } ({\varvec{\upmu}}) \) decreases with the time interval upper bound \( T \) increase, which is in accordance with the engineering qualitative analysis. From Fig. 14, one can see that the reliability \( P_{r}^{(\eta )} \) estimated by the Kriging method can match well with that the MCS method solution, which illustrates the accuracy of the Kriging method. Figure 14 also shows that the reliability \( P_{r}^{(\eta )} \) decreases with the time interval upper bound \( T \) increase, and the reliability \( P_{r}^{(\eta )} \) has a stable robustness on the time interval upper bound. Table 5 shows that the proposed Kriging method is more efficient than the MCS method. Therefore, the proposed Kriging technique is an accurate and efficient method on estimating the reliability \( P_{r}^{(\eta )} \). Similar to the Examples 4.1 and 4.2, Fig. 15 shows that the reliability \( P_{R} \) always bigger than the reliability \( P_{r}^{(\eta )} \). But the actual reliability of the structure may reach to the reliability \( P_{r}^{(\eta )} \). In the engineering application, the conservative estimation of the reliability is more reasonable to guidance the design and the optimization instead of the reliability \( P_{R} \) when the interval inputs are involved.
6 Conclusions
A dynamic reliability analysis model and its solution are proposed in this paper for the structure with both the random variables and the interval variables. Before establishing the reliability analysis model, the non-probabilistic reliability index \( \eta ({\mathbf{X}},t) \) is defined as the shortest distance measured by the infinite norm \( ||{\varvec{\updelta}}||_{\infty } \) from the coordinate origin to the failure domain in the expansion space of the normalized interval variables. Then the structure can be regarded as safe when \( \eta ({\mathbf{X}},t) > 1 \) and failure when \( \eta ({\mathbf{X}},t) \le 1 \). Finally, the second level limit state function is constructed and the reliability can be obtained by analyzing the general dynamic model with only the random variables. Furthermore, it is easy to understand that the reliability is the actual reliability interval lower bound based on the probabilistic theory.
For efficiently estimating the dynamic reliability, the one-dimensional optimization algorithm for the static structure is firstly extended to calculate the non-probabilistic reliability index. After a double-loop optimization process is proposed to estimate the minimum value of the non-probabilistic reliability index, the MCS process is proposed to estimate the dynamic reliability. In order to further improve the efficiency, the active learning Kriging surrogate method is established. This method constructs the surrogate model between the minimum value of the non-probabilistic reliability index and the random variables. When the surrogate model is constructed, the reliability can be obtained by calling the surrogate model instead of the actual model.
Three examples involving a cylindrical pressure vessel, an automobile front axle and a planar 10-bar structure are employed to illustrate the validity of the established reliability analysis model for the structure with both the random variables and the interval variables. By comparing with the solution estimated with complete probabilistic reliability theory, the rationality of the proposed method is demonstrated. At the same time, the efficiency of the proposed active learning Kriging method is also illustrated.
References
Abdelal, G.F., Abuelfoutouh, N., Hamdy, A.: Mechanical fatigue and spectrum analysis of small-statellite structure. Int. J. Mech. Mater. Des. 4(3), 265–278 (2008)
Abdelal, G.F., Cooper, J.E., Robotham, A.J.: Reliability assessment of 3D space frame structures applying stochastic finite element analysis. Int. J. Mech. Mater. Des. 9(1), 1–9 (2013)
Antonio, C.C., Hoffbauer, L.N.: Uncertainty propagation in inverse reliability-based design of composite structures. Int. J. Mech. Mater. Des. 6(1), 89–102 (2010)
Balu, A.S., Rao, B.N.: Explicit fuzzy analysis of systems with imprecise properties. Int. J. Mech. Mater. Des. 7(4), 283–289 (2017)
Ben-Haim, Y.: A non-probabilistic concept of reliability. Struct. Saf. 14(4), 227–245 (1994)
Ben-Haim, Y.: Discussion on the paper: a non-probabilistic concept of reliability. Struct. Saf. 17(3), 195–199 (1995)
Carneiro, G.N., Antonio, C.C.: Robustness and reliability of composite structures: effects of different sources of uncertainty. Int. J. Mech. Mater. Des. (2017). https://doi.org/10.1007/s10999-017-9401-6
Chen, X., Yao, W., Zhao, Y.: An extended probabilistic method for reliability analysis under mixed aleatory and epistemic uncertainties with flexible intervals. Struct. Multidiscip. Optim. 54(6), 1641–1652 (2016)
Du, X.P., Sudjianto, A., Huang, B.Q.: Reliability-based design with the mixture of random and interval variables. J. Mech. Des. 127(6), 1068–1076 (2005)
Echars, B., Gayton, N., Lemaire, M.: AK-MCS: an active learning reliability method combining Kriging and Monte Carlo simulation. Struct. Saf. 33, 145–154 (2011)
Elishakoff, I.: Essay on uncertainties in elastic and viscoelastic structure: from A.M. Freudenthal’s criticisms to modern convex modeling. Comput. Struct. 56(6), 871–895 (1995)
Geng, X.Y., Wang, X.J., Wang, L., et al.: Non-probabilistic time-dependent kinematic reliability assessment for function generation mechanisms with joint clearances. Mech. Mach. Theory 104, 202–221 (2016)
Guo, S.X., Lu, Z.Z.: Hybrid probabilistic and non-probabilistic model of structural reliability. J. Mech. Strength 24(4), 524–526 (2002)
Guo, S.X., Lu, Z.Z., Feng, Y.S.: A non-probabilistic model of structural reliability based on interval analysis. Chin. J. Comput. Mech. 18, 56–60 (2001)
Guo, S.X., Zhang, L., Li, Y.: Procedures for computing the non-probabilistic reliability index of uncertain in structures. Chin. J. Comput. Mech. 22, 227–231 (2002)
Guo, J., Wang, Y., Zeng, S.: Nonintrusive-polynomial-chaos-based kinematic reliability analysis for mechanisms with mixed uncertainty. Adv. Mech. Eng. 6, 690985 (2015)
Hu, Z., Du, X.: Time-dependent reliability analysis with joint upcrossing rates. Struct. Multidiscip. Optim. 48(5), 893–907 (2013)
Huang, Z.L., Jiang, C., Zhou, Y.S., Zheng, J., Long, X.Y.: Reliability-based design optimization for problems with interval distribution parameters. Struct. Multidiscip. Optim. 55, 513–528 (2017)
Jiang, T., Chen, J.J., Jiang, P.G., et al.: A one-dimensional optimization algorithm for non-probabilistic reliability index. Eng. Mech. 24(7), 23–27 (2007)
Jiang, C., Lu, G.Y., Han, X., et al.: A new reliability analysis method for uncertain structures with random and interval variables. Int. J. Mech. Mater. Des. 8, 169–182 (2012)
Jiang, C., Bi, R.G., Lu, G.Y., et al.: Structural reliability analysis using non-probabilistic convex model. Comput. Methods Appl. Mech. Eng. 254, 83–98 (2013)
Jiang, C., Huang, X.P., Wei, X.P.: A time-variant reliability analysis method for structural systems based on stochastic process discretization. Int. J. Mech. Mater. Des. 13(2), 173–193 (2017)
Jiang, C., Zheng, J., Han, X.: Probability-interval hybrid uncertainty analysis for structures with both aleatory and epistemic uncertainties: a review. Struct. Multidiscip. Optim. 57(6), 2485–2502 (2018)
Lemaire, M.: Structural Reliability. Wiley, London (2009)
Liu, J., Sun, X.S., Meng, X.H.: A novel shape function approach of dynamic load identification for the structures with interval uncertainty. Int. J. Mech. Mater. Des. 12(3), 375–386 (2016)
Lophaven, S.N., Nielsen, H.B., Søndergaard, J.: DACE-A MATLAB Kriging Toolbox. Technical University of Denmark, Kongens Lyngby (2002)
Pang, H., Yu, T.X., Song, B.F.: Failure mechanism analysis and reliability assessment of an aircraft slat. Eng. Fail. Anal. 60, 261–279 (2016)
Qiu, Z.P., Mueller, P.C., Frommer, A.: The new non-probabilistic criterion of failure for dynamical systems based on convex models. Math. Comput. Model. 40, 201–215 (2004)
Qiu, Z.P., Ma, L.H., Wang, X.J.: Non-probabilistic interval analysis method for dynamic response analysis of nonlinear systems with uncertainty. J. Sound Vib. 319, 531–540 (2009)
Shi, Y., Lu, Z.Z., Cheng, K., et al.: Temporal and spatial multi-parameter dynamic reliability and global reliability sensitivity analysis based on the extreme value moments. Struct. Multidiscip. Optim. 56(1), 117–129 (2017)
Sobol’, I.M.: On quasi-monte carlo integrations. Math. Comput. Simul. 47(2), 103–112 (1998)
Stampouloglou, I.H., Theotokoglou, E.E.: Investigation of the problem of a plane axisymmetric cylindrical tube under internal and external pressures. Int. J. Mech. Mater. Des. 3(1), 59–71 (2006)
Wu, J.L., Luo, Z., Zhang, N., Zhang, Y.Q.: A new uncertain analysis method and its application in vehicle dynamics. Mech. Syst. Signal Process. 50–51, 659–675 (2015)
Zheng, J., Luo, Z., Li, H., Jiang, C.: Robust topology optimization for cellular composites with hybrid uncertainties. Int. J. Numer. Meth. Eng. 115(6), 695–713 (2018)
Zou, L., Liu, X., Hu, X.L., et al.: Dynamic reliability of shock absorption rubber structure with probability-interval mixed uncertainty. Chin. J. Appl. Mech. 32(2), 197–204 (2015)
Acknowledgements
This work was supported by the Natural Science Foundation of China (Grants 51475370 and 51775439).
Author information
Authors and Affiliations
Corresponding author
Rights and permissions
About this article
Cite this article
Shi, Y., Lu, Z. Dynamic reliability analysis model for structure with both random and interval uncertainties. Int J Mech Mater Des 15, 521–537 (2019). https://doi.org/10.1007/s10999-018-9427-4
Received:
Accepted:
Published:
Issue Date:
DOI: https://doi.org/10.1007/s10999-018-9427-4