Abstract
The symbiosis potential of microalgae and yeast is inherited with distinct advantages, providing an economical venue for their scale-up application. To assess the advantage of the mixed culture of microalgae Chlorella vulgaris and yeast Yarrowia lipolytica for treatment of liquid digestate of yeast industry (YILD) and cogeneration of biofuel feedstock, the cell growth characteristic, the nutrient removal efficiency, the energy storage potential of the mono, and mixed culture were investigated. The results indicated that the biomass concentration of the mixed culture (1.39–1.56 g/L of 5 times dilution group and 1.23–1.53 g/L of 10 times dilution group) was higher than those of mono cultures. The NH3-N and SO42− removal rates of the mixed culture were superior to mono cultures. Besides the higher lipid yield (0.073–0.154 g/L of 5 times dilution group and 0.112–0.183 g/L of 10 times dilution group), the higher yield of higher heating value (20.06–29.76 kJ/L of 5 times dilution group and 21.83–29.85 kJ/L of 10 times dilution group) was also obtained in the mixed culture. This study provides feasibility for remediation of YILD and cogeneration of biofuel feedstock using the mixed culture of microalgae and yeast.
Similar content being viewed by others
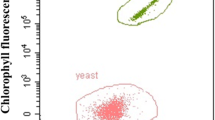
Explore related subjects
Discover the latest articles, news and stories from top researchers in related subjects.Avoid common mistakes on your manuscript.
Introduction
The number of yeast industry is expanding in China during the last decade due to the increasing demand of export and the change of the mode of Chinese traditional fermented food that inevitably generate a large quantity of high-strength liquid wastes namely yeast wastewater [1]. Yeast wastewater is dark color and contains a higher amount of total nitrogen (TN), and various non-biodegradable organic pollutants [2]. The development of easily operative methods for the treatment of yeast wastewater before runoff into environment is a challenging task for scientists and environmental engineers as yeast wastewater is characterized with very high chemical oxygen demand (COD) (4000–130,000 mg/L) and biochemical oxygen demand (BODx) (200–96,000 mg/L) [3]. In 2010, China produces 240,000 t yeast, and it was reported that the production is 1 t of yeast process about 100 m3 of wastewater. According to the guidelines of Ministry of Environmental Protection of the People’s Republic of China, dairy farms, industries (e.g., food/ beverage, breweries), and municipalities are required to meet the standards for the handling and recycling of wastewater (especially nutrients, phosphorus, and nitrogen) prior discharge wastewater that poses serious environmental challenges to the receiving water bodies. According to the national standard of China “Discharge standard of water pollutants for yeast industry (GB 25462-2010),” the limit value of COD, TN, TP, and NH3-N is 400, 40, 2.0, and 25 mg/L, respectively, for indirect discharge which refers to the discharge of pollutants from the factory to the public sewage treatment system. So far, there is no simple, robust, and easily adaptable process available for treating the yeast wastewater. The yeast factories in China have developed and improved conventional anaerobic treatment processes to treat wastewater. Although the anaerobic processing can recover most organic matter in the form of methane, it is limited to the removal of nitrogen and phosphorus. The liquid digestate needs further chemical and physical-chemical treatment to meet the discharge standard; however, chemical treatment of wastewaters is expensive and can pose long-term environmental effects.
The use of microalgae in wastewater treatment and the generation of biomass have been long promoted because many species of microalgae can effectively grow in wastewater using organic carbon and inorganic N and P from wastewater as nutrients and simultaneously can remove access N, P, as well as heavy metals such as Cd and Zn [4, 5]. Microalgae culture conjunction with wastewater treatment can save the cost of wastewater treatment and enhance the economic feasibility and sustainability of microalgae biofuel production [6,7,8]. Therefore, researchers are interested in using anaerobic liquid digestate for microalgae culture [9,10,11]. Most of the reported study used anaerobic liquid digestate from anaerobic treatment industry of livestock wastewater, kitchen wastewater, piggy wastewater, etc.; however, liquid digestate from yeast industry has not been studied.
Symbiosis of microalgae and yeast was studied by many researchers, and reviews elucidated that due to the higher carbon dioxide available for microalgae for photosynthesis and the higher oxygen availability for heterotrophy of yeast, the combination of yeast and microalgae culture in one process shows many significant advantages over the mono microalgae culture, like higher yield of high value products, such as lipid, and faster growth rate and higher biomass concentration and removal of organic materials and nutrients from wastewater [12, 13]. A significant number of reports indicate the potential of some kinds of yeasts using glycerol or crude glycerol, generated in the various oleo-chemical facilities employing transformation of vegetable or animal fats, as a carbon source for a plethora of metabolic compounds of value-added production, such as microbial lipids (also called single cell oils, SCO) [14, 15]. In the co-culture of photosynthetic microalgae and heterotrophic yeast process, microalgae act as an O2 generator and provide higher level O2 for the heterotrophic growth of yeast; on the other hand, later produced CO2 by the yeast assimilation of the organic carbon source can be used by microalgae for growth and lipid production [16].
Exploiting the reciprocity between yeast and microalgae strains in the mixed culture system with low-value substances is an innovative strategy to govern high biomass and/or lipid productivity and decrease the cost of feedstock for biofuel production. The aim of this work was to assess the advantage of the mixed culture of Chlorella vulgaris and Yarrowia lipolytica with YILD as low-value substance. The biotic and abiotic characteristics including the growth of C. vulgaris and Y. lipolytica, the nutrient removal efficiency, and the energy storage potential of the mono and mixed culture system were studied in detail to assess the feasibility of using the mixed culture of microalgae and yeast in the treatment of liquid digestate of yeast industry and cogeneration of biofuel feedstock.
Material and Methods
Strain
Microalgae strain C. vulgaris was purchased from The Microbial Culture Collection at the National Institute for Environmental Studies, Japan (strain number NIES-227). The axenic culture which sent from Japan was transferred into new C medium and incubated at 25 °C and checked the growth day after day. Repeat the transfers till the steady growth of the culture. The C medium was described as follows: 100 mL medium contained Ca(NO3)2·4H2O 15 mg, KNO3 10 mg, β-Na2 glycerophosphate·5H2O 5 mg, MgSO4·7H2O 4 mg, vitamin B12 0.01 μg, biotin 0.01 μg, thiamine HCl 1 μg, PIV metals, 0.3 mL, and tris(hydroxymethyl)aminomethane 50 mg. The composition of PIV metals was Na2EDTA·2H2O 100 mg, FeCl3·6H2O 19.6 mg, MnCl2·4H2O 3.6 mg, ZnSO4·7H2O 2.2 mg, CoCl2·6H2O 0.4 mg, Na2MoO4·2H2O 0.25 mg, and distilled water 100 mL. The medium was sterilized at 121 °C for 20 min before use.
Yeast stain Y. lipolytica was purchased from Guangdong Microbiology Culture Center at Guangdong Institute of Microbiology, China (strain number GIM2.197). The strain was maintained in YPD medium (glucose 20 g/L, yeast extract 10 g/L, and peptone 20 g/L).
Medium and Liquid Digestate of Yeast Industry Wastewater
Seed media of C. vulgaris and Y. lipolytica were BG11 and YPD, respectively. The yeast wastewater was collected from the production process of medicinal yeast using sugarcane molasses of Guangdong Wuzhou Pharmaceutical Co., Ltd., located in Guangdong Province of China and stored at 4 °C for anaerobic digestion. A 2.5-L anaerobic digester with a working volume of 2 L was utilized for anaerobic digestion. Anaerobic digester was filled with 1 L yeast wastewater and 1 L inoculums, and the pH value was adjusted to 7.20 using 1 mol/L sodium hydroxide. The inoculum was taken from the stable operating mesophilic continuous stirred tank reactor (CSTR), which was fed an artificially prepared substrate containing glucose, starch, cellulose, xylose, yeast powder, and peptone [17]. The anaerobic digester was placed in a water bath at 35 °C for 50 days following nitrogen stripping. The YILD was autoclaved followed by centrifugation at 6000 rpm for 5 min. The characteristics of autoclaved liquid digestate are shown in Table 1.
Experimental Setup
The Y. lipolytica was transferred to 250-mL flasks containing 100 mL YPD medium, cultivated at 28 °C and 150 rpm for 36 h, and used as seed culture. The C. vulgaris was transferred to column glass photobioreactor (Ф = 5.5 cm, 70 cm high) containing 500 mL BG11 medium, cultivated at 25 ± 1 °C, and illuminated with white fluorescent lamps at the single side (light intensity of 300 ± 10 μmol photons/m2/s) and supplemented with 2% CO2 at a rate of 1 vvm (volume gas per volume media per minute) at the bottom of the photobioreactor for 3 days, and used as seed culture. The seed cultures were then centrifuged at 3000 rpm for 5 min at 25 ± 1 °C and appropriate dilution using sterile water to obtain the high cell density inoculums.
The pH of autoclaved YILD was adjusted to 6.7 with HCl solution (4 mol/L) under the aseptic condition before culture the inoculums. The dilution ratios of autoclaved YILD and initial cell density of microalgae and/or yeast are presented in Table 2. Glycerol was added to each treatment with final concentration of 40 mM. All cultures were performed in light shaker using 250-mL flasks with 100 mL working volume and cultivated at 28 ± 1 °C and 150 rpm for 240 h with the light supply of 45 ± 3 μmol photons/m2/s. All the experiments were conducted in triplicate, and the results were presented with the mean including standard deviation unless the specifically states otherwise.
Total 8 mL samples were collected at 48, 96, 144, and 240 h. A 20 μL sample was used for microscopic photography and counting. The rest samples were centrifuged (6000 rpm, 5 min), and the supernatant was used for analyses of COD, NH3-N, total inorganic carbon (TIC), total organic carbon (TOC), NO3−, PO43−, SO42−, Cl−, and sediments were used for the cell growth determination. In addition, collected biomass at the end of the culture was lyophilized for lipid analysis and elemental analysis.
Analytical Methods
Biomass Measurement
Dry biomass was estimated by gravimetric method; the 3 mL culture was centrifuged at 6000 rpm for 5 min at ambient temperature; cell pellets were washed with purified water twice and then incubated at 60 °C until constant weight to determinate the dry biomass weight. Biomass concentration and biomass productivity were calculated according to Qin et al. [7]
Nutrient Analysis
COD and NH3-N were determined using a Hach DR2700 Spectrophotometer (Hach Co., USA) and Hach reagents (CAT No. 2125915 and 2606945) following the manufacturer’s procedure. TC, TIC, and TOC concentrations were determined using the total organic carbon analyzer (Elementar vario TOC, Germany). The concentration of SO42−, Cl−, NO3−, and PO43− was determined by ion chromatography (Metrohm883 Compact IC, Switzerland). The percentage of the removal of nutrients was calculated according to described by Qin et al. [7].
Lipid Content Analysis
A modified method was applied to quantify the amount of total lipid content [18]. Total 80–100 mg of lyophilized samples were extracted with 2 mL of methanol containing 10% dimethyl sulfoxide (DMSO) in a water bath shaker at 45 °C for 45 min. The mixture was centrifuged at 3000 rpm for 10 min. The supernatant was collected, and the leftover was re-extracted twice following the same procedures. Then, the leftover was extracted with a 4 mL mixture of hexane and ether (1:1, v/v) 45 °C for 60 min. The mixture was centrifuged at 3000 rpm for 10 min, after which the supernatant was collected and the leftover was re-extracted twice. All the supernatants were incorporated, and 6 mL of distilled water was added to the combined extracts. The organic phases were combined into a pre-weighed glass tube and evaporated to dryness under the protection of nitrogen. Then, the lipids were lyophilized for 24 h. The total lipids were measured gravimetrically, and the total lipid content and lipid productivity were calculated according to Qin et al. [7].
Elemental Analysis and HHV Calculation
About 5 mg lyophilized samples were used for elemental analysis, using vario EL cube (Elementar, Germany). Based on the elemental composition, HHV was calculated using well-established correlations given by [19].
Results and Discussion
Microorganism Growth
The microbial biomass is an important parameter to evaluate the output of the culture system. In this study, the mono C. vulgaris, the mono Y. lipolytica, and the mixed culture were cultivated in YILD with 5 and 10 times dilution and 40 mM glycerol as a carbon source. As shown in Fig. 1, the mixed culture and the mono yeast culture can grow well while the mono microalgae show poor growth performance. The biomass concentrations of the mixed culture groups of 48 h (1.39–1.56 g/L of 5 times dilution and 1.23–1.53 g/L of 10 times dilution) were higher than those of the mono Y. lipolytica (1.15 g/L of 5 times dilution and 1.04 g/L of 10 times dilution, respectively). The biomass productivity on the 48 h of the mixed culture groups (594.38–650.13 mg/L/day of 5 times dilution and 534.00–588.12 mg/L/day of 10 times dilution) was higher than those of the mono Y. lipolytica group (521.00 mg/L/day of 5 times dilution and 464.75 mg/L/day of 10 times dilution, respectively), which is higher than those of the mono microalgae group (79.13 mg/L/day of 5 times dilution and 113.50 mg/L/day of 10 times dilution, respectively) (Table 3). It is widely documented that there was symbiotic relationship between microalgae and yeast in the mixed culture, further providing higher biomass production compared with the mono culture of each organism [12]. Including O2/CO2 exchange, microalgae acted an O2 generator for yeast while yeast provided CO2 to microalgae; the synergistic effect on pH adjustment and substance exchange between microalgae and yeast can contribute to the biomass enhancement [20, 21]. However, there was no considerable increase of biomass in mixed culture when compared with the sum of the two mono cultures, T4 with (T1 + T2) and T9 with (T6 + T7), maybe due to the depletion of nutrients, and the attenuation of light intensity caused by the increased yeast cell which contributes to the poor growth of microalgae in the mixed culture [12, 22].
The growth of C. vulgaris in this work is poorer than previous reports which were cultivated in different types of liquid digestate such as, when cultured in digested starch wastewater, Yang et al. achieved 3.01 g/L biomass concentration and 580 mg/L/day biomass productivity [23]; 2.05 g/L biomass concentration and 630 mg/L/day biomass productivity were achieved when cultivated in starch processing wastewater [24]; biomass concentration (2.11 g/L) and biomass productivity (450 mg/L/day) were achieved when cultured in sludge liquor concentration [25]. This may be due to the inappropriate nutritional proportion of YILD, especially the presence of high salinity contributors (Cl−, SO42−), to the disadvantage of the growth of C. vulgaris even though the liquid digestate was diluted. The poor growth of performance of C. vulgaris causes that the biomass in the mixed culture system was dominated by the growth of Y. lipolytica which can use glycerol as a carbon source [26]. These experimental outcomes suggested that YILD can be considered as a medium for culture of Y. lipolytica and the mixed culture can as a strategy for the improved the microbial biomass production.
Nutrient Removal Comparison
Nutrient removal efficiency is an important indicator for evaluating the effectiveness of the microalgae-yeast wastewater cultivation system. Considering that liquid digestate contains nitrogen which is preferably in the form of ammonium and phosphorus which is preferably in the form of phosphate [27], we have chosen NH3-N and PO43− to characterize the nitrogen and phosphorus change situation. Because the PO43− concentration of the autoclaved YILD was 16.16 mg/L and the PO43− of 48 h was not detected, this study mainly focused on the removal of the abundant ingredients including COD, NH3-N, TIC, TOC, Cl−, and SO42−.
Nitrogen is an essential element for various biological substance syntheses (e.g., protein, nucleic acid, and phospholipid) [28]. Nutrient removal efficiencies of biological method mainly depend on the microbial species and the growth status. In the present study, the NH3-N removal effects of the mixed culture were superior to the mono Y. lipolytica culture and the mono C. vulgaris culture (Fig. 2a). This indicated that the microbial uptake may be the main way for NH3-N removal in this work. Furthermore, the NH3-N concentration after 48 h of the mixed culture and the mono yeast culture display increase trend, especially the mono yeast culture. It was reported that ammonia releases a mechanism of protection from yeast cell death during colony development under limited nutrient conditions [29]. This suggested that there was the NH3-N release after 48 h in the mono yeast and the mixed culture, and the presence of microalgae in the mixed culture can alleviate the ammonia release from yeast cell. Comparing with previous studies that achieved 100% removal of NH3-N when cultured Chlorella in liquid digestate of dairy manure [30, 31], the NH3-N removal of mono microalgae culture of this study was not a satisfactory result. This may be due to the poor growth performance of C. vulgaris which limits the use of nitrogen sources. Furthermore, the NH3-N removal of the mixed culture groups shows the gradient variation which in consistent with the initial concentration of microalgae (T5 > T4 > T3 and T10 > T9 > T8). The NH3-N removal rate increases with the increase of dilution ratio (the maximum NH3-N removal rate 80.25% obtained in 10 times dilution group) (Fig. 2a and Table 4).
COD in liquid digestate includes volatile fatty acids (VFAs) (mainly in the form of acetic acid) and inorganic carbon sources (mainly in the form of bicarbonate) which can be utilized by microalgae and/or yeast [27, 32]. Glycerol as sole carbon source could enhance biomass and lipid production in the mixed culture of Rhodotorula glutinis and C. vulgaris [22]. In this study, to ensure the growth of microbes, and then fulfill the removal of N and P from the YILD, glycerol (initial concentration 40 mM) as a carbon source was introduced into culture system. The total COD removal effects of the mixed culture (67.05–68.55% of 5 times dilution and 79.23–80.38% of 10 times dilution) were similar to those of the mono Y. lipolytica culture (67.55% of 5 times dilution and 79.40% of 10 times dilution) and significantly better than those of the mono C. vulgaris culture (13.19% of 5 times dilution and 13.88% of 10 times dilution). The total COD removal rate increases with the increase of the dilution ratio (the maximum total COD removal rate of 240 h 80.38% obtained in 10 times dilution group) (Fig. 2b and Table 4). According to the experimental design, glycerol accounted for the proportion of total COD was 69.06 and 81.69% in 5 times diluted and 10 times diluted groups, respectively. The total COD removal rates of the mixed culture and the mono yeast culture after 48 h are similar to the glycerol proportion of total COD. Taking a low content of TIC and the limitations of microalgae in the use of TOC into consideration (Table 5), we concluded that Y. lipolytica plays a dominant role in the removal of total COD and the mixed culture did not significantly enhance the removal efficiency of total COD comparing with the mono Y. lipolytica culture. The relatively low inherent COD removal efficiency can attribute to the percentage of inherent organic carbon matter in the liquid digestate that was inert, and the microalgae and yeast have difficulty using this source because of the more utilizable organic carbon sources already utilized by anaerobic bacteria during anaerobic fermentation [24].
Ammonium sulfate, sodium chloride, magnesium sulfate, and other nutrients based on yeast species were added in fermentation system when using molasses as carbon source for yeast product. Hence, large amounts of sulfate and chloride ion consist in yeast wastewater and transfer to the liquid digestate by anaerobic process. Because a high concentration of sulfate and chloride ion is one of the typical characteristics of YILD, assessment of the removal effect of sulfate and chloride ion in the mixed culture system is very necessary. In terms of Cl− removal, the mixed culture shows no obvious advantage compared with the mono culture system, especially the mono yeast culture (Table 5). The removal rate of Cl− of 48 h falls between 10.79 and 15.74% and did not show a tendency to increase with the dilution ratio. Similar to the removal of Cl−, the 48 h SO42− removal rate of the mixed culture (23.47–28.60% of 5 times dilution and 34.78–47.60% of 10 times dilution) shows no obvious advantage compared with the mono yeast culture (22.87% of 5 times dilution and 37.39% of 10 times dilution). However, comparing with the mono microalgae culture (about 15% SO42− removal rate), the mixed culture and the mono yeast culture show an exact advantage of the 48 h SO42− removal rate. Furthermore, the removal rate of the mixed culture and the mono yeast culture increases with the dilution ratio. The inorganic forms of S in liquid digestate consist mainly of sulfates (SO42−). Assimilatory reduction of sulfate ion integrates, together with O2 bioproduction, CO2 fixation, nitrate ion reduction, and N2 fixation, the biological processes essential to aerobic life. The demand for the yeast growth of sulfate ion is more necessary than the chloride ion [33]. Focusing on the removal effect of SO42− and the biomass concentration at 48 h, the theoretical sulfur content of the biomass was between 1.07 and 3.69% if the removal of sulfate is due to the biological assimilation. However, that theoretical sulfur content of biomass at 48 h was definitely greater than the actual sulfur content (0.19–0.65%) at 240 h which was directly determined by elemental analysis (Table 6). Therefore, we speculate that the removal of sulfate is partially due to the biological assimilation or sulfur was released from biomass along with intracellular substances during growth cessation stage.
Overall, although the mixed culture displays exactly advantages compared to the mono culture in inherent pollutant removal from YILD, further researches about selection of strain, glycerol concentration, growth control, and synergy mechanism of mixed culture system should be implemented to improve the pollutant removal effect.
Energy Output Evaluation
The wastewater can act as low-cost substrate for microbial biomass production, and the obtained microbial biomass can be utilized as renewable energy, feedstuff, and chemical industry [34, 35]. Conjunction with liquid digestate treatment and microbial biofuel product by mixed microalgae and yeast culture is the original intention of this study. Hence, the lipid content and productivity and the HHV, which is an indicator of the amount of energy stored within biomass, were analyzed to evaluate the energy output efficiency of the mono and mixed culture. The lipid content of the mono C. vulgaris culture (14.49% of 5 times dilution and 17.93% of 10 times dilution) was higher than those of the mixed culture (6.66–10.07% of 5 times dilution and 9.21–12.21% of 10 times dilution) and the mono Y. lipolytica culture (5.41% of 5 times dilution and 8.46% of 10 times dilution). The lipid content of the mixed culture showed the gradient variation, T5 > T4 > T3 and T10 > T9 > T8, which in consistence with the initial concentration of microalgae. The lipid content of 10 times dilution is higher than 5 times dilution (Table 6). Although the lipid content of the mixed culture was lower than that of the mono microalgae culture, the lipid yield of the mixed culture (0.073–0.154 g/L of 5 times dilution and 0.112–0.183 g/L of 10 times dilution) was higher than that of the mono microalgae culture in 5 and 10 times diluted groups owing to the higher biomass in the mixed culture. The result was consistent with previous studies, which reported that the mixed culture could enhance the lipid production [12, 20, 36].
Thermochemical conversion is considered as a simpler route to produce biofuels. The technology can be a complement to chemical and biochemical methods for the maximal utilization of microbial biomass [37]. The solid biofuel performance is related to the elemental composition, including carbon, hydrogen, nitrogen, and oxygen content. To assess solid biofuel performance of biomass obtained from mono cultures and the mixed culture, the elemental composition and the estimated HHV, which is a major indicator of biomass quality in energy properties, were analyzed and are presented in Table 6. Excepting HHV values of 10 times dilution group that were higher than 5 times dilution group, respectively, some common characteristics in 5 times dilution and 10 times dilution group were listed as follows: (1) the estimated HHV values of mixed culture (18.24–19.04 MJ/kg of 5 times dilution and 18.98–19.41 MJ/kg of 10 times dilution) were higher than the mono yeast culture (17.25 MJ/kg of 5 times dilution and 17.34 MJ/kg of 10 times dilution) and lower than the mono microalgae culture (20.03 MJ/kg of 5 times dilution and 20.81 MJ/kg of 10 times dilution); (2) the gradient variation which similar to the rules of the NH3-N removal rates, T5 > T4 > T3 and T10 > T9 > T8. Additionally, nitrogen content gradually increased along with the initial concentration of microalgae. The HHV of the mono C. vulgaris in this work (20.03 MJ/kg of 5 times dilution and 20.81 MJ/kg of 10 times dilution) is very close to other reported HHV of Chlorella spp. (20.4 MJ/kg) [38]. However, because the low HHV of Y. lipolytica biomass and the yeast was the main contributor of the biomass from the mixed culture, the HHV of the mixed culture also falls somewhere between the mono C. vulgaris and the mono Y. lipolytica culture. Regarding solid biofuel efficiency, it is necessary to increase the HHV yield of the culture system, requiring a balance between HHV value and the biomass yield. The mixed culture system received perfect HHV yield (20.06–29.76 kJ/L of 5 times dilution and 21.83–29.85 kJ/L of 10 times dilution), which were higher than those of the mono yeast culture and the mono microalgae culture.
Conclusion
The YILD was observed to be a perfect medium for the mixed culture of C. vulgaris and Y. lipolytica, and the mixed culture improved the microbial biomass production. The mixed culture enhanced the removal efficiency of nitrogen and SO42−. The lipid and HHV yields in the mixed culture were higher than those in mono cultures. This work suggested that the mixed culture of microalgae and yeast could be applied to strengthen the YILD treatment and resource utilization. A credible package of YILD treatment coupling microbial biofuel feedstock production of mixed culture will be fulfilled with further researches for the selection and engineering of suitable strain, mutually benefited growth control, underlying synergy mechanism, and so on.
References
Jia, C. H., & Jukes, D. (2013). The national food safety control system of China—a systematic review. Food Control, 32(1), 236–245.
Comelli, R. N., Seluy, L. G., Grossmann, I. E., & Isla, M. A. (2015). The treatment of high-strength wastewater from the sugar-sweetened beverage industry via an alcoholic fermentation process. Industrial & Engineering Chemistry Research, 54(31), 7687–7693.
Pirsaheb, M., Rostamifar, M., Mansouri, A. M., Zinatizadeh, A. A. L., & Sharafi, K. (2015). Performance of an anaerobic baffled reactor (ABR) treating high strength baker’s yeast manufacturing wastewater. Journal of the Taiwan Institute of Chemical Engineers, 47, 137–148.
Alam, M. A., Wan, C., Zhao, X. Q., Chen, L. J., Chang, J. S., & Bai, F. W. (2015). Enhanced removal of Zn(2+) or Cd(2+) by the flocculating Chlorella vulgaris JSC-7. Journal of Hazardous Materials, 289, 38–45.
Chen, G. Y., Zhao, L., & Qi, Y. (2015). Enhancing the productivity of microalgae cultivated in wastewater toward biofuel production: a critical review. Applied Energy, 137, 282–291.
Pittman, J. K., Dean, A. P., Osundeko, O., Pandey, A., Lee, D. J., & Logan, B. E. (2011). The potential of sustainable algal biofuel production using wastewater resources. Bioresource Technology, 102(1), 17–25.
Qin, L., Wang, Z., Sun, Y., Shu, Q., Feng, P., Zhu, L., Xu, J., & Yuan, Z. (2016). Microalgae consortia cultivation in dairy wastewater to improve the potential of nutrient removal and biodiesel feedstock production. Environmental Science & Pollution Research, 23(9), 8379–8387.
Rawat, I., Kumar, R. R., Mutanda, T., & Bux, F. (2011). Dual role of microalgae: phycoremediation of domestic wastewater and biomass production for sustainable biofuels production. Applied Energy, 88(10), 3411–3424.
Franchino, M., Tigini, V., Varese, G. C., Mussat, S. R., & Bona, F. (2016). Microalgae treatment removes nutrients and reduces ecotoxicity of diluted piggery digestate. Science of the Total Environment, 569-570, 40–45.
Monlau, F., Sambusiti, C., Ficara, E., Aboulkas, A., Barakat, A., & Carrère, H. (2015). New opportunities for agricultural digestate valorization: current situation and perspectives. Energy & Environmental Science, 8(9), 2600–2621.
Uggetti, E., Sialve, B., Latrille, E., & Steyer, J. P. (2014). Anaerobic digestate as substrate for microalgae culture: the role of ammonium concentration on the microalgae productivity. Bioresource Technology, 152(1), 437–443.
Ling, J., Nip, S., Cheok, W. L., de Toledo, R. A., & Shim, H. (2014). Lipid production by a mixed culture of oleaginous yeast and microalga from distillery and domestic mixed wastewater. Bioresource Technology, 173, 132–139.
Santos, C. A., & Reis, A. (2014). Microalgal symbiosis in biotechnology. Applied Microbiology and Biotechnology, 98(13), 5839–5846.
Tchakouteu, S. S., Kalantzi, O., Gardeli, C., Koutinas, A. A., Aggelis, G., & Papanikolaou, S. (2015). Lipid production by yeasts growing on biodiesel-derived crude glycerol: strain selection and impact of substrate concentration on the fermentation efficiency. Journal of Applied Microbiology, 118(4), 911–927.
Ersahin, M. E., Ozgun H., Dereli R. K., Ozturk, I. (2011). Anaerobic treatment of industrial effluents: An overview of applications. InTech.
Magdouli, S., Brar, S. K., & Blais, J. F. (2016). Co-culture for lipid production: advances and challenges. Biomass & Bioenergy, 92, 20–30.
Li, L., Li, Y., Sun, Y., Yuan, Z., Lv, P., Kang, X., Zhang, Y., & Yang, G. (2018). Influence of the feedstock ratio and organic loading rate on the co-digestion performance of Pennisetum hybrid and cow manure. Energy & Fuels, 32(4), 5171–5180.
Bigogno, C., Khozin-Goldberg, I., Boussiba, S., Vonshak, A., & Cohen, Z. (2002). Lipid and fatty acid composition of the green oleaginous alga Parietochloris incisa, the richest plant source of arachidonic acid. Phytochemistry, 60(5), 497–503.
Friedl, A., Padouvas, E., Rotter, H., & Varmuza, K. (2005). Prediction of heating values of biomass fuel from elemental composition. Analytica Chimica Acta, 544(1–2), 191–198.
Zhang, Z., Ji, H., Gong, G., Zhang, X., & Tan, T. (2014). Synergistic effects of oleaginous yeast Rhodotorula glutinis and microalga Chlorella vulgaris for enhancement of biomass and lipid yields. Bioresource Technology, 164(7), 93–99.
Cheirsilp, B., Suwannarat, W., & Niyomdecha, R. (2011). Mixed culture of oleaginous yeast Rhodotorula glutinis and microalga Chlorella vulgaris for lipid production from industrial wastes and its use as biodiesel feedstock. New Biotechnology, 28(4), 362–368.
Cheirsilp, B., Kitcha, S., & Torpee, S. (2012). Co-culture of an oleaginous yeast Rhodotorula glutinis and a microalga Chlorella vulgaris for biomass and lipid production using pure and crude glycerol as a sole carbon source. Annals of Microbiology, 62(3), 987–993.
Yang, L., Tan, X., Li, D., Chu, H., Zhou, X., Zhang, Y., & Yu, H. (2015). Nutrients removal and lipids production by Chlorella pyrenoidosa cultivation using anaerobic digested starch wastewater and alcohol wastewater. Bioresource Technology, 181, 54–61.
Tan, X., Chu, H., Zhang, Y., Yang, L., Zhao, F., & Zhou, X. (2014). Chlorella pyrenoidosa cultivation using anaerobic digested starch processing wastewater in an airlift circulation photobioreactor. Bioresource Technology, 170(5), 538–548.
Åkerström, A. M., Mortensen, L. M., Rusten, B., & Gislerød, H. R. (2014). Biomass production and nutrient removal by Chlorella sp. as affected by sludge liquor concentration. Journal of Environmental Management, 144(21), 118–124.
Sestric, R., Munch, G., Cicek, N., Sparling, R., & Levin, D. B. (2014). Growth and neutral lipid synthesis by Yarrowia lipolytica on various carbon substrates under nutrient-sufficient and nutrient-limited conditions. Bioresource Technology, 164(7), 41–46.
Xia, A., & Murphy, J. D. (2016). Microalgal cultivation in treating liquid digestate from biogas systems. Trends in Biotechnology, 34(4), 264–275.
Xu, J., Zhao, Y., Zhao, G., & Zhang, H. (2015). Nutrient removal and biogas upgrading by integrating freshwater algae cultivation with piggery anaerobic digestate liquid treatment. Applied Microbiology and Biotechnology, 99(15), 6493–6501.
Vachova, L., & Palkova, Z. (2005). Physiological regulation of yeast cell death in multicellular colonies is triggered by ammonia. Journal of Cell Biology, 169(5), 711–717.
Wang, L. A., Li, Y. C., Chen, P., Min, M., Chen, Y. F., Zhu, J., et al. (2010). Anaerobic digested dairy manure as a nutrient supplement for cultivation of oil-rich green microalgae Chlorella sp. Bioresource Technology, 101(8), 2623–2628.
Wang, L., Wang, Y., Chen, P., & Ruan, R. (2010). Semi-continuous cultivation of Chlorella vulgaris for treating undigested and digested dairy manures. Applied Biochemistry and Biotechnology, 162(8), 2324–2332.
Coelho, M. A. Z., Amaral P. F. F., Belo I. (2010). Yarrowia lipolytica: An industrial workhorse. Formatex.
Trenčevski, K., & Kera, S. (2013). Identification of the sulphate ion as one of the key components of yeast spoilage of a sports drink through genome-wide expression analysis. Journal of General and Applied Microbiology, 59(3), 227–238.
Bajpai, P. (2017). Microorganisms used for single-cell protein production. In: Single cell protein production from lignocellulosic biomass. SpringerBriefs in Molecular Science. Springer.
Qin, L., Liu, L., Zeng, A. P., & Wei, D. (2017). From low-cost substrates to single cell oils synthesized by oleaginous yeasts. Bioresource Technology, 245(Pt B), 1507–1519.
Yen, H. W., Chen, P. W., & Chen, L. J. (2015). The synergistic effects for the co-cultivation of oleaginous yeast-Rhodotorula glutinis and microalgae-Scenedesmus obliquus on the biomass and total lipids accumulation. Bioresource Technology, 184, 148–152.
Vardon, D. R., Sharma, B. K., Blazina, G. V., Rajagopalan, K., & Strathmann, T. J. (2012). Thermochemical conversion of raw and defatted algal biomass via hydrothermal liquefaction and slow pyrolysis. Bioresource Technology, 109, 178–187.
Rizzo, A. M., Prussi, M., Bettucci, L., Libelli, I. M., & Chiaramonti, D. (2013). Characterization of microalga Chlorella as a fuel and its thermogravimetric behavior. Applied Energy, 102(2), 24–31.
Acknowledgements
This work was supported by the National Natural Science Foundation of China (Grant No. 21606230), the Sciences and Technology of Guangzhou (Grant No. 201704030084), the Natural Science Foundation for research team of Guangdong Province (Grant No. 2016A030312007), the Science and Technology Program of Guangdong (Grant No. 2015A020216003, 2016A010105001), and the National Key Research and Development Program-China (2016YFB0601004). This work is partly supported by the 111 Project (B17018).
Author information
Authors and Affiliations
Corresponding author
Ethics declarations
Conflict of Interest
The authors declare that they have no competing interests.
Rights and permissions
About this article
Cite this article
Qin, L., Wei, D., Wang, Z. et al. Advantage Assessment of Mixed Culture of Chlorella vulgaris and Yarrowia lipolytica for Treatment of Liquid Digestate of Yeast Industry and Cogeneration of Biofuel Feedstock. Appl Biochem Biotechnol 187, 856–869 (2019). https://doi.org/10.1007/s12010-018-2854-8
Received:
Accepted:
Published:
Issue Date:
DOI: https://doi.org/10.1007/s12010-018-2854-8