Abstract
Thermal analysis was used to study the influence of CaCl2 and urea as possible chemical additives inhibiting coal oxidation process at temperatures 100–300 °C. Weight increase due to oxygen chemisorption and corresponding amount of evolved heat were evaluated as main indicative parameters. TA experiments with different heating rates enabled determination of effective activation energy E a as a dependence of conversion. In the studied range of temperatures, the interaction of oxygen with (untreated) coal was confirmed rather as a complex process giving effective activation energies changing continuously from 70 kJ mol−1 (at about 100 °C) to ca. 180 kJ mol−1 at temperatures about 250 °C. The similar trend in E a was found when chemical agents were added to the coal. However, while the presence of CaCl2 leads to higher values of the effective activation energies during the whole temperature range, urea causes increase in E a only at temperatures below 200 °C. Exceeding the temperature 200 °C, the presence of urea in the coal induces decrease in activation energy of the oxidation process indicating rather catalysing than inhibiting action on coal oxidation. Thus, CaCl2 can only be recommended as a ‘real’ inhibitor affecting interaction of coal with oxygen at temperatures up to 300 °C.
Similar content being viewed by others
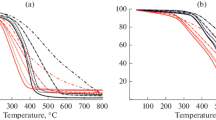
Explore related subjects
Discover the latest articles, news and stories from top researchers in related subjects.Avoid common mistakes on your manuscript.
Introduction
Impregnation of coal by solution of appropriate additive is one of the possible ways to prevent the process of spontaneous combustion of coal. For the purpose, wide range of inorganic and organic additives has been examined [1–4]. At ambient temperatures, hindered access of oxygen to the coal surface when coated by the additive solution is generally assumed to be basic principle of the inhibitors action [1, 3]. However, at higher temperatures (ca. 300 °C), chemical reactions between coal and additives were also observed [1].
Based on our earlier calorimetric investigations, calcium chloride and urea were recognised as effective agents decreasing a heat evolution during coal oxidation at ambient temperatures [5]. The paper is aimed at evaluating the influence of these additives on coal oxidation at temperatures from 100 to 300 °C, and, thus, to offer more complete view on their behaviour. Since coal oxidation at the higher temperatures is accompanied with both changes in coal weight and pronounced heat evolution [6–8], simultaneous TG-DSC measurements were used as the most efficient experimental approach in the study.
Experimental
Sample of typical, high volatile bituminous coal of Ostrava-Karviná Coal Mines District (Czech Republic) was used for the experiments. Table 1 summarizes basic characteristics of the coal. The coal lump was milled and sieved; fragmentation 0.25–0.80 mm was used for the experimental investigations.
Aqueous solutions of additives at concentration 0.1 M were prepared by dissolving appropriate amount of CaCl2 (p.a.) or urea (p.a.) in deionised water.
For testing the effect of additives on coal oxidation, 2 cm3 of the additive solution was added to 0.5 g of coal, mechanically homogenized and dried for several days on air at room temperature (samples denoted ‘C-CaCl2’ and/or ‘C-urea’). As a comparative basis, coal sample pre-treated by the same way with deionised water only was used (denoted sample ‘C’). In addition, to elucidate stability of the additives over the studied temperature range, blank test was designed consisting of the same pre-treatment procedure as mentioned above, however, instead of coal, powder of α-Al2O3 (p.a., annealed at 1300 °C before use) was used as an inert supporting solid (samples denoted ‘A-CaCl2’ and/or ‘A-urea’).
Simultaneous TG-DSC measurements (Netzsch STA 449C) with different heating rates (2, 5, 10 and 20 K min−1) in the temperature range 30–300 °C in dynamic atmosphere of oxygen (100 cm3 min−1) were performed in crucibles from α-Al2O3 (initial sample mass 19–21 mg, 20 mg of α-Al2O3 used as a reference). Thermogravimetric data were applied for determination of dependence of effective activation energy E a on conversion using isoconversional method of Kissinger–Akahira–Sunose [9] based on equation
where T α is temperature at which given extent of conversion is reached during heating with heating rate βi.
Results and discussion
Typical development of the coal sample weight during its oxidation in the temperature range 30–300 °C is illustrated in Fig. 1. Decrease in weight can be seen at the beginning of heating (up to about 120 °C) followed by increase in weight at temperatures 120–250 °C. The coal weight decrease can be explained mainly by moisture loss. On the other hand, increase in coal mass is ascribed to oxygen chemisorption occurring at these temperatures [3] and manifested by marked heat evolution (cf. DSC curve, Fig. 1, sample C). The oxygen chemisorption stage is in the focus of the present study. As basic parameters characterizing the chemisorption stage of coal oxidation, temperature of maximum sample weight T max, weight increase due to oxygen chemisorption w O as well as heat evolved during oxygen chemisorption Q O were evaluated [3].
TG curves of coal oxidation in the presence of additives (Fig. 1, samples ‘C-CaCl2’ and ‘C-urea’) have similar shape, however, they are evidently influenced by lability of the additives in the studied temperature range as deduced from the experiments with additive-coated α-Al2O3 (Fig. 1, samples ‘A-CaCl2’ and ‘A-urea’). CaCl2 loses weight mainly below 100 °C (probably hydration water) while urea starts to decompose between 100 and 200 °C. Both the processes are endothermic in nature with very low heat consumption (cf. Fig. 1). With this respect, to obtain unaffected TG and/or DSC curves (TGcorr and DSCcorr) of oxygen interaction with additive-coated coal, corrections were made by subtraction of TG and/or DSC curve of ‘A-CaCl2’ and/or ‘A-urea’ samples, respectively.
Comparison of corrected TG curves of additive-treated coal with that of untreated coal at different heating rates is demonstrated in Fig. 2. In general, chemisorption stage of coal oxidation for all the samples is shifted to higher temperatures when heating rate increases; simultaneously, weight increase of coal due to oxygen bonding becomes smaller. It is understandable because low heating rate enables interaction between oxygen and coal to reach higher conversion at lower temperature.
From the corrected TG and/or DSC curves, basic parameters characterizing chemisorption stage of coal oxidation were then determined (Fig. 3, Table 2) [3].
The results show that the presence of CaCl2 and/or urea during coal oxidation causes just a slight shift of maximal temperature T max to higher values. In general, reaching the value of T max , coal oxidation can be considered to pass from oxygen chemisorption stage to flammable combustion stage. So, there is probably no considerable effect of the additives on the transition of coal oxidation to the combustion stage. On the other hand, increase in weight w O and evolved heat Q O during the oxygen chemisorption stage are evidently affected by the additives. The presence of both the additives caused increase in weight of the chemisorbed oxygen while evolved oxidation heat Q O was surprisingly lower in comparison with untreated coal (Table 2). The reason of such behaviour can be seen in probable changes in coal oxidation mechanism induced by the additives at the temperatures. However, influence of possible change in coal properties (e.g. thermal conductivity) in the presence of additives cannot be excluded as a reason. Irrespective of the uncertainty, it is worth mentioning that the lower values of coal oxidation heat were determined in the presence of both CaCl2 and urea also earlier at low-temperature range (30 °C) using direct calorimetric measurements [3].
It is interesting to follow the effect of additives on kinetics of coal-oxygen interaction, namely on its activation energy. Dependence of conversion on temperature (under different heating rate) is required to study dependence of effective activation energy on conversion by isoconversional methods. Thus, corrected thermogravimetric data were used for conversion calculation according to the formula
where TGcorr,i is corrected value of TG signal at temperature (or time) i, m 0 is TG value before the beginning of weight increase and m ∞ is TG value at temperature T max (maximum of the sample weight) as indicated in Fig. 3. All TG values were used in percentage scale.
Resulting values of the effective activation energy E a as dependences on conversion and temperature, respectively, are depicted in Fig. 4. In general, the interaction of coal with oxygen in studied range was confirmed as complex process [10] with continuous change in effective activation energies from ca. 70 kJ mol−1 at the beginning of reaction (conversion 0.05) to about 180 kJ mol−1 at conversion ca. 0.95. The similar trend in E a was found in the presence of the studied inhibitors. However, the presence of CaCl2 leads to higher values of the effective activation energy (by ca. 15–25 kJ mol−1) during the whole temperature range 150–250 °C while urea causes increase in E a only at temperatures below 200 °C. The main reason of such behaviour of the both additives can be seen in their different effects on coal oxidation. Concerning the inhibiting ability of the calcium chloride, hindered access of oxygen to the coal surface when coated by CaCl2 is generally assumed to be the principle of its action [1, 3, 11]. Based on the obtained results, the inhibiting principle of CaCl2 appears to be thus confirmed at all studied temperatures. As to urea, its preferred attack on free radicals (i.e. primary active sites of coal low-temperature oxidation [12]) resulting in their recombination can be expected [3]. Figure 4 then indicates that such an inhibiting effect of urea works to about 200 °C only. The loss of the urea inhibiting ability exceeding 200 °C can be ascribed both its (at least partial) decomposition (cf. Fig. 1) and possible changes in coal oxidation mechanistic pathway at the temperatures [13]. In every case, above the temperature level, urea acts rather as ‘catalyst’ with decrease in values of effective activation energy in comparison with untreated coal.
Conclusions
Thermoanalytical study of the influence of CaCl2 and urea on coal oxidation process proved that both additives cause decrease in oxidation heat at temperatures 100–250 °C. However, amount of chemisorbed oxygen was found to be increased in the presence of the additives in comparison with untreated coal.
Based on the temperature dependences of the effective activation energy of coal oxidation, CaCl2 was found to shift the activation energies E a to higher values in comparison with untreated coal during the whole temperature range to be studied. On the other hand, the presence of urea results in increase of E a only at temperatures below 200 °C, while exceeding 200 °C it induces evident decrease in activation energy. Thus, for the temperatures above 200 °C, urea can hardly be recommended as inhibiting agent of coal oxidation process, its action becoming rather catalytic.
References
Smith AC, Miron Y, Lazzara CP. Inhibition of spontaneous combustion of coal. Report of investigation–USA Bureau of Mines, RI 9196, 1988.
Watanabe WS, Zhang DK. The effect of inherent and added inorganic matter on low-temperature oxidation reaction of coal. Fuel Process Technol. 2001;74:145–60.
Saranchuk VI, et al. Oxidation and self-heating of the coal. Kiev: Naukova Dumka; 1994. (in Russian).
Singh AK, Sahay N, Ahmad I, Mondal S. Role of inorganic compounds as inhibitor in diminishing self-heating phenomena of Indian coal. J Mines Metals Fuels. 2002;50:356–9.
Taraba B, Peter R, Slovák V. Calorimetric investigation of chemical additives affecting oxidation of coal at low temperatures. Fuel Process Technol. 2011;92:712–5.
Mohalik NK, Panigrahi DC, Singh VK. Application of thermal analysis techniques to assess proneness of coal to spontaneous heating. J Therm Anal Calorim. 2009;98:507–19.
Kok MV, Pokol G, Keskin C, et al. Combustion characteristics of lignite and oil shale samples by thermal analysis techniques. J Therm Anal Calorim. 2004;76:247–54.
Slovák V, Taraba B. Effect of experimental conditions on parameters derived from TG-DSC measurements of low-temperature oxidation of coal. J Therm Anal Calorim. 2010;101:641–6.
Akahira T, Sunose T. Method of determining activation deterioration constant of electrical insulating materials. Res Rep Chiba Inst Technol (Sci Technol). 1971;16:22–31.
Vyazovkin SV, Lesnikovich AI. An approach to the solution of the inverse kinetic problem in the case of complex processes: Part 1. Methods employing a series of thermoanalytical curves. Thermochim Acta. 1990;165:273–80.
Sujanti W, Zhang DK. A laboratory study of spontaneous combustion of coal: the influence of inorganic matter and reactor size. Fuel. 1999;78:549–56.
Liotta R, Brons G, Isaacs J. Oxidative weathering of Illinois no. 6 coal. Fuel. 1983;62:781–91.
Calemma V, Iwanski P, Rausa R, Girardi E. Changes in coal structure accompanying the formation of regenerated humic acids during air oxidation. Fuel. 1994;73:700–7.
Acknowledgements
The article has been done in connection with the project Institute of Environmental Technologies, Reg. No. CZ.1.05/2.1.00/03.0100 supported by Research and Development for Innovations Operational Programme financed by Structural Funds of European Union and from the means of state budget of the Czech Republic.
Author information
Authors and Affiliations
Corresponding author
Rights and permissions
About this article
Cite this article
Slovák, V., Taraba, B. Urea and CaCl2 as inhibitors of coal low-temperature oxidation. J Therm Anal Calorim 110, 363–367 (2012). https://doi.org/10.1007/s10973-012-2482-4
Published:
Issue Date:
DOI: https://doi.org/10.1007/s10973-012-2482-4