Abstract
In this study the effect of ceria addition on the performance of a model Ba-based lean NO x trap (LNT) catalyst was examined. The presence of ceria improved NO x storage capacity in the temperature range 200–400 °C under both continuous lean and lean-rich cycling conditions. Temperature-programmed experiments showed that NO x stored in the ceria-containing catalyst was thermally less stable and more reactive to reduction with both H2 and CO as reductants, albeit at the expense of additional reductant consumed by reduction of the ceria. These findings demonstrate that the incorporation of ceria in LNTs not only improves NO x storage efficiency but also positively impacts LNT regeneration behavior.
Similar content being viewed by others
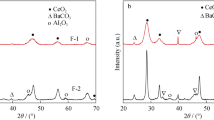
Explore related subjects
Discover the latest articles, news and stories from top researchers in related subjects.Avoid common mistakes on your manuscript.
1 Introduction
Lean-burn engines, including diesel and gasoline direct injection engines, are generally more fuel-efficient than stoichiometric gasoline engines and emit less carbon dioxide. Thus there are both economic and environmental incentives to increase the use of lean-burn vehicles. However, the development of effective after treatment methods for the abatement of lean exhaust emissions represents a challenge to the automotive industry. While conventional three-way catalysts are highly effective for control of nitrogen oxides (NO x ), CO and hydrocarbons (HCs) from stoichiometric exhaust, the technology for removal of NO x from lean exhaust is still not fully developed. Specifically, the excess oxygen present in lean exhaust competes with NO x for available reductants (H2, CO, HCs), and significantly decreases NO x reduction efficiency.
Of the several technologies proposed for lean NO x removal, the lean NO x trap (LNT), also known as the NO x Storage-Reduction (NSR) catalyst or the NO x Adsorber Catalyst (NAC), is considered a promising candidate. LNT catalysts contain precious metals (generally Pt and Rh) and an alkali or alkaline-earth metal storage component (most commonly BaO) supported on a high surface area material (usually alumina). Under typical lean exhaust conditions, NO is oxidized to NO2 over precious metal sites and reversibly stored as nitrates or nitrites on the storage materials. Stored NO x species are subsequently decomposed, released and reduced to N2 during short periodic excursions to rich (i.e., net reducing) conditions. The trapping ability of the LNT catalyst is thus restored after a lean-rich cycle.
A major issue still remaining for LNT catalysts is that of deactivation due to sulfur poisoning. Decomposition of barium sulfate requires high temperatures (around 700 °C) and reducing conditions. Such treatments reduce the high fuel efficiency of lean-burn engines and result in catalyst deterioration due to sintering of the precious metal and NO x storage components, as well as the occurrence of unwanted reactions between washcoat components. Therefore, the improvement of LNT durability represents a key challenge.
Ceria is an important component of LNTs formulated for lean burn gasoline applications, its role being to provide the necessary oxygen storage capacity when the engine is operating under stoichiometric conditions, i.e., when the LNT is required to function as a conventional three-way catalyst [1–3]. However, to date, the role of ceria in LNT catalysis has received little attention. Theis and co-workers reported that the addition of ceria improved NO x trap sulfur tolerance [4]. It is well known that ceria is able to store sulfur (as sulfate) [5], which may help to protect the main NO x storage component from sulfur poisoning. Additionally, Pt-promoted ceria is known to be a very effective catalyst for the water-gas shift (WGS) reaction [6, 7], and the hydrogen produced can be beneficial to LNT regeneration and desulfation. However, during rich purges oxygen stored by the ceria reacts with the reductants, increasing the total amount of reductant required for trap regeneration. In order to gain a better understanding of the benefits and disadvantages of ceria addition to LNT catalysts, we have studied the impact of ceria on NOx storage under both continuous lean flowing and lean-rich cycling conditions, as well as the impact on LNT regeneration characteristics.
2 Experimental
2.1 Catalyst Preparation
Pt/CeO2 and Pt/BaO/Al2O3 powders were prepared by incipient wetness impregnation. CeO2 (Rhodia, surface area of 119 m2/g) was impregnated with an aqueous solution of tetraammineplatinum(II) nitrate. The impregnated sample was dried and then calcined in air at 500 °C for 3 h. Pt/BaO/Al2O3 was prepared in a sequential manner. γ-alumina (surface area of 132 m2/g) was impregnated with aqueous Ba(NO3)2, dried and calcined at 500 °C in air. The Ba-loaded Al2O3 was subsequently impregnated with aqueous tetraammineplatinum(II) nitrate and further calcined at 500 °C. The Pt loading of both materials was 1 wt%, and the BaO content in the Pt/BaO/Al2O3 sample was 20 wt%. To prepare a ceria-containing LNT catalyst, a portion of Pt/BaO/Al2O3 was physically mixed with Pt/CeO2 in a 74:26 weight ratio.
2.2 NO x Storage and Lean-rich Cycling Experiments
A microreactor loaded with ca. 150 mg of powder catalyst was employed to explore the NO x storage and regeneration behavior of the two model catalysts (see Fig. 1), the effluent gases being analyzed with a mass spectrometer (SRS RGA100). All flow conditions were operated at a gas hourly space velocity (GHSV) of 30,000 h−1. Before each experiment the catalysts were pretreated in 1% H2/Ar flow at 450 °C for 1 h. For NO x storage measurements, the catalyst was then subjected to typical rich conditions—3375 ppm H2, 5625 ppm CO, 5% CO2 and 5% H2O in Ar at 120 cm3 (STP)/min (sccm) at 450 °C for an additional hour and then cooled to the desired temperature. NO x storage was recorded for 60 min while flowing typical lean conditions—300 ppm NO, 8% O2, 5% CO2 and 5% H2O in Ar at 120 sccm. This step was followed by a 15-min exposure to rich conditions, and then the 60-min cycle was repeated. This storage cycle was repeated until the measured storage value was consistent—up to six times.
NO x storage-regeneration experiments were performed while cycling between lean and rich conditions. Following pretreatment the catalyst was cooled to 400 °C, followed by cycling between lean and rich conditions until the catalyst reached a cycle-average steady-state. Once this steady state lean-rich cycle had been recorded, the catalyst was cooled to 300 °C while cycling. A steady-state cycle was then recorded at 300 °C followed by cooling to 200 °C. The total lean-rich cycle consisted of a 6 min lean phase, a 30 s transition to rich, a 30 s rich-phase, and then another 30 s transition to lean. A pneumatically-actuated 4-way valve was used to switch phases from lean to rich. For the purpose of NO x storage and release calculations, the NO x storage phase was taken to be 6.5 min in length (lean phase plus subsequent 30 s transition) and the regeneration phase was taken to be 1.0 min in length (rich phase plus subsequent 30 s transition). In part due to the length of these transitions, exotherms were minimal in the reactor system, the maximum observed being ca. 5 °C.
2.3 TPR and TPD Experiments
A temperature-programmed reduction (TPR) procedure was used to study how different reductants and H2O impact the LNT regeneration behavior. The catalysts were pretreated as before and then cooled in 1% H2/Ar to 300 °C. NO x was stored at 300 °C in the absence of CO2 and H2O for a period of typically 100–120 min in 300 ppm NO and 8% O2 at 120 sccm. Under these conditions, the catalysts were still not saturated (typically ca. 0.4 mmol NO x /g stored, versus >0.6 mmol NO x /g stored at saturation). Subsequently, the catalysts were purged in Ar and cooled to 50 °C. For experiments in the absence of H2O the reductant flow was established in the exhausted portion of the 4-way valve while the reactor was being purged in Ar. At the beginning of the temperature ramp the flow was switched from the purge stream to the reductant stream. The furnace was ramped at 10 °C/min to 500 °C, and then held for 30 min. The microreactor system introduces water vapor after the 4-way valve, so a different approach was necessary when H2O was included in the TPR. Once the reactor had cooled to 50 °C, the reactor was sealed in Ar and the reductant stream was stabilized in the reactor bypass loop. At the beginning of the temperature ramp the flow was manually switched from the bypass loop to the reactor, and then the TPR proceeded as previously described.
3 Results and Discussion
3.1 NO x Storage Capacity
NO x storage measurements were performed on two catalyst samples, Pt/BaO/Al2O3 (hereafter denoted as PBA) and a physical mixture of Pt/BaO/Al2O3 and Pt/CeO2 (74:26 weight ratio, denoted as PBAC), using feed gas containing 300 ppm NO, 8% O2, 5% CO2 and 5% H2O. As shown in Fig. 2, NO x slip was observed from both catalysts immediately after exposure to the gas mixture, although NO x storage continued for more than 1 h before the catalysts were saturated. For both PBA and PBAC, maximum NO x storage after 1 h was observed at 300 °C. For PBA, the measured storage capacity at this temperature (0.27 mmol NO x /g cat., see Table 1) corresponded to 84% utilization of the total Ba present. The lowest NO x storage on PBA was observed at 200 °C (0.19 mmol/g cat.), with only 59% of the loaded Ba being utilized. Compared to PBA, PBAC showed higher NO x storage capacity (0.28 mmol NO x /g cat) at 300 °C after 1 h, indicating a slight benefit from the presence of ceria. At 200 °C, a significant improvement in NO x storage capacity was found for the ceria-containing catalyst, the quantity of stored NO x increasing from 0.19 mmol/g for PBA to 0.24 mmol/g for PBAC. Clearly, the addition of ceria significantly improved NO x storage at low temperature. However, at 400 °C, the presence of ceria resulted in decreased NO x storage capacity (0.17 mmol/g for PBAC versus 0.24 mmol/g for PBA). The NO x storage capacity of PBAC at this temperature corresponds to 71% of that for PBA, being almost equivalent to the percentage of the PBA component in catalyst PBAC. This implies that the NO x storage capacity of PBAC at high temperature derives from the Ba component only, with no benefit from the added ceria. In a previous DRIFTS study [8], we observed that cerium nitrates were formed on the surface of Pt/CeO2 upon exposure to NO or NO2. Upon heating in inert gas, these nitrates were largely stable to 300 °C, but completely disappeared upon heating to 400 °C. In a separate experiment under flowing NO/O2, nitrate bands were observed at 400 °C, although with greatly reduced intensity relative to the spectrum obtained at 300 °C. Evidently the NO x storage capacity of ceria is greatly diminished at 400 °C, whereas at lower temperatures it can contribute significantly to the NO x storage capacity of LNT catalysts. The ability of ceria to store NO x was also reported by Haneda et al. [9], and it was found that doping Zr into CeO2 can improve the NO x storage capacity.
The superior storage efficiency of PBAC relative to PBA is also manifested at short storage times. At 200 °C, a storage efficiency of 87% was obtained for PBAC for the first 6 min of the experiment, compared to only 69% for PBA (storage efficiency being defined as the percentage of NO x in the feed that is stored, see Table 1). Interestingly, the benefit of ceria addition to NO x storage efficiency during the first 6 min extended over the entire temperature range. After 60 min, the average storage efficiencies for PBAC and PBA were only 25% and 20%, respectively, implying a significant decrease in NO x storage efficiency with time. Similar to the 60 min data, at short storage times the benefit in NO x storage capacity resulting from ceria addition decreases with increasing temperature.
3.2 NO x Storage-reduction Performance
To understand the effect of ceria addition on NO x storage during lean-rich cycling, NO x storage-reduction experiments were performed under long cycling conditions (6.0 min lean and 0.5 min rich with 30 s allowed for each transition). As shown in Fig. 3, after reaching a cycle-average steady state, slightly higher lean phase NO x slip was observed for PBA compared to PBAC at each of the three temperatures examined. Table 2 summarizes the NO x storage, unconverted NO x release (slip) and NO x reduction measured for the two catalysts during lean-rich cycling. Similar to the continuous lean flow experiments above, both catalysts showed optimal NO x storage at 300 °C with a measured NO x storage capacity of 47.4 μmol/g for PBA and 56.0 μmol/g for PBAC. However, the beneficial effect of ceria on NO x storage extended over the whole temperature range from 200 to 400 °C. Consistent with the improved NO x storage properties of PBAC at low temperature under continuous lean flowing conditions, the improvement in the lean phase NO x storage for PBAC relative to PBA was most evident at 200 °C during lean-rich cycling, while PBAC exhibited only a slight advantage at 400 °C. After switching to the rich phase, both catalysts showed very similar NO x release performance at the three temperatures, the largest NO x slip (1.6 μmol NO x /g for PBA versus 1.7 μmol NO x /g for PBAC) being observed at 200 °C and the smallest (0.5 μmol NO x /g for both PBA and PBAC) at 300 °C. Based on the amount of NO x stored, only ∼1% of the stored NO x was released without being reduced after switching to the rich phase at 300 °C. Given the low concentration of NO x slip during the rich phase, the NO x conversion averaged over lean-rich cycles was largely dependent on the effective lean phase NO x storage efficiency, from which it follows that catalyst PBAC afforded higher NO x conversion than PBA at each temperature.
Outlet NO x concentration as a function of time during lean phase under lean-rich cycling over (a) PBA and (b) PBAC. Conditions are the same as in Table 2
It is also noteworthy that PBAC displayed a superior selectivity to N2 over PBA for the entire temperature range (Table 2). A possible explanation for this observation lies in the fact that high [H2]:[NO x ] ratios favor NO x reduction to NH3 [10]. Given the expected higher oxygen storage capacity of PBAC relative to PBA, the effective [H2]:[NO x ] ratio should be lower in PBAC due to partial consumption of the reductants by the reaction with stored oxygen. Additionally (or alternatively), for PBAC, ceria may play a role in helping to oxidize any NH3 formed to N2 as the reaction front propagates along the length of the catalyst bed, as suggested by the results of recently published spatially resolved mass spectrometric studies [11].
It must be appreciated that under cycling conditions the lean phase NO x storage efficiency represents the product of the intrinsic storage efficiency (i.e., as measured under lean-only conditions) and the rich phase regeneration efficiency. Thus the superior performance of PBAC under cycling conditions can be a function of the intrinsic storage efficiency and/or the rich phase regeneration efficiency. To further understand the difference in regeneration behavior between PBAC and PBA, the thermal stability and reactivity of NO x stored on both PBAC and PBA was studied under different atmospheres (inert and reducing) by means of temperature-programmed techniques.
3.3 Thermal Stability of Stored NO x
The thermal stability of NO x stored on the two catalysts was explored by means of temperature-programmed desorption (TPD) in flowing Ar. NO x was first stored on the catalysts at 300 °C for ca. 2 h using a feed containing 300 ppm NO and 8% O2. The samples were then cooled to room temperature in flowing Ar, prior to ramping to 500 °C at a rate of 10 °C/min. As shown in Fig. 4, NO x evolution was not detected below 300 °C. This is in line with literature reports that thermal desorption of NO x does not occur below the temperature at which adsorption was performed [12–14]. Decomposition of the adsorbed NO x species commenced slightly above 300 °C, as evidenced by the evolution of NO x , this process extending up to 500 °C for both catalysts. However, the temperature corresponding to maximum NO x release was different for the two catalysts. PBAC showed a maximum NO x release at ∼470 °C, whereas PBA demonstrated a maximum at ∼500 °C. During the TPD, 85% of NO x stored on PBAC was released, compared to 46% for PBA. From this it follows that a significant fraction of the adsorbed NO x species in PBAC exhibited lower thermal stability than those present in PBA, a finding that can be attributed to the lower thermal stability of cerium nitrates formed in PBAC in comparison with barium nitrate species.
3.4 Reduction Reactivity of Stored NO x
The reactivity of stored NO x was investigated by means of temperature-programmed reduction (TPR) experiments. After NO x storage at 300 °C, the catalysts were cooled to ∼50 °C in flowing Ar; TPR followed with either 2000 ppm H2 (H2-TPR), 3000 ppm CO (CO-TPR), or 3000 ppm CO + 5% H2O (CO + H2O-TPR). In the case of H2-TPR, minimal NO x release was observed from either sample, indicating that almost all of the stored NO x was reduced to N2, NH3 and/or N2O (accurate quantification of the latter two species being impossible with the analytical system used). Figure 5 shows the concentrations of N2 and H2 in the effluent as a function of time/temperature during H2-TPR. Compared to Ar-TPD, the catalysts were regenerated at significantly lower temperatures. On PBA, both H2 consumption and N2 production began simultaneously at 150 °C and ceased at ca. 385 °C; however, for PBAC, H2 consumption started 70 °C lower than N2 production, 80 °C versus 150 °C (Table 3). This low temperature consumption is associated with reduction of the ceria from an oxidized to a reduced state. N2 production and H2 consumption simultaneously ceased at 295 °C for PBAC, i.e., 90 °C lower than PBA. These findings suggest that the NO x species in PBAC are more easily decomposed in the presence of H2 than are those in PBA.
CO-TPR demonstrated a small increase in the level of unconverted NO x release, respectively 6 and 19 μmol NO x /gcat for PBA and PBAC (versus 543 and 596 μmol NO x /gcat stored, respectively). For PBA, NO x evolution occurred in the range 139 to 290 °C, as compared to the range 114 to 195 °C for PBAC (not shown). The onset of N2 production from the reduction of stored NO x by CO occurred at 195 °C for both catalysts, which is a significantly higher temperature than the 150 °C observed during H2-TPR (Fig. 6a). N2 production terminated at 427 °C on PBAC, while it extended up to 497 °C on PBA. Upon heating to 500 °C, 30% of the NO x stored on PBAC was reduced to N2 by CO, compared to 42% for PBA. This suggests that there may be some nitrate remaining on the catalysts even after heating to 500 °C. It is apparent that CO shows lower reduction efficiency than H2, as reported by several research groups [15–17]. In TPR with CO, the NO x released from the surface can be replaced by a crust of BaCO3 which impedes migration of the remaining sub-surface NO x . We have performed a similar study using DRIFT spectroscopy that also suggests CO-only reduction results in unremoved nitrates (Unpublished results).
CO-TPR of stored NO x was also studied in the presence of H2O (CO + H2O-TPR). As shown in Fig. 6b, the addition of H2O significantly altered the reduction behavior of NO x with CO. Compared to CO-TPR, the onset of N2 production was shifted to lower temperature—corresponding to 135 °C for PBAC and 180 °C for PBA. Furthermore, on PBAC the detection of N2 ceased at a lower temperature relative to CO-TPR—362 °C versus 427 °C. As shown in Fig. 7, H2 was evolved over both catalysts during CO + H2O-TPR, in each case attaining a maximum concentration circa 400 °C. In order to better understand this process, CO + H2O-TPR was performed using catalysts which had not been exposed to NO x . The resulting data show that both catalysts are highly active for the water-gas shift reaction. H2 production commenced at temperatures as low as 140 °C, with PBAC exhibiting slightly higher activity than PBA across the entire temperature range. This most likely accounts for the more facile reduction of the stored NO x in PBAC during CO + H2O-TPR.
Both H2-TPR and CO-TPR results suggest that the adsorbed NO x species in PBAC are more easily decomposed in the presence of reducing agents than those in PBA. We hypothesize that the improved regeneration characteristics of PBAC are likely a consequence of the competitive capture of NO x by the Pt/CeO2 component, which results in reduced formation of bulk Ba(NO3)2 in PBAC relative to PBA. This is akin to the idea that the ability of ceria to store sulfur (as sulfate) can be expected to help protect the main LNT NO x storage component from sulfur poisoning [4]. It is well known that upon exposure to NO x , surface nitrates are initially formed on BaO, while increased exposure results in the subsequent formation of bulk nitrates. Furthermore, Peden et al. [17] have previously shown that bulk Ba(NO3)2 is significantly more difficult to reduce than surface Ba(NO3)2. Studies are currently in progress to address this issue.
4 Conclusions
These findings show that the addition of ceria to Ba-based LNT catalysts is beneficial with respect to NO x storage capacity at temperatures up to 400 °C, as demonstrated by the results of both lean flowing experiments (in which the intrinsic NO x storage capacity is measured), and lean-rich cycling experiments (in which the effective storage capacity is determined, given that intrinsic NO x storage capacity may not be completely regenerated). Rich phase NO x slip during cycling was found to be similar for both catalysts studied, with the consequence that overall NO x conversion was significantly higher for the ceria-containing catalyst. The ceria-containing catalyst also exhibited superior regeneration characteristics. H2- and CO-TPR experiments suggest that adsorbed NO x species are more easily decomposed in the presence of reducing agents than are those in the ceria-free analog. This is likely a consequence of the competitive capture of NO x by the Pt/CeO2 component, which results in reduced formation of (less reactive) bulk Ba(NO3)2. It can be inferred that under some rich operating conditions in the temperature range used in this study (200–500 °C) a portion of the bulk nitrate is not decomposed and thus cannot participate in NO x abatement through storage and regeneration. Instead, surface nitrates play the major role in NO x storage and reduction during lean-rich cycling.
References
Matsumoto S (1994) Toyota Tec Rev 44:10
Yao HC, Yao YF (1984) J Catal 86:254
Fornasiero P, Balducci G, Di Monte R, Kaspar J, Sergo V, Gubitosa G, Ferrero A, Graziani MJ (1996) J Catal 164:173
Theis J, Ura J, Goralski C Jr, Jen H, Thanasiu E, Graves Y, Takami A, Yamada H, Miyoshi S (2003) SAE Technical Paper Series 2003-01-1160
Truex T (1999) SAE Technical Paper Series 1999-01-1543
Jacobs G, Williams L, Graham U, Sparks DE, Davis BH (2003) Appl Catal A 252:107
Phatak AA, Koryabkina N, Rai S, Ratts JL, Ruettinger W, Farrauto RJ, Blau GE, Delgass WN, Ribeiro FH (2007) Catal Today 123:224
Ji Y, Toops TJ, Uschi G, Jacobs G, Crocker M (2006) Catal Lett 110:29
Haneda M, Morita T, Nagao Y, Kintaichi Y, Hamada H (2001) Phys Chem Chem Phys 3:4696
Pihl JA, Parks JE, Daw CS, Root TW (2006) SAE Technical Paper Series 2006-01-3441
Parks J, Huff S, Swartz M, West B (2007) presentation at 10th CLEERS Workshop, Dearborn, MI
Nova I, Lietti L, Castoldi L, Tronconi E, Forzatti P (2006) J Catal 239:244
Szanyi J, Kwak JH, Hanson J, Wang C, Szailer T, Peden CHF (2005) J Phys Chem B 109:7339
Piacentini M, Maciejewski M, Burgi T, Baiker A (2004) Top Catal 30/31:71
Joza P, Jobson E, Larsson M (2004) Top Catal 30/31:177
Poulston S, Rajaram R (2003) Catal Today 81:603
Szailer T, Kwak JH, Kim DH, Hanson JC, Peden CHF, Szanyi J (2006) J. Catal. 239:51
Acknowledgments
This publication was prepared with the support of the U.S. Department of Energy, under Award No. DE-FC26–05NT42631. However, any opinions, findings, conclusions, or recommendations expressed herein are those of the authors and do not necessarily reflect the views of the DOE.
Author information
Authors and Affiliations
Corresponding author
Rights and permissions
About this article
Cite this article
Ji, Y., Toops, T.J. & Crocker, M. Effect of Ceria on the Storage and Regeneration Behavior of a Model Lean NO x Trap Catalyst. Catal Lett 119, 257–264 (2007). https://doi.org/10.1007/s10562-007-9226-2
Received:
Revised:
Accepted:
Published:
Issue Date:
DOI: https://doi.org/10.1007/s10562-007-9226-2