Abstract
In this modern era, customers demand improved functional fabrics along with some other properties. The product developments can be done in various methods; the blending of various fibres to make fabric with enhanced properties is one of them. The wet processing can affect the comfort properties of fabrics made out of different fibrous material. Here, the effect of wet processing (scouring and dyeing) was studied on the comfort and other properties of plain-woven fabrics made using weft of 100% cotton, 50:50 cotton/tencel and 50:50 cotton/modal blend was studied. The results reveal that the air permeability decreases in all samples (100% cotton fabric, cotton/modal blended fabric and Tencel/cotton blended fabric) after scouring but no significant change has been seen after dyeing. The overall moisture management capacity increases significantly in all samples after scouring and further increases after dyeing. Fabric strength increases after scouring and decreases after dying. The fabric bending modulus decreases after scouring in all fabric samples and there is not significantly change has been seen after dyeing.
Access provided by Autonomous University of Puebla. Download conference paper PDF
Similar content being viewed by others
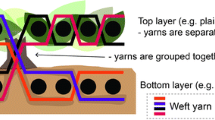
Keyworlds
- Air permeability
- Blended yarn
- Fabric comfort
- Fabric hand
- Modal fibre
- Moisture transport properties
- Tencel fibre
1 Introduction
To survive in throat-cutting competitive environment and to satisfy modern customers; the textile manufacturers and researchers are searching some new products which have improved properties. Modern customers consider comfort as one of the most important attributes in their purchase of textile and apparel products [1]. To achieve improved functional textiles; one attempt is to produce cotton/modal blended fabric and cotton/tencel blended fabrics.
Cotton is a natural cellulosic fibre while Modal and Tencel Lyocell are regenerated cellulosic fibres. The Modal® and Tencel® LF are cellulosic regenerated fibres manufactured by Lenzing Company, Austria. Like viscose, Tencel is produced from wood pulp but the process is chemically much less complex. Modal is a type of high wet modulus rayon and manufactured using cellulose obtained from beech trees [2,3,4]. The Tencel fibre has highest strength, elongation and moisture regain followed by modal fibre and cotton fibres. Although, wet tenacity reduced in both Modal and Tencel fibres; while it increases in cotton fibre. The cotton fibres show highest wet tenacity followed by Tencel fibres and modal fibres [2, 4]. The cross-sectional shapes of various fibres are shown in Fig. 1.
Mostly all cellulosic fabrics are gone through the two main wet processing stages: scouring and dyeing. These may alter the structure and properties of fabrics. This requires a detailed study. In the present work, three types of plain-woven fabrics are made using cotton yarn, cotton/tencel and cotton/modal blended yarns in weft only. The effect of wet processing on the comfort properties of these fabric samples is studied in three stages, i.e. greige state, after scouring and after dyeing. The fabric physical factors (cover factor, fabric thickness, fabric weight), air permeability, moisture transport properties, fabric stiffness and tensile properties of the fabrics were evaluated. The results are statistically analysed at 95% confidential limits.
2 Materials and Methods
2.1 Materials
Three types of plain-woven fabric samples were made using ring spun weft yarns of 30s Ne with 100% cotton fibres, 50:50% cotton/modal blend and 50:50% cotton/tencel blend yarn in weft. The warp yarn for all fabric samples is cotton/polyester (60:40 with 2/40s Ne). These three fabric samples ware processed for scouring and then dyeing. Thus, a total of nine fabric samples (three samples each of greige, scoured and dyed stage) produced to study the impact of wet processing on properties.
-
i.
Preparation of yarns
Weft yarn of 30s Ne was produced by ring spinning technique using 3.5 twist multiplier. Cotton sample was made by two varieties: J-34 and S-6 in 50:50 ratio. These two varieties are mixed in blow room stage. Modal fibres and tencel fibres were blended each with the cotton fibres in 50:50 ratio at drawing stage. The yarns parameters are given in Table 1.
-
ii.
Preparation of greige fabric samples
The plain-woven fabrics were prepared on rapier loom with a warp beam containing cotton/polyester 60:40 (2/40 s count) for all samples. For making fabric samples, three types of yarns: 100% cotton yarn, 50–50% cotton-modal blended yarn and 50–50% cotton-tencel blended yarns were used in weft only. The ends per/inch and picks/per inch were kept about 61.5 and 43.5 respectively.
-
iii.
Preparation of scoured fabric samples
The scouring is done to remove the natural as well as added impurities and make fabric more absorbent. To make scoured samples, all three greige fabric samples were processed in kier for 2 h at boiling temperature using following scouring recipe:
Material to liquor ratio: 1:10.
Caustic soda (alkali): 2% (on the weight of material).
Soda ash: 2%
Detergent: 0.3%
Wetting Agent: 0.1%
Sodium silicate: 0.5%
Sodium sulphite: 0.5%
-
iv.
Preparation of dyed fabric samples
Dyed samples were made by dyeing the scoured samples with reactive dye. The dye is able to react chemically with the substrate to form a covalent dye substrate linkage. The reactive dyes have a reactive group and this group makes covalent bond with fibre polymer and act as an integral part of fibre [5].
2.2 Methods
The fabric samples were tested for its physical factors (EPI, PPI, Cover Factor, GSM and Thickness), air permeability, moisture management properties, strength and stiffness test.
-
i.
Physical factors
Fabric cover factor was calculated using the following formula:
where, CFwrp = Warp cover factor = n/√N (n = ends per inch and N = thread count).
The fabric weight per square meter (GSM) was measured according to ASTM D 3776–02 standards [6].
Fabric thickness was determined at 100 g/cm2 pressure with the help of a precision thickness tester with accuracy 0.01 mm and pressure foot dia 10 mm.
-
ii.
Air permeability test
Air permeability was measured at 185 Pa pressure by using the Digital Air Permeability Tester (YG461E Type) and expressed in mm/s [7] for all samples. The nozzle diameter and test area were 6 mm and 20 cm2 respectively.
-
iii.
Moisture management test
The SDL ATLAS Moisture Management Tester (MMT) was used to measure the liquid moisture management capabilities of the samples [8]. The instrument measures, evaluates and classifies liquid management properties of fabrics. It can measure overall moisture management capacity along with five other properties.
-
iv.
Fabric breaking strength
The breaking strength and elongation of textile fabrics may be determined using the strip method test using the Aimil Universal Testing Machine [9].
-
v.
Fabric stiffness test
Fabric stiffness is a property of fabric to keep standing without any support. It is an important factor in the study of handle and drape of fabric. The fabric stiffness was measured by Shirley Stiffness Tester [10] work on cantilever principle as per B.S. 3356:1990 test [11]. A 25 mm wide and 200 mm long rectangular strip of fabric was mounted on a horizontal platform in such a way that it hangs like a cantilever and bends downwards. The length of the fabric required to bend to a fixed angle is measured. This is known as bending length.
The stiffness of a fabric in bending is very dependent on its thickness, the thicker the fabric, the stiffer it is if all factors remain same [10]. The bending modulus is independent of the dimension of the strip tested.
where,
- G:
-
Flexural rigidity = M X C3 X 9.807 X10−6 µNm,
- C:
-
Bending length (mm) and dependent on weight of the fabric.
- M:
-
fabric mass per unit area (GSM).
- T:
-
Thickness (mm).
3 Result and Discussion
Fabric physical factors (EPI, PPI, Cover factor, GSM and fabric thickness), comfort properties (air permeability and moisture management properties) and mechanical properties (tensile strength, stiffness) are evaluated and results are tabulated in Table 2.
3.1 Fabric Physical Properties
-
i.
Cover factor
The results of cover factor are tabulated in Table 2 and the impact of wet processing is shown in Fig. 2. Result shows that after scouring, the cover factor increases in all fabrics samples due to fabric shrinkage and further increases slightly in cotton/modal (C/M) and cotton/tencel (C/T) samples after dyeing while in cotton (C) samples, it decreases slightly. There is a very slight difference in cover factor of all the samples.
-
ii.
Fabric weight (GSM)
Fabric weight has been analysed and results are tabulated in Table 2 and the impact of wet processing is shown in Fig. 3.
Figure 3 shows that the fabric weight (GSM) of all the three types of fabrics has increased significantly after scouring and further increases in dyeing perhaps due to shrinkage of samples in each step of wet processing.
From the graphical result, it is found that in greige stage, all fabric having nearer same GSM value. After wet processing steps, i.e. in scouring and dyeing, the cotton/tencel blend has highest GSM value followed by cotton/modal blend fabrics and 100% cotton fabric.
-
iii.
Fabric thickness
Thickness of a fabric plays important role in its comfort properties as well as handling and drape properties. The data of thickness is tabulated in Table 2 and the impact of wet processing is shown in Fig. 4.
After scoring the fabric thickness increases in all fabric samples significantly and further increases after dyeing. This may be due to shrinkage in process of wet processing. There is a very slight difference in between the different fabric sample in each stage.
3.2 Comfort Related Properties
-
i.
Air permeability
The results of air permeability of the samples are tabulated in Table 2 and the effects of wet processing on various materials were shown in Fig. 5.
The air permeability decreases after scouring in all samples but there is no any significant changes in after dyeing. This may be perhaps due to mostly all shrinkage takes place at scouring and very little alteration in shrinkage after dyeing. After scouring, the resultant effect of shrinkage and fibre swelling take place and the yarns come closer resulting in decreasing of the gaps to let the air pass and this result in decrease of air permeability after scouring.
In greige stage, the air permeability of cotton-modal blend was the highest followed by cotton-tencel blend and 100% cotton weft yarn fabric samples. After scoring, air permeability of cotton/tencel is highest followed by cotton/modal and 100% cotton fabric. After dyeing, the cotton/modal blended fabric shows highest air permeability followed by tencel/cotton blended fabric and 100% cotton fabric.
The air permeability of the fabrics depends on structure of the fabric, i.e. size of the pores, fabric thickness and tortuosity of the pores. Most of the air passes through the pores between the yarns but when the fabric is denser, the air also passes through the micro-voids inside the yarns (i.e. the pores between the fibres). There is good correlation (Table 3) between air permeability and fabric cover factor (R = −0.86) and GSM (R = −0.72) and fabric thickness (R = −0.66).
-
ii.
Moisture management capacity
The overall moisture management capacity (OMMC) as measured by the Moisture Management Tester are furnished in Table 2 and the effect of wet processing illustrated in Fig. 6.
The overall moisture management capacity (OMMC) is based on three factors, the moisture absorption rate at the bottom of the fabric (ARB), the spreading speed at the bottom (SSB) and accumulative one-way transfer rate of liquid moisture from top to the bottom of the fabric. Higher value of OMMC is associated with higher capillary action.
The overall moisture management capacity increases significantly in all samples after scouring and further increases after dyeing. This may be due to removal of cotton wax/spin finish from the cuticle/outer surface of the fibres resulting in improved water transport from the fibrous material. In the greige stage, cotton/tencel blended fabric has the highest value of OMMC followed by cotton/modal blended fabric and 100% cotton fabric. After scouring and dyeing, 100% cotton fabric has highest value of OMMC followed by cotton/tencel and cotton/modal fabric.
There is fair correlation has been found (Table 3) in between OMMC and fabric cover factor (R = -0.72) and GSM (R = 0.65) and fabric thickness (R = 0.61).
3.3 Fabric’s Mechanical Properties
-
i.
Breaking strength
Fabric breaking strength was tested using ravelled strip method test in weft direction and the results are tabulated in Table 2 and Fig. 7.
Figure 7 shows that the fabric strength increases after scouring and decreases after dying in all samples (100% cotton fabric, cotton/modal blended fabric and cotton/tencel blended fabric. In both greige stage and scoured stage, the breaking strength of cotton/tencel blended fabric is highest followed by 100% cotton fabric and cotton/modal blended fabric. More strength of tencel is attributed to crystalline arrangement of its cellulose units which are extremely greatly oriented in the longitudinal axis of the fibre [12]. After dyeing, the breaking strength of 100% cotton fabric is highest followed by cotton/tencel blended fabric and cotton/modal blended fabric. Fabric strength is not good correlated with cover factor, GSM and fabric thickness.
-
ii.
Stiffness
Stiffness of fabric was measured in terms of bending modulus. It has impact on fabric handle. As the bending modulus increases, the fabric will be stiffer. More stiff fabric will have less drape thus will not fall freely in a garment. The results are tabulated in Table 2 and the effect of wet processing in weft direction is shown in Fig. 8.
Figure 8 shows the bending modulus of fabrics in various stages, i.e. greige stag, scoured stage and dyed stage predicting the stiffness of samples. The fabric bending modulus decreases after scouring and there is no any significant change has been found after dyeing in mostly all samples.
There is no significant difference that has been found in cotton fabric and cotton/modal blended fabric samples but the cotton/tencel blended fabric has lesser bending modulus in all three stages, i.e. in greige stage, scoured stage and dyed samples.
There is very good correlation (Table 3) of bending modulus with cover factor (R = −0.95), with GSM (R = −0.91) and with thickness (R = −0.75).
4 Conclusions
Results are concluded as under:
-
1.
The air permeability decreases significantly after scouring but after dyeing the air permeability alter slightly and this difference is not significant. Air permeability was highest in cotton/modal blend followed by cotton/tencel blend and 100% cotton plain woven fabric in greige stages. After scouring the cotton/tencel blended fabric having the highest value followed by cotton/modal blend and 100% cotton. After dyeing the cotton/modal blend has highest air permeability values followed by cotton/tencel and 100% cotton fabric. In all cases the air permeability of cotton/tencel blend and cotton/modal blend was higher than 100% cotton fabric. There is good correlation between air permeability and fabric cover factor (R = −0.86) and GSM (R = −0.72) and fabric thickness (R = −0.66).
-
2.
After scouring, the OMMC value increases sharply and further increases slightly after dyeing. In greige fabrics, cotton/tencel blend has the highest value of OMMC followed by cotton/modal and 100% cotton fabric. After scouring and dyeing the 100% cotton fabric has highest OMMC followed by cotton/tencel and cotton/modal blend fabric. There is fair correlation has been found in between OMMC and fabric cover factor (R = −0.72) and GSM (R = 0.65) and fabric thickness (R = 0.61).
-
3.
In all fabric samples, the fabric breaking strength increases after scouring and decreases after dyeing. In greige stage and scoured stage, the breaking strength of cotton/tencel blended fabric followed by 100% cotton fabric and cotton/modal blended fabric. After dyeing the 100% cotton fabric shows highest strength followed by cotton/tencel blended fabric and cotton/modal blend fabric. Fabric strength is not good correlated with cover factor, GSM and fabric thickness.
-
4.
In all samples, fabric bending modulus decreases abruptly after scouring and no further change after dyeing significantly. There is no significant difference has been found in cotton fabric and cotton/modal blended fabric samples but the cotton/tencel blended fabric has lesser bending modulus in all three stages, i.e. in greige stage, scoured stage and dyed samples. There is very good correlation of bending modulus with cover factor (R = −0.95), with GSM (R = −0.91) and with thickness (R = −0.75).
References
Mukhopadhyay A, Ishtiaque A, Uttam D (2011) Impact of structural variations in hollow yarn on heat and moisture transport properties of fabrics. J. Text. Inst. 102(8):700–712
Mather RR, Wardman RH (2011) Regenerated Fibres, The Chemistry of Textile Fibres. RSC Publications, Cambridge, U.K., pp 100–127
Udomkichdecha W, Chiarakorn S, Potiaraj P (2002) Relationship between fibrillation behaviour of Lyocell fibres and their physical properties. Text. Res. J. 72(11):939–943
Basit A, Latif W, Baig SA, Afzal A (2018) The mechanical and comfort properties of sustainable blended fabrics of Bamboo and with cotton and regenerated fibres. Cloth. And Text. Res. J. 36(4):267–280
Dyeing of cotton fabrics with reactive dyes. https://textilelearner.blogspot.com/2012/01/dyeing-of-cotton-fabric-with-reactive.html. Assessed 28 Sep 2019
ASTM D3776–96 (Reapproved 2002). Standard Test Method for Mass per unit area (weight) for Fabric, ASTM International, 100 Barr Harbor Drive, PO. Box C700, West Conshohochen, PA19428–2959, United States
YG461E/II type, digital air permeability tester. User’s Manual, Wuhan Guoliang instrument Co. Ltd., Wuhan, China
SDL Atas Moisture Management Tester. https://sdlatalas.com Assessed 25 Aug 2019
Aimil Universal Testing Machine (Computerised). https://aimil.com Assessed 25 Aug 2019
Saville, B.P.: Objective Evaluation of Fabric Handle. Physical Testing of Textiles. pp. 256–259
BS3356:1990. Method for Determining of Bending Length and Flexural Rigidity of Fabrics. British Standard Institute, UK
Xu Y, Lu Z, Tang R (2007) Structure and thermal properties of bamboo viscose, tencel and conventional viscose fibre. J. Ther. Ana. Cal. 89(1):197–201
Author information
Authors and Affiliations
Corresponding author
Editor information
Editors and Affiliations
Rights and permissions
Copyright information
© 2021 The Editor(s) (if applicable) and The Author(s), under exclusive license to Springer Nature Singapore Pte Ltd.
About this paper
Cite this paper
Uttam, D., Ahlawat, G. (2021). The Effect of Wet Processing on the Comfort and Mechanical Properties of Fabrics Made from Cotton Fibres and Its Blends with Modal and Tencel Fibres in Weft. In: Midha, V., Mukhopadhyay, A. (eds) Recent Trends in Traditional and Technical Textiles. Springer, Singapore. https://doi.org/10.1007/978-981-15-9995-8_11
Download citation
DOI: https://doi.org/10.1007/978-981-15-9995-8_11
Published:
Publisher Name: Springer, Singapore
Print ISBN: 978-981-15-9994-1
Online ISBN: 978-981-15-9995-8
eBook Packages: Chemistry and Materials ScienceChemistry and Material Science (R0)