Abstract
Since its first introduction in the 1950s, Ti6Al4V became the most sympathetic titanium alloy due to its attractive mechanical and physicochemical properties and is currently extensively used, for e.g., in machining, automotive, aerospace, as well as biomedical industry. However, its poor tribological properties limit its use in machining, automotive, aerospace, and orthopedic applications. Hence, a variety of attempts have been made in order to improve tribological performance of titanium alloys, especially focusing on surface modification. This paper represents an overview of significance of surface modification applied on Ti6Al4V alloy. Several solutions have been followed to improve the machinability of these alloys: development of new machining techniques, tool geometries, and protection of tools’ surface with coatings to yield high productivity, good surface finish of the work-piece, and extended tool life. In this work, Ni coating on Ti-based alloys is tested to evaluate their potential for machining as well as for biomedical applications. The tribological behavior is evaluated at room temperature in wet lubricated conditions on pin-on-disk equipment, by testing Ni-coated pins of 10 mm diameter and 30 mm long against EN-31 flat plate. Friction coefficient of coated pins in wet condition is observed to be less, as compared to the tests performed with uncoated pins. Coated sample tested in lubricated condition showed much more reduction in wear and friction coefficient than their performance under uncoated condition. From experimental investigation, it is observed that the Ti alloys with Ni coating show improved wear rate and friction coefficient as compared to without coating.
Similar content being viewed by others
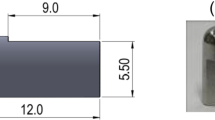
Explore related subjects
Discover the latest articles, news and stories from top researchers in related subjects.Avoid common mistakes on your manuscript.
1 Introduction
Modern engineering materials such as metallic alloys, ceramics, composites, and plastics are often subjected to harsh working conditions during their operation, what results in wear, corrosion development, and fatigue. Active work on removing or minimizing materials failures is nowadays necessary due to existing raw materials and energy shortage. Among all engineering materials, titanium and its alloys are considered attractive materials in numerous branches of industry, due to their excellent properties such as high strength-to-weight ratio, low elastic modulus, anti-magnetic properties, high biocompatibility, and acceptable corrosion resistance [1]. Hence, since its first introduction in the early 1950s [2, 3], Ti6Al4V has become the most favorable titanium alloy. Ti6Al4V alloy covers about 50% of total titanium world production [2] and today is extensively used in automotive, aerospace, chemical, marine, and biomedical industries.
Ti–6Al–4V is a titanium alloy grade 5 with good mechanical properties, excellent corrosion resistance, and having low density [4]. However, the grade 5 titanium alloys have poor tribological properties since it has poor wear resistance, lower hardness, and high coefficient of friction [5]. Therefore, the improvement of these properties is required to increase the performance of the engineering components and to extend their life service without any un-anticipated failure. One of the methods to meet this requirement is to perform the hard surface coating onto this alloy using ceramic particles on the surface melted with TIG torch technique. This section presents a literature review of titanium alloy and its potential applications in engineering components, surface modification techniques, titanium aluminum nitride (TiAlN) coating, aluminum chromium nitride (AlCrN) coating, chromium interlayer for an improved bonding strength, and molybdenum disulphide (MoS2) coating. This section also reviews the tribological testing methods such as scratch test, pin-on-disk test, and reciprocating tribometer test.
Boyer et al. [5] reported the applications of titanium and its alloys in aerospace industry. It has high strength-to-weight ratio, excellent corrosion resistance, and compatibility with composite structure but its usage is strongly limited by its higher cost compared to aluminum alloys and steels. About 80–90% used in aircraft structure is Grade-5 alloy (Ti6Al4V). It is used in all sections of the aircraft such as aircraft fuselage, nacelles, landing gear, wing, fin deck, and empennage. Buytoz [6] investigated experimentally the effects of tungsten inert gas arc-processing (TIG) parameters on the microstructure and microhardness of SiC (silicon carbide) coatings developed with TIG processing on an SAE 1020 steel substrate. Wang [7] reviewed the applications of titanium alloy in total joint replacement arthroplasty. Titanium alloys were used as a bio-material due to their superior biocompatibility, enhanced corrosion resistance, and lower elastic modulus as compared to cobalt-based alloys and stainless steels. The biomedical use of titanium alloys has been limited due to their poor wear resistance and shear strength. The improved biocompatibility and reduced modulus of elasticity in biomedical alloys were achieved based on solution treatment. The wear resistance of β-Ti alloys shows some improvement when compared to α + β alloys. Dong et al. [8] reported that untreated Ti6Al4V is not suitable under sliding conditions even with lubrication because of its severe adhesive wear tendency. The authors also studied the wear resistance of untreated and thermal oxidation-treated Ti6Al4V surfaces by rolling–sliding motion. Thermal oxidation treatment enhances the wear resistance of the titanium alloy by reducing the adhesive wear. Thermally treated titanium alloy surfaces improve the wear life by two orders of magnitude than the untreated alloy. Long and Rack [9] investigated the friction and surface behavior of solution-treated, single-phase, metastable-β titanium alloys and two-phase Ti–6Al–4V during reciprocating sliding motion against hardened steel counter body. The lower shear resistance and increased material transfer occurred with increasing number of cycles on the single-phase alloys relative to the α + β alloy. The surface deformation of metastable β alloy pins higher than the Ti–6Al–4V pins, plowing being representative of surface damage for the two-phase α + β alloy. The surface damage and titanium transfer increased with increasing contact stress and always being greater for the metastable-β alloys than for the two-phase Ti–6Al–4V. The surface roughness of the worn surfaces was approximately two orders of magnitude greater than the initial polished surfaces. The roughness of the metastable-β alloy surfaces was higher than the Ti–6Al–4V. Choubey et al. [10] studied the friction and wear performance of biomaterials under fretting contact conditions against 8-mm-diameter bearing steel counter body. The important bio-metallic alloys, CP Titanium, Ti–5Al–2.5Fe, Ti–13Nb–13Zr, Ti–6Al–4V, Ti–13Nb–13Zr, and Co–28Cr–6Mo were selected for the fretting wear test at 80 μm stroke, 10 Hz frequency, and 10 N normal load. Hank’s balanced salt solution was used to evaluate the performance of the materials in simulated body fluid (physiological) solution. The lowest coefficient of friction of 0.3 was observed for Ti–5Al–2.5Fe/steel couple, while for other Ti-based alloys, coefficient of friction was in the range of 0.46–0.50. The smooth surface along with the non-existence of cracking and deep abrasive grooves on the owned surface of Ti–5Al–2.5Fe is responsible for the low coefficient of friction. For CP titanium, Ti–13Nb–13Zr, and Ti–6Al–4V, material removal occurs through the formation of non-protective tribochemical oxide layer. The cracking and spalling of the tribolayer leads to severe wear of these materials. The major wear mechanism of the titanium alloys was found to be tribomechanical abrasion, transfer layer formation, and cracking. Qu et al. [11] studied the friction and wear of titanium alloys using pin-on-disk tester against polymer, metal, and ceramic counterfaces. Two different titanium alloy (Ti–6Al–4V and Ti–6Al–2Sn–4Zr–2Mo) disks were slid against fixed bearing balls of diameter 9.53 mm composed of 440C stainless steel, silicon nitride, alumina, and polytetrafluoroethylene (PTFE) at two speeds: 0.3 and 1.0 m/s. The similar friction and wear performance was achieved on both Ti alloys, even though their grain structures and compositions are different. At higher sliding speed, the coefficient of friction and wear rate were lower. The higher wear rate tendency was observed on ceramics than steel and this trend is contrary in relation to their hardness but proportional relation with their corresponding fracture toughness. The tendency of Ti alloys to transfer material to their counterfaces and suggested possible tribochemical reactions between the ceramic balls and Ti alloy disks. These reaction products, which stick to the ceramic sliders, may degrade the mechanical properties of the contact areas and result in high wear. Cui et al. [12] investigated the wear behavior of Ti6Al4V under reciprocating sliding with different normal load conditions. Dry and lubricated surface conditions produced “W” (scar with multiple valleys) and “U” (scar with single valley)-shaped scars on both specimen and pad, respectively. The wear volume was linearly proportional to cumulative product of contact load and relative slip as well as to the total dissipated energy. These correlations suggest that linear relationships exist to characterize the fretting wear of a material which is independent of the contact load, relative slip, contact geometry, lubrication, and applied cyclic load on the substrate (specimen). The microscopy image of wear scars showed that the wear was caused by both adhesion and abrasion processes.
Takadoum et al. [13] studied the effect of substrate surface roughness and coating thickness on the adhesion and tribological behavior of TiN deposited by reactive ion plating on steel substrates. The coating on the smooth surface showed superior bonding strength than that of the coating on the rough surface. Increase in coating thickness and surface roughness increases the wear rate. Wilson et al. [14] investigated the tribological performance of Ti6Al4V by low-frequency reciprocating wear tester before and after various surface treatments such as plasma-assisted PVD-coated Titanium Nitride, plasma nitriding, and ion implantation by nitrogen. PAPVD-coated Titanium Nitride coating increased the surface micro-hardness and therefore the sliding wear resistance has been superior as compared to the nitrogen ion implantation and plasma nitriding surface treatments. However, Sampath Kumar et al. [15] studied metallurgical characterization of TiAlN/AlCrN multilayer coating on a tungsten carbide substrate. The composite coatings were deposited using plasma-enhanced physical vapor deposition (PEPVD) process. The microstructure of the coating was examined and it was found that the TiAlN/AlCrN coating was uniform, highly dense, and less porous. TiAlN/AlCrN exhibited higher hardness, higher young modulus, and superior scratch resistance when compared with conventional coatings, such as TiAlN, AlCrN, and TiN. The interlayer bonding strength of the coating is better for the TiAlN/AlCrN bilayer coating, due to its high adhesive strength, and because delamination occurs at a slower rate.
From literature review for “tribological behavior of uncoated and coated titanium alloys” it is observed that the attractive properties such as lower modulus, superior biocompatibility, and better corrosion resistance possessed by Ti–6Al–4V (α + β alloy) led to its higher usage in structural and automobile field. Among the α + β alloys, Ti–6Al–4V is by far the most popular titanium alloy. More than 50% of all the alloys in use today are of this composition. About 80–90% used in aircraft structure is Grade-5 alloy (Ti–6Al–4V). Titanium and its alloys are poor in wear resistance and it is not suitable for, e.g., in machining, automotive, aerospace as well as biomedical industry, bearing surface applications without a coating or surface treatment [16, 17]. Untreated Ti–6Al–4V is not suitable under sliding conditions even with lubrication because of its severe adhesive wear tendency [18]. Hence, in this paper, the contact phenomenon in between tool and workwise used for machining operation in various machines tool is tried to simulate with Ni layer coating to estimate the coefficient of friction (COF), frictional force (FF), and wear rate of titanium alloy grade 5 (Ti–6Al–4V).
2 Experimental Methodology
2.1 Test Method
Standard test method is carried out on a pin-on-disk apparatus for wear testing. The wear rate in various systems will rely on the conditions such as the applied load, speed, the environment, sliding distance, and the material characteristics with coating and without coating. Because the pin-on-disk test method will not attempt to duplicate all the conditions that may be experienced in service for example lubrication, load, pressure, contact geometry, removal of wear debris, and presence of corrosive environment.
2.2 Disk
The minimum speed of disk is 200 rpm and maximum speed is 2000 rpm. The material used for disk is EN-31 hardened to 60 HRC and 1.6 Ra (surface roughness). The diameter of disk is about 30 mm to 100 mm. The thickness is in between 2 and 10 mm. The diameter of wear track can be varied in between 50 and 160 mm.
2.3 Sample Preparation
The cylindrical pins were made from mild annealed titanium alloy (Ti6Al4V, grade 5), consisting of (in wt%) 4.23V, 6.36Al, 0.126Fe, 0.002C, and 88.94 Ti. As received, cylindrical pins were machined to a uniform diameter as per the cutting tools requirement of suitable machine tools. The cylindrical pins were machined with diameter 10 mm and 30 mm length. The pin is clamped in a jaw. The cutting tools Ti6Al4V to be tested should fulfill the norms of G 99 [19]. These norms are like dimensions, surface finish, material type, composition, and processing treatments.
2.4 Load
Various trials are performed on titanium alloys with minimum track diameter of 50 mm for durations of 5, 7.5, and 10 min for load of 5 kg, 6 kg, 7 kg, 8 kg, 9 kg, and 10 kg with disk speeds of 400 rpm, 500 rpm, 600 rpm, 700 rpm, 800 rpm, and 900 rpm. The different load and the speed are selected as per the cutting tools requirements (Fig. 1). At different loads and speed variation of wear, frictional force and COF with duration of rubbing are compared and investigated.
2.5 Coating Deposition and Characterization
The cylindrical pin substrates were cleaned in ultrasonic bath using acetone prior to nickel deposition. A thin layer of 40–42 µm with Ni interlayer was incorporated using X-ray fluorescence test method. The coating was carried out as per ASTM B764. Measurement was performed by exposing the parts to X-ray radiation. A collimator was used to focus the X-ray onto exactly defined area of the test specimen. Adhesion test was carried out as per ASTM B 571. No peeling was observed. During adhesion test, the specimens were heated at 250 °C for 1 h and quenched in water at room temperature.
2.6 Experimental Setup
Figure 1 shows the experimental setup of pin-on-disk apparatus. The main component of pin-on-disk apparatus is pin and rotating disk. The pin-on-disk is equipped with load cell and LVDT to measure the frictional force and vertical displacement of pin. The disk is rotated by motor at different speeds in such a way that vibration does not affect the test. The specimen holder is attached to the lever arm which has pivot. The pin specimens to be tested are of cylindrical shape. The material for the disk is EN-31 and the pin is fed against the rotating disk by applying dead-weight-load on pin due to which the wear of pin takes place. Machine is equipped with a controller, data acquisition system, and WINDUCOM 2010 software to obtain the required results. Tribological characteristics are determined on pin-on-disk apparatus for different gear materials and loading conditions. The friction force induced in between pin and disk, and this friction force is sensed by load cell.
The minimum speed of disk is 200 rpm and maximum speed is 1800 rpm. The material used for disk is EN-31 hardened to 60 HRC and 1.6 Ra (surface roughness). The diameter of disk is about 30 mm to 100 mm. The thickness is in between 2 and 10 mm. The diameter of wear track is varied between 50 and 100 mm. Various tests are conducted in a load ranging from 5 to 10 kg. At various loads and sliding velocities, tribological behavior of Ti6Al4V is studied and investigated.
The pin which is to be tested is clamped in a pin holder and is brought in contact with disk as shown in Fig. 2. The wear track of 50 mm is fixed as per application. The speed of disk is varied from 400 to 900 rpm. The time durations for each trial were fixed as 5 min, 7.5 min, and 10 min. The readings were directly displayed in a digital display. The load applied on the pin is varied as 5 kg, 6 kg, 7 kg, 8 kg, 9 kg, and 10 kg, respectively. All the specimens of 10 mm diameter and 30 mm long are tested on pin-on-disk machine to know the study effect of vanadium and aluminum content on tribological behavior on cutting tool alloys.
3 Results and Discussion
The aim of the experiment was to study the effect of Ni coating on Ti6Al4V substrate to study the friction and wear behavior of these tool alloys. The experiments are carried out for Titanium alloys at varying load conditions of 5 kg to 10 kg at different sliding speeds varying from 400 to 900 rpm. The tests are conducted on pin-on-disk machine with lubrication for time duration of 5, 7.5, and 10 min. The Lubricant used is the regular coolant used for metal cutting process which is more suitable for turning process. During working, a combination of 50:50 (means 50% cutting fluid and 50% water) was used. The results obtained are summarized in Tables 1 and 2.
3.1 Variation of Wear
Tables 1 and 2 show the measured values of wear rate, frictional force, and coefficient for time period of 5 min with different loads and speeds on Pin-on-Disk apparatus. Figure 3 shows the variation in the wear for Ti6Al4V under the loads varying from 50 to 100 N for wet test condition. From Fig. 3, it is observed that there is continuous increase in wear with some fluctuations as load increases from 50 to 90 N and then wear remains almost constant after 90 N for 5-min test duration without coating (red line) condition [20, 21]. With Ni coating (blue line), it is observed that wear deceases substantially from 115.27 microns to 103.55 microns for load 50 N at speed of 400 rpm for test of 5 min duration. Similar trend is observed when load varies 60 N to 100 N with varying speed from 500 to 900 rpm. From this it is concluded that samples with Ni coating result in improved wear resistance as compared to without coated. Similar trend is observed for test of 7.5 min and 10 min. Figures 4 and 5 present that Ni-coated sample results in better wear resistance as compared to without coated (red line) samples.
3.2 Variation of Friction Force
From Fig. 6 it is observed that there is decrease in FF with respect to load and speed, which continues for Ni-coating samples till 90 N at 900 rpm for 5-min test. Again as load increases from 90 to 100 N, there occurs a drastic increase in wear as well as friction force, but both parameters show improvement when compared to uncoated samples for 5-min test. From Figs. 7 and 8 similar trend is observed in wear and FF pattern during 7.5-min and 10-min test. Wear rate remains almost constant after 10 min [20, 21]. After careful observation of Fig. 7, it is observed that there is significant decrease in FF for Ni-coated samples for 7.5-min test.
3.3 Variation of Coefficient of Friction
Figures 9, 10, and 11 show the variation of COF with load for 5-, 7.5-, and 10-min test without and with Ni coating. During 5-min test, it is observed that COF decreases drastically due to application of Ni coating (blue line) as load varies from 50 to 100 N and speed 400–900 rpm. During 7.5- and 10-min test it is seen that due to Ni coating there is improvement in COF especially as load varies from 70 to 90 N.
4 Conclusions
The objective of this work is to simulate the contact phenomenon in between tool and workwise used for machining operation in various machine tools with and without coating to estimate the wear rate, friction force (FF), and coefficient of friction (COF) of titanium alloy grade 5 (Ti–6Al–4V). The tests are performed on a titanium alloy for durations of 5, 7.5, and 10 min for load varying from 50 to 100 N with disk speeds varying from 400 to 900 rpm.
Friction coefficient of coated pins in wet condition is observed to be less, as compared to the tests performed with uncoated pins. Coated sample tested in lubricated condition showed much more reduction in wear and friction coefficient than their performance under uncoated condition. From test results, it is observed that as load increases from 50 to 100 N wear as well COF decreases for coated samples with insignificant impact of variation of disk speeds. From experimental investigation, it is observed that the Ti alloys with Ni coating show improved wear rate, friction force, and friction coefficient as compared to without coating.
Change history
07 August 2023
A Correction to this paper has been published: https://doi.org/10.1007/s40735-023-00788-z
References
Lepicka M, Gradzka-Dahlke M (2016) Surface modification of Ti6Al4V titanium alloy for biomedical applications and its effect on tribological performance: a review. Rev Adv Mater Sci 46:86–103
Atar E, Kayali ES, Cimenoglu H (2008) Characteristics and wear performance of borided Ti6Al4V alloy. Surf Coat Technol 202(19):4583–4590
Zhecheva A, Sha W, Malinov S, Long A (2005) Enhancing the microstructure and properties of titanium alloys through nitriding and other surface engineering methods. Surf Coat Technol 200(7):2192–2207
Dewidar M (2006) Improvement of hardness and wear resistance of Ti-6Al-4V alloy by thermal oxidation for biomedical application. J Eng Sci 34(6):1941–1951
Boyer R, Welsch G, Collings EW (1994) Materials properties handbook: titanium alloys, ASM International, pp 1–1169. ISBN: 978-0-87170-481-8
Buytoz S (2006) Microstructural properties of SiC based hard facing on low alloy steel. Surf Coat Technol 200(12-13):3734–3742
Wang K (1996) The use of titanium for medical applications in the USA. Mater Sci Eng A 213(1–2):134–137
Dong H, Groll EA, Bell T (1999) Potential of improving tribological performance of UHMWPE by engineering the Ti6Al4V. Counterfaces 225–229(Part 2):874–884
Long M, Rack HJ (2001) Friction and surface behavior of selected titanium alloys during reciprocating-sliding motion. Wear 249(1–2):157–167
Choubey A, Basu B, Balasubramania R (2005) Tribological behaviour of Ti-based alloys in simulated bodyfluid solution at fretting contacts. Trends Biomater Artif Organs 18(2):141–147
Qu J, Blau PJ, Watkins T, Kulkrani NS (2005) Friction and wear of titanium alloys sliding against metal, polymer, and ceramic counterfaces. Wear 258(9):1348–1356
Cui XH, Mao YS, Wei MX, Wang SQ (2012) Wear characteristics of Ti-6Al-4V alloy at 20–400°C. Tribol Trans 55(2):185–190
Takadoum J, Pivin JC, Chaumont J, Roque-Carmes C (1985) Friction and wear of amorphous Ni-B, Ni-P films obtained by ion implantation into nickel. J Mater Sci 20(4):1480–1493
Wilson AD, Leyland A, Matthews A (1999) A comparative study of the influence of plasma treatments, PVD coatings and ion implantation on the tribological performance of Ti–6Al–4V. Surf Coat Technol 114(1):70–80
Sampath Kumar T, Balasivanandha Prabu S, Manivasagam G, Padmanabhan KA (2014) Comparison of TiAlN, AlCrN, and AlCrN/TiAlN coatings for cutting-tool applications. Int J Miner Metall Mater 21(8):796–805
Kumar D, Deepak KB, Muzakkir SM, Wani MF, Lijesh KP (2018) Enhancing tribological performance of Ti-6Al-4V by sliding process. Tribology. https://doi.org/10.1080/17515831.2018.1482676
Din SH, Shah MA, Sheikh NA (2018) (2018) Tribological performance of titanium alloy Ti–6Al–4V via CVD-diamond coatings. J Superhard Mater 40(1):26–39
Long M, Rack HJ (1998) Titanium alloys in total joint replacement: a materials science perspective. Biomaterials 19(18):1621–1639
ASTM standards test method for wear testing with a pin-on-disk apparatus, designation G99–95a (Reapproved 2000)
Santhosha Rathnam G, Rathnam Ch (2020) Experimental investigations on tribological characteristics of Ti-6Al-4V under wet conditions. J Bio Tribo Corros 6(1):1–7. https://doi.org/10.1007/s40735-019-0314-9
Gawande SH, Patil AA (2020) Experimental study on tribological characteristics of steel alloys for CNC bending machine. J Bio Tribo Corros 4(4):1–13. https://doi.org/10.1007/s40735-018-0191-7
Funding
This work is not supported fully or partially by any funding organization or agency.
Author information
Authors and Affiliations
Corresponding author
Ethics declarations
Conflict of interest
The authors declare that there is no conflict of interests regarding the publication of this paper.
Additional information
Publisher's Note
Springer Nature remains neutral with regard to jurisdictional claims in published maps and institutional affiliations.
The original online version of this article was corrected: The spelling of Ch. Ratnam's name was corrected.
Rights and permissions
Springer Nature or its licensor (e.g. a society or other partner) holds exclusive rights to this article under a publishing agreement with the author(s) or other rightsholder(s); author self-archiving of the accepted manuscript version of this article is solely governed by the terms of such publishing agreement and applicable law.
About this article
Cite this article
Santhosha Rathnam, G., Ratnam, C. Performance Assessment of Ni-Coated Titanium Alloys Under Wet Conditions. J Bio Tribo Corros 6, 42 (2020). https://doi.org/10.1007/s40735-020-00343-0
Received:
Revised:
Accepted:
Published:
DOI: https://doi.org/10.1007/s40735-020-00343-0