Abstract
Vegetable oils are well known for their potential applications in green chemistry, including use as hydraulic fluids. Among oilseed crops, Crambe abyssinica Hochst. EX R.E.Fr. gained attention for its low-input requirements during cultivation and for the properties of its oil, characterised by a high erucic acid content. This long-chain mono-unsaturated fatty acid provides appreciable features that make the oil suitable for interesting green chemistry sectors, as biolubricants and cosmetics. In the present work, Crambe oil was tested as a hydraulic fluid for sustainable agricultural applications. Crambe oil was partially refined through phospholipid removal and added with a food-grade antioxidant (tert-butylhydroquinone) at two different concentrations. The fluid efficiency tests were carried out using an experimental test rig, able to simulate a real hydraulic device, performing heavy work cycles at 40-MPa pressure and at 100 °C temperature, with the aim of strongly accelerating the ageing of the tested fluid. At a lower antioxidant concentration, 0.25 g kg−1, the oil underwent a very quick degradation process. However, increasing the additive dose to 2.0 g kg−1, the fluid maintained stable performances. Indeed, all parameters, referred to oil chemical-physical stability and technical performance, were constant along the entire work cycle, up to 290 h. Finally, the present work showed how Crambe seed cultivation, oil extraction and exploitation in the hydraulic circuit of farm machinery could be developed applying green chemistry approaches aiming at small-scale biorefineries linked to the local supply.

Graphical abstract
Similar content being viewed by others
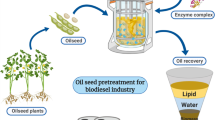
Explore related subjects
Discover the latest articles, news and stories from top researchers in related subjects.Avoid common mistakes on your manuscript.
1 Introduction
The hydraulic mineral-based lubricants, used across all industrial sectors, are characterised by excellent tribological properties and should have the following missions: power transmission to all the moving parts (pumps, valves and actuators) with minimum losses, lubrication of surfaces moving against each other and protection of metal surfaces from corrosion and high temperatures. Hydraulic fluids can also be classified as “high risk loss” lubricants in the environment as a consequence of a wide application of large volumes in self-propelled machines and farm equipment that are often susceptible to spilling phenomena. In view of their high toxicity and low biodegradability, mineral-based lubricants constitute a considerable threat to the environment. Green lubricants, representing a sustainable alternative to the petroleum-based products, should be evaluated in relation to (i) energy conservation (and efficiency); (ii) development of durable products able to minimise wear in the machinery; and (iii) optimisation of performance and service lifetime, in order to reduce the required amount of lubricant [1].
The growing importance of these criteria in lubricant development should increase consistently the application in the next future of sustainable oils. With respect to mineral fluids, vegetable-based oils show good lubricity properties, along with renewability, biodegradability and low toxicity [2, 3]. In addition, they are well known as hydraulic fluids for a number of agricultural applications [4, 5]. Virgin oils and their ester derivatives may provide a wide range of physical-chemical properties in terms of high viscosity, low volatility and good cold behaviour. They also have drawbacks, associated to the triglyceride chemical nature, including susceptibility to oxidative and thermal degradation and their propensity to undergo hydrolysis in alkaline media. Depending on the application fields, these problems can be attenuated, as reported by Schneider [6], by expensive chemical modification, to replace the β hydrogen in the structure of the triglyceride with polyols such as trimethylolpropane, neopentyl glycol or pentaerythritol, or using specific low-input additives to improve their performance and to formulate more stable, low-cost and sustainable lubricants [7].
In addition, contamination or poor-quality hydraulic fluid could cause unnecessary wear and tear, and damages to the hydraulic system. Contamination can be caused by water or by small particles such as dirt, and also by some neo-formed sludge, caused by oil polymerisation or excessive phospholipid presence. Damages may include sticking, valves and filter blocking, and wear on moving parts, resulting in decreased performance or machine failure.
Many studies have been carried out to develop hydraulic fluids from oil-bearing crops, such as rapeseed [8], soybean [9], passion fruit and moringa [10], and sunflower with high oleic acid content [11].
The oilseed crop Crambe abyssinica Hochst. EX R.E.Fr. (Crambe) shows interesting agronomic features [12, 13], such as low-input requirements, robustness, high drought tolerance, adaptability to marginal lands and short life cycle [14]. Seeds have a good oil content (32–36%), with a valuable composition, interesting for several important industrial applications [15,16,17]. Indeed, Crambe is a less known oilseed crop, but it has been seriously reconsidered in the recent years as a new dedicated industrial oilseed crop [18], thanks to the relatively low content of polyunsaturated fatty acids (PUFA) and above all the significant erucic acid (cis-13-docosenoic acid, 22:1ω9 - CAS 112-86-7) content. Erucic acid is a long-chain mono-unsaturated fatty acid, with high molecular weight, and represents a potential starting material for the oleochemical industry. Due to its technical properties, high erucic acid oil can be used in the textile, steel and shipping industries as a biolubricant. It is in fact characterised by high viscosity, high smoke point, good wettability on different materials and high heat removal capability [19]. Crambe oil, in fact, shows a high kinematic viscosity (at 40 °C) and is one of the few native natural oils with properties close to conventional ISO 46 fluids normally used for hydraulic systems. For this reason, unlike other vegetable oils, Crambe oil does not require the addition of synthetic viscosity improvers. Furthermore, an erucic acid amide derivative, the erucamide, is used as a slip agent and for biodegradable plastic production, thus increasing the value of this oil [20]. Transgenic Crambe lines with an erucic acid content up to 73% and genetically engineering genotypes with an ultra-high erucic acid content up to 79.2% were recently reported and described [21, 22], even if, at the moment, only natural Crambe strains are utilised as a source of C22:1.
The aim of the present work was to investigate the use of native Crambe oil as a hydraulic fluid for agricultural applications; in particular, (i) Crambe was cultivated adopting low-input techniques in a virtuous green chemistry approach since the agricultural phase; (ii) the oil was mechanically extracted and partially refined for phospholipid removal; (iii) the addition of a common food-grade antioxidant (tert-butylhydroquinone (TBHQ)) was tested at the lab and small pilot scale in order to better understand the impact of additive concentration on oxidative stability; and (iv) the fluid efficiency tests were finally carried out using an oil test rig (OTR) simulating a real hydraulic device, performing heavy work cycles with the aim of strongly accelerating the ageing of the tested fluids, and monitoring fluid hydraulic performances and chemical-physical properties.
2 Materials and methods
2.1 Crambe cultivation
Crambe VAR. Mario, from CREA-CI Brassicales collection [23], was cultivated in Italy, at the experimental station of CREA-CI located at Budrio (Bologna) in the Po Valley area (44° 32′ 00″ N; 11° 29′ 33″ E, 28 m above sea level), at an open field level adopting low-input techniques both for energy and for fertilisers, whilst no pesticides were requested. A spring sowing was adopted in March 2017 on a 1600-m−2 experimental plot prepared with a plough and a spring-tooth harrow. Fertilisation was mainly provided through pelletised cattle manure–based amendment (C/N 15%) at a rate of 600 kg ha−1, at sowing time. The harvest was performed during the first decade of July. After harvesting, seeds were cleaned, partially dried, ground to 0.5-mm size and characterised for the following parameters. Dry matter content was determined by oven-drying the seeds at 105 °C for 12 h and evaluating the difference in weight before and after treatment. The oil content was determined by the standard automated continuous extraction, following the Twisselmann principle, by an E-816 ECE (Economic Continuous Extraction) extraction unit (BÜCHI Labortechnik AG, Switzerland), which utilised hexane as the solvent. Nitrogen content was determined by using the elemental analyser (LECO Corp., mod. CHN TruSpec, St. Joseph, MI, USA), and the crude protein content was calculated from nitrogen content using the conventional factor of 6.25. The same analyses were performed on the defatted seed meal obtained after oil extraction.
2.2 Oil extraction
The Crambe seeds were partly defatted by a screw press equipped with a pre-heater (80 °C) provided by MIG srl (Fornovo San Giovanni, Bergamo, Italy). Seeds were not dehulled or milled before extraction. The extracted oil was left to stand in the dark for some days in order to settle down the suspended particles and finally filtered at room temperature by using a laboratory filter paper.
2.3 Oil degumming
Extracted Crambe oil was degummed in an acid environment to minimise the content of phospholipids, calcium and phosphorus as well as of metallic contamination. The oil was heated at 70 °C under stirring, and a solution of 10% citric acid was slowly added. The amount of citric acid solution was calculated starting from the Ca content (see section 2.6 for analysis description), and the consequent hydration step was achieved by simultaneous homogenisation by using Ultra-Turrax (basic model T-50) for 15 min at 70 °C. The solution was then slowly agitated for another 30 min with a low-speed blade mixer. Agitation and heating were then stopped, and the solution was left to stand overnight. The formed precipitate was then separated by centrifugation, and the obtained clear oily phase was separated and washed by water under gentle agitation at 70 °C for 5 min. The lower water phase was removed by vacuum suction, and the oil phase was filtered on paper/cotton wool in order to remove the residual water. Finally, the oil was filtered again through a filter press and a 7-μm porosity paper.
2.4 Oil additivation studies
Degummed Crambe oil was first mixed with the antioxidant TBHQ (CAS1948-33-0) at the minimum concentration of 0.25 g kg−1 of TBHQ to be tested in the OTR. A stock solution, tenfold more concentrated, was firstly prepared by solubilising the product in a small amount of oil heated at 60 °C and then added to the rest of the oil to be used. The Rancimat test (see section 2.6 for method description) was performed to the oil before use. In a second phase, due to the unsatisfactory results obtained during the first trial in the OTR, a more detailed study was performed in laboratory tests by using the Rancimat equipment. The study permitted the evaluation of the TBHQ dose-response effect on the oil stability and the optimisation of the additive concentration in the range between 0 and 2.0 g kg−1. The maximum effective concentration of 2.0 g kg−1 was then chosen for the second OTR trial.
2.5 The oil test rig
The fluid efficiency tests were carried out in an oil test rig (OTR) (Fig. 1) designed at CREA-IT for hydrodynamic tests on hydraulic fluids [24]. The OTR consisted of a 30-dm3 reservoir for the oil to be tested. By means of a centrifugal pump (Ebara, mod. Matrix TE 3, Tokyo, Japan; max flowrate: 80 dm3min−1, max pressure: 0.5 MPa; power 0.75 kW), the fluid was sent to a high-pressure pump (Atos, mod. PFR203, Sesto Calende, Italy; max. pressure: 50 MPa; max. power: 5 kW; max. speed: 1800 min−1; displacement: 3.5 cm3; max. flow: 6.3 dm3 min−1) that forced it through a 40-MPa preloaded overpressure valve (Bosch Rexroth, mod DBDS 1G &X, Lohr am Mein, Germany), causing its lamination [25]. The oil outflowing the overpressure valve at high temperature was afterward conveyed to a heat exchanger (Pacetti, mod. BV 50, Ferrara, Italy) and cooled before coming back to the reservoir. The control of operating temperature has been set to maintain the oil entering the high-pressure pump at T ≤ 60 °C, in compliance with the operating limits defined by the manufacturer.
Views of the OTR. (A) Fluid reservoir; (B) low-pressure circulation pump; (C) main filter (25-μm filtration mesh); (D) high-pressure piston pump; (E) distributor block with 4 solenoid valves and 4 pressure valves (10, 20, 30, 40 MPa); (F) series of three fine filters (3, 6, 10-μm filtration mesh) and bypass; (G) heat exchanger; (H) electronic control and command module; (I) inverter operating the high-pressure pump; (L) oil heater unit with the 5 spiral-shaped steel pipes; and (M) oval gear flow metre
Compared to the OTR just described, the version used in this study was implemented with a compact oil heating unit (designed by CREA-IT) with the aim of increasing the thermal stress on the fluid [26]. It was installed in the flow line between the high-pressure pump and the overpressure valve: the line was prolonged and divided into 5 parallel, spiral-shaped steel pipes (each 6 m long, with 6-mm inner diameter), immersed in a water/ethylene glycol solution heated by three electric resistors within an insulated tank (volume: 60 l). Thereby, due to the wide contact surface between oil and heating solution and to the prolonged time of contact, the oil into the high-pressure section undergoes a thermal leap of about 40 °C, instead of the 20 °C of the OTR previous version, and the temperature of the oil outflowing the overpressure valve reaches about 100 °C. The OTR was used to apply severe work cycles to the oil under test with the aim of accelerating its ageing for the effect of both hydraulic work and thermal stress. During the work cycle, samples of the fluid were taken and analysed to monitor the evolution of the main typical parameters of hydraulic and lubricant fluids. Since the beginning of the test, the sample withdrawals (200 ml) were generally carried out according to the following schedule: new oil (from the container), after 1 h of work at OTR and every 30 h until the end of the test.
2.6 Oil chemical-physical characterisation and analyses
The extracted oil, in the crude form, as well as partially refined oil, and fluids sampled during the OTR test were subjected to the following analyses.
-
Fatty acid composition: the fatty acid composition of extracted oil was determined according to the ISO 12966-4:2015 [27] and ISO 12966-2:2017 [28]. The analyses were carried out by a gas chromatograph FOCUS (ThermoQuest Instrument, Rodano (MI), Italy) equipped with a flame ionisation detector (GC-FID), using a capillary column (Supelco, Bellefonte, PA, USA; l = 100 m, 0.32-mm i.d., film thickness 0.25 μm) after derivatisation of fatty acids into the corresponding methyl esters. The following analytical conditions were used: carrier gas (He) flowrate, 1.5 ml min−1; injector and detector temperatures, 250 and 260 °C, respectively; column oven temperature initially maintained at 90 °C, followed by a gradient to 240 °C, with a rate of 7 °C min−1; injected quantity 1 μl. A split injection system was applied (1:40).
-
Metal content analysis: extracted oil and fluids sampled from the test rig were analysed for trace metal and phosphorous content by inductively coupled plasma atomic/optic emission spectrometry (ICP-OES) equipment (PerkinElmer, Waltham, MA, USA) after dilution of samples in hydrogenated kerosene (Fluka, Buchs, Switzerland), according to ISO 21033:2016 standard [29].
-
Water content: the water content of the tested fluid was determined by means of a Karl Fischer automatic titrimeter (Metrohm, Herisau, Switzerland), according to ISO 8534:2017 standard [30].
-
Acidity and acid value (AV) analysis: free fatty acids were evaluated by means of volumetric titration by phenolphthalein as an indicator following the ISO 660:2020 method [31].
-
Peroxide value: fluid peroxide value was assessed according to ISO 3960:2017 standard [32]. It was determined by means of volumetric titration based on the liberation of iodine from potassium iodide in the presence of hydroperoxides. A starch aqueous solution was used as an indicator.
-
Oxidation stability evaluation: oxidation stability of the neat and added oils was performed by the Rancimat accelerated oxidation test, according to ISO 6886:2016 standard [33]. Oxidation induction times were measured by a Rancimat apparatus model 743 (Metrohm AG, Herisau, Switzerland) on 3 g of oil heated at 110 °C or 120 °C, depending on the predicted induction time, under a purified air flow of 10 l h−1 and 50 ml distilled water. In practice, the sample was introduced in a glass test tube and connected to the Rancimat heating block. At the same time, an air flow was passed through the heated sample, and the air stream was collected in a second vessel, containing distilled water and equipped by a conductimetric device. Heating and air flow promoted the oxidation of sample. When the oxidation phenomenon became incipient, formic and acetic acids were produced and distilled from the reaction vessel into the measurement vessel, where a significant increase in conductivity was recorded. All Rancimat tests provided a graphic result, where time and electric conductivity were reported as abscissa and ordinate, respectively. The sudden change in slope caused by oxidation start was identified as the “Rancimat induction time” (RIT).
-
Kinematic viscosity: the ASTM D445 standard method [34] was used in order to determine oil kinematic viscosity. The method was based on the measurement of time required for the complete flow of a fixed amount of sample through a calibrated and thermostated tube. Two different measurements carried out at 40 and 100 °C allowed the calculation of viscosity index, by means of tables reported in ASTM D2270 [35].
-
Antioxidant fluid content: the evaluation of antioxidant (TBHQ) fluid content was carried out by the HPLC reversed phase method, as described by Tagliabue et al. [36], with minor modifications. The quantitative evaluation was done using an external standardisation. The experimental conditions in use were as follows: HPLC System Shimadzu Nexera (Shimadzu Italia, Milan, Italy) equipped with a reverse phase column Ascentis Supelco 25% carbon load 5 μn, 250 mm × 4.6 mm ID (Supelco, Bellefonte, MA, USA). The elution was obtained in gradient mode (A: water with 0.5% H3PO4; B: methanol with 0.5% H3PO4; C: acetonitrile) at a flowrate of 1 ml min−1, according to the following gradient programme: 85% A/15% B/0% C in 30 min to 0% A, 50% B, 50% C. Samples were dissolved in isopropanol at a concentration of 0.05 g ml−1, the detector UV was set at 280 nm and the column temperature was 30 °C.
-
Calorific power: ASTM D240 and ASTM D5291 [37, 38] were used to evaluate the fluid lower calorific value and the hydrogen content, respectively. From these data, the upper calorific value was calculated.
2.7 Statistical analysis
All reported results are the average values of two independent evaluations, after repeatability requirement check. For each standard method, the uncertainty of measurement is reported with 95% probability. All other analyses were carried out in duplicate, and the standard deviation was calculated.
3 Results and discussion
3.1 Crambe cultivation
The Crambe cultivation did not show any particular problem and the entire cycle did not request any chemical support. The harvest seed amount obtained from the experimental plot was around 300 kg, implying a potential yield of 1.9 t ha−1. The obtained yield was consistent and rather high probably due to the good soil fertility derived from a 3-year rotation. The yield was near or better than those obtained in other trials conducted in northern Italy with larger amounts of fertilisers [39], and even with the same variety Mario [40].
Therefore, considering the extremely low input applied, Crambe could represent a novel alternative for small-/medium-scale farms for which a sustainable production of straight vegetable oil is already under evaluation [41]. Moreover, its exploitation as a biofuel and/or lubricant for self-consumption could add value to the chain [42].
3.2 Oil extraction and product characterisation
Oil seed content was determined as 32.8% based on dry weight (DW), consistent with other papers [43]. An oil mechanical extraction method was chosen as a simpler and safer technique if compared to solvent extraction, able to produce high-quality oil. Both cold- and hot-press extraction methods were followed, the latter involving the seed heat pre-treatment at 80 °C. High temperature application usually facilitates the oil release in terms of speed of the extraction process, but at the same time could affect the oil oxidative stability and quality in terms of valuable components and reduce oil keeping quality [44]. The results from the two extraction methods are presented in Table 1. Heat application did not have a great influence on the final yield of extracted oil, around 40% of total oil, in both cold- and hot-press extraction methods. Indeed, the residual oil content of the two samples of defatted seed meal derived from cold- and hot-press methods was comparable and quite high, probably because the seeds were not dehulled before extraction, with the aim of better preserving seed quality during storage [45]. The obtained two oil samples were analysed for quality characterisation, and Table 2 shows oil fatty acid composition, with a high percentage of erucic acid for both samples, as expected [46], whilst no important differences in fatty acid composition were found between the two oils. On the other hand, results from the element analysis (Table 3) evidenced a difference between the two oil samples, particularly in the calcium and phosphorus contents, two parameters closely linked to the oil phospholipidic content. These two elements resulted much higher in the hot-pressed sample. However, this drawback was overcome by applying the degumming process of the hot-pressed oil which determined a drastic reduction of the two-element concentration as shown in Table 3 for degummed oil. Besides, the absence of other metal contaminations or pro-oxidants was evidenced in both samples, whilst the oil total acidity was quite low and reflected one of the seed sources for both samples, as determined by standard solvent extraction (not shown). In this case, hot-pressed extraction did not remarkably improve the oil yield (Table 1) and, on the contrary, has slightly worsened the oil quality (Table 3), making the heating during the extraction phase counterproductive. Nevertheless, the crushing yield could be improved by the optimisation of some operating parameters, such as screw design, screw rotating speed, feeding rate and final pressure at the end of the machine, with special attention to the relationship existing between oil yield and oil properties.
For the OTR trials, a mixture of equal amounts of the untreated cold-pressed oil and the degummed hot-pressed oil samples was used.
Finally, the residual defatted seed meal, representing the 86–87% of the seed weight (Table 1), was analysed for the protein content, determined as 23.5% (based on dry weight). This is an important aspect to be explored, considering that this material could be a good source of protein, useful for feed, food or non-food agricultural applications, as already investigated for other oilseed crops [47,48,49]. Therefore, defatted seed meal represents a valuable co-product of oil extraction that, if well valorised, could improve the entire value of the chain.
3.3 Antioxidant selection and first oil additivation
Following a green chemistry approach, a critical evaluation for antioxidant selection was carried out before the experimental tests. Based on previous experiences [50], the TBHQ was chosen for the preliminary test, as a product that meets several required properties in terms of safety. Indeed, TBHQ is a food-grade additive, accepted for its efficacy, as it stabilises lipid matrix at ambient temperatures and at high temperatures as well. Furthermore, it is very soluble in a fatty environment (minimising the risk of sludge formation) and finally, it contributes for only a small part to the total acidity of the fluid, thanks to its very weak acid properties [51, 52]. Therefore, based on preliminary evaluations, the oil was firstly added with 0.25 g kg−1 of TBHQ, tested for oxidative stability by the accelerated oxidation test, the Rancimat method, performed at 110 °C and compared with neat oil. The TBHQ addition to the oil determined a shift of the RIT from 15.7 h to more than 24 h, indicating an increasing oil resistance to oxidation.
3.4 First oil endurance test
The experimental OTR performs heavy hydraulic work cycles with small oil volumes (25 dm3), with the aim of strongly accelerating the ageing of the tested fluid with respect to what usually occurs, e.g. in agricultural tractors (oil volume up to 180 dm3 with a service lifetime of 800–1000 h), according to a non-standard test methodology developed considering the variables characterising the hydraulic systems. In the case of a hydraulic fluid, the ageing should be achieved through the effects of the continuous lamination into the high-pressure section and of the thermal stress. Controlling the operating pressure and the fluid flowrate allows the real-time calculation of the exerted hydraulic power and the hydraulic work done. The possibility to control and adjust them and to repeat the work cycles allows the comparative evaluation of different fluids observing the evolution of their performances and of their chemical-physical properties. The maximum values of the technical performance (fluid operating pressure and temperature, flowrate, power) applicable with the OTR to the tested fluid are reported in Table 4. They were continuously measured (frequency of acquisition: 1 Hz) and monitored in real time to observe any variation caused by changes in fluid properties, storing the average values of 1-min acquisitions. With a flowrate of 5.7 dm3 min−1, in 1 h, the whole mass of oil was recirculated approximately 13 times. Basing on data from previous studies on the utilisation of agricultural tractors [53, 54], it has been assessed that a 150-h work cycle under the conditions reported in Table 4 corresponds to the hydraulic work done by the hydraulic system of a medium-power agricultural tractor in about 1 year, with major thermal stress. Therefore, an OTR single work cycle should last a minimum of 150 h. Such assessment only aims at providing an order of magnitude of the intensity of the work cycle because, however, it must be considered that most of tractors are supplied with multifunctional oils that besides the hydraulic function also carry out the lubrication of the transmission. Moreover, the lifetime of conventional hydraulic oils is commonly very long, of several thousand hours and often for life.
The Crambe oil added with 0.25 g kg−1 of TBHQ was first tested in the OTR. After 50 h of test, the oil degradation became evident in terms of viscosity (at 40 and 100 °C), which started to increase up to exceed 20% variation (at about 70 h), the maximum admitted value before oil change according to the standard ASTM D445 (Fig. 2a). The peroxide value reached its maximum level of 170 meq O2 kg−1 after about 70 h and then began to decrease until 125 meq O2 kg−1, probably as a consequence of peroxide degradation in polymerised structures. This phenomenon was correlated with the observed increase in viscosity. The acidity value (AV) was low at the beginning of the trial but started to increase after 60–70 h, reaching values higher than 2.0 mg KOH g−1, which are considered dangerous for system corrosion (Fig. 2b).
Due to complications related to the presumed loss of the lubricating properties of the tested fluid, and in order to preserve the operating integrity of the high-pressure pump, the first Crambe oil endurance test was suspended after 134 h of hydraulic work at OTR. It is possible to state that this formulation did not fit for agricultural applications, although the oil, as reported in Fig. 3, was able to maintain sensitively constant the technical performance. However, as to metal contamination of fluid samples during the test (Table 5), increasing amounts of Cu (probably released from some pipelines of the hydraulic circuit) seemed to indicate the start of a corrosion process. Such contamination could be related to the high concentration of peroxides, due to the Cu pro-oxidant properties. At the same time, the observed increases in Ca, P and, in lesser extent, Mg could derive from the release of additive elements deposited in the OTR by previously tested fluids. Instead, fluid water content slightly decreased at the beginning of the process, but soon stabilised at about 500 mg kg−1, thus showing a reduced moisture intake at the proposed operating conditions.
3.5 tert-Butylhydroquinone dose optimisation
Due to severe oxidative degradation, which occurred with Crambe oil during the first endurance test, a more detailed additivation study was performed by adding increasing TBHQ concentrations to the oil and registering the RIT for oxidative stability final evaluation (Fig. 4). This time, the Rancimat test was performed at 120 °C in order to appreciate differences in the RIT at high TBHQ concentrations, otherwise not detectable (RIT > 24 h) if performed at 110 °C as in previous tests. Figure 4 shows how RIT increase was directly proportional to TBHQ concentration up to 1.0 g kg−1; instead, a minor increase was registered for the last antioxidant addition of 2.0 g kg−1. Higher TBHQ quantities were not considered as further improvement in RIT would not be significant and would have caused possible solubility problems. Therefore, the TBHQ concentration chosen for the second trials was 2.0 g kg−1.
Evaluation of the effect of TBHQ on the oxidative stability of Crambe oil, determined by the Rancimat test performed at 120 °C. TBHQ amount is expressed in g kg−1 and Rancimat induction time (RIT) is expressed in hours (h). The reported results represent the average value of two independent analyses ± uncertainty of measurement
3.6 Second oil endurance test
The performances of Crambe oil, added with 2.0 g kg−1 of TBHQ, significantly improved in the second test. The reported graphics show that no increase in kinematic viscosity, viscosity index (Fig. 2a), peroxide value and AV (Fig. 2b) was observed during the test in the OTR up to 290 h. In addition, the technical performance, such as fluid operating pressure and flowrate (Fig. 3a), fluid temperature and hydraulic power (Fig. 3b) remained significantly constant along the entire work cycle, as confirmed by the low values of the standard deviations and coefficients of variation (CV) reported in Table 6. Basing on these results, the oil lifetime in the second endurance test can be considered technically at least quadrupled compared to the first test (70 h) and corresponds to almost 2 years of work, according to the assumptions of the hypothesis on the 150-h work cycle.
The elemental analysis of fluids sampled during the rig test did not show any important change in metal contamination (Table 7). The results indicated that no OTR components were affected by corrosion caused by the tested fluid. The increase in Cu contamination observed in the first test did not occur in this case. The only exception was represented by the Zn concentration: it started to increase after 134 h and resulted anyway remarkably lower than in the first test. However, the origin of Zn contamination deserves further investigation.
3.7 Determination of residual TBHQ concentration and Rancimat test in OTR-sampled fluids
The RIT and the THBQ content in fluid samples were also determined in order to assess the residual oil lifetime and the residual amount of antioxidant, respectively. Figure 5 shows that both parameters had similar decreasing trends, suggesting that, after the 290-h work cycle, the oil was very close to the end of its technical life as a hydraulic fluid, having exhausted the protective action of the antioxidant additive. The evaluation of residual TBHQ concentration on the sample taken after 290 h was not possible because of the presence of some interfering signals in HPLC-RP analysis. Results also showed that both parameters could be a valuable index of fluid degradation for preventive substitution.
The Rancimat induction time (RIT) test performed at 120 °C and residual TBHQ quantification performed on OTR fluids sampled at different times (h) during the second test on Crambe oil additivated with 2 g kg−1 of antioxidant. TBHQ results, expressed in g kg−1 of fluid, represent the average value of two independent analyses ± standard deviation. RIT results (h) represent the average value of two independent analyses ± uncertainty of measurement
3.8 Possible exhausted oil utilisations
From the circular economy point of view, not only should each technical product be renewable, biodegradable and environmentally friendly, but also its destiny at the end of the life cycle should be considered. On this concern, the Crambe oil at the end of its lifetime showed modest increases in viscosity, peroxide value, AV and metal contamination, thereby representing a very interesting feedstock for biodiesel and technical glycerol production. The interest is great also in consideration of the classification of this material as a waste of a primary process, which makes it a candidate for the so-called double counting status. According to the European Regulation, using “double counting fluids” allows fuel companies to cut off 50% the mandatory value of blending with biodiesel (from a maximum of 7% down to 3.5% in volume). The hypothesis of using exhausted Crambe oil as base stock for biodiesel production is also supported by the calorific values determined in the oil samples before and after the test. In fact, higher and lower calorific power and hydrogen content did not show any significant difference, as reported in Table 8.
4 Conclusions
The present study concerns the feasibility of using natural Crambe oil, given its tribological properties, as a hydraulic fluid after a partial refining and a simple but suitable addition of antioxidant. According to the results of a test based on a heavy hydraulic work cycle in a test rig, the pre-treated Crambe oil provided very promising results, encouraging further experiments on its use under real working conditions.
Furthermore, from an agronomic point of view, the satisfactory seed yield and the potential exploitation of defatted seed meal as a co-product could open novel industrial applications, if we consider the several environmental advantages reached by replacing mineral-based oils with base stocks of vegetable origin. Such a process will contribute to improve the sustainability of the entire agricultural system, in terms of both environmental and workers’ protection.
Another important issue to consider is the risk of contamination of vegetable food by hydrocarbons resulting, for example, from failures and consequent losses that occurred in plants and systems used in production processes [55, 56]. The partial or total replacement of mineral oils with vegetable oil–based fluids must be implemented, in the next future, in order to reduce food contamination.
Moreover, the possibility of reusing the “hydraulic Crambe oil”, at the end of its lifetime, in the sector of bioenergy/biodiesel or, more generally, as a feedstock for the production of fatty acids and natural technical glycerol, could increase the interest of the entire production chain. In any case, at the end of their lifetime, the cultivation residues derived from vegetable sources could be composted, whilst those of chemical origin must be treated as a toxic waste with additional cost and pollution. The reduced amount of non-vegetable oil constituents might allow the transformation of the used fluid in bioenergy with simple unit operations, whilst the recovery of free fatty acids after splitting can be regarded to valorise other as a possible option. In addition, the exploitation of the extraction co-product defatted seed meal for feed and agricultural uses goes towards the biorefinery concept for the development of a sustainable production chain.
Data availability
Not applicable
References
Boyde S (2002) Green lubricants: environmental benefits and impacts of lubrication. Green Chem 4:293–307. https://doi.org/10.1039/B202272A
Adamczewska JZ, Wilson D (1997) Development of ecologically responsive lubricants. J Synthetic Lubr 14(2):129–141. https://doi.org/10.1002/jsl.3000140203
Bondioli P, Della Bella L, Manglaviti A (2002) Synthesis of biolubricants with high viscosity and high oxidation stability. OCL-OL Corps Gras Li 10(2):150–154
Mendoza G, Igartua A, Fernandez-Diaz F, Urquiola F, Vivanco S, Arguizoniz R (2011) Vegetable oils as hydraulic fluids for agricultural applications. Grasas Aceites 62(1):29–38. https://doi.org/10.3989/gya.056210
Pochi D, Fanigliulo R, Bisaglia C, Cutini M, Grilli R, Betto M, Fornaciari L (2020) Vegetable-based oil as UTTO fluid for agricultural tractors application. Appl Eng Agric 36(1):79–88. https://doi.org/10.13031/aea.13488
Schneider M (2006) Plant-oil-based lubricants and hydraulic fluids. Sci Food Agric 86:1769–1780. https://doi.org/10.1002/jsfa.2559
Erhan SZ, Sharma BK, Perez JM (2006) Oxidation and low temperature stability of vegetable oil-based lubricants. Ind Crop Prod 24:292–299. https://doi.org/10.1016/j.indcrop.2006.06.008
Remmele E, Widmann B (1999) Suitability and environmental compatibility of rapeseed oil based hydraulic fluids for agricultural machinery. J Syn Lubr 16(2):129–145
Honary LAT (1996) An investigation of the use of soybean oil in hydraulic systems. Bioresour Technol 56:41–47
Silva MS, Foletto EL, Alves SM, de Castro Dantas TN, Dantas Neto AA (2015) New hydraulic biolubricants based on passion fruit and moringa oils and their epoxy. Ind Crop Prod 69:362–370. https://doi.org/10.1016/j.indcrop.2015.02.037
Leao JD, Bouillon V, Muntada L, Johnson C, Wilson P, Vergnes O, Dano C, Igartua A, Mendoza G (2016) New formulations of sunflower based bio-lubricants with high oleic acid content – VOSOLUB project. OCL-OL Corps Gras Li 23(5):D509. https://doi.org/10.1051/ocl/2016033
Mastebroek HD, Wallenburg SC, van Soest LJM (1994) Variation for agronomic characteristics in Crambe (Crambe abyssinica Hochst. ex Fries). Ind Crop Prod 2(2):129–136. https://doi.org/10.1016/0926-6690(94)90094-9
Fontana F, Lazzeri L, Malaguti L, Galletti S (1998) Agronomic characterization of some Crambe abyssinica genotypes in a locality of the Po Valley. Eur J Agron 9:117–126. https://doi.org/10.1016/s1161-0301(98)00037-9
Righini D, Zanetti F, Monti A (2016) The bio-based economy can serve as the springboard for camelina and Crambe to quit the limbo. OCL-OL Corps Gras Li 23(5):D504. https://doi.org/10.1051/ocl/2016021
Lalas S, Gortzi O, Athanasiadis V, Dourtoglou E, Dourtoglou V (2012) Full characterization of Crambe abyssinica Hochst. seed oil. J Am Oil Chem Soc 89:2253–2258. https://doi.org/10.1007/s11746-012-2122-y
Lazzeri L, De Mattei F, Bucelli F, Palmieri S (1997) Crambe oil - a potential new hydraulic oil and quenchant. Ind Lubr Tribol 49(2):71–77. https://doi.org/10.1108/00368799710163893
Bondioli P, Inzaghi L, Postorino G, Quartuccio P (1999) Crambe abyssinica oil and its derivatives as renewable lubricants: synthesis and characterization of different esters based on Crambe fatty acids. J Syn Lubr 15:271–283
Zhu LH (2016) Crambe (Crambe abyssinica). In: McKeon TA, Hayes DG, Hildebrand DF, Weselake RJ (eds) Industrial oil crops. Academic Press and AOCS Press, p 195. https://doi.org/10.1016/B978-1-893997-98-1.00007-5
Vargas-Lopez JM, Wiesenborn D, Tostenson K, Cihacek L (1999) Processing of Crambe for oil and isolation of erucic acid. J Am Oil Chem Soc 76(7):801–809. https://doi.org/10.1007/s11746-999-0069-4
Zorn K, Oroz-Guinea I, Bornscheuer UT (2019) Strategies for enriching erucic acid from Crambe abyssinica oil by improved Candida antarctica lipase A variants. Process Biochem 79:65–73. https://doi.org/10.1016/j.procbio.2018.12.022
Li X, Van Loo EN, Gruber J, Fan J, Guan R, Frentzen M, Stymne S, Zhu LH (2012) Development of ultra-high erucic acid oil in the industrial oil crop Crambe abyssinica. Plant Biotechnol J 10(7):862–870. https://doi.org/10.1111/j.1467-7652.2012.00709.x
Qi W, Tinnenbroek-Capel IEM, Salentijn EMJ, Zhang Z, Huang B, Cheng J, Shao H, Visser RGF, Krens FA, Van Loo EN (2018) Genetically engineering Crambe abyssinica – a potentially high-value oil crop for salt land improvement. Land Degrad Dev 29:1096–1106. https://doi.org/10.1002/ldr.2847
Lazzeri L, Malaguti L, Bagatta M, D’Avino L, Ugolini L, De Nicola GR, Casadei N, Cinti Matteo S, Iori R (2013) Characterization of the main glucosinolate content and fatty acid composition in non-food Brassicaceae seeds. Acta Hortic 1005:331–338. https://doi.org/10.17660/ActaHortic.2013.1005.38
Pochi D, Fanigliulo R, Grilli R, Fornaciari L, Bisaglia C, Cutini M, Brambilla M, Sagliano A, Capuzzi L, Palmieri F, Chiatti G (2020) Design and assessment of a test rig for hydrodynamic tests on hydraulic fluids. In: Coppola A, Di Renzo GC, Altieri G, D’Antonio P (eds) Innovative biosystems engineering for sustainable agriculture, forestry and food production, MID-TERM AIIA 2019. “Lecture notes in civil engineering” Book Series, vol 67. Springer Nature, Cham, pp 419–429. https://doi.org/10.1007/978-3-030-39299-4_47
Totten GE, Melief HM, Bishop RJ (2000) Hydraulic fluid qualification using the Rexroth high-pressure piston pump test. NFPA Technical Paper Series I00-9(2):241–249
Pochi D, Fanigliulo R, Bisaglia C, Cutini M, Grilli R, Fornaciari L, Betto M, Pari L, Gallucci F, Capuzzi L, Sagliano A, Palmieri F, Chiatti G (2020) Test rig and method for comparative evaluation of conventional and bio-based hydraulic fluids and lubricants for agricultural transmissions. Sustainability 12(20):8564. https://doi.org/10.3390/su12208564
ISO 12966-4:2015 - Animal and vegetable fats and oils - gas chromatography of fatty acid methyl esters - Part 4: determination by capillary gas chromatography, The International Organization for Standardization, Geneva, Switzerland, 2015
ISO 12966-2:2017- Animal and vegetable fats and oils - gas chromatography of fatty acid methyl esters - Part 2: preparation of methyl esters of fatty acids, The International Organization for Standardization, Geneva, Switzerland, 2017
ISO 21033:2016 - Animal and vegetable fats and oils - determination of trace elements by inductively coupled plasma optical emission spectroscopy (ICP-OES), The International Organization for Standardization, Geneva, Switzerland, 2016
ISO 8534:2017 - Animal and vegetable fats and oils - determination of water content - Karl Fischer method (pyridine free), The International Organization for Standardization, Geneva, Switzerland, 2017
ISO 660:2020 - Animal and vegetable fats and oils - determination of acid value and acidity, The International Organization for Standardization, Geneva, Switzerland, 2020
ISO 3960:2017 - Animal and vegetable fats and oils - determination of peroxide value - iodometric (visual) endpoint determination, The International Organization for Standardization, Geneva, Switzerland, 2017
ISO 6886:2016 - Animal and vegetable fats and oils - determination of oxidative stability (accelerated oxidation test), The International Organization for Standardization, Geneva, Switzerland, 2016
ASTM, ASTM D445-06, Standard test method for kinematic viscosity of transparent and opaque liquids (and calculation of dynamic viscosity), ASTM International, West Conshohocken, Pennsylvania, USA, 2006
ASTM, ASTM D2270-10(2016), Standard practice for calculating viscosity index from kinematic viscosity at 40 °C and 100 °C, ASTM International, West Conshohocken, Pennsylvania, USA, 2016
Tagliabue S, Gasparoli A, Della Bella L, Bondioli P (2004) Quali-quantitative determination of synthetic antioxidants in biodiesel. Riv Ital Sostanze Gr 81:37–40
ASTM, ASTM D240-17, Standard test method for heat of combustion of liquid hydrocarbon fuels by bomb calorimeter, , ASTM International, West Conshohocken, Pennsylvania, USA, 2017
ASTM, ASTM D5291-16, Standard test methods for instrumental determination of carbon, hydrogen, and nitrogen in petroleum products and lubricants, ASTM International, West Conshohocken, Pennsylvania, USA, 2016
Laghetti G, Piergiovanni AR, Perrino P (1995) Yield and oil quality in selected lines of Crambe abyssinica Hochst. ex R.E. Fries and C. hispanica L. grown in Italy. Ind Crop Prod 4(3):203–212. https://doi.org/10.1016/0926-6690(95)00033-9
Zanetti F, Scordia D, Vamerali T, Copani V, Dal Cortivo C, Mosca G (2016) Crambe abyssinica a non-food crop with potential for the Mediterranean climate: insights on productive performances and root growth. Ind Crop Prod 90:152–160. https://doi.org/10.1016/j.indcrop.2016.06.023
Viccaro M, Cozzi M, Rocchi B, Romano S (2019) Conservation agriculture to promote inland biofuel production in Italy: an economic assessment of rapeseed straight vegetable oil as a self-supply agricultural biofuel. J Clean Prod 217:153–161. https://doi.org/10.1016/j.jclepro.2019.01.251
Baquero G, Esteban B, Rius A, Riba JR, Puig R (2010) Small-scale production of straight vegetable oil from rapeseed and its use as biofuel in the Spanish territory. Energ Policy 38(1):189–196. https://doi.org/10.1016/j.enpol.2009.09.004
Costa E, Almeida MF, Alvim-Ferraz C, Dias JM (2019) The cycle of biodiesel production from Crambe abyssinica in Portugal. Ind Crop Prod 129(5):51–58. https://doi.org/10.1016/j.indcrop.2018.11.032
Yusuf AK (2018) A review of methods used for seed oil extraction. Int J Sci Res 7(12):233–238. https://doi.org/10.21275/1121804
Santos SS, Biaggioni MAM, Monteiro IMC, Sartori MMP, Brandão FJB (2019) Storage potential of peeled Crambe for oil quality. Eng Agríc 39(4):518–523. ISSN 1809-4430. https://doi.org/10.1590/1809-4430-Eng.Agric.v39n4p518-523/2019
Lazzeri L, Leoni O, Conte LS, Palmieri S (1994) Some technological characteristics and potential uses of Crambe abyssinica products. Ind Crop Prod 3(1–2):103–112. https://doi.org/10.1016/0926-6690(94)90083-3
Massoura E, Vereijken JM, Kolster P, Derksen JTP (1996) Isolation and functional properties of proteins from Crambe abyssinica oil seeds. In: Janick J (ed) Progress in new crops. ASHS Press, Alexandria, p 322
Ugolini L, Cinti S, Righetti L, Stefan A, Matteo R, D’Avino L, Lazzeri L (2015) Production of an enzymatic protein hydrolyzate from defatted sunflower seed meal for potential application as a plant biostimulant. Ind Crop Prod 75:15–23. https://doi.org/10.1016/j.indcrop.2014.11.026
Canistro D, Vivarelli F, Ugolini L, Pinna C, Grandi M, Antonazzo IC, Cirillo S, Sapone A, Cinti S, Lazzeri L, Conte E, Biagi G (2017) Digestibility, toxicity and metabolic effects of rapeseed and sunflower protein hydrolysates in mice. Ital J Anim Sci 16(3):462–473. https://doi.org/10.1080/1828051X.2017.1298410
Bondioli P, Gasparoli A, Della Bella L, Tagliabue S, Toso G (2003) Biodiesel stability under commercial storage conditions over one year. Eur J Lipid Sci Tech 105:735–741. https://doi.org/10.1002/ejlt.200300783
Schober S, Mittelbach M (2004) The impact of antioxidants on biodiesel oxidation stability. Eur J Lipid Sci Tech 106(6):382–389. https://doi.org/10.1002/ejlt.200400954
Prasad N, Siddaramaiah B, Banu M (2015) Effect of antioxidant tertiary butyl hydroquinone on the thermal and oxidative stability of sesame oil (Sesamum indicum) by ultrasonic studies. J Food Sci Technol 52(4):2238–2246. https://doi.org/10.1007/s13197-014-1276-z
Renius KT (1985) Tractors: technology and its application. BLV Publishing Society, Munchen
Osinenko P (2014) Optimal slip control for tractors with feedback of drive torque. Dissertation, Technische Universität Dresden
Lacoste F (2014) Undesirable substances in vegetable oils: anything to declare? OCL-OL Corps Gras Li 21(1):A103. https://doi.org/10.1051/ocl/2013060
Matthaus B, Lacoste F, Bruehl L (2016) Contaminants in edible fats and oils – fresh news. Eur J Lipid Sci Tech 118(3):337–338. https://doi.org/10.1002/ejlt.201600056
Acknowledgments
We thank Nerio Casadei (CREA-CI) for supporting Crambe reproduction in Bologna and Crambe oil extraction and Stefano Benigni (CREA-IT) for technical support during the oil endurance tests.
Funding
This research has been carried out in the ambit of the AGROENER Research Project, WP4 – Integrated biorefineries in agro-food production chains, granted by MiPAAF, the Italian Ministry of Agriculture, Food and Forestry Policies (D.D. n. 26329).
Author information
Authors and Affiliations
Corresponding author
Ethics declarations
Conflict of interest
The authors declare that they have no conflict of interest.
Code availability
Not applicable
Additional information
Publisher’s Note
Springer Nature remains neutral with regard to jurisdictional claims in published maps and institutional affiliations.
Rights and permissions
About this article
Cite this article
Fanigliulo, R., Pochi, D., Bondioli, P. et al. Semi-refined Crambe abyssinica (Hochst. EX R.E.Fr.) oil as a biobased hydraulic fluid for agricultural applications. Biomass Conv. Bioref. 13, 1859–1871 (2023). https://doi.org/10.1007/s13399-020-01213-y
Received:
Revised:
Accepted:
Published:
Issue Date:
DOI: https://doi.org/10.1007/s13399-020-01213-y