Abstract
The study proposes a cold chain location-allocation configuration decision model for shippers and customers by considering value deterioration and coordination by using big data approximation. Value deterioration is assessed in terms of limited shelf life, opportunity cost, and units of product transportation. In this study, a customer can be defined as a member of any cold chain, such as cold warehouse stores, retailers, and last mile service providers. Each customer only manages products that are in a certain stage of the product life cycle, which is referred to as the expected shelf life. Because of the geographical dispersion of customers and their unpredictable demands as well as the varying shelf life of products, complexity is another challenge in a cold chain. Improved coordination between shippers and customers is expected to reduce this complexity, and this is introduced in the model as a longitudinal factor for service distance requirement. We use big data information that reflects geospatial attributes of location to derive the real feasible distance between shippers and customers. We formulate the cold chain location-allocation decision problem as a mixed integer linear programming problem, which is solved using the CPLEX solver. The proposed decision model increases efficiency, adequately equates supply and demand, and reduces wastage. Our study encourages managers to ship full truck load consignments, to be aware of uneven allocation based on proximity, and to supervise heterogeneous product allocation according to storage requirements.
Similar content being viewed by others
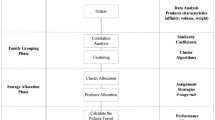
Avoid common mistakes on your manuscript.
1 Introduction
Changes in lifestyle and income increases in developed and developing countries have escalated the demand for healthy and nutritious food products. The demand for frozen food, currently valued at US$224.74 billion, is projected to reach US$293.75 billion by 2019 (Meneghetti and Monti 2015). Fruits, vegetables, and pharmaceutical goods are typical examples of perishable products that tend to deteriorate exponentially over time (Bai and Kendall 2008); therefore, monitoring and controlling storage temperature is essential to enhance the safety and quality of such products. The objective of cold chain configuration design is to protect perishable products while minimizing cost, waste, and energy. Currently, cold chain configuration is neither adequately developed nor applicable to bottom line users, who are highly fragmented and characterized by the many geographically dispersed primary producers and intermediaries followed by manufacturers, retailers, and so forth. The major reason for this fragmentation is the supply and demand mismatch which arises from a seasonal production but a year-long demand requirement. The few attempts that have been made to equate cold chain demand with supply have resulted in searches for suppliers beyond regional boundaries. Regulations on products imported by sea are typically different from those imposed when the same product is produced and consumed locally. This differentiation is a crucial characteristic to be considered when designing a cold chain distribution network configuration strategy because the product value and deterioration depends on the product’s age and not its durability. The specific requirements for storage and transportation configuration under controlled conditions further amplify the complexity that requires customized strategies to enable efficient functioning of cold chain operations.
High safety and quality requirements for perishable products, particularly food products, have resulted in considerable wastage, leading to economic and social losses. This is a major concern in emerging economies, specifically in China, where 370 million tons of fruits and vegetables (worth 75 billion Yuan), which can feed 200 million people, are wasted annually. Similarly, in India, poor infrastructure and inadequate monitoring results in substantial (35–40 %) wastage of fruits and vegetables (Shih and Wang 2016). The effects of temperature and time on the internal characteristics of food products are irreversible, which places stringent requirements on preserving food safety and quality. Food loss is primarily attributed to inadequate storage infrastructure and inappropriate handling and transportation. Decision makers at all stages of food manufacturing must differentiate between appropriate use of frozen storage and cool storage. The aforementioned factors also lead to misinterpretation of information by multiple actors at various stages (Thakur and Forås 2015).
Food supply chains are similar to value chains except in that the deployment of appropriate refrigeration technology is critical to maintaining the quality, nutritional, and financial value of the product (Dodd and Bouwer 2014). Although effective cold chain management primarily decelerates the deterioration of harvested products, it may not necessarily enhance the nutritional value. Some attributes that increase the complexity of cold chain are distance, change of transport, and storage units, as well as other trade and border regulations.
Involvement of heterogeneous customers further complicates the operation and functioning of cold chains. The standard location–allocation problem in a conventional supply chain includes aggregating demand and service requirements by customers rather than by products. However, to develop a suitable cold chain configuration for perishable products, shelf life and stringent storage requirements are critical factors that must be considered in the location—allocation decision.
We propose a decision model for analyzing how certain customers identify cold storage locations and allocate according to the demand for perishable products. In addition to shelf life, we consider four other factors that are most essential in location allocation for cold chains: coordination among fragmented and heterogeneous customers, opportunity cost in terms of deterioration of value with time, units of product transportation, and distance calculation by using big data approximation. A critical aspect considered in the model is the difference between product value and market price. Shelf life represents the marketable life of a product and not necessarily its physical condition or deterioration rate (Wang et al. 2009).
The present study contributes to the literature on location—allocation by integrating the aspect of perishability in decision-making. Location—allocation studies that have addressed durable products have been modeled using customer service requirements. In this study, a customer is any member of a cold chain, such as cold warehouse stores, retailers, and last-mile service providers. Each customer can manage only products that are in a certain stage of the product life cycle, which is referred to as the expected shelf life (ESL). Moreover, the same product might be required by various customers with different ESL and different product value on account of order frequency, proximity from point of use (PoU), and selling market. Geographically fragmented customers with different ESL increase the complexity of coordination necessary for satisfying demands. Coordination is achieved by selecting and allocating storage locations that satisfy the ESL of customers. This is incorporated into the model by translating ESL into a service distance requirement. The proposed model allows both discrete and continuous transportation units for products. For example, a piecewise product flows in discrete units, whereas weight (in kilograms) flows in continuous units. Value for perishable products deteriorates with time (Coelho and Laporte 2014) and unmet demand for perishable products can then be considered opportunity cost. We define opportunity cost as a value of product ESL perceived by customers that determines the bundling of products when storage capacity is limited. The study utilizes big data information that reflects geospatial attributes of location to derive the real feasible distance between shippers and customers. The conceptual description of the problem is detailed in Sect. 3. The results of this study provide several valuable insights into aspects such as full truck load (FTL) shipments, uneven allocation based on proximity, and heterogeneous product allocation according to storage requirements. Finally, the role of opportunity cost is illustrated under capacity allocation decision. The optimization model facilitates coordination by encapsulating the service distance requirement of perishable products to a heterogeneous group of customers.
The remainder of the paper is organized as follows: Sect. 2 presents a discussion of the literature on cold chain storage requirement and coordination concerns, location–allocation problem, and summary of the gaps in literature. Section 3 provides a conceptual description of the problem and is followed by mathematical formulation in Sect. 4 and an illustrative example in Sect. 5. Finally, the results are discussed in Sect. 6, and the conclusions, prospects for future research, and limitations of the study are presented in Sects. 7, 8, and 9, respectively.
2 Literature review
2.1 Cold chain storage requirement and coordination concerns
Cold chain creates customer value by merging logistics activities related to perishable products with prevalent business processes (Shih and Wang 2016). Cold supply chains require storage and transportation of associated products in temperatures approximately equal to or less than their freezing points; this places emphasis on appropriate temperature settings in refrigerated warehouses and trucks to fulfill the needs of the customers. Refrigerant energy leakage is proportional to the cooling capacity of the system. In conventional supply chains, the warehouse capacity is dependent on throughput (demand rate) and actual stock-keeping capacity. However, the operating cost for cold storage increases drastically with the addition of a refrigeration system; this means that warehouse capacity is influenced by demand pattern, inventory policy, and customer service requirements as well as actual physical capacity (Saif and Elhedhli 2016). Consideration of customer service requirement is driven by the shelf life of products: acceptable safety and quality levels should be maintained when the products reach the customer.
The quality of food products is dependent on the temperature, time, and atmosphere of storage, all of which affect-depending on the sensitivity of the product to time and temperature-the degree of deterioration of products. The average storage time at distribution centers depends upon the batch size of transfer between producers and distributors, which influences variable cost, whereas fixed cost depends on the set-up costs for cooling and treatment units (Zanoni and Zavanella 2012).
Consolidation in storage for durable products is mostly influenced by external features such as shape, size, weight, and volume of the products. The ability to share the same storage space depends on compatibility in terms of the modular design of products, which differs between perishable and durable products. Different holding temperature requirements restrict the combining of cold items for shipment and storage. Clustering of cold items, such as dairy products (milk and chocolate milk) can be facilitated by enabling sharing of storage and transportation capacity to fulfill the demand requirements (Bozorgi 2016).
Speed, reliability, and specialized transportation and storage units impose additional requirements on a food supply chain. Modern food chains entail multiple products with multiple temperature requirements, defying the notion of “one size fits all.” Food contamination depends on external factors (humidity, temperature) and internal factors (microbial contamination and composition) as well as the duration of exposure to these conditions (Thakur and Forås 2015).
Chen et al. (2016) identified that uncertain factors, such as weather, temperature, and customer preferences, influence the demand for agriculture products. China, with its decentralized and complex agriculture configuration, requires an organized farming structure, such as the facility agricultural supply chain prevalent in Eastern China. The operation of organized farming is structured to allow supermarkets to order from the facility agricultural enterprises according to the demand. This further enables the development of a plan for upstream farm producers through adequate coordination. In China, shortages of third-party logistics (3PL) warehousing for cold chains are because of the following reasons: (i) low capacity and low space utilization rate, (ii) low utilization rate per year due to seasonality of the products, (iii) difficulties in guaranteeing product quality, and (iv) low operational efficiency due to manual entry and untimely updates (Zhang et al. 2012).
Dissimilar products should have different types of service levels. Warehouse locations for frozen products may be located closer to either the harvest (or production) center or the market. Temperature control ensures food product quality and safety. On the basis of temperature control, food products can be classified as frozen (lower than \(-18\,{^{\circ }}\)C), ambient (room temperature), and chilled (\(0-15\,{^{\circ }}\)C) products, with further diversification or clustering (Fredriksson and Liljestrand 2015). Frozen food stores in Germany are classified as follows: (1) plant cold stores (number [n] = approximately 20, temperature [T] \(< -20\,{^{\circ }}\)C); (2) central cold stores (n = approximately 80, T \(< -24\,{^{\circ }}\)C); distribution cold stores (n = approximately 200, T \(< -20\,{^{\circ }}\)C); freezing cabinets in retail (n = approximately \(2 \times 105\), T = approximately \(-18\,{^{\circ }}\)C). The British Frozen Food Federation has differentiated primary cold stores for frozen foods as those with temperatures ranging between \(-20\) and \(-28\,{^{\circ }}\)C, with the ability to reduce the temperature to \(-18\,{^{\circ }}\)C and with a tolerance of \(3\,{^{\circ }}\)C in primary distribution. The American Society of Heating, Refrigerating and Air-Conditioning Engineers require temperatures for frozen food storage to be between \(-23\) and \(-29\,{^{\circ }}\)C, whereas the Italian Frozen Food Institute guidelines suggest a maximum storage temperature of \(-22\,{^{\circ }}\)C (Arduino et al. 2015). The difference in temperature requirements for different countries, stages, and measuring units of temperature increases complexity in coordination because of the presence of multiple actors and potential for misinterpretation of information.
Producers and farmers face greater risks and lower margins primarily because of a low level of consolidation. This has resulted in higher bargaining power possessed by a small number of retailers in fresh fruits and vegetables supply chains. Farmers are seeking measures to grow either individually or in associated groups or cooperatives to benefit from high levels of consolidation. The integration needs to be complemented by simultaneous collaboration with downstream partners. Planning of production associated with farmers is influenced by external factors related to demand forecasting as well as by internal factors that pertain to the distribution of demand among associated members. The cooperative structure is not effective because of asymmetric information and decentralized control, which are primarily attributed to farmers’ reluctance to share cost structures and expected outputs (Mason and Villalobos 2015).
2.2 Location-allocation problem
Location problems can be depicted on a graph network with nodes (location) and arcs (distance between locations). Locations on networks are differentiated as either tree-like structures or with cycles (Tansel et al. 1983). The tree-like structures are utilized when cycles are expensive, for example, to depict interstate highways. The functions of distance for tree-like structures functions are often convex, whereas those for cyclic networks are non-convex. In Daskin et al. (1992), determination of planning horizon for the first period decision served as an efficient tool for the dynamic uncapacitated fixed-charge location problem.
Facility location problems are of two types: number of facility locations, which is a p-median problem, and service levels (based on distance), which is set covering problem. Other types of problems are formulated by combining these aspects with additional criteria. Owen and Daskin (1998) reviewed decision making methods for facility location problems, including p-median, set covering, and p-center problems, and established that the robustness of a facility location model depends on uncertain future events and changes in the state of the system. Long-term planning characterizes the complexity and importance of facility location as it involves high initial investment and uncertainty. Substantial reduction in computational time was achieved in solving such complex problems by sequential arrangement of inherent quality. Inventory costs at distribution centers and economies of scale associated with transportation cost are expected to help in solving the facility location problem (Daskin et al. 2002). Ghaderi and Jabalameli (2013) provided a solution for the longitudinal uncapacitated facility location-network design problem with budget constraints for opening the facility and creating links during each period of planning horizon and demonstrated the practical feasibility of the proposed approach by applying it to health care facilities in Iran.
Warehouse site selection is a strategic decision with high initial investment and requires a process that integrates both tangible and intangible criteria into the decision-making process. The analytical hierarchical process (AHP), which is used to link corporate objectives with site selection criteria in the form of hierarchical relationships, facilitates the prioritization of warehouse sites (decision alternatives) (Korpela and Tuominen 1996). Fischer (2002) modeled duopolistic location planning with variable locations and prices to reach an equilibrium price and a sequential problem with the leader assessing the actions of the follower to make pricing decisions. The effect of knowledge spillovers on location choice for new entrants in the United States from 1985 to 1994 revealed that firms tend to align physically with locations of high academic innovation while also considering the impact of outward knowledge spillovers. Technological factors are also attributed to the selection of location sites: less technologically advanced regions emphasize industrial innovative regions and more technologically advanced regions avoid such regions to reduce outward spillover to competitors (Alcácer and Chung 2007). The function for weightage of demand point with time enabled the identification of optimal locations, relocation times, and total cost (Farahani et al. 2009). Avella et al. (2012) performed a clustering analysis wherein p facilities (medians) were located by minimizing the sum of distances from each facility to the nearest facility. Clustering involves grouping a set of similar patterns into clusters to reduce the size of the problem and further solving each cluster as a p-median problem. The material location–allocation problem in dual warehouses for allocating material quantity between owned warehouses and those rented from 3PL would be beneficial when the storage capacity constraint of manufacturer’s warehouse requires renting a 3PL warehouse, which incurs storage rental and transportation costs and excludes the initial investment for the site (Wutthisirisart et al. 2015). Drexl and Schneider (2015) highlighted using planar locations, instead of any location on plane, to eliminate the problem of forbidden regions. The authors also emphasized the need for integrating other logistical factors with the problem to apply a more holistic approach.
2.3 Analyzing real-time data in the cold chain perspective
Tracking technologies vary from paper-based entry to computer-based information technologies and highly sophisticated biological technologies. Qualitative traceability involves the ability to trace the physical flow along with additional information on ingredients, quantity, supplier, producer, and the linkage among them. Moreover, identifying the source of contamination and assessment of variance in quality is helpful. Most food products are treated as commodities that can be easily substituted, thereby complicating the tracing process (Turi et al. 2014).
Wang et al. (2015) emphasized the development of real-time environment monitoring to maintain the safety and quality of perishable food products. Transportation and storage conditions, such as the state of motion of the transporting vehicle, vibrations, unexpected fall, loading, unloading, and power management in non-joined status, are critical factors affecting value added attributes of food products. Although installed thermometers and humidity sensors capture the macroscopic environment in warehouses and vehicles, they fail to provide continuous and microscopic information. The categories and their respective information attribute characteristics in a food supply chain are as follows: (i) environmental conditions: temperature, humidity, and carbon dioxide concentration; (ii) state of motion: abnormal vibration, unexpected fall, excessive tilt, and illegal opening; (iii) location: geographical positioning system (GPS) and (iv) network status: voltage network topology.
Various studies have employed databases and online application of temperature monitoring through the application of temperature monitoring technologies. Thakur and Forås (2015) developed an approach for online temperature monitoring and traceability in a cold chain. Electronic Product Code Information Services (EPCIS), a web-based temperature monitoring system, was deployed during various phases of product flow for monitoring temperature and tracking. Gogou et al. (2015) developed a cold chain database (CCD) tool to manage and evaluate food products. The tool estimated the product shelf life on the basis of existing or user-defined kinetic data. Grunow and Piramuthu (2013) estimated the remaining product shelf life using radio frequency identification (RFID) for waste reduction. Applicability of RFID use among retailers, distributors, and customers was compared with barcode using return on investment as a (ROI) measure. Derens-Bertheau et al. (2015) used the real-time-temperature profile of a Frisbee field test to measure the time–temperature performance of chilled food.
2.4 Summary of research gaps
An analysis of the literature provided the following insights into the unexplored area of the location–allocation problem in cold chain configuration, which requires development to preserve value by ensuring acceptable shelf life quality (Wang and Shih 2016) and emphasizing specific storage requirements (Saif and Elhedhli 2016; Zanoni and Zavanella 2012): First, the necessity to characterize cold chain service requirement on the basis of the product level (Fredriksson and Liljestrand 2015) with emphasis on addition of touch points to avoid wastage and uninterrupted supply; second, the misinterpretation of information, because of different temperature requirements at various stages (Arduino et al. 2015), and asymmetric information and decentralized control (Mason and Villalobos 2015) require coordination with an initiative originating from mature downstream members; finally, the necessity to monitor the temperature-time relationship requires the sophisticated use of technology to ensure safety and quality of products. However, most studies (Wang et al. 2015; Thakur and Forås 2015; Gogou et al. 2015; Grunow and Piramuthu 2013; Derens-Bertheau et al. 2015 have been conducted at an operational level and not at a planning level. The incorporation of perishability and deterioration at the planning stage would facilitate the design of a robust system and form a suitable framework for incorporating such technologies.
The accumulation of extensive quantum diverse datasets in an analytics environment requires decision makers to devise a mechanism for integrating the two aspects in the evaluation of alternatives. Hazen et al. (2016) suggested the need to bridge the gap between operations research/supply chain management and big data analytics by synergizing decision-making with quantitative results, transitioning to business analytics, enhancing data quality, diversifying team structure, and defining a structured plan for alternative selection. Recent research on big data sets in the operations management domain includes the studies by Wang et al. (2016) which focused on developing a capacitated network design to locate distribution centers for scattered demand points and Tail and Singh (2016) which focused on the facility layout problem. Aloysius et al. (2016) investigated the role of technology enablers and privacy inhibitors in big data customer transactions in the realization of competitive advantage by retailers. The role of decision-making is altered with the advent of big data, and reading relevant information is an asset that is expected to assist in achieving the appropriate results for gaining a competitive advantage.
The location–allocation problem is a long-range decision problem with high initial investment (Owen and Daskin 1998); the addition of product-related aspects (Wutthisirisart et al. 2015) in site selection and allocation requires more attention. Few studies (e.g., Ghaderi and Jabalameli 2013) have used period data to investigate location–allocation problems under different environments, thereby complicating the use of such data in cold chain configuration with a longitudinal product characteristic (shelf life). The use of a seed or potential locations as input parameters in the model is expected to not only lead to more practical results by avoiding the possible selection of forbidden locations (Drexl and Schneider 2015) but also to simplify the modeling of such problems. The attributes of cold chain storage requirements and coordination aspects are illustrated in Tables 1 and 2, respectively.
Given the gaps in the literature, the current study addresses the following concerns for the location–allocation problem in cold chain configuration:
-
(a)
Incorporation of perishable product attributes (shelf life, age-based value, or opportunity cost)
-
(b)
Heterogeneous product-service requirements by different customers
-
(c)
Use of big data in incorporating practical parameters
-
(d)
Coordination to reduce complexity due to fragmentation
3 Problem description
The location–allocation problem in cold chain configuration requires the consideration of inherent product attributes, such as transient shelf life, storage time at warehouse, and time-dependent product value. Traditional location–allocation problems have focused specifically on locations with aggregate weight to minimize the total weighted average distance, which is subject to demand satisfaction. Product characteristic is a crucial characteristic for location allocation in cold chains. In this study, we consider a heterogeneous group of customers. Each customer only manages products that are in a certain stage of the product life cycle, which is referred to as ESL.
The objective of the problem is to identify location(s) on the basis of customer requirements to meet product demands. Traditional location–allocation problems use location points on a two dimensional plane and evaluate them numerically to identify these locations. Drexl and Schneider (2015) suggested that potential locations, instead of locations on the plane, be used to avoid the problem of forbidden locations. For example, the potential search outcome from location allocation may result in an isolated location with inadequate infrastructure and other capabilities. Therefore, understanding the importance of these locations is imperative because they involve high initial investment and long-term benefits. The existing warehouse(s) along with a set of seed locations are the potential locations in the model. Furthermore, prospective potential locations along with existing warehouse(s) are chosen in sufficient numbers and are densely scattered along the demand grid. We use big data, which actually transforms textual data into sensible information, for distance calculation to include shelf life in the problem; detailed descriptions are provided in Sects. 3.1 and 3.2.
3.1 Haversine formula for distance calculation
Sinnott (1984) devised the Haversine formula to calculate the distance between two locations on the basis of latitude and longitude. The use of Euclidean distance, which is based on point-to-point straight-line distance, provides the shortest distance between two locations. However, the Haversine formula considers the spherical shape of the earth for a more realistic distance calculation. The distance Dist\(_\mathrm{AB}\) between two points A and B using the Haversine formula is defined as follows in Eq. (1):
where \(\hbox {X}_{a}\) and \(\hbox {X}_{b}\) are latitudes and \(\hbox {Y}_{a}\) and \(\hbox {Y}_{b}\) are longitudes for A and B, respectively. R is the radius of earth in kilometers (km), approximated as 6371 km. We converted latitude and longitude units from degrees to radians by multiplying the radians terms by (\(\pi /180\)). The use of latitude and longitude for locations enabled in calculating distance without employing the use of distance engines with reasonable accuracy compared to actual road distance. It offered considerable benefit over straight-line distance and adequate approximation of actual road distance.
Customer service requirement for a product in terms of ESL is translated into a service distance requirement. The identification of many potential location sites requires determination of distance matrix from each warehouse to each customer. For instance, with “m” customers and “n” potential locations, the input requirement would be an m*n distance matrix from each potential location to each customer. Determining actual road distance from an open search engine, such as Google, would require considerable time and effort to retrieve sensible information from smaller areas. For example, a smaller area with 10 locations and 20 customers would have 200 possible combinations. In addition, Google has a per day data retrieval limitation: 2500 times per customer (Google Maps API 2016). Hence, the use of big data approximation, such as the Haversine formula, will substantially reduce the effort to transform the distance information from a small combination of (m + n) customers and warehouse locations.
3.2 Incorporating shelf life in the problem
Perishability of products can be classified in terms of using the product at the right time without considering deterioration, such as previous year’s calendar, and the deterioration of the product (such as fruits, vegetables, and medicines) with respect to time (Coelho and Laporte 2014). Our model addresses the second category, namely deterioration of product value with respect to time or before the expiry date. The inability to use the product within the shelf life results in wastage of the product. Therefore, to reduce the wastage of perishable products, researchers and practitioners worldwide should address the issue at a strategic or design level. The location–allocation process typically begins with the identification of location(s); the selection of location depends on the product of total weighted distance and aggregate demand. The concern of similar and different products perishability along with heterogeneous shelf life is considered in the location–allocation problem. Our model is applicable at a strategic level and is expected to aid in future location selection.
Our model derives the time dimension from four sources, such as distance, average speed of the vehicle, shelf life, and ESL. We assume that the shelf life of a product includes three phases: storage time at the warehouse (or location), transit time, and ESL requirement for customer, as demonstrated in Fig. 1. The service distance is calculated using Eq. (2). The allocation of customer and product to a particular location is competed on the basis of the comparison between actual and service distance and is expected to be less than or equal to service distance. The difference between shelf life and ESL provides the maximum available time for transportation, which is used as service distance requirement in the problem.
For example, consider a product “A” with a shelf life of “T” time units reaching storage location at time “t”. The location–allocation problem is based on the remaining time (T–t) for product A. Product A is required by a heterogeneous group of customers with different remaining shelf life requirement (ESL) according to order frequency and proximity from the PoU and different product values according to market price. The market price versus remaining shelf life requirement (ESL) for product A for different customers is shown in Fig. 2.
Shelf life is the marketable life of a product and may not necessarily represent the deterioration rate of the product (Wang et al. 2009). Product value is different from market price because it captures the deterioration effect with respect to increase in time. The rate of product value deterioration depends on the controlled environment that the product is stored in. The linear relationship assumption between deterioration and time for products with a shelf life of 5 period units deteriorate at a rate of US$10 per period is shown in Fig. 3. The aforementioned factor is considered in the model as opportunity cost that includes the combined effect of ESL and opportunity cost factor per period. Figure 2 shows that product value depends on market price. The model can be used to determine the optimal bundling of products on the basis of the cost function. In other words, considering opportunity cost prioritizes cumulative product value for customers to identify relative worth of fulfilling versus not fulfilling the demand. The preceding scenario is applicable when the capacities of potential warehouses that provide the product to the customer are less than the demand for the product.
3.3 Assumptions
Cold chain location–allocation problem is formulated on the basis of the following set of assumptions:
-
(i)
Transportation cost is directly proportional to the distance. Similarly, aggregate demand and FTL deliveries tariff charge is directly proportional to the distance.
-
(ii)
All locations, inclusive of potential warehouses and customer points, are located within a bounded habitual region. This is to satisfy the land transportation mode.
-
(iii)
The shelf life for a product denotes the duration of time left for the product after it reaches the storage location (fixed in this case) by incorporating time spent in upstream operations. Thus, the product always reaches with the same shelf life at the storage location.
-
(iv)
The product value decreases linearly with time because of deterioration.
-
(v)
Products are constantly available in cold storage for instant allocation.
4 Mathematical formulations
The cold chain location–allocation configuration is formulated as a mixed integer linear programming (MILP) problem for location selection and allocation of products based on customer service requirements with warehouse storage capacity constraints. The inclusion of ESL and service requirements allows coordination between warehouse and customer points. Tables 3, 4, 5, and 6 depict indices, set of entities, input parameters, and decision variables used in the model, respectively.
Equations (3) and (4) calculate service distance requirement and actual distance, as illustrated in Sects. 3.1 and 3.2. Equation (5) indicates service level parameter \(\theta _{jip}\) for serving a customer when actual distance is less than or equal to service distance requirement. Equation (6) evaluates energy consumption on the basis of the duration of a product at the warehouse. From Sect. 3.2, we can calculate storage time at the warehouse by deducting ESL and transit time from shelf life. Equation (7) is the big value for each customer and is estimated as the maximum value among all other cost components apart from opportunity cost to derive an appreciably higher value in the objective function. Equation (8) is aggregate opportunity cost for a product unsold with remaining ESL. It uses the BigM factor to calculate the opportunity cost for not meeting the demand. However, when the warehouse capacity under the service requirement is limited, this coefficient determines the least costly product bundling given the capacity constraints. Perishable products are valued on the basis of age and opportunity cost, which denotes the loss incurred for not selling a particular valued product (Assumption iv in Sect. 3.3). The derived parameters in Eqs. (3)–(8) represent approximation of big data used in the model.
The location–allocation MILP problem is formulated with the objective of minimizing transportation cost (weighted distance), opportunity cost (unmet demand), cost incurred in consumption of energy, fixed cost for opening a new warehouse, and cost incurred for closing an existing warehouse. The objective function for the problem is presented the Eq. (9).
Minimize:
subject to
\(ShipQty_{jip}\) and \(UnmetDem_{ip}\) decision variables may be either continuous or discrete (float or integer), depending on the type of the product illustrated by parameter \(ProdTyp_{p}\). The model ensures allocated quantity flow between warehouse and customer point depending on the product type. Hence, although all types of products are incorporated, allocation is based on product type.
Constraint (10) imposes restriction on the allocation of a product to a customer point from among maximum number of open warehouses. Constraint (11) imposes a restriction on customer points served by open warehouses when the actual distance is less than or equal to the service distance constraint. Constraint (12) imposes the same restriction on quantity dispatched from open warehouses to a customer point to be less than or equal to the demand for the product. The aforementioned two constraints are related to perishability, ensuring that the customer point receives the product at acceptable quality (i.e., within the ESL), thus enabling coordination between the warehouse and customer point.
Constraint (13) ensures that the warehouse storage capacity is within the upper bound capacity. Different products might have different units of measurement (UoM) and are therefore multiplied by the UoM factor for converting all units into kilogram (kg). Constraint (14) is the demand-balance equality. Constraint (15) identifies the existing warehouses that are closed. The objective function includes the demand fulfillment cost (transportation cost), unmet demand cost (opportunity cost), energy cost, and fixed cost for opening and closing the warehouse. Because the value of opportunity cost is relatively lesser in magnitude when compared with the other costs, the model optimizes by not meeting the demand because the cost of meeting demand exceeds that of the unmet demand. Constraints (16)–(20) represent various cost components that are used for minimizing total cost in the objective function. The bounds for decision variables are stratified by type in Table 6.
5 An illustrative example
A hypothetical location–allocation problem is illustrated using real-time geographical coordinates of locations in the Zhejiang and Jiangsi provinces in China. The current configuration comprises an existing cold storage warehouse serving as a major customer point. The increase in both magnitude and number of customer points along with storage facility capacity constraint results in more wastage and loss of sales. In addition to the existing warehouse, a set of nine warehouse sites, evenly distributed across the region, is considered as potential locations for establishing storage facilities. Location information with latitude and longitude are depicted in Table 7. The geographical distribution of locations is presented in Fig. 4. The product information in Table 8 describes whether a product is continuous or discrete; the UoM, a factor for converting demand into kg and shelf life into hours; and energy consumed per hour. The shelf life denotes the time left for the product after it reaches the storage location. Tables 9 and 10 denote the demand and warehouse data. The average speed of the transport vehicle is assumed to be 50 km/h.
6 Results and discussions
6.1 Computational result
The location–allocation MILP problem is solved using the IBM concert technology on C#.Net platform using a library from CPLEX 12.5 solver. The computations are executed on a system equipped with 4GB RAM, and input data is read from the MS Access database. Results of the allocation of demand quantity to a warehouse are depicted and summarized in Table 11. The results suggest that when warehouses WH1, WH3, and WH6 were opened in addition to the existing warehouse (WH4), the total cost incurred was US$2,887,489, with fixed cost component contributing 95 % to the value of $2,743,000. The transportation cost measured as weighted average amounted to $144,465, but it might substantially vary from the actual transportation cost depending on factors such as shipping schedule, tariffs, and load.
6.2 Managerial implications
6.2.1 Operational constraint for small shipments
The solution reveals that a small proportion of demand for product P1 allocated to customer point C1 was divided between WH1 and WH6, primarily because of the total cost reduction. The crucial point to be considered in this situation is assessing the operational complexity of coordination for such small shipments with multiple storage locations. The consideration of product compatibility during storage and transportation should be considered further to evaluate the possibility of combining P1 and P2 for C1 from these locations, which might offset the disadvantage of small loads. If such combining is not possible, then the evaluation of opportunity cost allows for eliminating the product with a lesser value. The absolute cost magnitude might not reveal the actual situation, but a relative comparison of cost structures is an adequate indicator for such analysis involving site selection.
6.2.2 Multiple sourcing and warehouse capacity planning
Figure 5 provides insights into warehouse site selection, mapping of customer with warehouse, and distance coverage for each warehouse (maximum service distance). Customer point C1 was served by warehouses WH1, WH4, and WH6, with different distances for two products P1 and P2. Although product P1 was served from the nearest warehouse (WH4), product P2 was served by the three warehouses, with the majority of demand allocated to the highly distant warehouse (WH6). Therefore, several aspects should be considered during allocation and warehouse capacity planning.
The model utilizes constraints on capacity for warehouse and service distance of product in allocating demand to multiple warehouses. Both products P1 and P2, having different storage requirements, were sourced from three warehouses, and the decision makers had to consider the allocation of storage capacity for these products to ensure operational feasibility.
The initial fixed cost related to land and equipment was an approximation and decision makers had to further evaluate deployment of storage equipment type with its capacity.
Warehouses close to customers fully used their capacity compared with the distant warehouses having ineffective capacity utilization (Fig. 6). This aspect provides valuable insights regarding the amount of investment for land area on the basis of capacity. Because closer warehouses (WH1 and WH4) are fully utilized, evaluating the possibility of leasing or buying more land space at those locations must be considered. Similarly, the prospect of reducing capacity for distant warehouses (WH3 and WH6) must be evaluated. Because demand volumes are predicted by considering the growth in future requirements, utilizing unwanted buffer may not be necessary. Storage capacity should be maintained at a higher utilization rate (approximately 75–80 %) for distant warehouses. Intuitively, maintaining greater capacity at near locations, particularly for perishable products, is reasonable.
A major aspect of allocation and capacity decision-making is identifying storage allocation for different products. The demand for product P2 was uniform across regions, whereas that for products P3 and P1 was higher in the north and east region, respectively, based on warehouse locations (Fig. 7). The market distribution of products across geography will further aid in determining the capacity for storage equipment.
The aforementioned aspects, particularly relating to the capacity utilization for selected warehouses and product category distribution across regions, are expected to refine the decisions in the allocation of storage capacity for different equipment. The decisions must consider the technology aspect of storage and the possibility of product consolidation.
6.2.3 Product allocation under limited capacity
Various opportunity costs are associated with different products. To understand the effect of opportunity cost, we must consider the capacity limitations; namely, if the same capacity is to be allocated among two product categories, then the demand has to be met by fulfilling the product that has a higher opportunity cost. Therefore, we modified the inputs in our problem by introducing the demand for products P1 and P2 for customer C2 with 200 units each, with the ESL of 8 and 4 time units and opportunity cost per period per unit as US$1.7 and US$1.2, respectively. Furthermore, warehouse WH2 was removed and the capacity of WH1 was reduced to 400 kg. Thus, we had customer C2 with a demand for all three products P1, P2, and P3 and only one prospective warehouse to serve the demand. The model was run with modified input parameters to understand the effect of opportunity cost under capacity limitations. The results revealed that the demand of product P3 for customer C2 was not satisfied because it had least opportunity cost per unit among the three products.
The practical implication of the preceding illustration is relevant when the potential sites offer limited capacity and the appropriate bundling of products to be allocated is determined with minimal loss of opportunity cost. Although the role of transportation cost is questioned at this instance, because we primarily focus on perishability and have allocated an extremely high penalty for not meeting the demand, compared with that for not meeting the other costs, the effect of opportunity cost is evident only among the product.
7 Conclusions
The location–allocation problem for perishable products in a cold chain configuration warrants focus on specific attributes, such as shelf life, physical demand locations, and units of product transportation, while emphasizing the need for safety and quality of products. The study contributes to the location–allocation literature by including an additional dimension of perishability. Location–allocation studies have modeled durable products using customer service requirements. This study is formulated a MILP problem with the aim of minimizing transaction costs in occupying new resources (warehouses) or discarding of existing resources (existing warehouse) with coordination between the entities (in the form of shelf life). The study incorporated big data as a substitute to real data, the retrieval of which might require more effort and time. Various big data approximations, such as the Haversine formula to calculate distance between two locations, service level computation, storage time, and consideration for deterioration of value (opportunity cost), are used in the model. Previous studies on perishable products have primarily focused on inventory and planning problems with longitudinal data. The existing location–allocation solutions for the identification of the most suitable location site have been based on Greenfield analysis and aggregate demand. The current study attempts to combine the location–allocation of perishable products for heterogeneous demand customers with varied requirements. The common goal of demand satisfaction, in addition to quality and safety requirements, requires institutional innovation between members to ensure fulfillment. The study applies a logical location–allocation system for cold chain configuration. The cold chain configuration model can help managers to identify prospective alternatives (location sites) from among a set of potential locations in appreciable time with big data approximations and cold chain characteristics for rapid and reliable results.
8 Future research directions
The location–allocation problem provides an alternative solution for the selection of location site from among a set of prospective locations and allocation between customer points. The result provides an efficient solution by considering capacity, deterioration, and shelf life (customer service requirement), which are typical characteristics of a cold chain. The study addresses the unexplored gap in cold chain and location–allocation literature by incorporating practical aspects with aid of real location data. However, the study is built on certain assumptions, which must be considered during its application. The problem provides a directional result that requires additional evaluations with alternate analysis at tactical and operational levels. The transportation cost evaluated at a flat level can become more evident if there is an estimation of cost function with distance based on road infrastructure, logistic service providers (LSPs) accessibility, tariffs, and other factors. Another area that can increase the robustness of the model is the identification of the deterioration rate function for different products under a controlled environment. This will enable in evaluating value on the basis of age, opportunity cost of lost sales, and waste. Multiple touch points, rather than a single touch point, can be introduced to allocate demand for widely scattered customers at remote locations. Testing the model and its variants using large datasets and various instances, with a focus on reduction of the computational effort and identification of ill conditioning, is also a major prospect for future studies.
9 Limitations of study
The preceding discussions have highlighted the boundaries of cold chain location–allocation problem. The location–allocation model is widely considered a strategic decision problem and can be extended to understand tactical- and operational-level decisions. The result is a directional indication of the prospective locations and must be verified with other operational costs related to transportation and inventory. The transportation cost is calculated on the basis of high level assumptions of positive linear dependency with distance, without applying differential tariff rates. However, in practical situations, the tariffs are charged on the basis of weight bracket for shipment of less than truck load (LTL) and as a flat tariff for FTLs. The cold chain location–allocation problem does not consider the frequency of shipments, differential rate structures based on route, and storage aspects. Therefore, location–allocation must be used in conjugation with other tactical approaches in choosing relevant alternatives from among a set of decision alternatives. Moreover, the perishability of products in a controlled environment may not be linear, and the determination of deterioration rate would provide a more accurate insight into the fulfillment of service level.
References
Alcácer, J., & Chung, W. (2007). Location strategies and knowledge spillovers. Management Science, 53(5), 760–776.
Aloysius, J. A., Hoehle, H., Goodarzi, S., & Venkatesh, V. (2016). Big data initiatives in retail environments: Linking service process perceptions to shopping outcomes. Annals of Operations Research,. doi:10.1007/s10479-016-2276-3.
Arduino, G., Murillo, D. C., & Parola, F. (2015). Refrigerated container versus bulk: Evidence from the banana cold chain. Maritime Policy and Management, 42(3), 228–245.
Avella, P., Boccia, M., Salerno, S., & Vasilyev, I. (2012). An aggregation heuristic for large scale p-median problem. Computers and Operations Research, 39, 1625–1632.
Bai, R., & Kendall, G. (2008). A model for fresh produce shelf space allocation and inventory management with freshness condition dependent demand. INFORMS Journal on Computing, 20(1), 78–85.
Bozorgi, A. (2016). Multi-product inventory model for cold items with cost and emission consideration. International Journal of Production Economics, 176, 123–142.
Chen, W., Li, J., & Jin, X. (2016). The replenishment policy of agri-products with stochastic demand in integrated agricultural supply chains. Expert Systems with Applications, 48, 55–66.
Coelho, C. L., & Laporte, G. (2014). Optimal joint replenishment, delivery and inventory management policies for perishable products. Computers and Operations Research, 47, 42–52.
Daskin, M. S., Coullard, C., & Shen, Z. J. M. (2002). An inventory-location model: Formulation, solution algorithm and computational results. Annals of Operations Research, 110, 83–106.
Daskin, M. S., Hopp, W. J., & Medina, B. (1992). Forecast horizons and dynamic facility location planning. Annals of Operations Research, 40, 125–141.
Derens-Bertheau, E., Osswald, V., Laguerre, O., & Alvarez, G. (2015). Cold chain of chilled food in France. International Journal of Refrigeration, 52, 161–167.
Dodd, M.C., & Bouwer, J.J. (2014). The supply value chain of fresh produce from field to home: Refrigeration and other supporting technologies. In Postharvest handling, 3rd Ed., A systems approach, pp. 449–483.
Drexl, M., & Schneider, M. (2015). A survey of variants and extensions of the location-routing problem. European Journal of Operational Research, 241(2), 283–308.
Farahani, R. Z., Drezner, Z., & Asgari, N. (2009). Single facility location and relocation problem with time dependent weights and discrete planning horizon. Annals of Operations Research, 167, 353–368.
Fischer, K. (2002). Sequential discrete p-facility models for competitive location planning. Annals of Operations Research, 111, 253–270.
Fredriksson, A., & Liljestrand, K. (2015). Capturing food logistics: A literature review and research agenda. International Journal of Logistics Research and Applications, 18(1), 16–34.
Ghaderi, A., & Jabalameli, M. S. (2013). Modeling the budget-constrained dynamic uncapacitated facility location-network design problem and solving it via two efficient heuristics: A case study of health care. Mathematical and Computer Modelling, 57(3–4), 382–400.
Gogou, E., Katsaros, G., Derens, E., Alvarez, G., & Taoukis, P. S. (2015). Cold chain database development and application as a tool for the cold chain management and food quality evaluation. International Journal of Refrigeration, 52, 109–121.
Google Maps API. (2016). https://developers.google.com/maps/documentation/geocoding/usage-limits.
Grunow, M., & Piramuthu, S. (2013). RFID in highly perishable food supply chains—Remaining shelf life to supplant expiry date? International Journal of Production Economics, 146(2), 717–727.
Hazen, B. T., Skipper, J. B., Boone, C. A., & Hill, R. R. (2016). Back in business: operations research in support of big data analytics for operations and supply chain management. Annals of Operations Research,. doi:10.1007/s10479-016-2226-0.
Korpela, J., & Tuominen, M. (1996). A decision aid in warehouse site selection. International Journal of Production Economics, 45(1–3), 169–180.
Mason, A. N., & Villalobos, J. R. (2015). Coordination of perishable crop production using auction mechanisms. Agricultural Systems, 138, 18–30.
Meneghetti, A., & Monti, L. (2015). Greening the food supply chain: An optimisation model for sustainable design of refrigerated automated warehouses. International Journal of Production Research, 53(21), 6567–6587.
Owen, S. H., & Daskin, M. S. (1998). Strategic facility location: A review. European Journal of Operational Research, 111(3), 423–447.
Saif, A., & Elhedhli, S. (2016). Cold supply chain design with environmental considerations: A simulation-optimization approach. European Journal of Operational Research, 251(1), 274–287.
Shih, C. W., & Wang, C. H. (2016). Integrating wireless sensor networks with statistical quality control to develop a cold chain system in food industries. Computer Standards and Interfaces, 45, 62–78.
Sinnott, R. W. (1984). Virtues of the Haversine. Sky and Telescope, 68(2), 159.
Tansel, B. C., Francis, R. L., & Lowe, T. J. (1983). State of the art-location on networks: A survey. Part I: The p-center and p-median problems. Management Science, 29(4), 482–497.
Tayal, A., & Singh, S. P. (2016). Integrating big data analytic and hybrid firefly-chaotic simulated annealing approach for facility layout problem. Annals of Operations Research,. doi:10.1007/s10479-016-2237-x.
Thakur, M., & Forås, E. (2015). EPCIS based online temperature monitoring and traceability in a cold meat chain. Computers and Electronics in Agriculture, 117, 22–30.
Turi, A., Goncalves, G., & Mocan, M. (2014). Challenges and competitiveness indicators for the sustainable development of the supply chain in food industry. Procedia— Social and Behavioral Sciences, 124, 133–141.
Wang, G., Gunasekaran, A., & Ngai, E. W. T. (2016). Distribution network design with big data: model and analysis. Annals of Operations Research,. doi:10.1007/s10479-016-2263-8.
Wang, J., Wang, H., He, J., Li, L., Shen, M., Tan, X., et al. (2015). Wireless sensor network for real-time perishable food supply chain management. Computers and Electronics in Agriculture, 110, 196–207.
Wang, X., Li, D., & O’Brien, C. (2009). Optimisation of traceability and operations planning: An integrated model for perishable food production. International Journal of Production Research, 47(11), 2865–2886.
Wutthisirisart, P., Sir, M. Y., & Noble, J. S. (2015). The two-warehouse material location selection problem. International Journal of Production Economics, 170(C), 780–789.
Zanoni, S., & Zavanella, L. (2012). Chilled or frozen? Decision strategies for sustainable food supply chains. International Journal of Production Economics, 140(2), 731–736.
Zhang, Z., Zhang, K. & Song, B. (2012). The information construction of third-party warehousing in the cold chain logistics. In LISS 2012: Proceedings of 2nd International Conference on Logistics, Informatics and Service Science.
Acknowledgments
The authors acknowledge the support from National Natural Science Foundation of China (Grant No. 71471092), Ningbo Science and Technology Bureau (2014A35006) and the International Academy for Marine Economy and Technology (IAMET) for funding this research.
Author information
Authors and Affiliations
Corresponding author
Rights and permissions
About this article
Cite this article
Singh, A.K., Subramanian, N., Pawar, K.S. et al. Cold chain configuration design: location-allocation decision-making using coordination, value deterioration, and big data approximation. Ann Oper Res 270, 433–457 (2018). https://doi.org/10.1007/s10479-016-2332-z
Published:
Issue Date:
DOI: https://doi.org/10.1007/s10479-016-2332-z