Abstract
The market interest in ornamental rocks commercially referred to as “stones” has grown significantly in recent years, particularly regarding basalt. This has resulted in the widespread use of diamond wire equipped with sintered diamond beads for precision sawing in basalt quarries, especially those located in the industrialized countries; it also has the advantage of preventing rock damages. Diamond wire has been widely used in up-line cutting and other sawing works in both marble and granite quarries for decades; therefore, performance data about the use of this tool on these two different types of rocks are widely documented in academic literature. However, for basalt sawing, information pertaining to the use of diamond wire is unavailable due to various reasons, but mostly because of to its relatively recent introduction in the basalt quarries and also to the historical low market demand for processed basalt in the past. This study offers a possible solution to this lack of information and provides a technical, economic and environmental assessment of diamond wire used in quarrying basalt for ornamental purposes. After an overview on the state of the art of diamond wire and on the final use of processed basalt, the study describes the experimental plan and the results. These show a tool yield much higher than those measured when diamond wire is used on other silicate dimension stones (e.g. granites). Moreover, the composition of basalt sawdust (sludge) has been analysed in the laboratory and has indicated the absence of polluting materials related to tool wear; therefore, basalt sludge, which is made of water and micronized basalt, can be used as a secondary raw material for the environmental restoration of the area or for any other purpose. Further research on other lithotypes is also proposed.
Similar content being viewed by others
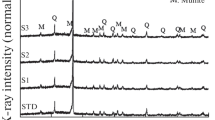
Explore related subjects
Discover the latest articles, news and stories from top researchers in related subjects.Avoid common mistakes on your manuscript.
Introduction
Basalt has been used in Sardinia since prehistoric times (Blake 1998), as evidenced by the Giants’ graves and nuragic towers, which are on the World Heritage List (UNESCO 1997). In later centuries, basaltic stones were used locally for the construction of small buildings and road paving of the civic centre (Consorzio 21 2002). However, after the process of industrialization of the Sardinian dimension stones sector, which can be traced back to 1870 (Careddu et al. 2017), basalt has been considered less interesting than other ornamental stones commonly used on the Island such as various types of granite.
Currently, because of an increased interest in the restoration of buildings and historic areas along with a greater demand for stone materials to be used for street furnishing purposes, the demand for stones such as basalt has greatly increased (Montani 2016). In particular, local governments are focusing on the renovation of their civic centres and the rebuilding of original paving, which, before the advent of asphalt, had been constructed from stones quarried in the geographical area of the town.
The increase in the marketing of processed basalt coincided with an increase in the supply and use of advanced technologies for basalt sawing and processing to improve the quarry yield and, at the same time, to reduce the amount of material sent to landfills. However, the increase in the use of new technologies applied to basalt quarrying was not accompanied by an adequate study of the economic and environmental sustainability.
This lack of studies is easily explained. When diamond wire (DW) was first introduced in the quarries for sawing abrasive rocks (silicate) in the mid 80s (Biasco 1993), it was primarily used on granite and, rarely, on trachytes, sandstones, diorites and gneiss. The low market value of basalt and the low demand (limited to the local market) did not create enough interest in the use of DW because of its high cost.
The recent increase in demand of basalt due to the relaunch of several civic centres, and the growing interest in “ancient and rustic” materials (Careddu 2012), has led to an increase in the use of the diamond wire in basalt quarrying over the last 10 years.
This study aims at filling the gap in information about the use of DW in basalt quarry works.
Evolution of DW in hard stone sawing
Pliny the Elder (77 A.D.), in his Naturalis Historia, described the sawing of stone by means of abrasive sand pushed on the rock by an iron saw moved back and forth.
A similar concept was introduced again in 1854 when helical wire was invented (Capuzzi et al. 1975–1976) for the detachment of marble blocks in quarries. The widespread use of the helical wire was due to the brilliant introduction of the “penetrating pulley” by Italian engineer Attilio Monticolo in 1897, which allowed up-line cutting in any position, even without having to dig wells (Branca 1974). When compared with competing technologies at that time, this excavation system that was adopted in marble quarries contributed to a more rational exploitation of stone deposits and greatly limited the waste of useful material. It also improved work safety and reduced excavation time and costs.
Helical wire was used until the late 1970s when it was replaced by diamond wire with electroplated beads (Primavori 1999).
Thanks to the new technology, sawing costs were reduced significantly, while productivity (measured in m2/h) increased (Trancu 1980). However, diamond wire was used only for sawing marble travertine or limestone materials (non-abrasive rocks). DW use for cutting granite was generally not suggested, for economic reasons, although, in some cases, it was still occurring.
In the mid 1980s, the improved wear behaviour of sintered beads resulted in their use to cut granite economically (Thoreau 1986); the decrease in costs of both sintering and diamond in later years favoured a wider use of DW in granite quarries until the mid 1990s, when all ornamental granite quarries of industrialized countries had the DW machines (Careddu and Cai 2014).
DW technology is perfect for sawing abrasive rocks, as the market itself announced following the successful launch of multiwire machinery for block sawing, which is currently taking over the traditional pendulum gangsaws (Careddu and Cai 2014).
The DW currently used in quarrying has sintered beads with an external diameter of 11–11.5 mm which are assembled on a steel rope with a nominal diameter of 5 mm. Due to the high price of cobalt (and its related health problems) the use of other metal powders (Fe, Cu, Sn, Ni, W) in diamond beads production has increased (Brookes 2011). It should be noted that the diamond grits and the matrix material of the sawing tool work together in any given stone sawing application and it is up to the manufacturers to provide the best combination based upon the properties of the workpiece stone material (Büyüksaǧiş 2010).
The protection from any abrasive wear of the steel rope is provided by the injection of moulded plastic spacers. Moreover, by preventing the flow of beads on the rope, the use of plastic maintains both the geometric and dimensional integrity of the tool and, therefore, gives a longer service life. The adoption of rubber or plastic as spacers has greatly contributed to lowering the risk of wire breakage by preventing the high-speed projection of loose beads (Castelli and Cai 1989).
Studies on diamond wire performances on abrasive rocks
Although data on the performance of diamond wire on calcareous rocks began to be released from the late 1970s (Cai et al. 1983; Pinzari 1983), the first information on the benefits of using DW for hard and abrasive rocks sawing was published from the early to mid 1980s.
Biasco (1993) produced performance data (sawing speed in m2/h) and wire productivity (m2/m) in quarries of abrasive rocks such as granites, diorites, gneiss, sandstone and trachyte. Daniel (1986) reported results from other silicate rock sawing using DW in several quarries, by dividing the stones into three categories: soft (i.e. gneiss, shales), medium (Sardinian granites) and hard (very abrasive granites). These data were then updated by Wright (1991). Butler-Smith (1995) focused on improving DW sawing performance in South African quarries from a technical and economical point of view. Ciccu et al. (1998) published data on the cutting rate and quarry yield separating hard stone into two different groups: granites and other silicate stones such as gabbro, trachytes, sandstones, labradorites etc. Primavori (1999) updated previous data by providing the performance of DW on other abrasive stones commercialized worldwide. Özçelik (2003) tried to study the DW wear in andesitic stone by using statistical analysis. Agus et al. (2003) tested diamond wire on a wide range of abrasive stones in order to build a predictive model of DW cutting rate and wear in relation to the rock micro-hardness, mineral composition and crystal size. Sánchez Delgado et al. (2005) compared both rock hardness and quartz content of granite with the sawing rate. Cai et al. (2007) studied the DW performance on granite considering the variations in operating parameters such as peripheral wire speed and the cutting rate.
However, it appears that a lack of data about basalt sawing by diamond wire still exists.
Studies on sawing sludges and environment
The bibliography concerning the characterization of sawing sludges deriving from hard rock sawing and aimed at the subsequent re-use of microfine sawdust, is comprehensive. However, past studies were almost exclusively related to the problems of sludge resulting from the sawing of blocks in plants; therefore, this research generally considered the sludges which were produced by the traditional granite gangsaws and had high iron content (due to the steel grit and blade wear).
Research in the 1970s and 1980s was justified by economic issues and aimed to improve the technical performances of sawing. During the 1990s, the “golden time” of the so-called “commercial granites” (Careddu et al. 2017), studies on the residual sludge mostly addressed three different fields: usage as waterproofing material for municipal landfills (Bertolini and Celsi 1989; Frisa Morandini and Verga 1990), feldspar and quartz recovery for use in the ceramic and glass sectors (Curreli et al. 1992; Sassone and Danasino 1995) and producing inactive sludge by applying the same technologies employed in the ceramics and glass sectors (Pelino et al. 1998; Rincón and Romero 2010).
At the end of the 1990s and in the following years, different ways of re-utilizing these materials other than topsoil were tested, such as their use during the process of quarry rehabilitation (Burragato et al. 1999; Barrientos et al. 2010; Sivrikaya et al. 2014). However, environmental compatibility continues to be the necessary condition towards recovery.
Manca et al. (2015) recently studied the use of basalt sludge from stone-processing plants for the production of bricks for civic purposes. Nevertheless, the relatively smaller production of basalt compared with granite has resulted in limited research on the reuse of basalt sludge, for reasons similar to those described above.
Equipment and materials
Basalt
Basalt is one of the most common effusive igneous rocks. It typically shows a dark colour and it is relatively poor in quartz; it mainly consists of calcic plagioclase, pyroxene and olivine.
Sardinia’s most exploited basalt formations are located in the western part of the Island, specifically in the area of Monte Arci and Giara di Gesturi, in the highlands of Abbasanta and Campeda and in the historical regions of Montiferru and Barigadu (Piras 2000).
These formations arise primarily from the cycle of subsidence and the associated igneous activity related to the formation of Campidano’s Graben. This reducing tectonic activity, with faulting in the NW–SE direction, affected Sardinia during the Pliocene–Pleistocene era, about four million and up to 1 million years ago (Grillo et al. 2009).
Because of its rapid cooling, basaltic matrix has a very fine grain which, in some cases, is often amorphous and is crossed by fractures. Minerals are not visible to the naked eye. The minerals that constitute basalt are rich in iron and manganese, which is why the rock has the dark colour. A reddish-vinaceus colour (Careddu et al. 2015), showing a deterioration by oxidation appears in some areas only.
Basalt quarry
The basalt quarry where the study was carried out is located in the area called “Su Inzale” in the municipality of Santu Lussurgiu (OR), between the plateau of Abbasanta and the massif of Montiferru, as shown in Fig. 1.
The petrographic analysis showed similar features over the entire stone deposit. Figure 2 shows a porphyritic structure with intersertal texture in the basaltic rock. The olivine phenocrystals and clinopyroxenes are enclosed in a matrix of calcic plagioclase. Olivine typically shows a consequence of reddish borders altered to hiddingsite.
Some of the physical and mechanical properties of the basalt are given in Table 1. The physical and mechanical properties were determined by a whole range of laboratory tests which were carried out in accordance with CEN-EN standards.
In the quarry area, basalt naturally occurs in parallelepiped-shaped blocks, with rounded edges and vertices larger than 2 m; sometimes, natural blocks are much bigger, their longer sides reaching 4 m.
One-terrace vertical striping is the adopted excavation method in the quarry; blocks are removed from the quarry face by the excavator.
The quarry face is not homogeneous; the blocks that gradually emerge are, in fact, already separated by rock-mass discontinuities, which are often filled with fine materials resulting from weathering.
The first step is to remove the topsoil over the block to be extracted, which is often thick (several decimeters): however, in some areas, it is totally absent. A bed of detritus is then prepared, on which to place the block that will be sawn; the block is placed on fractured materials (rubble) to prevent (minimize) use of the drilling machine. In this way, it will not have to be left on the ground, which creates a free passageway where diamond wire must be inserted. Whenever this is not possible, the workman should drill a passage hole.
Once moved away from the quarry face, the blocks are reduced by diamond wire sawing (using different cuts) until they reach the maximum volume of 7 m3 (about 20 tons), due to the lifting limit of the crane located in the stone-processing plant.
The current quarry yield is about 35%.
Diamond wire
A DW with injected vulcanized rubber was used to saw the basalt blocks; this DW has 40 sintered beads per meter and the beads have an external diameter of about 11.4 mm. Industrial diamonds are used to produce this kind of bead suitable for basalt sawing; diamond grain size classes (expressed in US mesh) are distributed as follow: 40% 30–40, 55% 40–50 and 5% 50–60. Both diamond concentration and the exact metal matrix compounds are always regarded as an industrial secret.
The initial length of the DW was 30 m. Given that the beads must have homogeneous wear along their lateral surface, it is advisable to give 1.5 twists/m to the tool in the tightening direction of the strand; this is done manually by the operator before “loop” closing the DW using hydraulic crimping.
The operator draws a red line on the block to highlight where the DW will start its sawing process; the sharp edges are eliminated with a hammer, because they will wear out the tool more rapidly.
The diamond wire sawing machine used in the quarry is a S625EGT provided by the Italian Dazzini Macchine. The peripheral speed of the wire can be adjusted electronically at any time of the process and it can range from 0 to more than 30 m/s. The optimal value on this type of rock is about 28 m/s.
Tension in the wire is maintained by retreat of the sawing machine on its tracks; the backward and forward movement and speed are controlled by an inverter.
A very important datum which is hardly ever reported, concerns the sawing. During this phase, the DW is provided by a constant supply of water of about 7–8 l/min, to cool and keep it clean; nevertheless, this flowing rate should not be too high to prevent aquaplaning. The water hose is placed on the block above the saw line.
Experimental
In order to evaluate the use of the diamond wire on basalt from different points of view (technical, economic and environmental), the following information data/parameters were monitored:
-
DW length (m) and number of beads (N);
-
bead diameter decrease (mm);
-
sawed areas (m2);
-
rock characterization around the sawed surface;
-
sludge characterization.
Data concerning cutting the times were also obtained; however, they will be discussed in a future article.
The experimental plan in the quarry took about 7 months.
Diamond wire length and number of beads
DW length may not be constant throughout the service life of the tool. In fact, during quarrying works, accidents happen, e.g. entrapment, thread breakage at the junction, etc. Every time something unusual happens, the operator must stop sawing and re-join the wire, resulting in the loss of at least two beads. In addition, it may be necessary to saw small areas (of about 4 m2), which means that the operator needs to cut the DW in two and use only one half. Subsequently, the two halves could be re-jointed to reform a longer DW.
Beads’ diameter decrease
In order to have good information about this parameter, it was decided to measure a bead every 2 m, for a total of 15 beads. Each bead was marked with a permanent marker so that it could be easily recognized after the sawing.
Three measurement planes were identified for each bead, called anterior, median and posterior (A, M, P), according to the sawing direction. On each plane, the beads’ diameter was measured in two directions perpendicular to each other, as shown in Fig. 3, using digital callipers and entering the data on a chart. This operation was carried out before the first sawing and repeated after the following seven sawings; measurements were then repeated about halfway through the service life of the tool and after its depletion.
Sawed areas
Each sawed area was measured using the following methodology. A photograph was taken perpendicularly to one of the two surfaces obtained from each sawing, making sure to put a measure on the surface as a reference; the photographs were then processed with ImageJ 1.47v software, provided by National Institute of Health (NIH, USA), by setting the scale with the help of the image (Fig. 4).
Rock and sludge characterization
Several rock samples and sludge-sawdust samples were collected after the sawing processes. The importance of having both rock samples and sludge from the same sawing lies in the fact that it is necessary to see if there are chemical differences related to the release of heavy metals caused by wear of the DW.
Seven samples of sludge, each coming from a different sawing, were collected and dried in a fan-assisted oven; the resulting sawdust samples were then analysed. Seven rock samples were milled for analysis.
Atomic emission spectroscopy (AES) was carried out on both sawdust samples and milled rock, with the aim of highlighting the differences in chemical composition between the two types of samples. Analysis was done by an inductively coupled plasma spectrometer (ICP-AES) 710-ES, provided by Varian.
The structural analysis of crystalline materials of each sample was carried out with the desktop X-Ray diffractometer Miniflex II provided by the Rigaku Corporation.
The bulk density of each sample material was determined using an AccuPyc 1330 gas pycnometer manufactured by Micromeritics Instruments. Grain size analysis was conducted on the sawdust samples using a Sedigraph 5100 analyser.
Results and discussion
Technical-economical results
Figure 5 shows the decrease in bead diameter with the increase of total sawed area.
It is quite evident how the correlation between the reduction of bead diameter and the sawed area is perfectly linear (R > 0.99). This result should not be taken for granted, as it closely depends on the optimal use of the tool by the operator, who works on the sawing machine operating parameters to make sure that the tool works at its best when needed.
It is important to note that one cannot actually keep sawing until the diamond-metal alloy has totally worn out (i.e. when the bead’s diameter coincides with the extremal diameter of the 8.0-mm support: in this case, it meant a decrease to 8.90 mm). In fact, the service life of the tool does not just depend on this factor but also on both the decrease in number of beads per meter (from the initial Nb = 40 beads/m to approximately 38 beads/m) and the weakening of the wire for the reasons mentioned above.
The diamond wire, initially 30 m long (L), with 1200 beads, gradually reduced to the final length of 20.11 m with 766 beads and even 11 joints! Therefore, its use was no longer advantageous from a technical point of view.
Total sawed area (A) by the DW was measured as 843.52 m2, which allowed the DW yield (y) of the wire to be calculated as follows:
This value can be used to evaluate the DW unit cost (cu); if the market price (P) of DW is 60 €/m:
Lastly, it is also possible to calculate the (theoretical) productivity of each bead:
Figure 6 shows that the decrease in the number of beads of the DW is not linear during the sawing process. Marginal loss of beads increases with the increased sawed area and, therefore, along with the aging of the wire.
Chemical-environmental results
As shown in Table 2, chemical analysis of microfine dust samples shows an absence of pollutants deriving from stone sawing. The differences in the content may be linked to the small differences in chemical composition in various parts of the basalt deposit, as already noted in the in situ rock. Because of this outcome, basalt sawdust can be simply recovered and re-used in accordance with Italian regulations (ILD no. 152, 2006).
All the samples show very similar X-ray diffraction (XRD) patterns, which are consistent with the presence of the augite, forsterite, labradorite and anorthoclase. For example, Fig. 7 shows the XRD spectrum of basalt sawdust derived from a starting cut.
In addition, this kind of waste is classified as inert as it does not exceed the concentration levels allowed in landfills (ILD 2010). Furthermore, the analytical results obtained here confirm that this type of waste does not require treatment as a hazardous waste and that basalt dust can be used as a secondary raw material.
The particle size distribution curves of the five samples indicate the fineness of the products. Most of the materials have grain sizes below 15 μm as shown in Fig. 8. More specifically, D50 ranges between 9.7 and 12.6 µm. According to ASTM (2000), the uniformity coefficient CU = D60/D10 is useful to assess whether the sample is well graded or not; a CU, ratio less than 3 describe a well-graded sample. The collected basalt sawdust samples have CU ranging from 5.30 to 6.93, which is considered well graded.
These results are very similar to what has already been measured in previous studies on the marble (Careddu et al. 2014) and granite (Careddu and Dino 2016). The recycling of this sawdust as a secondary raw material could have various advantages since it avoids the cost of micronization.
Results indicate that the basalt sludge and other quarry scraps can all be reused during environmental rehabilitation of depleted areas of the quarry.
Other observations
It is important to note that the service life of the DW does not end when the diamonded-metal alloy is completely worn out but before it reaches that stage. In fact, other factors impact the DW depletion:
-
Some beads show failures that others do not (such as cracks and/or breaks); moreover, as noted during their measurement, the beads which are located immediately after the joints show more evidence of wear than those further away;
-
When the DW breaks, it must be re-jointed with a new junction. This action involves the loss of at least two beads;
-
Even the steel cable ages due to its continuous tearing and twisting: this means that the DW becomes weaker and weaker with its use. Therefore, even when the beads can theoretically still be used, the DW may be useless.
Conclusion
The study showed that the DW used in the basalt quarries for ornamental use wears out slowly when compared with other silicate rocks such as granite. This results in two main benefits: the DW has a higher productivity (more than 28 m2/m) and results in a lower contribution of the tool to the total sawing cost (which includes other items such as: machinery depreciation, maintenance, energy, water, manpower, etc.).
The release of polluting material consistent with the wearing out of the tool was virtually nil in the sludge, confirmed in the chemical analyses. In fact, the values of heavy metals in the basalt sawdust are always below legal limits, and they never deviate from the measured values of the rock samples. The sawdust samples showed almost identical bulk density, grain size distribution, petrographic and mineralogical features.
Based on the chemical analysis results, it was possible to establish that the quarry scraps can be reused during rehabilitation of quarry excavations. As a result, an adequate recycling of this basalt sawdust as a secondary raw material can be further developed.
Basalt sawing DW is sustainable from an environmental point of view, especially when compared with other techniques often used in quarries. Furthermore, explosives were never used during any of the quarry operations/testing.
The decrease in the number of beads which are assembled on the steel cable “accelerates” as the tool wears. This depends mainly on the need to open up the cable to re-joint it for each sawing and, to a lesser extent, on the incidents that may occur during the sawing process. To reduce the effect of the junction during the shortening of the DW, special focus should be made on finding/creating a jointing technique that does not involve the removal of two beads every time the cable needs to be repaired.
Finally, to develop this line of investigation on DW further, the study of its use on different ornamental stones should be carried out, particularly those materials that have never been tested or those that are out of favour, such as trachytes and sandstone, but whose market demand is currently increasing.
References
Agus M, Bortolussi A, Careddu N, Ciccu R, Grosso B, Massacci G (2003) Influence of stone properties on diamond wire performance. In: Proceedings of fourth international conference on computer applications in the minerals industries (CAMI 2003), September 8–10, 2003. Calgary, Alberta, Canada. Singhal/Fytas/Chiwetelu (ed)
ASTM (2000) Standard practice for classification of soils for engineering purposes (Unified Soil Classification System). Designation: D 2487-00
Barrientos V, Delgado J, Navarro V, Juncosa R, Falcón I, Vázquez A (2010) Characterization and geochemical–geotechnical properties of granite sawdust produced by the dimension stone industry of O Porriño (Pontevedra, Spain). Q J Eng Geol Hydrogeol 43:141–155
Bertolini R, Celsi S (1989) Ipotesi di riutilizzo dei fanghi derivanti dalla lavorazione di materiali lapidei. Atti Convegno su: Situazione e Prospettive dell’Industria Lapidea. Cagliari (Italy), April 1989, pp 384–390 (in Italian)
Biasco G (1993) Diamond wire for quarrying hard rocks. Ind Diamond Rev 53(558):252–255
Blake E (1998) Sardinia’s nuraghi: four millennia of becoming. World Archaeology 30(1):59–71
Branca FP (1974) Studio del meccanismo di segagione del filo elicoidale. 1° Convegno Internazionale sulla Coltivazione di Pietre e Minerali Litoidi. Torino 4-5-6-Ottobre 1974, vol II, pp 1–31 (in Italian)
Brookes K (2011) Hardmetal meet at World Congress. Met Powder Rep 66(2):10–14
Burragato F, Mecella G, Scandella P (1999) Waste muds from Processing of the siliceous sands from Priverno: potential use for environmental rehabilitation. In: 2nd national congress “Valorisation and recycling of industrial wastes”. L’Aquila, Italy, 5–8 July 1999
Butler-Smith P (1995) The cost effectiveness of diamond wire sawing in quarry. Diamante—Applicazioni and Tecnologia, n. 4—Anno 1995, pp 145–150
Büyüksaǧiş IS (2010) The effects of circular sawblade diamond segment characteristics on marble processing performance. Proc Inst Mech Eng Part C J Mech Eng Sci 224(8):1559–1565
Cai O, Mannolini A, Rubino A (1983) Applicazioni e sviluppi del filo diamantato nel taglio primario in cave di marmo e travertino. Marmo Macch 54(1983):122–127
Cai O, Careddu N, Mereu M, Mulas I (2007) The influence of operating parameters on the total productivity of diamond wire in cutting granite. Ind Diam Rev 3(2007):25–30
Caius Plinius Secundis (77 A.D.) Naturalis Historiae, vol X, book 36, section IX
Capuzzi Q, Carriero M, Failla S (1975–76) Ricerca coltivazione e utilizzazione dei marmi Apuani—Tecniche di estrazione, Carrara Marmi, n. 2, Marzo 1975, n. 5 Dicembre 1975, n. 7 Giugno 1976, Comune di Carrara, Italy, pp 7–18 (in Italian)
Careddu N (2012) Rough surface finishing of stone-faced sandwich panels using high pressure waterjet. J Mater Civ Eng 24:907–915
Careddu N, Cai O (2014) Granite sawing by diamond wire: from Madrigali “bicycle” to modern multi-wires. Diamante—Applicazioni and Tecnologia, n. 79, Anno 20, Dicembre 2014, pp 33–50. Ed. G & M Associated Sas, Milan, Italy
Careddu N, Dino GA (2016) Reuse of residual sludge from stone processing: differences and similarities between sludge coming from carbonate and silicate stones—Italian experiences. Environ Earth Sci 75:1075
Careddu N, Marras G, Siotto G (2014) Recovery of sawdust resulting from marble processing plants for future uses in high value added products. J Clean Prod 84(2014):533–539
Careddu N, Scanu M, Desogus P (eds) (2015) Map of natural stones from Sardinia. Cagliari, Italy
Careddu N, Siotto G, Marras G (2017) The crisis of granite and the success of marble: errors and market strategies. The Sardinian case. Resour Policy 52(2017):273–276
Castelli M, Cai O (1989) Safety in the use of diamond wire in quarrying. Marmo Macch, n 85, pp 94–103
Ciccu R, Agus M, Bortolussi A, Massacci G, Careddu N (1998) Diamond wire sawing of hard rocks. In Proceedings of “superabrasive and CVD diamond—theory and application”, Ultrahard Materials Technical Conference, May 28–30, 1998—Windsor, Ontario, Canada. Also printed in: Diamante—Applicazioni e Tecnologia, Dicembre 1998, pp 78–95, and in: Finer Points, vol 11, no. 4 1999, pp 22–30. Skyland, NC, Industrial Diamond Association of America (Pub)
Consorzio 21 (2002) Natural stone from Sardinia. La Poligrafica Solinas s.r.l. (ed) Nuoro/Bolotana, Italy
Curreli L, Ferrara G, Ghiani M, Macchiavelli G, Pala M, Salaris M (1992) Produzione di feldspati per uso ceramico da rocce granitiche. Resoc Ass Min Sarda anno XCV, pp 69–86 (in Italian)
Daniel P (1986) More granites succumb to diamond wire. Ind Diam Rev 5(86):189–194
Frisa Morandini A, Verga G (1990) Problemi connessi con lo smaltimento dei residui di lavorazione delle pietre ornamentali. Bollettino della Associazione Mineraria Subalpina, Anno XXVII, numero 1–2, pp 247–253 (in Italian)
Grillo S, Mocci S, Pia G, Spanu N, Tuveri L (2009) Il manuale tematico della pietra. In: Atzeni C (ed) U Sanna. Itaca, Italy (in Italian). ISBN 978-88-496-6821-6
ILD (2006) Regolamento recante modifiche al decreto ministeriale 5 febbraio 1998 (Italian Legislative Decree no. 186, 05/04/2006. Regulation modifying the Ministerial decree of 5 February 1998). “Individuazione dei rifiuti non pericolosi sottoposti alle procedure semplificate di recupero, ai sensi degli articoli 31 e 33 del decreto legislativo 5 febbraio 1997, n. 22”. G.U. n. 115, 19/05/2006 (in Italian)
ILD (2010) Italian Legislative Decree, 27/09/2010. Criteria Pertaining to Waste Allowed to be Disposed of in Landfill. Definizione dei criteri di ammissibilità dei rifiuti in discarica, in sostituzione di quelli contenuti nel decreto del Ministro dell’ambiente e della tutela del territorio 3 agosto 2005. G.U. n.281, 01/12/2010 (in Italian)
Manca PP, Orrù G, Desogus P (2015) Recycling of sludge from ornamental stone processing as resource in civil constructions. Int J Min Reclam Environ 29(2):141–155
Montani C (2016) XXVII Report marble and stones in the world 2016. Ed. Aldus Casa di Edizioni in Carrara, Italy
Özçelik Y (2003) Multivariate statistical analysis of the wear on diamond beads in the cutting of andesitic rocks. Key Engineering Materials, vol 250. Trans Tech Publications
Pelino M, Cantalini C, Socchera A, Cisi G, Ullu F, Cabiddu P (1998) Aspetti scientifici e tecnologici di un impianto di vetrificazione di rifiuti industriali pericolosi. In: Atti del 4° Congresso Nazionale AIMAT, Chia Laguna (CA); Italy, 8–11/06/1998. AIMAT-PTM ed., pp 570–577 (in Italian)
Pinzari M (1983) Quarrying stone by diamond wire in Italy. Ind Diam Rev 43(498):231–236
Piras M (2000) Il basalto nell’evoluzione geologica del Guilcier. In: Basalto, ISKRA (ed) Ghilarza, Italy, pp 11–26 (in Italian)
Primavori P (1999) 20 years of diamond wire. Marmo Macch Anno 29°, 149, pp 278–304
Rincón JM, Romero M (2010) Frits from natural stone wastes for obtention of composites applied as construction materials. In: Proceedings of global stone congress 2010, 2–5 March 2010, Alicante, Spain. S3-13. AIDICO (Instituto de la Construcción) (ed), València (ISBN: 978-84-614-1147)
Sánchez Delgado N, Rodríguez-Rey A, Suárez del Río LM, Díez Sarriá I, Callejaa L, Ruiz de Argandoña VG (2005) The influence of rock microhardness on the sawability of Pink Porrino granite (Spain). Int J Rock Mech Min Sci 42(2005):161–166
Sassone P, Danasino P (1995) Caratterizzazione di fanghi di segagione di Pietra di Luserna per la valorizzazione come materie prime secondarie. Atti del 2° Incontro Int. Giovani Ricercatori in Geologia Applicata (I.M.Y.R.A.G.), Peveragno (CN), 11–13 ottobre 1995, pp 510–515 (in Italian)
Sivrikaya O, Kıyıldı KR, Karaca Z (2014) Recycling waste from natural stone processing plants to stabilise clayey soil. Environ Earth Sci 71:4397–4407
Thoreau B (1986) Utilisation du cable diamanté pour le sciage du granit en carrière. Le Mausolee Mars 1986:384–386 (in French)
Trancu TC (1980) La “Bicicletta” che taglia grandi blocchi di marmo da 6000 tonnellate. Informazione sui Diamanti, T 45, De Beers Industrial Diamond Division, Milano, Italy (in Italian)
UNESCO (1997) Su Nuraxi di Barumini. In: World Heritage Committee Inscribes 46 New Sites on World Heritage List. http://whc.unesco.org/en/news/180/. Accessed 17 Jan 2017
Wright DN (1991) Progress in the mining and processing of natural stone with diamond tools. Technical paper, SME MR910166
Acknowledgements
The authors wish to thank Perdas s.a.s Company for allowing us to carry out this study and especially Mr. Alessandro Secchi for his technical support.
Author information
Authors and Affiliations
Corresponding author
Rights and permissions
About this article
Cite this article
Careddu, N., Perra, E.S. & Masala, O. Diamond wire sawing in ornamental basalt quarries: technical, economic and environmental considerations. Bull Eng Geol Environ 78, 557–568 (2019). https://doi.org/10.1007/s10064-017-1112-6
Received:
Accepted:
Published:
Issue Date:
DOI: https://doi.org/10.1007/s10064-017-1112-6