An experimental high-strength steel 20Kh2G2SNMA with high resistance of supercooled austenite to formation of diffusion transformation products is studied. Dilatometric analysis of the phase and structural transformations under continuous cooling and isothermal holding is performed. The time-temperature ranges of the transformations are found. The thermokinetic diagram is plotted. The mechanical properties of the steel are determined after different treatments, i.e., annealing, normalizing, quenching, tempering, isothermal and step quenching. It is shown that the presence of bainite in the structure lowers the impact toughness of the steel independently of its morphology and of the temperature range of its formation.
Similar content being viewed by others
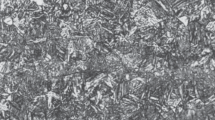
Avoid common mistakes on your manuscript.
Introduction
Steels with high resistance of supercooled austenite to formation of ferrite-bainite mixture have considerable advantages over the low-alloy structural steels used widely in mechanical engineering [1, 2]. The advantages include the possibility of the use of decelerated cooling in heat treatment, which lowers the level of residual stresses and provides a homogeneous structure over the entire cross section of the part [3,4,5,6]. In its turn, this makes the heat treatment processes easier to implement and raises the stability of the mechanical and functional properties of ready steel parts including large-size ones.
Steels with elevated content of chromium and nickel (18Kh2N4MA, 25Kh2N4MA, 38KhN3MA) [7, 8] and low-carbon martensitic steels (12Kh2G2NMFt, 15Kh2NMFBA, 27Kh2G2NMFBA) [9,10,11] with high stability of supercooled austenite are classified conventionally as martensitic steels (Guillet classification). All these steels contain expensive alloying elements (Ni, Mo, Ni, Nb, V) and their application is not always expedient economically.
The aim of the present work was to study the special features of formation of structure and mechanical properties of an advanced sparingly alloyed high-strength steel 20Kh2G2SNM with high stability of supercooled austenite.
Methods of Study
We studied low-carbon alloyed martensitic steel 20Kh2G2SNM containing the following main alloying elements (in wt.%): 0.22 C, 1.96 Cr, 2.02 Mn, 0.96 Si, 1.09 Ni, and 0.31 Mo.
The occurrence of transformations in supercooled austenite in the steel was studied using a LINSEIS L78 R.I.T.A. dilatometer. Cylindrical specimens with diameter 4 mm and length 10 mm were heated in vacuum to an austenitization temperature of 900°C at a rate of 10 K/sec. The hold at this temperature was 15 min. Continuous cooling of the specimens was conducted at a constant rate of 0.1 – 30 K/sec. The temperatures of the start and finish of the transformations under the heating and the cooling were determined by the method of detachment of a tangent drawn to the linear part of the curve describing the dependence of the elongation of the specimen on the temperature [12].
We also studied the kinetics of the isothermal transformation of supercooled austenite in the steel by the method of dilatometry. After 15-min austenitization at 900°C the specimens were cooled in the chamber of the dilatometer at a rate vcool = 30 K/sec to the required temperature of isothermal hold. The hold lasted for 2–3 h. Then the specimens were cooled arbitrarily in the chamber of the dilatometer.
We analyzed the transformations of supercooled austenite under continuous cooling and isothermal hold using the dilatometric data by the method of [13, 14].
In the next stage of the study we performed a laboratory heat treatment of specimens in chamber furnaces (austenitization and tempering) and in a tank shaft furnace with a melt of 50% KNO3 + 50% NaNO3 (isothermal holding) by the following variants.
-
1.
Austenitization at 900°C for 60 min and cooling under different conditions, i.e., with the furnace (the average cooling rate in the range of martensitic transformation 0.02 K/sec), in air in a container with iron strips (0.2 K/sec), in still air (2 K/sec), and in quenching oil I20A (20 K/sec).
-
2.
Austenitization at 900°C for 60 min, oil cooling, tempering at 200 – 600°C for 3 h, and air cooling (QT variants).
-
3.
Austenitization at 900°C for 60 min, hold in molten salt at 280 – 380°C for 90 min, oil cooling, and tempering at 180°C for3h (AT variants).
-
4.
Austenitization at 900°C for 60 min, hold in molten salt at 280°C for 10 min, oil cooling, and tempering at 180°C for 3 h (variant QP1).
-
5.
Austenitization at 900°C for 60 min, hold in molten salt at 280°C for 10 min, hold at 350°C for 60 min, oil cooling, and tempering at 180°C for 3 h (variant QP2).
-
6.
Austenitization at 900°C for 60 min, hold in molten salt at 280°C for 10 min, oil cooling, hold at 350°C for 60 min, oil cooling, and tempering at 180°C for 3 h (variant QPT).
The mechanical properties of the steel (the yield limit σ0.2, the ultimate strength σr, the elongation δ, and the contraction ψ) after the treatments mentioned were determined using an INSTRON facility at room temperature according to GOST 1497. The specimens for the tests were shaped as cylinders (type III) with functional part with diameter 6 mm and length 30 mm. In tests for impact bending were performed with the help of a pendulum hammer according to GOST 9454 at room temperature for standard V-notched specimens. The Rockwell hardness was measured according to GOST 9013 (scale C).
The microstructure was studied using MEIJI IM7200, OPYMPUS and other optical microscopes. To uncover the microstructure, the polished sections were etched in a 5% alcoholic solution of nitric acid.
Results and Discussion
The dilatometric analysis gave us the critical tempertures of the steel under heating, i.e., Ac1 = 780°C and Ac3 = 860°C. We established that cooling from 900°C at a constant rate of 0.1 – 30 K/sec produced a bainitic structure in the range of 355 – 480°C and a martensitic structure starting with 355°C (Fig. 1a ). By the data of the dilatometry, the content of bainite in the structure was 15 – 20% at vcool = 0.1 – 0.3 K/sec and 5 – 10% at vcool =1– 10 K/sec.
The microstructure of the steel after cooling from 900°C at different rates does not differ substantially and has a lath structure in all the cases (Fig. 2a and b ). The hardness grows from 45 HRC (vcool = 0.1 K/sec) to 49 HRC (vcool = 30 K/sec), which correlates with the content of bainite determined by the dilatometry. Thus, the bainite formed in continuous cooling of the steel in the range of 0.1 – 30 K/sec has a morphology close to a martensitic one though the temperature of the start of formation of martensite is quite high. The thermokinetic diagram of the transformation of supercooled austenite in the steel is presented in Fig. 1b.
We determined the mechanical properties of the steel after cooling it with different intensities. It turned out that the decrease in the cooling rate by a factor of 1000 (from 20 to 0.02 K/sec) results in lowering of the strength characteristics, i.e., from 1300 to 1050 MPa (by 19%) for σ0.2 and from 1540 to 1375 MPa (by 10%) for σr. The elongation remains invariable (δ = 12 – 14%). However, when the cooling rate is reduced from 20 to 0.02 K/sec, the impact toughness KCV decreases substantially (from 0.89 to 0.35 MJ/m2, i.e., by 60%).
By the data of the metallographic studies, the structure of the steel cooled at a rate of 0.02 K/sec acquires a considerable content of upper bainite (Fig. 2c ), which explains the minimal level of the impact toughness typical for this type of microstructure. However, the impact toughness lowers considerably even when the cooling rate is lowered from 30 to 0.1–2 K/sec, when the microstructure does not contain upper bainite (Fig. 2d ). This is explainable by the fact that the lower bainite in the steel studied, just like the upper bainite, has a lower level of impact toughness than martensite, while it is expected that after the cooling at 20 K/sec the steel should acquire a maximum content of martensite.
To prove this hypothesis, we subjected the steel to isothermal quenching in the range of 280 – 380°C (Ms = 355°C) in order to form a bainitic structure. By the data of the dilatometry, the steel undergoes an isothermal bainitic transformation of supercooled austenite in this temperature range, both above and below Ms (Fig. 3a ). According to [15, 16], most grades of structural steels undergo an isothermal bainitic transformation in the temperature range of formation of martensite.
Kinetic curves of bainitic transformation (qa is the fraction of the transformation) during holding at 340 and 380°C (a) and variation of the length of the specimen (∆l) in cooling after the isothermal hold at 340 and 380°C (the white arrows point at the start of formation of carbon-enriched martensite) (b ).
Our dilatometric studies show that the steel acquires some carbon-enriched martensite below 240°C (Fig. 3b ) in cooling after the isothermal hold at 340°C (below Ms). Therefore, the structure of the steel (Fig. 4a ) after the isothermal treatment below 355 should consist of “primary” martensite formed during the cooling to the temperature of the isothermal hold, bainite, freshly formed high-carbon martensite, and retained austenite stable at room temperature and located in regions bainite and martensite in the form of layers between α-plates and in the form of blocky components [15,16,17,18]. The content of “primary” martensite in the structure of the steel subjected to isothermal quenching below Ms can be assessed from the curve describing the dependence of the fraction of martensite on the temperature plotted in continuous cooling (Fig. 1a ). In cooling to the temperature of the isothermal holds at 280, 320 and 340°C its content should be 75, 30 and 10%, respectively.
As a result of the isothermal quenching at 380°C, the bainitic transformation develops incompletely, and the untransformed austenite is enriched with carbon. As a consequence, the final cooling after the hold produces carbon-enriched martensite in the structure of the steel (Fig. 3b ). The temperature of the start of its formation (315°C) is somewhat lower than the point Ms of the initial steel but much higher than after the isothermal hold at 340°C. This indicates a lower redistribution of carbon between the α-and γ-phases in the process of formation of upper bainite and, as a consequence, a lower stability of the austenite. The bainite formed in the structure at a temperature above Ms has a granular structure. Its content can be assessed metallographically (Fig. 4b ). It amounts to about 80 and 60% at the isothermal hold at 360 and 380°C, respectively.
The ultimate strength of the steel depends little on the temperature of the isothermal hold and amounts to σr = 1400 – 1500 MPa. The ultimate strength is mainly affected by the content of the formed bainite, i.e., is minimal (σr = 930°C) when the temperature of the isothermal hold is 340°C, when the structure acquires up to 85% bainite. The contraction remains virtually invariable (ψ= 45 – 55%) and the elongation decreases from δ = 15% for the isothermal hold at 280°C to δ = 11% for the hold at 380°C.
When the temperature of the isothermal hold is raised from 280 to 340°C, i.e., in the range below Ms, the impact toughness decreases from 0.72 to 0.40 MJ/m2 (Fig. 5a ), which correlates with the content of bainite in the structure of the steel. Elevation of the temperature of the isothermal hold to > 360°C raises the impact toughness to 0.52 MJ/m2, which is also related to the decrease in the proportion of bainite in the structure. The data of Fig. 5b confirm that it is the formation of bainite, including the lower one, which causes the decrease in the impact toughness, i.e., prolongation of the time of the hold at 350°C from 5 to 90 min reduces the value of KCV from 0.72 to 0.49 MJ/m2. The behavior of the curve correlates with the kinetics of formation of bainite.
Step quenching known as “quenching-partitioning” [19] does not increase substantially the toughness and the ductility properties of the steel studied as compared to the treatment for martensite. In the case of a single-step quenching QP1, the level of the ductility is the same as after the oil quenching and low-temperature tempering, i.e., σ0.2 = 1290 MPa, σr = 1560 MPa. However, the value of the impact toughness (KCV = 0.68 MJ/m2) is lower than that of the steel with martensitic structure (KCV = 0.89 MJ/m2).
As a result of the two-step quenching QP2, the difference between the yield strength (σ0.2 = 945 MPa) and the ultimate strength (σr = 1550 MPa) is the highest, δ = 15%, KCV = 0.70 MJ/m2. The lowering of the yield strength of the steel in the case of the two-step quenching is a result of fuller occurrence of the bainitic transformation; the hold at 280°C is followed by an additional hold at 350°C in which the bainitic transformation continues to develop. The yield strength is also affected by the content of retained austenite, which should be somewhat higher in the case of the two-step quenching due to the greater fraction of bainite and the higher temperature promoting the redistribution of carbon.
After the step quenching with medium-temperature tempering (QPT) the strength characteristics of the steel (σ0.2 = 1300 MPa, σr = 1480 MPa) do not change substantially with respect to those obtained in QP1, but the level of the impact toughness decreases to KCV = 0.47 MJ/m2. This is connected with the development of temper brittleness. It has been shown [20] that tempering of martensite at a temperature above 300°C lowers the impact toughness of the steel from 0.89 to 0.15 MJ/m2. Tempering at 600°C, even despite the growth in the ductility (δ = 18%, ψ = 63%) does not promote growth in the impact toughness (KCV = 0.25 MJ/m2). This indicates that temper brittleness develops intensely due to nonuniform precipitation of carbide particles in the tempering of martensite and possible segregation of impurity atoms over the boundaries of martensite laths and grains.
Figure 6 presents the results of a comparative analysis of the mechanical properties of the studied steel after different heat treatments. It can be seen that the use of isothermal and step quenching does not cause considerable increase in the toughness and ductility parameters, i.e., the maximum impact toughness (KCV = 0.89 MJ/m2 ) is detected after quenching for martensite and low-temperature tempering (in this case σ0.2 = 1300 MPa, σr = 1540 MPa). In all the other cases (tempering of martensite, formation of bainite) the level of the impact toughness is not higher. The main reasons behind the lowering of the impact toughness of the steel, as well as of steel 30Kh2GSN2VM considered in [21, 22], are the insufficient stability of the retained austenite (which can be inferred from formation of martensite in cooling after the isothermal hold) and the temper brittleness due to precipitation of carbide particles. However, it should be noted that at σr = 1400 MPa (σ0.2 = 1000 MPa) isothermal quenching at 280 – 300°C provides the highest impact toughness in the steel as compared to quenching and medium-temperature tempering and normalizing or annealing (the variants with decelerated cooling from the austenitization temperature). Therefore, isothermal quenching can be expedient in some cases for attaining the required characteristics in ready parts.
Thus, the bainite in the steel studied possesses reduced toughness with respect to the martensite independently of its morphology and the temperature range of formation. Despite the reduced level of impact toughness under decelerated cooling, the high strength and ductility of the steel make it possible to use it for manufacturing large-size parts and to employ air or gas cooling media for its heat treatment.
It should be noted that the steel in question does not contain too much expensive alloying elements, and its cost should be 20 – 30% lower than that of its nearest counter- parts like 18Kh2N4MA, 25Kh2N4MA, 30Kh2GSN2VM etc.
Conclusions
-
1.
We have studied an advanced sparingly alloyed high-strength steel 20Kh2G2SNMA with Ac1 = 780°C and Ac3 = 860°C.
-
2.
When cooled continuously at a rate of 0.1 – 30 K/sec, the steel undergoes a bainitic transformation in the range of 355 – 480°C and a martensitic transformation below Ms = 355°C.
-
3.
When the cooling rate from the austenitization temperature is reduced by a factor or 1000 (from 20 to 0.02 K/sec), the strength of the steel decreases by only 10% (from 1540 to 1375 MPa), the ductility remains invariable (δ = 12 – 14%), but the impact toughness KCV lowers by 60% (from 0.89 to 0.35 MJ/m2).
-
4.
The impact toughness of the steel with bainitic structure is lower than that with martensitic structure, i.e., KCV = 0.4 – 0.7 MJ/m2 after isothermal (or step) quenching in the range of 280 – 380°C (bainitic-martensitic structure) and KCV = 0.89 MJ/m2 after oil quenching and low-temperature tempering (totally martensitic structure).
References
S. Zubchenko (ed.), Grades of Steels and Alloys [in Russian], Mashinostroenie, Moscow (2003), 784 p.
Shan and L. Fu, “Heat treating of air-hardening high-strength structural steels,” in: J. L. Dossett and G. E. Totten (eds.), Heat Treating of Irons and Steels, Vol. 4D, ASM Int., USA (2014), pp. 169 – 178.
V. M. Maisuradze, M. A. Ryzhkov, Yu. V. Yudin, and A. A. Ershov, “Heat treatment of parts with variable cross section from high-strength engineering steels,” Metallurg, No. 8, 101 – 104 (2014).
M. V. Maisuradze, Yu. V. Yudin, and D. I. Lebedev, “Thermal strengthening of large parts made from high-strength sparingly doped steel in air,” Steel in Trans., 50(5), 61 – 66 (2020).
G. F. Totten (ed.), Steel Heat Treatment. Metallurgy and Technologies, CRC Press (2006), 848 p.
Yu. N. Simonov, N. Panov, M. Yu. Simonov, et al., “Principles of design of the chemical composition of steels for forming a structure of lower carbide-free bainite under delayed cooling,” Metal Sci. Heat Treat., 57, 386 – 394 (2015).
L. E. Popova and A. A. Popov, Diagrams of Transformation of Austenite in Steels and of Beta-Solution in Titanium Alloys [in Russian], Metallurgiya, Moscow (1991), 503 p.
Transformation Characteristics of Direct-Hardening Nickel-Alloy Steels, The Mond Nickel Company, UK (1958), 91 p.
S. K. Berezin, A. A. Shatsov, P. O. Bykova, and D. M. Larinin, “Martensitic transformation in low-carbon steels,” Metal Sci. Heat Treat., 59(7 – 8), 479 – 485 (2017).
L. M. Kleiner, D. M. Larynina, L. V. Spivak, and A. A. Shatsov, “Phase and structural transformations in low-carbon martensitic steels,” Phys. Met. Metallogr., 108(2), 153 – 160 (2009).
J. Pacyna and L. Witek, “The effect of carbides on fracture toughness of steels of ferritic matrix,” Mater. Technol., 59(2), 68 – 74 (1988).
M. A. Ryzhkov and A. A. Popov, “Methodological aspects of plotting of thermokinetic diagrams of transformation of supercooled austenite in low-alloy steels,” Metal Sci. Heat Treat., 52(11 – 12), 612 – 616 (2011).
M. V. Maisuradze, M. A. Ryzhkov, Yu. V. Yudin, and A. A. Kuklina, “Transformations of supercooled austenite in a promising high-strength steel grade under continuous cooling conditions,” Metal Sci. Heat Treat., 59(7 – 8), 486 – 490 (2017).
M. V. Maisuradze, Yu. V. Yudin, and A. A. Kuklina, “A novel approach for analytical description of the isothermal bainite transformation in alloyed steels,” Mater. Perform. Charact., 8(2), 80 – 95 (2019).
K. W. Kim, K. I. Lim, C.-H. Lee, et al., “On control of retained austenite morphology through double bainitic transformation,” Mater. Sci. Eng. A, 673, 557 – 561 (2016).
Navarro-López, J. Hidalgo, J. Sietsma, and M. J. Santofimia, “Characterization of bainitic/martensitic structures formed in isothermal treatments below the Ms temperature,” Mater. Charact., 128, 248 – 256 (2017).
Argüelles, F. Barbés, J. I. Espeso, and C. Garcia-Mateo, “Cryogenic study of the magnetic and thermal stability of retained austenite in nanostructured bainite,” Sci. Technol. Adv. Mater., 20(1), 673 – 687 (2019).
J. G. Speer, “Phase transformations in quenched and partitioned steels,” in: E. Pereloma and D. V. Edmonds (eds.), Phase Transformations in Steels, Woodhead Publishing Ltd, Cambridge (2012), pp. 247 – 270.
L. Wang and J. G. Speer, “Quenching and partitioning steel heat treatment,” Metallogr., Microstr., Anal., 2, 268 – 281(2013).
M. V. Maisuradze, M. A. Ryzhkov, and D. I. Lebedev, “Microstructure and mechanical properties of martensitic high-strength engineering steel,” Metallurgist, 64(7 – 8), 640 – 651 (2020).
M. V. Maisuradze, Yu. V. Yudin, A. A. Kuklina, and S. I. Lebedev, “Formation of microstructure and properties during isothermal treatment of aircraft building steel,” Metallurgist, 65(9 – 10), 1008 – 1019 (2022).
M. V. Maisuradze, M. A. Ryzhkov, and D. I. Lebedev, “Mechanical properties of a mild-alloy steel for aerospace engineering,” Defect Diffus. Forum, 410, 221 – 226 (2021).
The work has been performed to implement grant No. 22-29-00106 of the Russian Scientific Foundation.
Author information
Authors and Affiliations
Additional information
Translated from Metallovedenie i Termicheskaya Obrabotka Metallov, No. 9, pp. 51 – 57, September, 2022.
Rights and permissions
Springer Nature or its licensor (e.g. a society or other partner) holds exclusive rights to this article under a publishing agreement with the author(s) or other rightsholder(s); author self-archiving of the accepted manuscript version of this article is solely governed by the terms of such publishing agreement and applicable law.
About this article
Cite this article
Maisuradze, M.V., Yudin, Y.V., Kuklina, A.A. et al. Effect of Heat Treatment on Mechanical Properties and Microstructure of Advanced High-Strength Steel. Met Sci Heat Treat 64, 522–527 (2023). https://doi.org/10.1007/s11041-023-00845-x
Received:
Published:
Issue Date:
DOI: https://doi.org/10.1007/s11041-023-00845-x