Abstract
Quality cost is not only the cost that manufacturing have to pay for poor quality, but also includes cost that has to be paid by the customers. In manufacturing, customers have a high quality product requirement. In producing high quality products, the manufacturer must improve the production process continuosly. Taguchi’s loss function is a common model to quantify the quality loss. Taguchi’s loss function can be applied to nominal the best, smaller the better, and larger the better quality characteristic. In this study, we developed an optimization model to determine the optimal process parameters by taking into consideration of the imperfection of quality inspection. The imperfect quality inspection involves two kind of errors, namely Type I and Type II errors. Inspectors may make an error in categorizing non-defective items as defectives and some defective items as non-defectives. The inspection errors will increase the quality cost as one components of total cost considered in this study. From the numerical example, the calculation results are the expected cost for 100% inspection is $ 3.1395, and the expected cost for proposed model is $ 3.0898 with the optimal process mean for the proposed model is µn = 15.411 mm, the optimal standard deviation is σn = 0.20076 mm and the optimal multiplier of standard deviation is r = 3.996.
Access provided by Autonomous University of Puebla. Download conference paper PDF
Similar content being viewed by others
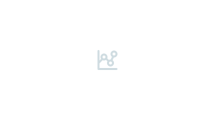
Keywords
1 Introduction
The development of knowledge, and technology among companies is has made competition getting tighter. The company is required to produce high-quality with low-cost products. Five manufacturing competitive priorities - quality, flexibility, cost, delivery and innovation [1]. It becomes a challenge for companies to produce products with the higher quality, lower selling price as other competitors butat the same time can minimize the manufacturing cost. Quality cost has to be reduced by the companies mean that they have to give more attention to their quality problems. Hence, quality improvement must be carried out continuously to reduce the quality costs.
Quality improvement is the reduction of variability in processes and products [2]. Quality costs or cost of quality is a means to quantify the total cost of quality-related efforts and deficiencies [3]. Quality costs are often a direct result of the hidden factory that is, the portion of the business that deals with waste, scrap, rework, work-in-process inventories, delays, and other business inefficiencies [2]. Many manufacturing and service organizations use four categories of quality costs: prevention costs, appraisal costs, internal failure costs, and external failure costs [2]. In 1987, Kapur [4] pointed out that the present process can be improved, then a short term approach to decrease variance of the items shipped to the customer is to put spesification limits on the process and truncate the distribution by inspection.In their research, [4] applied the Taguchi’s quadratic quality lossfunction for designing the economic specification limits of the qualitycharacteristic with normal distribution. Taguchi’s idea is to replace the concept of “Quality” by its complement “Quality Loss”. This means that parts of acceptable quality inherent the lowest quality loss, particularly zero. On the other hand, the engineering experience shows that quality degrades, with some exceptions, continuously [5]. Taguchi’s main objectives are to improve process and product design through the identificationof controllable factors and their settings, which minimize the variation of a product around atarget response [6].
Reference [7] developed a model based on the research of [4] by determining the optimal value of spesification limits and the adjusment process parameters. The Model of [7] aims to determine the total quality loss by adjusment of product’s process parameter i.e. mean, standard deviation, and the spesification limits. The model involved quality inspection activities but the inspection is assumed to be perfect. Inreality, the inspection carried out by an inspector must have inspection errors. The inspector may make an error in an his inspection which has two types of error, namely Type I and type II errors [8]. In this research, we extend the research of Kao [7] by incorporating imperfect inspection to determine the optimal value of certain quality characteristic process parameters with the objective function to minimize total quality cost.
2 Assumption and Notation
This paper has the following three assumptions, there are:initial process mean and standar deviation are known, product quality characteristic are normally distributed and scrap cost, adjusted mean cost, adjusted standard deviation cost, cost of falsely accepting a defective products and cost of falsely rejecting a non-defective products are known
The following notations are used in this paper:
-
\( \gamma \): percentage of defective items
-
\( \gamma_{\text{e}} \): percentage of defective items observed by the inspector
-
m1: random variable representing Type I error
-
m2:random variable representing Type II error
-
Ca: cost of falsely accepting a defective products (Type I)
-
Cr: cost of falsely rejecting a non-defective products (Type II)
-
ICa: cost of falsely accepting a defective products
-
ICr: cost of falsely rejecting a non-defective products
-
MC: adjusting mean cost per unit
-
DC: adjusting standard deviation per unit
-
SC: scrap cost per unit
-
k: loss cost per unit
-
\( y_{0} \): target value
-
\( \sigma_{1} \): initial standard deviation
-
\( \sigma_{2} \): minimum standard deviation under the ideal production
-
\( \sigma_{n} \): optimal standard deviation
-
\( \mu_{n} \): optimalmean process
-
\( \sigma_{t,n} \): standard deviation of truncated normal distribution
-
\( \mu_{t,n} \): mean of truncated normal distribution
-
\( q_{n} \): probabilities that a random variable falls inside the specification limits
-
u: \( \left( {y_{0} - \mu_{n} } \right)/ \sigma_{n} + w \)
-
v: \( \left( {y_{0} - \mu_{n} } \right)/ \sigma_{n} - w \)
-
r: multiplier of standard deviation
-
\( \phi \left( . \right) \): PDF of the standard normal distribution
-
\( \varPhi \left( . \right) \): CDF of the standard normal distribution
-
\( y_{n} \): random variable of normal distribution.
3 Model Development
3.1 The Basic Model
Basic Total Expected Cost
Reference [7] proposed a quality loss model using Taguchi loss function and process capability indices for normal distribution. Kao’s model aimed to determine the optimal adjusted process mean, adjusted standard deviation and specification limits. The components of total cost includes inspection cost (cost false of rejection and cost false of acceptance), scrap cost, and adjusted process cost. They assumed that quality characteristic Y follows the normal distribution with known mean and variance. According to [7], the total expected cost (TC) can be expressed as Eq. (1).
The expected quality loss for nominal-the-best type quality characteristic is presented as
Where
Imperfect Inspection Cost
Errors in the inspection process will result in additional costs that must be incurred by the manufacturer. According to Khan [8], there are two types of costs arising from inspection errors, namely cost of false rejection (Cr) and cost of false acceptance (Ca). The cost of false rejection occurs when the inspectors make a type I error, which is they classify the non-defective product as a defective one. While the cost of false acceptance occurs when the inspectors make a type II error, which is they classify a defective product as a non-defective one. The fraction of defective units as perceived by the inspectors would be:
Where
The total cost of false rejection (Cr) and cost of false acceptance (Ca) are shown in Eqs. (10) and (11) respectively.
3.2 Proposed Model
The total expected quality loss per item in this research is expressed in Eq. (12)
This proposed model is combined model [7] and [8] that is calculate the minimum totally expected loss model considering imperfect inspection for normal distribution
4 Numerical Example
In this research, we use backrest thread component as the case study of numerical example. The product is one of components of hospital bed of the Supramax 73004 type produced by MAK (Mega AndalanKalasan), there is backrest thread 180 mm. The process used in the backrest thread are cutting and turning. The backrest thread 180 mm divided into 2, namely minor diameter and major diameter. In this study, we will use only the minor diameter data. We collected 40 data to estimate the initial mean and standard deviation. Table 1 lists sample of minor diameter of backrest thread 180 mm.
Backrest thread has a major diameter of 18.70 mm, minor diameter of 15.40 mm with 180 mm length. From the table, the initial mean \( \mu_{1} = 15.59625 \) mm and the initial standard deviation \( \sigma_{1} = 0.20076 \) mm. The process mean does not meet the target because the value of process mean is larger than the target (y0 = 15.40 mm).
For 100% inspection, Let k = 8, IC = 0.1, SC = 2, MC = 1, DC = 1 and the ideal standard deviation (σ2) is 0.05 mm. By Kao (2010) model, the optimal process mean is µn = 15.411 mm, the optimal standar deviation is σn = 0.20076 mm and the optimal multiplier of standard deviation is r = 3.996. The total expected cost is TC = $ 3.1395, and specification limits LSL = 14.5977 mm and USL = 16.2023 mm.
For the proposed model in this research, let k = 8, ICa = 0.5, ICr = 0.2, SC = 2, MC = 1, DC = 1, m1 = m2 = 0.2, r = 3 and the ideal standard deviation (σ2) is 0.05 mm. The optimal process mean for the proposed model is µn = 15.411 mm, the optimal stand- ard deviation is σn = 0.20076 mm and the optimal multiplier of standard deviation is r = 3.996. Hence, we get the total expected cost of TC = $ 3.0898 with the specification limits of LSL = 14.5977 mm and USL = 16.2023 mm. The initial value of the standard deviation is optimal, so there is no adjusment for standard deviation parameter process (σn).
From the results above, the proposed model has a lower total expected cost than the previous model. Total expected cost that considering imperfect inspection results is lower than considering perfect inspection. This is due to perfect inspections carried out on all products so that inspection costs are high. But it is quite realistic to account for Type I and Type II errors committed by inspectors in this process. So there will be an additional costs for Type I errors, and for Type II errors it is possible returned products from the market. With lower total expected cost, the proposed model gives benefit for both manufacturer and buyer in the form of cost and quality of the product.
5 Conclusion
In manufacturing, the buyer has a high quality product requirement. High quality means the manufacturer must spend a lot of funds. The base model [7] have presented a totally expected quality loss model using Taguchi’s loss function for normal distribution. Reference [8] describe that inspection cost divided into two costs, such as cost of false rejection occurs when the inspector makes a type I error, and the cost of false acceptance occurs when the inspector makes a type II error. This study proposed modified totally expected loss model considering imperfect inspection for normal distribution. In [7] model’s, involved quality inspection activities but the inspection is assumed to be perfect. In this study, inspection which has two types error. From the calculation results, the expected cost for 100% inspection is $ 3.1395, and the expected cost for proposed model is $ 3.0898. Model that considering imperfect inspection has a lower expected cost than 100% inspection. With lower total expected cost, the proposed model gives benefit for both manufacturer and buyer in the form of cost and quality of the product.
References
Russel, S.N., Millar, H.H.: Competitive priorities of manufacturing firms in the Caribbean. IOSR J. Bus. Manage. 16(10), 72–82 (2014)
Montgomery, D.C.: Introduction to Statistical Quality Control, 7th edn. Wiley, New York (2012)
Feigenbaum, A.V.: Total quality control. Harvard Bus. Rev. (1956)
Kapur, K.C., Wang, C.J.: Economic design of specifications based on Taguchi’s concept of quality function. In: The Winter Annual Meeting of the American Society of Mechanical Engineer, Boston, pp. 23–36 (2010)
Academia. https://www.academia.edu/4265348/Taguchi_loss_function. Accessed 17 July 2019
Vacarescu, C.F., Vacarescu, V.: The Taguchi’s quality loss function in development and design for bulk goods in the automotive field. In: Annals of DAAAM for 2010 and Proceedings of the 21st International DAAAM Symposium, vol. 21, no. 1 (2010)
Kao, S.C.: Deciding optimal spesification limits and process adjusments under quality loss function and process capability indices. Int. J. Ind. Eng. 17(3), 212–222 (2010)
Khan, M., Jaber, M.Y., Ahmad, A.R.: An integrated supply chain model with errors in quality inspection and learning in production. Omega 42, 16–24 (2014)
Acknowledgement
This research was fully funded by Research and Community Service (P2 M) PNBP funds 2019 budgeting year with contract number 516/UNS27.21/PM/2019.
Author information
Authors and Affiliations
Corresponding author
Editor information
Editors and Affiliations
Rights and permissions
Copyright information
© 2020 Springer Nature Singapore Pte Ltd.
About this paper
Cite this paper
Ramadhanty, M.D., Rosyidi, C.N., Jauhari, W.A. (2020). A Quality Improvement Model Based on Taguchi’s Loss Function Considering Imperfect Quality Inspection. In: Osman Zahid, M., Abd. Aziz, R., Yusoff, A., Mat Yahya, N., Abdul Aziz, F., Yazid Abu, M. (eds) iMEC-APCOMS 2019. iMEC-APCOMS 2019. Lecture Notes in Mechanical Engineering. Springer, Singapore. https://doi.org/10.1007/978-981-15-0950-6_20
Download citation
DOI: https://doi.org/10.1007/978-981-15-0950-6_20
Published:
Publisher Name: Springer, Singapore
Print ISBN: 978-981-15-0949-0
Online ISBN: 978-981-15-0950-6
eBook Packages: EngineeringEngineering (R0)