Abstract
This study intends to investigate how copper chill affects the fatigue behaviour of composites made of aluminium alloy A356 and hematite. It was cast by altering the weight fraction particles of hematite (0 to 12%wt in increments of 3%wt) by sand casting method with and without copper chills at its end to get isotropic and homogenous significant characteristics under liquid metallurgical way. The test specimens were prepared in accordance with ASTM specifications. Ducom-type fatigue testing equipment (rotating bending-low cycle fatigue) is used in experiments to examine fatigue behaviour. The micrographic images were taken with a scanning electron microscope (SEM) and interpreted uniform reinforcement of hematite particles, and X-ray diffraction (XRD) patterns were used to reveal microscopic details. The existence of the hematite particles and their phases was revealed by the X-ray diffraction analysis. The results show that the composites cast with copper chills have significantly greater fatigue strength than the casting obtained without copper chills. It was also observed that at 9%wt, copper chilled composite shows improve in fatigue strength about 10.2% as compared without chilled composites.
Similar content being viewed by others
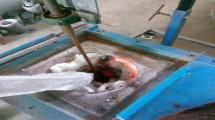
Avoid common mistakes on your manuscript.
1 Introduction
The contemporary scientific community, the most common alloy utilized in industries to improve performance is an aluminium alloy. Aluminium matrix composites (AMCs) are widely employed in a variety of applications, including automotive, defence, and aviation, because of their high toughness, hardness, strength, ductility, corrosion and wear resistance. The addition of strong iron ore particles known as hematite to an aluminium matrix, has increased wear resistance qualities for usage in wear and tear applications [1,2,3]. By employing metallic elements such as copper as end chills in sand casting of aluminium alloys has revealed improved microstructure, mechanical and tribological properties [4, 5]. Chilled casting using sand moulds through the liquid metallurgy process is the most efficient and widely used way for metal matric composites (MMCs) castability [6]. Vasanth Kumar et al. [7] studied the fatigue and fracture behaviour of a cast Al6061 alloy reinforced with a Boron Carbide (B4C) composite.
The addition of B4C particle reinforcement depicts the improved fatigue strength and fracture toughness of the AMCs. Mahendra et al., [8] reported the fatigue and fracture behaviour of an Al6061 alloy blend with a different weight percentage of aluminium oxide Al2O3 MMCs, and it was found that the fatigue strength of an Al 6061 with 4% wt of Al2O3 composite specimen has been enhanced by 12% when compared to the base alloy. It was also found that the fatigue property and facture stress are significantly impacted by Al2O3. Krishnaraj et al., [9] reported the fatigue behaviour of the Al 6061 blend with a diverse weight percentage of SiC, TiO2, and magnesium (Mg) hybrid reinforced composite at room temperature.
A low-cycle fatigue study has been conducted for the prepared composites. It was found that the addition of reinforced particles to the hybrid composites enhanced the fatigue strength by 380 MPA. Sanju et al., [10] investigated the corrosion and fatigue behaviour of Al LM13 blend with hematite particles at varying percentages of Metal Matrix Composite (MMCs) and it was observed that the heat-treated fatigue specimen illustrates higher fatigue strength than the as-cast samples. Furthermore, it was noticed that the heat-treated corrosion test specimen revealed a lower corrosion rate than as compared to as-cast samples. Achutha et al., [11] reported that the fatigue and mechanical properties of Al LM 25 mixed with hybrid composite for different weight segments of silicon carbide (SiC) and graphite particles were examined. It was found that the fatigue life of Al-SIC-Gr hybrid composites containing 2.5 wt% isexperimentally determined at different stress levels (0.9 σu, 0.7σu and 0.5σu, σu = ultimate strength of the composite) and associated with that of LM 25 alloy. When Compared to the base alloy LM 25, the hybrid composite displayed an improved fatigue resistance by 15%.
Myriounis et al., [12] reported on the fatigue behaviour of Silicon Carbide (SiC)-blend with Al A359 alloy matrix composite; a variety of thermal treatments (T6, HT1 and T1 condition) have been performed on the A356/SiC composite. It was found that higher fatigue strength was observed at T6 heat treated as compared with T1 and HT1, and also stated that heat treatment had a significant consequence on fatigue strength. Ramesh et al., [13] studied the stir casting technique was adopted to prepare the composites of Al6061 blend with diverse weight segments of silicon carbide (SiC) and zirconium dioxide (ZrO2). The composite was prepared with two combinations, first (Al + 5% wt of Sic) and second (Al + 3%wt of ZrO2 + 2%wt of Sic). The prepared samples were subjected to hardness, tensile and fatigue studies. It was noted that the second composition showed higher hardness (53.6 BHN) tensile (96.143 N/mm2) and fatigue (life cycle to failure of 105 cycles with a stress value of 79.062 MPa) values as compared with the first composition hardness (42.9 BHN), tensile (67.229 N/mm2) and fatigue (104 cycles with a stress value of 150.651 MPa).
Girija Moona et al., [14] studied the fatigue properties of hybrid composites, which were synthesized by the reinforced Al 7075-T6 with diverse weight fractions of eggshell, aluminium oxide and particles of silicon carbide cast through an electromagnetic stir casting approach. The developed samples were experimented by means of a rotating beam fatigue testing machine. It was found that the hybrid composite samples (Al 7075-T6 + 1.5% wt of egg shell + 1.5%wt of Al2O3 + 1. 5%wt of Sic) depict significant improvement in fatigue strength (4560 load cycles) as compared to the as-cast (94 load cycles) composite. Ramesh et al., [15] have studied the fatigue behaviour of Al6061 alloy armored with Ni–P coated Silicon Nitride (Si3N4) particles at diverse weight fractions. It was found that the fatigue strength of hot forged (500°c with a 300-ton hydraulic hammer) and as-cast mixtures are significantly enhanced by increasing the reinforcement content. It was noticed that forged alloys and composites have greater fatigue strength than their cast matrix alloys. The above literature studies have revealed that little research has been carried out on the fatigue behaviour of composites made up of A356-hematite particles. Takao Kobayashi and Donald [16] studied the fracture surface topography analysis (FASTA) to analyze the failure initiation time and load conditions, average crack growth rate and details such as accelerations, decelerations, hesitations, and arrests. The details of micro failure initiation and how a crack front interacts with microstructural features and fracture toughness and other continuum fracture mechanics parameters are got directly from a fracture surface. Gonzalo et al., [17] studied the crack propagation and fatigue endurance on Al 6063 at T5 using rotating bending fatigue testing machine for pre corroded and post corroded specimens. The corrosion test carried out with hydro chloric acid as a corrosion agent, results depict that rotating bending fatigue endurance decreases with time of corrosion attack in pre-corroded specimens. The fracture surfaces analysis shows that corrosion pitting holes were the sites for crack initiation and propagation. Wojciech Macek [18] studied the distribution of fracture surface roughness on 2017 A –T4 aluminium alloy under bending fatigue using surface measurement technique by using fracture zone concept. Result depicts that the fatigue fracture surfaces have smallest roughness values at the crack initiation stage and a gradual increase during the fatigue crack growth stage [19,20,21].
The present investigation aims to determine the fatigue fracture behavior of developed A356-hematite particulate composites using sand casting technique followed through chill casting (copper chill in all the four sides) seems to be new in the composite and tested using ducom-type fatigue testing equipment under the influence of copper chill. EDAX, XRD, and SEM photos were used to study the presence of reinforcement and microstructure of the developed composites and also studied the fatigue fractured surface analysis and fractography. The SEM images are used to study the combination of fractured modes on fractured surface and fractography gives evidence to the mode of fracture.
2 Experimental details
2.1 Material selection
The A356 alloy was chosen as a matrix material because, it has wide range of applications in the automotive and aerospace sectors. The hematite particles between 80 and 100 µm in size were chosen as reinforcement as shown in Fig. 1. Tables 1 and 2 depict the reinforcement and matrix materials, along with their chemical compositions [10, 22]. Tables 3 and 4 list the additional (other) properties of both materials [22].
2.2 Composite preparation
The stir-casting technique was used to produce a metal matrix composite reinforced with hematite particulate. The A356 alloy is melted at 752 °C with continual stirring at 560 rpm in a 6-KW electric resistance oven. After being preheated to 400 °C, hematite particles were added to a furnace containing a molten A356 metal alloy (at 750°C) and the stirring is continued for several minutes. The reinforcement and matrix are thoroughly wetted by continual whirling (Fig. 2). The prepared molten metal was poured to both with and without copper chilling which results in a heated sand mould as shown in Fig. 3. For various hematite particle weight proportions, the casting process was repeated with base alloy ranging from 0 to 12% in a step size of 3%. Figure 4 demonstrates how the casting was done by using copper chilling to make a sand mould that was 170 × 200 × 25 mm in size for various reinforcement combinations. The process diagram of the work is demonstrated in Fig. 2 [25].
2.3 Experimentation
The fatigue specimen having a diameter of 6.35 mm and length 101.6 mm were machined in cast composite as shown in Fig. 5. A rotating-bending type low cycle Fatigue Test machine as shown in Fig. 6a (made by Ducom Instruments, Bangalore) with model number TM7001 was utilized to conduct the fatigue tests at room temperature in accordance with ASTM E606 standard, along with specimen attachment as shown in Fig. 6b. The specifications of DUCOM Machine as shown in Table 5. During the tests, 50 Hz (3000 revs/min constant) cyclic frequency was maintained with an application of rotating bending stress with a stress ratio (R) of 1. The fatigue life (Nf) is considered as the number of cycles (stress) until complete separation or failure occurs. The gauge segment of the test samples was maintained at a constant surface finish of 1 μm by using fine grades of emery paper to minimize the effect of surface irregularities. Further the maximum stresses varied from 50 to 260 MPa. The average of three results was used to find out the life of fatigue (Nf).
The stress produced in test samples due to fatigue is calculated from the observed experimental data using the equations (for rotating bending type) for both without and with copper chill composites.
where M b = \(\frac{FL}{4}\) – Bending Moment,Z =\(\frac{\mathrm{\pi d}3}{32}\)—Section Modulus.
After being metallographically prepared for microscopic investigation and the microstructure samples were etched using Keller’s solution and then images are printed using scanning electron microscope (SEM). The microstructure of copper cold samples with varied weight percentages is shown in Fig. 14 and SEM was used to examine the size, shape, and dispersion of hematite particles in A356 alloy mixtures. The EDX test was conducted using JDE 2300 Software, which was coupled to the SEM apparatus. The SEM examination was performed on specimens with a microstructure that measured \(5\) mm in height and 15 \(\mathrm{mm}\) in diameter. A machine polishing velvet substance was used to achieve a faultless surface quality. The following are polished with 44 \(\mathrm{m}\) m-thick paper and the specimen's surface was ground with 240, 600, and 800 grind sheets. The specimens were cleaned with distilled water to remove contaminants like dust or other foreign particles that were on the polished surface. Finally, Keller's reagent was used to etch the samples’ surfaces. [17].
In order to distinguish between different phases in Al alloy matrix compositions, X-ray diffraction investigations on A356 alloy composites were performed. For the XRD experiments, the A356 alloy with 9% wt hematite composites was employed with a specimen size of \(15 \mathrm{mm}\) in diameter and \(2\mathrm{ mm}\) in height [18]. Panalytical XRD experiments were carried out with CU-K alpha radiation, and the two range is meant to encompass all the intense peaks of the predicted segments of material. [19].
The zones of fatigue, where the load is completely reversed are captured using fractography of the samples and the consistent striations and haphazard positions of fracture fronts is seen in the fractography produced by SEM.
3 Results and discussion
3.1 Microstructure analysis
According to the micrograph results, the hematite particles appear to be discretely distributed throughout the A356 matrix at various weight fractions, as shown in Fig. 7 a to e. This is due to efficient stirring produced by using the right process parameters. The mixtures’ fatigue resistance will be increased by using homogenous dispersion on the hematite components and the quick cooling rate will impose a fine-grained structure by using copper chill, which also improves the performance under fatigue [23].
The elemental analysis of A356 with a combination of 9% wt hematite is shown in Fig. 8. The dispersion of hematite particles in the A356 alloy mixture is confirmed by the presence of \({\mathrm{Fe}}_{2}{\mathrm{O}}_{3}\) and MgO. A356 and A356-9wt% hematite composites were subjected to X-ray Diffractometer examination with several aluminium phases present at different peaks is shown in Fig. 9a at various intensities of 390, 450, 650, and 7 80. The maximum intensity A1 phases is 390 [25].
Figure 9b displays the XRD pattern of A356 with 9% hematite particles. It shows a number of different phases, including Al and \({\mathrm{Fe}}_{2}{\mathrm{O}}_{3}\). While hematite particles phases are found at 290, 470, 560, and 780, the JCPDS form of the produced Al-Hematite fusions is 98–6077 with various angles at 2θ with varying intensities [22,23,24].
3.2 Fatigue strength
Figures 10 and 11 depict the outcome of stress versus the number of cycles of failure for the composites of A356-Hematite without and with copper chill conditions, respectively. From the experimental results, it was found that the fatigue life increases with a decrease in stress amplitude because of the addition of hard hematite particles in the composite. The development in the fatigue strength of the developing mixes remains significant at lower stress levels than at higher stress levels in both without and with copper chill composites [11]. In both cases, the maximum heaviness proportion of hematite elements showed substantial development in fatigue strength of the mixtures as associated with an un-reinforced alloy. This is due to the existence of solid hematite elements. It was also observed from the experimental results that, the mechanical properties of composite like tensile strength, bending and fatigue are highest for 9% of composites as compared to other beyond that (for 12% hematite particles), these values are decreased due brittleness property of the reinforcement [20].
The consistent size and dispersal of hematite elements over the composites enhance the plastic strain necessary for crack initiation into the composite materials. The fatigue strength improves with the volume segment of the components due to the weight existing passed to the harder particle strengthening and overall lowered strains for specified fatigue stress. The creation of voids leads to the proliferation of cracks at a quicker rate. It was also reported that chilled composite specimens show higher fatigue strength than copper chill specimens. The rapid chilling effect will impose a fine-grained structure by employing copper chill which also optimize fatigue performance of 10.2% for 9%wt of composites with copper chill specimens as compared to without copper chill specimens which is due to the presence of iron oxide and magnesium oxide in the composites [15, 24].
3.3 Fractured surface analysis
Figure 12a to d depicts the fatigue fracture surfaces of A356-hematite 9%wt composites with and without a copper chill. It was noted that the following combination of fracture modes evidently present in fractured surfaces are discussed [18]
-
A crack initiates and propagates in a matrix substantially.
-
Fracture and Decohesion of reinforced particles.
-
Development of macro and micro voids in the matrix substantial
-
Fractography study
The surface of a fractured area without copper chill composite consists of dimples, macro and micro voids (Fig. 12 a) whereas the chilled composite contains micro voids and displays limited ductility (Fig. 12 b). The Initiation of crack for 9%wt of composite without copper chill is show in Fig. 12c, it is evident from the SEM images of the fractured surface that, the crack initiation in the 9%wt of composite without copper chill is associated with the presence of porosity. The existence of porosity act as a stress concentrator and facilitates the initiation crack. Further, the crack is seen in Fig. 12a that it has originated from the surface from without copper chill composite. There was no indication of particle decohesion or fracture can be seen in the region around the crack. In addition, particle fracture has been observed in several regions of chilled composites as shown in Fig. 13. Thus, it is evident that crack initiation is due to surface imperfections/porosities in composites of copper without chill and not at the matrix-particle interface region [13].
Since the crack originated at the defective point, it circulated along the regions of the weakest portion (i.e., in the alloy of a matrix), because of the existence of hematite elements that act as robust obstacles (Fig. 14). The various micro porosities in the alloy of the matrix inter-relate through a crack, causing the high development proportion of the crack. The matrix region about the reinforced segment exhibits micro voids due to the condensed ductility of the alloy of the matrix [15].
Though the initiation and propagation of the crack in the matrix region of chilled composites are away from the particles, so there are no cracks are observed at the interface (Fig. 15).
It has been found that without copper chill mixtures have multiple crack initiation points (Fig. 16). But in chilled composites crack initiation points are significantly fewer. Because of the huge volume fraction and unvarying spreading of hematite particles. The crack proliferation velocity is constantly higher in composites without copper chill due to limited restraints. However, the propagation of cracks has remained restricted in the chilled mixtures due to the huge constraints. Hence, the principal mechanisms of fracture in chilled composites are the creation of micro-voids in the region of the matrix and cracks in the reinforcement elements. The fracture in the chilled composites has flat (flat fractured) surfaces due to the partial ductility of the matrix, indicating brittle fracture (Fig. 17).
The chilled A356-hematite composites exhibit large quantities of voids due to the brittle flow of matrix material and the decohesion of reinforcement phases. It also seems that the bigger-sized reinforced elements have remained fractured, also decohesion has ensued with the minor-sized elements. A few of the voids have been found in fractured surfaces which have a diameter that is greater or smaller than the normal size of the reinforced elements [25].
3.4 Fractography
Figure 18a and b shows that clear inferences are often drawn by reference to the method of fracture which is a brittle one, shown by the cleavage facets from the transgranular crystallographic plane & cleavage is a representative of transgranular brittle fracture [19]. An intergranular fracture can be identified by the appearance of “rock candy structure” when the crack follows grain boundaries. The semi-elliptical lines are observed in the fractography are a sign of striations that arises outward from the origin and mark the crack front location with each successive stress cycle. The arrangement of fatigue striations is typically uniform. The crescent-shaped marks can be referred as “beach marks” indicates the succeeding stages of advanced crack growth that ensue due to variations in loading or varying stress intensity. In order to analyze the failure mechanism within a component, the Fractography of a fatigue specimen is precious [17].
4 Concluding remarks
The composites of A356-hematite without and with copper chill were prepared through sand casting practice. The microstructural analysis clearly reveals the presence of hematite elements dispersed throughout the matrix of an alloy of A356 and its mixtures. The XRD analysis reveals the presence of hematite particles and their phases in the A356 alloy matrix. Using a Rotating Bending Machine (RBM-ASTM E606 standard), the fatigue strength and number of cycles to failure of A356-Hematite composites were calculated. The outcome of the study are as follows.
-
The fatigue strength was found to be increased by 10.2% for 9wt% of composites with copper chill specimens as compared to those without copper chill specimens.
-
Due to the presence of iron oxide and magnesium oxide in the composites, the specimens of the copper-chilled composite are stronger than those without copper chill composites.
-
There was an improvement in fatigue strength at lower stress levels (63.5 MPa) both without and with copper chill composites compared to higher stress levels (254 MPa).
-
Crack initiation is caused by surface defects or porosities in the matrix alloy, not in the portion of the matrix and particle interface.
-
The cleavage facets from the trans granular crystallographic plane and striations indicate that the overall mode of fracture is a brittle in nature.
-
It is concluded from the results that hematite plays a substantial role in enhancing the fatigue behaviour of the aluminium matrix composite.
Data availability
All data used in this manuscript have been presented within the article.
Abbreviations
- σ :
-
Stress
- Z :
-
Section Modulus
- M b :
-
Bending Moment
- FL:
-
Force
- Nf:
-
Fatigue Life
- RBM :
-
Rotating Bending Machine
- AMCs :
-
Aluminium matrix composites
- SEM :
-
Scanning electron microscope
- XRD :
-
X-ray diffraction
- B 4 C :
-
Boron Carbide
- MMCs :
-
Metal Matrix Composite
- SiC :
-
Silicon carbide
- ZrO 2 :
-
Zirconium dioxide
- Si 3 N 4 :
-
Silicon Nitride
- FASTA :
-
Fracture surface topography analysis
- ASTM :
-
American Society for Testing and Material
- JCPDS :
-
Joint Committee on Powder Diffraction Standards
- MPa :
-
Mega Pascal
- EDX :
-
Energy-dispersive X-ray
References
American ASM Handbook Properties and Selection: Nonferrous Alloys and Special-Purpose Materials (1990) 2:PP 1-1328
ASM Handbook, Fatigue and Fracture (1996) 19:PP. 1-2592
Heinz A, Haszler A (2000) Recent developments in aluminum alloys for aerospace applications. Mater Sci Eng 1:102–107
Seah KHW, Hemanth J, Sharma SC, Rao KVS (1999) Solidification behavior of water-cooled and subzero chilled cast iron. J Alloys Compd 290:172–180. https://doi.org/10.1361/105994901770345231
Naeem HT, Abdullah FF (2019) Effects of garnet particles and chill casting conditions on properties of aluminum matrix hybrid composites. Eclética QuímicaJournal 44(2):1678–4618
Hiremath A, Hemanth J (2017) Experimental evaluation of the chill casting method for the fabrication of LM-25 aluminum alloy-borosilicate glass(p) composites. Adv Mater Eng Mater 748:69–73. https://doi.org/10.4028/www.scientific.net/KEM.748.69
Vasanth Kumar HS, Kempaiah UN, Mallesh G (2020) Fatigue and fracture behaviour of Al6061-B4C aluminium matrix composites. Int J Eng Adv Technol (IJEAT) 9(4):121–2125
Mahendra HM, Prakash GS, Keerthi Prasad KS, Rajanna S (2020) Fatigue and facture behaviour of Al6061-Al2O3 metal matrix composite: effect of heat treatment. IOP Conf Series: Mater Sci Eng 925:1–15. https://doi.org/10.1088/1757-899X/925/1/012042. (ICCEMS-2020)
Krishnaraj S, Elatharasan (2020) Fatigue behaviour of aluminium reinforced metal matrix hybrid composites. Int J Rapid Manuf 9(1):16–24. https://doi.org/10.1504/IJRAPIDM.2020.10026150
Sanju H, Reddy MM, Chandra BT, Madhu B (2016) Evolution of fatigue and corrosion test of Al LM13 reinforced with hematite. Int J R Eng Technol 5(6):219–223
Achutha MV, Sridhara BK, Budan A (2008) Fatigue life estimation of hybrid aluminium matrix composites. Int J Des Manuf Technol 2(1):14–21. https://doi.org/10.18000/ijodam.70022
Myriounis DP, Matikas TE, Hasan ST (2012) Fatigue behaviour of SiC particulate-reinforced A359 aluminium matrix composites. Int Exp Mech 48:333–341. https://doi.org/10.1111/j.1475-1305.2011.00827.x
Ramesh S, Govindaraju N, Suryanarayan CP (2018) Investigation on mechanical and fatigue behaviour of aluminium based SiC/ZrO2 particle reinforced MMC. IOP Conf Ser: Mater Sci Eng 346:1–8. https://doi.org/10.1088/1757-899X/346/1/012030
Moona G, Walia RS, Rastogi V, Sharma R (2019) Parametric optimization of fatigue behaviour of hybrid aluminium metal matrix composites. Mater Today Proc 21:1441–1445. https://doi.org/10.1016/j.matpr.2019.10.002
Ramesha CS, Keshavamurthy R, Madhusudhan C (2014) Fatigue behavior of Ni-P coated Si3N4 reinforced Al6061 composites. ICMPC 2014 Procedia Mater Sci 6:1444–1454. https://doi.org/10.1016/j.mspro.2014.07.124
Kobayashi T, Shockey DA (2010) Fracture surface topography analysis (FRASTA)—development, accomplishments, and future applications. Eng Fract Mech 77(12):2370–2384. https://doi.org/10.1016/j.engfracmech.2010.05.016
Domínguez GM, Almaraz JL, Ambriz Á, Calderón EC (2012) Fatigue endurance and crack propagation under rotating bending fatigue tests on aluminum alloy AISI 6063–T5 with controlled corrosion attack. Eng Fract Mech 93:119–131. https://doi.org/10.1016/j.engfracmech.2012.06.012
Macek W (2022) Fracture surface formation of notched 2017A–T4 aluminium alloy under bending fatigue. Int J Fract 234:141–157. https://doi.org/10.1007/s10704-021-00579-y
Srivatsan TS, Al-Hajri M, Petraroli M, Hotton B, Lam PC (2002) Influence of silicon carbide particulate reinforcement on quasi static and cyclic fatigue fracture behavior of 6061 aluminium alloy composites. J Mater Sci Eng Elsevier 325:202–214. https://doi.org/10.1109/FAME.2010.5714802
Umesh H, Suresh N, Sundresh S (2016) Fatigue behaviour of fly ash reinforced with LM6 aluminium metal matric composite. Int J Adv Sci Res Eng (IJASRE) 02(09):1–13
Ceschini L, Minak G, Morri A (2006) Tensile and fatigue properties of the AA6061/20 Vol.% Al2O3p and AA7005/10 Vol.% Al2O3p composites. Compos Sci Technol 66:333–342. https://doi.org/10.1016/j.compscitech.2005.04.044
Santhosh N, Kempaiah UN, Sajjan G, Gowda AC (2017) Fatigue behaviour of silicon carbide and fly ash dispersion strengthened high performance hybrid Al 5083 metal matrix composites. J Miner Mater Charact Eng 5:274–287. https://doi.org/10.4236/jmmce.2017.55023
Nagaral M, Deshapande RG, Auradi V, Boppana SB, Anil Kumar MR (2021) Mechanical and wear characterization of ceramic boron carbide-reinforced Al2024 alloy metal composites. J Bio Tribo Corros 17(19):7–19. https://doi.org/10.1007/s40735-020-00454-8. (Springer)
Nagaral M, Auradi V, Kori SA, Hiremath V (2019) Investigation on mechanical and wear behavior of nano Al2O3 particulates reinforced AA7475 alloy composites. J Mech Eng Sci 13:4623–4635. https://doi.org/10.15282/jmes.13.1.2019.19.0389
Sunil Kumar M, Sathisha N, Jagannatha N, Chandra BT (2022) Tribological study on effect of chill casting on aluminium A356 reinforced with hematite paticulated composites. J Bio Tribo Corros 18(52):1–13. https://doi.org/10.1007/s40735-022-00635-7
Acknowledgements
The authors express their gratitude to Princess Nourah bint Abdulrahman University Researchers Supporting Project (Grant No. pnursp2023R12), Princess Nourah bint Abdulrahman University, Riyadh, Saudi Arabia.
Author information
Authors and Affiliations
Contributions
MSK; Conceptualization, Methodology, and Software, NS and NT Data curation, Writing-Original draft preparation, SM; Visualization, Investigation, SJN Software, Validation, MIK; Writing- Reviewing and Editing and Supervision.
Corresponding author
Ethics declarations
Ethics approval and consent to participate
Not applicable.
Consent for publication
Not applicable.
Competing interests
The authors declare no competing interests.
Additional information
Publisher's note
Springer Nature remains neutral with regard to jurisdictional claims in published maps and institutional affiliations.
Rights and permissions
Springer Nature or its licensor (e.g. a society or other partner) holds exclusive rights to this article under a publishing agreement with the author(s) or other rightsholder(s); author self-archiving of the accepted manuscript version of this article is solely governed by the terms of such publishing agreement and applicable law.
About this article
Cite this article
Kumar, M.S., Sathisha, N., Manjnatha, S. et al. Fatigue surface analysis of AL A356 alloy reinforced hematite metal matrix composites. Biomass Conv. Bioref. (2023). https://doi.org/10.1007/s13399-023-04634-7
Received:
Revised:
Accepted:
Published:
DOI: https://doi.org/10.1007/s13399-023-04634-7