Abstract
This paper involves the study of mechanical and tribological characteristics of as-cast aluminium A356 metal matrix composites reinforced with calcium hexaboride (CaB6) particulates. Two Composite specimens with varying reinforcement weight percentages of 2.5% and 5% were fabricated using stir casting method. Mechanical properties (hardness and tensile strength) of as-cast and composite specimens were studied, and its tensile fracture surface behaviours were examined under scanning electron microscope. In addition, wear and friction characteristics were observed at dry sliding atmospheric condition for as-cast and composite specimens. Wear and friction tests were performed with three different loads (10 N, 20 N and 30 N) and two sliding velocities (1 m/s and 3 m/s) parametric condition. The responses of coefficient of friction and wear rate measurements were recorded for further analysis. Worn out surfaces of test samples were analysed through SEM (Scanning Electron Microscope) and the wear mechanisms were studied. From experiments it is found that, the hardness and tensile strength had increased for higher weight percentage added composites (5% CaB6). The same higher weight percentage composite specimen exhibited lower wear rate and higher coefficient of friction than the other combinational test samples. The developed higher weight percentage added composite sample is recommended for replacing automobile components.
Similar content being viewed by others
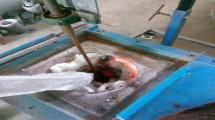
Explore related subjects
Discover the latest articles, news and stories from top researchers in related subjects.Avoid common mistakes on your manuscript.
Introduction
Metal matrix composite materials consist of a metallic matrix or an alloy reinforced with the fibre or ceramics to produce composite materials. Metal matrix composites exhibits greater strength, stiffness, good resistance to wear and corrosion when compared to other alloys [1]. Due to these properties, they are extensively utilized in advanced application areas like automotive, manufacturing, aerospace, chemical industries, etc. [2]. Aluminium metal matrix has been tremendously used in different engineering, structural and functional applications due to its mechanical and tribological properties by adding different compositions of reinforcement [3]. A356 possess high ductility, surface hardness, fatigue strength, corrosion resistance compared to other metal matrices, so they are typically suitable for the applications like water cooled engine cylinder blocks, aircraft fittings, automotive transmission cases, aircraft pump parts, etc. [4]. Stir casting, squeeze casting and powder metallurgy techniques were used in order to fabricate aluminium metal matrix composites and from the above techniques, stir casting is more flexible, easy and low cost. The properties of the developed composite materials mainly depend upon the matrix materials and its reinforcement (volume, shape and size [5,6,7]). A vast number of researchers have made research in this area by adding TiC,TiB2, Al2O3, B4C, SiC, Si3N4, ZrO2, MgO, AlN, ZnO were used as reinforcements into the aluminium metal matrix for improving the properties of aluminium metal [8,9,10,11,12,13,14,15,16].
Calcium hexaboride (CaB6) is a reinforcement particle which possess high melting point (2373 K), low density (2.45 g cm−3), higher hardness (27 GPa), low thermal coefficient of expansion (6.5×10−6 K−1), high modulus of elasticity (379 GPa), high thermal, chemical, electrical and mechanical stability compared to the other reinforcements [17,18,19,20,21,22,23]. Owing to the above aforementioned properties, CaB6 was chosen as reinforcements for A356.
Cui et al. [24] studied that Al-CaB6 composite offered higher hardness when compared with pure aluminium metal. Kumar et al. [25] concluded that the wear resistant properties of A356 alloy can be enhanced by incorporating Al2O3 and MoS2 particulates into the matrix. When A356 alloy composites were produced by stir cum squeeze casting with 20 weight percentage of SiC followed by T6 heat-treatment, the produced composite sample shows better mechanical and wear resistant properties [26]. Vinod et al. [27] conducted a research after fabrication of A356 alloy composites through double stir casting method reinforced with fly ash and rice husk under various weight compositions of 0, 5, 7.5, 10 and 12.5% and concluded that there occurs a significant increase in mechanical properties.
From the above literature review, it was revealed that many researchers have focussed upon assessing the mechanical properties of aluminium metal matrix composites. Few of the researchers have focussed upon the aluminium metal matrix composites and evaluated their tribological properties. So, this work will be focussing on comparing the mechanical and tribological properties of virgin A356 alloy with its composites (2.5 wt% and 5 wt% of CaB6) under room atmospheric conditions and their wear mechanisms were studied.
Methodology
Materials Used
In this work, matrix metal is chosen as A356 aluminium alloy and it is purchased from the Coimbatore metal mart, Coimbatore. The purchased alloy A356 was tested by using spectroscopy to ensure the originality and its alloying elements (in wt%), and it is shown in Table 1. Among various reinforcements, chosen reinforcement is calcium hexaboride (CaB6) because of its high melting point (2235 °C), low weight/density (2.45 g cm−3), less CTE (Coefficient of Thermal Expansion as 6.2 × 10−6/°C), high hardness (27 GPa), chemically stable and at different environmental conditions it offers better wear resistant properties and it is shown in Fig. 1.
Processing
To prepare the aluminium metal matrix composites in a cost-efficient manner, stir casting methodology is adopted. The setup consists of a main furnace, a preheating furnace and a mechanical stirrer which is coupled with the electrical motor, and it is shown in Fig. 2. Three test samples were processed by using this setup in which the first sample was virgin one and next two samples with a reinforcement addition by varying 2.5 and 5 wt% of CaB6 with A356 matrix. One kg of A356 alloy was taken and melted around 720 °C to remove slag, and then, the molten metal was poured into the preheated 225 °C die and then allowing the molten metal to undergo solidification process for a few minutes to attain a sound casting. In continuing, the second and third samples were prepared by adding the preheated (300 °C) reinforcement particles (2.5 wt% CaB6 and 5 wt% CaB6) on the molten (720 °C) metal in the crucible and simultaneously the stirrer was rotated at 500 rpm in the molten metal for few minutes and then transferred to the preheated die and the casted samples were obtained. The casted samples were further machined, and it is shown in Fig. 3.
The prepared virgin and two composite specimens were tested under vicker’s microhardness testing machine (DHT 1000, Model Number: JMHVS-1000-XYZ) at 500 gm loading condition and obtained average hardness value of 74, 87, 96 VHN, respectively. It was observed that evenly distribution with higher wt% of the calcium hexaboride particulates in the matrix shows higher hardness value than the virgin one. Further, all the three test specimens are taken for examining the tribological properties and mechanical properties by using a pin-on-disc tribometer apparatus and universal testing machine, respectively.
Tensile Test
UTM (Universal testing machine Instron, Model: TUE-C1000) is utilized to interrogate the tensile behaviour of pure A356 alloy and its composites at room atmospheric conditions, and it is shown in Fig. 4. Then the casted and composite specimens were subjected to machining process according to ASTM: E8 standard prior to take the tensile test and it is shown in Fig. 3. To assure the reproducibility in results, for each composition two samples were used. The fractured surface morphology was studied by using a SEM.
Wear Test
After tensile test, stir casted specimens were subjected to machining process to produce rectangular specimens of size 12 mm width and 40 mm height as per ASTM G99-05 standards. At dry sliding conditions, tribological properties were found by using Pin-on-disc tribometer (Ducom Tr-20LE-M108) apparatus. The machined pin specimens were fixed in a specimen holder and allowed to have contact against the steel disc counter face (EN-32) with a hardness of 73 HRC. Pin specimen and counter disc have a surface roughness (Ra) of magnitude 0.8 μm, and 1.6 μm, respectively.
Sliding test experiment was performed at three different applying loads [10 N, 20 N and 30 N] with two different sliding velocity conditions [1 m/s and 3 m/s] and for a constant sliding distance of 1000 m. The observed test results like wear loss/wear rate and COF (coefficient of friction) were measured, and the worn out pin surface was further analysed.
Results and Discussion
Tensile Test Results
Table 2 depicts the tensile test results of the stir casted specimens tested under room temperature. Virgin A356 alloy exhibits yield strength of 63.5 MPa and ultimate tensile strength of 137.2 MPa. Yield strength results revealed that there occurs an increase in 17.5% and 35.6% for the composite sample 2 and 3, respectively, when compared with the virgin alloy. Sample 2(97.5% A356 + 2.5% CaB6) and sample 3(95% A356 + 5% CaB6) exhibit 6.7% and 16.1%, respectively, increase in ultimate tensile strength when compared with the virgin alloy. It is because the reinforcement content in the softer matrix material causes the composite specimen to record the higher value of yield and ultimate tensile strength. Then the fractured specimens were examined under scanning electron microscopy to study their fracture behaviour.
Figure 5a shows the SEM analysis of virgin A356 aluminium alloy sample. The above figure has few dimples in various fractured regions. The above features on the surface of virgin A356 aluminium alloy implies that ductile mode of fracture has occurred.
In composite sample 2(97.5% A356 + 2.5% CaB6) shown in Fig. 5b, hard reinforcing ceramic particulates were evenly dispersed and makes good bond with the soft A356 aluminium alloy matrix. The above figure of the composite sample contains few dimples, and CaB6 particulates were also noticed.
For the composite sample 3(95% A356 + 5% CaB6), few cracks and dimples were witnessed and are shown in Fig. 5c. The reason for this feature is due to the presence of CaB6 particulates fills the void of softer matrix which resists the A356 alloy deformation by obstructing the dislocations of atoms when subjected to loading. When the magnitude of tensile load increases, cleavage fracture formation initiates through CaB6 particulates and results in the formation of cracks. This proceeds further and results in fracture. Also, few dimples were noticed. Thus, it is understood that the fracture mode for the sample 3(95% A356 + 5% CaB6) is a combination of brittle and ductile. However, due to lower weight of reinforcement particles inside the softer matrix, ductile mode of fracture is dominated.
Wear Rate
Figure 6a–c depicts the wear rate for virgin and composite pins with respect to the various applied loads (10 N, 20 N and 30 N) and sliding velocities (1 m/s and 3 m/s) at a constant sliding distance of 1000 m, respectively. After completion of wear test, from the results it was revealed that that 95% A356 and 5% CaB6 stir casted pin specimen exposed lower wear rate at all the sliding conditions when compared with the remaining pin specimens because of good interfacial bonding between CaB6 (ceramic) particulates with the A356 matrix material. While stir casting process, there occurs a uniform scattering of CaB6 particulates having higher hardness value attributed to bear lesser wear rate than the remaining pin specimens. Also, it was revealed that the wear rate is directly proportional to the applied load for all the casted pin samples. When a lower load of 10 N was applied on the pin, there develops a lower magnitude of stress which yields debris in diminished quantity. After completion of sliding test, the quantity of debris (Inferred from wear rate) is comparatively lower when compared with the remaining pin samples. Similarly, when a higher load (30 N) is applied, it causes higher amount of stress. It leads to undergo intense wear and more damage on the pin surface. Quantitatively, stir casted A356 with 5 wt% of CaB6 composite pin sample exhibited 40.33% lower wear rate than the virgin as-cast pin A356 pin sample at 30 N load sliding velocity 3 m/s for 1000 m sliding distance [14]. At lower load condition (10 N), wear rate varies linearly with respect to the sliding velocity. When a higher load of 30 N, wear rate steadily increases from 1 to 3 m/s then almost steady state wear condition was observed at a higher velocity of 3 m/s.
Coefficient of Friction
Figure 7a–c depicts the relationship between coefficient of friction for the virgin and composite pins for the above said sliding conditions. 95 wt% A356 with 5 wt% CaB6 showed a high coefficient of friction as well as least value of wear rate when compared with the remaining two pin specimens at all the sliding conditions. This is due to the influence of CaB6 hard ceramic particulates into the A356 soft matrix which leads the composite pin to produce higher frictional force when sliding action takes place against the counterface. From Fig. 7a, it was seen that at 10 N loading condition, the coefficient of friction varies linearly with respect to the sliding velocity. Similarly, at a higher load of 30 N (Fig. 7c), the coefficient of friction exhibits almost a steady state phenomenon at all the sliding conditions. Due to the raise in load (30 N), the pin surface is severely damaged. It leads to particulates in the pin to trap inside the counterface, and it causes to exhibit a high coefficient of friction [14]. Also, it was observed that the same trend was seen for all three test specimens. Quantitatively, stir casted A356 with 5 wt% of CaB6 composite pin sample exhibited 17.39% higher coefficient of friction than the virgin as-cast A356 pin sample at 30 N applied loading with a sliding velocity of 3 m/s for 1000 m sliding parametric condition. From Fig. 7a, b, it was seen that compared to higher load of 30 N coefficient of friction was more linear in nature for a lower load of 10 N.
SEM Image Analysis
Figures 8 and 9 show the scanning electron microscopic images of the worn out pin surfaces of the A356–CaB6 composite under constant sliding distance of 1000 m with two different sliding loads of 10 N and 30 N and at two various sliding velocities of 1 m/s and 3 m/s, respectively. The worn out pin surfaces of the A356–CaB6 composites shown in the SEM image were investigated to assess the effect of the various wear parameters under room temperature conditions.
Figure 8a shows the worn out pin image of virgin A356 alloy pin with a sliding velocity of 1 m/s at 10 N. At this sliding condition, few cracks were observed on the pin. In addition to the cracks, large amount of material loss was noticed and deeper grooves were also seen along the direction of sliding.
At the same sliding conditions, 97.5% A356 + 2.5% CaB6 pin sample was examined under SEM and is indicated in Fig. 8b. It was seen that comparatively less mass loss was seen on the pin surface. Also, thin grooves were also seen on the pin surface along the sliding direction.
Figure 8c refers the 95% A356 + 5% CaB6 composite pin under the same sliding conditions, and it was examined under SEM. It was seen very less mass loss was occurred on the pin at this sliding condition. Along the sliding direction, very thin grooves were also observed. And also few debris were stick upon the pin surface. It was seen that for all three pin specimens, abrasion wear mechanism was observed as the dominant wear mechanism at the sliding condition of 1 ms−1 with 10 N for a distance of 1000 m.
Figure 9a projects the worn out pin image of virgin A356 alloy pin with a sliding velocity of 3 m/s at 30 N for a sliding distance of 1000 m. At this sliding condition, intense wear was occurred on the pin surface and immense mass loss was discerned. When the pin surface was examined, it was seen deeper and wider grooves were observed on the pin surface.
For the same sliding condition, 97.5% A356 + 2.5% CaB6 composite pin was studied and it is shown in Fig. 9b. On this condition, comparatively less mass loss was seen and thin grooves were seen. Also, few debris particles were also seen on the pin surface. So, for the above two sliding conditions, abrasion was observed as the dominant wear mechanism.
Figure 9c shows the worn out pin image of 95% A356 + 5% CaB6 alloy pin with a sliding velocity of 3 m/s at 30 N. At this sliding condition, minimal mass loss was seen on the pin when compared with the other two pins. SEM Micrographs were also revealed on the pin surface the same that thin grooves were noticed. In addition to this, few oxide layers were seen on the pin surface. These oxide layers restrict the wear loss occurring on the pin which was reported by few other researchers [28,29,30].
Thus, we can able to conclude that Oxidation and Abrasion wear mechanisms were dominated on the pin surface under the sliding conditions of 3 m/s with a load of 30 N for the sliding distance of 1000 m.
Conclusion
In the present study, virgin A356 and two composite specimens (97.5% A356 and 2.5% CaB6, 95%A356 and 5% CaB6) were fabricated through stir casting methodology.
-
The stir casted specimens were subjected to tensile and tribological experiments.
-
From the tensile test it was noticed that, the specimen of 95% A356 and 5% CaB6 composite specimen exhibits an increase in 35.6% and 16.1% of yield strength and ultimate tensile strength, respectively, when compared with the virgin alloyA356 under room atmospheric conditions.
-
After completing tensile test, the fractured specimens were studied under SEM and the characteristics were recorded.
-
From the fractography analysis, it was found that ductile mode was dominant for all the three specimens.
-
Under wear test, both the coefficient of friction and wear rate of the specimens vary with the applied normal loads (10 N, 20 N and 30 N) and the sliding velocities (1 m/s and 3 m/s).
-
Specimen 3 of 95% A356 and 5% CaB6 composite pin at all the sliding conditions, shows 40.33% lower wear rate and 17.39% higher friction coefficient than the virgin pin specimen. This is because of the influence of the uniform distribution of reinforcement particulates inside the softer A356 alloy.
-
Various wear mechanisms occurred at the different sliding conditions on the pin samples were examined under SEM.
References
P.S. Reddy, R. Kesavan, B.V. Ramnath, Investigation of mechanical properties of aluminium 6061-silicon carbide, boron carbide metal matrix composite. SILICON 10(2), 495–502 (2018). https://doi.org/10.1007/s12633-016-9479-8
L.F. Xavier, P. Suresh, Wear behavior of aluminium metal matrix composite prepared from industrial waste. Sci. World J. (2016). https://doi.org/10.1155/2016/6538345
M. Imran, A.R.A. Khan, Characterization of Al-7075 metal matrix composites: a review. J. Mater. Res. Technol. 8(3), 3347–3356 (2019). https://doi.org/10.1016/j.jmrt.2017.10.012
J.-G. Li, S.-Q. Wang, Distortion caused by residual stresses in machining aeronautical aluminum alloy parts: recent advances. Int. J. Adv. Manuf. Technol. 89(1–4), 997–1012 (2017). https://doi.org/10.1007/s00170-016-9066-6
V. Mohanavel, K. Rajan, M. Ravichandran, Synthesis, characterization and properties of stir cast AA6351-aluminium nitride (AlN) composites. J. Mater. Res. 31(24), 3824 (2016). https://doi.org/10.1557/jmr.2016.460
T. Ye, Y. Xu, J. Ren, Effects of SiC particle size on mechanical properties of SiC particle reinforced aluminum metal matrix composite. Mater. Sci. Eng. A 753, 146–155 (2019). https://doi.org/10.1016/j.msea.2019.03.037
A.O. Inegbenebor, C.A. Bolu, P.O. Babalola, A.I. Inegbenebor, O.S.I. Fayomi, Aluminum silicon carbide particulate metal matrix composite development via stir casting processing. SILICON 10(2), 343–347 (2018). https://doi.org/10.1007/s12633-016-9451-7
K. Kaviyarasan, R. Soundararajan, P. Seenuvasaperumal, A. Sathishkumar, Experimental investigation of dry sliding wear behaviour on ceramic reinforced magnesium composite by powder metallurgy technique. Mater. Today Proc. 18, 4082–4091 (2019). https://doi.org/10.1016/j.matpr.2019.07.352
S.B. Boppana, In situ synthesis of titanium carbide in pure aluminium. J. Mater. Sci. Chem. Eng. 8(1), 1–10 (2019). https://doi.org/10.4236/msce.2020.81001
R.N. Harsha, M.V. Kulkarni, B.S. Babu, Study of mechanical properties of aluminium/nano-zirconia metal matrix composites. Mater. Today Proc. (2020). https://doi.org/10.1016/j.matpr.2020.02.641
K. Shirvanimoghaddam, H. Khayyam, H. Abdizadeh, M.K. Akbari, A.H. Pakseresht, F. Abdi, A. Abbasi, M. Naebe, Effect of B4C, TiB2 and ZrSiO4 ceramic particles on mechanical properties of aluminium matrix composites: experimental investigation and predictive modelling. Ceram. Int. 42(5), 6206–6220 (2016). https://doi.org/10.1016/j.ceramint.2015.12.181
R. Raj, D.G. Thakur, Qualitative and quantitative assessment of microstructure in Al-B4C metal matrix composite processed by modified stir casting technique. Arch. Civ. Mech. Eng. 16(4), 949–960 (2016). https://doi.org/10.1016/j.acme.2016.07.004
P.K. Yadav, G. Dixit, Erosive-corrosive wear of aluminium-silicon matrix (AA336) and SiC p/TiB 2p ceramic composites. SILICON 11(3), 1649–1660 (2019). https://doi.org/10.1007/s12633-018-9981-2
M. Karbalaei Akbari, S. Rajabi, K. Shirvanimoghaddam, H.R. Baharvandi, Wear and friction behavior of nanosized TiB2 and TiO2 particle-reinforced casting A356 aluminum nanocomposites: A comparative study focusing on particle capture in matrix. J. Compos. Mater. 49(29), 3665–3681 (2015). https://doi.org/10.1177/0021998314568327
X. Qu, F. Wang, C. Shi, N. Zhao, E. Liu, C. He, F. He, In situ synthesis of a gamma-Al2O3 whisker reinforced aluminium matrix composite by cold pressing and sintering. Mater. Sci. Eng. A 709, 223–231 (2018). https://doi.org/10.1016/j.msea.2017.10.063
K. Kaviyarasan, J. Pradheep Kumar, S. Karthik Anandh, M. Sivavishnu, S. Gokul, Comparison of mechanical properties of Al6063 alloy with ceramic particles. Mater. Today Proc. 22, 3067–3074 (2020). https://doi.org/10.1016/j.matpr.2020.03.442
M.T. Alam, A.H. Ansari, S. Arif, M.N. Alam, Mechanical properties and morphology of aluminium metal matrix nanocomposites-stir cast products. Adv. Mater. Process. Technol. 3(4), 600–615 (2017). https://doi.org/10.1080/2374068X.2017.1350543
J. Ding, C. Cui, Y. Sun, J. Ding, L. Zhao, S. Cui, Microstructures and mechanical properties of in-situ CaB6 ceramic particles reinforced Al-Cu-Mn composite. Ceram. Int. 45(17), 21668–21675 (2019). https://doi.org/10.1016/j.ceramint.2019.07.165
Y. Wang, G.-H. Zhang, X.-B. He, B.-J. Yan, Preparation of refractory metal diboride powder by reducing refractory metal oxide with calcium hexaboride. Ceram. Int. 45(12), 15772–15777 (2019). https://doi.org/10.1016/j.ceramint.2019.04.225
Y. Chernov, E. Filatov, N. Shurov, V. Smolenski, N. Tkachev, Synthesis of calcium hexaboride by electrolysis of molten salt. Metall. Mater. Trans. B. 50(4), 1745–1751 (2019). https://doi.org/10.1007/s11663-019-01626-9
X. Cui, H. Cui, Y. Wu, X. Liu, Surface modification of A390 alloy with CaB6 composite coating. J. Market. Res. 9(2), 1405–1411 (2020). https://doi.org/10.1016/j.jmrt.2019.11.067
L. Bao, X. Qi, L. Chao, O. Tegus, Synthesis, and magnetic and optical properties of nanocrystalline alkaline-earth hexaborides. CrystEngComm 18(7), 1223–1229 (2016). https://doi.org/10.1039/C5CE02060C
H. Liu, L. Zhang, G. Zhao, G. Feng, G. Min, Growth evolution of CaB6 thin films deposited by DC magnetron sputtering. Ceram. Int. 41(6), 7745–7750 (2015). https://doi.org/10.1016/j.ceramint.2015.02.106
X. Cui, Y. Wu, X. Zhu, X. Liu, In-situ formation of Al-CaB 6 composites with low resistivity. Rare Met. 31(6), 578–581 (2012). https://doi.org/10.1007/s12598-012-0561-0
M.S.A. Kumar, C. Honnaiaha, S.L.A. Prasad, Influence of extrusion process on mechanical and tribological properties of aluminium A356-AL2O3 Stir Cast MMC. Mater. Today Proc. 5(13), 26918–26924 (2018). https://doi.org/10.1016/j.matpr.2018.08.179
R. Soundararajan, S. Sivasankaran, N. Babu, G.P.R. Adhithya, Appraisal of tribological properties of A356 with 20% SiC composites under dry sliding condition. J. Braz. Soc. Mech. Sci. Eng. 42(3), 1–12 (2020). https://doi.org/10.1007/s40430-020-2231-8
B. Vinod, S. Ramanathan, V. Ananthi, N. Selvakumar, Fabrication and characterization of organic and in-organic reinforced A356 aluminium matrix hybrid composite by improved double-stir casting. SILICON 11(2), 817–829 (2019). https://doi.org/10.1007/s12633-018-9881-5
S. Arif, M.T. Alam, A.H. Ansari, M.A. Siddiqui, M. Mohsin, Study of mechanical and tribological behaviour of Al/SiC/ZrO2 hybrid composites fabricated through powder metallurgy technique. Mater Res Express 4(7), 076511 (2017). https://doi.org/10.1088/2053-1591/aa7b5f
L. Falcon-Franco, E. Bedolla-Becerril, J. Lemus-Ruiz, J.G. Gonzalez-Rodríguez, R. Guardian, I. Rosales, Wear performance of TiC as reinforcement of a magnesium alloy matrix composite. Compos. B Eng. 42(2), 275–279 (2011). https://doi.org/10.1016/j.compositesb.2010.11.012
M. Habibnejad-Korayem, R. Mahmudi, H.M. Ghasemi, W.J. Poole, Tribological behavior of pure Mg and AZ31 magnesium alloy strengthened by Al2O3 nano-particles. Wear 268(3–4), 405–412 (2010). https://doi.org/10.1016/j.wear.2009.08.031
Acknowledgements
The entire research work was carried in Sri Krishna college of Technology, Coimbatore, Tamilnadu, India.
Funding
There was no funding for this research work.
Author information
Authors and Affiliations
Corresponding author
Ethics declarations
Declaration
Author is assuring that this work has not been presented elsewhere or not being consideration for presentation in any journal.
Additional information
Publisher's Note
Springer Nature remains neutral with regard to jurisdictional claims in published maps and institutional affiliations.
Rights and permissions
About this article
Cite this article
Kaviyarasan, K., Soundararajan, R., Raj, A. et al. Assessment of Mechanical and Tribological Characteristics of A356 Reinforced with x wt% CaB6 Composites. J. Inst. Eng. India Ser. D 103, 75–84 (2022). https://doi.org/10.1007/s40033-021-00303-z
Received:
Accepted:
Published:
Issue Date:
DOI: https://doi.org/10.1007/s40033-021-00303-z