Abstract
Purpose: The aim of this study was to investigate the enhancement of very high gravity (VHG) bioethanol production using co-substrates of cassava chip hydrolysates and molasses by Kluyveromyces marxianus DMKU-KS07. Methods: The factors effecting cassava chip hydrolysis by raw starch degrading enzyme (RSDE) from the thermophilic bacterium Laceyella sacchari LP175 and commercial glucoamylase were investigated. The obtained raw cassava chip hydrolysate was co-fermented with molasses by the thermotolerant K. marxianus DMKU-KS07 at 42°C under nonsterile system. Results: Factors affecting sugar syrup production from raw cassava chips by synergistic hydrolysis and enzyme saccharification were optimized at temperature, substrate concentration and agitation rate of 50 °C, 250 g/L and 200 rpm, respectively. A yield of 98.6 g/L was obtained at 6 h of incubation, equivalent to 45.9% saccharification and 51.4% hydrolysis of starch, respectively. High bioethanol concentration at 118 g/L, with highest productivity of 2.19 g/L/h and ethanol yield (YP/S) at 0.44 g EtOH/g total sugar, equivalent to 86.3% theoretical yield, was obtained by modified simultaneous saccharification and fermentation (Modified SSF) with co-fermentation of substrates from the enzymatic hydrolysates of raw cassava chips at 42 °C for 12 h. Subsequent addition of molasses increased the final concentration to 100 g total sugar/L at 36 h. Conclusions: Co-fermentation of raw cassava chip hydrolysates with molasses enhanced production of bioethanol at VHG condition, and showed potential for application in ethanol production by enhancing the fermentation process and reducing energy consumption.
Graphic Abstract

Similar content being viewed by others
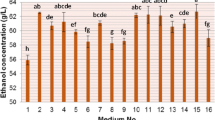
Explore related subjects
Discover the latest articles, news and stories from top researchers in related subjects.Avoid common mistakes on your manuscript.
Statement of Novelty
The novelty and significance of this research involve the application of raw starch degrading enzyme (RSDE) from L. sacchari LP175 in the bioethanol production process under very high gravity (VHG) condition using cassava chips and molasses as a co-substrate without the high temperature heating process. Highest bioethanol production was obtained by fermentation of the thermotolerant yeast Kluyveromyces marxianus DMKU-KS07 at 42 °C under a non-sterile system. The local waste and biomass can be applied for bioethanol production to increase the value of agricultural crops through biotechnological processes. This strategy could be used as an alternative choice to enhance bioethanol production at the industrial level with reduced energy consumption and operational costs.
Introduction
Bioethanol is a clean energy source that reduces CO2 emissions by 90% compared to conventional gasoline [1]. Bioethanol is derived from the fermentation of renewable resources such as cassava, molasses and sugar cane and used as an alternative biofuel in many countries [2,3,4].
Very high gravity (VHG) ethanol fermentation is a process applied to increase the final ethanol yield and productivity [4]. VHG fermentation involves the preparation of media containing at least 25% (w/v) of initial fermentable sugars to produce ethanol at high concentration (11–15%, v/v) [4, 5]. Application of VHG ethanol fermentation reduces energy use in downstream distillation processes and subsequently reduces the amount of wastewater from the distillation processes [5]. However, VHG fermentation requires a yeast strain that can tolerate high osmotic pressure from the increased concentration of initial substrate, with ability to withstand high ethanol accumulation. High osmotic pressure was reported to affect ethanol fermentation due to loss of cell viability [3, 6]. Udeh and Kgatla [7] found that the VHG bioethanol fermentation process caused the alteration of yeast cellular membrane lipids and inhibited the function of H+-ATPase activity, thereby impacting membrane transport systems. To maintain functional living yeast cells in VHG ethanol fermentation requires studying various factors such as strain of fermentation yeast, carbon source, nitrogen source, osmoprotectants, and aeration rate [3, 8, 9].
Cassava is a cheap substrate which is highly suitable for the production of ethanol under VHG conditions when molasses is not available [10, 11]. Raw starch degrading enzyme (RSDE) is applied in the ethanol fermentation process to hydrolyze starchy materials such cassava starch and cassava chips [12, 13]. Application of RSDE reduces energy consumption and operational costs since starch granules can be hydrolyzed below the gelatinization temperature compared to conventional starch hydrolysis at 80–100 °C [14, 15]. Recently, Lomthong et al. [13] used RSDE produced by Laceyella sacchari LP175 hydrolysis of cassava chips at 50 °C and the obtained sugar syrup as the substrate for bioethanol fermentation. Trakarnpaiboon et al. [16] reported that hydrolysis and saccharification of cassava chips at low temperature (50 °C) without the heating process promoted bioethanol fermentation by Kluyveromyces marxianus DMKU-KS07 at 42 °C under non-sterile conditions. Molasses, as a waste product from the sugar industry, are used as the major substrate for bioethanol production [16, 17]. Molasses contain high contents of sucrose and other nutrients that are suitable for microbial utilization [17]. Arshad et al. [18] reported on VHG bioethanol fermentation by S. cerevisiae using molasses as a substrate, giving maximum ethanol production at 122 g/L. Compared with other substrates, molasses has advantages for production of bioethanol with no need for pretreatment and saccharification steps [17]. However, molasses contains high levels of metal ions that inhibit the activity of microbial metabolic enzymes and reduce the yield of ethanol production [9, 17]. Phomikhet et al. [19] reported that calcium ions in molasses precipitated phosphate and magnesium ions that impacted growth of yeast cells and yield of bioethanol. Therefore, this study evaluated very high gravity (VHG) bioethanol production using co-substrates of cassava chip hydrolysates and molasses by Kluyveromyces marxianus DMKU-KS07. Moreover, optimal conditions for hydrolysis of raw cassava chips by RSDE produced from L. sacchari LP175 with commercial glucoamylase (GA) were also investigated.
Materials and Methods
Raw Material and Reagents
Raw cassava chips were obtained from the Cassava and Starch Technology Research Unit (CSTRU) at Kasetsart University. Cassava chips were ground to powder using an electric grinder and stored in the dry until required for use. Total starch assay (Megazyme International Ireland, Wicklow, Ireland) and amylose content (Amperometric titration with potassium iodate solution, [20, 21]) were performed by the Cassava and Starch Technology Research Unit (CSTRU) at Kasetsart University. Protein, fat and fiber contents were determined following the Association of Official Analytical Chemists methods (AOAC) [22].
Molasses was obtained from the NK Molasses Co., Ltd., Nong Khai Province, Thailand and kept at 4 °C until required for use. Analysis of molasses was performed by the Overseas Merchandise Inspection Co., Ltd., Bangkok Laboratory [23].
All analytical grade chemicals and reagents used in this study including dinitrosalicylic acid (DNS), glucose oxidase reagents, and orcinol staining reagent were provided by Sigma-Aldrich (USA) and Merck (Germany).
Microorganisms, Inoculum Preparation and Cultivation
Laceyella sacchari LP175, a potent thermophilic filamentous bacterial strain for production of RSDE, was isolated from soil in Thailand [24] and kept at the Thailand Institute of Scientific and Technological Research (TISTR) Bangkok MIRCEN culture collection as TISTR 2280 [12]. Inoculum of LP175 strain was grown in a nutrient broth (3 g/L beef extract, 5 g/L peptone) at 50 °C and 150 rpm for 12 h. After centrifugation at 5,000 rpm, 4 °C for 10 min the cell pellets were suspended in 0.85% NaCl solution with optical density (OD) of 0.7 at a wavelength of 600 nm, and used as inoculum (10% v/v) for enzyme production as described by Lomthong et al. [12].
Kluyveromyces marxianus DMKU-KS07, a potent bacterial strain for ethanol production at high temperature (42 °C) was obtained from the culture collection of Prof. Dr. Savitree Limtong, Department of Microbiology, Faculty of Science, Kasetsart University. The yeast culture was grown in YM medium (3 g/L yeast extract, 3 g/L malt extract, and 5 g/L peptone, supplemented with 10 g/L glucose) at 42 °C for 16 h, and used as inoculum (15% v/v) for bioethanol production [13].
Enzymes Used for Saccharification of Raw Cassava Chips
RSDE was conducted in a 10.0 L airlift fermenter using 7.0 L working volume and optimized medium of 4.93 g/L cassava starch, 2.8 g/L yeast extract, 0.5 g/L K2HPO4, 0.5 g/L MgSO4.7H2O, and 1.0 g/L CaCl2 (pH 6.5) [12]. Fermentation was operated at the optimized conditions (temperature 45 °C with aeration rate of 0.5 vvm for 36 h) as reported by Lomthong et al. [13]. The obtained enzyme was concentrated by a Freeze Dryer (OPERON FDU-8624, Korea) and dissolved in 0.1 M phosphate buffer pH 6.5 as the enzyme for hydrolysis of cassava chips. RSDE produced from L. sacchari LP175 was reported as α-amylase, which randomly hydrolyses starch to oligosaccharides, with maltose as the major product. Commercial glucoamylase (GA) was obtained from Dextrozyme® glucoamylase, GA (Novozymes, Bagsvaerd, Denmark) and kept at −20 °C until required for use. GA consecutively hydrolyzed α-1,4 glycosidic bonds of starch and oligomers to glucose. GA could synergistically enhance the hydrolysis of cassava starch with RSDE as reported by Lomthong et al. [13].
Optimization of Cassava Chip Hydrolysis with RSDE and Commercial GA
The hydrolysis reaction for production of sugar syrup from cassava chips was investigated using a 50 mL reaction mixture of 0.1 M phosphate buffer (pH 6.5) in a 250 mL Erlenmeyer flask containing 5.0 g dried cassava chips (equivalent to 100 g/L), RSDE (660 U/g cassava chips) from L. sacchari LP175 and commercial GA at 66 U/g substrate [13]. The reaction mixture was incubated in an incubator shaker (150 rpm) at 40–60 °C for 6 h. Cassava chips at 100–300 g/L were applied to the reaction and incubated at the optimal temperature for 6 h. Optimal shaking speed was investigated at 100–300 rpm with the optimal temperature and substrate concentration. Concentrations of reducing sugar and glucose were determined by the dinitrosalicylic acid (DNS) [25] and glucose oxidase methods [26], respectively. Percentage of starch hydrolysis or saccharification was calculated as:
where 0.9 is the molar mass conversion of starch to sugars, and 0.69 is g starch per g dried cassava chip powder, respectively [13, 27].
A scanning electron microscope (SEM) was used to study the residue of cassava chip powder after hydrolysis with RSDE and commercial GA as described above. Untreated cassava chips were used as a control. All samples were determined by SEM (model SU8020; Hitachi, Tokyo, Japan) at 10.0 kV. Hydrolysis products of cassava chips at each time interval were qualitatively determined by thin layer chromatography (TLC) [28]. A silica gel chromatography plate (Merck, 20 × 20 cm) was used to determine the solvent mixture of ethyl acetate/2-propanol/glacial acetic acid/water (4:2:2:1, v/v). The TLC plate was developed by spraying with a solution of orcinol-sulfuric acid and heating at 100 °C for 10 min. Glucose, maltose and maltotriose were used as standards.
Bioethanol Fermentation
Bioethanol Fermentation Using Molasses as a Sole Substrate
Molasses fermentation was prepared by dilution to final total sugars at 250 g/L and then supplemented with nutrients to obtain a final concentration of 6.0 g/L yeast extract, 4.0 g/L (NH4)2SO4, 2.0 g/L MgSO4, and 8.0 g/L of KH2PO4, with an initial pH of 5.0 [13]. The fermentation process was inoculated with 15% v/v of K. marxianus DMKU-KS07 and incubated at 42 °C with agitation speed of 200 rpm for 48 h. A sample was taken every 12 h to determine reducing sugars and ethanol concentrations.
Bioethanol Fermentation by Modified simultaneous Saccharification and Fermentation (Modified-SSF) Using Raw Cassava Chips as the Sole Substrate
A modified SSF process was previously reported by Lomthong et al. [13]. The optimal concentration of cassava chips was hydrolyzed by RSDE produced from L. sacchari LP175 and commercial GA, at the optimized conditions from the previous study for 6 h and then cooled to 42 °C. The obtained hydrolyzed cassava chips were supplemented with nutrients to obtain a final concentration of 6.0 g/L yeast extract, 4.0 g/L (NH4)2SO4, 2.0 g/L MgSO4, and 8.0 g/L of KH2PO4, with an initial pH of 5.0 as described above. Then, 15% v/v of K. marxianus DMKU-KS07 was added to the reaction and incubated at 42 °C with agitation speed of 200 rpm for 48 h. A sample was taken every 12 h to determine total sugar, reducing sugars and ethanol concentrations.
Bioethanol Fermentation Using Modified SSF with Co-fermentation of Substrates
Co-fermentation of substrates was investigated by hydrolysis of cassava chips, using RSDE produced from L. sacchari LP175 and commercial GA at the optimized conditions as described above for 6 h, and then cooled to 42 °C. Supplementary any nutrient was added to obtain a final concentration of 6.0 g/L yeast extract, 4.0 g/L (NH4)2SO4, 2.0 g/L MgSO4, and 8.0 g/L of KH2PO4, with an initial pH of 5.0 as described above. Then, 15% v/v of K. marxianus DMKU-KS07 was added to the reaction and incubated at 42 °C, with agitation speed of 200 rpm for 12 h. A final concentration at 100 g total sugar/L of molasses was then added to the fermentation and further cultivated for 36 h. Samples from the reaction were taken every 12 h to determine total sugar, reducing sugars and ethanol concentrations.
Enzyme Activities Assay
RSDE activity was determined followed the method of Mitsuiki et al. [29] by analysis of reducing sugars released during the hydrolysis of raw cassava starch, as previously described by Lomthong et al. [12]. One unit of RSDE activity was defined as the amount of enzyme releasing 1 µg of glucose equivalent per min under standard assay conditions. Glucoamylase activity was determined by analysis of liberated glucose measured by the glucose oxidase method of Kingsley and Getchell [30]. One unit of glucoamylase activity was defined as the amount of enzyme releasing 1 µg of glucose per min under standard assay conditions.
Analysis of Sugar and Ethanol Contents
The DNS method [25] was used to determine the amount of reducing sugars released from the hydrolysis of cassava chip powder. Total sugars were determined by the phenol sulfuric acid assay [31]. Ethanol concentration was analyzed by gas chromatography (GC4000; GL Sciences, Tokyo, Japan) using a glass column (Chromosorb 103, 60/80 mesh, ID 3 mm × 3 m; Shinwa Chemical Industries, Kyoto, Japan) with a flame ionization detector and n-propanol as an internal standard [13, 32].
Statistical Analysis
All data were analyzed using SPSS for Windows version 23 (SPSS Inc, USA). Differences among the mean values were tested using the least significant difference multiple range test, with significance at the p < 0.05 level.
Results and Discussion
Hydrolysis of Cassava Chips with RSDE and Commercial GA
Cassava chips contained high content of starch (69.28%) as shown in Table 1. This was a good source for sugar syrup production at low temperature hydrolysis by RSDE produced from L. sacchari LP175 and commercial GA without the heating process.
The optimal temperature for hydrolysis of raw cassava chips (100 g/L) by RSDE and commercial GA was determined at 50 °C (Fig. 1a), yielding 33.6 g/L after incubation for 6 h, equivalent to 43.8% hydrolysis and 40.4% saccharification. Hydrolysis cassava chips at 50 °C will benefit industrial applications by removing the step for liquefaction at high temperature (90 °C) as reported by Trakarnpaiboon et al. [16]. Optimal concentration of cassava chips for maximum sugar syrup production was determined at 250 g/L. This gave maximum sugar syrup production at 89.7 g/L (equivalent to 46.8% hydrolysis and 42.1% saccharification) as shown in Fig. 1b. At higher cassava chip concentrations than 250 g/L, the reaction was limited; the substrate swelled from absorption of enzyme as well as physical inaccessibility of some starch granules that became entrapped in the fibrous matrix of the cassava material [16, 33]. Agitation rate at 200–300 rpm gave similar results for sugar syrup production. At 200 rpm, sugar syrup production was 98.6 g/L, equivalent to 51.4% hydrolysis and 46.0% saccharification (Fig. 1c). Therefore, optimal conditions for production of sugar syrup from cassava chips by synergistical hydrolysis of RSDE produced from L. sacchari LP175 and commercial GA were 50 °C, substrate concentration at 250 g/L and shaking at 200 rpm. The time course for hydrolysis of cassava chips in a 2.0 L stirrer is shown in Fig. 2.
Thin layer chromatography (TLC) revealed that the mixed enzyme between RSDE from L. sacchari LP175 and commercial GA synergistically hydrolyzed raw cassava chip powder at 50 °C to glucose as the main product. (Fig. 3). Lomthong et al. [12] reported that RSDE from L. sacchari LP175 acted as α-amylase that randomly hydrolyses starch to oligosaccharides with maltose as the major product. This explained why addition of commercial GA was required for saccharification of starch.
SEM images of native cassava chips and chips digested at 3 h and 6 h are shown in Fig. 4. Native granules of cassava chip powder showed globular shapes (Fig. 4a), while after digestion by RSDE from L. sacchari LP175, damage to the granules was observed. Pits formed on the surfaces and some particles showed loss of granule structure (Fig. 4b, c). This result confirmed the feasibility of using RSDE and commercial GA for production of glucose syrup at 50 °C without the gelatinization process, as compared to the conventional process.
Bioethanol Fermentation
Bioethanol fermentation was investigated separately, following the three processes described in the materials and methods sections. Results are summarized in Table 2. In the first process, molasses was used as the sole substrate at 250 g/L total sugar to obtain VHG ethanol production. Maximum ethanol obtained was only 68.0 g/L with productivity at 1.42 g/L/h. Using molasses as the sole carbon source did not achieve a high yield of ethanol production, possibly due to high osmotic pressure of molasses at high concentration that the yeast strain could not tolerate, as reflected by the low substrate utilization ability [17,18,19].
The chemical composition analysis of molasses is shown in Table 3. The high calcium content (Ca2+) at 7,065.27 mg/kg and magnesium (Mg2+) at 3,246.74 mg/kg may stimulate growth and ethanol production. Phomikhet et al. [19] determined Mg2+ as a cofactor that activated over 300 different enzymes, while phosphate substrate is used by microbial cells to generate adenosine triphosphate (ATP) energy-carrying molecules and nucleic acid. However, Ca2+ in the molasses precipitates the phosphate and Mg2+ and impacts growth of yeast cells and yield of bioethanol. Moreover, Ca2+ ions also inhibit invertase activity and reduce ethanol production [17]. This knowledge explained why an optimal concentration of molasses in the fermentation process is required to avoid inhibition from the high content of Ca2+ ions.
In the second process, enzymatic hydrolysis of cassava chip powder by RSDE and commercial GA was used as the sole substrate for growth and bioethanol production of the yeast strain. Fiber content was found at 3.86%, and this was used as the carrier for cell attachment of the yeast strain during bioethanol fermentation. Wattanagonniyom et al. [9] reported that the existence of cassava hydrolysis residue in the reaction increased the bioethanol fermentation process by protecting the yeast cells from various stress conditions. Maximum ethanol production was 72.9 g/L, equivalent to 1.35 g/L/h, 0.44 g EtOH/g sugar of ethanol yield (YP/S) and 86.3% of theoretical yield (Fig. 5). High ethanol production obtained in this process was reflected by high saccharification of raw cassava chips, achieved as a result of reduced feedback inhibition of enzyme activities by released reducing sugars. Percentage of saccharification from the ethanol concentration was calculated at 74.6%. This showed the feasibility of using cassava chips as a substrate for production of bioethanol with hydrolysis of RSDE and commercial GA. However, using cassava chips as the sole carbon source cannot operate at higher concentration since high viscosity limits the capacity of mixing in the reaction, as reported by Trakarnpaiboon et al. [16]. This explained why co-fermentation (substrates) of cassava chip hydrolysis with molasses was required in this study.
The third process as modified SSF with co-fermentation of substrates consisted of the hydrolysis of cassava chips for 6 h and subsequent fermentation with K. marxianus DMKU-KS07 at 42 °C for 12 h. Then, molasses was added to the reaction to increase the final concentration to 100 g total sugars/L. Ethanol production was 118 g/L, productivity (Qp) of ethanol fermentation was 2.19 g/L/h with 0.44 g EtOH/g sugar of ethanol yield (YP/S), equivalent to 86.3% of the theoretical yield as shown in Table 2. The time course during hydrolysis and fermentation of the two steps of fermentation strategy is shown in Fig. 6a. K. marxianus is a potent yeast species for bioethanol production at high temperature [34] and appropriate for application in processes operated at high temperature without the cooling process. Recently, Wu et al. [35] reported the application of K. marxianus K21 for bioethanol production at 40 °C without a cooling system, by simultaneous saccharification and fermentation (SSF) using taro waste as substrate, yielding 48.98 g/L equivalent to 2.23 g/L/h of productivity. In this study, cassava chips were hydrolyzed by RSDE from L. sacchari LP175 and commercial GA at 50 °C, with subsequent simultaneous saccharification and fermentation using K. marxianus DMKU-KS07. Results demonstrated the advantage of K. marxianus DMKU-KS07 that converted fermentable sugars from the reaction to bioethanol, while RSDE and GA still remained to hydrolyse cassava chips and continuously liberate fermentable sugars for fermentation. Bioethanol production from the different processes was summarized compared to previous reports as shown in Table 4. Arshad et al. [18] reported that VHG bioethanol production by the fed-batch fermentation process by mutant S. cerevisiae using molasses at 40 Brix° as a substrate, yielded 122 g/L ethanol with aeration of 0.2 vvm. Molasses has been widely used as a substrate for bioethanol production; however, molasses-based ethanol relies on the seasonal availability of feedstock, and cassava has become an important option for bioethanol production [10]. Arshad et al. [36] reported that the cost of molasses varied each year and also from season to season and this impacted the cost of ethanol production. During the last decade, cassava chips have been used as a substrate for ethanol production at an industrial scale using the enzymatic liquefaction process in Thailand, as reported by Sriroth et al. [37], while Krajang and Chamsart [38] reported that bioethanol production by cassava starch hydrolysis, using a combination of cassava starch hydrolysis and fermentation with molasses in a 200-L pilot-scale fermenter, yielded 82 g/L ethanol. This result supported this research for the development of bioethanol using cassava chips as a co-substrate with molasses. Lomthong et al. [13] reported that bioethanol fermentation using cassava chips as the substrate by K. marxianus DMKU-KS07 yielded 90.9 g/L, while Trakarnpaiboon et al. [16] reported that fermentation of cassava chip hydrolysis by RSDE produced from Rhizopus microsporus with addition of molasses at the beginning of fermentation, yielded 102.2 g/L with 78% fermentation efficiency. In this study, modified SSF with co-fermentation under a non-sterile system was developed from the modified SSF fermentation process as described by Lomthong et al. [13] with co-fermentation substrate as reported by Trakarnpaiboon et al. [16]. Bioethanol yield increased due to reduced inhibition from high concentration of molasses. Wattanagonniyom et al. [9] prepared sugar syrup from cassava waste pulp by a series of enzymatic hydrolyses including cellulase at 50 °C for 24 h, subsequent hydrolysis by α-amylase at 85 °C for 1 h, and glucoamylase at 60 °C for 3 h. The obtained sugar syrup was co-fermented with molasses by Saccharomyces cerevisiae TISTR 5606 (SC 90) at 30 °C, yielding 74.36 g/L.
Bioethanol fermentation using modified SSF with co-fermentation of cassava chips hydrolysate and molasses; a time course of bioethanol fermentation, and b scanning electron micrograph of K. marxianus DMKU-KS07 existing in solid residues of cassava chips after incubation at 42 °C for 48 h. (Color figure online)
Scanning electron micrographs of cassava chip residues with K. marxianus DMKU-KS07 after incubation at 42 °C for 48 h are shown in Fig. 6b. K. marxianus DMKU-KS07 grew on the hydrolysate residues of the cassava chips by attaching cells to the filaments of cassava chip hydrolysates. Wattanagonniyom et al. [9] reported that yeast cells growing on the hydrolysis residues of agricultural crops and wastes increased the yield of bioethanol in the reaction because the hydrolysis residue protected them from shear forces and osmotic stress. These results indicated that solid residues from enzymatic hydrolysis could be used as carriers for yeast cell growth to improve bioethanol production by fermentation of co-substrates with molasses.
The outcome of this research demonstrated the feasibility of VHG ethanol production using modified SSF with co-fermentation of substrates under a non-sterile system. In terms of cost, this process reduced the energy required and operational costs for hydrolysis of cassava chips at high temperature, compared to conventional cassava-based bioethanol production by about 20% of fuel value for ethanol processing [15]. Cost of waste treatment generated from the molasses-based bioethanol production process also reduced. The modified SSF with co-substrate fermentation of cassava chip hydrolysates and molasses showed high performance for application in VHG bioethanol production by reduction of osmotic pressure under the VHG-modified SSF approach, supporting the results of Wattanagonniyom et al. [9] and Puligundla et al. [11].
Conclusion
RSDE from L. sacchari LP175 synergistically hydrolyzed raw cassava chips with commercial GA via low temperature hydrolysis and saccharification without the heating process. Optimal conditions for sugar syrup production were 50 °C, raw cassava chip powder at 250 g/L and shaking speed at 200 rpm, yielded 98.6 g/L reducing sugar, equivalent to 51.4% hydrolysis. Very high gravity, VHG, bioethanol fermentation by K. marxianus DMKU-KS07 at 42 °C using co-fermentation of enzymatic cassava chip hydrolysates and molasses increased yield of bioethanol up to 118 g/L. This research provided an alternative simplified process for VHG bioethanol production by co-fermentation of cassava chip hydrolysates with RSDE from the thermophilic bacterium L. sacchari LP175 and molasses that reduced energy consumption and operational costs.
Abbreviations
- DNS:
-
Dinitrosalicylic acid
- EtOH:
-
Ethanol
- YP/S :
-
Ethanol yield
- GA:
-
Glucoamylase
- OD:
-
Optical density
- Qp:
-
Productivity
- RSDE:
-
Raw starch degrading enzyme
- SEM:
-
Scanning electron microscope
- SSF:
-
Simultaneous saccharification and fermentation
- TLC:
-
Thin layer chromatography
- VHG:
-
Very high gravity
References
Ward, O.P., Singh, A.: Bioethanol technology: development and perspectives. Adv. Appl. Microbiol. 51, 53–80 (2002)
Nguyen, T.L.T., Gheewala, S.H.: Life cycle assessment of fuel ethanol from cane molasses in Thailand. Int. J. Life Cycle Assess. (2008). https://doi.org/10.1007/s11367-008-0011-2
Silalertruksa, T., Gheewala, S.H.: Environmental sustainability assessment of bio-ethanol production in Thailand. Energy. (2009). https://doi.org/10.1016/j.energy.2009.08.002
Deesuth, O., Laopaiboon, P., Laopaiboon, L.: High ethanol production under optimal aeration conditions and yeast composition in a very high gravity fermentation from sweet sorghum juice by Saccharomyces cerevisiae. Ind. Crops. Prod. (2016). https://doi.org/10.1016/j.indcrop.2016.07.042
Bai, F.W., Anderson, W.A., Moo-Young, M.: Ethanol fermentation technologies from sugar and starch feedstocks. Biotechnol. Adv. (2008). https://doi.org/10.1016/j.biotechadv.2007.09.002
Laopaiboon, L., Nuanpeng, S., Srinophakun, P., Klanrit, P., Laopaiboon, P.: Ethanol production from sweet sorghum juice using very high gravity technology: Effects of carbon and nitrogen supplementations. Bioresour. Technol. (2009). https://doi.org/10.1016/j.biortech.2009.03.046
Udeh, H.O., Kgatla, T.E.: Role of magnesium ions on yeast performance during very high gravity fermentation. J. Brew. Distilling. (2013). https://doi.org/10.5897/JBD2013.0041
Pradeep, P., Reddy, O.V.S.: High gravity fermentation of sugarcane molasses to produce ethanol: Effect of nutrients. Indian J. Microbiol. (2010). https://doi.org/10.1007/s12088-010-0006-0
Wattanagonniyom, T., Lee, W.C., Tolieng, V., Tanasupawat, S., Akaracharanya, A.: Co-fermentation of cassava waste pulp hydrolysate with molasses to ethanol for economic optimization. Ann. Microbiol. (2017). https://doi.org/10.1007/s13213-016-1245-z
Nguyen, T.L.T., Gheewala, S.H., Bonnet, S.: Life cycle cost analysis of fuel ethanol produced from cassava in Thailand. Int. J. Life Cycle Assess. (2008). https://doi.org/10.1007/s11367-008-0035-7
Puligundla, P., Smogrovicova, D., Mok, C., Obulam, V.S.R.: A review of recent advances in high gravity ethanol fermentation. Renew. Energy. (2019). https://doi.org/10.1016/j.renene.2018.06.062
Lomthong, T., Chotineeranat, S., Kitpreechavanich, V.: Production and characterization of raw starch degrading enzyme from a newly isolated thermophilic filamentous bacterium, Laceyella sacchari LP175. Starch-Stärke. (2015). https://doi.org/10.1002/star.201400150
Lomthong, T., Lertwattanasakul, N., Kitpreechavanich, V.: Production of raw starch degrading enzyme by the thermophilic filamentous bacterium Laceyella sacchari LP175 and its application for ethanol production from dried cassava chips. Starch-Stärke. (2016). https://doi.org/10.1002/star.201600018
Cinelli, B.A., Castilho, L.R., Freire, D.M.G., Castro, A.M.: A brief review on the emerging technology of ethanol production by cold hydrolysis of raw starch. Fuel (2015). https://doi.org/10.1016/j.fuel.2015.02.063
Lomthong, T., Chotineeranat, S., Cioci, G., Laville, E., Duquesne, S., Choowongkomon, K., Kitpreechavanich, V.: Molecular cloning and sequencing of raw starch degrading gene from Laceyella sacchari LP175 and its functional expression in Escherichia coli. Chiang Mai J. Sci. 45, 1634–1648 (2018)
Trakarnpaiboon, S., Srisuk, N., Piyachomkwan, K., Sakai, K., Kitpreechavanich, V.: Enhanced production of raw starch degrading enzyme using agro-industrial waste mixtures by thermotolerant Rhizopus microsporus for raw cassava chip saccharification in ethanol production. Prep. Biochem. Biotech. (2017). https://doi.org/10.1080/10826068.2017.1342264
Chotineeranat, S., Wansuksri, R., Piyachomkwan, K., Chatakanonda, P., Weerathaworn, P., Sriroth, K.: Effect of calcium ions on ethanol production from molasses by Saccharomyces cerevisiae. Sugar Tech. (2010). https://doi.org/10.1007/s12355-010-0024-6
Arshad, M., Hussain, T., Iqbal, M., Abbas, M.: Enhanced ethanol production at commercial scale from molasses using high gravity technology by mutant S. cerevisiae. Braz. J. Microbiol. (2017). https://doi.org/10.1016/j.bjm.2017.02.003
Phomikhet, P., Lorliam, W., Thaniyavarn, S., Tanasupawat, S., Savarajara, A.: Supplementation of sugarcane molasses for maximization of ethanol production by Saccharomyces cerevisiae using response surface method. Sci. Asia. (2019). https://doi.org/10.2306/scienceasia1513-1874.2019.45.229
Gibson, T.S., Solah, V.A., McCleary, B.V.: A procedure to measure amylose in cereal starches and flours with concanavalin A. J. Cereal Sci. (1997). https://doi.org/10.1006/jcrs.1996.0086
Takeda, Y., Hizukuri, S., Juliano, B.O.: Structures of rice amylopectins with low and high affinities for iodine. Carbohydr. Res. (1987). https://doi.org/10.1016/0008-6215(87)80008-3
Helrich, K.: Official methods of analysis of the association of official analytical chemists, 15th edn. Association of Official Analytical Chemists, Arlington, Virginia (1990)
Association of Official Analytical Chemists: Official methods of analysis of AOAC International, 20th edn. AOAC International, Rockville, USA (2016)
Hanphakphoom, S., Maneewong, N., Sukkhum, S., Tokuyama, S., Kitpreechavanich, V.: Characterization of poly(L-lactide)- degrading enzyme produced by thermophilic filamentous bacteria Laceyella sacchari LP175. J. Gen. Appl. Microbiol. (2014). https://doi.org/10.2323/jgam.60.13
Miller, G.L.: Use of dinitrosalicylic acid reagent for determination of reducing sugar. Anal. Chem. (1959). https://doi.org/10.1021/ac60147a030
Kapustka, L.A., Annala, A.E., Swanson, W.C.: The peroxidase-glucose oxidase system: a new method to determine glucose liberated by carbohydrate degrading soil enzymes. Plant Soil. (1981). https://doi.org/10.1007/BF02370048
Zhang, B., Dhital, S., Gidley, M.J.: Synergistic and antagonistic effects of α-amylase and amyloglucosidase on starch digestion. Biomacromol (2013). https://doi.org/10.1021/bm400332a
Sassaki, G.L., de Souza, L.M., Cipriani, T.R., Iacomini, M.: TLC of carbohydrates. In: Waksmundzka‐Hajnos, M., Sherma, J., Kowalska, T. (eds.) Thin layer chromatography in phytochemistry. CRC Press, Boca Raton (2008)
Mitsuiki, S., Mukae, K., Sakai, M., Goto, M., Hayashida, S., Furukawa, K.: Comparative characterization of raw starch hydrolyzing α-amylases from various Bacillus strains. Enzyme Microb. Tech. (2005). https://doi.org/10.1016/j.enzmictec.2005.02.022
Kingsley, G.R., Getchell, G.: Direct ultramicro glucose oxidase method for determination of glucose in biologic fluids. Clin. Chem. (1969). https://doi.org/10.1093/clinchem/6.5.466
Taylor, K.A.: A modification of the phenol/sulfuric acid assay for total carbohydrates giving more comparable absorbances. Appl. Biochem. Biotechnol. (1995). https://doi.org/10.1007/BF02783496
Apiwatanapiwat, W., Rugthaworn, P., Vaithanomsat, P., Thanapase, W., Kosugi, A., Arai, T.: Ethanol production at high temperature from cassava pulp by a newly isolated Kluyveromyces marxianus strain, TISTR 5925. AIMS Energy. (2013). https://doi.org/10.3934/ENERGY.2013.1.3
Papong, S., Malakul, P.: Life-cycle energy and environmental analysis of bioethanol production from cassava in Thailand. Bioresour. Technol. (2010). https://doi.org/10.1016/j.biortech.2009.09.006
Limtong, S., Sringiew, C., Yongmanitchai, W.: Production of fuel ethanol at high temperature from sugar cane juice by a newly isolated Kluyveromyces marxianus. Bioresource. Technol. (2007). https://doi.org/10.1016/j.biortech.2006.10.044
Wu, W.H., Hung, W.C., Lo, K.Y., Chen, Y.H., Wan, H.P., Cheng, K.C.: Bioethanol production from taro waste using thermo-tolerant yeast Kluyveromyces marxianus K21. Bioresource. Technol. (2016). https://doi.org/10.1016/j.biortech.2015.11.015
Arshad, M., Abbas, M., Iqbal, M.: Ethanol production from molasses: Environmental and socioeconomic prospects in Pakistan: Feasibility and economic analysis. Environ. Technol. Inno. (2019). https://doi.org/10.1016/j.eti.2019.100317
Sriroth, K., Piyachomkwan, K., Wanlapatit, S., Nivitchanyong, S.: The promise of a technology revolution in cassava bioethanol: From Thai practice to the world practice. Fuel (2010). https://doi.org/10.1016/j.fuel.2009.12.008
Krajang, M., Chamsart, S.: Raw cassava starch hydrolysis for single-step ethanol production using combination of raw starch hydrolysis and fermentation to pilot-scale. Rmutto. (2015). https://doi.org/10.21203/rs.3.rs-58171/v1
Acknowledgements
This research was supported by the RGJ Advanced Program (Grant No. RAP61K0008) and the Faculty of Science, Kasetsart University. The authors wish to thank Prof. Dr. Savitree Limtong for kindly providing the yeast strains, and the Faculty of Science and Technology, Rajamangala University of Technology Thanyaburi (RMUTT) for all materials and use of fermentation machine facilities.
Author information
Authors and Affiliations
Corresponding author
Ethics declarations
Conflict of interest
The authors declare that they have no conflicts of interest.
Additional information
Publisher's Note
Springer Nature remains neutral with regard to jurisdictional claims in published maps and institutional affiliations.
Rights and permissions
About this article
Cite this article
Lomthong, T., Netprasom, P., Kancharu, N. et al. Very high Gravity (VHG) Bioethanol Production Using Modified Simultaneous Saccharification and Fermentation of Raw Cassava Chips with Molasses by Kluyveromyces marxianus DMKU-KS07. Waste Biomass Valor 12, 3683–3693 (2021). https://doi.org/10.1007/s12649-020-01257-1
Received:
Accepted:
Published:
Issue Date:
DOI: https://doi.org/10.1007/s12649-020-01257-1