Abstract
Copper smelting slag is a useful secondary resource containing high iron and copper, which can be utilized to prepare crude Fe-Cu alloy by a direct reduction–magnetic separation process for making weathering-resistant steel. However, it is difficult to recover iron and copper from the slag by direct reduction since the iron mainly occurs in fayalite and the copper is held in copper sulfide. Therefore, enhancement reduction of copper slag is conducted to improve the recovery of copper and iron. Additives such as Na2CO3 has been proven to be capable of reinforcing the reduction of refractory iron ore. In this research, the effect of Na2CO3 on the carbothermic reduction of copper slag was investigated, and phase transformations during reduction and the distributing characteristics of iron and copper in the alloy and non-metallic phases of the reduced pellets were also studied. The results show that the metallization rate of iron and copper was increased with the addition of Na2CO3, leading to higher iron and copper recovery in Fe-Cu alloy powder. X-ray diffraction (XRD) and scanning electron microscopy-energy dispersive spectroscopy (SEM-EDS) results confirm that Na2CO3 is capable of enhancing the reduction of fayaltie, copper silicate and copper sulfide, which agrees well with thermodynamic analysis. Furthermore, the reduction mechanism of copper slag was demonstrated based on systematic experimental observations.
Similar content being viewed by others
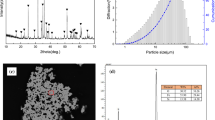
Explore related subjects
Discover the latest articles, news and stories from top researchers in related subjects.Avoid common mistakes on your manuscript.
Introduction
Copper smelting slag is a waste generated from pyro-metallurgical production of copper from copper sulfide concentrate. Production of 1 ton of copper generates approximately 2.2–3 tons of copper slag, and nearly 30 million tons of slag is deposited every year in the world.1,2 Considerable amounts of copper slag are stored naturally, resulting in serious economic and ecological issues, such as occupation of large areas of land, secondary environmental pollution and a waste of resources.3 Hence, it is extremely urgent to develop appropriate technology for comprehensive utilization of copper smelting slag.
Typically, copper smelting slag contains 40–45 wt.% of iron and about 1.0 wt.% of copper, as well as minor amounts of other elements, indicating that it is a valuable resource for utilization.4,5,6 In recent years, many treatment processes have been proposed with the aims of recycling and reusing the slag, including chemical leaching,7,8 bio-leaching,9 magnetic roasting,10 selective agglomeration–reverse flotation,11,12 slag modification–physical separation13,14,15 and direct reduction–magnetic separation.16,17 It is noted that the direct reduction process to upgrade this type of complex and refractory slag has recently been a topic of metallurgical interest. In the carbothermic direct reduction process of copper slag, the iron oxides are reduced to metallic iron and copper sulfide is reduced to metallic copper, and simultaneously the metallic copper dissolves into a metallic iron matrix-forming alloy (Fe-Cu). Then, the crude alloy powder is obtained by magnetic separation, which can replace part of the sponge iron, scrap steel and electrolytic copper to produce weathering-resistant steel by an electric arc furnace. However, the long reduction time, high energy consumption and low iron and copper metallization rates are the major problems in the direct reduction process of copper slag, since iron mainly exists in the form of fayalite and copper is present in matte. Unfortunately, few studies of the enhancement reduction of copper slag have so far been conducted. Pre-oxidation of copper slag and the addition of additives are the main technical routes to enhance copper slag reduction. Zhu et al. considered the effect of a compound additive containing iron oxides on the carbothermic reduction of copper slag.16 The results showed that compound additives significantly increased iron recovery due to the growth of metallic iron particles. Zuo et al. revealed the effects of burnt lime on the reduction of copper slag. It is pointed out that CaO can promote the separation of Fe and Si, which favors of the reduction of copper slag.18 However, excessive addition of CaO may suppress reduction reactions.
The purpose of this research was to investigate the effect of Na2CO3 on the carbothermic reduction of copper slag, while optimizing the ratio of Na2CO3 to enhance the reduction of copper slag and reveal the reaction mechanism of the carbothermic reduction process.
Experiments
Materials
The copper smelting slag used in the current experiment was collected from Tongling Non-ferrous Metals Group (China). The chemical compositions of the slag measured using x-ray fluorescence is presented in Table I, which shows that the main ingredients of the copper slag are 39.85 wt.% FeO and 32.33 wt.% SiO2, meanwhile the Cu content also reaches as high as 0.65%. The main crystal phases of copper slag determined by x-ray diffraction (XRD) are fayalite and magnetite (as shown in supplemental Fig. 1). Chemical phases and distribution of copper in copper slag are listed in Table I which shows that the copper mainly occurs in copper sulfide, metallic copper and copper silicate.
The soft coal was used as reductant, with fixed carbon of 52.12% on an air dry basis (FCad), volatile matter of 30.41% on dry ash free (V daf), ash of 4.49% on a air dry basis (A ad), 0.58% of S and a melting temperature of 1376°C.
Analytic-grade Na2CO3 was used as an additive to promote the reduction of the copper slag, and 100% of its particles passed through a 0.074-mm sieve.
Experimental Methods
The ground copper slag and sodium carbonate were mixed thoroughly for balling. The green pellets were prepared in a disc pelletizer with 800 mm in diameter and 200 mm rim depth, rotating at 38 rpm and being inclined at 47° to the horizontal. Green pellets (diameter of 8–12 mm) were dried at 110°C for 2 h in a drying oven until their mass was unchanged. Approximately 60 g of dry pellets with a certain amount of coals were loaded into a corundum crucible (72 mm in diameter and 164 mm height) and roasted at 1250°C for 80 min in a muffle furnace (model KSY-12-18). After reducing, the crucible was removed from the furnace, and the reduced pellets were cooled to ambient temperature under the protection of nitrogen in preparation for the subsequent beneficiation process. The experiments and the respective conditions for each run are listed in Table II.
The reduced pellets were crushed to below 1 mm, and then a 20-g sample with 20 g water was ground to a particle size of 82.5% passing 0.074 mm in an XMQ240 × 90 ball mill. After that, the mix slurry was subjected to magnetic separation by a XCGS-73 Davies Magnetic Tube at a magnetic field intensity of 1800 Gs to produce Fe-Cu alloy powder.
The composition of the crude Fe-Cu alloy powder was measured by chemical analysis based on the national standards (GB/T 223.7-2002 and GBT15249.3-2009). The mineral compositions of the reduced pellets were identified by XRD (RIGAKU, D/Max-2500). Microstructures of the reduced pellets were performed by Leica DMLP optical microscopy, FEI Quata-200 scanning electron microscope (SEM) and EDAX32 genesis spectrometer. SEM images were recorded in backscatter electron mode operating in low vacuum mode at 0.5 Torr and 20 keV.
Results and Discussion
Thermodynamic Analysis
Many previous works have reported that the reduction of pure magnetite proceeds stepwise (Fe3O4 → FeO → Fe).19,20 Hence, the detailed discussion about that will not be demonstrated in current study. However, when the fayalite exists in the cooper slag, the thermodynamic conditions are obviously changing in the system and its reduction behaviors vary accordingly. The thermodynamic analysis of the reactions which possibly take place in the FeO-SiO2-C(CO) system is made up as follows:
Figure 1a shows the correlation of the standard free energy (ΔG θ) with the temperature for Eqs. 1 and 6. According to thermodynamic calculations, the fayalite is difficult to reduced by C or CO (Eqs. 1 and 3), but easier with the addition of sodium carbonate (Eqs. 2 and 4). Na2CO3 can promote the fayalite reduction by chemically combining with SiO2 to form free “FeO” and sodium silicate.
Copper in the copper slag mostly occurs in metallic copper, copper sulfide and copper silicate. The most likely reduction reactions in the Cu2S-Cu2SiO3-C(CO) system in the absence or presence of Na2CO3 are as follows:
Figure 1b shows the correlation of the standard free energy (ΔG θ) with the temperature for Eqs. 7–12. As can be seen, individual copper sulfide is very difficult to reduce to metallic copper. However, the presence of Na2CO3 provides a thermodynamic driving force for the reduction of copper sulfide. Meanwhile, the Na2CO3 is also capable of decreasing the free energy of reduction reactions of copper silicate, leading to more metallic copper generation.
Metal Recovery
Figure 2 shows the effects of Na2CO3 dosage on the metallization degree of the reduced slag pellets, and the iron and copper recovery of magnetic separation of the reduced slag pellets. The recovery of iron and copper and the metallization degree of iron and copper are increased significantly with an increase of Na2CO3 dosage from 0% to 8%, while the iron and copper contents of magnetic concentrate are changed slightly. When the Na2CO3 dosage is further increased, all the indexes remain. This is because the Na2CO3 can promote the reduction of fayalite, copper sulfide and copper silicate as discussed above (Fig. 1a and b). In addition, research has also revealed that Na2O can accelerate the transport of electrons from Fe3+ to Fe0 during the reduction process, change the lattice structure of iron oxides, and reduce the reaction activation energy, consequently improving reduction of copper slag.21
Phase Transformation of Copper Slag During Reduction Process
XRD analysis shown in Fig. 3a was carried out to reveal the difference in mineral compositions between two types of reduced pellets. As can be seen, the fayalite, silica and iron peaks appear in the reduced pellets without Na2CO3. It means that the some fayalite is also not reduced and remains in the slag. With the addition of 8% Na2CO3, the peaks of metallic iron are sharply enhanced, while that of fayalite are weaker, and even vanish, which is caused by the full reduction of the fayalite. Therefore, it is confirmed that the XRD patterns are in good accordance with the thermodynamic analysis. However, the peak of copper sulfide is not observed in the XRD pattern due to its low content within the reduced pellets.
As shown in Fig. 3b, it is clear that much iron and copper sulfide (matte(Cu2S-FeS)), which is the main copper–bearing mineral and is present as the golden phase, often exists around the metallic particles or bridges different large metallic particles in the reduced pellets without Na2CO3. With the addition of Na2CO3, the content of the iron and copper sulfide phase is gradually decreased. When the dosage of Na2CO3 is 8%, the matte is not observed, which implies that almost all of these sulfides are reduced to the metallic phase. As a result, the copper metallization rate and copper recovery are correspondingly elevated.
Iron and Copper Element Distribution Behaviors
Figure 4 shows the map scanning and EDS in the reduced pellets. As can be seen from Fig. 4a, the copper distribution has a consistency with sulfur, and the aggregations of the copper and sulfur mainly contain Fe, Cu and S. For example, area 2 contains 33.48% S, 47.51% Fe and 30.91% Cu, which further confirms that the copper compounds in the pellets without Na2CO3 are not completely reduced and still exist as copper sulfide(matte), resulting in lower copper recovery and high sulfur content in the Fe-Cu alloy powder.
In contrast, there is no obvious aggregation between the copper phase and the sulfur phase (Fig. 4b), while the sulfur phase distributes dispersively in the reduced pellets with 8% Na2CO3. Additionally, the sodium phase shows the same distribution shape with silica, and they distinctly separate from the iron phase. This result is identical with the line scanning results shown in Fig. 4c. It can be inferred from this that Na2CO3 not only reinforces the reduction of copper sulfide but also promotes the metallic iron generation by reacting with the fayalite to generate sodium silicate. Hence, the liberation of the alloy phase from the gangue will become easier, which favors the magnetic separation process, leading to a higher recovery of copper and iron.
The iron and copper content in the slag is important since it determines not only the degree of reduction of the iron and copper minerals but also how efficiently iron and copper transfers from the silicate slag to the metallic alloy (Fe-Cu) phase during the reduction process. In Figs. 5 and 6, the iron and copper content was detected at six values determined by EDS point analysis in the slag phase. With the addition of Na2CO3, the iron and copper content of the slag phase is obviously decreased. For this decrease, it was inferred that the iron and copper compounds involving the fayalite and copper silicate were gradually reduced to the metallic phase, and subsequently the metallic grains emigrated into the metallic iron phase to form coarse alloy particles. Moreover, this result also further reveals that Na2CO3 is capable of enhancing the reduction of silicate minerals (fayalite and copper silicate), which agrees well with the thermodynamic analysis.
Combining all the information discussed previously, the direct reaction mechanism of copper slag was summarized (as shown in supplemental Fig. 2). In the absence of Na2CO3, the carbothermic reductions of the fayalite, iron sulfide, copper sulfide and copper silicate require an extremely high temperature. Therefore, a large amount of copper still remains as copper sulfide in the gangue instead of being reduced and entering into the metallic iron phase to form the alloy. In the presence of Na2CO3, the reduction of those compounds becomes easier due to the reaction and decomposition of the complex silicate and matte with Na2CO3 to form Na2SiO3 and Na2S. As a result, more Fe-Cu alloy phase is generated.
Conclusions
The effect of Na2CO3 on the enhancement of carbothermic direct reduction of copper slag was studied and the following conclusions can be drawn:
-
1.
Sodium carbonate enhances the beneficiation of Fe and Cu during the carbothermic reduction–magnetic separation process of copper slag. With the addition of 10% sodium carbonate, the metallization rate of the iron and copper in the reduced pellets rose from 67.78% to 93.21% and from 69.54% to 83.45%, respectively. Meanwhile, the recovery of iron and copper in the magnetic separation process increased from 78.13% to 95.08% and 73.53% to 85.33%, respectively.
-
2.
Thermodynamic calculations show that the Na2CO3 is capable of enhancing the reduction of the fayalite, copper sulfide and copper silicate, leading to improvements in the iron and copper metallization rates. Phase transformation and element distribution behaviors of the reduced pellets in the absence or presence of Na2CO3 confirm the results of the thermodynamic calculations.
References
B. Gorai, R. Jana, and M. Premchand, Resour. Conserv. Recycl. 39, 4 (2003).
H. Shen and E. Forssberg, Waste Manag. 23, 10 (2003).
H. Wang, J. Guangdong Nom-ferr. Met. (In China) 13, 4 (2010).
A. Harvey, Resour. Conserv. Recycl. 43, 353 (2005).
J.H. Heo, Y. Chung, and J.H. Park, J. Clean. Prod. 13, 777 (2016).
M. Sánchez and M. Sudbury, J. Min. Metall. B 49, 161 (2013).
I. Muravyov, V. Fomchenko, V. Usoltsev, A. Vasilyev, and F. Kondrateva, Hydrometallurgy 119, 40 (2012).
D. Urosevic, M. Dimitrijevic, Z. Jankovic, and D. Antic, Physicochem. Probl. Min. Process. 51, 71 (2015).
S. Panda, S. Mishra, D.S. Rao, N. Pradhan, U. Mohapatra, S. Angadi, and B.K. Mishra, Korean J. Chem. Eng. 32, 667 (2015).
K. Mawejaa, T. Mukongob, and I. Mutomboc, J. Hazard. Mater. 164, 856 (2009).
W. Bruckard, M. Somerville, and F. Hao, Miner. Eng. 17, 495 (2004).
A. Sarrafi, B. Rahmati, and H.R. Hassani, Miner. Eng. 17, 457 (2004).
Z.Q. Guo, D.Q. Zhu, J. Pan, T.J. Wu, and F. Zhang, Metals 6, 86 (2016).
Z.Q. Guo, D.Q. Zhu, J. Pan, and F. Zhang, JOM 69, 2341 (2016).
Y. Fan, E. Shibata, A. Iizuka, and T. Nakamura, MMTB 46, 2158 (2015).
X.L. Zhou, D.Q. Zhu, J. Pan, and T.J. Wu, Int. ISIJ 55, 1347 (2015).
B. Su, S. Kim, S. Ki Jo, D. Shin, J.C. Lee, and S.B. Jeong, Int. J. Miner. Process. 143, 43–49 (2015).
Z. Zuo, Q. Yu, J. Liu, Q. Qin, H. Xie, F. Yang, and W. Duan, Int. ISIJ. 57, 220 (2017).
B. Chanchal, G. Prithviraj, and D. Arnab, Int. J. Min. Metall. Mater. 12, 1360 (2016).
B. Peters and F. Hoffmann, Chem. Eng. J. 304, 692 (2016).
D.Q. Zhu, Z.Q. Guo, J. Pan, and F. Zhang, Metals 6, 6 (2016).
Acknowledgements
The authors wish to express their thanks to the National Key Technology R&D Program of China (No. 2013BAB03B04) for the financial support of this research, and also would like to thank Co-Innovation Center for Clean and Efficient Utilization of Strategic Metal Mineral Resources of Hunan Province, which supplied us the facilities and funds to fulfill the experiments.
Author information
Authors and Affiliations
Corresponding author
Electronic supplementary material
Below is the link to the electronic supplementary material.
Rights and permissions
About this article
Cite this article
Guo, Z., Zhu, D., Pan, J. et al. Effect of Na2CO3 Addition on Carbothermic Reduction of Copper Smelting Slag to Prepare Crude Fe-Cu Alloy. JOM 69, 1688–1695 (2017). https://doi.org/10.1007/s11837-017-2410-y
Received:
Accepted:
Published:
Issue Date:
DOI: https://doi.org/10.1007/s11837-017-2410-y