Abstract
The crack propagation behavior of pipeline steels with or without AC application was studied in high pH solution using the crack propagation experiment (cyclic load). The results show that there is a significant difference in the crack propagation behavior of steels with or without AC interference. The crack growth rate (CGR) of steel under superimposed AC is considerably greater than that without AC. AC could cause an obvious effect on the crack propagation behavior, and enhance the CGR. The crack propagation behavior of steel under AC application in high pH solution is analogous to that in near-neutral pH solution.
Similar content being viewed by others
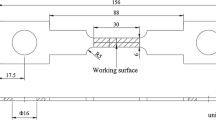
Avoid common mistakes on your manuscript.
Introduction
With the rapid development of high-voltage AC power transmission lines, AC-powered rail transit systems and their sharing common right of way with the pipelines, AC corrosion is becoming the great threat to the safe operation of pipelines (Ref 1, 2). Fu (Ref 3) found that an applied AC could degrade passivity of carbon steel developed in carbonate/bicarbonate solutions. Xu (Ref 4) indicated that the corrosion of 16Mn pipeline steel was enhanced by the applied AC current density of 0-400A/m2. Kuang (Ref 5) thought that pitting corrosion could be initiated on the steel at sufficiently high AC current densities in both high pH and near-neutral pH solutions.
Our previous research (Ref 6) indicated that ×80 pipeline steel under a long-term effect of AC interference exhibited a high SCC susceptibility in high pH solution and the crack propagation mode is transgranular. Moreover, the research result suggested that the crack propagation rate of the steel was enhanced due to AC application, compared to that in the absence of AC current (i.e. IGSCC fracture). At present, there is no related research about the crack propagation behavior of pipeline steel under AC application. In order to further quantify the crack growth rate (CGR) of the steel tested in the presence of AC, in this paper, the crack propagation behavior of ×80 pipeline steel under applied AC was investigated in high pH solution using the crack propagation experiment.
Experimental
The compact tension (CT) specimen was cut from hot-rolled plate of API ×80 pipeline steel. The chemical composition of the steel is (wt.%): C 0.070, Si 0.216, Mn 1.80, P 0.0137, S 0.0009, Mo 0.182, Cr 0.266, Cu 0.221, Ni 0.168, Nb 0.105, Al 0.026, Ti 0.013, V 0.001, N 0.003 and Fe balance. The mechanical properties at room temperature were measured with tensile strength of 635 MPa and yield strength of 560 MPa. The specimen was made according to the procedures described in ASTM E647-08 (Fig. 1). In order to achieve an accurate measurement, the surface of the CT specimen was polished to 2000 grit finish prior to pre-fatigue cracking in air, and the crack length was measured using an optical microscope. In this paper, the classical solution system of high-pH SCC (0.5 mol/L Na2CO3 + 1 mol/L NaHCO3) was used as the solution. The pH of the solution was 9.32.
The crack propagation experiment was conducted using a WDML-30KN Materials Test System. Cycle loads were applied to the CT specimen. Each cycle started from the maximum load (17,500 N) to the minimum load (10,000 N), and then the process was reversed. The initial corresponding △K value is 25.226 Mpa m0.5. The test was performed at a frequency of 0.00125 Hz (800 s/cycle) for the entire process. The specimen was fixed in an organic glass container, and the container was kept airproof. The test was carried out using a three-electrode cell system, where the CT specimen was used as a working electrode, a platinum plate as a counter electrode, and a saturated calomel electrode (SCE) as a reference electrode. The specimen was maintained at a polarized potential of −580 mV (versus SCE). The potential applied to the specimen was in the middle of the potential range causing IGSCC (intergranular stress corrosion crack) (Ref 7). The sample was maintained at the potential by means of a PS-12 potentiostat.
In order to compare the crack propagation behavior of the steel without superimposed AC, a function generator of AT1645-3 model was used to provide the AC signal of 5 V. The AC sine wave with a frequency of 50 Hz was applied between the CT specimen and the platinum plate. The applied AC root mean square value of 10 mA in this work was measured using a clamp meter. During the whole process of the crack propagation test, the applied AC and DC currents were maintained at the initial condition. The experiment was performed at ambient temperature (~22 °C). After the test was completed, the corrosion product formed on the specimen was removed by a chemical method. By degreasing with acetone, followed by cleaning with deionized water, and finally drying in vacuum. The crack propagation morphologies were observed by stereo microscopy.
Results and Discussion
Microstructure Morphology
Figure 2 shows the microstructure of ×80 pipeline steel. The microstructure of the steel is mainly composed of polygonal ferrite, acicular ferrite and a number of granular bainites distributed at grain boundaries.
The microstructure of ×80 pipeline steel (Ref 8)
Crack Propagation Analysis
Figure 3 shows the crack length of ×80 steels with or without AC application versus number of cycles. As seen in Fig. 3, a remarkable difference in the crack propagation behavior is found between the sample under superimposed AC and that without AC application. It is clearly seen that the crack length of the steel tested in the presence of AC increases rapidly with the increase of cycle number, while the crack length increases slightly in the absence of AC current. At the same number of cycles, the crack length in the former case is significantly longer than the latter one. Therefore, for the conditions used the CGR of the steel with AC application is greater than that when no AC is applied. This demonstrates that the CGR of ×80 steel in high pH solution is greatly enhanced by applying superimposed AC.
Figure 4 shows the average crack propagation rates of ×80 steels under conditions with and without AC application. Under AC application, when the cycle number of the cyclic load test is 804, the crack length could reach up to 4.539 mm. In contrast, without the superimposed AC, the crack length is as short as about 0.485 mm at the cycle number of 809. By comparison, at the nearly same cycle number, the crack length of the steel tested in the absence of AC is much shorter than that with an AC application. As observed from the calculation, the average crack propagation rate (da/dt) of steel with the applied AC is 5.645 × 10−3 mm/cycle (7.056 × 10−6 mm/s), while that without AC application is 5.99 × 10−4 mm/cycle (7.48 × 10−7 mm/s). This indicates that there is a remarkable difference between the average crack propagation rates of ×80 steels under conditions of with and without AC application. AC could accelerate the crack propagation rate of ×80 pipeline steel in high pH solution.
It was reported that (Ref 9) the crack growth rates (CGR) of pipeline steel in near-neutral pH solution could reach up to 10−6 mm/s. In this paper, the CGR of steel under AC application is close to that of steel in a near-neutral pH-SCC. Therefore, these research results indicate that the crack propagation behavior is analogous to that of pipeline steel in near-neutral pH solution, which is shown in the previous literature (Ref 6).
Figure 5 shows the CGR versus △K in the presence of AC application. The crack propagation rate of ×80 steel increases with the increasing △K. The range of da/dN is from 0 to 0.00565 mm/cycle. At the initial stage of crack propagation, the da/dN rapidly increases with the increasing △K, and then, the da/dN increases steadily. This indicates that the crack tip of the steel with AC application propagates more stably.
Figure 6 shows the crack propagation morphologies of ×80 steels under conditions with and without AC application. Obvious differences in the crack propagation morphologies are observed between the specimens tested in the presence of AC and that without AC application. In the absence of AC, the crack is narrow, shallow and short. And the corrosion of the crack wall is slight. Moreover, a crack branching is observed, and the crack propagation is flexural. All these characteristics are similar to that of classical intergranular fracture. In contrast, when AC is applied, the crack is very wide, deep and long. The crack propagation shows a straight line, and there is no crack branching phenomenon. In addition, the crack wall exhibits a severe corrosion phenomenon. Those features are analogous to the classical TGSCC (transgranular stress corrosion crack) fracture. The significant differences in these morphologies indicate that AC application could cause important effect on the crack propagation behavior of ×80 steel and could enhance the crack propagation rate. It is also verified that the mechanism of high-pH SCC of pipeline could be changed due to the application of AC current (Ref 6). It may be noted that due to the very slow frequency of load cycling, a complex combination of SCC and corrosion fatigue is occurring.
Conclusions
The result of the crack propagation test shows that there is a significant difference between the crack propagation behaviors of ×80 steels under conditions with and without the application of AC. The average crack propagation rates (da/dt) of the steels tested with and without AC application are 7.056 × 10−6 and 7.48 × 10−7 mm/s, respectively. The CGR of steel under superimposed AC condition is considerably greater than that without AC interference. AC accelerates the crack propagation rate of pipeline steel. The crack propagation behavior of steel under AC application in high pH solution is analogous to that in a near-neutral pH solution (TGSCC).
References
L.W. Wang, X.H. Wang, Z.Y. Cui, C.W. Du, and X.G. Li, Effect of Alternating Voltage on Corrosion of ×80 and ×100 Steels in a Chloride Containing Solution—Investigated by AC Voltammetry Technique, Corros. Sci., 2014, 86, p 213–222
S. Goidanich, L. Lazzari, M. Ormellese, and A.C. Corrosion, Part 2: Parameters Influencing Corrosion Rate, Corros. Sci., 2010, 52, p 916–922
A.Q. Fu and Y.F. Cheng, Effects of Alternating Current on Corrosion of a Coated Pipeline Steel in a Chloride-Containing Carbonate/Bicarbonate Solution, Corros. Sci., 2010, 52, p 612–619
L.Y. Xu, X. Su, Z.X. Yin, Y.H. Tang, and Y.F. Cheng, Development of a Real-Time AC/DC Data Acquisition Technique for Studies of AC Corrosion of Pipelines, Corros. Sci., 2012, 61, p 215–223
D. Kuang and Y.F. Cheng, Understand the AC Induced Pitting Corrosion on Pipelines in Both High pH and Neutral pH Carbonate/Bicarbonate Solutions, Corros. Sci., 2014, 85, p 304–310
M. Zhu, C.W. Du, X.G. Li, Z.Y. Liu, H. Li, and D.W. Zhang, Effect of AC on Stress Corrosion Cracking Behavior and Mechanism of ×80 Pipeline Steel in Carbonate/Bicarbonate Solution, Corros. Sci., 2014, 87, p 224–232
Z.F. Wang and A. Atrens, Initiation of Stress Corrosion Cracking for Pipeline Steels in a Carbonate-Bicarbonate Solution, Metall. Mater. Trans. A, 1996, 27A, p 2686–2691
M. Zhu, C.W. Du, X.G. Li, Z.Y. Liu, S.R. Wang, T.L. Zhao, and J.H. Jia, Effect of Strength and Microstructure on Stress Corrosion Cracking Behavior and Mechanism of ×80 Pipeline Steel in High pH Carbonate/Bicarbonate Solution, J. Mater. Eng. Perform., 2014, 23, p 1358–1365
R.N. Parkins, W.K. Blanchard, Jr., and B.S. Delanty, Transgranular Stress Corrosion Cracking of High Pressure Pipelines in contact with Solutions of Near Neutral pH, Corrosion, 1994, 50, p 394–408
Acknowledgments
The authors gratefully acknowledge the financial support from the National Natural Science Foundation of China (No. 51371036 and No. 51131001), and the Science Foundation of Zhejiang Sci-Tech University (ZSTU).
Author information
Authors and Affiliations
Corresponding author
Rights and permissions
About this article
Cite this article
Zhu, M., Ou, G.F., Jin, H.Z. et al. Study on the Crack Propagation Behavior of ×80 Pipeline Steel Under AC Application in High pH Solution. J. of Materi Eng and Perform 24, 2422–2425 (2015). https://doi.org/10.1007/s11665-015-1498-x
Received:
Revised:
Published:
Issue Date:
DOI: https://doi.org/10.1007/s11665-015-1498-x