Abstract
In a cycle tubular photobioreactor, Chlorella pyrenoidosa was cultured in undiluted wastewater from ethanol fermentation using cassava powder as raw material. The results showed that the optimum cultivation conditions were initial pH of 6.0, temperature at 27°C, continuous illumination at 3,000 lux, and cycle speed of 110 ml min−1. Under these optimum conditions, after the logarithmic phase of batch cultivation with wastewater of pH 6.0, the reactor could be continuously operated with natural pH wastewater (3.8) as feed solution. By a dilution ratio of 0.17 day−1, it could be operated stably for over 30 days in continuous cultivation. pH, removal rate of chemical oxygen demand, and biomass (cell dry weight) concentration ranged from 6.22 to 6.47, 72.21 to 76.32% and 3.55 to 3.73 g l−1, respectively. After treatment, the wastewater could be used again in the process of ethanol fermentation.
Similar content being viewed by others
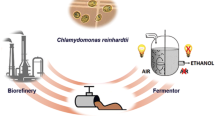
Explore related subjects
Discover the latest articles, news and stories from top researchers in related subjects.Avoid common mistakes on your manuscript.
Introduction
Cassava is a major and widely planted agricultural product in southern China. Due to its high starch content and low cost, it becomes an important raw material of fuel ethanol production. About 8–10 ton wastewater is discharged when 1 ton of anhydrous alcohol is produced. The wastewater containing organic and acidic substances is harmful to the environment. Because of its poor nutrient content, low BOD5/CODcr ratio, and low pH (Hu et al. 1998), the productivity was very low when Candida or methane-producing bacteria were used to produce single cell protein or methane using the wastewater as material. The high production cost limits the application of these technologies.
With microalgae and macrophytes, a two-step sequential treatment process was used to treat the recalcitrant wastewater from ethanol and citric acid production. The wastewater was diluted 10 times with wash water from the production line (Valderrama et al. 2002). Microalgae or cyanobacteria have also been cultured in many other kinds of wastewater for algal production and to treat the waste water, for example Spirulina maxima and Chlorella pyrenoidosa in swine wastewater (Canizares-Villanueva et al. 1995) and olive mill wastewater (Villasclaras et al. 1996), respectively. The wastewater must be pretreated with percolation, dilution, pH regulation, and sterilization. This process consumes a large quantity of fresh water for dilution.
In our laboratory, we have selected and acclimatized the microalga C. pyrenoidosa which has been previously cultured in undiluted wastewater from cassava ethanol production (WCEP). In this article, a simplified cycle tubular photobioreactor on an experimental scale is reported, aimed at producing C. pyrenoidosa with WCEP which would be treated economically at same time. The operating conditions and process of the photobioreactor were analyzed and discussed. The results indicate that the process was successful. This method of bio-treating wastewater with poor nutrient content could reduce dilution, save freshwater and be applied to production. If it was combined with the process of ethanol production, almost zero discharge of wastewater would be realized.
Materials and methods
Maintenance and pre-culture of microalgae
C. pyrenoidosa, FACHB-9 was purchased from Institute of Hydrobiology, the Chinese Academy of Sciences, Wuhan, China. After it had been acclimatized, it was maintained on WCEP of pH 6.0.
The inocula were performed under sterile conditions. Aliquots of 20 ml were transferred to 250-ml conical flasks containing with 100 ml of WCEP of pH 6.0 and cultured at temperature (25°C) under continuous illumination (2,000 lux) and artificial intermittent shaking (four times in a day) for 5 days.
WCEP preparation
In a 25-l fermenter, ethanol fermentation was carried out in the medium consisted of cassava powder and water at the ratio of 1:3 (g:g). After 60-h fermentation, the ethanol content, reducing sugars, total sugars, and pH of culture liquid were analyzed. Ethanol was removed by distillation. As a pretreatment, the effluent obtained was centrifuged at 2,000g for 10 min to decrease the concentration of total solid substance (TSS). The supernatant was designated as wastewater from cassava ethanol production (WCEP). The COD, BOD, TSS, and pH of WCEP were 9.32 × 104 mg l−1, 4.61 × 104 mg l−1, 670 mg l−1, and 3.80, respectively. WCEP was kept at −10°C for future use.
Cycle tubular photobioreactor and culture method
A schematic diagram (Fig. 1) shows a 200-ml laboratory scale cycle tubular photobioreactor which was comprised of: a cycle glass tubular, fluorescent lamp, and two constant pumps, designed according to methods described by Watanabe and Saiki (1997), Travieso et al. (2001), Scragg et al. (2002), and Walter et al. (2003). This design has some advantages, such as a large surface-to-volume ratio, easy control of temperature, and occupies a small ground area. The reactor was set in a simple greenhouse with an air-conditioner, filled with hypochlorous acid for 1 day, flowed and washed clearly with sterile water for use. Batch, fed-batch, and continuous operation were used to culture the microalgae, according to each case condition.
Analytical determinations
The algal cells were washed with 0.5 M HCl to remove the precipitated salts and other inorganic substances, rinsed with distilled water, dried at 105°C for 24 h and weighed. When the volume of sample was so small in batch operation or the cell concentration was so low that cell weight could not be accurately determined, it was estimated by measuring the optical density at 680 nm (Spectrophotometer U3000, Japan). In the latter case, the O.D. readings were converted to cell dry concentration using predetermined calibration curves. COD, BOD, TSS, and organic acid were analyzed according to standard methods (APHA et al. 1992). Ethanol content was determined by distillation. pH was measured by Mettler Toledo Electrochemical analytical meter Model Seven Multi. Microscopy was performed using an Olympus Microscope Model CX31. Light intensity was measured by DT-1301 Light meter, CEM Company limited (Hong Kong). The quantity of organic acid was confirmed by external standard method with Agilent, HP-1100, US. COD removal rate (CODrr), productivity value (P) (different operation with different formula), and conversion yield of COD into algal cell weight (Y B/COD ) were calculated using the following formulae:
-
CODrr = (CODinital − CODfinal)/CODinital × 100%
-
Pbatch = cell weight/culture time (used in batch operation, culture time = 6)
-
Pfed-batch = cell weight × partition (used in fed-batch operation)
-
Pcontinuous = cell weight × D (used in continuous operation)
-
Y B/COD = cell weight/(CODinital−CODfinal)
All data were the average of the triplicates for sample.
Results and discussion
Effect of cultivation conditions on C. pyrenoidosa
Cultivation conditions have an important effect on the growth of microalgae (Pirt et al. 1983; Shi et al. 2000; Walter et al. 2003) and the effects of different cultivation conditions vary. Thus, it was necessary to study the optimum conditions for growth of C. pyrenoidosa in WCEP. The main factors to impact on microalgal growth included pH, temperature, light intensity, and mixture of culture liquid.
Initial pH
The pH in the medium could affect the efficiency of carbon usage, absorbability of ions, recycling, and toxicity of metabolites in the growth of microalgae (Borowitzka and Borowitzka 1988). The optimum growth pH was different between different algae. Figure 2A illustrated that C. pyrenoidosa could grow at initial pH values between 5.0 and 7.5, but pH 6.0 was optimum.
Temperature
The temperature is also an important factor which could affect algal metabolism (Goldman and Carpenter 1974). According to the optimum growth temperature, Chlorella could be divided into two kinds of strains: low temperature (25–30°C) and high temperature (35–40°C) strains (Sorokin 1959). Generally, the low temperature strains are chosen to be cultured in industry to save energy costs (Martinez and Orus 1991; Ogbonna et al. 1997). Figure 2B shows that the optimum culture temperature was 27°C. By the way, the tubular photobioreactor could operate well in a simple greenhouse to save heating and artificial illumination costs.
Light intensity
There existed an optimum light intensity which was called “light saturation point” in the growth of each microalga (Gong and Chen 1997). The overfull light intensity could not be used by algae and would increase the production cost. Deficient light intensity limited microalgal growth (Myers 1953). The result was that light saturation point was 3,000 lux (Fig. 2C).
Cycle speed
Flowing cultivation was an important condition to be used in order to maximize biomass. Good mixing can increase photosynthetic efficiency, prevent agglomeration and sinking of microalgae, and reduce the concentration gradients of substrates and metabolites (Borowitzka and Borowitzka 1988). The result (Fig. 2D) further proved the thesis. If the cycle speed was too low to mix the culture liquid well, the algae could not grow well. On the other hand, a cycle speed so fast that the shear stress of the pump on the algae was increased also led to poor growth. The optimum cycle speed was 110 ml min−1 (Fig. 2D).
In conclusion, the results mentioned above showed that the optimum cultivation conditions were initial pH of 6.0, temperature at 27°C, illumination at 3,000 lux, and cycle speed of 110 ml min−1.
Batch operation in photobioreactor
Under above optimum conditions, batch operation was operated with undiluted WCEP in which the pH was regulated with 2 M NaOH, 3 ml culture liquid was sampled from outlet (Fig. 1-(5)). Cell weight, COD, the content of organic acids, and pH were examined every morning at the same time. The growth of C. pyrenoidosa in batch operation is shown in Fig. 3. The logarithmic phase was from 1 to 4 days.
The cell weight achieved the maximum (3.64 g l−1) at the 6th day. pH rose from 6.00 to 8.52. CODrr, P, and Y B/COD were 71.21%, 0.61 g (day × l)−1, and 0.05 g g−1, respectively (Table 1). The removal rate of lactic acid, acetic acid, citric acid, and succin acid were 96.42%, 100%, 95.89%, and 39.44%, respectively (Table 2).
As a culture grew, the pH of the medium changed greatly when either nitrate or ammonium was used. In particular, the rapid utilization of ammonium ion by an alga caused a severe drop in pH (Shi et al. 2000). However, in this study, the pattern of pH, cell weight, and CODrr showed the COD was bioconverted by algae. Furthermore, the pH rise in medium was very significant. This phenomena suggested that fed-batch and continuous operation might be operated with WCEP of unadjusted pH (3.8) as feed solution.
Fed-batch operation with unadjusted pH (3.8) WCEP as the feed solution
First, the photobioreactor was operated as batch reactor with undiluted WCEP (pH 6.0) as medium. The growth of C. pyrenoidosa was very similar to that shown in Fig. 3. Second, from the 5th day of batch operation, fed-batch operation was operated by a partition of 20% (V/V) every day. Briefly, 40 ml culture liquid was removed, and simultaneously the same volume of undiluted and sterile WCEP of natural pH (3.8) was added to the reactor daily. Cell weight, pH, and COD of samples were measured. Figure 4 shows that the bioreactor could be operated for 6 days at this partition.
C. pyrenoidosa could utilize the substances in WCEP and this resulted in a significant rise in pH (Fig. 3). However, Fig. 4 shows that fed-batch operation with natural pH (3.8) WCEP at this partition (20% day−1) resulted in the newly added acidic material not being fully bio-converted by the microalgae in a day. Systematically, the pH decreased day by day. At the 6th day, the pH decreased to 5.54 (Table 1). If natural pH WCEP was pumped in, the initial pH would decrease to below 5.0 and the microalgae could not be cultured (Fig. 2A). Therefore, the whole culture period consisted of two steps: 5 days batch operation and 6 days fed-batch operation by a partition of 20% day−1. During the latter step, the pH decreased from 8.12 to 5.54. Maximum values of P and Y B/COD were 0.71 g (day × l)−1 and 0.06 g g−1, respectively.
Fed-batch operation saved the time for washing of the system and preparation of microalgal seeds, so it was easier to operate and more economical than batch operation.
Continuous operation with natural pH (3.8) WCEP as the feed solution
In the first step, the photobioreactor was operated as batch reactor for 5 days, as described previously.
In the second step (Fig. 5-I) and fourth step (Fig. 5-IV), the dilution ratio (D) was 0.20 day−1, and 40 ml culture liquid was collected at the same time every day from the sample collector (Fig. 1-(7)). The second step was from the 5th day of batch operation, the cycle bioreactor was operated in continuous cultivation with natural pH (3.8) WCEP as the feed solution for 12 days. The pH decreased slowly day by day over the period. Maximum values of P and Y B/COD were 0.74 g (day × l)−1 and 0.06 g g−1, respectively. The fourth step was started at day 48. The pH decreased to below 5.0 at day 54. This step remained for only 6 days. The results show that continuous operation (D = 0.2 day−1) could last more than 12 days, and was easier to operate than fed-batch operation (partition of 20% day−1). However, at this dilution ratio, the reactor could not be operated stably.
The result of continuous operation (A: pH, B: COD removal rate, C: Biomass). I, II, III, and IV represent D = 0.20 day−1(unsteady), D = 0.17 day−1(unsteady), D = 0.17 day−1(steady), and D = 0.20 day−1(unsteady), respectively. In each subfigure, points denoted by a different lower case letter differ significantly with t-test at P ≤ 0.05. Bars represent standard deviation
In the third step, starting at day 12, the reactor was operated at a dilution ratio of 0.17 day−1, in continuous operation with the same feed solution. About 34 ml culture liquid was gathered every day. After a regulated period (Fig. 5-II), the reactor could be operated for over 30 days stably (Fig. 5-III), keeping almost the same pH, same CODrr, and same biomass. They ranged from 6.22 to 6.47, 72.21 to 76.32%, and 3.55 to 3.73 g l−1, respectively (Table 1). Continuous operation (D = 0.17 day−1) which could omit the time for addition of medium and discharge of culture liquid, preparation of microalgal inoculum, washing of the system, and other non-productive processes, was the most stable, most economical, and easiest process to operate. After treatment, algae could be harvested. The pH of the wastewater was adjusted. A drop in COD which ranged from 2.59 to 2.21 × 104 mg l−1 with an average of 2.31 × 104 mg l−1 was achieved.
Treated water was recycled in ethanol fermentation
According to our preciously study (Zhang and Fan 1989; Ding et al. 2003), most of the lees filtrate could be recycled in the process of ethanol production, after the pH of wastewater had been adjusted with NaOH. The discharged wastewater could be reduced greatly. However, the wastewater could not be ignored and must be treated. The treated water could be recycled in the ethanol fermentation with 500-ml flasks, and then newly produced WCEP could be bio-treated with the process again. The result (Table 3) showed that the treated water had no negative effect in the process of ethanol production through four times recycle.
Conclusion
It was very economic that the wastewater from cassava ethanol fermentation could be treated by microalgae in order to produce microalgal biomass, regulate pH, and make a drop of COD. After harvesting the algae, although some part of COD remained in the treated water, it was so low (2.31 × 104 mg l−1) that it had no negative effect in the process of ethanol production. The character of our technology for wastewater biotreatment were that WCEP was not diluted and directly used by the microalgae, and the treated wastewater could be recycled in the process of ethanol production entirely and directly.
References
APHA, AWW, WPCF (1992) Standard methods for the examination of water and wastewater, 17th edn. Diaz de Santos, Madrid
Borowitzka MA, Borowitzka LJ (1988) Microalgal biotechnology. Cambridge University Press, Cambridge
Canizares-Villanueva RO, Dominguez AR, Cruz MS, Rios-Leal E (1995) Chemical composition of cyanobacteria grown in diluted aerated swine wastewater. Bioresour Technol 51:111–116. doi:10.1016/0960-8524(94)00099-M
Ding Z-y, Wang Y-h, Zhang L, Shi G-y, Zhang K-c (2003) Study on recycling the filtrate of distillage filtrated by membrane. Liquor Mak 30:61–63 (in Chinese)
Goldman JC, Carpenter EJ (1974) A kinetic approach to the effect of temperature on algal growth. Limnol Oceanogr 19:756–766
Gong X-d, Chen F (1997) Optimisation of culture medium for growth of Haematococcus pluvialis. J Appl Phycol 9:437–444. doi:10.1023/A:1007944922264
Hu Y-y, Wu C-f, Ye W-s, Cen C-p (1998) A preliminary study on solid–liquid separation of waste distillers from alcohol production with dry cassava. Res Environ Sci 11:45–48 (in Chinese)
Martinez F, Orus MI (1991) Interactions between glucose and inorganic carbon metabolism in Chlorella vulgaris strain UAM 101. Plant Physiol 95:1150–1155
Myers J (1953) Growth characteristics of algae in relation to the problems of mass culture. In: Burlew JS (ed) Algal culture—from laboratory to pilot plant. The Kirby Lithographic Company Inc, Washington, D.C
Ogbonna JC, Masui H, Tanaka H (1997) Sequential heterotrophic/autotrophic cultivation—an efficient method of producing Chlorella biomass for health food and animal feed. J Appl Phycol 9:359–366. doi:10.1023/A:1007981930676
Pirt SJ, Lee YK, Walach MR, Pirt MW, Balyuzi HH, Bazin MJ (1983) A tubular bioreactor for photosynthetic production of biomass from carbon dioxide: design and performance. J Chem Technol Biotechnol 33B:35–58
Scragg AH, Illman AM, Carden A, Shales SW (2002) Growth of microalgae with increased calorific values in a tubular bioreactor. Biomass Bioenergy 23:67–73. doi:10.1016/S0961-9534(02)00028-4
Shi X-m, Zhang X-w, Chen F (2000) Heterotrophic production of biomass and lutein by Chlorella protothecoides on various nitrogen sources. Enzyme Microb Technol 27:312–318. doi:10.1016/S0141-0229(00)00208-8
Sorokin C (1959) Tabular comparative data for the low-and high-temperature strains of Chlorella. Nature 184:613–614. doi:10.1038/184613a0
Travieso L, Hall DO, Rao KK, Benitez F, Sanchez E, Borja R (2001) A helical tubular photobioreactor producing Spirulina in a semicontinuous mode. Int Biodeterior Biodegradation 47:151–155. doi:10.1016/S0964-8305(01)00043-9
Valderrama LT, Campo CMD, Rodriguez CM, de-Bashan LE, Bashan Y (2002) Treatment of recalcitrant wastewater from ethanol and citric acid production using the microalga Chlorella vulgaris and the macrophyte Lemna minuscula. Water Res 36:4185–4192. doi:10.1016/S0043-1354(02)00143-4
Villasclaras SS, Sancho MEM, Caballero MTE, Perez AD (1996) Production of microalgae from olive mill wastewater. Int Biodeterior Biodegradation 38:245–247. doi:10.1016/S0964-8305(96)00057-1
Walter C, Steinau T, Gerbsch N, Buchholz R (2003) Monoseptic cultivation of phototrophic microorganisms-development and scale-up of a photobioreactor system with thermal sterilization. Biomolecul Eng 20:261–271. doi:10.1016/S1389-0344(03)00068-6
Watanabe Y, Saiki H (1997) Development of a photobioreactor incorporating Chlorella sp. for removal of CO2 in stack gas. Energy Conserv Manage 38(suppl):S499–S503. doi:10.1016/S0196-8904(96)00317-2
Zhang K-c, Fan Z-h (1989) Ethanol production technics of recycling lees filtrate (in Chinese). State intellectual property office of P.R.C 88101404.4, China
Author information
Authors and Affiliations
Corresponding author
Rights and permissions
About this article
Cite this article
Yang, Cf., Ding, Zy. & Zhang, Kc. Growth of Chlorella pyrenoidosa in wastewater from cassava ethanol fermentation. World J Microbiol Biotechnol 24, 2919–2925 (2008). https://doi.org/10.1007/s11274-008-9833-0
Received:
Accepted:
Published:
Issue Date:
DOI: https://doi.org/10.1007/s11274-008-9833-0