Abstract
Bamboo fibers are very promising reinforcements for polymer composites production due to its high aspect ratio and strong mechanical performances. In order to better understand their reinforcing potential, the mechanical properties of single bamboo fibers extracted from eleven commercial bamboo species in China were measured with a newly developed microtensile technique. For comparison, the mechanical properties of mature single Chinese Fir and Masson Pine wood fibers were measured. The results show that the average longitudinal tensile modulus of the eleven kinds of bamboo fibers ranges from 25.5 to 46.3 GPa with an average value of 36.7 GPa. For tensile strength, the value ranges from 1.20 to 1.93 GPa with an average value of 1.55 GPa. The tensile strength and modulus of bamboo fibers are nearly two times of that of single Chinese Fir and Masson Pine fibers, and significantly higher than most of the published data for other softwood fibers. The average elongation at break of bamboo fibers is about 4.84 %, only a little lower than the value 5.15 % of the tested mature softwood fibers. Additionally, bamboo fibers were found to have smaller diameters and larger aspect ratio than most documented wood fibers, which favored an improved reinforcing effect. These combined mechanical and morphological advantages highlight the potential of bamboo fibers as the reinforcing phase in polymer composites for structural purpose.
Similar content being viewed by others
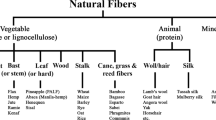
Explore related subjects
Discover the latest articles, news and stories from top researchers in related subjects.Avoid common mistakes on your manuscript.
Introduction
It is well acknowledged that the extraordinary mechanical performances of bamboo mainly originate from its fiber components [1, 2]. Bamboo fibers possess versatile advantages of biodegradability, fast renewability, easy accessibility, high aspect ratio, and strength to weight ratio, which make them ideal potential replacements for man-made fibers used in the production of fiber-reinforced composites. Therefore, bamboo fiber-reinforced composites are attracting great attention in the field of materials science, with large numbers of papers, recently reviewed by Liu et al. [3] and Khalil et al. [4], having been published on this subject.
Reinforcing fibers significantly influence the mechanical performance of composites. Therefore, having a large amount of reference data on the mechanical properties of bamboo fibers is very helpful for screening fibers to produce composites of certain desired grades. Although several studies have been performed on the mechanical properties of bamboo fibers, most of these properties are measured at the fiber bundle level [5, 6]. In order to better understand the maximal reinforcing potential of bamboo fibers in polymer composites, as well as the fiber-to-fiber interaction in solid bamboo, mechanical performance at the single fiber level should be measured. However, measurements at this level are often subject to large error, primarily caused by the lack of adequate techniques and equipment to properly grip fibers. This is especially true for short plant fibers, such as those typically found in wood and bamboo. These fibers normally range from 0.5 to 3 mm in length and 5 to 40 μm in diameter and require specialized methods and equipment to obtain precise and repeatable mechanical property testing results. One widely used approach is the microtension method, initially developed for characterization of single wood fibers by Jayne [7]. Since 1959, many investigations have been performed to improve the accuracy and efficiency of this method [8–11]. These studies have shown that apart from fiber gripping, stress concentration caused by deviation of fibers from the tensile direction is another important source of error in single fiber testing [12]. This factor was widely overlooked in most previous investigations. Therefore, recently, an improved microtensile technique for the mechanical measurement of single short plant fibers was developed and successfully used to measure the mechanical properties of single Moso bamboo fibers [13–18].
In this paper, this newly developed microtensile technique was expanded upon and utilized to obtain mechanical properties of single bamboo fibers chemically extracted from eleven types of commercial bamboo species found in China. Our purpose was to establish a statistically significant mechanical database of bamboo fibers, which has potential applications for the design and development of bamboo fiber-reinforced polymer composites or other bamboo fiber-based products. For comparison, single tracheid of Chinese Fir and Masson Pine were also tested, with results analyzed in terms of cell wall structure.
Materials and methods
Fiber preparation
Two-to-three-year old samples from eleven bamboo species were taken from different bamboo plantations in China. Cubic blocks were cut out from bamboo culm sections taken from 2 m above the basal node and then split into sticks measuring about 1 (radial) × 1 (tangential) × 15 (longitudinal) mm3. Wood blocks with similar size were taken from the mature xylem at breast height of Chinese Fir and Masson Pine. The background information for both bamboo and wood is listed in Table 1. The bamboo and wood sticks were macerated at 60 °C in a soft solution composed of one part 30 % hydrogen peroxide, four parts distilled water and five parts glacial acetic acid for 24 h. Subsequently, fibers were washed several times in distilled water and dried on glass slides at room temperature.
Microtension of single fibers
The widely accepted methodology of “ball and socket” fiber gripping was adopted for microtensile testing. Using fine tweezers, two epoxy droplets of approximately 200 μm in diameter were placed on each fiber with a spacing of 0.7–0.8 mm (Fig. 1a). The epoxy was allowed to solidify at 60 °C for 24 h, followed by an additional balance at room condition for 24 h. More details for sample preparation can be found Groom et al. [9]. A custom-built fiber-gripping system was specially developed and combined with a small commercial high-resolution mechanical tester (Instron Microtester 5848, USA, Fig. 1b) to measure the mechanical properties of short single plant fibers like bamboo. The key part of the fiber-gripping system is a pair of patented fiber grips that can grasp the epoxy droplets at the ends of fibers in tension (Fig. 1c). The fiber grips are designed to deal with fibers with length of more than 1.2 mm and diameter larger than 7 μm. The position of the grips can be finely adjusted in X, Y, and Z directions through an integrated 3D micro-adjustment stage by means of a horizontal and a vertical digital microscope. This ensured that the tensile direction was aligned exactly with the fiber axis. The initial length of fibers can be measured directly with the vertical microscope. The capacity of load cell used was 5 N. Elongation was recorded from the crosshead movement with a resolution of 0.02 μm and a constant speed of 48 μm min−1. More than 80 fibers were tested for each species of bamboo and wood to ensure that more than 50 reliable measurements were recorded. All the tensile testing was carried out under an environment of 23 °C and at 15–35 % relative humidity.
To calculate the tensile strength and modulus of bamboo fibers, the cell wall areas of every broken fiber were determined with a confocal scanning laser microscope (Meta 510 CSLM, Zeiss). The broken fibers were first immersed in 0.1 % acridine orange solution for 20 s and then rinsed several times in distilled water. The fibers were then imaged with a 63× immersion oil objective. Figure 2 shows the cross sections of the 11 types of bamboo fibers and the two softwood fibers, based on which the cell wall area of the fibers were then measured with software provided by the instrument producer. Load–elongation curves were then converted to stress–strain curves and the tensile strength and modulus obtained.
Microfibrillar angle measurement
Microfibrillar angle (MFA) refers to the angle between the cellulose orientation in the dominant S2 layer and fiber axis, which is widely known to have significant effects on most of the physical and mechanical properties of wood. An X-ray diffractometer (X’pert Pro, Panalytical, America) was used to determine the MFA of bamboo slices cut from the same blocks as those for fiber maceration to explore how MFA affects the tensile mechanical properties of single bamboo fibers. These samples have the dimensions of 1 (radial) × 10 (tangential) × 30 (longitudinal) mm3. A point-focused X-ray beam was applied to the tangential section with a scanning angle range of 0–360°. From the obtained diffraction intensity curves, MFA of bamboo fibers were determined based on the well-established 0.6 T method [19, 20].
Morphological measurement of fibers
A common transmission light microscope equipped with image software was used to measure the length, diameter, and aspect ratio of all the 11 types of bamboo fibers with the same origin as those for mechanical testing. More than 100 fibers were measured for each bamboo species.
Results and discussions
Typical stress–strain curves of single bamboo fibers
The typical stress–strain curves of single bamboo and wood fibers in tension are presented in Fig. 3. All the fibers tested exhibited a quasi-linear stress–strain behavior to failure. For wood fibers, the shape of the stress–strain curve is a function of MFA [9]. Fibers with MFA larger than 20° exhibit curvilinear behavior up to 60 % of the load-carrying capacity of fibers followed by linear behavior to failure, while fibers with MFA less than 20° appear to be fully linear during testing. In this paper, the tested wood fibers are extracted from the mature region of wood and normally have a MFA less than 20°, while the bamboo fibers tested normally have a MFA of less than 10° (as shown in Fig. 6). That explains why all the tested bamboo and wood fibers behaved linearly until failure.
The mechanical properties of single bamboo fibers
Figure 4 shows the histogram of longitudinal tensile modulus, ultimate strength, and elongation at break of the eleven types of bamboo fibers. The fibers from Bambusa longispiculata Gamble ex Brandis have the highest modulus of 46.3 GPa and the highest ultimate strength of 1.93 GPa. Meanwhile, its extensibility is also rather good with a value of 5.39 %. The fibers from Bambusa pervariabilis McClure have the lowest tensile modulus of 25.5 GPa, moderate ultimate strength of 1.44 GPa, and the highest elongation at break of 6.48 %. The average values of the 11 types of bamboo fibers were calculated at 36.7 GPa for tensile modulus, 1.55 GPa for ultimate strength, and 4.84 % for elongation at break.
Due to the previous lack of appropriate experimental methods and equipment, there is very limited information on the mechanical properties of single bamboo fibers. The only previous reported experimental data were by Yu et al. [13] for Moso bamboo [Phyllostachys heterocycla (Carr.)]. However, the data for tensile strength and modulus of bamboo fiber bundles can be found in several publications. Amada et al. [5] observed a tensile strength of 0.61 GPa and a tensile modulus of 46 GPa for bamboo fiber bundles, which were calculated based on the volume ratio of fibers to parenchymal cells and the macroscopic tensile modulus and strength of bamboo. Recently, Shao et al. [6] experimentally found the tensile strength and modulus of fiber bundles of Moso bamboo to be 0.482 and 33.9 GPa, respectively. Accordingly, tensile modulus measured on single bamboo fibers is comparable to that of fiber bundles, whereas the tensile strength is much higher than the latter. This is reasonable, as the de-bonding between fibers during tension will significantly reduce the loading capacity of bamboo fiber bundles.
As a direct comparison, Fig. 5 shows the histogram of tensile modulus, ultimate strength, and elongation at break of mature latewood tracheid fibers from Chinese Fir [Cunninghamia lanceolata (Lamb.Hook.)] and Masson Pine [Pinus massoniana (Lamb.)]. Insignificant differences were found between the two types of fibers in tensile modulus, ultimate strength, and elongation at break. Their average values were 17.9 GPa for tensile modulus, 0.79 GPa for tensile strength, and 5.16 % for elongation at break. Several commercially important wood species have been tested for their fiber mechanical properties. A large variability was found, dependent on the testing protocol adopted, the type of fibers investigated (earlywood or latewood fibers), the MFA, and, or, the juvenility [10, 21, 22]. Groom et al. [9, 23] and Mott et al. [24] have conducted more statistically reliable and precise measurements for Loblolly pine fibers. The average elastic modulus and ultimate tensile strength of all the Loblolly pine fibers, distributed in equal proportion to earlywood and latewood, was 17.3 and 0.824 GPa, respectively. As a whole, our test results of wood fibers agree well with the available published data.
Therefore, bamboo fibers are far superior to wood fibers in terms of mechanical performance. In our direct comparison, the tensile strength and modulus of bamboo fibers are nearly two times that of single Chinese Fir and Masson Pine fibers. It is widely accepted that larger MFA values tend to weaken the mechanical performance of plant fibers. The MFA of mature Chinese Fir and Masson Pine fibers tested here are about 12°, while bamboo fibers normally have an average MFA of less than 10° with small variability (Fig. 6). Yu et al. [20] showed that the average MFA of Moso bamboo fibers was about 9° and exhibited little variation with respect to the locations in the culm. However, the difference in MFA seems to be incapable of fully explaining the large difference in mechanical performance between bamboo and wood fibers. The cell wall microstructural differences between them must also be considered. Figure 7 shows the distribution and size of pits in Ma bamboo fibers, Chinese Fir fibers, and Masson Pine fibers. It can be observed that both the amount and size of pits in Ma bamboo fibers are much smaller than those of the two wood fibers, which means the negative effect of pits on mechanical performances of bamboo fibers is much smaller than that on wood fibers. Furthermore, the extremely large ratio of cell wall to cavity of bamboo fibers improves their tolerance to failures compared to wood fibers. It was astonishing to find that the average elongation at break of 11 types of bamboo fibers is comparable to that of mature Chinese Fir and Massion Pine softwood fibers, especially when one takes into account that the former is much stronger and stiffer than the latter. This might be mainly due to the nearly solid cell wall of bamboo fibers, which reduced the possibility of pre-failure during tension compared to wood fibers featured with thin cell wall. Additionally, the layered structure of regular alteration of broad and narrow lamellae of bamboo fiber might also improve the extensibility of bamboo fibers. The thin lamellae was characterized with high MFA (80°–90°) and low hemicelluloses content, while the cellulose microfibrils in the broad lamellae was almost parallel to the fiber axis [25, 26]. As a result, the interface between the broad and narrow lamellae should be rather weak, which might be in favor of the slipping between the broad and thin lamellae during tension. However, this inner slipping might have a negative effect on the tensile modulus of bamboo fibers.
The effect of MFA on the mechanical properties of single bamboo fibers
Many wood properties are to a large extent dependent on MFA and the relationships among them have been extensively investigated during the past decades [27]. The tensile stiffness and strength of wood cell walls in the axial direction are negatively affected by MFA, while the elongation at break is positively correlated. This has been demonstrated in studies on tissues [28, 29] and on individual wood fibers [9, 10, 23, 30]. However, bamboo shows much less variation for MFA compared with wood. For example, Yu et al. [20] found that the MFA of Moso bamboo fibers only varied from 8° to 10° even when fibers were taken from different locations along culm walls with different ages. In this paper, we further demonstrated that the MFA variation in species is small, ranging from about 7.5° for B. longispiculata Gamble ex Brandis to 10.6° for B. pervariabilis McClure (Fig. 6). For each bamboo species, the variability in MFA is also very small with a coefficient of variability ranging from 1.63 to 8.24 %. In order to give a deeper insight into how the MFA affects the tensile mechanical properties of bamboo fibers, the correlations among tensile modulus, strength, elongation at break, and MFA for all the 11 bamboo species are plotted in Fig. 8. A clear and stable decreasing trend with rising MFA from 7.5° to 10.6° was observed for tensile modulus. For tensile strength, although the fibers with a MFA of about 7.5° showed the highest value of 1.93 GPa, no stable trend existed for the fibers with MFA from 8.5° to 10.6°. The fibers with a MFA of 10.6° showed the best extensibility of 6.48 % at elongation at break, but similarly no stable trend was found for the other MFA values. This is reasonable since the latter two indicators are closely related to fracture process of the fibers except for MFA.
The geometrical characteristics of bamboo fibers
The reinforcing effect of fibers not only depends on their mechanical performances, but also on their geometrical characteristics. Figure 9 shows the fiber length, diameter, and aspect ratio of the eleven types of bamboo fibers. The average length and diameter range from 1.54 to 2.73 mm and 12.41 to 15.63 μm, respectively, depending on the bamboo species measured. As a whole, bamboo fibers are much thinner than wood fibers but shorter than softwood fiber. Aspect ratio of fiber is a very important indicator in terms of composite application, as higher aspect ratio results in more efficient stress transfer from the matrix to the fiber. In a previous investigation, Stark and Rowlands [31] found the addition of wood fiber to Polypropylene (PP). Significantly improved the strength of composites compared with that of wood flour. Therefore, higher aspect ratio of wood fibers resulted in a stronger composite. In general, bamboo fibers have notably higher aspect ratios compared to wood fibers. In the present paper, the largest aspect ratio is about 196 for the fibers from C [Neosinocalamus affinis (Rendle) Keng f.] while the smallest one is about 120 for H (Bambusa albo-lingata Chia). The average aspect ratio of all the 11 types of bamboo fibers is 152. In comparison, wood fiber has a smaller aspect ratio of about 100 for softwood and just 60 for hardwood fibers [32].
Conclusions
The mechanical and morphological properties of eleven types of bamboo fibers and two types of wood fibers were tested and compared. Bamboo fiber is much stronger and stiffer than wood fiber and comparable in extensibility due to its unique cell wall structure. Furthermore, bamboo fibers generally have much larger aspect ratios compared to wood fibers, which implies higher efficiency of stress transfer in polymer composites. Therefore, our results first demonstrate the excellent potential of bamboo fibers for use as the reinforcing phase of natural fiber polymer composites with structural applications.
References
Amada S, Untao S (2001) Fracture properties of bamboo. Compos B 32:451–459
Lo TY, Cui HZ, Leung HC (2004) The effect of fiber density on strength capacity of bamboo. Mater Lett 58:2595–2598
Liu DG, Song JW, Anderson DP, Chang PR, Hua Y (2012) Bamboo fiber and its reinforced composites: structure and properties. Cellulose 19(5):1449–1480
Khalil HPSA, Bhat AH, Yusra AFI (2012) Green composites from sustainable cellulose nanofibrils: a review. Carbohydr Polym 87(2):963–979
Amada S, Ichikawa Y, Munekata T, Nagase Y, Shimizu H (1997) Fiber texture and mechanical graded structure of bamboo. Compos B 28:13–20
Shao ZP, Fang CH, Huang SX, Tian GL (2010) Tensile properties of Moso bamboo (Phyllostachys pubescens) and its components with respect to its fiber-reinforced composite structure. Wood Sci Technol 44(4):655–666
Jayne BA (1959) Mechanical properties of wood fibers. Tappi 42:461–467
Page DH, El-Hosseiny F (1983) The mechanical properties of single wood pulp fibres. Part VI. Fibril angle and the shape of the stress-strain curve. J Pulp Pap Sci 9:1–2
Groom LH, Mott L, Shaler SM (2002) Mechanical properties of individual southern pine fibers. Part I: determination and variability of stress-strain curves with respect to tree height and juvenility. Wood Fiber Sci 34:14–27
Burgert I, Keckes J, Fruhmann K, Fratzl P, Tschegg SE (2002) A comparison of two techniques for wood fiber isolation-evaluation by tensile tests on single fibers with different microfibril angle. Plant Biol 4:9–12
Burgert I, Frühmann K, Keckes J, Fratzl P, Stanzl-Tschegg SE (2003) Microtensile testing of wood fibers combined with video extensometry for efficient strain detection. Holzforschung 57:661–664
Sedighi-Gilani M, Navi P (2007) Experimental observations and micromechanical modeling of successive-damaging phenomenon in wood cells’ tensile behavior. Wood Sci Technol 41:69–85
Yu Y, Jiang ZH, Fei BH, Wang G, Wang HK (2011) An improved microtensile technique for mechanical characterization of short plant fibers: a case study on bamboo fibers. J Mater Sci 46(3):739–746. doi:10.1007/s10853-010-4806-8
Yu Y, Tian GL, Wang HK, Fei BH, Wang G (2011) Mechanical characterization of single bamboo fibers with nanoindentation and microtensile technique. Holzforschung 65:113–119
Wang G, ShiSheldon Q, Yu Y (2011) Tensile properties of four types of individual cellulosic fibers. Wood Fiber Sci 43(4):353–364
Wang G, Yu Y, ShiSheldon Q (2011) Microtension test method for measuring tensile properties of individual cellulosic fibers. Wood Fiber Sci 43(3):251–261
Chen H, Wang G, Cheng HT (2011) Properties of single bamboo fibers isolated by different chemical methods. Wood Fiber Sci 43(2):1–10
Huang YH, Fei BH, Yu Y, Zhao RJ (2012) Plant age effect on mechanical properties of MOSO bamboo (Phyllostachys heterocycla var. Pubescens) single fibers. Wood Fiber Sci 44(2):196–201
Cave ID (1966) Theory of X-ray measurement of microfibril angle in wood. For Prod J 16:37–42
Yu Y, Wang G, Qin DC, Zhang B (2007) Variation in microfibril angle of Moso Bamboo by X-ray diffraction (in Chinese). J North East For Univ 35:28–30
Jayne BA (1960) Some mechanical properties of wood fibers in tension. For Prod J 10:316–322
Hardacker KW (1963) The automatic recording of the load-elongation characteristics of single papermaking fibers. Tappi 45:237–246
Groom LH, Shaler S, Mott L (2002) Mechanical properties of individual southern pine fibers. Part III. Global relationships between fiber properties and fiber location within an individual tree. Wood Fiber Sci 34:238–250
Mott L, Groom L, Shaler S (2002) Mechanical properties of individual southern pine fibers. Part II. Comparison of earlywood and latewood fibers with respect to tree height and juvenility. Wood Fiber Sci 34:221–237
Parameswaran N, Liese W (1976) On the fine structure of bamboo fibres. Wood Sci Technol 10:231–246
Gritsch CS, Kleist G, Murphy RJ (2004) Developmental changes in cell wall structure of phloem fibres of the bamboo Dendrocalamus asper. Ann Bot 94:497–505
Butterfield BG (ed) (1998) Microfibril angles in wood. University of Canterbury, Christchurch
Cave ID (1969) The longitudinal Young’s modulus of Pinus radiata. Wood Sci Technol 3(1):40–48
Reiterer A, Lichtenegger H, Tschegg S, Fratzl P (1999) Experimental evidence for a mechanical function of the cellulose microfibril angle in wood cell walls. Philos Mag A 79:2173–2184
Page DH, El-Hosseiny F, Winkler K (1971) Behavior of single wood fibers under axial tensile strain. Nature 229:252–253
Stark NM, Rowlands RE (2003) Effects of wood fibre characteristics on mechanical properties of wood/polypropylene composites. Wood Fibre Sci 35:167–174
Khiari R, Mhenni MF, Belgacem MN, Mauret E (2010) Chemical composition and pulping of date palm rachis and Posidonia oceanic—a comparison with other wood and non-wood fibre sources. Bioresour Technol 101(2):775–780
Acknowledgements
We would like to thank National Natural and Science Foundation of China (31070491) for financial support of the research.
Author information
Authors and Affiliations
Corresponding author
Rights and permissions
About this article
Cite this article
Yu, Y., Wang, H., Lu, F. et al. Bamboo fibers for composite applications: a mechanical and morphological investigation. J Mater Sci 49, 2559–2566 (2014). https://doi.org/10.1007/s10853-013-7951-z
Received:
Accepted:
Published:
Issue Date:
DOI: https://doi.org/10.1007/s10853-013-7951-z