Abstract
Although silicon is the preferred choice for microelectromechanical systems (MEMS) piezoresistive pressure sensors, such devices are not preferred for application in harsh environmental conditions due to the exponential increase in leakage current with temperature. To alleviate such shortcomings of silicon-based pressure sensors in extreme conditions including elevated temperature and intense vibration, this study strives to shift focus from core complementary metal–oxide–semiconductor (CMOS) materials to silicon carbide. In this work, we adopt an analytical and simulation approach to model and analyze various characteristics of such silicon carbide piezoresistive sensors and determine an optimal design. A square diaphragm is modeled using the analytical expressions for a thin plate in combination with small-deflection theory, providing quick insight for estimation of critical parameters and thus the behavior of the pressure sensor. Both clamped and freely supported edge conditions of the diaphragm are explored. Although many studies and discussions are available on the rigidly supported loading condition, the freely supported edge condition for a square diaphragm has received little attention. The deflection, stress, strain, and sensitivity of the square diaphragm under both loading conditions are reported herein then compared to understand which of the two loading conditions results in more significant outputs.
Similar content being viewed by others
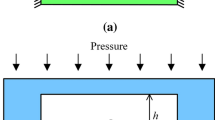
Avoid common mistakes on your manuscript.
1 Introduction
Microelectromechanical systems (MEMS) rely on the integration or combination of microelectrical and mechanical components that can sense and function to generate effects [2]. Due to its exceptional mechanical properties, silicon is often used to micromachine different micromechanical components such as cantilevers, beams, and diaphragms. Silicon is also the core CMOS material used in fabrication of integrated circuits (ICs) and their integration to obtain high-performance MEMS devices. MEMS pressure sensors work on the principle of micromechanical deformation of a thin diaphragm due to an externally applied pressure [6, 8]. Such deformation is too small to be measured directly [5], hence a transduction mechanism is used to convert the mechanical deformation into a measurable electrical signal [13]. Piezoresistive transduction is a favored mechanism for MEMS manufacturers, due to its considerable advantages [16], including simple fabrication and low cost. In comparison with capacitive pressure sensors, piezoresistive pressure sensors show good linearity over wide pressure ranges [3]. Depending on the application environment, either piezoresistive or capacitive pressure sensors may be preferred [10]. In cases where linearity, reliability, size, and cost are significant factors, a piezoresistive pressure sensor is the most favorable choice. The amount of deflection can then be found by solving the differential equations of plate theory with appropriate boundary conditions. The pressure sensor can be modeled using the analytical expressions for thin plates in combination with small-deflection theory [4, 20].
Small-deflection theory assumes that the deflection at the midpoint of the surface of a diaphragm is much less than its thickness [9, 23]. MEMS devices find applications in aerospace due to their light weight, small size, and low power consumption. Such applications require pressure sensors to work reliably in extreme conditions including elevated temperature and intense vibration [17]. Silicon carbide pressure sensors have drawn attention for use at elevated temperature, where conventional silicon pressure sensors fail to perform [11, 22]. In the work presented herein, a square diaphragm is used, as it exhibits greater sensitivity compared with a circular diaphragm of the same thickness. It is also noteworthy that square diaphragms can be fabricated easily using straightforward fabrication processes based on wet etching [7, 9, 12]. Furthermore, the increased aspect ratio, resulting in reduced differential stress and subsequently lower sensitivity, makes the square diaphragm superior to other geometries [9, 12]. The behavior of a sensing element strongly depends on its boundary conditions [4], which may include rigidly clamped and freely supported structures. While freely supported structures may not be physically possible, they more closely match the behavior of poorly supported diaphragms compared with their rigidly clamped counterparts. Regardless of the difficulties in modeling a poorly supported diaphragm analytically, the freely supported edge condition can be used to accurately account for the behavior of poorly clamped diaphragms. The focus of this work is to reveal the potential of silicon carbide-based pressure sensors compared with conventional silicon pressure sensors for use in aerospace applications, where pressure sensors must operate in harsh environments. The proposed silicon carbide pressure sensor shows improved sensitivity compared with silicon-based alternatives. Therefore, despite the difficulties posed by use of silicon carbide material, such as low reactivity and extremely high melting point, such devices have great relevance for space missions.
The present section of this paper highlights the motivation for and underlying objectives of this study, including basic information regarding MEMS technology, the dominance of silicon material, and the potential of moving to silicon carbide for space applications. The second section delves into the operation of the pressure sensor and its piezoresistive mechanism. The third section illustrates and sheds light on the loading conditions of the diaphragm. The fourth section presents all the analytical expressions necessary to establish the deflection, stress, stain, and sensitivity of the device. Simulation of the performance parameters was carried out using MATLAB. The “Results” section provide a broad graphical illustration of all the relevant parameters. The final section provides the reader with a brief overview and summarizes the significant contributions of this work.
2 Principle of operation
Application of external pressure causes the midplane of the diaphragm to deflect, inducing stress in the diaphragm [21]. To measure the strain developed and the resulting geometric deformation due to the application of an external load, sensing resistors are placed on top of the diaphragm. Four resistors are arranged in a Wheatstone bridge circuit [1, 18]. The advantage of using four resistors instead of just one is to maximize the voltage sensitivity as well as to minimize the temperature dependence. With no external pressure, the Wheatstone bridge is balanced, resulting in zero output voltage. When pressure is applied, stress is induced in the diaphragm. Since the piezoresistors also lie on the surface, they too experience stress, causing their resistance to change from the nominal value [14, 19]. The unbalanced bridge therefore results in a pressure sensor output. The primary aim here is to obtain a linear and highly sensitive pressure sensor [15]. To obtain a linear relationship between the pressure applied and stress developed, conventional theories of solid mechanics were applied to determine the optimal position, orientation, and length of the sensing resistors. Since the desired response is linear, small-deflection theory was used. Small-deflection theory assumes that the maximum deflection is much less than the thickness of the diaphragm, to be precise, less than one-fifth of the diaphragm thickness [8] (Fig. 1).
3 Loading conditions
The loading or edge conditions of a diaphragm are simply its boundary conditions. The analytical modeling of the pressure sensor involves solving the plate equations using appropriate boundary conditions.
3.1 Freely supported edge loading condition
In this case, the diaphragm is not fixed, but is simply placed against a support (Fig. 2).
3.2 Rigidly clamped loading condition
In this case, the ends of the diaphragm are clamped to a fixed surface, as shown in Fig. 3.
4 Solution of the plate equation
4.1 Rigidly clamped square diaphragm
In this case, the pressure is exerted uniformly above the diaphragm, in the z-direction, normal to the plane of the plate. The main differential equation for a two-dimensional plate with applied uniform pressure P can be written as (Fig. 4)
The surface stresses on the diaphragm can then be calculated as
The boundary conditions for a square diaphragm with clamped edges can be given as
Although not accurate, several empirical solutions have been proposed for a square diaphragm.
The deflection of the plate can be given by
The boundary conditions may be satisfied by taking w in the form
Substitution of Eq. (7) into Eq. (1) yields
\( w_{0} = w_{\hbox{max} } \) is the maximum deflection of the plate, which occurs at \( x = y = 0 \).
From Eq. (8), one has
Hence, the deflection (w) of the diaphragm at a given point (x, y) is
Substitution of Eq. (7) into Eqs. (2) and (3) yields
The strain in the diaphragm is then given by
Substitution of Eq. (7) into Eqs. (13) and (14) and subsequently solving the partial differential equations yields
The Kirchhoff shear forces \( V_{x} \) and \( V_{y} \) are given by
Solving Eqs. (17) and (18) by substitution of Eq. (7) yields
4.2 Freely supported square diaphragm
The diaphragm is assumed to be a thin plate, freely supported at all edges. Analytical expressions can then be used to calculate the deflection, stress distribution, and strain developed due to a uniformly applied load. Consider a freely supported square plate, as shown in Fig. 5. The boundary conditions corresponding to the freely supported edge condition for the square diaphragm are as follows:
where
\( D = \frac{{Eh^{3} }}{{12\left( {1 - \upsilon^{2} } \right)}} \) is known as the flexural rigidity of the diaphragm, w is the diaphragm deflection at (x, y), E is the Young’s modulus of silicon carbide, h is the diaphragm thickness, and \( \upsilon \) is the Poisson’s ratio of silicon carbide.
Equations (1) and (2) can be rewritten according to the boundary conditions as
It is assumed that the plate is flat and that its thickness is small compared with the side length of the square. It is also ensured that the deflection is smaller than the thickness of the diaphragm.
The above set of boundary conditions can be satisfied by taking w in the form
where w0 is a constant chosen so as to satisfy the plate equation
Substitution of Eq. (22) into the plate equation(23) results in \( w_{0} = w_{\rm max} \), which is the maximum deflection occurring at the center of the plate at \( x = y = \frac{a}{2} \):
Hence, the deflection w of the diaphragm at any point (x, y) is obtained as
It is now necessary to determine the stress distribution on the surface of the diaphragm, as it determines the location of the piezoresistors on the diaphragm. To obtain higher voltage output and thus greater sensitivity, the piezoresistors must be placed where the stresses are maximum. The expression for w obtained above can be used to calculate the surface stress in the diaphragm using the following equations:
where \( \sigma_{x} ,\sigma_{y} \) are the x, y-directed surface stresses, respectively. Stress results in the diaphragm due to the applied load. Since the piezoresistors are placed on the top of the diaphragm, the piezoresistors also experience this stress.
Solution of Eqs. (20) and (21) yields the moments at any point (x, y) on the freely supported square diaphragm as
The Kirchhoff shear forces \( V_{x} \) and \( V_{y} \) are given by
Solution of Eqs. (30) and (31) yields the Kirchhoff shear forces at any point (x, y) on the freely supported square diaphragm as
The bending strain is given by small-deflection theory as
Substitution of Eq. (25) into Eqs. (34) and (35) and solving the differential equations yields the bending strains as
4.3 General Wheatstone bridge circuit
Figure 6 shows a sensor resistor \( R_{1} \), which is a piezoresistor placed on the freely supported square diaphragm. When pressure is applied to the diaphragm, the resistance of this sensor resistor changes. The variable resistor \( R_{2} \) aids in nullifying any offset voltage that might arise due to residual stresses. Further, the fixed resistor \( R_{3} \) serves to balance the bridge, while R4 is a reference resistor, identical in dimensions and nominal resistance to the sensor resistor \( R_{1} \). The advantage of using four resistors instead of just one is to maximize the voltage sensitivity as well as minimize the temperature dependence.
When no pressure is applied, the output of the Wheatstone bridge circuit shown in Fig. 6 can be expressed as
When all the resistances are equal to R at the initial stage,
Unlike the rigidly clamped loading condition, where stresses are maximum at the center of the edges, the stress in a freely supported diaphragm is maximum at the center and decreases towards the edges. Therefore, for greater sensitivity, the piezoresistors must lie within this high-stress region.
4.4 Voltage output of the pressure sensor
Initially, when no load is applied, the diaphragm is unstressed and all resistors have equal resistance, so the balanced bridge gives zero output voltage. Each of the four resistors experience two stresses, viz. lateral stress, \( \sigma_{\text{l}} \) and transverse stress, \( \sigma_{\text{t}} \).
When stresses are experienced, the relative resistance change is given by
where \( \pi_{\text{l}} ,\pi_{\text{t}} \) are the longitudinal and transverse piezoresistive coefficients of silicon carbide, and \( \alpha_{1} ,\alpha_{2} \) are the relative changes in resistance.
The output voltage of the sensor can then be written as
p-type piezoresistors have higher piezoresistive coefficients compared with n-type piezoresistors. As the output voltage is directly proportional to the piezoresistive coefficient, P-type piezoresistors are preferred.
The output voltage of the pressure sensor is given as
5 Results and discussion
Results were simulated using MATLAB Simulink software. The output graphs for the deflection, stress, and strain are shown, using the simulation parameters presented in Table 1.
5.1 Rigidly clamped diaphragm
The deflection of the diaphragm from its mean position with respect to the length of the diaphragm is shown in Fig. 7. We observe that the deflection of the square diaphragm is maximum at the center. Since the square plate is perfectly clamped around its edges, the displacement drops as one moves away from the center. Thinner membranes show larger deflection, greater strains, and therefore higher sensitivity. However, thinner membranes cause an increase in nonlinearity. Thus, to strike a balance between sensitivity and linearity, a not too thin diaphragm of 50 μm was used, fulfilling the need for an accurate pressure sensor while preventing the nonlinearity from exceeding a certain range.
The x-component of the stress versus the distance from the center of the diaphragm along the x-axis is plotted in Fig. 8. The stress distribution was determined by keeping the y coordinate fixed and moving along the x-axis on either side of the center. The piezoresistors must be placed in high-stress regions so as to obtain the maximum sensitivity. The location of the piezoresistors was determined from the stress distribution on the diaphragm. This graph shows that the stress in the diaphragm is maximum at the edges and minimum at the center. This is why the piezoresistors were placed at the midpoint of the edges of the square diaphragm to measure the induced stress and to provide a relevant output in terms of voltage.
The output voltage is plotted versus the applied pressure in Fig. 9. The sensitivity of a pressure sensor is defined as the relative change in the output voltage per unit applied pressure, providing a measure of its ability to convert an applied pressure into an electrically measurable output voltage. The sensitivity of the square diaphragm is proportional to the differential stress \( (\sigma_{y} - \sigma_{x} ) \) as stated in Eq. (42), making it an important indicator of the output voltage of the sensor. The surface stresses in a square and circular diaphragms are \( \sigma_{{{\text{square}}(\hbox{max} )}} = 1.64\sigma_{{{\text{circular}}(\hbox{max} )}} \) [8]. Due to the higher surface stresses, the square diaphragm is found to show higher sensitivity compared with several other geometries used for sensor diaphragms. The sensitivity can be calculated from this graph using Eq. (43). Figure 9 shows the sensitivity of the clamped square diaphragm to be 78.12 mV/V/psi.
5.2 Freely supported edge diaphragm
The deflection of the square freely supported diaphragm can be found from Eq. (10). Figure 10 shows the displacement of the diaphragm under a uniform pressure of 100 psi. It is seen that the deflection is maximum at the center and decreases towards the edges. Compared with the rigidly supported case, the freely supported diaphragm is seen to show higher deflections for a similar applied pressure range, reaching 4.5 × 10−7 m at the center. The deflection at each point of the diaphragm was found for the full-scale pressure of 100 psi. It is noteworthy that the full-scale pressure is much lower than the burst pressure of the silicon carbide material, preventing any rupture or breakage of the diaphragm.
Figure 11 shows the x-component of the stress distribution along the cut line. It can be inferred that the stresses are maximum at the center of the freely supported diaphragm and decrease towards the edges, unlike the clamped edge condition where the stress is maximum at the edges and minimum at the center of the diaphragm. To obtain the maximum output voltage, the piezoresistors must be located within the high-stress region [24]. On the other hand, the stresses are maximum at the midpoint of the edges for the rigidly supported case. It can be seen that resistors on a freely supported diaphragm experience higher stresses, which will result in greater sensitivity. The stress distribution was calculated from Eqs. (26) and (27).
Figure 12 shows the strain distribution in a square diaphragm (1400 μm in length, 50 μm in thickness) under uniform pressure of 100 psi. It can be concluded that the strain is higher at the center of the diaphragm than at other positions.
6 Conclusions
This study determines performance parameters such as the deflection, stress, strain, and sensitivity for rigidly clamped and freely supported edge conditions. For each of the specified performance parameters, a comparison is made between the two loading conditions. All the analytical steps for the calculation of the results for the freely supported and rigidly clamped silicon carbide diaphragm are provided. Furthermore, this work aims to motivate a shift to silicon carbide pressure sensors for use in aerospace applications. Also, the square diaphragm was seen to provide superior performance compared with other available geometries. The sensitivity for the rigidly clamped square diaphragm was found to be near 78.12 mV/V/psi, greater than for a circular diaphragm having the same dimensions. Both the rigidly clamped and freely supported edge conditions were explored. The analytical solutions provided for various sensor characteristics, such as the deflection, stress distribution, stain, and sensitivity, will be useful for formulation of square diaphragm piezoresistive pressure sensors with an optimal design.
References
Bae, B., et al.: Design optimization of a piezoresistive pressure sensor considering the output signal-to-noise ratio. J. Micromech. Microeng. 14, 1597–1607 (2004)
Bao, M.: Analysis and Design Principles of MEMS Devices. Elsevier, Amsterdam (2005)
Beeby, S.P., Stuttle, M., White, N.M.: Design and fabrication of low cost microengineered silicon pressure sensor with linearized output. IEEE Proc. Sci. Meas. Technol. 147(3), 127–130 (2000)
Jindal, S.K., Raghuwanshi, S.K.: A complete analytical model for circular diaphragm pressure sensor with clamped edge. J. Circuit Syst. 1(2), 19–27 (2013)
Jindal, S.K., Raghuwanshi, S.K.: A complete analytical model for circular diaphragm pressure sensor with freely supported edge. Microsyst. Technol. 21(5), 1073–1079 (2015)
Jindal, S.K., Mahajan, A., Raghuwanshi, S.K.: A complete analytical model for clamped edge circular diaphragm non-touch and touch mode capacitive pressure sensor. Microsyst. Technol. 22(5), 1143–1150 (2015)
Kumar, S.S., Pant, B.D.: Design of piezoresistive MEMS absolute pressure sensor. In: Proceedings of the SPIE 8549 Kumar SS, Pant BD (2013) Effect of Temperature on Etch Rate and Undercutting of (100) Silicon Using 25% TMAH. In: Proceedings of the International Conference on Emerging Technologies Micro to Nano (ETMN), Goa (2012)
Kumar, S.S., Pant, B.D.: Design principles and considerations for the ‘ideal’ silicon piezoresistive pressure sensor: a focused review. Microsyst. Technol. 20, 1213–1247 (2014)
Kumar, S.S., Pant, B.D.: Polysilicon thin film piezoresistive pressure microsensor: design, fabrication and characterization. Microsyst. Technol. (2014). https://doi.org/10.1007/s00542-014-2318-1
Kumar, S.S., Ojha, A.K., Nambisan, R., Sharma, A.K., Pant, B.D.: Design and simulation of MEMS silicon piezoresistive pressure sensor for barometric applications. In: Proceedings of the ARTCom&ARTEE PEIE&itSIP and PCIE, pp 339–345. Elsevier (2013). ISBN978-81-910691-8-3
Kumar, S.S., Ojha, A.K., Pant, B.D.: Experimental evaluation of sensitivity and non-linearity in polysilicon piezoresistive pressure sensors with different diaphragm sizes. Microsyst. Technol. (2014). https://doi.org/10.1007/s00542-014-2369-3
Khakpour, R. et al.: Analytical comparison for square, rectangular and circular diaphragms in MEMS applications. In: International Conference on Electronic Devices. Systems and Applications, pp. 297–299 (2010)
Li, S., Zhang, Z., Tang, J., Ding, D.: A novel signal conditioning circuit for piezoresistive pressure sensor. Unifying Electr. Eng. Electron. Eng. 238, 1707–1713 (2014). https://doi.org/10.1007/978-1-4614-4981-2_187
Li, C., Cordovilla, F., Jagdheesh, R., Ocaña, J.L.: Design and optimization of a novel structural MEMS piezoresistive pressure sensor. Microsyst. Technol. (2016). https://doi.org/10.1007/s00542-016-3187-6
Lin, L., Chu, H.-C., Lu, Y.-W.: A simulation program for the sensitivity and linearity of piezoresistive pressure sensors. J. Microelectromech. Syst. 8, 514–522 (1999). https://doi.org/10.1109/84.809067
Santosh Kumar, S., Pant, B.D.: Polysilicon thin film piezoresistive pressure microsensor: design, fabrication and characterisation. Microsyst. Technol. 21, 1949–1958 (2015)
Sharma, A., Mukhiya, R., Kumar, S.S., Pant, B.D.: Design and simulation of bulk micromachined accelerometer for avionics application. VLSI Des. Test 382, 94–99 (2013). https://doi.org/10.1007/978-3-642-42024-5_12
Song, J.W., Lee, J.-S., An, J.-E., Park, C.G.: Design of a MEMS piezoresistive differential pressure sensor with small thermal hysteresis for air data modules. Rev. Sci. Instrum. 86, 65003 (2015). https://doi.org/10.1063/1.4921862
Smith, C.S.: Piezoresistive effect in germanium and silicon. Phys. Rev. 94, 42–49 (1954)
Timoshenko, S.P., Woinowsky-Kreiger, S.: Theory of Plates and Shells, 2nd edn. McGraw Hill, New York (1959)
Wang, X., Li, B., Lee, S., Sun, Y., Roman, H.T., Chin, K., Farmer, K.R.: A new method to design pressure sensor diaphragm. NSTI Nanotechnol. 1, 324–327 (2004)
Werner, M., Gluche, P., Adamschik, M., Kohn, E., Fecht, H.J.: Review of diamond based piezoresistive sensors. Proc. IEEE Int. Symp. Ind. Electron. 1, 147–152 (1998)
Zhang, Y., Wise, K.D.: Performance of non-planar silicon diaphragms under large deflections. J. Microelectromech. Syst. 3, 59–68 (1994)
Zhang, Y.-H., Yang, C., Zhang, Z.-H., Lin, Z.H.-W., Liu, L.-T., Ren, T.-L.: A novel pressure microsensor with 30-μm-thick diaphragm and meander-shaped piezoresistors partially distributed on high-stress bulk silicon region. IEEE Sens. J. 7, 1742–1748 (2007)
Author information
Authors and Affiliations
Corresponding author
Rights and permissions
About this article
Cite this article
Jindal, S.K., Magam, S.P. & Shaklya, M. Analytical modeling and simulation of MEMS piezoresistive pressure sensors with a square silicon carbide diaphragm as the primary sensing element under different loading conditions. J Comput Electron 17, 1780–1789 (2018). https://doi.org/10.1007/s10825-018-1223-8
Published:
Issue Date:
DOI: https://doi.org/10.1007/s10825-018-1223-8