Abstract
Alumina modified by MgO as the catalyst support loading Co3O4 for the N2O decomposition were investigated. It was found that MgAl2O4 was formed over the alumina surface by the MgO reacting with Al2O3 after calcination at 900 °C and using the composited support containing 30 wt% MgO loading Co3O4 can effectively suppress undesired CoAl2O4 formation under 700 °C. In the 20Co/30Mg–Al catalyst, it was found that about half of the cobalt is present as (Co,Mg)O solid solution and the rest exists as Co3O4, as characterized by Raman spectroscopy and H2-TPR. The catalyst exhibited much higher and stable activity for the N2O decomposition compared with the 20Co/Al without MgO modification.
Graphical Abstract

Similar content being viewed by others
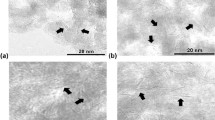
Explore related subjects
Discover the latest articles, news and stories from top researchers in related subjects.Avoid common mistakes on your manuscript.
1 Introduction
Nitrous oxide (N2O) is the third most significant anthropogenic greenhouse gas and the largest stratospheric-ozone-depleting substance [1, 2]. Nitric and adipic acids plants are the primary industrial contributors emitting this pollutant gas [3]. Several after-treatment technologies to control of N2O emission was developed, in which catalytic decomposition of the N2O is most promising, due to its simplicity, high efficiency, and low energy requirements [1, 2].
To eliminate the N2O emitted from nitric acid plants in this approach, a large number of catalysts have been investigated, such as simple and mixed oxides [4,5,6,7], spinels [8,9,10], perovskites [11, 12], zeolites [13, 14] as well as supported oxides [15,16,17,18,19]. In recent years, spinel-type oxides with the chemical formula AB2O4 (where A = Mg, Ca, Mn, Co, Ni, Cu, Cr, Fe, Zn and B = Cr, Fe, Co) as the N2O decomposition catalyst have attracted increasing interest, due to their adequate thermal stability and catalytic activity [20]. Among the spinel-type oxides, cobalt spinels are the most promising generic materials for catalyzing the reaction [8]. Russo et al. [20] found that the spinels, MgCo2O4, ZnCo2O4 and Co3O4, with Co at the B sites exhibit high catalytic activity. Stelmachowski et al. [21] explored the impact arisen from the replacement of both the Co2+ cation at the tetrahedral A site and the Co3+ cations at the octahedral B sites in Co3O4 by non-redox Mg2+ and Al3+ cations by means of experimental and theoretical studies, further proposed that the N2O decomposition is primarily catalyzed by the octahedral Co3+ ions, whereas the tetrahedral Co2+ ion is essentially less active to the reaction.
Despite the high catalytic activity, the Co3O4 in the bulk form is limited for practical applications due to its insufficient mechanical stability and high cost. These drawbacks may be overcome by the dispersion of the spinel over a cheap and mechanically robust carrier. In this regard, there are several investigations in literature concerning the dispersion of the cobalt spinel on alumina [15], zirconia [16], ceria [17] or even on metallic monoliths [19].
Although alumina was widely known to be one of the industrial catalysts supports due to its easy availability, large surface, advantageous mechanical properties, facile processing and shaping [22], its strong interaction with the cobalt oxides is much undesirable. As the interaction at high temperature leads to Co ions occupying the inactive A sites i.e. results in the formation of CoAl2O4 [23] that is less active for the N2O decomposition, how to maintain the active state of Co3O4 on the alumina support become a challenging topic. Jongsomjit et al. found that co-impregnation of ruthenium and cobalt on Al2O3 could inhibit the interaction of cobalt oxide with alumina [24], and zirconia is more effective for blocking the cobalt aluminate formation [25]. Based on the studies with and without BaO in the CoOx/Al2O3–BaO catalysts, Liotta et al. reported that BaO has the function of stabilizing the γ-Al2O3 phase and suppressing solid state diffusion of Co2+ ions into alumina bulk phase [26, 27]. Grzybek et al. have found that Co(NO3)2 precursor is more favorable than CoCl2 for the cobalt maintaining the active state, Co3O4, when supported on alumina and calcined at 600 °C [28]. They have also found that for the cobalt oxide, using α-Al2O3 as support is beneficial to maintain its active state, though the alumina in other phases (γ-, δ- and θ-Al2O3) give rise to high dispersion of the cobalt [22]. However, in the case of α-Al2O3 loading cobalt oxide, the catalyst surface is greatly sacrificed.
The problem that the strong interaction between active species and the support made the activity of the catalyst largely decrease is also exist in the case of alumina loading other transitional oxides. For instance, the NiO/γ-Al2O3 catalyst used for methane combustion is suffered from the inactive NiAl2O4 formation. Gayán found that when γ-Al2O3 support was coated with MgO and calcined at 800 °C, a stable MgAl2O4 spinel layer can be produced on the support surface. Using the composited support loading NiO, can effectively minimize the interaction of NiO with the support [29]. In light of this report, we suppose that the MgAl2O4 spinel layer on Al2O3 support would be able to protect the active Co3O4 from the strong interaction with support. Hence, this paper investigates the physical and chemical structure as well as the catalytic activity of the Co/Mg–Al catalyst for N2O decomposition, so as to develop a possible industrial meaning catalyst working at higher temperature.
2 Experimental
2.1 Catalyst Preparation
Al(OH)3 was prepared by adding NH3·H2O to Al(NO3)3·9H2O aqueous solution under drastic stirring, washing the precipitate with distilled water and drying the gel at 110 °C overnight. Based on the Al(OH)3, the following different materials that were used as supports for loading cobalt oxide were respectively obtained. Alumina was obtained by calcining the Al(OH)3 in air at 900 °C for 3 h. The bimetal oxide xMgO–Al2O3, which is denoted as xMg–Al with MgO weight percent x%, were prepared by adding NH3·H2O in dropwise into Al(OH)3 slurry that containing desired amount of Mg(NO3)2·6H2O under stirring at 30 °C until the pH of mother liquor reached about 11. The resulting material was then aged for 1 h, washed, dried, and calcined in the same way as that for obtaining the alumina. For a purpose of comparison, magnesium aluminate spinel (MgAl2O4) was prepared by adding NH3·H2O into an aqueous solution containing stoichiometric amount of Mg(NO3)2·6H2O and Al(NO3)3·9H2O, washing, drying and calcining the resulted material in the same way.
Co3O4/Al2O3, Co3O4/MgO–Al2O3 and Co3O4/MgO catalysts with desired Co3O4 weight percent (y%) were respectively prepared by impregnating Co(NO3)2·6H2O on the above mentioned alumina, xMgO–Al2O3 and a commercial MgO (purchased from Dunhuang chemical plant) at room temperature for 24 h, drying and calcining the resulted material respectively at 110 °C overnight and 700 °C for 3 h. The obtained catalysts were represented as yCo/Al, yCo/xMg–Al and yCo/Mg respectively. For instance, the 3Co/10Mg–Al denotes the catalyst prepared by loading 3 wt% Co3O4 on the 10 wt%MgO–Al2O3 support. For comparision, pure Co3O4 was prepared by precipitation method and calcined at 700 °C for 3 h, according to our previous work [8].
2.2 Catalyst Characterization
X-ray powder diffraction (XRD) of the catalysts was carried out on a Rigaku Smartlab 9 X-ray diffractometer with Cu Kα radiation (λ = 1.5406 Å) at 45 kV and 200 mA. The diffractograms were recorded with step of 0.02° and a speed of 8°/min. BET surface area of each sample was measured on Micromeritics ASAP 2020 through the nitrogen adsorption at − 196 °C. Before the measurement, the sample was degassed at 300 °C under vacuum for 10 h. Micro-Raman spectra of the samples were recorded at room temperature using a Thermo Fisher DXR Microscope Raman spectrometer with an excitation wavelength of 532 nm. Diffuse reflectance UV–vis spectra of the samples were recorded on a JASCO V-550 spectrophotometer using BaSO4 as a reference in ambient conditions. Temperature programmed reduction (H2-TPR) was performed on a ChemBET TPR/TPD Chemisorption Analyzer. 0.050 g sample (with the sieve fraction of 40–60 mesh) was pretreated in 30 vol% O2/Ar flow at 500 °C for 10 min and cooled to 100 °C. After that, the H2-TPR profiles were recorded in the 5 vol% H2/Ar flow of 100 mL/min at temperature ramp 10 °C/min.
2.3 N2O Decomposition Tests
N2O decomposition were conducted in a fixed-bed quartz flow reactor loading 0.200 g of catalyst (40–60 mesh). The catalyst was pretreated in Ar at 700 °C for 30 min and then the gas mixture composed of 2000 ppmv N2O, O2 (5 vol%, when present), H2O (2 vol. when present), NO (100 ppmv, when present) in Ar was fed into the reactor with a total flow rate of 50 mL/min. The gas composition was analyzed by gas chromatography equipped with porapak Q column (4 m in length and 3 mm in inner diameter) using TCD as detector. Steady-state activity data were recorded at each temperature descending from 700 to 450 °C or at a constant temperature (for measuring the catalyst durability). N2O conversion was calculated according to the equation
3 Results and Discussion
3.1 Alumina Modified with Different Amount of Magnesium Oxide
Figure 1 shows XRD patterns of the Al2O3, the bimetal oxide 10Mg–Al and 30Mg–Al calcined at 900 °C for 3 h. For the Al2O3, which give a small specific surface area of 18.06 m2/g, it exhibited sharp peaks due to α-Al2O3 and lower peaks arisen from θ-Al2O3. Whereas, in the case of 10Mg–Al, which gave a specific surface area of 50.79 m2/g, no peaks ascribed to α-Al2O3 could be observed. Instead, strong peaks due to MgAl2O4 phase (JCPDS 21-1152) appeared on the sample. Clearly, it is the MgAl2O4 formation which suppressed the phase transformation from θ- to α-Al2O3, though the atomic ratio of Mg/Al is about 0.14 that is much less than the stoichiometric ratio (0.5) of MgAl2O4. On the 30Mg–Al, the diffraction of MgAl2O4 became more intensive and besides which some diffraction peaks belong to MgO (JCPDS 43-1022) were appeared. It means that 30 wt% of MgO is enough to produce MgAl2O4 covering the Al2O3 surface.
3.2 Chemical State of Cobalt in the 3Co/xMg–Al Influenced by the Magnesium Oxide Amount
Figure 2 shows Raman spectra of 3Co/Al, 3Co/10Mg–Al and 3Co/30Mg–Al in comparison with that of Co3O4. On the Co3O4, five Raman peaks at 189, 467, 511, 609 and 672 cm−1 corresponding to the Eg, 3xF2g and A1g vibrational modes of the crystalline [30] appeared. On the 3Co/Al, although the first three peaks belong to the Co3O4 crystalline with a slight blue shift could be confirmed, a splitting band of A1g at about 690 cm−1 being associated with the Al3+ substituting octahedral Co3+ in the spinel structure [28] clearly appeared. It indicates that both of Co3O4 and CoAl2O4 exist in the 3Co/Al. Unexpectedly, the band splitting is more evident for the 3Co/10Mg–Al compared with that of the 3Co/Al, which indicates that the transformation of the Co3O4 to CoAl2O4 due to the calcination is even more severe for the 3Co/10Mg–Al compared with the 3Co/Al. The same conclusion could be obtained from optical diffuse reflectance spectra of the two samples. As shown in the Fig. 3, the characteristic triplet absorption at 1.97, 2.13 and 2.28 eV due to the spin-forbidden 4A2(F) → 2T1(G), 2E(G), spin-allowed 4A2(F) → 4T1(P), and spin-forbidden 4A2(F) → 2T2(G) transitions for the tetracoordinated Co2+ [31] is more remarkable for the 3Co/10Mg–Al compared with that of the 3Co/Al, indicating that there are more CoAl2O4 existing in the 3Co/10Mg–Al with respect to the 3Co/Al. The more θ-Al2O3 phase of the 10Mg–Al compared with the Al2O3 should be responsible for the undesired results. In the case of the Al2O3 loading Co3O4 after the calcination, as discussed in the Sect. 3.1, as the alumina primarily exists as α-Al2O3, it properly inhibited the transformation of the Co3O4 to CoAl2O4 [22]. Considering that although all of magnesium in the 10Mg–Al exist as MgAl2O4, it could not effectively protect the cobalt from transforming to the CoAl2O4, 30Mg–Al was investigated as the support to load cobalt oxide. As shown in the Fig. 2, no Raman bands belong to either CoAl2O4 or Co3O4 were observed on the 3Co/30Mg–Al, and instead, two broad absorption bands respectively appeared at about 398 cm−1 and 594 cm−1. The former band can be ascribed to that of MgAl2O4, because the MgAl2O4 gave the same band at 398 cm−1 (a, in Fig. 2). Furthermore, it is strongly supported by the literature [32]. For the band at about 594 cm−1, it can be ascribed to solid solution of (Co,Mg)O, which will be discussed in details below.
It has been reported that the solid solution (Co,Mg)O (JCPDS 02-1201) can be formed from solid-state reaction of cobalt oxide with magnesium oxide [33]. It was confirmed by the XRD of the MgO and 20Co/Mg samples, as shown in the Fig. 4. On the 20Co/Mg, the diffraction peaks arisen from MgO (or composite metal oxides) clearly shifted to lower angles compared with that of the pure MgO (refer to the insert). For instance, the strongest peak arising from the (2 0 0) reflection for the pure MgO at 42.90o shifted to 42.83o for the 20Co/Mg, corresponding to the Co2+ with larger radius (74 pm) replacing the Mg2+ with smaller radius (65 pm). Figure 5 shows the Raman spectra of the 3Co/Mg and 20Co/Mg samples. It can be seen that the broad band similar to that of the 3Co/30Mg–Al but centered at 579 cm−1 appeared on the both samples and that the intensity of the peak increased with the Co content increasing. These results clearly confirmed that the broad band at about 579 cm−1 is characteristic of the cobalt in the (Co,Mg)O phase. Hence, the broad band at about 594 cm−1 observed on the 3Co/30Mg–Al can be reasonably assigned to the cobalt in (Co,Mg)O solid solution.
The catalytic activities of the 3Co/xMg–Al (x = 0, 10, 20, 30) with the same cobalt loading amount (3 wt% Co3O4) are compared (Fig. 6). It generates the activity order 3Co/30Mg–Al > 3Co/20Mg–Al > 3Co/Al > 3Co/10Mg–Al. Clearly, the order can be interpreted well by the primary chemical state of cobalt in the catalysts. The small amount (10 wt%) of MgO addition to the Al2O3 support led to marked decrease of the activity, which is associated with the more inactive CoAl2O4 formation in the 3Co/10Mg–Al. Interestingly, 30 wt% of MgO addition to the Al2O3 support made the activity of the corresponding catalyst significantly increased. It is in line with the formation of (Co,Mg)O instead of that of CoAl2O4 in the catalyst, as discussed afore (in Raman spectroscopy). No further activity increasing was observed when the more MgO was used for modifying the Al2O3 support, which may be resulted from the large surface area losing of the corresponding catalysts. Herein, a recent report given by Klegová et al. [18] should be noticed, who compared 70%MgO/30%Al2O3 and 30%MgO/70%Al2O3 loading definite amount of Co3O4 (25.2 wt% accounted in Co), in which the Al2O3 was used as binder to benefit the support shaping, and found that the Co3O4/70%MgO/30%Al2O3 catalyst is more active than the counterpart for the N2O decomposition. Their results also significantly indicate that the cobalt on the MgO surface is more active than that on the Al2O3 surface.
3.3 Impact of the Magnesium Oxide on the Activity of the 20Co/30Mg–Al
Figure 7a shows the activity variation of the catalysts with the Co3O4 loading amount change on the 30Mg–Al. With the Co3O4 loading amount increase in the range of 3–20 wt%, the N2O conversion over the catalysts at each reaction temperature greatly increased. However, no significant increase in the N2O conversion could be observed when the Co3O4 loading amount was further increased to 30 wt%, which may be resulted from the surface area losing of the 30Co/30Mg–Al (42.75 m2/g) with respect to the 20Co/30Mg–Al (52.93 m2/g). Based on the results, specific reaction rates of the N2O decomposition over the yCo/30Mg–Al catalysts at 550 °C in unit amount of Co were calculated (Fig. 7b), from which it is can be known that the 20Co/30Mg–Al gives an outstanding large N2O decomposition specific reaction rate in the unit amount of Co among the catalysts with different Co3O4 loadings. It indicates that the cobalt component in the 20Co/30Mg–Al works in the highest effectiveness for catalyzing the reaction among the catalysts. From the Raman spectrum (Fig. 8), it can be known that part of cobalt exists as (Co,Mg)O solid solution, as discussed in the Sect. 3.2, and the rest exists as Co3O4 phase in the 20Co/30Mg–Al. Thus, for the yCo/30Mg–Al catalysts, the N2O decomposition specific reaction rates over them changed with the Co3O4 loading amount could be explained as follows. When the cobalt oxide loading amount increased in the yCo/30Mg–Al in the percent y = 3–10, the cobalt is primarily present in (Co,Mg)O solid solution, and the average depth of the cobalt location in the solid solution increases, which negatively influences the specific reaction rate. Whereas, when the Co3O4 loading amount further increased, for instance, from 10 wt% to 20 wt%, the Co3O4 species that is more active than the (Co,Mg)O for the reaction begins to be produced, which interprets why the 20Co/30Mg–Al gives the much higher specific reaction rate compared to the yCo/30Mg–Al with lower Co3O4 loading amounts. Based on the above discussion, the chemical structure of the 20Co/30Mg–Al can be schematically represented in Fig. 9.
Figure 10 shows H2-TPR profiles of the 20Co/30Mg–Al comparing with those of 20Co/Al and the bulk Co3O4 sample. Two hydrogen consumption peaks at 401 and 440 °C appeared on the bulk Co3O4 sample, which could be respectively ascribed to the reduction of Co3+ to Co2+ and Co2+ to Co0 [17]. However, on the 20Co/Al, the peaks markedly shifted to about 486 and 563 °C and the hydrogen consumption below 440 °C was almost negligible. It reveals that the cobalt in the 20Co/Al is predominantly present as CoAl2O4 [23], which is in agreement with that measured by Raman spectroscopy (Fig. 8). Interestingly, it can be found from the figure, that the primary hydrogen consumption peak over the 20Co/30Mg–Al appeared at 395 °C that is even lower than those on the bulk Co3O4 sample. The result indicates that the oxygen ions of the Co3O4 species in the 20Co/30Mg–Al are more active towards reduction, i.e. Co–O bond in the Co3O4 species is weaker in somewhat compared with that in the bulk Co3O4 sample. For the transitional based catalysts, it has been documented that their active sites regeneration concerning the Co–O bond rupture controls N2O decomposition over the catalysts [2]. Thus, the activity of the active sites must be reflected by temperature of the reduction peak in the H2-TPR. In Fig. 10, it can be also found that the area of the reduction peak for the 20Co/30Mg–Al below 470 °C is about half of the bulk Co3O4. The results indicate that the corresponding portion of the cobalt is present as Co3O4 species in the 20Co/30Mg–Al while the rest exists in the state that hardly reduced by H2, which is in good consistent with that measured by Raman spectroscopy (Fig. 8) and supports the chemical structure of the 20Co/30Mg–Al catalyst illustrated in Fig. 9.
As expected, the 20Co/30Mg–Al exhibited much higher activity at each reaction temperature compared with the 20Co/Al (Fig. 11). For instance, the 20Co/30Mg–Al at 550 °C gave the N2O conversion of 76% that is about 5 times as high as that of the 20Co/Al under the same reaction conditions.
3.4 Catalytic Performance of the 20Co/30Mg–Al
Figure 12 shows the N2O decomposition results of 2000 ppmv N2O in the presence of some impurities over the 20Co/30Mg–Al catalyst. For the 2000 ppmv N2O in Ar, the N2O was completely decomposed at 600 °C. 100 ppmv NO and 5% O2 existing in the gas stream just made the temperature for the complete N2O decomposition over the catalyst shifted from 600 to 650 °C. In the figure, it can be found that, the impurity gas giving the largest impact on the catalytic activity among the 100 ppmv NO, 5 vol% O2 and 2 vol% H2O is the 2 vol% H2O. Nevertheless, the 20Co/30Mg–Al catalyst still completely eliminated the N2O at 700 °C under the most severe condition of the three impurity gases coexisting in the gas stream.
N2O conversion over the 20Co/30Mg–Al for the feed gas 2000 ppmv N2O/Ar (multiple sign) in the presence of 100 ppmv NO (open triangle), 5 vol% O2 (plus sign), 100 ppmv NO + 5 vol% O2 (open square), 2 vol% H2O (open diamond), 2 vol% H2O + 5 vol% O2 (open circle) or 2 vol% H2O + 100 ppmv NO + 5 vol% O2 (filled triangle)
To estimate the industrial potential of using the 20Co/30Mg–Al catalyst processes the N2O by decomposition, the durability of the catalyst was tested at 550 °C. As shown in Fig. 13, there was no obvious evidence of catalytic activity lost in the time on stream of 22 h for the catalyst in the 2000 ppmv N2O/Ar, thereby demonstrated that the catalyst has stable catalytic activity for the N2O decomposition.
4 Conclusions
Using the support of alumina modified with MgO to load Co3O4, can effectively avoid undesired CoAl2O4 formation at high temperature (700 °C) as long as the adequate amount of MgO (ca. 30 wt%) was used in the modification. The modification was realized by depositing Mg(OH)2 on Al(OH)3 and calcining the resulted material at 900 °C. For the 20Co/30Mg–Al catalyst, which was prepared by modifying alumina with 30 wt% MgO and loading 20 wt% Co3O4 on the composited support, about half of the cobalt exists as (Co,Mg)O solid solution and the rest exists as Co3O4 in the catalyst. Almost no CoAl2O4 was produced even though the catalyst had been subjected to the calcination at 700 °C for 3 h. Hence, the catalyst has much higher and stable activity for the N2O decomposition compared with the 20Co/Al that contains the same amount of cobalt with that of the 20Co/30Mg–Al but without MgO modifying the alumina.
References
Pérez-Ramı́rez J, Kapteijn F, Schöffel K, Moulijn JA (2003) Appl Catal B 44:117–151
Konsolakis M (2015) Acs Catal 5:6397–6421
Lee SJ, Ryu IS, Kim BM, Moon SH (2011) Int J Greenh Gas Con 5:167–176
Ohnishi C, Asano K, Iwamoto S, Chikama K, Inoue M (2007) Catal Today 120:145–150
Stelmachowski P, Zasada F, Piskorz W, Kotarba A, Paul JF, Sojka Z (2008) Catal Today 137:423–428
Zhang FF, Wang XP, Zhang XX, Turxun M, Yu HB, Zhao JJ (2014) Chem Eng J 256:365–371
Zabilskiy M, Erjavec B, Djinović P, Pintar A (2014) Chem Eng J 254:153–162
Yu HB, Tursun M, Wang XP, Wu XX (2016) Appl Catal B 185:110–118
Abu-Zied BM, Soliman SA, Abdellah SE (2015) J Ind Eng Chem 21:814–821
Yu HB, Wang XP, Wu XX, Chen Y (2018) Chem Eng J 334:800–806
Ivanov DV, Sadovskaya EM, Pinaeva LG, Isupova LA (2009) J Catal 267:5–13
Wu Y, Ni X, Beaurain A, Dujardin C, Granger P (2012) Appl Catal B 125:149–157
Ates A (2014) Catal Sci Technol 4:2031–2041
da Cruz RS, Mascarenhas AJS, Andrade HMC (1998) Appl Catal B 18:223–231
Gudyka S, Grzybek G, Grybos J, Indyka P, Leszczynski B, Kotarba A, Sojka Z (2017) Appl Catal B 201:339–347
Pietrogiacomi D, Campa MC, Carbone LR, Tuti S, Occhiuzzi M (2016) Appl Catal B 187:218–227
Grzybek G, Stelmachowski P, Gudyka S, Indyka P, Sojka Z, Guillén-Hurtado N, Rico-Pérez V, Bueno-López A, Kotarba A (2016) Appl Catal B 180:622–629
Klegová A, Pacultová K, Fridrichová D, Volodarskaja A, Kovanda F, Jirátová K (2017) Chem Eng Technol 40:981–990
Boissel V, Tahir S, Koh CA (2006) Appl Catal B 64:234–242
Russo N, Fino D, Saracco G, Specchia V (2007) Catal Today 119:228–232
Stelmachowski P, Maniak G, Kaczmarczyk J, Zasada F, Piskorz W, Kotarba A, Sojka Z (2014) Appl Catal B 146:105–111
Grzybek G, Ciura K, Wójcik S, Gryboś J, Indyka P, Inger M, Antoniak-Jurak K, Kowalik P, Kotarba A, Sojka Z (2017) Catal Sci Technol 7:5723–5732
Ji YG, Zhao Z, Duan AJ, Jiang GY, Liu J (2009) J Phys Chem C 113:7186–7199
Jongsomjit B, Panpranot J, Goodwin JG Jr (2001) J Catal 204:98–109
Jongsomjit B, Panpranot J, Goodwin JG Jr (2003) J Catal 215:66–77
Liotta LF, Pantaleo G, Macaluso A, Di Carlo G, Deganello G (2003) Appl Catal A 245:167–177
Liotta LF, Pantaleo G, Di Carlo G, Marcı̀ G, Deganello G (2004) Appl Catal B 52:1–10
Grzybek G, Wójcik S, Ciura K, Gryboś J, Indyka P, Oszajca M, Stelmachowski P, Witkowski S, Inger M, Kotarba A, Sojka Z (2017) Appl Catal B 210:34–44
Gayán P, de Diego LF, García-Labiano F, Adánez J, Abad A, Dueso C (2008) Fuel 87:2641–2650
Hadjiev VG, Iliev MN, Vergilov IV (1988) J Phys C 21:L199–L201
Keppler H, Bagdassarov N (1999) Chem Geol 158:105–115
Kushwaha AK (2010) Phys B 405:2795–2798
Wang HY, Ruckenstein E (2001) Appl Catal A 209:207–215
Acknowledgements
This work was financially supported by the National Natural Science Foundation of China (Grant Nos. 21277019 and 21777015).
Author information
Authors and Affiliations
Corresponding author
Additional information
Publisher's Note
Springer Nature remains neutral with regard to jurisdictional claims in published maps and institutional affiliations.
Rights and permissions
About this article
Cite this article
Li, Y., Wang, X. MgO Modifying Al2O3 to Load Cobalt Oxide for Catalytic N2O Decomposition. Catal Lett 149, 1856–1863 (2019). https://doi.org/10.1007/s10562-019-02789-5
Received:
Accepted:
Published:
Issue Date:
DOI: https://doi.org/10.1007/s10562-019-02789-5