Abstract
The interfacial reactions between Cu and Sn3Ag0.5Cu (SAC305) solder reflowed under various cooling rates were investigated. It is found that the cooling rate is an important parameter in solder reflow process because it influences not only microstructure of solder alloy but also the morphology and growth of intermetallic compounds (IMCs) formed between solder and Cu substrate. The experimental results indicate that only scallop-like Cu6Sn5 IMC layer is observed between solder and Cu substrate in case of water cooling and air cooling, while bilayer composed of scallop-like Cu6Sn5 and thin layer-like Cu3Sn is detected under furnace cooling due to sufficient reaction time to form Cu3Sn between Cu6Sn5 IMC and Cu substrate which resulted from slow cooling rate. Samples with different reflow cooling rates were further thermal-aged at 423 K. And it is found that the thickness of IMC increases linearly with square root of aging time. The growth constants of interfacial IMC layer during aging were obtained and compared for different cooling rates, indicating that the IMC layer thickness increased faster in samples under low cooling rate than in the high cooling rate under the same aging condition. The long prismatic grains were formed on the existing interfacial Cu6Sn5 grains to extrude deeply into solder matrix with lower cooling rate and long-term aging, and the Cu6Sn5 grains coarsened linearly with cubic root of aging time.
Similar content being viewed by others
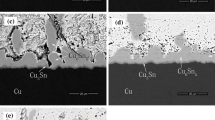
Avoid common mistakes on your manuscript.
1 Introduction
Due to concerns regarding the toxicity of Pb, which can threaten the environment and the human health, the evolution of a substitutional Pb-free solder solution has become an important issue for electronic interconnection materials [1–4]. Among all series of lead-free solders, SnAgCu-based solders are one of the most promising Pb-free solder alloys for aerospace applications and are already used widely in domestic applications [1, 2, 5, 6]. It is, therefore, important to thoroughly investigate the microstructure and reliability of Sn–Ag–Cu solder.
During solder reflow, the molten solder reacts with the metallization forming a layer of intermetallic compounds (IMCs) [7–10]. Although the presence of IMCs at the solder interface is an indication that a good metallurgical bond has been formed, their inherent brittle nature and tendency to concentrate stress and create defects often undermine reliability under stress conditions, such as thermal cycling. The excessive growth of intermetallic compounds may be detrimental to the reliability of the solder joint because of the brittleness of the intermetallic compounds layer, and the stress concentration generated from the volume change or complete consumption of the solderable substrate. The layer of IMCs is mainly composed of Cu6Sn5. When the solder joint is aged for at high temperature or long time, a layer of Cu3Sn is formed between the Cu6Sn5 and the Cu substrate. Generally speaking, the layer of interfacial IMCs has remarkable effect on the reliability of solder joints [11–13].
Additionally, in a soldering reflow process, post-reflow cooling rate is an important parameter. In one hand, the cooling requires being sufficiently slow to prevent thermal shock damage to the packaging and substrate materials. However, an excessively slow cooling rate may unnecessarily lengthen the fabrication process. Thus, an appropriate cooling rate has to be chosen. In other hand, the cooling rate affects the microstructure of the interfacial IMCs layer of solder joints, which in turn affects the reliability of the solder joints. Therefore, it is necessary to understand the influence of the post-reflow cooling rate on the interfacial IMCs layer. In the present study, the effects of cooling rate on the morphology and growth kinetics of the IMC formed between Sn3Ag0.5Cu (SAC305) and Cu substrate during both liquid-state reaction and solid-state aging were investigated. The growth mechanism of Cu6Sn5 is discussed, too.
2 Experimental procedure
The substrate used in this study was prepared from pure Cu plate (99.99 %) with dimensions of 40 × 40 × 2 mm3. The Sn3.0Ag0.5Cu solder alloy was prepared by induction melting of high-purity raw materials (99.99 wt% Sn, 99.95 wt% Ag and 99.9 wt% Cu) in a purified Ar atmosphere (99.999 %). The solder alloy was cut into sheet with 5 mm in diameter and 1 mm in thickness.
Before reflowing, the copper surface was carefully polished by using 0.1-μm diamond paste and then rinsed in water and methanol alcohol. Five solder sheets were placed on the fresh Cu pads employing rosin mildly activated (RMA) flux, as schematically shown in Fig. 1, which was used in previous study [4]. In the reflow process, the solder sheet was placed onto the Cu pad prepared as the above procedure and then sent into a reflow oven. Three thermocouples were used to monitor the temperature change during reflow process. The temperature profiles were controlled such that the solder was heated at the rate of 2 K/s to a peak temperature of 523 K (33 K above the melting temperature of Sn3Ag0.5Cu solder) and held for 300 s. Then, the samples were cooled in oven, air and quenched in water with cooling rate of 0.35, 3.0 and 45 K/s (hereafter referred to as slow, medium and fast cooling rate), respectively. The cooling rate was calculated in the temperature range from melting point to 30 K below the melting point of solder alloy. These reflowed solder samples with different cooling rates were aged at 423 K for 24, 120, 240 and 360 h, respectively.
Reflowed and aged samples were prepared for observations on the cross-sectional structure and top view of the IMC morphology under SEM. The common metallography practice was followed to reveal the cross-sectional view. In order to observe the top view of intermetallic compounds, majority of the solder was ground away first, followed by etching in 2 % HCl to dissolve the remaining solder.
As well known, the shape of the interfacial IMC layers is irregular, as shown in Fig. 2a, their equivalent thickness was digitally measured by using the software “Image J.” And, the average equivalent thickness of the IMC layers (X) at the interface of solder joints was calculated through dividing the integrated area (A) by the length of the IMC layers (L), as shown in the following equation:
Each sample was measured for more than ten locations.
In order to study the coarsening behavior of the interfacial Cu6Sn5 grains, their top view of micrographs was captured via SEM, and the mean equivalent spherical diameters of the interfacial Cu6Sn5 grains were then determined by using the “Image J” program through dividing the length (L) by number of grains (N), as schematically shown in Fig. 2b. Over 200 individual grains were measured for each experimental condition. The errors of the IMC equivalent thickness and equivalent diameter were obtained by using the standard deviation function from the measured data.
3 Results and discussion
Figure 3 shows the morphology of the IMCs layer at the interface between the SAC305 solder and Cu substrate after water quenching (Fig. 3a), air cooling (Fig. 3b) and furnace cooling (Fig. 3c). It is clearly seen that, in both cases, the interfacial reaction between SAC305 solder and Cu substrate leads to the formation of a scallop-like Cu6Sn5 phase. The Cu6Sn5 phase grows as scallop-like grains into the solder, which results in a very rough interfacial morphology between the IMC layer and the solder. After reflowing, only Cu6Sn5 IMC layer can be observed obviously in case of water and air cooling, but a tiny thin Cu3Sn layer can be detected between Cu6Sn5 and Cu with furnace cooling.
From the cross-sectional SEM micrographs, it is obviously seen that the IMC thickness is greater when the cooling rate is lower during reflow. The thicknesses of interfacial IMCs layer for each cooling condition, calculated by dividing IMC layer area by interface length (schematically illustrated in Fig. 2a), is shown in Fig. 3d. The thicknesses of the interfacial IMC layers corresponding to water cooling, air cooling and furnace cooling is 3.86, 5.48 and 8.35 μm, respectively. The thickness of the IMC layer with water cooling is slightly less than that with air cooling. It is indicated that the Cu–Sn IMC layer is mainly formed during the reflow stage (liquid-state reaction). The IMC layer is only slightly thicker after air cooling because the time for growth of interfacial IMC under this cooling condition is longer than that under water cooling condition. According to the study proposed by Yang and Zhang [14], there are two mechanisms of growth of interfacial Cu6Sn5. One is that Cu atoms from the substrate react directly with molten Sn. Because there is a concentration gradient of Cu atoms between Cu6Sn5 grains with different radius, Cu atoms can diffuse from small grains to large grains, inducing growth of large Cu6Sn5 grains and shrinkage of small grains [15]. Another is diffusion of Cu atoms from small Cu6Sn5 grains to large grains formed by reaction with Sn atoms at the solder/Cu6Sn5 interface. And the second mechanism dominates the growth of interfacial Cu6Sn5 layer with low cooling rate during reflow, such as the air or furnace cooling.
Besides, the cooling rate during reflow not only affected the growth of interfacial IMCs, but also influenced the precipitation and morphology of IMCs in the solder bulk. As shown from Fig. 3a–c, no obvious Cu6Sn5 or Ag3Sn IMCs were detected in the solder bulk of solder joint quenched in water. In contrast, some chunk-like Cu6Sn5 and Ag3Sn particles were observed in the solder matrix of solder joints cooled with air and furnace, and the sizes of Cu6Sn5 and Ag3Sn increased with the decreasing cooling rate.
Summarily, high cooling rate favors nucleation, while since the holding time at high temperature stage is shorter, resulting in a shorter effective time for IMCs growth. Subsequently, a thin layer and fine IMCs form at the interface and in solder bulk.
All SAC305/Cu solder joints reflowed for 300 s and cooled in various mediums (water, air and furnace) were aged at 423 K for different duration time. Figures 4, 5 and 6 show the cross-sectional microstructure of samples reflowed for 300 s then cooled in water, air and furnace and aged at 423 K for various hours, respectively. It can be found that the morphologies of the interfacial IMC layer are not dramatically changed in all samples, comparing with those of as-reflowed soldered samples. In Figs. 4 and 5, there is only a single Cu6Sn5 layer at interface in the aged samples for both 24 and 120 h, and a thin Cu3Sn layer can form between Cu6Sn5 and Cu as the aging time is prolonged to 240 h or 360 h. In the case of furnace cooling, double layer of Cu6Sn5 and Cu3Sn IMCs is detected for all aged solder joints, as presented in Fig. 6.
The formation of Cu3Sn is affected by the phase stability of Cu6Sn5 according to the following reaction,
It can be deduced that slow cooling rate during reflowing will result in more Cu atoms and can diffuse toward to Cu6Sn5 to form Cu3Sn phase within a sufficient time. Because the high aging temperature and long-term aging can lead Cu atoms to diffuse from substrate toward to Cu6Sn5/solder interface with enough time, subsequently, more Cu atoms can participate into the reaction with the existed Cu6Sn5 phase to form Cu3Sn phase. Thus, thicker Cu3Sn IMC layer can be observed when the aging time increases, as shown in Figs. 5d and 6d.
As well known, a thick interfacial IMCs layer is feasible to result in crack within the IMCs because of the brittle property of IMCs. So it is reasonable to explain that a crack is observed in the interfacial IMC layer of solder joint with furnace cooling and aged for 120 h, which is illustrated as the red arrow in Fig. 6b. According to the previous researches [16, 17], the Kirkendall void forms mainly within the Cu3Sn layer with long term of solid-state reaction, as indicated with the white circles in Fig. 6d.
Figure 7 and Table 1 show the measured thickness of interfacial IMCs layer of all samples investigated in the present paper. It is indicated that both the thicknesses of Cu6Sn5 and Cu3Sn increase with decreasing cooling rate or increasing aging time. The kinetics of IMCs growth can be dominated by the diffusion or interfacial chemical reaction [18]. The growth kinetic parameters of an IMC layer can be determined by plotting its measured thickness as a function of the aging time at a given temperature, such as given in Fig. 8. In the present work, accordingly, the growth of interfacial IMC during solid-state aging procedure is controlled by the diffusion. Accordingly, the relationship between IMC layer thickness and aging duration can be expressed as the following equation [19, 20]:
where X t is the IMC layer thickness at aging time t, X 0 is the initial IMC layer thickness after soldering and K is the diffusion coefficient as a function of temperature. And, the values of K respond to solder joints cooled with various rates are listed in Table 1.
In order to determine the diameter of the interfacial Cu6Sn5 IMC grains at the SAC305/Cu interface and compare the coarsening behavior of IMC grains in terms of diameter and thickness (as shown by the cross-sectional views: Figs. 4, 5, 6), IMCs were also examined from the top view. Figures 9, 10, 11 show the top views of the IMCs that formed at the interface of as-reflowed or aged joints cooled in water, air and furnace, respectively. The solder portion was entirely removed so that the surface morphology of the Cu6Sn5 IMC grains could be observed. Interestingly, the morphologies of the Cu6Sn5 grains form in the water, air and furnace cooling cases are different.
As indicated in Fig. 9, the interfacial Cu6Sn5 IMC of SAC305/Cu solder joints exhibits stone-like morphology after reflow and aging treatment. The morphologies of those IMCs are scallop-like for all solder joints irrespective to aging duration. According to Kim’s research [15], the growth of scallop-like Cu6Sn5 grains is because of two kinetic processes, one is ripening and another is interfacial reactions. Comparing with the interfacial Cu6Sn5 grains in the case of water cooling, the grains in the case of air cooling are coarser than that of water cooling with the same reflowing or aging processes, as shown in Fig. 10. With further decreased cooling rate, the scallop-like Cu6Sn5 grains possess larger size, which are illustrated in Fig. 11. Interestingly, some long prismatic grains form on the existing interfacial Cu6Sn5 grains, as shown in Figs. 10c and 11c. The causes for the formation of prismatic Cu6Sn5 IMC have been explained by Yang et al. [21, 22], who found that the long prismatic Cu6Sn5 extruded deeply into solder matrix as the precipitated Cu was enough in quantity during solidification of solder alloy and long-term aging. Additionally, some white microparticles were detected on the surface of Cu6Sn5 grains, which were identified to be Ag3Sn phase formed in the solder bulk. It is obviously seen that the grain size increases with aging time.
In order to investigate the coarsening mechanism, the diameters of IMC grains after reflow and thermal aging were measured from the top morphology, and the relationship between the mean diameter of grains and the cubic root of aging time was established, as illustrated in Fig. 12. This relationship was inconsistent with the coarsening mechanism developed by Tu et al. [15, 23]. According to the FDR model [23], it shows that the Cu6Sn5 grains dispersed at the interface grow by a ripening process controlled by volume diffusion in solder. And, the detailed relationships between interfacial Cu6Sn5 grain diameter and cubic root of aging time for water, air and furnace cooling conditions were obtained as following equations:
where d is the diameter of Cu6Sn5 grain and t is the aging time. It is obviously seen that there is a linear relationship between the Cu6Sn5 grain diameter and cubic root of aging time. This relationship is consistent with the theoretical analysis of coarsening mechanism of Cu6Sn5 grains at the interface developed by Tu et al. [15, 23], in which the grains are assumed to grow in a self-similar manner, i.e., a constant aspect ratio between perpendicular length and lateral width is preserved, and the average grain size is expected to follow a 1/3 power law in aging time.
4 Conclusion
Scallop-like Cu6Sn5 and thin layer-like Cu3Sn IMC grains are formed between SAC305 solder and Cu substrate with different cooling rate during reflow process. When cooling rate decreases, both the thickness of interfacial IMC and amount of chunk-type IMC in solder bulk increase, meaning that the interfacial IMCs layer was not only affected by the reaction between liquid solder and solid substrate, but also by the solidification of solder alloy during cooling.
During aging process, the IMC growth has linear relation with square root of aging time. The growth constants of interfacial IMC layer are 2.32, 3.08 and 4.79 × 10−3 μm s−1/2 for water, air and furnace cooling condition, respectively. The mean diameters of the Cu6Sn5 grains are found to increase with decreasing cooling rate during reflowing as well as increasing aging time, and the grains coarsened linearly with cubic root of aging time. The long prismatic grains are formed on the existing interfacial Cu6Sn5 grains to extrude deeply into solder matrix with decreasing cooling rate and long-term aging.
References
L. Zhang, L.L. Gao, Interfacial compounds growth of SnAgCu (nano La2O3)/Cu solder joints based on experiments and FEM. J. Alloys Compd. 635, 55–60 (2015)
J. Wang, H.M. Wei, P. He, T.S. Lin, F.J. Lu, Microstructure and mechanical properties of tin–bismuth solder reinforced by aluminum borate whiskers. J. Electron. Mater. 44, 3872–3879 (2015)
L. Zhang, L. Sun, Y.H. Guo, Microstructures and properties of Sn58Bi, Sn35Bi0.3Ag, Sn35Bi1.0Ag solder and solder joints. J. Mater. Sci. Mater. Electron. 26, 7629–7634 (2015)
X.W. Hu, Q. Huang, Y.L. Li, Y. Liu, Z.X. Min, A study on the interfacial reaction of Sn58Bi/Cu soldered joints under various cooling and aging conditions. J. Mater. Sci. Mater. Electron. 26, 5140–5151 (2015)
Q.K. Zhang, W.M. Long, X.Q. Yu, Y.Y. Pei, P.X. Qiao, Effects of Ga addition on microstructure and properties of Sn–Ag–Cu/Cu solder joints. J. Alloys Compd. 622, 973–978 (2015)
A. Sharma, B.G. Baek, J.P. Jung, Influence of La2O3 nanoparticle additions on microstructure, wetting, and tensile characteristics of Sn–Ag–Cu alloy. Mater. Des. 87, 370–379 (2015)
X.W. Hu, Y.L. Li, Z.X. Min, Interfacial reaction and growth behavior of IMCs layer between Sn–58Bi solders and a Cu substrate. J. Mater. Sci. Mater. Electron. 24, 2027–2034 (2013)
X.W. Hu, Y.L. Li, Z.X. Min, Interfacial reaction and IMC growth between Bi-containing Sn0.7Cu solders and Cu substrate during soldering and aging. J. Alloys Compd. 582, 341–347 (2014)
X.C. Lv, T.S. Lin, J. Wang, J. An, P. He, Morphology characterization of multi-walled carbon nanotubes in Sn–58Bi/CNTs composites. Mater. Trans. 54, 1228–1231 (2013)
P. He, X.C. Lv, T.S. Lin, H.X. Li, J. An, X. Ma, J.C. Feng, Y. Zhang, Q. Li, Y.Y. Qian, Improvement of mechanical properties of Sn–58Bi alloy with multi-walled carbon nanotubes. Trans. Nonferr. Met. Soc. China 22, s692–s696 (2012)
X.W. Hu, Y.L. Li, Y. Liu, Y. Liu, Z.X. Min, Microstructure and shear strength of Sn37Pb/Cu solder joints subjected to isothermal aging. Microelectron. Reliab. 54, 1575–1582 (2014)
X.W. Hu, W.J. Chen, X. Yu, Y.L. Li, Y. Liu, Z.X. Min, Shear strengths and fracture behaviors of Cu/Sn37Pb/Cu soldered joints subjected to different displacement rates. J. Alloys Compd. 600, 13–20 (2014)
K. Maslinda, A.S. Anasyida, M.S. Nurulakmal, Effect of Al addition to bulk microstructure, IMC formation, wetting and mechanical properties of low-Ag SAC solder. J. Mater. Sci. Mater. Electron. (2015). doi:10.1007/s10854-015-3780-y
L. Yang, Z.F. Zhang, Growth behavior of intermetallic compounds in Cu/Sn3.0Ag0.5Cu solder joints with different rates of cooling. J. Electron. Mater. 44, 590–596 (2015)
H.K. Kim, K.N. Tu, Kinetic analysis of the soldering reaction between eutectic SnPb alloy and Cu accompanied by ripening. Phys. Rev. B 53(23), 16027–16033 (1996)
X.W. Hu, Z.R. Ke, Growth behavior of interfacial Cu–Sn intermetallic compounds of Sn/Cu reaction couples during dip soldering and aging. J. Mater. Sci. Mater. 25, 936–945 (2014)
X.W. Hu, Y.L. Li, K. Li, Z.X. Min, Effect of Bi segregation on the asymmetrical growth of Cu–Sn intermetallic compounds in Cu/Sn–58Bi/Cu sandwich solder joints during isothermal. Aging 42, 3567–3572 (2013)
M. Yang, M.Y. Li, J. Kim, Texture evolution and its effects on growth of intermetallic compounds formed at eutectic Sn37Pb/Cu interface during solid-state aging. Intermetallics 31, 177–185 (2012)
M. He, Z. Chen, G.J. Qi, C.C. Wong, S.G. Mhaisalkar, Effect of post-reflow cooling rate on intermetallic compound formation between Sn–3.5Ag solder and Ni–P under bump metallization. Thin Solid Films 462–463, 363–369 (2004)
J. Hu, A.M. Hu, M. Li, D.L. Mao, Depressing effect of 0.1 wt% Cr addition into Sn–9Zn solder alloy on the intermetallic growth with Cu substrate during isothermal aging. Mater. Character. 61, 355–361 (2010)
M. Yang, Y. Cao, S. Joo, H. Chen, X. Ma, M. Li, Cu6Sn5 precipitation during Sn-based solder/Cu joint solidification and its effects on the growth of interfacial intermetallic compounds. J. Alloys Compd. 582, 688–695 (2014)
M.Y. Li, M. Yang, J. Kim, Textured growth of Cu6Sn5 grains formed at a Sn3.5Ag/Cu interface. Mater. Lett. 66, 135–137 (2012)
A.M. Gusak, K.N. Tu, Kinetic theory of flux-driven ripening. Phys. Rev. B 66, 115403-1–11540314 (2002)
Acknowledgments
This work was supported by the Nature Science Foundation of China (No. 51465039), Nature Science Foundation of Jiangxi Province (20151BAB206041), Science and Technology project of Jiangxi Department of Education (GJJ14108) and Fund of the State Key Laboratory of Solidification Processing in NWPU (SKLSP201508).
Author information
Authors and Affiliations
Corresponding author
Rights and permissions
About this article
Cite this article
Hu, X., Xu, T., Jiang, X. et al. Effects of post-reflow cooling rate and thermal aging on growth behavior of interfacial intermetallic compound between SAC305 solder and Cu substrate. Appl. Phys. A 122, 278 (2016). https://doi.org/10.1007/s00339-016-9893-1
Received:
Accepted:
Published:
DOI: https://doi.org/10.1007/s00339-016-9893-1