Abstract
As one of the important factors affecting the quality of soldered joints, the interfacial intermetallic compound (IMC) formed at the solder/substrate interface is of increasing concern to researchers. Thus, the growth behavior of interfacial IMC in Sn58Bi/Cu solder joints was investigated as different cooling methods-quenched water, cooling in air, and cooling in a furnace during reflowing were used. In this work, the effect of cooling rate on interfacial IMC growth is studied in Sn58Bi/Cu system. Morphology and growth kinetics of the interfacial Cu–Sn IMC under various cooling rates were studied. It was found that only scallop-like Cu6Sn5 IMC layer was observed between solder and Cu substrate in cases of water cooling and air cooling, while bi-layer composed of scallop-like Cu6Sn5 and planar Cu3Sn was detected under furnace cooling due to sufficient reaction time to form Cu3Sn between Cu6Sn5 IMC and Cu substrate which resulted from slow cooling rate. Samples with different reflow cooling rate were further thermal aged at 373 and 393 K, respectively. The results showed that the morphology of interfacial Cu–Sn IMC layer would transform from scallop-like to planar-like with increasing aging time, and the thickness of IMC increased linearly with square root of aging time. The growth constants of interfacial IMC layer were obtained and compared for different cooling rates and aging temperatures, indicating that the IMC layer thickness increased faster in samples under slow cooling rate than the fast cooling ones under the same aging condition, and higher aging temperature could result in faster growth of IMC layer. The interfacial Cu6Sn5 grains gradually transformed to facet prismatic shape as the cooling rate decreased, and the grain size increased dramatically as the samples were cooled in furnace, comparing with that of samples cooled in water and air.
Similar content being viewed by others
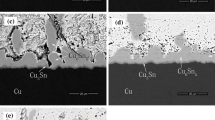
Avoid common mistakes on your manuscript.
1 Introduction
Sn–Bi solder is proposed as one of the most promising substitutes for lead-containing solder due to its lower melting temperature (412 K) and low coefficient of thermal expansion [1]. These characteristics provide its useful applications on energy saving, step soldering and the process that is sensitive to temperature or thermal damage [2]. Besides, Sn–58Bi solder has good wettability, yield strength, cost efficiency, joint strength, and large creep resistance [3].
Commonly, Cu is the most used substrate materials in electronics packaging. The nucleation and growth of intermetallic compounds (IMC) between the Cu substrate and the solders during the soldering process are critical steps in the formation of reliable solder joints. The existence of IMC is a key indication of an adequate metallurgical bond in solder joints [4–6]. The layer of interfacial IMC is mainly composed of Cu6Sn5. When the solder joint is aged at high temperature for a long time, a layer of Cu3Sn formed between the Cu6Sn5 and the Cu substrate. Generally speaking, the layer of interfacial compounds has remarkable effect on the reliability of solder joints [7–9]. For instance, a thin IMC layer and small Cu6Sn5 grain on interface are beneficial to the reliability of solder joints. While thick interfacial IMC layer and large Cu6Sn5 grain are undesirable due to the initiation of cracks can occur near the thick IMC layer, resulting in failure of solder joints.
It’s well known that the cooling rate affects both the microstructure of bulk solder and the interfacial IMC layer. And, there have been some studies about cooling rate effect on lead-free solders, such as SnAg [10, 11] and SnAgCu [12, 13]. Some have focused on the microstructure of the bulk solders, interfacial IMC, and the joint reliability was evaluated by a mechanical test [10–13]. Less attention has been paid to the influence of cooling rate on the morphology and growth of the IMC. The main purpose of this paper is to study the effect of cooling rate during reflowing on the morphology and growth kinetics of the IMC formed between Sn–58Bi and Cu pad in liquid state reaction, as well as the aging condition in solid state reaction.
2 Experimental procedure
The substrate used in this study was prepared from pure Cu plate (99.99 wt%) with dimensions of 40 × 40 × 2 mm3. The Sn–58Bi eutectic alloy was prepared by induction melting of high-purity raw materials, including Sn (99.99 wt%) and Bi (99.95 wt%) in a purified Ar atmosphere (99.999 %). The selection of this eutectic solder is based on the consideration that it has a low-melting point (411 K) and is much cheaper than other low-melting-point solders such as Sn–In. The solder alloy was cut into thin sheet with 5 mm in diameter and 1 mm in thickness.
Before soldering, the copper surface was carefully polished by using 0.1 μm diamond paste, and then rinsed in water and methanol alcohol. Nine pieces of solder sheet were placed on the fresh Cu pads employing rosin mildly activated (RMA) flux, as shown in Fig. 1. In the reflow process, the solder sheet was placed onto the Cu pad prepared as the above procedure and then sent into a reflow oven. Three thermocouples were used to monitor the temperature change during reflow process. The temperature profiles were controlled such that the solder was heated at the rate of 2 K/s to a peak temperature of 473 K (61 K above the melting temperature of Sn–58Bi solder) and held for 300 s. Then samples were cooled in oven, air and quenched in water with cooling rate of 0.35, 3.0 and 45 K/s (hereafter referred to as slow, medium and fast cooling rate), respectively. The cooling rate was calculated in the temperature range from melting point to 30 K below the melting point of solder alloy. These reflowed solder samples with different cooling rates were aged at 373 and 393 K for 24, 120, 240 and 360 h, respectively.
Reflowed and aged samples were prepared for observations on the cross sectional structure and top view of the IMC morphology under a FEI Quanta 200F scanning electron microscope (SEM). An X-ray microanalysis using energy dispersive spectroscopy (EDS), allows the SEM to qualitatively analyze the elements present in a selected area of backscattered electron image. The common metallography practice was followed to reveal the cross sectional view. In order to observe top view of IMC, majority of the solder was ground away first, followed by ultrasonic deep etching in distilled water with 10 % HNO3 to dissolve the remaining solder. Image analysis software was used to measure the area and length of IMC in cross sectional SEM images. The average thickness of IMC layer was calculated using measured area divided by length in the area. Each sample was measured more than ten locations. And the Cu6Sn5 IMC grains size were measured from the top view micrograph by using Image analysis software, too.
3 Results and discussion
3.1 Effect of the cooling rate on Cu–Sn IMC growth during liquid state interfacial reaction
Figure 2a, b, c show the cross section microstructures of samples reflowed for 300 s then cooled in water, air and furnace, respectively. The microstructure of the Sn–58Bi solder consists of the Sn-rich phase (grey phase) and the Bi-rich phase (white phase), as indicated in Fig. 2a. As can be seen from Fig. 2, the interfacial IMC layers show similar shapes for all solder joints after reflow. Cu diffuses rapidly into the molten solder and forms scallop-like η-Cu6Sn5 IMC layers between the solder and the Cu substrates during reflow under cooling in water and air, as shown in Fig. 2a, b. But in the case of furnace cooling condition (Fig. 2c), Cu6Sn5 IMCs near the solder side and Cu3Sn IMCs near the Cu pad side are both observed at the interface of solder joints, which are confirmed by EDX analysis, as illustrated in Fig. 3. It’s indicated that the scallop-like Cu6Sn5 phase is composed of 51.91 at.% Cu and 48.09 at.% Sn, and planar Cu3Sn phase is composed of 75.76 at.% Cu and 24.24 at.% Sn. During the reflow process, an IMC layer is formed at the interface between the Cu bonding pad and the solder and is the reaction product between Cu and Sn atoms. This means that the IMC is not a product of the reaction between the Cu from the bonding pad and Bi from the solder. The Cu–Bi binary phase diagram [14] shows that no IMC phase between Bi and Cu. Cu and Bi are essentially mutually insoluble under 543 K [15–17].
EDS results of interfacial Cu–Sn IMCs in Fig. 2c, a spectrum 1, b spectrum 2
From the cross sectional SEM micrographs, it is clear that the IMC thickness is greater when the cooling rate is slower during reflow. Average thickness of total interfacial IMC layers formed between Sn–58Bi solder and Cu under various cooling rates was measured. The measured thickness with different cooling rates was plotted in Fig. 4, and the thickness of interfacial IMC layer was 0.81, 1.06 and 3.56 μm for solder joints cooled in water, air and furnace, respectively. It is concluded that reflowing for 300 s, Cu–Sn IMCs thickness increases dramatically with decreasing cooling rate. This indicates that the interfacial IMC growth is dependent on cooling rate during reflowing and the interfacial IMCs layer is not only affected by the reaction between liquid solder and solid substrate, but also by the solidification of solder alloy during cooling.
3.2 Growth of Cu–Sn IMC during isothermal solid-state aging
All Sn–58Bi/Cu solder joints reflowed for 300 s and cooled under different cooling rates were aged at 373 and 393 K, respectively. Figures 5 and 6 show the cross sectional microstructure of samples reflowed for 300 s then cooled in water and aged at 373 and 393 K for various hours, respectively. In Fig. 5, only scallop-like Cu6Sn5 IMC layer was observed at the interface of all aged samples. The shapes of interfacial IMC layers were similar under aging temperature of 373 K with 24, 120, 240 and 360 h. It is obviously seen that the interfacial IMC thickness increased with increasing aging time. As the aging temperature increased to 393 K, the observed IMC layer between Sn–58Bi solder and Cu pad differed from that in aging temperature of 373 K. As can be seen from Fig. 6, only a thin layer of Cu6Sn5 IMC was observed from the soldered joints aged at 393 K for 24 h (Fig. 6a), but double layers composed of Cu6Sn5 and Cu3Sn IMCs were detected in soldered joints aged at 393 K for 120, 240 and 360 h (Fig. 6b–d). As similar to the results of the interfacial microstructure in Fig. 5, the thickness of the interfacial IMC layer increased with increasing aging time, too. Besides, the IMC layer changed from scallop-like (Fig. 6a, b) to planar-like (Fig. 6c, d) as the aging time increased.
Figures 7, 8, 9 and 10 show the cross sectional microstructure of samples reflowed for 300 s then cooled in air and furnace, then aged at 373 and 393 K for various hours, respectively. Comparing the interfacial IMC layer of soldered joints under different cooling rates, they had similar shape but the thickness increased with decreasing cooling rate during reflowing. In Fig. 7, only Cu6Sn5 IMC single layer was observed between Sn–58Bi solder and Cu substrate. However, both the Cu6Sn5 and Cu3Sn phase were found at the joint interface when the joints were subjected to slow cooling rate, high temperature or long-term aging treatment, as shown in Figs. 8, 9 and 10 (except for Fig. 8a). Those results indicate that slow cooling rate, high aging temperature and long aging time can promote the growth of Cu3Sn IMC layer. Accordingly, the growth of the Cu3Sn phase is governed mainly by the following reaction.
It’s can be deduced that slow cooling rate during reflowing will result in more Cu atoms can diffuse toward to Cu6Sn5 to form Cu3Sn phase within a sufficient time. Due to the high aging temperature and long-term aging can lead Cu atoms from substrate to diffuse with enough time, subsequently, more Cu atoms can participate into the reaction with the existed Cu6Sn5 phase to form Cu3Sn phase. Thus, thicker Cu3Sn IMC layer can be observed when the aging temperature and time increase, as shown in Figs. 8, 9 and 10.
In addition, as illustrated in Figs. 7, 8, 9 and 10, the morphology of the IMC layers after the thermal aging changed significantly. With the aging time increasing, the IMC layer became planar. This might be attributed to following two aspects. One is the IMC grain growth, resulting from large grains merging small grains. Another is the solution equilibrium of IMC in solder bulk. Planar interface is the indication of equilibrium. It has been reported that the interfacial IMCs grain growth at the early stages of solid-state is controlled by the grain boundary diffusion, and rarely related to the volume diffusion. However, after long-term thermal aging, Cu6Sn5 grains grow large enough and the fraction of grain boundary area decreases enough to lead to the ripening of two neighbor Cu6Sn5 grains, in this case, the volume diffusion will takes over as the predominant transport mechanism [18].
It is worth noting that, a Bi-rich layer was observed between Cu6Sn5 and Sn–58Bi solder in joints aged at 393 K for 240 or 360 h, as indicated in Fig. 6c, d. Similar to the formed Pb-rich layer in Sn37Pb/Co system [19]. The formed interfacial IMC layer is not affected by Bi, even with such large Bi content. This suggests that Bi has no strong interaction with Cu, it is consistent with the Cu–Bi phase diagram [14]. In addition, Cu and Bi have very little solubility with each other. It illustrates that the interatomic bond between Cu and Bi is repulsive, and therefore, Bi is chemically inert to Cu. This inference is in good agreement with the interfacial microstructure in the present work.
Furthermore, not only Bi-rich layer could be observed between solder and IMC, but Bi-rich particles were also obviously found at the Cu3Sn/Cu interface in samples which were long-term aged at high temperature or cooled slowly, indicated as white circles in Figs. 6d, 10c, d. Commonly, Bi segregation at the Cu3Sn/Cu interface always occurs in the Bi-containing solder/Cu couples [20–22]. Unfortunately, the Bi segregation dramatically deteriorates the mechanical properties of solder joints [23, 24].
As indicated as the red squares in Figs. 6, 8, 9 and 10, some voids were detected in Cu3Sn layer or the neighborhood of the Cu3Sn/Cu interface. According to the previous studies [25], those voids were defined to be Kirkendall voids, which were resulted from the faster diffusion of Cu than that of Sn. In general, the Kirkendall void formation in the solder joint on Cu substrate occurs by two steps. First, vacancies are generated in Cu near Cu3Sn layer after the Cu atoms have left the Cu pad and diffused towards the solder. Second, the vacancies coalesce into voids. The vacancy generation in Cu is unavoidable because of the unbalanced inter-diffusion of Cu and Sn. Subsequently, the Kirkendall voids form between Cu and Cu3Sn will result in a porous Cu/Cu3Sn interface and Cu3Sn layer, which obviously deteriorate the mechanical and electrical properties of the solder joints.
Figure 11 shows the average thicknesses of the IMC layers quantitatively. The IMC thickness increases linearly with the square root of aging time. This relationship can be represented by
where δ and δ 0 is the thickness of the IMC at time t and zero, respectively, and k the growth rate constant. The values of k in the present work are listed in Table 1. This means that the interfacial Cu–Sn IMCs growth under isothermal aging is a diffusion-controlled process. This conclusion is agreed with other researchers’ results [26–28] on various soldering systems. For the Sn–58Bi/Cu soldered joints, it is reasonable that the k value at 393 K is greater than that of 373 K, as indicated in Table 1.
In order to determine the diameter of the IMC grains at the Sn–58Bi/Cu interface and compare the coarsening behavior of IMC grains in terms of diameter and thickness (as shown by the cross-sectional views: Figs. 5, 6, 7, 8, 9 and 10), IMCs were also examined from the top view. Figure 12 shows the top views of the IMCs at the solder/substrate interface after deep etching. As seen in Fig. 12, the grain sizes of the IMCs at the Sn–58Bi/Cu interface increased after thermal aging, and it seemed that the larger grains grew at the expense of the smaller grains. Comparing with the morphologies of Cu6Sn5 grains in Fig. 12, the Cu6Sn5 grains showed scallop-like (Fig. 12a1, a2, b1, b2), but some grains gradually transformed to facet prismatic shape as the cooling rate decreases, as indicated in Fig. 12c1, c2. It is similar to the morphology evolution of interfacial IMCs formed at the Sn–58Bi/OSP-finished Cu interface for different reflow times developed by Lee et al. [29], in which the shape of IMCs changed from a scallop-like to a facet-like as the reflow time increased.
The growth of scallop-like η-Cu6Sn5 grains is because of two kinetic processes: ripening and interfacial reactions [30]. The ripening reaction is the result of the reaction between scallop-like Cu6Sn5 grains, in which they grow larger in size but fewer in number over time, meaning that large grains grow at the expense of smaller grains. The η-Cu6Sn5 IMC layers also grow as the result of the interfacial reaction between the solder alloy and Cu. After the formation of scallop-like η-Cu6Sn5 grains, solder channels between the Cu6Sn5 grains provide direct contact between the solder alloy and Cu. These grain boundary channels serve as fast diffusion and dissolution paths for Cu into the solder alloy.
In order to study the coarsening mechanism, the IMC grain diameters after reflow and thermal aging were measured from the top view and were analyzed by preparing a log–log plot of the mean diameter versus the aging time, as indicated in Fig. 13. The relationship between the mean diameters of the Cu6Sn5 grains and the aging time is exponential as follows [31]:
in which d is the mean diameter of the Cu6Sn5 grains, C and n are two constants, and t is the aging time. As seen fro Fig. 9, the obtained exponent n is 0.071, 0.086 and 0.014 for samples cooled in water, air and furnace then aged at 373 K, but 0.072, 0.095 and 0.029 for samples aged at 393 K, respectively.
4 Conclusion
In the present study, the effects of cooling rate on the morphology and growth behavior of the interfacial IMCs of reflowed and aged Sn–58Bi/Cu soldered joints were studied. On the basis of the experimental results main conclusions were:
-
1.
The thickness of interfacial Cu–Sn IMCs layer after quenching in water was thinner than that after cooling in air and furnace, meaning that the interfacial IMCs layer was not only affected by the reaction between liquid solder and solid substrate, but also by the solidification of solder alloy during cooling.
-
2.
The growth behavior of interfacial IMC layers is controlled by and inversely thickens with cooling rate, which is determined by the cooling medium during reflowing.
-
3.
During aging process, the IMC growth has linear relationship with square root of aging time. The growth constant increases with samples undergoing low cooling rate due to the IMC microstructure difference under different cooling rates.
-
4.
The cooling rate during reflowing has a remarkable effect on the morphology and size of interfacial Cu6Sn5 grains. The mean diameters of the Cu6Sn5 grains are found to increase with decreasing cooling rate during reflowing as well as increased aging time. The morphology of interfacial Cu6Sn5 grain would transform from a scallop-like to a facet-like with decreasing cooling rate. Fast cooling is beneficial for formation of small interfacial Cu6Sn5 IMC grains.
References
W.R. Myung, Y. Kim, S.B. Jung, Mechanical property of the epoxy-contained Sn-58Bi solder with OSP surface finish. J. Alloys Compd. 615, S411–S417 (2014)
Z. Mei, J.W. Morris, Characterization of eutectic Sn–Bi solder joints. J. Electron. Mater. 21, 599–607 (1992)
X. Hu, Y. Li, Z. Min, Interfacial reaction and growth behavior of IMCs layer between Sn–58Bi solders and a Cu substrate. J. Mater. Sci.: Mater. Electron. 24, 2027–2034 (2013)
L. Zhang, C. He, Y. Guo, J. Han, Y. Zhang, X. Wang, Development of SnAg-based lead free solders in electronics packaging. Microelectron. Reliab. 52, 559–578 (2012)
M. Yang, Y. Cao, S. Joo, H. Chen, X. Ma, M. Li, Cu6Sn5 precipitation during Sn-based solder/Cu joint solidification and its effects on the growth of interfacial intermetallic compounds. J. Alloys Compd. 582, 688–695 (2014)
M.S. Park, M.K. Stephenson, C. Shannon, L.A.C. Diaz, K.A. Hudspeth, S.L. Gibbons, J. Munoz-Saldana, R. Arroyave, Experimental and computational study of the morphological evolution of intermetallic compound (Cu6Sn5) layers at the Cu/Sn interface under isothermal soldering conditions. Acta Mater. 60, 5125–5134 (2012)
X. Hu, W. Chen, X. Yu, Y. Li, Y. Liu, Z. Min, Shear strengths and fracture behaviors of Cu/Sn37Pb/Cu soldered joints subjected to different displacement rates. J. Alloys Compd. 600, 13–20 (2014)
X. Hu, Y. Li, Y. Liu, Y. Liu, Z. Min, Microstructure and shear strength of Sn37Pb/Cu solder joints subjected to isothermal aging. Microelectron. Reliab. 54, 1575–1582 (2014)
Q.V. Bui, S.B. Jung, Characterization of low speed shear test reliability of Sn-1.0Ag-XCe/ENEPIG solder joint. J. Alloys Compd. 560, 54–61 (2013)
M. He, Z. Chen, G. Qi, C.C. Wong, S.G. Mhaisalkar, Effect of post-reflow cooling rate on intermetallic compound formation between Sn–3.5 Ag solder and Ni–P under bump metallization. Thin Solid Films 462–463, 363–369 (2004)
H.T. Ma, J. Wang, L. Qu, N. Zhao, A. Kunwar, A study on the physical properties and interfacial reactions with Cu substrate of rapidly solidified Sn–3.5 Ag lead-free solder. J. Electron. Mater. 42, 2686–2695 (2013)
K.S. Kim, S.H. Huh, K. Suganuma, Effects of cooling speed on microstructure and tensile properties of Sn–Ag–Cu alloys. Mater. Sci. Eng., A 333, 106–114 (2002)
L. Yang, Z.F. Zhang, Growth behavior of intermetallic compounds in Cu/Sn3.0Ag0.5Cu solder joints with different rates of cooling. J. Electron. Mater. 44, 590–596 (2015)
T.B. Massalski, J.L. Murray, L.H. Bennet, H. Baker, Binary alloy phase diagrams, vol 1, 2nd edn. (ASM 1990, Materials Park, 1990), pp. 732–733
V.J. Keast, A.L. Fontaine, J.D. Plessis, Variability in the segregation of bismuth between grain boundaries in copper. Acta Mater. 55, 5149–5155 (2007)
G. Duscher, M.F. Chisholm, U. Alber, M. Rühle, Bismuth-induced embrittlement of copper grain boundaries. Nat. Mater. 3, 621–626 (2004)
R. Schweinfest, A.T. Paxton, M.W. Finnis, Bismuth embrittlement of copper is an atomic size effect. Nature 432, 1008–1011 (2004)
M. Schaefer, R.A. Fournelle, J. Liang, Theory for intermetallic phase growth between cu and liquid Sn–Pb solder based on grain boundary diffusion control. J. Electron. Mater. 27, 1167–1176 (1998)
C. Wang, C. Kuo, Interfacial reactions between eutectic Sn–Pb solder and Co substrate. J. Mater. Sci. 46, 2654–2661 (2011)
X. Hu, Y. Li, K. Li, Z. Min, Effect of Bi segregation on the asymmetrical growth of Cu–Sn ntermetallic compounds in Cu/Sn–58Bi/Cu sandwich solder joints during isothermal aging. J. Electron. Mater. 42, 3567–3572 (2013)
X. Hu, Y. Li, Z. Min, Interfacial reaction and IMC growth between Bi-containing Sn0.7Cu solders and Cu substrate during soldering and aging. J. Alloys Compd. 582, 341–347 (2014)
T.Y. Kang, Y.Y. Xiu, C.Z. Liu, L. Hui, J.J. Wang, W.P. Tong, Bismuth segregation enhances intermetallic compound growth in SnBi/Cu microelectronic interconnect. J. Alloy. Compd. 509, 1785–1789 (2011)
X.Y. Pang, Z.Q. Liu, S.Q. Wang, J.K. Shang, Effects of Bi segregation on the tensile properties of Cu/Cu3Sn(100) interface. Microelectron. Reliab. 51, 2330–2335 (2011)
H.F. Zou, Q.K. Zhang, Z.F. Zhang, Interfacial microstructure and mechanical properties of SnBi/Cu joints by alloying Cu substrate. Mater. Sci. Eng., A 532, 167–177 (2012)
X. Hu, Z. Ke, Growth behavior of interfacial Cu–Sn intermetallic compounds of Sn/Cu reaction couples during dip soldering and aging. J. Mater. Sci.: Mater. Electron. 25, 936–945 (2014)
H. Sun, Q. Li, Y.C. Chan, A study of Ag additive methods by comparing mechanical properties between Sn57.6Bi0.4Ag and 0.4 wt% nano-Ag-doped Sn58Bi BGA solder joints. J. Mater. Sci.: Mater. Electron. 25, 4380–4390 (2014)
J. Shen, Y. Pu, H. Yin, D. Luo, J. Chen, Effects of minor Cu and Zn additions on the thermal, microstructure and tensile properties of Sn–Bi-based solder alloys. J. Alloy Compd. 614, 63–70 (2014)
S. Lin, T.L. Nguyen, S. Wu, Y. Wang, Effective suppression of interfacial intermetallic compound growth between Sn–58 wt% Bi solders and Cu substrates by minor Ga addition. J. Alloys Compd. 586, 319–327 (2014)
S.M. Lee, J.W. Yoon, S.B. Jung, Interfacial reaction and mechanical properties between low melting temperature Sn–58Bi solder and various surface finishes during reflow reactions. J. Mater. Sci.: Mater. Electron. (2014). doi:10.1007/s10854-014-2589-4
H.K. Kim, K.N. Tu, Kinetic analysis of the soldering reaction between eutectic SnPb alloy and Cu accompanied by ripening. Phys. Rev. B 53, 16027–16034 (1996)
M. Yang, M. Li, J. Kim, Texture evolution and its effects on growth of intermetallic compounds formed at eutectic Sn37Pb/Cu interface during solid-state aging. Intermetallics 31, 177–185 (2012)
Acknowledgments
This work was supported by the Nature Science Foundation of China (No. 51465039) and the Science and Technology project of Jiangxi Department of Education (GJJ14108).
Author information
Authors and Affiliations
Corresponding author
Rights and permissions
About this article
Cite this article
Hu, X., Huang, Q., Li, Y. et al. A study on the interfacial reaction of Sn58Bi/Cu soldered joints under various cooling and aging conditions. J Mater Sci: Mater Electron 26, 5140–5151 (2015). https://doi.org/10.1007/s10854-015-3042-z
Received:
Accepted:
Published:
Issue Date:
DOI: https://doi.org/10.1007/s10854-015-3042-z