Abstract
The application of micro-mechanical cutting operations, such as micro-drilling, is crucial for producing microsystem components. In the production of jet engine parts, Inconel 718 superalloy has been used to produce these components due to its high performance at high temperatures. Due to the low thermal conductivity and the high work hardening tendencies of Inconel 718, a high amount of the cutting temperature dissipates toward the cutting tool instead of the chip. When using micro-scale drilling (micro-drilling), heat dissipation becomes more challenging. This affects the tool life and the machined surface quality; therefore, when machining these alloys, a cutting fluid is required to decrease the high amounts of generated heat. Flood coolant is commonly used to reduce the cutting temperature; however, government regulations have been published for alternative cooling processes to decrease the influences of flood coolant on the environment and the operator’s health. Minimum quantity lubrication (MQL) has been used as an alternative to conventional cutting fluids because it minimizes the consumption of cooling lubricants and reduces the environmental and health impacts; however, pure MQL cooling has an ineffective cooling ability. In order to enhance thermal conductivity, viscosity, and wettability of the MQL base fluid, an MQL-nanofluid was used. This study investigated the performance of a micro-drilling process using an MQL-nanofluid with regard to thrust forces, tool wear, and burr formation, and compared it to flood cooling and a pure MQL. Micro-drilling experiments involving Inconel 718 were conducted using the same cutting parameters, drilling tool, and machining environment for both the MQL and the flood coolant. The results revealed that the MQL-nanofluid approach was promising in terms of machining outputs as well as sustainability.
Similar content being viewed by others
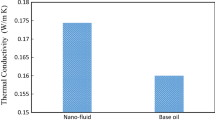
Avoid common mistakes on your manuscript.
1 Introduction
The implementation of micro-mechanical cutting operations like micro-drilling is important for producing microsystem components. In the aviation industry, these components need to be produced from high-performance materials such as Inconel 718 superalloy. This nickel-based alloy makes up 50% of an aircraft engine, including the blades, sheets, and discs. This is due to its outstanding properties, such as good heat resistance and the ability to retain strength at high temperatures [1]. However, the drilling operation of Inconel 718 superalloy is challenging because of the alloy’s conductivity property and the high precision requirements of the aviation industry. Because of the low thermal conductivity of the alloy, most of the heat caused by the machining process is dissipated by the cutting tool and the coolant (cutting fluid). When using micro-scale drilling (micro-drilling), heat dissipation becomes more challenging, particularly in parts produced from Inconel 718 superalloy [2, 3]. Strain hardening is another challenge during the machining of Inconel 718 due to the presence of elements such as niobium and molybdenum in the alloy [4].
This study investigated using an environmentally friendly cooling/lubrication approach (MQL-nanofluid) during the micro-drilling of Inconel 718 superalloy. Micro-drilling is a micro-machining process which makes holes using drills with diameters smaller than 1 mm [5, 6]. The diameter of the drilling tool is small, and cooling issues can cause wear and tear or even tool damage. These micro-scale holes are created by micro-drilling methods such as mechanical micro-drilling, electrical discharge machining (EDM), laser drilling, and electrochemical machining (ECM). Mechanical micro-drilling is a conventional micro-machining process [7].
Numerous researchers have investigated the micro-drilling of Inconel 718 using non-conventional micro-drilling techniques because of their accuracy [8,9,10,11]. However, these techniques often encounter issues in terms of costs, setting assistance equipment parameters, ability to machine only conductive materials (such as in EDM), instability, tool wear and low material removal rate [12]. In comparison, only mechanical parameters (e.g., cutting speed and feed) need to be considered in mechanical micro-drilling. In this work, micro-drilling experiments for Inconel 718 superalloy were thus performed by using mechanical micro-drilling.
Much of the literature has revealed that the machining of Inconel 718 superalloy is associated with unsatisfactory surface finish quality and excessive tool wear due to the high cutting temperature [13,14,15]; therefore, the application of a cutting fluid is required during machining operations to reduce the induced cutting heat in the shear zone, and to deliver cutting fluid at the tool-workpiece interface to preserve the cutting tool. Flood cooling is the most common cooling approach, but this approach is expensive because it uses a large amount of coolant. Also, health problems can arise when flood coolant is mishandled during use, storage, or disposal. Other health risks occur if bacteria grow in the flood coolant over a period of time and if metal debris contaminates the machine coolant [16, 17]. The economic, environmental, and human health problems associated with flood machining have prompted scholars to investigate techniques to reduce the amount of cutting fluids used in machining.
An interesting technology that is being increasingly employed in metal removal processes is minimum quantity lubrication (MQL). It is also known as near-dry machining (NDM) or micro-lubrication [18, 19]. In the implementation of cutting fluids, the MQL technique is considered to be a sustainable and clean cooling/lubrication technique because it minimizes the consumption of the cutting fluid and reduces impacts on operator health and the environment [20,21,22,23,24].
Much research has been done on the effects of the MQL method on machining efficiency. Bhowmick et al. [25] investigated the impacts of MQL cooling on the micro-drilling performance of magnesium alloys compared to dry machining. They found that MQL provided a significant contribution to decreasing the tool wear, thrust force, and torque compared to dry machining. Percin et al. [5] studied the effects of cutting parameters and different cooling/lubrication techniques (dry, flood, MQL, and cryogenic) on the micro-drilling of Ti-6Al-4V alloy. The cryogenic cooling approach showed the highest thrust force, while the MQL approach provided the highest engagement torque amplitude compared to the other cooling methods. They also reported that using different cooling conditions did not considerably influence the burr formation. Nam and Lee [26] also found that MQL minimized the thrust forces and drilling torques when performing micro-drilling of titanium alloy. Aslantas et al. [27] investigated the effects of using different cooling/lubrication approaches (dry, MQL, ethanol, and oil-water emulsion) on tool wear, surface quality, and burr formation in micro-milling of Inconel 718 superalloy. They reported that, among these cooling techniques, MQL cooling and dry cutting provided the best surface quality. The MQL approach also showed the lowest burr height compared to the other cooling/lubrication approaches.
Sun et al. [28] found that MQL machining enhanced the tool life by 50% and 80% compared to flood coolant and dry machining respectively. They also concluded that this reduction in cutting force was caused by the better lubrication effects of the MQL approach. Other studies have investigated novel implementations in the MQL approach to achieve more effective machining. Vazquez et al. [29] applied MQL when micro-milling Ti-6Al-4V alloy to enhance the surface quality and dimensional accuracy of the machined micro-channel, and to decrease the tool wear. The authors found that MQL cooling significantly affected the dimensional accuracy. Another study performed by Li et al. [30] investigated the effectiveness of the MQL approach in near micro-milling when compared to the dry condition. Experiments were conducted using hot work die steel as a workpiece material with a 0.6-mm diameter end mill, and micro-scale milling. They found that the use of MQL cooling noticeably extended the tool life as well as enhanced the surface roughness and the burr formation compared to the dry condition. Overall, all of these studies suggested that the use of MQL provided promising machining outputs.
Although the MQL technique has shown promising lubricating features, it has some problems such as clogging of chips/debris and an inefficient cooling capacity compared to the flood coolant, particularly when cutting difficult-to-cut materials. Several researchers have attempted to use different techniques to enhance the MQL’s cooling capacity. One of these techniques is MQL-nanofluid (MQLNF). Nanofluids are produced by dispersing nanoparticles into the MQL base fluid, which is typically oil or water. Nanoparticles are typically metals or metallic oxides. Various types of nanoparticles with excellent properties, such as aluminum oxide (Al2O3), carbon nanotubes (CNTs), TiO2, MoS2, C60, CuO, and diamond, have been used to improve the thermal conductivity and lubricity of an MQL coolant [31,32,33]. Nanoparticles have remarkable properties, such as high thermal conductivity and convection coefficients, which could improve the cooling and lubricating properties of an MQL coolant. Furthermore, by dispersing nanoparticles into the base fluid, the viscosity and thermal conductivity of an MQL coolant is enhanced [34]. The homogeneous distribution of nanoparticles into the base cutting fluid has been shown to be beneficial to the machining process as it helps to decrease the friction induced at the tool/chip interface [35].
Huang et al. [36] investigated the influence of adding multi-walled carbon nanotube (MWCNT) nano-additives to an MQL coolant during the grinding of NAK80 mold steel. The study found that nanofluid enhanced the grinding performance in terms of grinding temperature, surface roughness, and grinding forces compared to dry machining and pure MQL. Shen et al. [37] used water-based Al2O3 and diamond nanofluid in the grinding process. They found that using nanofluid reduced the grinding temperature and grinding force and improved the surface roughness. More recently, Shakti et al. [38] evaluated the machining performance of Inconel 718 experimentally using flood coolant, MQL, and MQL-nanofluid. They found that MQL-nanofluid significantly reduced the tool wear and coefficients of friction. They also reported that the use of MQL-nanofluid minimized the cutting forces as a result of the tribological aspect of the nanoparticles. Other studies have concentrated on the micro-machining processes. Lee et al. [39] performed experiments with micro-drilling on 7075-T6 aluminum alloy using nanofluid with both Al2O3 nanoparticles and nanodiamond. They found that applying MQL-nanofluid decreased the cutting force and the torque, and efficiently reduced the burr formation around the drilled holes. This was also confirmed by Jung et al. [40] when conducting micro-drilling experiments on aluminum using an MQL-nanofluid. They found that using an appropriate amount of nanofluid could reduce the machining force, tool wear, and burr formation. Jung et al. [41] implemented the MQL-nanofluid using nanodiamond particles to conduct the micro-drilling process on titanium alloy. They observed that the MQL-nanofluid increased the number of drilled holes, reduced the drilling torques and thrust forces, and reduced the remaining chips and burrs. They also reported that the use of MQL-nanofluid minimized the cutting forces due to the tribological aspect of the nanoparticles.
The above studies provide evidence that the MQL-nanofluid approach can be an effective alternative sustainable cooling strategy to conventional cutting fluid strategies. MQL-nanofluid has not, however, been extensively studied for the micro-drilling of Inconel 718 superalloy. Therefore, the current study chose to explore the machining performance of MQL-nanofluid in the mechanical micro-drilling of Inconel 718 superalloy in terms of thrust forces, tool wear, and burr formation, and to compare it to pure MQL cooling and flood coolant.
2 Experimental methodology
2.1 Workpiece material
The micro-drilling experiments were performed on a square plate of Inconel 718 superalloy with dimensions of 75 × 75 mm and a thickness of 2.08 mm. The Inconel 718 superalloy had been annealed at 1700–1850 °F. The workpiece material plate was supplied by Rolled Alloys Canada. The chemical composition and mechanical properties of the Inconel 718 superalloy at room temperature are provided in Tables 1 and 2 respectively [42]. This alloy is used in airplane engine gas turbine applications because of its properties, such as high performance at elevated temperatures and corrosion resistance.
2.2 Micro-drilling test
Drilling experiments were conducted using a CNC Haas milling machine. The tungsten carbide micro-drill is one of the most popular micro-drill bits. It is usually used in mechanical micro-drilling operations due to its outstanding mechanical properties, such as high hardness, higher melting point, and high wear resistance [43]. In this work, a solid tungsten carbide drill bit of 0.9-mm diameter was used for the micro-machining trials. This drill had a point angle of 140°. Additionally, this drill was made such that the shank diameter of the drill bit was 3 mm and had 2 flutes. In this study, the cutting speed was 5540 RPM and the feed rate was 39.878 mm/min (1.57 in./min) as recommended by the tool supplier [44]. A peck depth of 0.1 mm was employed in performing this micro-drilling process to improve tool life. Furthermore, 5% TRIM MicroSol 690XT high-lubricity, semi-synthetic, and micro-emulsion oil was used as a cutting fluid during the flood micro-drilling tests. Also, an external minimum quantity lubrication (MQL) system was used during the MQL micro-machining tests (Fig. 1). ECOLUBRIC E200 vegetable oil (rapeseed oil) was employed as a base cutting fluid of MQL. This vegetable oil is confirmed as being environmentally friendly and has a biodegradability of 90% over 28 days [45]. Compressed air was mixed with the base cutting fluid, which was based in the nozzle. The mist was delivered to the drilling zone with a base fluid volume flow rate of 60 ml/h and an air pressure of 0.5 MPa. The MQL nozzle was located at 45 degrees to ensure that the mist was delivered over the entire drilling zone. A schematic diagram of the experimental setup is shown in Fig. 1, and the experimental cutting conditions are shown in Table 3. To prepare the MQL-nanofluid, aluminum oxide gamma nanoparticles (Al2O3) were used as nano-additives. This type of nanoparticle was used due to its superior tribological properties and antitoxic aspects. These nanoparticles are 18 nm in diameter, have a purity of 93%, and specific surface area of 138 m2/g. The nanoparticles were dispersed into a vegetable oil with a fraction weight of 4 wt% as used in a previous work [31]. An ultrasonic device was used for dispersing the nanoparticles into the base fluid over a period of 3 h at 60 °C (see Fig. 2). After that, a magnetic stirrer was employed to stir for 30 min to confirm that the nanoparticles were fully dispersed into the resultant nanofluid. Furthermore, to enhance the stability of the resultant nanofluid and make it more hydrophilic, 0.2 mg of sodium dodecyl sulfate was added as a surfactant. In the current study, a standard procedure was regulated in order to decrease any environmental concerns or hazards when applying the MQL-nanofluid cooling. In addition, certain safety regulations were followed during the experimentation phase to retain a specific health and safety level in the lab to avoid any environmental concerns or health hazards.
Three different cooling/lubrication techniques were applied in this work: flood, MQL, and MQL-nanofluid. For each micro-drilling experiment, 30 micro-holes were drilled in the same workpiece for a total of 90 micro-holes drilled using three different tungsten carbide drill bits. Furthermore, a scanning electron microscope (SEM) and a high-resolution microscope were used to investigate and analyze the burr formation and tool flank wear. The maximum flank wear (VB) was determined, as illustrated in Fig. 2, after drilling each set of five holes. A dynamometer connected to the data acquisition system was used to record the thrust and torque force components generated during the micro-drilling of each hole (Fig. 3).
Flank wear measurements [46]
3 Results and discussion
This study performed micro-drilling on Inconel 718 superalloy to compare the effects of using flood, MQL, and MQL-nanofluid on thrust forces, tool wear, and exit burr formation. The results are discussed in the following sections.
3.1 Thrust forces
Figure 4 shows the measured drilling thrust forces with respect to the drilling time when applying MQL. The peaks on the thrust force curve result from the peck drilling process that was activated during each drilling operation to preserve the drill tool. The thrust force increased as the drill bit entered the material and then stabilized during the drilling process. As the drill bit exited the material, the force decreased steeply. The drilling thrust forces were averaged per 30 holes and plotted. The average thrust forces for all the micro-drilling experiments are presented in Fig. 5. The average thrust forces when using flood coolant were higher than those for pure MQL and MQL-nanofluid. However, the use of MQL-nanofluid showed a lower average thrust force compared to both flood and pure MQL. The lower thrust forces in MQL-nanofluid cooling could be due to the superior tribological aspects of nanoparticles where the spherical nanoparticles act as a spacer between the margin edges of the drilling tool and the inner surface of the drilled hole, thereby reducing the friction (Fig. 6). Also, when applying the MQL-nanofluid, the nanofluid mist might be able to easily penetrate the tool-work material interface and improve the lubrication, and as a result to reduce the thrust force.
3.2 Tool wear
Inspecting small drills to evaluate the flank tool wear is a challenge due to the micro-scale of the drill edge. Figure 7 shows the flank wear progression during the micro-drilling process under the three cooling techniques (flood, MQL, and MQL-nanofluid). For all cooling approaches, the flank wear increased slightly as the number of drilled holes increased. However, the flood coolant showed higher flank wear compared to the pure MQL and MQL-nanofluid. High tool wear progression on the flank face was observed when flood coolant was used because flood coolant could not easily penetrate the micro hole due to its small size and therefore could not reduce the high temperature. Therefore, due to the friction and high temperature, the flood coolant provided relatively higher flank wear and tear on the flank face. On the other hand, the MQL mist may be able to penetrate the small hole; while the drilling operation was performed, the MQL penetrated the drilled hole and formed a thin lubrication film between the inner surface of the drilled hole and the tool. The lowest tool wear observed with MQL-nanofluid compared to flood and pure MQL can be attributed to the formation by nanofluid of a tribo-film between the cutting tool and the inner drilled hole. This tribo-film reduces the rubbing action as a result of the rolling effect, thereby reducing the induced friction (Fig. 6). In addition, adding nanoparticles to the MQL base fluid enhances the thermal conductivity of the MQL-nanofluid due to the spherical shape, nano-size, and high thermal conductivity of the Al2O3 nanoparticles. Thus, the MQL-nanofluid was more effective than pure MQL in reducing the cutting temperature in the drilling zone.
Furthermore, there was indication of fracture variation on the drilling tool edge for all three coolants. Fractures could be due to the existence of high stress in the cutting zone. Scanning electronic microscope (SEM) images of the drills after drilling 30 holes in Inconel 718 alloy using the three cooling strategies are shown in Figs. 8 and 9. In this study, the condition of the drill flank face and the corner edge was also investigated. The tool used in the MQL-nanofluid cooling process showed less abrasion wear and less fractured edges compared to the pure MQL and flood coolant after drilling 30 holes. Less outer corner wear was also noticed in the case of MQL-nanofluid compared to flood and pure MQL (Fig. 8). These results can be attributed (1) to the enhancement in thermal conductivity of the base fluid in nanofluid after dispersal of 4 wt% nanoparticles, which increases the heat dissipation rate and (2) to the excellent tribological effect of nanoparticles, which minimizes the friction and the rubbing between tool and material surface. Figure 8 shows SEM images of the micro-drilling tool after the drilled 30 holes involving three cooling approaches. The drill bit surface looks cleaner (less adhered material) in case of flood and MQL-nanofluid cooling compared to the drill bit surface after using the pure MQL. This could be due to the reduced heat in flood and MQL-nanofluid which prevent debris in the drilled hole from adhering to the hot tool.
In terms of corner edge, excessive damage in the tool corner was observed in the case of flood cooling compared to pure MQL and MQL-nanofluid as shown in Fig. 8. The use of MQL-nanofluid showed the lowest corner edge damage. This is most probably because of the ball bearing effect of the nanoparticles, which decreases the rubbing action between the cutting tool edge and the inner surface of the drilled hole, thereby reducing the friction. According to Nam [26], the weight concentration of 0.4 wt% nanoparticles in nanofluid, as used in this study, should be sufficient for activating the rolling effect.
The degree of adhered material from the workpiece to the chisel edge and drill margin side was also investigated as shown in Fig. 9. Some chips adhered to the drill in the case of using pure MQL due to its inefficient cooling ability. This reveals that high temperature promotes adherence of small debris. Meanwhile, in the case of using MQL-nanofluid, chip adhesion and abrasion wear on the chisel edge were considerably reduced when compared to the flood and pure MQL. However, a small built-up edge (BUE) was observed in the case of using pure MQL and MQL-nanofluid. The formation of BUE is most likely due to the chemical reactivity of such superalloy. Furthermore, the cutting temperature is relatively high when using pure MQL and MQL-nanofluid compared to flood coolant. When the temperature of the removed chips or debris is very high, it promotes to adhere to cutting edge. The BUE is not permanently situated on the drill cutting edge but periodically becomes detached. Overall, the application of MQL-nanofluid reduced the wear and fractures on both the chisel and margin sides after drilling 30 holes compared to flood and pure MQL.
3.3 Burr formation
Figure 10 shows the SEM images of the fifth drilled hole illustrating the diameter of the exit burr in the three cooling techniques. The resultant effects of the three lubrication methods on the drilled holes precision were determined through dimensional measurements of the exit burr formation. When using MQL and MQL-nanofluid, burrs cut around the circumference of the drilled hole and the circularity errors were small compared to using flood coolant, as seen in Fig. 10. This is most likely due to the deficiency in cooling ability when using flood cooling, as the cutting fluid is unable to enter the nano-drilled hole. On the other hand, the MQL mist is able to penetrate the drilled hole to reduce the rubbing between the tool and the inner surfaces, thereby reducing the cutting heat.
Figures 11, 12, and 13 show the burr height measurements in all three cooling strategies. Flood cooling provided the largest burr height. MQL-nanofluid showed the lowest burr height (200 μm), followed by pure MQL (208 μm), then the flood coolant (241 μm). The burr height was reduced by using the MQL-nanofluid approach because the nanoparticles have the advantage of activating the rolling ball bearing effect between the tool and work material. Also, the edge tool has indirect effect on the drilled hole quality. The tool edge was sharper and better when using the MQL-nanofluid than when using pure MQL and flood coolant; as a result, the chips were cut better. Although the measurements of the burr width were not determined in this paper, it can be seen from the SEM images that the burr width using flood coolant was larger and more irregular. It can be concluded that the accuracy was significantly affected by the lubricant technique being used. The use of MQL-nanofluid improved the accuracy of drilled holes by reducing both circularity errors and burr height.
3.3.1 Deburr
Exit burr formation was observed in all trials; Section 3.3 was focused on exit burr formation because it needs a costly removing process (deburr process). Numerous companies remove burrs produced during the drilling process by using traditional methods, such as special brushes, tumbling, and vibratory deburring. The deburring process adds further steps to the entire manufacturing operation as well as additional labor costs. The deburring step can take minutes or hours depending on the type of material being drilled and the deburring method that is used. Eliminating this step in the manufacturing process would thus save a significant amount of time and money. Burrs with more height can impact the enclosure’s longevity, functionality, effectiveness, and safety [47], so sometimes it is necessary to perform the deburring process to achieve the desired product. The use of the MQL-nanofluid decreased the need to perform the deburring operation when compared to pure MQL and flood coolant because the MQL-nanofluid resulted in the lowest burr height.
4 Conclusions
In this work, an experimental evaluation of the machinability of Inconel 718 superalloy in the MQL-nanofluid micro-drilling process was made using Al2O3 nanoparticles. The results revealed that using MQL-nanofluid reduced the thrust forces compared to the pure MQL and flood coolant. It was shown that by using MQL-nanofluid when performing micro-drilling operations on Inconel 718 superalloy, there was a reduction in the flank wear, the outer corner damage, and the unexpected breaking of the micro-drilling tool. MQL-nanofluids with Al2O3 can penetrate the drilling zone more efficiently, allowing the nanoparticles to create a ball bearing effect between the tool and the material that could significantly reduce the friction and the thrust forces. In addition, the results indicated that the use of MQL-nanofluid improved the micro-drilling hole quality and decreased the burr formation. By applying this lubrication technique to Inconel 718 micro-drilling, burrs around the drilled holes were considerably reduced. The use of MQL-nanofluid improved the accuracy of drilled holes by reducing both circularity errors and burr height. This was due to the use of nanofluid, which enhanced the tribological and lubrication effects. It can be concluded that the MQL-nanofluid approach is promising in terms of machining outputs and sustainability.
References
Metals HS Inconel 718 for aerospace engine applications, Heanjia Super Metals Co. Ltd., 04 04 2016. [Online]. Available: https://super-metals.com/news/inconel-718-for-aerospace-engine-applications/. [Accessed 6 July 2019]
Beer N, Oezkaya E and Biermann D (2014) Drilling of Inconel 718 with geometry-modified twist drills, in Procedia CIRP - New Production Technologies in Aerospace Industry - 5th Machining Innovations Conference (MIC)
Sharif S, Abd Rahim E (2007) Performance of coated-and uncoated-carbide tools when drilling titanium alloy-Ti6Al4V. J Mater Process Technol 185(1–3):72–76
Hegab H, Kishawy H (2018) Towards sustainable machining of Inconel 718 using. J Manuf Mater Process 2(3)
Percin M, Aslantas K, Ucun I, Kaynak Y, Cicek A (2016) Micro-drilling of Ti–6Al–4V alloy: the effects of cooling/lubricating. Precis Eng 45:450–462
M. I. S. Co. Metalworking, MSC Industrial Supply Co., 2019. [Online]. Available: https://www.mscdirect.com/betterMRO/metalworking/micro-drilling-what-you-need-know. [Accessed 10 July 2019]
Nirala CK, Jain Y, Sharma S and Agrawal A (2017) Mechanical micro-drilling and micro-EDM-drilling: a comprehensive and comparative evaluation, in 10th international conference on precision, Meso, Micro and Nano engineering (COPEN-10), India
Bassoli E, Denti L, Gatto A, Iuliano L (2016) Influence of electrode size and geometry in electro-discharge drilling of Inconel 718. Int J Adv Manuf Technol 86(5–8):2329–2337
Feng Y, Guo Y, Ling Z, Zhang X (2019) Micro-holes EDM of superalloy Inconel 718 based on a magnetic suspension spindle system. Int J Adv Manuf Technol 101(5–8):2015–2026
Tanjilul M, Ahmed A, Kumar AS, Rahman M (2018) A study on EDM debris particle size and flushing mechanism for efficient debris removal in EDM-drilling of Inconel 718. J Mater Process Technol 255:263–274
Unune DR, Nirala CK, Mali HS (2019) Accuracy and quality of micro-holes in vibration assisted micro-electro-discharge drilling of Inconel 718. Measurement 135:424–437
D’Urso G, Maccarini G, Ravasio C (2014) Process performance of micro-EDM drilling of stainless steel. Int J Adv Manuf Technol 72:1287–1298
Khandekar S, Sanker M, Agnihotri V, Ramkumar J (2012) Nano-cutting fluid enhancement of metal cutting performance. J Mater Manuf Process 27:963–867
Amrita M, Srikant R, Sitaramaraju A (2014) Performance evaluation of nanographite-based cutting fluid in machining process. J Mater Manuf Process 29:600–605
Li B, Li C, Zhang Y, Wang Y, Jia D, Yang M, Zhang N, Wu Q, Han Z, Sun K (2017) Heat transfer performance of MQL grinding with different nanofluid for Ni-based alloy usingvegetable oil. J Clean Prod 154:1–11
Processors C CarbideProcessors.com, Carbide Processors Inc., 2019. [Online]. Available: http://www.carbideprocessors.com/pages/machine-coolant/bacteria-in-machine-coolant.html. [Accessed 14 7 2019]
Dixit U, Sarma D and Davim JP (2012) Major concerns in using cutting fluids, in Environmentally Friendly Machining, London, SpringerBriefs in Applied Sciences and Technology, pp. 10–11
Boswell B, Islam M, Davies J, Ginting Y, Ong A (2014) A review identifying the effectiveness of minimum quantity lubrication (MQL) during conventional machining. Int J Adv Manuf Technol 72:919–933
Dureja J, Singh R, Singh P, Dogra M, Singh R (2015) Performance evaluation of coated tool in machining of stainless steel (AISI 202) under minimum quantity lubrication (MQL). Int J Precis Eng Manuf Green Technol 2:123–129
Eltaggaz A, Zawada P, Hegab H, Deaib I, Kishawy H (2018) Coolant strategy influence on tool life and surface roughness when machining ADI. Int J Adv Manuf Technol 94:3875–3887
Davim J, Sreejith P, Silva J (2007) Turning of brasses using minimum quantity of lubricat (MQL) and flooded lubricant conditions. Mater Manuf Process 22:45–50
Eltaggaz A, Hegab H, Deiab I and Kishawy H (2017) On using nano-cutting fluid when maching austempered ductile iron," in Proceedings of the 26th CANCAM, Victoria, British Columbia, Canada
Emami M, Sadeghi M, Sarhan A (2013) Investigating the effects of liquid atomization and delivery parameters of minimum quantity lubrication on the grinding process of Al2O3 engineering ceramics. J Manuf Process 15:374–388
Lee P, Nam TS, Li C and Lee SW (2011) Environmentally-friendly nano-fluid minimum quantity lubrication (MQL) meso-scale grinding process using nano-diamond particles, in Manufacturing Automation (ICMA), DOI: https://doi.org/10.1109/ICMA.2010.27
Bhowmick S, Lukitsch M, Alpas A (2010) Dry and minimum quantity lubrication drilling of cast magnesium alloy (AM60). Int J Mach Tools Manuf 50(5):444–457
Nam J, Sang Won L (2017) Machinability of titanium alloy (Ti-6Al-4V) in environmentally-friendly micro-drilling process with nanofluid minimum quantity lubrication using nanodiamond particles. Int J Precis Eng Manuf Green Technol 5(1):29–53
Aslantas K and Çiçek A (2018) The effects of cooling/lubrication techniques on cutting performance in micro-milling of Inconel 718 superalloy, in 8th CIRP Conference on High Performance Cutting, Elsevier Ltd. , Budapest, Hungary
Sun J, Wong Y, Rahman M, Wang Z, Tan C (2016) Effects of coolant supply methods and cutting conditions on tool life in end milling tiyanium alloy. J Mach Sci Technol 10(3):355–370
Vazquez E, Gomar J, Ciurana J, Rodríguez CA (2015) Analyzing effects of cooling and lubrication conditions in micromilling of Ti6Al4V. J Clean Prod 8:906–913
Li K, Chou S (2010) Experimental evaluation of minimum quantity lubrication in near micro-milling. J Mater Process Technol 210(15):2163–2170
Eltaggaz A, Hegab H, Deiab I, Kishawy H (2018) Hybrid nano-fluid-minimum quantity lubrication strategy for machining austempered ductile iron (ADI). Int J Interact Des Manuf 12(4):1273–1281
Kishawy H, Hegab H, Deiab I, Eltaggaz A (2019) Sustainability assessment during machining Ti-6Al-4V with nano-additives-based minimum quantity lubrication. J Manuf Mater Process 3(61)
Huang W-T, Wu D-H, Chen J-T (2016) Robust design of using nanofluid/MQL in micro-drilling. Int J Adv Manuf Technol 85(9–12):2155–2161
Hajiyan M, Ebadil S, Mahmud S, Biglarbegian M, Abdullah H (2018) Experimental investigation of the effect of an external magntic field on the thermal conductivity and viscosity of Fe3O4-glycerol. J Therm Anal Calorim 133:1–14
Eltaggaz A and Deiab I (2018) The effect of nanoparticle concentration on Mql performance when machining Ti-6Al-4V titanium alloy, in Conference: 2018 Canadian Society for Mechanical Engineering (CSME) International Congress, Toronto
Huang WT, Liu WS, Wu DH (2016) Investigations into lubrication in grinding processes using MWCNTs nanofluids with ultrasonic-assisted dispersion. J Clean Prod 137:1553–1559
Shen B, Shih A, Tung S (2008) Application of naofluids in minimum quantity lubrication grinding. Tribol Trans 51:730–737
Shakti C, Eltaggaz A, Deiab I, Khanafer K and Abdul-latif A (2019) Investigation of hybird MQL-nanofluid performance when machining Inconel 718 super-alloy, in The Canadian Society for Mechanical Engineering (CSME) , London, Ontario, Canada
Lee P-H, Nam J, Li C, Lee S (2012) An experimental study on miro-grinding process with nanofluid minimum quantity lubrication (MQL). Int J Precis Eng Manuf 13(3):331–338
Jung SN, Pil-Ho L, Sang WL (2011) Experimental characterization of micro-drilling process using nanofluid. Int J Mach Tools Manuf 51:649–652
Sub KJ, Woo KJ, Won LS (2017) Experimental characterization on micro-end milling of titanium alloy using nanofluid minimum quantity lubrication with chilly gas. Int J Adv Manuf Technol 91:2741–2749
R. A. Company, “Rolled Alloys,” 07 2012. [Online]. Available: https://www.rolledalloys.ca/shared-content/technical-resources/datasheets/718_DS_US_EN.pdf. [Accessed 25 06 2019]
Hasan M, Jingwei Z, Zhengyi J (2017) A review of modern advancements in micro drilling techniques. J Manuf Process 29:343–375
“sowatool,” SOWA Metalworking Solutions, [Online]. Available: http://www.sowatool.com/Catalogue/4/260. [Accessed 25 06 2019]
Deiab I and Raza S (2014) Analysis of lubrication strategies for sustainable machining during turning of titanium Ti-6Al-4V alloy, in CIRP
Eltaggaz A, Deiab I (2019) Comparison of between direct and peck drilling for large aspect. Int J Adv Manuf Technol 102:2797–2805
Americal Products, Americal Products, 08 06 2017. [Online]. Available: https://amprodmfg.com/what-is-deburring/. [Accessed 3 10 2019]
Funding
This work was fully funded by the Kuwait Foundation for the Advancement of Sciences (KFAS) project (PR18-145C-01).
Author information
Authors and Affiliations
Corresponding author
Additional information
Publisher’s note
Springer Nature remains neutral with regard to jurisdictional claims in published maps and institutional affiliations.
Rights and permissions
About this article
Cite this article
Khanafer, K., Eltaggaz, A., Deiab, I. et al. Toward sustainable micro-drilling of Inconel 718 superalloy using MQL-Nanofluid. Int J Adv Manuf Technol 107, 3459–3469 (2020). https://doi.org/10.1007/s00170-020-05112-4
Received:
Accepted:
Published:
Issue Date:
DOI: https://doi.org/10.1007/s00170-020-05112-4