Abstract
Nowadays, the utilization of natural fiber-reinforced polymeric composites has increased due to its eco-friendly nature. Among all the natural fiber reinforced polymer composites, bamboo fibers have caught attention as reinforcement in the polymeric matrix due to its superior mechanical properties, sustainability, and recyclability. The bonding mechanism of the polymeric matrix, bamboo fiber reinforcement, and their interface plays a critical part in governing the properties and performance of the formed composite materials. Factors like moisture content and lignin tend to reduce the interfacial adhesion between matrix and reinforcement phases resulting in the formation of defects and loss of strength that degrades the quality of the composite materials. That is why the enhancement of interfacial bonding/adhesion is required to ensure optimal properties of bamboo reinforced composite materials. This article summarizes the chemical treatments and the interfacial agents such as mercerization, use of compatibilizers, and silane treatment that are employed to enhance the interfacial adhesion which eventually leads to an improvement of strength in tension, stiffness, flexural strength, interfacial shear strength and so forth.
Access provided by Autonomous University of Puebla. Download chapter PDF
Similar content being viewed by others
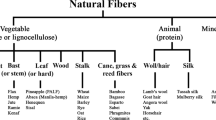
Keywords
- Bamboo fiber
- Bonding mechanism
- Interfacial adhesion
- Mercerization
- Compatibilizer
- Silane treatment
- Interfacial shear strength
1 Introduction
With the advent of nanotechnology, the nanoparticle-reinforced composites (called nanocomposites) have been developed as advanced materials [1,2,3,4,5,6]. Likewise, natural fibers have shown great potentials nowadays in producing eco-friendly green composites for wider areas of applications [7,8,9,10,11]. They are known for their biodegradability and enhanced properties. Among the natural plants, bamboo is quite advantageous because of its’ high growth rate, ability to fix carbon-di-oxide emission to the environment, lightweight, and high specific strength [12]. Bamboo fibers caught special attention owing to their longevity, mechanical characteristics, recyclability as well as their utilization as reinforcement in composite materials [13]. Earlier work on bamboo protective coatings with phenolic, epoxy, and styrenated coatings showed perfect adhesion between bamboo fiber and coating materials. However, work reported on the bamboo fiber-reinforced composite is very limited and a thorough study is required [14]. It has been suggested that some of the issues pose obstacle to the widespread use of bamboo fibers as reinforcement of composite matrix such as low moisture resistance, inadequate mechanical and chemical characteristics, current extraction procedure of bamboo fiber from bamboo culm is not suitable for manufacturing business [13]. The study found that the poor interfacial bond amid the matrix and bamboo fiber leads to the de-bonding of the composite on aging which results in poor mechanical and chemical properties. Hence, arises the concern for improving the interface of the bamboo fiber – composite matrix to meet the required property requirements [14].
2 Bamboo Structure
Bamboo culms are hollow, and several diaphragms divide each culm from inside, which are observed like rings from outside. The portion between rings is known as “Internode” where branches grow [12]. The bamboo culm contains vascular bundles that are attached in parenchyma tissue. The vascular bundles are kept in the longitudinal direction by the parenchyma tissue. It is observed that a high amount of vascular bundles is present near the outside culm of the bamboo whereas their percentage reduces on the inner side culm [13]. The fiber strand comprises of various fundamental fibers (mostly hexagonal and pentagonal shape) where nano-fibrils are aligned and attached with hemicellulose and lignin. Vascular bundles delimit culm strength. Hence, a suitable method is required to isolate the parenchyma tissue from the fiber strands and vascular bundles without any detrimental impact on the fibers which are extracted [13]. Figure 1 exhibits the components of a bamboo culm.
a Culm of a bamboo, b Bamboo culm cross-sectional view, c Vascular bundle, d Fiber strand, e Elementary fibers, f Model of polylamellae structure of bamboo [15]
2.1 Bamboo Fibers (BF)
Bamboo has the combined characteristics of grass and wood. They are quite robust (specifically longitudinally) because a resilient fiber bundle infiltrates their body from the base to the topmost part albeit bamboo pulp being shorter than ∼2 mm. So, the ordinary length of bamboo fiber is around 2 mm plus the regular diameter is 10–20 µm [16]. Hemicellulose, lignin, and cellulose consist of bamboo. Around half of the total chemical constituents are cellulose and hemicellulose. They are present as holo-cellulose. Lignin is also present in abundance. It provides the role of a binder and performs as the matrix for the cellulose fibers. Lignin participates in load-bearing actions as a fundamental part of the composite [17]. Other than these two constituents, bamboo contains starch, de-oxidized saccharide, fat, and protein [18]. Bamboo fibers also referred to as ‘natural glass fiber’ are getting more and more consideration from the researchers [19].
3 Bamboo Fiber Reinforced Polymer Composites
In general, BF is used as reinforcement for polymer composites. Inherently, BF is hydrophilic, while polymers are hydrophobic. Owing to the incompatibility in terms of their polarity structures, it is quite difficult to formulate a feasible composite having superior interfacial bonding [16]. Various approaches i.e. physical treatment (solvent extraction, heat treatment), physio-chemical treatment (laser, ultra-violet bombardment), and chemical modification have been endeavored to make lingo-cellulosic molecules of fiber and hydrocarbon-based polymers compatible to each other [20, 21]. It is well established that bamboo fiber can be used as a reinforcement for thermosetting composites, thermoplastic composites, rubber/elastomeric composites, and biocomposites.
3.1 Bamboo Fiber Reinforced Thermosetting Composites
These composites are composed of BF fibers which are large in size. Post-curing under a particular load is required for the preparation of the thermosetting composites. Phenolic resin, epoxy, and unsaturated polyester are the most commonly used thermoset polymer matrices for this type of composite [22].
3.2 Bamboo Fiber Reinforced Thermoplastic Composites
Unlike thermoset composites, short BF fibers are used for thermoplastic composites. Polymers (petroleum-based) that are chosen to be used as matrix material are polypropylene (PP), polyethylene (PE), nylon, and polyvinyl chloride (PVC). The short fibers are dispersed in the matrix in a random orientation. As a result, they exhibit isotropy [22].
3.3 Bamboo Fiber Reinforced Rubber/Elastomeric Composites
Rubber/elastomeric composite reinforced with short BF has several advantages including design flexibility, stiffness, damping, process economy [23].
3.4 Bamboo Fiber Filled Bio Composites
The use of BF in biocomposites is a recent practice. Biomass-derived biopolymers are utilized as matrix material. The most commonly used biopolymer matrices are polylactic acid (PLA), polybutylene succinate (PBS), protein, polycaprolactone (PCL), and starch [24].
4 BF-Polymer Matrix Interfacial Bonding Mechanism
The property and performance of any plant fiber (including bamboo fiber) composite rely on the bonding mechanism at the interface. The interface area of the matrix and the reinforcement has a prime role to play in controlling the performance of the material. The composite interface is created by the coupling of the fiber and matrix, which is, in essence, a region of structural, compositional, and property gradients, usually ranging in breadth from one atomic layer to many micrometers. Processes occurring at the different levels of the interface (macroscopic, atomic, and microscopic) are closely related. To accurately comprehend the interfacial phenomena, it is extremely important to understand the order of incidents happening at mentioned levels. Stress transfer between matrix and bamboo fiber is controlled by the interfacial region [25]. The molecular synergy at the interface as well as the thickness and strength of the interfacial region regulate the effectiveness of load transference [26].
Inter-diffusion, electrostatic adhesion, chemical reactions, and mechanical interlocking are the most common interfacial bonding mechanisms. All of these mechanisms are mutually responsible for adherence and typically one of them prevails [25]. Due to Van der Waals forces or hydrogen bonding, intimate intermolecular interaction occurs between fiber molecules and the polymer that causes inter-diffusion [22]. Adsorption and diffusion are two sub-stages of the adhesion mechanism. The first stage is governed by spreading and penetrating while the second stage indicates good wetting leading to inter-diffusion of fiber and matrix. The fiber-matrix compatibility controls the magnitude of the diffusion process [27]. For electrostatic adhesion, two opposite charges are formed at the interfacial region. Those are responsible for the adhesion of fiber and matrix. The chemisorption reactions form chemical bonds (ionic bond and atomic bond) between matrix and fiber (Fig. 2).
The mechanical interlocking phenomenon occurs when the holes, crevices, or other irregularities of the fiber are infiltrated by the matrix and the fibers get locked to the matrix mechanically [25]. It is seen that increasing surface roughness, increases the contact area for adhesion thus favoring mechanical interlocking [27]. Moreover, increasing mechanical interlocking displays potential improvement of bonding mechanism [25].
5 Controlling Factors of Interfacial Characteristics of BF Composites
5.1 Moisture Absorption
Under natural humidity situations, BF soaks a substantial quantity of moisture and thus it is known as a hydrophilic material. Moisture sorption hysteresis of BF is comparable to other natural fibers for instance hemp and flax [28]. The mechanical performance of the bamboo is affected by the absorption capability of BF. Moreover, poor adhesion between BF and water-repelling polymers (matrix) is observed due to moisture absorption [16]. Moisture has a detrimental effect on the polymeric matrix and the fibers. Moreover, the matrix-fiber interface can also be impaired due to the presence of moisture. Ultimately, poor stress transference from the matrix to reinforcement is observed. The cycle of deterioration begins when the cellulose fibers are swollen. It produces stress at the interface. As a result, micro-cracks appear in the matrix around the swollen fibers exacerbating the water absorption and weakening the interface. Intermolecular hydrogen bonding is formed with the fibers due to the absorbed water and thus interfacial adhesion is reduced. At the same time, water leaches out the soluble constituents from fibers. This occurrence eventually results in de-bonding at the interface. The study showed that due to moisture absorption extensibility of BF is increased but elastic modulus is decreased whereas the tensile strength remained unaffected. The effect of moisture absorption on interfacial shear strength (IFSS) was inspected for bamboo fiber—vinyl ester matrix composite. The IFSS in 20°C and 60% humidity was only 50% of what was achieved under dry conditions. For composites developed under 80–90% humidity conditions, negligible interfacial strength was observed. Significant damage to interfacial shear strength was observed for BF-vinyl ester matrix composite due to water absorption. Ultimately, the IFSS was reduced by 38% [22].
5.2 Presence of Lignin
Bamboo fiber contains 32.2% lignin approximately, which is greater than the percentage of lignin in other natural fibers [17]. Studies have found that bamboo strips containing lignin lead to ineffective interfacial adhesion [22]. Defects are formed due to poor interfacial adhesion and as a result, the composite lacks strength [16].
6 Treatments to Enhance Interfacial Adhesion of BF Reinforced Composite
Interfacial bonding/adhesion is the prime concern for producing BF reinforced composites having optimal properties. Various studies have conducted engineered enhancement of interfacial adhesion between BF and matrix materials. In turn, it leads to an effective increase in composite properties like tensile strength, flexural strength, interfacial shear strength (IFSS), stiffness, and many more. Different chemical treatment procedures, interfacial agents, filler materials, and bonding agents affecting the enhancement of the interfacial adhesion will be discussed below.
6.1 Alkaline Treatment or Mercerization
Alkaline treatment, namely mercerization, removes lignin and other unwanted constituents and thus helps to reduce the acrid aroma of BF. It forms cellulose micro- or nanocrystals that have irregular fiber surfaces due to the removal of amorphous cellulose from the cellulose fiber bundle. Hydroxyl groups in bamboo fiber are activated due to mercerization. The enlarged surface area results in better interfacial adhesion. Ultimately, the tensile and thermal properties of the composite are improved [22]. Usually, a NaOH solution (aqueous) is used to perform this treatment. The study showed that PLA (polylactic acid) composites containing delignified BF provide better tensile strength and bending modulus than a PLA composite with untreated BF. This improvement was ascribed to the surface alteration and the enhancement of the interface adherence between the BF and PLA matrix [29]. However, it is observed that superfluous alkali treatment results in excessive delignification that results in weakening and deterioration of the fiber being treated [25]. Alkali treatment (greater than 15%) proved to be detrimental to composite properties [30, 31].
6.2 Compatibilizer or Maleated Coupling Agents
Maleated coupling agents showed promising results in enhancing interfacial adhesion. The hydroxyl group of the plant fiber is removed by the maleic anhydride (MAH) group and thus reducing its’ hydrophilic tendency [25]. Additionally, a C–C bond is formed with the matrix. Improved adhesion is attained by the creation of covalent bonds at the interface between coupling agents and fibers along with molecular entanglement amid polymeric matrix and coupling agents [32]. Due to this treatment, the surface energy of fibers and matrix become closer resulting in improved wettability and enhanced adhesion at the interfacial region [33]. As a compatibilizer/coupling agent for the BF/PP composite, maleated polypropylene (PP) is the most frequently used. Studies showed that incrementing the content of MAH results in a little improvement in impact strength and modulus but the augmented degree of maleation increases tensile strength substantially [34].
Bamboo pulp fiber-reinforced composites showed improved strength and modulus but reduced toughness due to the addition of maleic anhydride grafted PHBV8 (Poly(3-hydroxybutyrate-co-3-hydroxyvalerate)) as compatibilizer. Isocyanates, MDI (Methylene diphenyl diisocyanate) are common compatibilizer used in BF reinforced composites. The fracture surface of PHBV8/bamboo pulp fiber composites with and without pMDI (Poly methylene diphenyl diisocyanate) is shown in Fig. 3. Without pMDI, a significant amount of fiber pullout is detected. This proved inadequate interfacial adhesion. However, interfacial bonding becomes strong due to the presence of pMDI and fracture surfaces show that all fibers are broken. Improved interfacial adhesion reduces the chance of fiber de-bonding and hinders the fiber pull out. Moreover, it enables higher stress transference between fiber and matrix and thus improves the modulus and the tensile strength of the composites [22]. The toughness of the composite is diminished owing to the interruption of fiber pull out, a key energy dissipation source throughout the composite deformation [36]. Therefore, the addition of compatibilizer helps to improve flexural and tensile strength, while the ductility of the composite is reduced.
SEM images of tensile a, c and impact b, d fracture surfaces of PHBV8/bamboo pulp fiber (80/20 w/w) composite without pMDI a, b and with pMDI c, d [35]
6.3 Silane Treatment
Silane (SiH4) is an inorganic substance. Two reactive groups are present in silane coupling agent. The alkoxysilane group interacts with hydroxyl rich fiber while the other is left to react with the matrix. Silane tends to react with water (absorbs moisture) to form silanol. The formed silanol further reacts with the hydroxyl group integrated to the cellulose, hemicellulose, and lignin molecules in the filler through ether linkage with the elimination of water. In contrast, hydrophobic molecules of silane are capable of reacting with a polymer matrix [37]. Because of covalent bonding between fiber and matrix, the hydrocarbon chain formed by the silane restrains swelling of the fiber by getting entangled and cross-linking of the networks [33, 38]. Furthermore, the presence of hydrocarbon chains is anticipated to have an impact on the fiber wettability and chemical affinity of the matrix and thus enhancing interfacial properties [25]. The amine groups of 3-aminopropyl triethoxysilane are favorable for increasing the adhesion at the interface of PLA (Polylactic acid)/ BF composites [22].
To enhance fiber-matrix interface adhesion, numerous other physical and chemical procedures are utilized. Some of them are acetylation, benzoylation, acrylation, permanganate treatment, argon plasma treatments, etc. [22].
7 Scientific Studies and Research on Interface Enhancement of BF Reinforced Composites
7.1 Alkali Treatment on BF Reinforced Polyester Composites
Wong et al. [39] studied two types of bamboo fibers: treated with NaOH concentration (1, 3, and 5%) and untreated. Interfacial shear strength (IFSS) of the fiber with polyester matrix at dissimilar embedment length of fibers were also studied.
For the characterization of the morphology of the fiber (before and after the tests), SEM (Scanning Electron Microscopy) was utilized. Both strength and stiffness were increased according to the result. Besides, higher NaOH concentration and longer embedment length showed increased IFSS. Figure 4a, b shows the effect of NaOH concentration and fiber embedment length on IFSS.
a The outcome of fiber embedment length to IFSS for treated and untreated fibers. b The outcome of alkali treatment to IFSS at different fiber embedment length [39]
However, It is necessary to remember that enhancement will be saturated after a certain proportion of alkali treatment [39].
7.2 BF Filled Rubber Composites with Bonding Agents
Ismail et al. [23] studied the adhesion between BF and natural rubber by the addition of bonding agents. In this study, phenol–formaldehyde and hexamethylene tetra-amine were used as bonding agents. SEM characterization of the tensile fracture surface showed that the presence of the bonding agent resulted in better interaction between fiber and rubber matrix interfacial adhesion.
7.3 BF Reinforced Poly Lactic Acid (PLA) Composite with Micro-Fibrillated Cellulose (MFC)
The study of [40] showed that small addition (10%) of MFC obtained from the wood pulp with the PLA/BF composite gives enhanced fracture toughness due to better interfacial adhesion and intertwined MFC fibers prevent the progress of cracks through the interface. Figure 5 exhibits a representative stress–strain curve of PLA/BF/MFC, PLA/BF, and PLA resin composites.
Stress–strain profiles of PLA, PLA/BF and PLA/BF/MFC composites [40]
It is quite clear from the graph that the addition of MFC content with PLA/BF composite enhanced interfacial adhesion thus increasing bending strength and elastic modulus. Nevertheless, the increasing ratio is insignificant for the sample with MFC content over 10% in weight.
Figures 6a, b display the fracture surface of PLA/BF and PLA/BF/MFC composites. Countless fiber pullouts are observed for PLA/BF composites, which is detrimental for interfacial adherence between matrix and fiber while only a small number of fiber pullouts are detected in the case of PLA/BF/MFC.
Fractography of a PLA/BF (50:50) composite and b PLA/BF/MFC (50:40:10) composite [40]
Moreover, high interfacial shear strength (IFSS) is observed (Fig. 7) due to the addition of a minor quantity of MFC in PLA/BF composites that also prevents interfacial failure.
Interfacial Shear Strength of PLA composite and PLA/BF/MFC composite [40]
In the case of PLA/BF, as soon as a crack reaches bamboo fiber, it propagates alongside the interface giving low fracture toughness. Improvement of fracture toughness was observed due to the addition of MFC with PLA/BF composite since intertwined MFC prevents crack progression along with the interface. Consequently, no de-bonding occurs. Figure 8 shows the fracture toughness of PLA, PLA/BF, and PLA/BF/MFC composites.
Graphical representation of fracture toughness of PLA, PLA/BF and PLA/BF/MFC composites [40]
Another study by [41] showed the effect of alkali-soaking treatment, silane coupling treatment, and maleic anhydride grafting treatment of the cellulose fiber on the mechanical characteristics of bamboo cellulose fiber reinforced PLA composites. Improved strength and modulus were observed for alkali soaked composite in comparison to the untreated specimens. Enhanced impact toughness and ductility are observed by silane treatment which is are higher than those of PLA composite filled with pristine bamboo cellulosic fibers. Maleic anhydride grafting showed a moderate effect on ductility and rigidity. SEM observation as well as FTIR spectrum analysis concluded that interfacial interactions amid fibers and matrix were enhanced due to all the above-mentioned modifications.
7.4 BF Reinforced Unidirectional Epoxy-Based Composite
Wang et al. [42] studied epoxy-based composite reinforced with BF which are chemically treated with NaOH solution of 1, 4, and 7% concentration at room temperature causing an increase in tensile strength of the composite by 17.78, 45.24, and 28.92% respectively. The addition of NaOH solution removes pectin, hemicellulose, and part of the lignin of bamboo fibers [43]. As a result, a large number of micro-fibrils on the fiber surface are exposed ensuring promising interaction with the epoxy resin matrix. So, interfacial adhesion enhancement improves tensile performance. However, at 7% NaOH concentration, the micro-fibril structure was damaged and interfacial adhesion became weak.
Toughness is dominated by interfacial adhesion too. It was also observed that with an increasing percentage of NaOH solution (1, 4, and 7%), elongation at break of composites increased respectively by 15.92%, 23.32%, and 41.70%. Fracture surface morphology indicates that with the increase of NaOH percentage, the fiber pullout phenomenon reduces due to better interfacial adhesion. However, a 7% NaOH solution causes the formation of disordered micro-fibrils, which is harmful to interfacial performance. Figure 9 shows the interfacial morphology of BF reinforced epoxy-based composite treated with numerous alkali concentrations. As shown in Fig. 9a, complete fiber pullout from the matrix occurred displaying poor interfacial adhesion. Figure 9b indicates the dispersion of fibers and an effective increase in the surface area of the fiber leading to improved interface adhesion. Figure 9c shows that broken fibers are firmly fixed in the epoxy resin indicating a well-bonded interface. Figure 9d also shows a well-bonded interface but some fiber pullout occurs due to the presence of disordered micro-fibrils in the fiber surface.
Interfacial morphology of BF reinforced epoxy based composite treated with numerous alkali concentrations of a 0% b 1% c 4% and d 7% [42]
The IFSS also increased by 30.79, 100.30, and 53.66% in the sample treated with 1,4, and 7% NaOH solution. In the case of, 7% concentration, cellulose crystal structure is damaged hence the decrease of IFSS. Moreover, the flexibility of the epoxy-based molecular chain is limited after the NaOH treatment which results in a higher glass transition temperature, Tg. They determined that this treatment improves decomposition temperature and exhibit enhanced thermal stability due to the better interfacial adhesion.
7.5 Interfacial Adhesion of BF Reinforced Thermoplastic Composites
Improved mechanical properties are already obtained with BF reinforced composites with a thermoset matrix. Good chemical bonding at the interface and low viscosity of the resin is attributed to this improvement [15]. However, they are neither biodegradable nor recyclable thus having a serious environmental impact. In search of eco-friendly BF reinforced polymer composites, Fuentes et al. [44] integrated the physical–chemical-mechanical methodology to study the influence of interfacial adhesion on the mechanical behavior of BF reinforced thermoplastic composites. Maleic anhydride grafted polypropylene (MAPP), polypropylene (PP), polyvinylidene-fluoride (PVDF), and polyethylene terephthalate (PET) are used as a thermoplastic matrix in this study. PP, MAPP, PET, PVDF composites reinforced with BF showed increased interfacial shear strength. Among the four of them, PVDF displayed best amalgamation of high work of adhesion, wetting parameters along with a positive spreading co-efficient assisting to attain a better wetting of the molten thermoplastic on the bamboo fiber. This is a direct result of strong physical adhesion at the interface owing to the presence of a highly basic component on the bamboo fiber’s surface and a highly acidic component of PVDF. Moreover, the relatively high total surface energy of both the matrix and fibers also attributes to this factor.
7.6 Cotton Shaped BF Reinforced Maleic Anhydride Modified Polypropylene (MAPP) Composites
Okubo and Fujii [19] observed the interfacial adhesion development of BF reinforced MAPP composites. They used the steam explosion technique for extracting bamboo fiber and compared its’ properties with mechanically extracted bamboo fiber. The study showed the modulus and tensile strength of PP based composites using steam-exploded fibers improved by 30% and 15%, correspondingly, owing to the good impregnation of the matrix into fibers and reduction of several voids, compared to mechanically extracted bamboo fiber PP composites.
The fiber extracted by the steam explosion method appeared as cotton fiber. They stated to it as “Bamboo Fiber Cotton (BFC)”. It is shown that the MAPP based Bamboo Fiber Cotton Eco-Composites (BFCEC) gives better strength as well as modulus compared to MAPP based Bamboo Fiber Eco-Composites (BFEC), which clearly indicates enhanced interfacial adhesion.
7.7 BF/Epoxy and BF/Polyester Composites with Polyester Amide Polyol (PEAP) as Interfacial Agent
Saxena and Gowri [14] examined the effect of PEAP on the BF as an interfacial agent and observed the properties of BF/Epoxy and BF/Polyester composite. The flexural and tensile strength of both the composites were improved owing to the PEAP treatment on BF. The polyester amide polyol acts as a bridge between the resin matrix and the fibers. The polyester amide polyol is attached to the fiber surface (containing surface reactive protons) due to hydrogen bonding.
This interaction is responsible for better wetting to the resin during application followed by chemical bonding. There is a further possibility of hydrogen bonding between PEAP treated fiber and resin matrices which in turn enhances fiber-matrix interface adhesion. Figure 10 shows the stress elongation curve of BF/epoxy and BF/Polyester composite in a treated and untreated condition. Evidently, the presence of PEAP improved the tensile strength of both types of composites.
Stress-elongation plot for bamboo composites untreated and treated with PEAP [14]
Another important characteristic, observed from this study is the reduction of water absorption percentage of BF with the addition of PEAP as an interfacial agent. Introduction of hydrophobicity to the fiber surface attributes to this phenomenon. The surface-treated composite absorbs less moisture/water than untreated composites, owing to the cross-linked interface region formed by the reaction between PEAP and resin matrix. Thus, interfacial adhesion enhancement reduces the moisture-induced degradation of the composites.
8 Conclusions and Future Perspectives
It is undeniable that interfacial adhesion between bamboo fiber and polymer matrix is a crucial part in determining the properties of composites. Modification of the interface through various physical, chemical, and mechanical treatments has resulted in enhanced strength, modulus, IFSS, water absorption capacity, toughness, ductility, etc. Due to the improved properties, the range of industrial and commercial applications of BF reinforced polymer composites is expanding substantially. However, there are many scopes for further investigation and innovation in this field to overcome the probable challenges ahead.
References
Tshai KY, Chai AB, Kong I, Hoque, ME, Tshai KH (2014) Hybrid fibre polylactide acid composite with empty fruit bunch: chopped glass strands. J Compos 2014: 1–7. (Article ID 987956). doi: https://doi.org/10.1155/2014/987956
Khalid M, Ratnam CT, Walvekar R, Ketabchi MR, Hoque ME (2017) Reinforced natural rubber nanocomposites: next generation advanced material. In: Jawaid M, Salit M, Alothman O (eds) Green biocomposites. green energy and technology. Springer, Switzerland. https://doi.org/https://doi.org/10.1007/978-3-319-49382-4_14
Das I, Sagadevan S, Chowdhury ZZ, Hoque ME (2018) (2018) Development, optimization and characterization of a two step sol–gel synthesis route for ZnO/SnO2 nanocomposite. J Mater Sci: Mater Electron 29:4128–4135. https://doi.org/10.1007/s10854-017-8357-5
Hossain SKS, Hoque ME (2018) Polymer nanocomposite materials in energy storage: properties and applications. In: Jawaid M, Mansoob Khan M (eds) Polymer-based nanocomposites for energy and environmental applications, Woodhead Publishing, Elsevier, UK. https://doi.org/https://doi.org/10.1016/B978-0-08-102262-7.00009-X
Wahab MA, Islam N, Hoque ME, Young DJ (2018) Recent advances in silver nanoparticle containing biopolymer nanocomposites for infectious disease control—a mini review. Curr Anal Chem 14(6):198–202. https://doi.org/10.2174/1573411013666171009163829
Sagadevan S, Fareen A, Hoque ME, Chowdhury ZZ, Johan MRB, Rafique RF, Aziz FA, Lett JA (2019) Nanostructured polymer biocomposites: pharmaceutical applications. In: Swain SK, Jawaid M (eds) Nanostructured polymer composites for biomedical application, Elsevier, UK. https://doi.org/https://doi.org/10.1016/B978-0-12-816771-7.00012-0
AL-Oqla FM, Sapuan SM, Anwer T, Jawaid M, Hoque ME (2015) Natural fiber reinforced conductive polymer composites as functional materials: a review. Synth Metals 206:42–54. dOI:https://doi.org/10.1016/j.synthmet.2015.04.014
Asim M, Abdan K, Jawaid M, Nasir M, Dashtizadeh Z, Ishak MR, Hoque ME, Deng Y (2015) A review on pineapple leaves fibre and its composites. Int J Polym Sci 950567:1–16. https://doi.org/10.1155/2015/950567
Haniffah WH, Sapuan SM, Abdan K, Khalid M, Hasan M, Hoque ME (2015) Kenaf fibre reinforced polypropylene composites: effect of cyclic immersion on tensile properties. Int J Polym Sci 2015:1–6. (Article ID 872387)
Hasan M, Hoque ME, Mir SS, Saba N, Sapuan SM (2015) Manufacturing of coir fibre-reinforced polymer composites by hot compression technique. In: Salit M, Jawaid M, Yusoff N, Hoque M (eds) Manufacturing of natural fibre reinforced polymer composites. Springer, Switzerland. https://doi.org/https://doi.org/10.1007/978-3-319-07944-8_15
Asha AB, Sharif A, Hoque ME (2017) Interface interaction of jute fiber reinforced PLA biocomposites for potential applications. In: Jawaid M, Salit M, Alothman O (eds) Green biocomposites. Green energy and technology. Springer, Switzerland. https://doi.org/https://doi.org/10.1007/978-3-319-49382-4_13
Janssen JJA (2000) Designing and building with bamboo. International Network for Bamboo and Rattan (INBAR technical report). Available at: https://books.google.com.bd/books?id=D6stAAAACAAJ.
Zakikhani P, Zahari R, Sultan MTH, Majid DL (2014) Bamboo fibre extraction and its reinforced polymer composite material. Int J Chem Biomol Metallurg Mater Sci Eng 8(4):271–274
Saxena M, Gowri VS (2003) Studies on bamboo polymer composites with polyester amide polyol as interfacial agent. Polym Compos 24(3):428–36
Osorio L, Trujillo E, Van Vuure AW, Verpoest I (2011) Morphological aspects and mechanical properties of single bamboo fibers and flexural characterization of bamboo/epoxy composites. J Reinf Plast Compos 30(5):396–408. https://doi.org/10.1177/0731684410397683
Verma D (2016)Green approaches to biocomposite materials science and engineering. IGI Global, Pennsylvania. doi: 10.4018/978-1-5225-0424-5
Jain S, Kumar R, Jindal UC (1992) Mechanical behaviour of bamboo and bamboo composite. J Mater Sci 27(17):4598–4604. https://doi.org/10.1007/BF01165993
Walter L (2002) The anatomy of bamboo culms. International Network for Bamboo and Rattan (INBAR), p 128. doi: https://doi.org/10.1007/BF00994018
Okubo K, Fujii T, Yamamoto Y (2004) Development of bamboo-based polymer composites and their mechanical properties. Compos a Appl Sci Manuf 35(3):377–383. https://doi.org/10.1016/j.compositesa.2003.09.017
El-Abbassi FE, Assarar M, Ayad R, Lamdouar N (2015) ‘Effect of alkali treatment on Alfa fibre as reinforcement for polypropylene based eco-composites: Mechanical behaviour and water ageing. Compos Struct 133:451–457. https://doi.org/10.1016/J.COMPSTRUCT.2015.07.112
Saheb DN, Jog JP (1999) ‘<Saheb (1999) NF composition 7- kenaf.pdf>’. 18(4):351–363. doi: https://doi.org/10.1002/(SICI)1098-2329(199924)18
Liu D, Song J, Anderson D, Chang P, Hua Y (2012) Bamboo fiber and its reinforced composites: structure and properties. Cellulose 19(5):1449–1480. https://doi.org/10.1007/s10570-012-9741-1
Ismail H, Edyham MR, Wirjosentono B (2002) Bamboo fibre filled natural rubber composites: the effects of filler loading and bonding agent. Polym Testing 21(2):139–144. https://doi.org/10.1016/S0142-9418(01)00060-5
John MJ, Thomas S (2008) Biofibres and biocomposites. Carbohyd Polym 71(3):343–364. https://doi.org/10.1016/j.carbpol.2007.05.040
Zhou Y, Fan M, Chen L (2016) Interface and bonding mechanisms of plant fibre composites: an overview, Composites part B: engineering. Elsevier Ltd. doi: 10.1016/j.compositesb.2016.06.055
Madhukar MS, Drzal LT (1992) Fiber-matrix adhesion and its effect on composite mechanical properties: IV. Mode I and mode II fracture toughness of graphite/epoxy composites. J Compos Mater 26(7):936–968. https://doi.org/10.1177/002199839202600701
Kuk Kim KJ, Pal K (2011) Recent advances in the processing of wood-plastic composites. Springer. doi: 10.1007/978-3-642-14877-4
Chen H, Miao M, Ding X (2009) Influence of moisture absorption on the interfacial strength of bamboo/vinyl ester composites. Compos A Appl Sci Manuf 40:2013–2019. https://doi.org/10.1016/j.compositesa.2009.09.003
Tae Kang J, Kim S (2011) Improvement in the mechanical properties of polylactide and bamboo fiber biocomposites by fiber surface modification. Macromol Res 19:789–796. https://doi.org/10.1007/s13233-011-0807-y
Das M, Chakraborty D (2009a) Effects of alkalization and fiber loading on the mechanical properties and morphology of bamboo fiber composites. II. Resol matrix. J Appl Polym Sci 112(1):447–453. https://doi.org/10.1002/app.29383
Das M, Chakraborty D (2009b) The effect of alkalization and fiber loading on the mechanical properties of bamboo fiber composites, part 1—polyester resin matrix. J Appl Polym Sci 112(1):489–495. https://doi.org/10.1002/app.29342
Huda MS, Drzal LT, Misra M, Mohanty AK (2006) Wood-fiber-reinforced poly(lactic acid) composites: evaluation of the physicomechanical and morphological properties. J Appl Polym Sci 102(5):4856–4869. https://doi.org/10.1002/app.24829
Li X, Tabil L, Panigrahi S (2007) Chemical treatments of natural fiber for use in natural fiber-reinforced composites: a review. J Polym Environ 15:25–33. https://doi.org/10.1007/s10924-006-0042-3
Mi Y, Chen X, Guo Q (1997) Bamboo fiber-reinforced polypropylene composites: crystallization and interfacial morphology. J Appl Polym Sci 64(7):1267–1273. https://doi.org/10.1002/(sici)1097-4628(19970516)64:7%3c1267::aid-app4%3e3.3.co;2-b
Jiang L, Chen F, Qian J, Huang J, Wolcott M, Liu L, Zhang J (2010) Reinforcing and toughening effects of bamboo pulp fiber on poly(3-hydroxybutyrate-C0-3-hydroxyvalerate) fiber composites. Ind Eng Chem Res 49(2):572–577. https://doi.org/10.1021/ie900953z
Jiang L, Huang J, Qian J, Chen F, Zhang J, Wolcott M, Zhu Y (2008) Study of poly(3-hydroxybutyrate- co -3-hydroxyvalerate) (PHBV)/bamboo pulp fiber composites: effects of nucleation agent and compatibilizer. J Polym Environ 16:83–93. https://doi.org/10.1007/s10924-008-0086-7
Zhou Y, Fan M, Chen L, Zhuang J (2015) Lignocellulosic fibre mediated rubber composites: an overview. Compos B Eng 76:180–191. https://doi.org/10.1016/j.compositesb.2015.02.028
Kalia S, Kaith BS, Kaur I (2009) Pretreatments of natural fibers and their application as reinforcing material in polymer composites-a review. Polym Eng Sci 49:1253–1272. https://doi.org/10.1002/pen.21328
Wong KJ, Yousif BF, Low KO (2010) The effects of alkali treatment on the interfacial adhesion of bamboo fibres. Proc Inst Mech Eng Part L J Mater Des Appl 224(3):139–148. https://doi.org/10.1243/14644207JMDA304
Okubo K, Fujii T (2013) Improvement of interfacial adhesion in bamboo polymer composite enhanced with microfibrillated cellulose. Polym Compos Biocompos 3:317–329. https://doi.org/10.1002/9783527674220.ch9
Lu T, Liu S, Jiang M, Xu X, Wang Y, Wang Z, Gou J, Hui D, Zhou Z (2014) Effects of modifications of bamboo cellulose fibers on the improved mechanical properties of cellulose reinforced poly(lactic acid) composites. Compos Part B Eng 62:191–197. https://doi.org/10.1016/j.compositesb.2014.02.030
Wang F, Lu M, Zhou S, Lu Z (2019) Molecules effect of fiber surface modification on the interfacial adhesion and thermo-mechanical performance of unidirectional epoxy-based composites reinforced with bamboo fibers. Molecules 24(15):2682
Zhang X, Wang F, ML Keer (2015) Influence of surface modification on the microstructure and thermo-mechanical properties of bamboo fibers. Materials 8:6597–6608. https://doi.org/10.3390/ma8105327
Fuentes C, Tran LQN, Van Hellemont M, Janssens V, Dupont C, Vuure AW, Verpoest I (2013) ‘Effect of physical adhesion on mechanical behaviour of bamboo fibre reinforced thermoplastic composites. Coll Surf A Phys Eng Aspects 418:7–15. doi: 10.1016/j.colsurfa.2012.11.018
Author information
Authors and Affiliations
Corresponding author
Editor information
Editors and Affiliations
Rights and permissions
Copyright information
© 2021 Springer Nature Singapore Pte Ltd.
About this chapter
Cite this chapter
Asrafuzzaman, Amin, K.F., Sharif, A., Hoque, M.E. (2021). Bonding Mechanism and Interface Enhancement of Bamboo Fiber Reinforced Composites. In: Jawaid, M., Mavinkere Rangappa, S., Siengchin, S. (eds) Bamboo Fiber Composites. Composites Science and Technology . Springer, Singapore. https://doi.org/10.1007/978-981-15-8489-3_12
Download citation
DOI: https://doi.org/10.1007/978-981-15-8489-3_12
Published:
Publisher Name: Springer, Singapore
Print ISBN: 978-981-15-8488-6
Online ISBN: 978-981-15-8489-3
eBook Packages: Chemistry and Materials ScienceChemistry and Material Science (R0)