Abstract
Force transducers are capable of determining the magnitude of force applied by measuring strain deformations. The strain induced on the transducer is measured using strain gauges. Usually, the force transducers, being unidirectional, are able to sense only axial force or torque. This paper presents an innovative force transducer for sensing triaxial loads and moments pertaining to its unique shape which allows strategic placement of strain gauges. The transducer is designed in a frame-like structure by stacking three cantilever beams one in each orthogonal axis. Each frame is sensitive to the load applied in the corresponding orthogonal direction. This configuration provides advantage of uniform sensitivity in triaxial loading applications with negligible cross sensitivity. The transducer is having a proportional force and moment conversion due to its single body structure and isotropic material properties. A new design for the transducer is also proposed and the comparative behavior of both, for uniaxial and triaxial loading, is presented. The two designs are analyzed by FE analysis in ABAQUS for principle and shear strain with varying loading conditions.
Access provided by Autonomous University of Puebla. Download conference paper PDF
Similar content being viewed by others
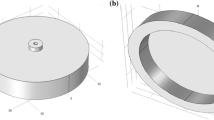
Keywords
1 Introduction
Force transducers are extensively used to measure the applied force on structural members. It generally consists of an elastic load-bearing element which undergoes strain deformation upon application of force or torque. This deformation could be measured using strain gauges, thus converting the applied force into a proportional electric signal.
Traditionally, force transducers are uniaxial and multiple such transducers could be used to contrive multiaxial transducers. For instance, Kaneko [1] demonstrated that a combination of two similar three-axis force sensors could form one six-axis force sensor and developed a characteristic matrix, connecting the load and sensor output vectors. Svinin and Uchiyama [2] proposed a generalized theoretical model for multidimensional force sensor designed using elastic components connected in parallel.
Kim et al. [3] and Kim [4] described a design and development procedure of a six-component force and moment sensor. They derived equations for calculating rated strains on the components of the sensor and performed a finite element (FEM) analysis for confirming the strains obtained from the theoretical analysis. Liu and Tzo [5] proposed identical T-shaped bar-type six-axis force sensor. They calculated the sensitivity of force-sensing member with respect to design parameters using finite element analysis in conjunction with a design optimization. Liu et al. [6] designed a six-dimensional piezoelectric heavy force sensor based on load-sharing principle. They performed a finite element analysis using ANSYS software for calculating the static and dynamic response of the designed sensor under heavy loading. The experiments on the fabricated sensor demonstrated very less nonlinearity errors and verified the numerical results. Liang et al. [7] and Sunand et al. [8] derived the equations of force and moment for the six-component force sensor and determined the theoretical value of strains. This result was validated using finite element method (FEM) and optimization method by trial and error, employing the response surface methodology (RSM).
Bayo and Stubbe [9] proposed a frame/truss-type six-axis sensor for robotic applications. They employed the axial deformation behavior of the six-axis sensor to eliminate disadvantages of the crossbar and obtained better measure of isotropy and decoupling. They also compared the performance parameters (condition number, overall static and dynamic stiffness, strain gauge sensitivity) and found significant improvement over the earlier design of six-axis wrist force sensor. Chao and Chen [10] applied penalty method to optimize the geometrical design parameters of a wrist-type elastic force sensor. They used calibration matrix along with strain gauge sensitivity as a performance index for design optimization. Based on these design criteria they devised a novel decoupled wrist force sensor with enhanced force sensitivity and minimum stiffness.
Kang [11] formulated closed-form solution of forward kinematics for 6-DoF Stewart platform based force transducer using linearization approach. Later, Dwarakanath et al. [12] performed design parameter sensitivity analysis for optimal size of Stewart platform based force transducer and fabricated a prototype of the sensor.
Present study is an extension to the work done by Deshpande et al. [13]. They did a mathematical analysis of a novel three-axis force transducer and validated the analytical results with experimental results. This paper incorporates finite element analysis to study the behavior of the initial design of force transducer (FT1) and determines the optimal locations for mounting the strain gauges. A modified design of the force transducer (FT2) is also proposed in order to enhance the performance of the cantilever-beam-type force-sensing elements. In the new design, the principal stress and shear stress are also analyzed using finite element analysis for various loading conditions. The comparison of analysis results is presented herewith. This sensor could find its application in robotic manipulators and multiaxial load cells.
2 Force Sensing in Strain Gauges
Force transducers are deployed for knowing the numerical value of the applied force and torque on the body, which is ideally equal to the true value of the applied load. The output of the transducer depends on the characterized relationship between the output value and the property under measurement. Force transducers are designed so as to have elastic member for loading elements in any of the six loading axes. The input loading creates deflection in the elastic member which in turn creates proportional elongation also known as strain. The strain is measured as a quantifiable change in resistance of the coiled conductor in the strain gauge. Thus, strain gauges proportionally convert the strain developed into change in the electric current at output terminals [14].
There are various methods used to determine torque and force applied on any elastic member among which the most common method is using strain gauges. The strain gauge can be configured to distinguish tensile and compressive strains, to give conversions in the form of positive or negative signals, thus making it possible to distinguish expansion as well as contractions of the members having strain gauges on it. The gauge factor is fundamental term correlating the sensitivity of the strain gauge. It is defined as the ratio of change in electrical resistance (R) to the mechanical strain ε captured by gauge conductor coil, and expressed as
where
-
ρ = Resistivity/conductivity constant,
-
L = Length of the sensor,
-
A = Cross-sectional area of sensor,
-
R = Electrical resistance of sensor,
-
ε = Mechanical strain, and
-
GF = Gauge factor.
Strain gauge rosettes are geometric combination of strain gauges which could be mounted on elastic transducer element to capture strains in desired loading axes. The strain induced due to loading is reliant on the shape and geometric configuration as well as the elastic modulus of that element. Every strain gauge in a rosette captures the local strain at that location, and through combination of these individual strain gauges, proportional force is estimated [15].
Usually, forces in real-life scenarios are multidirectional, dynamic, and fluctuating in nature. This makes it difficult for single-axis sensor to completely perceive the applied load. Multi-axis force transducers are well suited for such situations, which transfer input signals at elastic members due to applied force and torque to proportional voltage and estimates the proportional output with respect to external force/torque applied as input. The important applications are found in force and torque sensors including robotic control and manipulation, aerospace and industries [16].
3 Design of the Transducer
This paper presents an innovative design for a force transducer capable of sensing triaxial loads and moments. The transducer is designed in a frame-like structure by stacking three cantilever beams upon each as depicted in Fig. 1. Each frame carries its individual strain rosettes which are sensitive to a specific orthogonal loading direction. Stacking all three frames into a single structure produces a 3-DoF force-sensing transducer.
a CAD model depicting the force transducer (green) also schematics of pulleys and deadweight for loading (brown). b Experimental setup [14]
This paper also discusses variations to the original design of the transducer in order to enhance its sensing capabilities. The alterations were proposed to attain uniform stress distribution and better strain dispersion among the structural members. Figure 2a depicts the original and Fig. 2b depicts modified designs of the force transducer. The two designs are further evaluated for stress distribution patterns using FE analysis. For the sake of simplicity, the original design of the transducer will be denoted as FT1 and the modified new design would be denoted as FT2, further along this paper.
4 Transducer Analysis Using FEA
Finite element analysis is a numerical approach to determine the behavior of a structure under static or dynamic loading conditions. In FEM, a mathematical model compatible with the geometric and material properties of the structure is discretized into small, multiple finite elements. The change in field quantity over the entire domain of the structure is derived by analyzing these discrete finite elements. The FE model analysis was limited to static loading conditions. There are various commercial packages available for FE analysis. ABACUS was chosen for performing the static FE analysis on both the transducer designs.
4.1 Material Properties
The material used for constructing the transducer was considered to be isotropic and homogeneous. Standard structural steel properties were assumed as shown in Table 1.
4.2 FE Mesh Properties
The meshing for FE analysis was performed in ABAQUS using a ten-noded quadratic tetrahedron element (C3D10). Size of the mesh was program controlled. Figure 3 illustrates the meshing pattern for FT1 and FT2 transducer designs.
4.3 Boundary Conditions
The transducer was constrained in all directions at its base to depict a fixed–fixed boundary condition. This was done to replicate a real-life scenario when the transducer is firmly placed on a solid surface. The load was applied on the topmost surface of the transducer. The load was applied for uniaxial and triaxial loading conditions, with varying magnitudes, in order to achieve a detailed analysis. The boundary conditions and loading patterns were kept identical for FT1 and FT2 transducers as shown in Fig. 4.
4.4 Loading Parameters
The static analysis was performed by applying various discrete load levels having uniform increment from 0.2 to 2 N. Loads were applied in all three uniaxial directions (x, y, and z) independently. A triaxial loading was also applied for the same load levels. The load was applied on the cube-shaped block at the top of the transducer.
5 Results and Discussion
5.1 Principal Strain Analysis
Maximum principal strain contour on different elements of transducers FT1 and FT2 at 0.2 N, 1 N, and 2 N loads is depicted in Fig. 5a, c, e and Fig. 5b, d, f, respectively. Table 2 enumerates the maximum principal strain for different magnitudes of load in FT1 and FT2.
Figure 6 represents the linear relationship between magnitude of load and induced strain exhibited by the FT1 and FT2 transducers. It is observed that maximum strain occurs on the element which is sensitive to the direction of applied force. The experimental results of FT1 transducer [14] confirm this linear relationship.
Figure 7 shows the strain difference between FT1- and FT2-type transducers when the applied load is same. It is observed that the strain difference also increases linearly with load.
The modified design, FT2, has additional blocks at the end of each sensing element, which provide rigidity to the cantilever-sensing element. It is observed that in single loading conditions, the induced strain values in FT2 transducers are higher than FT1 transducers. It is also observed that in triaxial loading conditions, the strain difference between FT1 and FT2 is higher compared to single loading conditions. This infers that the modified design is more sensitive to smaller variations in the load. The advantage of the modified design is that it detects the strain when the applied load is very small and when there is a small variation in the applied load.
5.2 Shear Strain Analysis
The transducer FE model was analyzed for shear strain by applying biaxial combinational loading of varying magnitude. The load increment was similar to that used in principal strain analysis. The moment generated in the sensing element of the transducer was neglected in this analysis. The strain gauge deployed for direct strain estimation measures both the normal and shear components of the strains. The analysis carried out gives a better visualization of shear patterns as shown in Fig. 8a, c, e for FT1 and Fig. 8b, d, f for FT2. The maximum shear elastic strain in FT1 and FT2 is given in Table 3.
The variation in maximum shear strain with respect to applied load is represented in Fig. 9. The transducer exhibits linear relationship between load and induced shear strain in both FT1- and FT2-type transducers. The FT2 transducer exhibits higher strain values in x-y and z-x loading directions, whereas FT1 has higher strain magnitude in y–z direction. Figure 10 represents the shear strain difference between FT1- and FT2-type transducers when the applied load is same.
It is evident from the data enumerated in Tables 2 and 3 that FT2 shows enhanced stress concentration levels for similar loading conditions as FT1 for majority of the cases. This leads to more localized strain and provides an advantage of better stress sensitivity. One exception to the case could be noted in Y–Z principal shear stress loading, where FT2 shows the reduced sensitivity than its predecessor. It is also observed that change in maximum principal strain is least in X-direction. The member most sensitive to the X-directional loading is at the bottom and attached to the base. The rigidity provided by the fixed–fixed boundary condition and increased mass in the modified design could be attributed for this deficit. It warrants further research and possible alterations to the design of FT2 in order to rectify this problem.
6 Conclusions
This paper describes a detailed analysis of strain estimation in a triaxial force transducer which has engineering applications in platform-type sensor. The experimental observations reflect that the strain concentration at specific locations modifies the characteristics of the transducer. A comparative study of the strain estimation for two different transducer designs is also presented, which is necessary for the safe design and manufacturing of the transducers. The analysis of the strain patterns helps in determining the location of maximum stress concentration, which provides an estimate location to mount the strain gauges. Some of the notable observations from the FE analysis are summarized below:
-
1.
The experimental results for transducer FT1 show that a linear increase in load causes a linear increase in strain on the sensing element [13]. The transducer FT1 has been tested and validated in simulation environment.
-
2.
The estimation of strain for FT2 has been done by simulation and results suggest that the strain in the sensing elements increases linearly with the applied load, as in the case of FT1.
-
3.
In transducer FT2, the blocks added at the end of each sensing element confine the principal strain to a smaller region as compared to FT1. The advantage of the modified design is that it detects the strain when the applied load or the variation in the applied load is very small.
The strain-sensing capability of the proposed design (FT2) is better than that of the FT1 transducer. This kind of transducer finds applications in serial- and spatial-type parallel manipulators used for payload sensing.
References
Kaneko M (1993) A new design of six-axis force sensors. In: Proceedings of the IEEE international conference on robotics and automation, pp 961–967
Svinin MM, Uchiyama M (1995) Optimal geometric structures of force/torque sensors. Int J Robot Res 14:560–573
Kim GS, Kang DI, Rhee SH (1999) Design and fabrication of a six-component force/moment sensor. Sens Actuators A 77:209–220
Kim GS (2001) The design of a six-component force/moment sensor and evaluation of its uncertainty. Meas Sci Technol 12:1445
Liu SA, Tzo HL (2002) A novel six-component force sensor of good measurement isotropy and sensitivities. Sens Actuators A 100:223–230
Liu W, Li Y et al (2011) Research on parallel load sharing principle of piezoelectric six-dimensional heavy force/torque sensor. Mech Syst Signal Process 25:331–343
Liang Q, Zhang D et al (2013) Design and analysis of a novel six-component F/T sensor based on CPM for passive compliant assembly. Meas Sci Rev 13:253–264
Sunand Y, Liu Y et al (2015) Design and optimization of a novel six-axis force/torque sensor for space robot. Measurement 65:135–148
Bayo E, Stubbe J (1989) Six-axis force sensor evaluation and a new type of optimal frame truss design for robotic applications. J Field Robot 6:191–208
Chao LP, Chen KT (1997) Shape optimal design and force sensitivity evaluation of six-axis force sensors. Sens Actuators A Phys 63:105–112
Kang CG (2001) Closed-form force sensing of a 6-axis force transducer based on the Stewart platform. Sens Actuators A 90:31–37
Dwarakanath T, Dasgupta B, Mruthyunjaya T (2001) Design and development of a Stewart platform based force–torque sensor. Mechatronics 11:793–809
Deshpande M, Jawale HP, Thorat HT (2016) Development, calibration and testing of three axis force sensor. In: 2016 7th international conference on mechanical and aerospace engineering (ICMAE), IEEE, pp 285–289
Stefanescu DM (2011) Handbook of force transducers: principles and components. Springer Science & Business Media
Yurish S (2014) Modern sensors, transducers and sensor networks. Lulu.com
Chen D, Song A, Li A (2015) Design and calibration of a six-axis force/torque sensor with large measurement range used for the space manipulator. Procedia Eng 99:1164–1170
Author information
Authors and Affiliations
Corresponding author
Editor information
Editors and Affiliations
Rights and permissions
Copyright information
© 2020 Springer Nature Singapore Pte Ltd.
About this paper
Cite this paper
Jaiswal, A., Jawale, H.P., Shrivastava, K. (2020). Design and Simulation of 3-DoF Strain Gauge Force Transducer. In: Singh, B., Roy, A., Maiti, D. (eds) Recent Advances in Theoretical, Applied, Computational and Experimental Mechanics. Lecture Notes in Mechanical Engineering. Springer, Singapore. https://doi.org/10.1007/978-981-15-1189-9_3
Download citation
DOI: https://doi.org/10.1007/978-981-15-1189-9_3
Published:
Publisher Name: Springer, Singapore
Print ISBN: 978-981-15-1188-2
Online ISBN: 978-981-15-1189-9
eBook Packages: EngineeringEngineering (R0)