Abstract
During Laser Powder-Bed Fusion (LPBF), the surface formation of the selected-melted powder-bed region is subject to a melting-solidification process along the line-scans and sensitive to the process conditions. This study focuses on the surface formation of mesoscopic line-scans in LPBF and aims to investigate the effect of different process parameters, such as laser power and layer thickness, on the track morphology and surface roughness. For this purpose, single-track scans were produced by an LPBF system and then were characterized under a white-light interferometer. A discrete element method and 3D thermo-fluid modeling were applied to simulate powder spreading and laser scanning. The results show that the line-scan surface morphology and the surface roughness of the quasi-steady regions on the line scans are signifiscantly dependent on the process conditions both longitudinally and transversely. As a result of continuous melting in the line scans, increasing laser power and decreasing layer thickness lead to smoother surface finish, respectively.
Access provided by Autonomous University of Puebla. Download conference paper PDF
Similar content being viewed by others
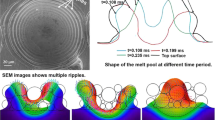
Keywords
Introduction
Metal laser powder-bed fusion (LPBF), additive manufacturing (AM) process utilizes a laser source to selectively fuse modeled regions on the metal powder bed, and continuously repeats the layer-wise deposition to generate 3D parts [1]. Due to the flexibility to fabricate complex geometries directly from the CAD model, LPBF has been growing popularity with high-demanded potentials among numerous AM technologies. Particularly, LPBF exhibits extraordinary advantages in surface quality compared with other powder-bed processes, i.e., electron beam melting (EBM). However, surface quality is a key assessment criterion in many AM applications [2, 3]. Although the surface quality can be improved largely by post-treatment or even during the build processing through re-melting [4, 5] and pulse shaping [6], the as-built surface quality is still a limit in the AM field.
Since the formation of 3D parts in LPBF is made up by the metallurgical bonding among adjacent raster line scans in successive layers, the individual line scans are considered as the fundamental component to examine the stability and quality of the fabricated parts [7]. Due to a complex thermal fluid dynamics interacting the heat source and metallic powder, the melt pool for the line scans goes through a continuous rapid melting-solidifying process. The applied fabrication process parameters and involved powder-bed status can significantly influence the quality of line-scan formation [8, 9]. Additionally, for a single line scan while traveling a long path, the melt pool may reach a thermodynamic balance status assuming the scan direction is not changed. However, as the laser practically experiences acceleration and deceleration while laser on and off or reaches at 180° turn points, the melt pool will lose the balance and reveal significantly different from the quasi-static region [10].
Recent years, many studies have investigated the LPBF fused metallic melt pool of single tracks. Experimentally, Gong et al. characterized the surface topology of single line scans using Ti-6Al-4V (Ti64) in LPBF, and exhibited the dissimilarity at different energy density situations [11]. Caprio et al. estimated the penetration depth of melt pool based on the detection of melt pool surface oscillations using a novel monitoring technique [12]. On the other hand, from the simulation perspective, Ahn et al. developed an analytical equation to predict the surface roughness for different inclination angles using measurement data from experiment and interpolation method [13]. Additionally, Dai and Gu applied a 3D volume of fluid (VOF) model using finite volume approach to predict the surface morphology based on the thermo-capillary effect and pressure boundary condition at the interface [14]. Powder-scale models were utilized to predict the free surface formation some studies by Khairallah et al. [15] and Xia et al. [16]. Shrestha et al. utilized a VOF model to predict the heat transfer, fluid flow, and resultant track morphology of the single-track formation [17].
The objective of this study is to investigate the mesoscopic surface formation with respect to different process conditions in LPBF, and to have reliable understanding on the quasi-static profile roughness of the mesoscopic surfaces. In this study, the single-track scanned specimens were fabricated in an LPBF system with Ti64 powder, and then examined using a white-light interferometer (WLI) to investigate the surface morphology and profile roughness. In addition, a discrete element method and 3D thermos-fluid modeling were applied to simulate the powder spreading and laser scanning process.
Experimental Methods
The experimental specimen consists of a semi-circular solid substrate and line scans exposed on the top surface of the substrate as shown in Fig. 1a. The distances between the neighboring tracks were far enough to avoid the influence of heat dissipation caused by overlapped melt pools. In addition to examine the effect of layer thickness on the single-track formation and to fabricate the tracks under the consistent build environment, a 20 µm stair in the semi-circular was designed as shown in Fig. 1b. As such, the single tracks could be deposited on the two sides of the semi-circular specimen with different layer thicknesses, 20 µm and 40 µm, respectively.
In this study, an EOS M270 LPBF system was utilized to fabricate the specimens. Pre-alloyed Ti64 powder supplied by LPW technology was used. All of the semi-circular substrates were manufactured using the EOS default parameter set to form full dense solids and consistent surface status. Then, the tracks were fabricated on the substrate surfaces with different conditions, as exhibited in Table 1. Specimens P1 to P3 were formed with different laser power at the layer thickness of 30 µm. Also, to fabricate the tracks at layer thicknesses of 20 and 40 µm, the build was performed at the 20 µm powder layer. After the substrate surface was finished, the 20 µm stair was exposed at the one half side of the surface, and at this layer, no tracks were exposed. Then, the next 20 µm powder layer was spread over. At the current layer, the thickness of the powder bed was 20 µm on the right side and 40 µm on the left, and thus, the track scans were produced at different powder layer thicknesses. In addition, all the tracks were produced with a fixed scan speed of 1000 mm/s with skywriting setting turned on.
Moreover, to examine the surface morphology, a non-contact WYKO NT1100 white-light interferometer was utilized, shown in Fig. 1d. The flat surface with single lines fabricated is face-up placed on the sample stage (Fig. 1e). The vertical scanning interferometry (VSI) measurement mode is applied to evaluate the rough surfaces. In this study, 0.5× magnification field-of-view (FOV) lens and 50× objective lens was built-in. The scan region and scan length were set based on the length and height of the deposited single line scans.
Results and Discussion
Track Surface Morphology
The as-built specimens were cut off from the build substrate after fabricated from EOS M270 system. The semi-circular specimens were placed with the flat surfaces upwards to observe the tracks under WLI. The surface morphology observation and roughness measurement of the mesoscopic surface formation are elaborated in this section.
Track Repeatability
Figure 2 shows the 5 replicates of 2 mm single tracks produced using a laser power of 150 W and a scan speed of 1000 mm/s at a layer thickness of 30 µm, respectively. The track profiles can be identified from the isometric view with various colors, indicatable of vertically elevated region in red and lowered region in blue. The scanning direction of these tracks were exposed from right-hand side to left in the view of Fig. 2. It is noticed that the 5 replicates of single tracks are consistently repeatable in general although unique morphology appears for every single-track scan.
Laser Power Effect on Single-Track Formation
3-dimensional displays of representative single-track scans produced using various laser powers are shown in Fig. 3, with the scan direction from back to front. It can be identified that the track produced with 120 W laser power shows a wavy profile and occasional discontinuous valleys in the longitudinal direction (Fig. 3a), whereas the laser powers of 150 and 180 W made continuous tracks (Fig. 3b, c); among the latter two tracks, the one using 180 W apparently shows an increase in height than 150 W due to more energy input contributed to deposit more powder. In addition, the bead width is observed to fluctuate along the tracks, and is generally ascending with an increase of laser energy input. It is also observed that the tails of tracks using laser powers of 120 and 150 W show irregularly distortion. The transient thermal dynamic behavior is considered that when the laser is off, the melt flow is slowed down while the boiling and evaporation of the melt powder create recoil pressure that leads to distortion of the single tracks [18]. Besides, the tracks formed by higher laser power applied present more powder particles attached on the track surface due to spatter generation caused by higher heat input [19].
Figure 4 shows the 2D profiles of the tracks in Fig. 3 in longitudinal and transverse directions. Both directional profiles present the surface fluctuation status of the middle cutoff of the tracks. Among these tracks, the one using 120 W laser power exhibits disconnection near the beginning of the scan and low profile at the center, leading to the instable profile, shown as Fig. 4a at the left. Although no discontinuity is observed in the other two tracks, occasional small peaks due to attached particles being noticed. Quantitatively, at the beginning region of tracks, the height of peaks exhibits dependent on the energy input, showing an increase (from 120 µm to 80 µm) with ascending laser power because higher energy deposition creates higher thermal gradient and assists melting more surrounding powder. Another peak region near the track tails is measured as well, and similar tendency with respect to the laser power is noticed. In addition, it can be seen that the ending region presents inclined that is considered caused by recoil force to the melted metal surface [20]. On the other hand, the profiles of the three track cutoffs in the transverse directions generally exhibit semi-circular morphologies, although fluctuation and spattering powder during solidification may cause distorted profiles. It is indicated that the height of the middle cross-sectional cutoffs shows increasing with a rising laser power. Due to the semi-circular shape, the peaks are basically around the center line of the profile, and thus, the track height can be analyzed with an overall view at the longitudinal profiles.
Layer Effect on Single-Track Formation
Additionally, the single tracks deposited via the same process parameters at different layer thickness powder bed were scanned under WLI, as shown in Fig. 5. As expected, it is observed that the track height displays dependent upon the layer thickness: The track built at 20 µm powder layer generally presents lower height than those built at 30 and 40 µm. Specifically, a shallow tail end of the 20 µm layer track is significantly shown in Fig. 5a. This can be because of insufficient flow of melt pool at the end of track scans after the laser is stopped, whereas the accumulated heat cannot dissipate immediately, and the melted surface is pushed down by recoil force [21]. Moreover, in terms of track continuity, three representative tracks do not exhibit disconnection due to sufficient energy input, which also does not lead to significant difference on the track width visually. Besides, the inclusions due to incomplete melting can be seen on the surfaces of the tracks and surrounding regions, with an increasing amount with the thickened powder layers during fabrication.
The 2D surface profiles in both longitudinal and transverse directions are investigated in Fig. 6. Similar to the observation in the 3D views, the profile height of these tracks displays dependent on the layer thickness, increasing to a peak value of 85 µm at the powder layer thickness of 40 µm. In addition, the continuity of the tracks without breakage reveals that the linear energy density created by the process parameter combination of 150 W laser power, and 1000 mm/s scan speed is sufficient in fabrication at the studied range of powder layer thickness. Specifically, it is noticed that the profile of the track built on 20 µm powder layer (Fig. 6a) exhibits a smoother surface finish along the track formation. In contrast, the other two tracks present obvious bumps on their profiles, showing ascending height values with an increase of layer thickness due to more powder melted during fabrication. On the other hand, the transverse cross-sectional profiles are shown in Fig. 6. It is noted that the transverse cutoffs exhibit semi-circular shape. Besides, the width of the track with 40 µm layer thickness (Fig. 6c) exhibits greater due to more powder fed during laser deposition.
Specifically, the shallow tail end of the track at 20 µm layer thickness has been noticed with a bimodal profile in the depressed zone and inclination on both sides in the transverse view of cutoff, shown in Fig. 7. Such a phenomenon can be contributed by Marangoni effect caused by temperature gradient, and thus, the fluid flows from low surface tension region to high surface tension region, exhibiting an outward flow from center to the edge of the melt pool [22].
Depressed tail of single track (Fig. 5a) made at 20 µm layer thickness. (Color figure online)
Quasi-static Surface Roughness
As the experimental 2 mm single tracks were experienced transient regions at both ends along the laser traveling direction, the surface roughness in this study would be measured for the dynamic-balanced region excluding the transient regions. The quasi-static length in the longitudinal direction was estimated in a range of 1062 µm to 1100 µm with an ascending tendency with decreasing laser power applied at 30 µm layer thickness. Therefore, to keep the Ra measurement consistent, a 1000 µm measure length in the middle portion of the tracks was applied to examine the quasi-static roughness.
The profile roughness measurement with respect of exposed laser power is shown in Fig. 8. The longitudinal roughness reveals that the lowest laser power (120 W) gives the highest roughness of 13 µm ± 1.8 µm compared to other two laser power levels, while not much difference of the roughness values (approximately 7.5 µm) is observed between 150 W and 180 W. In the transverse direction, the middle slice of the track was measured. It can be noticed that the transverse roughness increases with the increasing laser power.
In addition, single-track scans exposed at different layer thicknesses using 150 W laser power and 1000 mm/s scan speed were analyzed about the profile roughness. As shown in Fig. 9, the longitudinal roughness exhibits an increasing tendency with an increase of layer thickness; therein, the roughness of tracks deposited at 40 µm powder layer reveals almost twice value of that at 20 µm powder layer, which can be a reason that thicker layer may cause a higher bead height but wavier profile due to less energy density. On the other hand, the roughness in the transverse direction is observed that higher profile roughness occurs at thicker powder layer.
Numerical Study
A 3D thermo-fluid model was developed using FLOW-3D software. The powder over the base platform was imported from the LIGGGHTS simulation result. The domain was represented based on the fluid fraction. Powder and solid had a fluid fraction of 1 and the rest has 0 fluid fraction. Since the VOF model was used to predict the surface formation, a hexahedral mesh of 5 µm was applied. In addition, all the walls of the domain were assigned with adiabatic boundary conditions. During the simulation, the laser was turned on at 0.2 in positive X (along laser movement) and Y (transverse) directions and the total scan length used was 1 mm. After the laser traveled 1 mm, it was turned off and the melt pool was let to solidify. The process parameters used in the simulation were 150 W laser power and 1000 mm/s scan speed as consistent in the experiment.
Figure 10a shows the temperature distribution and the melt pool when the laser is in motion. The upper limit of the temperature distribution is limited to the melting temperature. Hence, the red area represents the melt pool. Besides, a depression is formed at the laser application area due to the recoil pressure. The single track formed after the solidification is shown in Fig. 10b.
Single-track scans at various layer thicknesses of 20, 30, and 40 µm were simulated. The 2D melt pool profiles of these tracks were obtained from the center of the domain, shown in Fig. 11. Generally, the longitudinal profiles show a decreasing melt pool penetration depth along the laser traveling direction. The depth of the track appears maximum at the beginning, and depression is observed at the end of track. The formation of such a profile occurs due to the backward melt flow driven by the thermo-capillary effect. The longitudinal profiles of the three tracks show little variation in the melt pool depth, while difference exists on the surface profiles that the 40 μm layer-thickness track (Fig. 11c) presents more fluctuation, which was observed in the experimental results as well. On the other hand, the transverse profiles of the three tracks are resulted semi-circular shape. Therein, the melt pool depth with 40 μm layer-thickness exhibits relative lower compared to those with 20 and 30 μm layer-thicknesses, while their transverse surface profiles do not vary with much variation. However, the counterparts from experiments were observed more fluctuation due to the presence of incomplete melted powder particles attached and denudation.
Conclusions
In this study, the mesoscopic formation of single-track scans was fabricated in a LPBF process, and examined the surface morphology under WLI. Using a consistent measure length of 1000 µm, the quasi-static regions of the single-track scans were examined in the longitudinal and transverse directions. Additionally, the discrete element method and 3D thermos-fluid modeling were utilized to simulate the powder spreading and laser scanning process.
The achieved findings are summarized: (1) The surface formation of single-track scans is significantly dependent on the fabrication parameters. At the powder laser thickness of 30 µm, higher laser power results in smoother surface finish, along with an increase in track width and bead height. (2) At a constant laser power and scan speed, the single-track scan formation is affected by the layer thickness. The increase in layer thickness leads to increasing track height. (3) When the layer thickness is 20 µm, a depression at the tail end of the track is observed. (4) In the longitudinal direction, the roughness of single-track scans exhibits an increase with a decreasing of laser power at a certain scan speed and layer thickness, and with an ascending layer thickness at a constant laser processing parameters, including laser power and scan speed. (5) In the transverse direction, the quasi-steady roughness of single tracks presents an increase with an increasing laser power at a certain scan speed and layer thickness, and with an increasing laser thickness at a constant laser processing.
References
ISO/ASTM52911-1-19, Additive manufacturing—Design—Part 1: Laser-based powder bed fusion of metals (2019). ASTM International, West Conshohocken, PA
Li P, Warner D, Fatemi A, Phan N (2016) Critical assessment of the fatigue performance of additively manufactured Ti–6Al–4V and perspective for future research. Int J Fatigue 85:130–143
Greitemeier D, Palm F, Syassen F, Melz T (2017) Fatigue performance of additive manufactured TiAl6V4 using electron and laser beam melting. Int J Fatigue 94:211–217
Kruth J-P, Deckers J, Yasa E (2008) Experimental investigation of laser surface remelting for the improvement of selective laser melting process. Paper presented at the 2008 international solid freeform fabrication symposium
Temmler A, Willenborg E, Wissenbach K (2011) Design surfaces by laser remelting. Phys Procedia 12:419–430
Mumtaz K, Hopkinson N (2010) Selective laser melting of thin wall parts using pulse shaping. J Mater Process Technol 210(2):279–287
Yadroitsev I, Smurov I (2010) Selective laser melting technology: from the single laser melted track stability to 3D parts of complex shape. Phys Procedia 5:551–560
Bidare P, Bitharas I, Ward R, Attallah M, Moore AJ (2018) Fluid and particle dynamics in laser powder bed fusion. Acta Mater 142:107–120
Qiu C, Panwisawas C, Ward M, Basoalto HC, Brooks JW, Attallah MM (2015) On the role of melt flow into the surface structure and porosity development during selective laser melting. Acta Mater 96:72–79
Martin AA, Calta NP, Khairallah SA, Wang J, Depond PJ, Fong AY, Thampy V, Guss GM, Kiss AM, Stone KH (2019) Dynamics of pore formation during laser powder bed fusion additive manufacturing. Nat Commun 10(1):1987
Gong H, Gu H, Zeng K, Dilip J, Pal D, Stucker B, Christiansen D, Beuth J, Lewandowski JJ (2014) Melt pool characterization for selective laser melting of Ti-6Al-4V pre-alloyed powder. Paper presented at the solid freeform fabrication symposium
Caprio L, Demir AG, Previtali B (2020) Observing molten pool surface oscillations during keyhole processing in laser powder bed fusion as a novel method to estimate the penetration depth. Addit Manuf 36: 101470
Ahn D, Kim H, Lee S (2009) Surface roughness prediction using measured data and interpolation in layered manufacturing. J Mater Process Technol 209(2):664–671
Dai D, Gu D (2015) Tailoring surface quality through mass and momentum transfer modeling using a volume of fluid method in selective laser melting of TiC/AlSi10Mg powder. Int J Mach Tools Manuf 88:95–107
Khairallah SA, Anderson A (2014) Mesoscopic simulation model of selective laser melting of stainless steel powder. J Mater Process Technol 214(11):2627–2636
Xia M, Gu D, Yu G, Dai D, Chen H, Shi Q (2016) Influence of hatch spacing on heat and mass transfer, thermodynamics and laser processability during additive manufacturing of Inconel 718 alloy. Int J Mach Tools Manuf 109:147–157
Shrestha S, Rauniyar S, Chou K (2019) Thermo-fluid modeling of selective laser melting: single-track formation incorporating metallic powder. J Mater Eng Perform 28(2):611–619
Yadroitsev I, Gusarov A, Yadroitsava I, Smurov I (2010) Single track formation in selective laser melting of metal powders. J Mater Process Technol 210(12):1624–1631
Mumtaz K, Hopkinson N (2010) Selective laser melting of Inconel 625 using pulse shaping. Rapid Prototyp J
Cheng B, Li X, Tuffile C, Ilin A, Willeck H, Hartel U (2018) Multi-physics modeling of single track scanning in selective laser melting: powder compaction effect. Paper presented at the 29th annual international solid freeform fabrication symposium—an additive manufacturing conference
Xiang Y, Zhang S, Wei Z, Li J, Wei P, Chen Z, Yang L, Jiang L (2018) Forming and defect analysis for single track scanning in selective laser melting of Ti6Al4V. Appl Phys A 124(10):685
Gu H, Wei C, Li L, Han Q, Setchi R, Ryan M, Li Q (2020) Multi-physics modelling of molten pool development and track formation in multi-track, multi-layer and multi-material selective laser melting. Int J Heat Mass Transf 151:119458
Acknowledgements
This study is supported by Navy STTR Program (Contract No. N68936-20-C-0023). The authors acknowledge the technical support from Additive Manufacturing Institute of Science and Technology (AMIST) at University of Louisville.
Author information
Authors and Affiliations
Corresponding author
Editor information
Editors and Affiliations
Rights and permissions
Copyright information
© 2021 The Minerals, Metals & Materials Society
About this paper
Cite this paper
Zhang, S., Shrestha, S., Chou, K. (2021). On Mesoscopic Surface Formation in Metal Laser Powder-Bed Fusion Process. In: TMS 2021 150th Annual Meeting & Exhibition Supplemental Proceedings. The Minerals, Metals & Materials Series. Springer, Cham. https://doi.org/10.1007/978-3-030-65261-6_14
Download citation
DOI: https://doi.org/10.1007/978-3-030-65261-6_14
Published:
Publisher Name: Springer, Cham
Print ISBN: 978-3-030-65260-9
Online ISBN: 978-3-030-65261-6
eBook Packages: Chemistry and Materials ScienceChemistry and Material Science (R0)