Abstract
Graphene oxide (GO)/carbon nanotube (CNT)/polypropylene (PP) nanocomposite materials were prepared by an epoxy resin (EP) using hand lay-up process. To enhance the mechanical properties and microstructure using 3-glycidyl ether oxy-propyl trimethoxysilane coupling agent in a one-step dipping coating process, the epoxy/polypropylene/carbon nanotube (EP-PP-CNT) functionalized composite with high bonding strength was created at the hierarchical structure, whereas reduced graphene oxides have been mingling within the epoxy resin. The solid-phase change structure was observed in an epoxy/polypropylene/graphene oxide/carbon nanotube (EP-PP-GO-CNT) functionalized composite, and the outer surface layer did not form the secondary dispersion. The tensile strength of EP-PP-GO-CNT functionalized samples was enhanced, reaching the yield point and elongation ratio of 38.1 MPa; moreover, epoxy/polypropylene/graphene oxide (EP-PP-GO) functionalized samples underwent ductility fractures. The average hardness value of EP (70%) blended with functionalized PP (10%), GO (10%) and CNT (10%) was highly present at 124 (Shore-D) in the outer surface layer. The three-point bending tests clearly indicated that the highest flexural modulus and flexural strength were observed in all composite materials. The microstructure was conducted on EP-PP-GO, EP-PP-CNT, and EP-PP-GO-CNT functionalized composites by scanning electron microscopy (SEM) and energy-dispersive spectroscopy (EDS), respectively. The nanocomposites friction and wear were reduced due to the significant concentrations of functionalized GO, PP, and CNTs.
Graphical abstract

Similar content being viewed by others
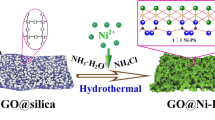
Explore related subjects
Discover the latest articles, news and stories from top researchers in related subjects.Avoid common mistakes on your manuscript.
Introduction
To produce a nanocomposite material with enhanced mechanical properties, composites must have nanofillers with a high surface-to-volume ratio in a matrix [1, 2]. The matrix materials used in polymeric composites employ thermosetting polymer matrices because they are more rigid and stronger than thermoplastic polymers. Epoxy resin is the most often utilized as thermosetting matrix material because it has good mechanical properties and a high rate of adhesion with the reinforcement [3, 4]. It has also been utilized for high-performance service environments because of its superior thermal, chemical, and electrical resistance properties [5, 6]. The quantity of nanofillers, the type, size, and shape of nanoparticles, as well as the synthesis and type of procedure, are all aspects that influence the quality level of nanocomposites [7], also a method of integrating nanoparticles directly into the matrix by chemical treatment, while using mechanical stirring and ultrasonic vibrations during the mechanical powder dispersion process. By functionalized nanoparticle surfaces, it is possible to increase particle/matrix interaction while decreasing particle affinities [8]. In fact, the surface treatment with a silane coupling enhances the interaction with the inorganic filler through the hydrolysable group while adhering to the matrix through its organic end. As a result, the effective reinforcing process forms a new filler–matrix interface [9, 10]. While many works have been carried out on epoxy-based systems, the tribological characterization and microstructure of hybrid functionalized nanocomposite epoxy have not been addressed in any work, and there have been limited developments in the functionalized arena.
Over the last decade, researchers have acquired desirable properties of the epoxy matrix through hybrids involving the use of carbon nanotubes, ceramics, hard oxides and carbides, graphene, polymers, and/or mineral silicates [11]. The mechanical characteristics of graphene oxide/epoxy nanocomposite were examined by Eqra et al. [12]. They suggested that GO content has the best composite properties due to its contribution to toughening, which serves as a barrier to stop the spread of cracks and their ion. Wan et al. [13] tried to improve the thermal and mechanical properties of silane-f-GO/epoxy composites. In comparison to pure epoxy and GO/epoxy composites, the silane-f-GO nanocomposite shows greater tensile and flexural strengths, as well as fracture toughness, and its glass transition temperature (150.5 °C) and thermal breakdown temperature (600 °C) increase. The applications of functionalized 0.5% (by wt) graphene oxide nanocomposite lower the average coefficient from 0.567 to 0.408 and reduce the wear rate by 75% compared to the average wear rate of pure epoxy [14]. The load transmission capacities between the epoxy resin and the functionalized CNT are examined using the pull-out method [15]. By adding amino groups with cross-linking interconnections in the CNT composite, their load transfers are enhanced over the pure CNT–epoxy composite by 5660.80%, respectively. Another author [16] has increased the tensile strength to 7.2%, 11.2%, 11.4%, and 14.2% for raw CNTs, carboxylates CNTs, octadecyl amide-functionalized CNTs, and hydroxylates CNTs, respectively, at 0.5% (by wt) CNT loading. Furthermore, functionalized CNTs-OH increased the glass transition temperature by 34%. Graphene oxide, carbon nanotubes, and their hybrids were used as reinforcements in the development of carbon nanofiller-based HAP composites in Jyoti et al. [17]. Among the composites taken into account here, the GCNTs composites exhibit the least plastic deformation during the indentation process, and as a result, they have the highest hardness value. Similar increases are also seen in the elastic modulus.
Many research works using various kinds of polymers loaded with graphene oxide and CNTs to evaluate mechanical behavior have been published in the literature. The primary emphasis of our study is on developing both single-filler (nanocomposite), and multi-filler (hybrid nanocomposite) reinforcing the pure epoxy matrix with nanometer-sized graphene oxide, carbon nanotubes, and polypropylene fillers. According to the authors’ knowledge, there are no studies on the mechanical and tribological behavior of silane-functionalized graphene oxide, CNTs, and polypropylene-filled epoxy polymers. The microstructure of the filler loading was simultaneously considered in this work.
Experimental
Materials and methods
The present studies were carried out on reduced graphene oxide (diameter of 20–30 nm and a purity of more than 95%). Carbon nanotube (diameter of 20–30 nm and a purity of more than 97%) and polypropylene (average particle size of 20–30 nm, ρ 0.87 g/mL) were purchased from Sigma Aldrich, Chennai, India, whereas epoxy resin was purchased from Araldite, Chennai, India. The mechanical properties and microstructure were improved using a 3-glycidyl-ether-oxy-propyl trimethoxysilane coupling agent (Sigma Aldrich, Chennai, India) in the dip coating process, as shown in Fig. 1. The nanomaterials utilized for the preparation of nanocomposites with better bonding structure were formed at 90:10 ratio using epoxy resin and a mixed hardener ratio, and making the nanocomposite of epoxy resin with 3-glycidyl ether oxy-propyl trimethoxysilane functionalized nanomaterials. The material composition used in this experiment is shown in Table 1. The 95–65% epoxy, 10–2.5% functionalized polypropylene, 10–2.5% functionalized graphene oxide, and 10–2.5% of single wall carbon nanotubes were prepared to matrix composite, which are stirred for 3 to 4 min at a rotation speed of 500 rpm using stirred machinery, whereas four different ratios were followed in the nanocomposite making by hand lay-up methods. The 200 mm × 100 mm × 3 mm thick composite was created at room temperature of 25 ºC.
Microstructure and mechanical properties
The different types of nanocomposite were prepared in 10 mm × 10 mm × 3 mm thickness dimensions for the microstructure studies (Carl Zeiss-V18, Germany). The Instron 5567 of tensile test has been conducted in accordance to ASTM D3039 standards with dimensions of 175 mm × 25 mm × 3 mm, whereas a rate of strain of 1 mm/min was maintained to achieve the tensile test. The three-point flexural testing (Instron 5567) was carried out according to ASTM D790 with dimensions of 125 mm × 12.7 mm × 3 mm. The composites having undergone an impact test in accordance with ASTM D256, the impact energy absorption was assessed using a Charpy impact testing device (Deepak Poly Plast, India) with dimensions of 65 mm × 13 mm × 3 mm. The hardness (Shore-D) profile test was conducted at the outer surface of the nanocomposite materials. The dwell period of 15 s was maintained at regular intervals of 0.50 mm and was taken from the hardness value.
Tribology
GO-CNT-PP epoxy nanocomposites were tested for wear and friction force under dry sliding conditions using pin-on-disk equipment (Magnum Engineers, India) in accordance with ASTM G99. In this investigation, flat-ended specimen pins and EN8 hard disks were employed. Figure 2 illustrates the schematic arrangement of the pin-on-disk experiment. The tests were conducted at different loads between 10 and 50 N and sliding speeds between 1 and 5 m/s. Wear rates are calculated from weight loss measurements. The sliding wear information provided here is the mean of at least three runs. The following equation is used to compute the friction coefficient [18].
where Fs as the sliding friction, and L as the applied load. Wear mechanisms were studied on a worn surface morphology using electron microscopy (Carl Zeiss EVO 18).
Results and discussion
Microstructural studies
The silane-functionalized of the graphene oxide (GO)/carbon nanotube (CNT)/polypropylene (PP) was used to improve the bonding strength of the nanocomposite materials. The Si–OCH3- groups of silane molecules implied covalent bonding between 3-glycidyl ether, oxy-propyl trimethoxysilane, and interface of f-GO-CNT-PP/epoxy. Figure 3a–f clearly indicates the bonding strength of the outer and inner surface layers of nanocomposite. A composite material of EP (80%)–PP (10%)–GO (10%) using the silane process significantly improved the inner surfaces, whereas minor holes and cracks were not observed in the outer surface layers. The graphene oxide powder created the secondary phase and solid grain boundaries of the microstructure, moreover avoiding the debonding and minor crack of the outer surface layer. The EP (80%)–PP (10%)–CNT (10%) composite material was mixed with carbon nanotubes and they have been forming in multiple structures. The silane processes were additional in joining the polypropylene and carbon nanotubes to improve the mechanical properties, making better composite materials. The high crystallization structure was formed in the EP-PP-CNT materials, protecting the outer surface layer, and reducing the carbon rate of the microstructure.
To improve the bonding strength of the silane coating process, EP (85%)–PP (7.5%)–GO (7.5%), was used, while the recrystallization structure gradually reduced the inner surface layers and micro-cracks were formed in the outer surface layer [19]. The silane coating process has not changed the bonding strength of multiple carbon nanotube structures; moreover, the outer surface strength of EP (85%)–PP (7.5%)–CNT (7.5%) composite structure, compared to graphene oxide strength, has suddenly decreased. The elongation ratio has decreased in the microstructure areas. The EP (70%)–PP (10%)–GO (10%)–CNT (10%) with silane-functionalized was executed on the composite materials. Furthermore, the fine boundary structures generated during the 10% of PP/GO/CNT nanocomposites process have been incorporated into the epoxy resin, with a strong binding strength above 2.5–5%. The carbon nanotube element is fully transferred into the hierarchical structure [20]. The fine grain growth is observed in the carbon nanotube structures, and graphene oxide particles are mixed within epoxy resin, whereas in the inner microstructure, no other crack has been formed [21, 22].
Tensile properties
The tensile testing of the silane coating process using graphene oxide (GO)/carbon nanotube (CNT)/polypropylene (PP) and epoxy resin was accompanied in the composite materials. The tensile testing samples were prepared at the dimensionally specified 125 mm × 3 mm thickness to improve the elongation ratio, as shown in Fig. 4. The tensile strength of EP (80%)–PP (10%)–GO (10%) has been reached at 24.6 MPa, whereas EP (95%)–PP (2.5%)–GO (2.5%) has attained at 18.4 MPa. The silane-functionalized graphene oxide powder was mingling with the epoxy resin to improve the bonding strength of the outer surface layer. GO (10%) samples have been 8%, slightly rising the bonding strength and yield point compared to a GO (5%) sample. Polypropylene and graphene oxide powder have not formed a proper bonding strength, and the elongation ratio has decreased in the outer surface layer. The low amount of carbon nanotubes is present in the EP (95%)–PP (2.5%)–CNT (2.5%) materials, but the elongation ratio is being highly observed in the 2.5% CNT materials compared to the 10% graphene oxide materials. The silane coupling has been fully blended into the carbon nanotubes powder sample, while an EP (80%)–PP (10%)–CNT (10%) sample is being grasped at 28.4 MPa. In addition to silane coupling being helpful to epoxy resin, carbon nanotubes and polypropylene powder have created the pulp phase, and strong bonding strengths have formed in the outer and inner surface layers of the composite materials. The carbon nanotubes had multiple structure formations that were helpful in improving the elongation and yield point of the composite outer and inner surface layers [23]. The 2.5–10% carbon nanotubes structure abruptly increased the tensile strength of the materials; additionally, 2.5–10% graphene oxide powder has been gradually increasing the tensile strength. The tensile strength of an EP (92.5%)–PP (2.5%)–GO (2.5%)–CNT (2.5%) sample was reached at 29.6 MPa, but graphene oxide was not dominant in the composite materials, where carbon nanotube powder has been found to retain the stability of a twin boundary structure. The major impact was produced in the graphene oxide and carbon nanotube materials within composite materials, but polypropylene powder was fully transformed into the pulp phase. The silane coupling and polypropylene powder were better reacted within graphene oxide and carbon nanotube structures, and the highest elongation of the tensile test sample was reached at 38.1 MPa. EP (70%)–PP (10%)–GO (10%)–CNT (10%) compositions have slightly stronger bonding than EP (85%)–PP (5%)–GO (5%)–CNT (5%), whereas the silane coupling coating process was improved with the multiple nanostructures.
Flexural strength
Flexural studies were carried out at ASTM D790 by dimensions of 125 mm × 12.7 mm × 3 mm using the silane-functionalized process for composite materials. The three-point studies were executed on the composite material to identify the bonding strength and microstructure properties. The elongation ratio of the composite materials improved with the silane coating methods. Flexural result of EP (95%)–PP (2.5%)–GO (2.5%) composite was extended at 34.7 MPa, whereas EP (85%)–PP (7.5%)–GO (7.5%) composition decreased at 34.5 MPa. The PP (5%) and GO (5%) elements achieved better results at 37.8 MPa. The high crystallization structure was formed in the inner and outer surface layers, which meant that PP and GO were properly mingling in the bonding properties. The EP (80%)–PP (10%)–GO (10%) composition was extended to 41.5 MPa. Flexural properties were highly present in polypropylene and graphene oxide, while epoxy and silane coating processes slightly increased the elongation ratio of the composite materials [24]. The flexural strength of EP (95%)–PP (2.5%)–CNT (2.5%) with silane coupling was reached at 35.2 MPa, where secondary phase and solid-stage structure were formed at the outer and inner surface layers as shown in Fig. 5. The 5–10% carbon nanostructure and polypropylene powder were mixed within the silane coupling coating, while a nanophase layer and blinded structure were formed in the carbon nanotube composite [25].
The EP (80%)–PP (10%)–CNT (10%) composition gave better results compared to the graphene oxide nanopowders. The carbon nanotubes compared to graphene oxide powder, reached the highest elongation. It is 4–8% more than graphene oxide powder. The epoxy resin and silane coupling coating process was a major contributor to the bonding strength of EP (92.5%)–PP (2.5%)–GO (2.5%)–CNT (2.5%). The 2.5% carbon nanotube, graphene oxide, and PP structure enhanced the microstructure and mechanical properties and increased the elongation of the base material. Flexural strength was slightly lowered by 5% of nanoparticles compared by 2.5% of nanoparticles, whereas the outer and inner surface layers have been mainly dislocated in the structure. The flexural strength of EP (70%)–PP (10%)–GO (10%)–CNT (10%) composite was attained at 53.9 MPa, while the outer surface was not collapsed in the composite materials and improved the elongation of the flexural strength.
Impact strength
The ASTM D256 standard for impact strength studies was carried out on the graphene oxide/carbon nanotube/polypropylene nanocomposites materials. The impact strength of epoxy resin, polypropylene, and graphene oxide composites was not properly observed. The microstructure was heavily damaged after impact strength, while the crystal structure was fully collapsed in the outer surface layer. The EP with 2.5% PP and GO samples had very low impact strengths reaching at 14 J/m2. The 5–10% of PP and GO reacting with the silane coupling coating process creates better strength. The silane coupling coating process could create the strong bonding of the composite materials, and 5–10% PP and GO have observed an increase in impact strength of 7–8%. The impact strength clearly indicated that carbon nanotubes compared to graphene oxide nanomaterials, increased impact strength. The silane and epoxy resin were directly mingling with the PP and CNT that were not formed in the colloidal phase of the inner and outer surfaces. The PP (10%)–CNT (10%) coating processes with silane coupling produced a strong bond with 80% epoxy resin, but 5–7.5% PP and CNT materials somewhat created the crystal structure of the outer surface. The 2.5%, 5%, and 7.5% PP and GO materials were not stable in the microstructure process, which is why their impact strength was reduced compared to the CNT composites. The impact strength of EP (92.5%)–PP (2.5%)–GO (2.5%)–CNT (2.5%) was reached at 49 J/m2. The EP (85%)–PP (5%)–GO (5%)–CNT (5%) was achieved at 64 J/m2 compared to the GO composition, which increased by 22%, as shown in Fig. 6. The 5% of silane-functionalized nanomaterials had extremely strong bonding strengths and created the microstructure. The impact strength of 5% PP, GO, and CNT materials was achieved at 64 J/m2, and boundary structure and bonding properties were gradually rising in the outer and inner surface layers. The EP (70%)–PP (10%)–GO (10%)–CNT (10%) composition was achieved at the highest impact strength of 82 J/m2, whereas silane coupling coating processes improved the adhesion texture to increase the microstructure and mechanical properties of the nanocomposites.
Hardness test
The epoxy resin and silane coupling processes were helpful in improving the hardness value of the nanocomposite materials. The 5–10% of PP and GO nanocomposite samples had slightly increased hardness values compared to the 2.5% nanomaterials, as shown in Fig. 7. The hardness values of EP (95%)–PP (2.5%)–CNT (2.5%) nanocomposite materials were reached at 87 D. The silane coupling of PP and GO composition was highly bonded, while the microstructure clearly indicated that the lattice structure has been formed in the outer surfaces.
The EP, PP, and CNT processes were mixed within silane coupling, and that process was protecting the outer and inner surface layers. The hardness value of the PP and CNT compositions compared to the graphene oxide nanopowder was highly increased. The added PP and CNT of 5–10% nanomaterials increased the bonding strength of the outer surface layer. The CNT nanomaterials avoided the holes and cracks of the outer surfaces. The hardness value of EP (92.5%)–PP (2.5%)–GO (2.5%)–CNT (2.5%) nanocomposite materials was reached at 112 D. At the same time, 5% of the PP, GO, and CNT compositions of hardness value compared to the 2.5% composition was gradually rising up to 108 D. The EP (70%)–PP (10%)–GO (10%)–CNT (10%) composite materials reached at the 124 D highest hardness value. On the outer and inner surface of the 10% nanomaterial samples, no cracks, holes, dimples, and voids were observed.
Tribological properties
Figures 8 and 9 show the wear behavior in terms of weight loss with respect to the applied load and sliding speed of graphene oxide/carbon nanotube/polypropylene nanocomposites materials. From the observation, higher wear resistance is obtained by incorporation of silane-functionalized PP, GO, and CNT in the epoxy matrix. As the load increases, the sliding causes the outer surface to crack and the temperature between them to rise. This increased the wear loss in composites and adhered to the EN8 disk, as shown in Fig. 8. According to the findings, the inclusion of functionalized GO and CNT particles lowered the specific wear rate of the composite. In comparison, the wear rate of the EP (70%)–PP (10%)–GO (10%)–CNT (10%) composite was 0.0026 g at 50 N. Overall, the increased loading of functionalized GO and CNT resulted in enhanced wear resistance as well as increased hardness. In this respect, the silane has created strong interfacial bonding between the matrix and nanofiller at higher-loading composites. Additionally, the use of GO and CNT will increase wearability by evenly distributing stress across the matrix [26].
At a constant applied load of 10 N, Fig. 9 shows the wear rate in relation to the sliding speed response of graphene oxide/carbon nanotube/polypropylene nanocomposites. With an increase in sliding velocity, it demonstrates a rising wear rate. Due to the fact that increased rubbing speeds cause the composites’ yield strength and Youngs modulus to drop and affect the wear resistance, surface cracks that occur at lower velocities are more common [27]. The presence of functionalized PP caused continuous slip bands to develop, which led to the composite being lost after prolonged abrasion cycles. When compared to other compositions, the EP (70%)–PP (10%)–GO (10%)–CNT (10%) composition achieved the least amount of weight loss, and the variance was likewise minimal as the velocity increased because the applied stress is less than the interface bonding strength threshold for the functionalized carbon nanotubes, graphene oxide, and polypropylene nanocomposites.
Figure 10 illustrates the response of sliding time and coefficient of friction of graphene oxide/carbon nanotube/polypropylene nanocomposites. The friction coefficient falls with increasing the loading of functionalized GO and CNTs and also decreases as the sliding duration rises, as shown in Fig. 10. The EP (95%)–PP (2.5%)–GO (2.5%) nanocomposite has a high coefficient of friction (0.66) for a short period of time (10 min) before it starts to reduce weight as a result of the transfer layer that has formed on the EN8 disk. While rubbing the interface between soft polymeric material and a hard metallic substance, a transfer film was created [22]. At a constant applied force of 30 N and a sliding speed of 1 m/s, the coefficient of friction decreases as functionalized GO and CNT loading increases in the EP matrix. The first source of an increase in coefficient of friction under dry sliding conditions might be abrasive wear occurring on the EP/GO/CNT/PP nanocomposites. It is reported that decreasing the direct contact between the EP and the disk results in a rise in the surface percentage of GO and CNTs. The self-lubrication of CNTs made it easier for them to slide between the mating metal surfaces, and lowering the friction coefficient [26].
The scanning electron microscope explored the dominant mechanisms of functionalized graphene oxide/carbon nanotube/polypropylene nanocomposites materials from worn out surfaces. Figure 11a and b shows the wear scars on the EP (70%)–PP (10%)–GO (10%)–CNT (10%) composite. All the other PP/CNT/GO loading materials had a similar wear mechanism that included interfacial and plastic deformation wear. It demonstrates that significant defects were noticed, including wear debris, micro-cracks, and dispersion of functionalized PP/CNT/GO components. This typically occurs because the polymer is transferred to the harder surface by adhesion and then it is removed as wear debris when a polymer and a hard surface (disk) slide over together [28]. Cohesive wear is shown in Fig. 11, which was discovered by looking at abrasive markings on the worn surface. The plastic deformation of the polymer surface and subsurface, which is brought about by the passing of tough patches on the disk, is what identifies this type of wear.
Conclusion
The current study examines the microstructure, mechanical, and wearing aspects of single-step dipping silane-functionalized graphene oxide/carbon nanotube/polypropylene into an epoxy matrix composite. The following findings are reached based on the experimental analysis:
-
Incorporations of carbon nanotubes, graphene oxide, and polypropylene have been silane-functionalized, which provide superior nanocomposite with enhanced mechanical characteristics. From the microstructural analysis, the fine grain growth in the carbon nanotube (CNT) structures was observed and the addition of graphene oxide (GO) particles to epoxy resin, composite fracture was prevented during mechanical stress.
-
The mechanical tests found that the functionalized graphene oxide and carbon nanotube structures were best for the reaction of the silane coupling and polypropylene powder, with the EP (70%)–PP (10%)–GO (10%)–CNT (10%) composite achieving the highest elongation of the tensile test at 38.1 MPa, the highest flexural strength at 53.9 MPa, the highest impact strength at 82 J/m2, and the highest hardness value at 124 D when compared to other composites.
-
The EP (70%)–PP (10%)–GO (10%)–CNT (10%) composite demonstrated minimal wear rate at 50 N of 0.0026 g, in contrast to other composites, because addition of functionalized GO and CNT particles reduce the composite's wear rate. It was observed that EP (95%)–PP (2.5%)–GO (2.5%) nanocomposite has a high coefficient of friction (0.66) for a short period of time (10 min).
Data availability
No data was used for the research described in the article.
References
Fu S, Sun Z, Huang P, Li Y, Hu N (2019) Some basic aspects of polymer nanocomposites: a critical review. Nano Mater Sci 1:2–30
Sanusi OM, Benelfellah A, Aït Hocine N (2020) Clays and carbon nanotubes as hybrid nanofillers in thermoplastic-based nanocomposites—a review. Appl Clay Sci 185:105408
Shankarganesh PSP, Muralikannan R, Selvabharathi R, Karuppasamy R (2019) Investigation of tensile, flexural and impact properties of Neem-Indian almond hybrid fiber based epoxy composites. Mater Res Express 6:085322
Thirukumaran M, Kannan LV, Sankar I (2018) Study on mechanical properties of glass wool/epoxy reinforced composite. Int J Comput Aided Eng Technol 10:15–25
Sukanto H, Raharjo WW, Ariawan D, Triyono J, Kaavesina M (2021) Epoxy resins thermosetting for mechanical engineering. Open Eng 11:797–814
Mousavi SR, Estaji S, Kiaei H, Mansourian-Tabaei M, Nouranian S, Jafari SH, Ruckdäschel H, Arjmand M, Khonakdar HA (2022) A review of electrical and thermal conductivities of epoxy resin systems reinforced with carbon nanotubes and graphene-based nanoparticles. Polym Test 112:107645
George J, Ishida H (2018) A review on the very high nanofiller-content nanocomposites: their preparation methods and properties with high aspect ratio fillers. Prog Polym Sci 86:1–39
Chan JX, Wong JF, Petrů M, Hassan A, Nirmal U, Othman N, Ilyas RA (2021) Effect of nanofillers on tribological properties of polymer nanocomposites: a review on recent development. Polymers (Basel) 13:1–47
Yao SS, Ma CL, Jin FL, Park SJ (2020) Fracture toughness enhancement of epoxy resin reinforced with graphene nanoplatelets and carbon nanotubes. Korean J Chem Eng 37:2075–2083
Davachi SM, Heidari BS, Sahraeian R, Abbaspourrad A (2019) The effect of nanoperlite and its silane treatment on the crystallinity, rheological, optical, and surface properties of polypropylene/nanoperlite nanocomposite films. Compos Part B Eng 175:107088
Thakur AS, Sharma N, Kango S, Sharma S (2020) Effect of nanoparticles on epoxy based composites: a short review. Mater Today Proc 44:4640–4642
Eqra R, Moghim MH, Eqra N (2021) A study on the mechanical properties of graphene oxide/epoxy nanocomposites. Polym Polym Compos 29:S556–S564
Wan YJ, Gong LX, Tang LC, Wu LB, Jiang JX (2014) Mechanical properties of epoxy composites filled with silane-functionalized graphene oxide. Compos Part A: Appl Sci Manuf 64:79–89
Wu H, Liu C, Cheng L, Yu Y, Zhao H, Wang L (2020) Enhancing the mechanical and tribological properties of epoxy composites: via incorporation of reactive bio-based epoxy functionalized graphene oxide. RSC Adv 10:40148–40156
Song Z, Li Y, Yang B (2021) The interfacial load-transfer enhancement mechanism of amino-functionalised carbon nanotube reinforced epoxy matrix composites: a molecular dynamics study. Compos Sci Technol 209:108790
Roy S, Petrova RS, Mitra S (2018) Effect of carbon nanotube (CNT) functionalization in epoxy-CNT composites. Nanotechnol Rev 7:475–485
Jyoti J, Kiran A, Sandhu M, Kumar A, Singh BP, Kumar N (2021) Improved nanomechanical and in-vitro biocompatibility of graphene oxide-carbon nanotube hydroxyapatite hybrid composites by synergistic effect. J Mech Behav Biomed Mater 117:104376
Manoharan T (2022) Experimental and statistical evaluation of wear and friction behaviour on AA 7475/GFRP multi-stacked fibre metal laminates. Proc Inst Mech Eng Part J: J Eng Tribol 237:199–209
Keyte J, Pancholi K, Njuguna J (2019) Recent developments in graphene oxide/epoxy carbon fiber-reinforced composites. Front Mater 6:1–30
Schütt F, Signetti S, Krüger H, Röder S, Smazna D, Kaps S, Gorb SN, Mishra YK, Pugno NM, Adelung R (2017) Hierarchical self-entangled carbon nanotube tube networks. Nat Commun 8:1–10
Papageorgiou DG, Kinloch IA, Young RJ (2017) Mechanical properties of graphene and graphene-based nanocomposites. Prog Mater Sci 90:75–127
Ranjkesh Adarmanabadi S, Jafari M, Hosseini Farrash SM, Heidari M (2021) Effect of nano clay, nano-graphene oxide and carbon nanotubes on the mechanical and tribological properties of crosslinked epoxy nanocomposite. PLoS ONE 16:1–15
Duan Q, Wang S, Wang Q, Li T, Chen S, Miao M, Zhang D (2019) Simultaneous improvement on strength, modulus, and elongation of carbon nanotube films functionalized by hyperbranched polymers. ACS Appl Mater Interf 11:36278–36285
Alo OA, Otunniyi IO (2021) Comparative study of flexural and physical properties of graphite-filled immiscible polypropylene/epoxy and high-density polyethylene/epoxy blends. Polym Polym Compos 29:S1103–S1112
Xin F, Li L (2012) The role of a silane coupling agent in carbon nanotube/polypropylene composites. J Compos Mater 46:3267–3275
Yetgin SH (2021) Impact of multi-walled carbon nanotube and graphene oxide on abrasive wear performance of polypropylene. Res Eng Struct Mater 7:157–171
Yetgin SH (2020) Tribological properties of compatabilizer and graphene oxide-filled polypropylene nanocomposites. Bull Mater Sci 43:4–11
Myshkin N, Kovalev A (2018) Adhesion and surface forces in polymer tribology—A review. Friction 6:143–155
Author information
Authors and Affiliations
Corresponding author
Rights and permissions
Springer Nature or its licensor (e.g. a society or other partner) holds exclusive rights to this article under a publishing agreement with the author(s) or other rightsholder(s); author self-archiving of the accepted manuscript version of this article is solely governed by the terms of such publishing agreement and applicable law.
About this article
Cite this article
Raja, G.M., Vasanthanathan, A. & Selvabharathi, R. Effect of one-step dipping coating process on microstructure and tribology of polypropylene/graphene oxide/carbon nanotube nanocomposites. Iran Polym J 32, 739–748 (2023). https://doi.org/10.1007/s13726-023-01161-0
Received:
Accepted:
Published:
Issue Date:
DOI: https://doi.org/10.1007/s13726-023-01161-0