Abstract
The grains of a hypereutectic Al-26 wt.% Si alloy were drastically refined by multi-pass equal-channel angular pressing (ECAP). Compression deformation characteristics of the alloy with different microstructure were examined at two dynamic strain rates (700, 1000 s−1) by a split-Hopkinson pressure bar system and at a quasi-static strain rate (0.001 s−1) by a universal testing machine, respectively. The results reveal that the Al-26 wt.% Si alloy is strain-rate sensitive under those compression conditions, i.e., the initial yield stress and the flow stress considerably increase with the strain rate. Grain refinement through ECAP improves the strain-rate sensitivity of the alloy. With rising the ECAP temperature, the yield stress of the ultrafine-grained alloy decreases but the strain value increases during dynamic compression.
Similar content being viewed by others
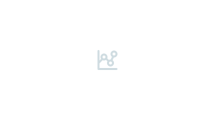
Avoid common mistakes on your manuscript.
Introduction
Recently, there are growing interests in hypereutectic Al-Si alloy because of its good wear resistance, low thermal-expansion coefficient, good amenability to casting, and relatively low cost (Ref 1, 2). Although cast Al-Si alloy has wide applications for lightweight components in automotive, aerospace, and construction industries, a critical limitation of its application is low toughness due to excessive growth of the primary Si particles and unfavorable shrinkage behavior in the melt (Ref 3, 4). This inherent difficulty of casting Al-Si alloy could be overcome by severe plastic deformation (SPD) procedure to obtain the ultrafine-grained (UFG) Al matrix with relatively fine primary Si crystals (Ref 5). Up to now, equal-channel angular pressing (EACP) process has been proved as one of the most effective SPD techniques (Ref 6), which could endow exceptional mechanical and/or physical advantages without remarkably changing the geometries of bulk metals (Ref 7-9). Our previous studies indicated that the impact toughness of an ECAP-processed (ECAPed) Al-23 wt.% Si alloy increased markedly, and the absorbed energy value measured by Charpy impact testing was 18 times higher than that of the as-cast alloy (Ref 5). This unusual phenomenon makes hypereutectic Al-Si alloy subjected to ECAP very attractive for engineering application.
From a practical design viewpoint, it is necessary to characterize mechanical properties of hypereutectic Al-Si alloy at a wide strain-rate range. Although plenty of researches have been done in recent years on exceptional mechanical behaviors of ECAPed metallic materials in quasi-static states at low strain rates (≤1 s−1) (Ref 10, 11); however, there are few reports available on their dynamic response at the high strain rates (>102 s−1). The responses of most metallic materials under dynamic loading are different from those under monotonic or quasi-static loading (Ref 12-17), because the temperature in the metal’s interior would remarkably change due to the adiabatic phenomenon during dynamic loading conditions. Undoubtedly, the systematic investigation and characterization for dynamic mechanical behaviors of the ECAPed metallic materials are important.
In the present work, compressive responses at room temperature of a hypereutectic Al-26 wt.% Si alloy subjected to different ECAP passes were investigated at two dynamic strain rates (700, 1000 s−1) by a split-Hopkinson pressure bar (SHPB) system and at a quasi-static strain rate (0.001 s−1) by a universal testing machine, respectively. The aim is to find the effect of microstructure characteristic on the deformation mechanism of this alloy under dynamic loading.
Experimental
In this work, the as-received material was a commercial Al-26 wt.% Si alloy. The chemical composition of the hypereutectic alloy is 25.8 wt.% Si, 0.3 wt.% Fe, and the balance of Al. A multi-pass ECAP procedure was employed to achieve the UFG structure. The ECAP processing was conducted with a die having a channel angle of 90° and through route A (Ref 18). The ECAP billets were 19.5 mm in diameter and 40 mm in length. The billets were continuously processed by ECAP from 1 to 16 passes at two different temperatures (573 and 623 K), respectively.
Compression properties of the as-received alloy with various ECAP passes were examined at three representative stain rates at room temperature. Cylindrical specimens used for dynamic compression testing or quasi-static compression testing were 16 mm in diameter and 8 mm in height, which were cut from the ECAP billets along with the longitudinal direction. A CMT5105 universal testing machine was used to perform quasi-static compression at the strain rate of 0.001 s−1. Dynamic compression tests were carried out using a SHPB at the high strain rate of 700 and 1000 s−1, respectively. This device, which details were given by Deshpande (Ref 19), utilizes elastic wave in two pressure bars to determine the relative displacement of two head faces of the specimen and the stress during impact testing.
The specimens before and after dynamic compression were characterized by an optical microscope (Olympus, BX51M, Japan) and a JEOL JSM-5200 scanning electron microscope (SEM) with energy dispersive spectroscope (EDS). Before microstructure observation, the specimens were polished and then etched with a 0.5% HF solution. Our previous investigation (Ref 5) presented that the average grain or grain fragment diameter of a hypereutectic Al-Si alloy was about 150 nm after multi-pass ECAP, and these grains or grain fragments had high-angle grain boundaries (HABs). Hence, the present work was focused on the size distribution of primary silicon particles in the UFG Al matrix. The size distribution of silicon particles in various samples was investigated by processing the images of the SEM morphologies via Image-Pro Plus 6.0 software. Considering the geometrical inhomogeneity of silicon particles, the average diameter was used to address the size distribution after various ECAP passes.
Experimental Results and Discussion
Microstructure Characterization
Optical micrographs of the as-cast Al-26 wt.% Si alloy at a low magnification and a high magnification are shown in Fig. 1(a) and (b), respectively. The casting defects were mainly the shrinkage cavities in the Al matrix and brittle primary silicon particles with random pores, which can be regarded as inclusions. Figure 1 presents that there are some shrinkage cavities in the hypereutectic Al-Si alloy (marked by the arrows of A in Fig. 1). Many large primary silicon particles with random pores exist in the as-cast alloy, and the formation of pores (marked by arrow B in Fig. 1b) is due to the brittleness of primary silicon particles. The shrinkage cavities in the Al matrix and the random pores of the primary silicon particles could be distinguished with metallographic morphology. Figure 2 presents the silicon crystals size distribution of the Al-26 wt.% Si alloy in various states. The average size of primary Si particles of the as-cast alloy is about 35 µm, and the size distribution is uneven. The existence of random pores can make the breakage of large primary Si particles easy during ECAP (Ref 20).
Figure 3 illustrates optical micrographs of the ECAPed Al-26 wt.% Si alloy, where (a), (c), and (e) were processed at 573 K for 4, 8, and 16 passes, respectively; (b), (d), and (f) were processed at 623 K for 4, 8, and 16 passes, respectively. After the initial 4 passes at 573 K (as shown in Fig. 3a), the large primary Si particles were fragmentized and became uniformly dispersive in comparison with the as-cast alloy (shown in Fig. 1a). The average size of primary Si particles decreased to 25 µm after 4 passes and obviously decreased with increasing number of passes up to 16. After 8 passes of ECAP at 573 K, the average size of the Si particles was below 15 µm. With increasing the ECAP pass to 16 at 573 K, most of the primary Si particles were fragmentized into very small particles (<10 µm) and less micro-cracks were found in the microstructure (as shown in Fig. 3e). It is obvious that the multi-pass ECAP results in the fragmentation and homogenous dispersion of primary Si particles. On the other hand, the alloy was processed by ECAP at 623 K to avoid the formation of micro-cracks or cavities. It is obvious that although the higher temperature results in the bigger Si particle size, the residual cavities are less (as shown in Fig. 3f). This result indicates that increasing the pressing pass at a high temperature may improve the toughness of the ECAPed Al-26 wt.% Si alloy.
Dynamic Compression Properties
Macroscopic observation showed that some macro-cracks appeared on the surface of the as-cast samples after SHPB testing, but no crack was found on the surface of the ECAPed samples. The results indicate that the multi-pass ECAP processing can improve toughness and dynamic compression properties of the hypereutectic Al-26 wt.% Si alloy. Figure 4 presents the stress-strain curves of the as-cast alloy compressed at the strain rate of 0.001, 700, and 1000 s−1, respectively. The alloy exhibits the typical strain-rate sensitivity characteristics similar to the dynamic-compressed 5056 Al alloy (Ref 21) and the SiCp/Al composite (Ref 22), namely the initial yield strength and the flow stress at a constant strain increase with rising the strain rate. When the strain rate increases from 0.001 to 700 s−1, the yield strength of the as-cast sample rises from 161 to 180 MPa. After initial yielding, the flow stress of all the samples at a constant strain increases monotonically with different strain hardening rates. Moreover, total strain and strain hardening effect of the as-cast alloy obviously increase under dynamic compression at 1000 s−1. Similar stress-strain curves at the strain rates of 700 and 1000 s−1 imply that the strain-rate hardening effect of the alloy is comparatively weaker than the strain hardening effect. Strain softening, caused by adiabatic heating and successive microstructural damage during dynamic compression, is not obvious in the stress-strain curves. It is thus clear that the total strains in these testing have been less than the hardening-softening transition strains, since the stress-strain curves are unchanged from the strain hardening stage to the strain softening stage.
Figure 5 presents the stress-strain curves at various strain rates of the ECAPed alloy, where (a), (b), and (c) were processed at 573 K for 4, 12, and 16 passes, respectively. The results show that the flow stress of the ECAPed alloy also considerably increases under dynamic loading. At unloading points of stress waves, the maximum strain for the 4-pass samples reaches 13.9% at 700 s−1 and 19.5% at 1000 s−1 (as shown in Fig. 5a), respectively. However, with increasing the ECAP pass, the strengthening effect at the strain rate ranging from 102 to 103 s−1 is comparatively weak and even an inverse strain-rate effect appears. Subsequently, the flow stress of the sample decreases gradually as the strain continuously increases. The stress-strain curves of the 12-pass sample at the strain rate between 700 and 1000 s−1 are also similar (as shown in Fig. 5b), but the strain near the unloading points of stress waves is significantly high at the strain rate of 1000 s−1. A declination of the hardening-softening transition strain is obviously observed on the stress-strain curve of the 16-pass sample at the strain rate of 1000 s−1 (in Fig. 5c). It suggests that the strain softening caused by adiabatic heating and damages overwhelms the strain hardening of plastic deformation.
The initial yield stress and the flow stress at a constant strain (ɛ = 5%) of the as-cast sample and the ECAPed samples at 573 K can be determined from Fig. 4 and 5, respectively. The initial yield stress of the as-cast sample and the 4-pass one are 180 and 161 MPa at the strain rate of 700 s−1, respectively. The yield stress value of the ECAPed Al-26 wt.% Si alloy further falls with more pressing passes. On the other hand, the initial yield stress of all the samples decreases when the strain rate is 1000 s−1. At the constant strain of 5%, the flow stress of the as-cast sample increases with the strain rate. The flow stress of the 16-pass sample is obviously lower than those of the samples for less passes, which are nearly identical at the constant strain.
Figure 6 presents stress-strain curves of the ECAPed samples for different passes at 573 and 623 K, respectively. At the given strain rate (1000 s−1), the initial yield stress and the flow stress decrease with increasing the ECAP temperature, but the declining trend of the ECAPed samples becomes less distinct with increasing the pressing pass. There are two main factors responsible for the declining trend: (1) dynamic recovery and recrystallization (Ref 23), which are easier at the high ECAP temperature and result in the slightly lower strength of the UFG Al matrix, and (2) the dislocation motion which is faster with increasing the ECAP temperature and results in lower large-angle grain boundaries. Due to complete dynamic recovery and recrystallization, the grains of the 16-pass samples processed at two different pressing temperatures are fine, uniform, and equiaxed, which provide good comprehensive mechanical properties. Because the increase of the ECAP pass weakens the effect of a high ECAP temperature, the stress-strain curves of the two 16-pass samples are almost overlapped at the strain rate of 1000 s−1.
The stress-strain curves at room temperature of the as-cast sample (in Fig. 4) were further compared with those of the samples ECAPed for different passes at 573 K (in Fig. 5). At the given strain rate of 1000 s−1, the initial yield stress of the as-cast sample is higher than those of the ECAPed ones. It is clear that coarse primary Si crystals with polygonal shape and the network eutectic Si crystals along the α-Al boundaries (as shown in Fig. 1) can inhibit intragranular dislocation motion and grain-boundary sliding in the as-cast alloy, and thus lead to the obvious deformation reinforcement effect and the higher yield stress. However, the maximum flow stresses of the ECAPed samples were higher than that of the as-cast one. The flow stresses of the ECAPed samples obviously increase with the increase of the strain, i.e., the ECAP process improves the strain hardening sensitivity of the Al-26 wt.% Si alloy. After primary 4 passes of ECAP, the maximum flow stress and the corresponding strain of the Al-26 wt.% Si alloy were significantly increase due to the combination of grain-boundary sliding and intragranular dislocation motion. When the ECAP pass reaches up to 16, the initial yield stress obviously decreases but the strain at the maximum flow stress markedly increases due to dynamic recovery and recrystallization. With increasing the pass of ECAP, dynamic mechanic properties of the Al-26 wt.% Si alloy tends to stabilization.
Strain Rate Sensitivity and Johnson-Cook Material Constants
Thermo-mechanical actions in the stress-strain curves of the Al-26 wt.% Si alloy under dynamic loading include strain hardening, strain-rate strengthening, and thermal softening caused by the adiabatic temperature increase. In order to estimate the strain rate sensitivity of the rate-dependent material during the high strain rate deformation, San Marchi et al. (Ref 15) quantified the strain-rate sensitivity parameter (R s) using the equation as follows:
where σ is the flow stress at a given plastic strain (5%), \( \dot{\upvarepsilon } \) is the strain rate with subscripts D, S referring to conditions of dynamic and quasi-static testing (0.001 s−1), and the asterisk refers to a reference strain rate of 0.001 s−1. Figure 7(a) and (b) present the variation of the flow stress of the Al-26 wt.% alloy with the strain rate at the given plastic strain of 6 and 10%, respectively.
At lower strains (below 5%), high strain rate flow stress data of SHPB testing do not show exact material property (Ref 24). The reason is that the deformation in the tested samples is inhomogeneous due to stress wave propagation (Ref 22). Herein, the R s value of the Al-26 wt.% Si alloy was calculated at ε = 6 and 10% according to the above equation. Figure 8 presents the variation of the strain-rate sensitivity parameter with the ECAP pass of the Al-26 wt.% Si alloy. The R s value of the as-cast sample at 700 s−1 is about 0.014 when the true strain is 6%. The value of the ECAPed alloy is about 0.043 after the initial 4 passes and remains unchanged after more ECAP passes at 573 K. It indicates that the multi-pass ECAP procedure improves the sensitivity of the strain-rate sensitive alloy, while the R s parameter initially increases and finally stabilizes with increasing the ECAP pass.
With the aim of predicting the response of a complex structure at a high strain rate by computer simulation, it is necessary to formulate an accurate constitutive relationship and obtain realistic material data. Johnson-Cook’s (J-C) material constitutive equation (Ref 25) has been developed to describe mechanical behaviors of metals under dynamic loading, which can be represented by the following:
where ε is the plastic strain, \( \dot{\upvarepsilon } \) is the strain rate (s−1), \( \dot{\upvarepsilon }_{0} \) is the reference strain rate (s−1), T is the temperature of the tested material (K), T m is the melting point of the tested material (K), and T r is room temperature (298 K). Coefficient A is the yield strength (MPa), B is the hardening modulus (MPa), C is the strain rate sensitivity coefficient, n is the hardening coefficient, and m is the thermal softening coefficient. Based on the quasi-static and dynamic compression test data of the alloy after various ECAP passes at 573 K and the as-cast counterpart, the J-C constants of the ECAPed Al-26 wt.% Si alloy are calculated and listed in Table 1. Table shows that the yield stress declines but the strain hardening ability enhances with increasing the ECAP pass of the Al-26 wt.% Si alloy. The strain-rate sensitivity coefficient (C) of the ECAPed alloy is higher than that of the as-cast one and gradually stabilizes with increasing the ECAP pass, which is similar to the change rule of the strain-rate sensitivity parameter.
Microstructure Observation of the Al-26 wt.% Si Alloy After Dynamic Compression
Figure 9 presents optical micrographs of the as-cast Al-26 wt.% Si alloy after SHPB dynamic compression tests. The dynamic compression makes a large number of holes and cracks in the as-cast samples. The splitting and interface opening of coarse primary Si particles are the main damage patterns of the as-cast alloy. Most of the damages are presented in the vicinity of the primary Si particles, and the damage degree increases with the increase of the strain rate. The coarse and brittle primary Si crystals with polygonal shapes are extremely uneven distributed and also badly wrecked the continuity of the α-Al matrix, and thus cause the inner or boundary cracks due to their inconsistent deformation with the α-Al phases. Besides, the casting defects (e.g., shrinkage porosity) are also vulnerable to the high velocity impact, which are firstly destroyed and formed the crack sources.
Figure 10 presents optical micrographs after dynamic compression of the Al-26 wt.% Si samples ECAPed at 573 K for various passes. At the same high strain rate, the cracks in the ECAPed samples are obviously less than those in the as-cast samples and decrease with increasing the ECAP passes. The more ECAP passes break the coarse primary Si crystals into fine particles, and thus dramatically reduce the fragmentation of the matrix and the stress concentration during the dynamic compression deformation. Furthermore, the multi-pass ECAP decreases the original casting defects. Therefore, dynamic mechanical properties of the ECAPed Al-26 wt.% Si alloy are improved due to those favorable factors. Thus, it is clear that grain refinement plays an important role in improving dynamic deformation behavior for the fragile structural metals.
Microstructure observation for the dynamic-compressed samples reveals that there are lots of large white areas in the Al matrix, especially at the high strain rate of 1000 s−1. Figure 11(a) presents SEM surface morphology after dynamic compression of the ECAPed sample for 16 passes at 573 K, while Fig. 11(b) and (c) present the EDS spectra of the white area and the Al matrix, respectively. As can be seen from the EDS spectra, the white area has a high oxygen content compared to the dark Al matrix area. One likely reason is that the local temperature of the sample rises immediately and promotes the oxidation of the Al matrix during dynamic compression at the high strain rate. The strain-stress curve of the 16-pass sample (as shown in Fig. 6c) reveals that the strengthening effect decreases with increasing the strain rate. At the high strain rate, the heat softening effect of the adiabatic compression is relatively stronger than the effect of both the strain hardening and the strain rate strengthening, and thus results in the local softening of the Al matrix and the large deformation. The microstructure feature of the 16-pass sample, which the fine Si particles are uniformly distributed in the UFG Al matrix, is easier to deform with the increase of the strain rate.
Conclusions
A hypereutectic Al-26 wt.% Si alloy was refined by ECAP for 4, 8, 12, and 16 passes at 573 and 623 K, respectively. Dynamic compression properties of the alloy before and after ECAP were investigated by a SHPB apparatus at the strain rates of 700 and 1000 s−1, in comparison with compression deformation characteristics at a quasi-static strain rate (0.001 s−1) .
-
(1)
The coarse α-Al grains and primary Si particles in the alloy are drastically refined by the ECAP process. After the initial 4 ECAP passes, the majority of the primary Si crystals are broken and some voids are formed around them. With increasing the ECAP passes, the size of the Si particles are decreased and the voids are reduced. There are only few voids in the ECAPed alloy after 16 passes.
-
(2)
The multi-pass ECAP procedure improves the sensitivity of the strain-rate sensitive Al-26 wt.% Si alloy. The strain rate sensitivity parameter obviously rises after the initial 4 ECAP passes but finally stabilizes with increasing the ECAP pass.
-
(3)
The yield stress of the ECAPed alloy is considerably lower than that of the as-cast one under dynamic compression. The maximal strain value before unloading increases with increasing the ECAP pass or the ECAP processing temperature. Those are due to the combined effects of the strain hardening, strain-rate strengthening and thermal softening caused by the adiabatic temperature rise.
-
(4)
During the dynamic compression, primary Si particle splitting and interface opening are the main damage patterns of the as-cast Al-26 wt.% Si alloy. Microstructure feature of the alloy after multi-pass ECAP procedure is easier to deform with increasing the strain rate under dynamic loading, when the interface opening between fine Si particles and the UFG Al matrix is the main damage pattern.
References
C.L. Xu, Y.F. Yang, H.Y. Wang, and Q.C. Jiang, Effects of Modification and Heat-Treatment on the Abrasive Wear Behavior of Hypereutectic Al-Si Alloys, J. Mater. Sci., 2007, 42, p 6331–6338
P.S. Mohanty and J.E. Gruzleski, Grain Refinement Mechanisms of Hypoeutectic Al-Si Alloys, Acta Mater., 1996, 44(9), p 3749–3760
P. Kapranos, D.H. Kirkwood, H.V. Atkinson, J.T. Rheinlander, J.J. Bentzen, P.T. Toft, C.P. Debel, G. Laslaz, L. Maenner, S. Blais, J.M. Rodriguez-Ibabe, L. Lasa, P. Giordano, G. Chiarmetta, and A. Giese, Thixo-forming of an Automotive Part in A390 Hypereutectic Al-Si Alloy, J. Mater. Process. Technol., 2003, 135, p 271–277
A. Bendijk, R. Delhez, L. Katgerman, Th.H. De Keijser, E.J. Mittemeijer, and N.M. Van Derpers, Characterization of Al-Si Alloys Rapidly Quenched from the Melt, J. Mater. Sci., 1980, 15(11), p 2803–2810
A. Ma, K. Suzuki, N. Saito, Y. Nishida, M. Takagi, I. Shigematsu, and H. Iwata, Impact Toughness of an Ingot Al-23mass%Si Alloy Improved by Rotary-Die Equal-Channel Angular Pressing, Mater. Sci. Eng. A, 2005, 399, p 181–189
R. Valiev and T. Langdon, Principles of Equal-Channel Angular Pressing as a Processing Tool for Grain Refinement, Prog. Mater. Sci., 2006, 51, p 881–981
W. Kim and Y. Lee, Enhanced Superplasticity of 1 wt%Ca-AZ80 Mg Alloy with Ultrafine Grains, Mater. Lett., 2010, 64, p 1759–1762
J. Jiang, A. Ma, D. Song, J. Shi, K. Wang, D. Yang, and J. Chen, Anticorrosion Behavior of Ultrafine-Grained Al-26 wt% Si Alloy Fabricated by ECAP, J. Mater. Sci., 2012, 47, p 7744–7750
H. Kim, M. Choi, C. Chung, and D. Shin, Fatigue Properties of Ultrafine Grained Low Carbon Steel Produced by Equal Channel Angular Pressing, Mater. Sci. Eng. A, 2003, 340, p 243–250
E.A. El-Danaf, M.S. Soliman, A.A. Almajid, and M.M. El-Rayes, Enhancement of Mechanical Properties and Grain Size Refinement of Commercial Purity Aluminum 1050 Processed by ECAP, Mater. Sci. Eng. A, 2007, 458(1–2), p 226–234
Y.H. Zhao, X.Z. Liao, Z. Jin, R.Z. Valiev, and Y.T. Zhu, Microstructures and Mechanical Properties of Ultrafine Grained 7075 Al Alloy Processed by ECAP and Their Evolutions During Annealing, Acta Mater., 2004, 52(15), p 4589–4599
Y. Zhou and Y. Xia, Experimental Study of the Rate-Sensitivity of SiCp/Al Composites and the Establishment of a Dynamic Constitutive Equation, Compos. Sci. Technol., 2000, 60, p 403–410
K. Ishikawa, H. Watanabe, and T. Mukai, High Strain Rate Deformation Behavior of an AZ91 Magnesium Alloy at Elevated Temperatures, Mater. Lett., 2005, 59, p 1511–1515
W.S. Lee, W.C. Sue, C.F. Lin, and C.J. Wu, The Strain Rate and Temperature Dependence of the Dynamic Impact Properties of 7075 Aluminum Alloy, J. Mater. Process. Technol., 2000, 100, p 116–122
C. San, Marchi, Cao Fahe, Kouzeli M, Mortensen A, Quasistatic and Dynamic Compression of Aluminum-Oxide Particle Reinforced Pure Aluminum, Mater. Sci. Eng. A, 2002, 337, p 202–211
R. Kapoor, J.B. Singh, and J.K. Chakravartty, High Strain Rate Behavior of Ultrafine-Grained Al-1.5 Mg, Mater. Sci. Eng. A, 2008, 496, p 308–315
Y.B. Xu, W.L. Zhong, Y.J. Chen, L.T. Shen, Q. Liu, Y.L. Bai, and M.A. Meyers, Shear Localization and Recrystallization in Dynamic Deformation of 8090 Al-Li alloy, Mater. Sci. Eng. A, 2001, 299, p 287–295
D. Song, A. Ma, J. Jiang, P. Lin, D. Yang, and J. Fan, Corrosion Behavior of Equal-Channel-Angular-Pressed Pure Magnesium in NaCl Aqueous Solution, Corros. Sci., 2010, 52(2), p 481–490
V.S. Deshpande and N.A. Fleck, High Strain Rate Compressive Behaviour of Aluminium Alloy Foams, Int. J. Impact Eng., 2000, 24, p 277–298
A. Ma, K. Suzuki, Y. Nishida, N. Saito et al., Impact Toughness of an Ultrafine-Grained Al-11mass%Si Alloy Processed by Rotary-Die Equal-Channel Angular Pressing, Acta Mater., 2005, 53, p 211–220
T. Mukai, M. Kawazoe, and K. Higashi, Dynamic Mechanical Properties of a Near-nano Aluminum Alloy Processed by Equal-Channel-Angular-Extrusion, Nanostruct. Mater., 1998, 10(5), p 755–765
J. Zhang, H. Shi, M. Cai, L. Liu, and P. Zhai, The Dynamic Properties of SiCp/Al Composites Fabricated by Spark Plasma Sintering with Powders Prepared by Mechanical Alloying Process, Mater. Sci. Eng. A, 2009, 527, p 218–224
K.C. Le and D.M. Kochmann, A Simple Model for Dynamic Recrystallization During Severe Plastic Deformation, Arch. Appl. Mech., 2009, 79, p 579–586
İ. Tirtom, M. Güden, and H. Yıldız, Simulation of the Strain Rate Sensitive Flow Behavior of SiC-Particulate Reinforced Aluminum Metal Matrix Composites, Comput. Mater. Sci., 2008, 42, p 570–578
D. Umbrello, R. M’Saoubi, and J.C. Outeiro, The Influence of Johnson-Cook Material Constants on Finite Element Simulation of Machining of AISI, 316L Steel, Int. J Mach. Tool Manuf., 2007, 47, p 462–470
Acknowledgments
This work was sponsored by Qing Lan Project, National Natural Science Foundation of China (Grant No. 51141002), Jiangsu Provincial Natural Science Foundation of China (Grant No. BK20131373) and the Fundamental Research Funds for the Central Universities of China (2009B15314).
Author information
Authors and Affiliations
Corresponding author
Rights and permissions
About this article
Cite this article
Jiang, J., Shi, J., Yao, Y. et al. Dynamic Compression Properties of an Ultrafine-Grained Al-26 wt.% Si Alloy Fabricated by Equal-Channel Angular Pressing. J. of Materi Eng and Perform 24, 2016–2024 (2015). https://doi.org/10.1007/s11665-015-1455-8
Received:
Revised:
Published:
Issue Date:
DOI: https://doi.org/10.1007/s11665-015-1455-8