Abstract
This work highlights the importance of renewable materials, specifically polymers derived from epoxidized oils, in promoting sustainable development and reducing the environmental impact of various industries. The use of carboxylic acids as hardeners for biobased resins from epoxidized oils is also discussed as a promising development in this field. However, there is a lack of research in this area, and finding the right combination of carboxylic acids and epoxidized oils remains a challenge. The present work aimed to address this gap by synthesizing biobased resins using epoxidized soybean oil (ESO) and dicarboxylic acids with specific aliphatic chain lengths, such as oxalic, succinic, adipic and sebacic acids with 0, 2, 4 and 8 carbons in aliphatic chain. The curing and properties of the resulting biopolymers were investigated using DSC, FTIR, TGA, and swelling ratio assessments. FTIR spectra evidenced that the reaction between epoxy and carboxylic groups occurred by the presence of ester groups, as verified after the disappearance of the epoxy bands at ~ 829 cm−1 and the appearance of related bands to hydroxyl (-OH) at ~ 3500 and ester at 1685–1742 cm−1, respectively. DSC scans presented exothermic peaks related to the curing reactions associated to an increasing enthalpy (ΔH) as the aliphatic chain size increases. The activation energy, Eac, estimated using Friedman and Vyazovkin approaches, is highly influenced by the chain size and pKa of the acids. Furthermore, the thermal and hydrocatalytic degradation increase with the decrease of aliphatic chain. The study also introduces oxalic acid as a biobased cross linker for ESO, which has not been so far combined without any synthetic modifications in its structure.
Similar content being viewed by others
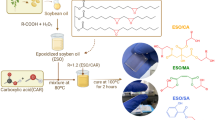
Explore related subjects
Discover the latest articles, news and stories from top researchers in related subjects.Avoid common mistakes on your manuscript.
Introduction
Renewable materials are essential for sustainable development as they offer a way to reduce the use of non-renewable resources and minimize the impact on the environment. Polymers are widely used in many industries, including packaging, textiles, construction, and electronics, and are typically derived from fossil fuels [25, 26, 43]. However, the development of renewable polymers can significantly reduce the environmental impact of these industries.
Epoxidized oils are a type of renewable material that can be used as a feedstock to produce polymers [36]. These oils are derived from vegetable oils, which are abundant and renewable resources, such as linseed and soybean cultures [2, 33]. The epoxidation process converts the unsaturated double bonds in the oils to epoxide groups, which can then be polymerized to form epoxy resins, that make up most polymers classified as thermosetting [28].
The use of carboxylic acids as hardeners for epoxy resins derived from epoxidized oils is also an important development in this field. Carboxylic acids can easily be derived from biomass (as example of succinic, tartaric and sebacic acids) and used as a sustainable alternative to conventional hardeners, which are often based on petrochemicals [1]. The development of biobased resins from epoxidized oils using carboxylic acids as hardeners has several benefits. Firstly, it reduces the dependence on non-renewable resources and helps to reduce the carbon footprint of the industry. Secondly, it offers a way to use biomass waste streams, which can help to reduce waste and improve the sustainability of the agricultural sector. Finally, biobased resins can be used in a range of applications, including coatings, adhesives, and composites, providing a sustainable alternative to conventional petroleum-based products [4, 10, 16, 17, 20, 35].
Despite the potential of carboxylic acids as hardeners for renewable polymers, there is still a lack of research in this area. One of the main challenges is to find the right combination of carboxylic acids and epoxidized oils to achieve the desired properties of the final product. Additionally, the synthesis of biobased resins from epoxidized oils using carboxylic acids as hardeners requires optimization of the reaction such as the ideal molar ratio, type of carboxylic acid based on the size of the main chain or the presence of other functionalities, to achieve high conversion and good properties of the resulting polymers [8, 23, 31].
Besides that, the kinetic curing evaluation of bio sourced epoxy resins based on epoxidized soybean oil (ESO) and the carboxylic acids used represents a crucial aspect in this field. Understanding the curing behavior and reaction kinetics is essential for optimizing the synthesis process and tailoring the properties of the resulting polymers [8, 27].
In the present work, biobased resins were synthesized by incorporating dicarboxylic acids derived from bio sources into epoxidized soybean oil. The dicarboxylic acids used had specific aliphatic chain lengths, ranging from ‘zero’ (oxalic acid) to 8 (sebacic acid) carbon atoms in the aliphatic chain, the curing was investigated using differential scanning calorimetry (DSC) and Fourier transformed infrared spectroscopy (FTIR). The acquired biopolymers were characterized in terms of thermal stability by thermogravimetry analysis (TGA). Moreover, the swelling ratio (in water and toluene), crosslinking density, gel content assessments were determined. It is worth mentioning, from our knowledge, so far, oxalic acid, with “zero” carbons in the aliphatic chain, has never been combined without any synthetic modifications in its structure as biobased cross linker for ESO.
Experimental
Materials
Epoxidized soybean oil (ESO) was kindly provided by BBC Química (São Paulo, Brazil) with the equivalent epoxy weight (EEW) of 238 g/mol and the number of epoxy groups per molecule equal to 4.3 (as determined by titration following the ASTM D1652-11. Oxalic, succinic, adipic, and sebacic acids (98% purity) were acquired from Sigma Aldrich Renewable (São Paulo, Brazil). Solvents, (toluene and acetone 98% of purity) were acquired from Sigma Aldrich (São Paulo, Brazil) and used to determine the swelling ratio and gel content, respectively. All chemicals were used as received without further purification.
Curing of Epoxidized Soybean Oil with Dicarboxylic Acids
Biobased resins of ESO and dicarboxylic acids (ESO/COOH) were formulated at a stoichiometric ratio of R = 1.2 epoxy/acid groups (or R = 0.83 acid groups/epoxy) respectively. The proper amount of ESO was heated at 60 °C, to reduce viscosity, afterward, the correspondent amount of dicarboxylic acid was added, and the compounds were mechanically stirred for 10 min until reaching complete homogenization. The temperature of the mixture chosen for each group takes into consideration the prevention of thermal degradation during the reaction (Table 1). Then, the uncured mixtures were poured out into a silicon mold and cured at 110 °C. A different procedure was adopted for oxalic acid, due to its high reactivity, and the amount of oxalic acid was diluted in isopropyl alcohol (3 mL) before being added to the ESO. Table 1 summarizes the tested parameters to produce the bio-resins (Scheme 1). The epoxy/COOH ratio was calculated based on the following Eq. 1:
where En is the gram equivalent of epoxy and COOH, respectively.
The determination of specific curing times posed practical challenges due to the significant impact of carboxylic acid chain length on the resulting material properties. Imposing a fixed curing time could not ensure complete crosslinking of the material. In an effort to standardize the curing process for all epoxy systems, an initial duration of 4 h was implemented. However, analysis of gel content measurements obtained from this experiment revealed that systems containing adipic and sebacic acids exhibited gel contents below 30%. These findings, along with other observations, highlight the need for a comprehensive assessment of the influence of aliphatic chain length of these carboxylic acids to achieve complete curing of the system. For that reason, different curing times were adopted as a function of carboxylic acid used.
Fourier Transform Infrared Spectroscopy (FTIR)
Uncured and cured samples of ESO/COOH resins were evaluated by infrared spectroscopy to follow the curing reactions through the formation of specific chemical bonds. Specimens were analyzed with the attenuated total reflectance (ATR) method using a spectrometer Spectrum 400 Series Perkin Elmer (United States) in the range of 650–4000 cm−1 wavenumber. The resolution and the number of scanning cycles were 4 cm−1 and 32 scans, respectively. The spectra presented in this manuscript were normalized in the software provided by the equipment using the peak at 2928 cm−1 as reference.
Differential Scanning Calorimetry (DSC)
Evaluation of the curing of ESO/COOH compounds took place using the DSC of TA Instruments model SDT 650 (United States). Specimens weighing 7–8 mg of ESO/COOH were sealed in alumina pans and heated from 30 ˚C to 300 °C under a synthetic air atmosphere with a flow rate of 50 mL/min. Non-isothermal curing systems were evaluated under the heating rates 5 °C.min−1, 10 °C.min−1, 15 °C.min−1, and 20 °C.min−1.
Acquired data during the heating programs were used to evaluate the kinetic and thermodynamic parameters, in addition the activation energy (Eac) versus degree of conversion (α) plots were computed with Friedman and Vyazovkin’s models through the kinetic modeling performed with the Kinetics Neo software of Netzsch.
Thermogravimetry (TGA)
The thermal stability of ESO and cured ESO/COOH biobased resins were evaluated using a THA Pyris-1 of Perkin Elmer (United States). Specimens with approximately 10 mg were placed in an alumina pan and heated from room temperature (~ 23 °C) to 650 °C, with a heating rate of 10 °C.min−1, under N2 atmosphere with gas flow of 50 mL.min−1.
Gel Content (GC)
Gel content is an important parameter that indicates the degree of conversion during the synthesis of any kind of resin and it is calculated using Eq. (2). The cured specimens (Mi) were embedded in filter paper and refluxed in acetone using a Soxhlet apparatus during 48 h. Afterward, the specimens were dried for 6 h until reaching a constant weight (Mf).
In vitro Hydrolytic Degradation
During the in vitro hydrolytic degradation, the initial specimens (Wi) were immersed in a phosphate-buffered saline (PBS) solution (pH 7,4) at 37 °C for predetermined periods, i.e., t = 7 days, 14 days, 21 days, and 28 days. Afterward, the specimens were removed from the solution, washed with distilled water, and dried at 50 °C until constant weight. The specimens were then weighted (Wt) and the hydrolytic degradation was determined using Eq. (3).
where Wi is the initial weight and Wt is the weight at a pre-determined time. The experiments were carried out in triplicate.
Swelling Ratio and Crosslink Density
The swelling ratio (Sr) was determined according to Eq. (4) and the results are shown as absorbed solvent content expressed in percentage units.
The tests were performed using toluene as solvent. Specimens with 1 ± 0.01 g as the initial weight (Wi) and with 15 × 15x5.3 mm3 were immersed in 50 mL of toluene for 24 h. Then, the specimens were gently dried to remove solvent excess and the final weights (Wf) were recorded.
The swelling ratio in toluene was used to determine the crosslink density (vd) and the molar mass between crosslinking points (Mc) of prepared resins. According to Flory-Rehner theory [13, 39], the crosslink density can be calculated using Eq. 5.
where \({v}_{s}\) is the solvent molar volume and \({X}_{1}\) is the Flory–Huggins polymer–solvent interaction parameter, which for toluene is equal to 106.27 cm3.mol−1 and ~ 0.391, respectively. The molar volume of the polymer \({v}_{p}\) can be calculated using Eq. (6).
where \({\rho }_{polymer}\) and \({\rho }_{solvent}\) are the densities of the polymer (calculated from the relation between mass and volume of specimens) and that of the solvent, while Sf is the swelling factor. The swelling factor (Sf) used in Eq. (6) was the unitary value of the swelling ratio (Sr) calculated in Eq. 4.
Measurement of the Curing Activation Energy, Eac
The degree of conversion can be determined by the exothermic peak present in the curves obtained by differential scanning calorimetry (DSC) through the ratio between partial peak integration (in this case, exothermic) at a given temperature T (\({\int }_{{T}_{0}}^{T}{H}_{T}\))) under the total integration of the event\(({\int }_{{T}_{0}}^{T\infty }{H}_{\infty }\)), as described by Eq. (7).
The conversion rate of a chemical reaction is commonly written as the product of a temperature-dependent rate constant k(T) and a conversion function f(α) characteristic of the reaction mechanism, as shown in Eq. (8).
As defined by Arrhenius, the conversion rate could be assumed a constant rate k(T) as shown in Eq. (9).
Assuming an iso-conventional model-free method, the activation energy (Eac) and the pre-exponential factor are functions of the degree of curing. In the present work, Eac was determined by the Friedman method [15] (and Vyazovkin as described in the next steps), based on the logarithmic form of the curing rate as shown in Eq. 10.
Where A and R are a constant pre-exponential factor and the universal gas constant, respectively.
As demonstrated in sundry works, the Friedman method is affected by significant numerical instability and noise interference because it employs instantaneous rate values and uses the differential term dα/dt during numerical calculation. As a result, the Vyazovkin method was employed, since the main objective of this method is to eliminate the systematic error in Eac as a function of changes in α.
Vyazovkin developed an advanced nonlinear procedure that performs integrations in small conversion intervals, Δα ≈0.01, where Eac is considered constant (Eq. 10)[41]. For a series of n experiments at different heating conditions, Eac is determined for each interval as the value that minimizes the function given by Eq. 12. Systematic errors associated with the main integrations are minimized by this method.
Eac of ESO/COOH was plotted as a function of the curing degree (α) through the Friedman and Vyazovkin methodologies. The statistical parameters of linear correlation (R2) for Eac are presented in the results and discussion section (Table 3).
Results and Discussions
Curing Mechanism Involving ESO and Dicarboxylic Acids
The mechanisms of the reactions among epoxide groups are quite complex and reactions beyond oxirane ring-opening such as esterification, etherification and condensation esterification can occur simultaneously. Based on the acquired data and previous studies [12, 38], two main mechanisms among epoxide groups and dicarboxylic acids are illustrated in Scheme 2.
Fourier Transform Infrared Spectroscopy (FTIR)
Figure 1 displays FTIR spectra of uncured and cured ESO/COOH bio-resins. The ESO spectra showed the main characteristics bands of the epoxide group at 848 and 824 cm−1 and the ester band centered at 1744 cm−1. Other bands such as 728 cm−1 (CH bending), 1084–1154 cm−1 (ester, antisymmetric stretch), and 2856–2924 cm−1 (methylene symmetric and antisymmetric stretch) are also observed, they are important to compare the structural changes during the curing.
The characteristic band due to the oxirane group at 826 cm−1 decreases along with the crosslinking reaction, and bands at 3456–3182 cm−1 referring to OH stretch of intermolecular bonding appear mostly due to the oxirane ring opening reactions, which is also an indication of esterification reaction [32, 42].
Still observing the bands that correspond to the C = O elongation of conjugate acid and the ester group at 1685–1742 cm−1, respectively, it is possible to evaluate the influence of the size of the aliphatic chain and molar ratio for the different groups of acids. The groups with oxalic and succinic acid do not show conjugate acid formation (1658 cm−1) in the uncured samples, certainly because they have the smallest size of an aliphatic chain (number of carbons = 0* and 2, respectively) and lower pKa values, which favor esterification reactions [37].
In the groups with adipic and sebacic acid, it is noticed that there is the presence of conjugate acid, and only after the curing step does the formation of ester bonds occur. Additionally, even after curing, it is verified the presence of a shoulder around 1658 cm−1 in cured specimens with ADI and SEB, indicating the presence of a small quantity of conjugate acids that did not react. This behavior is related to the size of the aliphatic chain of these acids, which are composed of 4 and 8 carbons, respectively, and provide steric and conformation impediments that make the dynamics of the polymerization reaction unfeasible [18, 21]. Additionally, etherification reactions are expected in systems where there is an excess of epoxy groups and low selectivity of the curing agent, which corroborates with the appearance of bands around 1240 cm−1 referring to the C–O–C elongation in the ADI and SEB compositions [12].
Differential Scanning Calorimetry (DSC)
Figure 2 displays the DSC scans acquired with 10 °C/min for the uncured bio resins (reactive mixture). Initially, it is observed endothermic peaks, approximately, at 110 °C, 140 °C, and 155 °C corresponding to the melting (Tm acid) of oxalic (OXA), adipic (ADI) and sebacic (SEB) acids, respectively. The melting point of succinic acid (SUC) occurs concurrently with the exothermic curing event (T ~ 185 °C). The exothermic events displayed in the heat flow versus temperature plots correspond to the curing reactions, presenting different enthalpies and temperatures, influenced by the characteristics of the dicarboxylic acid, as listed in Table 2.
Observing the curing behavior from the perspective of the -COOH chain length, it can be seen that the exothermic peak is shifted to higher temperature range, as there is an increase in the number of aliphatic carbons in the dicarboxylic acid chain (i.e. OXA < SUC < ADI < SEB). This phenomenon is provided by a decrease in the mobility of chain segments because of an increase in the number of aliphatic carbons. It is worth pointing out that the curing stages of epoxy resins from epoxidized vegetable oils occur through autocatalytic reactions (consumption of reactive groups, -COOH in this case) and diffusion reactions and, under some special conditions, through homopolymerization reactions (of the remaining ESO). Therefore, it is assumed that diffusion reactions are favored in acids that have a smaller aliphatic chain size since these have greater mobility [40].
The Eac was plotted as a function of the curing degree (α) through the Friedman and Vyazovkin methodologies as shown in Fig. 3, these kinetic models displayed good R2 results as shown in Table 3. ESO/OXA showed higher activation energy variation (ΔEac = 70 kJ/mol in the range of α = 0 ~ 80%) than expected for this composition, due the previous discussion regarding pKa. It was expected that due to the low pKa of oxalic acid, there would be a lower activation energy since the rapid dissociation promotes a faster availability of acid groups and the oxirane ring opening reactions would occur more quickly. However, it is important to point out that the rapid dissociation of oxalic acid also generates a greater availability of carboxylate ions, which are more stable and therefore can increase the activation energy during the reaction and could explain the observed behavior. The activation energy gradually increases during the aforementioned interval until reaches a maximum value (α = 87%) when decreases abruptly. At this stage, the Eac is possibly related to carboxylic groups (instead carboxylate ions) are available. It is worth to point out that different pKa associated to each dicarboxylic group present in the dicarboxylic acid (for oxalic is pka1 = 1.26 and pka2 = 4.28) and the remains COOH groups are low reactive compared to the first one, which also explains the abrupt decrease in Eac.
In the case of ESO/SUC, the autocatalytic processes probably occur at 0 < α < 30% conversion with ΔEac = 43 kJ/mol. The propagation stage occurs between 30 < α < 80% with constant activation energy, characteristic of this process. The sudden increase in the activation energy to values around 120 kJ/mol is characteristic of -OH groups consumption and homopolymerization reactions, since compositions with succinic acid propagate up to temperatures around 300 °C, as demonstrated in the conversion curves (α) versus temperature (T).
ESO/ADI and ESO/SEB show the highest values in the initial stage of conversion Eac = 88 and 97 kJ/mol. The activation energy values obtained by our study were slightly higher than reported [11, 45]. However, this has been attributed to the fact that the molecules in these compositions have longer carbon chains than oxalic and succinic acids (Carbons = 0* and 2, respectively). Furthermore, steric and electronic effects between epoxy groups in the same chain correspond to higher activation energy and this behavior is widely reported in the literature [19, 46]. It is important to mention that the absence of catalysts or initiators (for example, imidazole, which is the most used in epoxy systems based on epoxidized vegetable oils [32, 34, 38]) heads the dicarboxylic acids to act directly on the oxirane ring opening in the alkyl chains of the epoxidized soybean oil, which has a similar size to that of the dicarboxylic acids used. Due to the characteristics mentioned throughout the discussions (pKA and chain size), the initiation of the reaction demands a greater amount of energy that tends to stabilize throughout the reaction propagation. The final stages, in turn, α > 90%, are characterized by an increase in activation energy, mainly in the SEB group, which characterizes the action of the hydroxyl groups generated by the formation of ester bonds after the oxirane ring opening, acting in the continuation of the polymerization, mainly in the formation of ether bonds and homopolymerization.
Thermogravimetric Analysis (TGA)
The thermal stability of ESO/COOH specimens was investigated through thermogravimetric analysis and the plots are shown in Fig. 4. The thermal decomposition temperatures for weight loss equal to 5% (T5) and maximum decomposition (Tmax), in addition to the ash content, are listed in Table 4.
The first stage of the thermal degradation is characterized by the evaporation of surface water in the case of OXA group, and in the other groups, it refers to the decomposition of oligomers, remaining acid from the reaction and chain segments [7, 24].
The biobased resins, except ESO/OXA, presented two stages of degradation and, consequently, higher maximum degradation temperatures (Tmax) ranging between 400–410 °C for the first stage and 452–456 °C for the second. This degradation step corresponds to the breaking of ester bonds formed during the polymerization process and the ester bonds present in epoxidized soybean oil [6].
ESO curing using dicarboxylic acids must form a product with a predominance of crosslinking and may also contain some branches, formed by the encounter of chains that have reactive points opened by the dicarboxylic groups, but not necessarily with the dicarboxylic acid [45]. In this case, dicarboxylic acid appears as an initiator and curing agent at the same time.
This effect can be observed when comparing the reactivity of the acid, as in the case of oxalic acid (OXA). Because it has a low pKa (easy dissociation) and little steric hindrance (due to the short chain size—with zero aliphatic carbons) it has greater mobility during the polymerization reaction, guaranteeing its performance only as 'direct' curing [17, 29]. This behavior was proven through the determination of the Eac, by the models of Friedman and Vyazovkin in the later section.
But, from another perspective, ESO/OXA has the lowest thermal stability, with a temperature at 5% of weight loss (T5%) equal to 157 °C, which is low compared to the other acids that present values greater than 230 °C. The ESO/SEB system is the most stable (T5% = 272 and Tmax = 409–455 °C) which corroborates that a larger aliphatic chain size promotes greater thermal stability.
In vitro Hydrolytic Degradation
The in vitro hydrocatalytic degradation data in PBS (pH = 7.1) obtained through Eq. 3 for the ESO/-COOH compositions (where COOH = OXA, SUC, ADI and SEB) are presented in Fig. 5.
It is observed that after 28 days of testing it is not possible to guarantee that there was stabilization in the weight loss, but that the average weight loss is approximately 2.5 ± 1%. In fact, when comparing the results obtained in the TG analyzes for the SUC, ADI and SEB compositions to the hydrocatalitic degradation data, it is possible to observe that these groups present thermal stability at temperatures higher than 235 °C in the same weight loss range (weight loss = 5%). For the OXA group, the temperature at 5% weight loss (T5%) occurs around ~ 110 °C (Table 4). Despite being different degradation mechanisms (one through hydrolysis and the other thermal) the behavior in relation to the weight loss range (weight loss = 5%) indicates that the material presents stability due to the presence of a network with high density of crosslinks, as shown by the values of gel content. In addition, the presence of ester linkages being predominant and as ester-type bonds are reported in the literature as being the least likely to be broken by means of hydrolysis processes (at pH 7.2) and their thermal cleavage occurs at temperatures above 350 °C, this characteristic explains the stability in this scenario [5, 9].
The results referring to the OXA group are not reported because before 7 days of immersion in PBS the samples 'gelled' making it impossible to reliably weigh and evaluate the hydrocatalytic degradation. In fact, a hypothesis for this is that small amounts of oxalate were formed during the production of bioresins, and the oxalate reacts with sodium salts present in PBS, which may have led to acceleration of the degradation process. When observing the TG data, it is possible to notice that the OXA group presents a decomposition stage around 100–120 °C, which is related to the release of surface water, which shows a tendency of this composition to present ease water adsorption and, consequently, undergo hydrolysis processes [44].
Gel Content (GC)
GC data acquired using Eq. (2) for the ESO/COOH bio-resins are shown in Fig. 6. GC results indicate values around 80 ± 0.75% for the SUC, ADI, and SEB groups, which suggests the existence of reticulated networks with a considerable density of crosslinks. This result may be due to the good reactivity of ESO and the dicarboxylic acids investigated, since the data referring to the DSC show the total curing of the samples in the first heating stage, without the presence of curing events at temperatures above those presented in Table 7.
According to the literature, GC values equal to or greater than 80% indicate the predominance of crosslinks in the epoxy resins curing [11, 14, 30, 37, 40]. The values obtained can be considered low when compared to some systems reported in the literature, but it must be considered that no catalyst was used in the reaction and consequently the selectivity of dicarboxylic acids acts in different stages of polymerization due, for example, the different pKa presented for each carboxylic group as displayed in Table 1.
Swelling Ratio and Crosslink Density (v d)
The data acquired for the degree of swelling in toluene and its correlation with the crosslink density and the molar mass among the chain segments (Mc), obtained through Equation-5 are presented in Fig. 7. The use of non-polar solvents such as toluene demonstrates the ability of solvents to penetrate the microstructure of bio-resins and induce the displacement of macromolecular chains, without necessarily breaking the primary bonds. In other words, “specimens swell, but do not dissolve, in good solvents” and consequently, for this to happen, the presence of a structure with a high density of crosslinks is necessary (Montarnal et al., 2011).
On the other hand, to understand the behavior of the other acids, it is worth mentioning that the increase in the acid chain size leads to a greater distance between the segments of polymeric chains formed and, consequently, a more spaced structure that favors the penetration of the solvent (Fig. 7). This trend is observed for adipic acid, which presents the highest swelling values, but is not repeated for sebacic acid, which has an aliphatic chain with twice as many carbons.
In the case of sebacic acid, the size of the aliphatic chain results in a lower mobility of the acid segments during the reaction favors secondary reactions of homopolymerization and the formation of ether bonds. The polar character of the ether bonds (i.e. contrary to the non-polar character of toluene) would provide a molecular structure that is more resistant to solvent penetration due to the induction of dipole-type bonds [3, 22].
Collected data for swelling were used to estimate the density of crosslinks and the molar mass between crosslinks (Mc) through the theory described by Flory-Rehner [13, 39]. The results show that the resins obtained in the present work have crosslink density values similar to those reported for ESO/dicarboxylic acids/catalysts or ESO/amines/catalysts bio-resins [9],Frydrych et al.., 2015; Gopalakrishnan; Linda Fernando, 2012). Di Mauro et al., [9] developed bio-resins from different epoxidized vegetable oils with synthetic initiators and curing agents, (2,2'-dithiodibenzoic acid (DTBA), imidazole (IM), 1-methylimidazole (1 -MI) and N,N-dimethylbenzylamine (DMBA) and fixed molar ratio (R = 1.0), obtaining crosslink density values between 0.25 mmol/cm3 for the epoxidized karanja oil and 3 mmol/cm3 for the perilla oil. In this study, values around 0.5 mmol/cm3 were obtained.
Main Archievments of This Work
-
The development of biobased epoxy systems from epoxidized soybean oil (ESO) and the evaluation of the influence of aliphatic chain size of dicarboxylic acids in the curing process, evaluated using the Friedman and Vyazovkin approaches to obtain the activation energy, Eac;
-
Evaluating the reaction behavior taking in consideration the pKa values of the acids and how this characteristic affects the architecture of the acquired resins;
-
Adding value to literature data by evaluating oxalic acid as a curing agent in the epoxy system based on epoxidized soybean oil instead of linseed oil;
-
Complementing the information about the system of vegetable oils and dicarboxylic acids, when using acids with less than 10 carbons in the aliphatic chain;
Conclusions
Epoxidized soybean oil-based resins were prepared using a series of carboxylic acids with different aliphatic chains sizes and the influence of this characteristic on curing mechanism and physico-chemical properties were evaluated. During the curing, ether and ester bonding were evidenced through FTIR spectra. The curing took place during heating and from DSC scans endothermic peaks were noticed and are related to the melting temperature of oxalic, adipic and sebacic acids. This peak was not observed in ESO with succinic systems due an overlap with the exothermic peak referred to curing reaction. The enthalpy of curing, ΔH, increases with the aliphatic chain size of the dicarboxylic acids. However, the thermal and hydrocatalitic degradation increases with the decrease of aliphatic chain. The activation energy, Eac, versus conversion (α) is highly influenced by the pkA of the acids and by the chain size. The gel content results show a GC > 80% for all systems which indicates the presence of crosslinks. Otherwise, the results obtained in swelling ratio in toluene and approaches by Flory-Rehner theory of crosslink density, presented an increase in crosslink density when oxalic and succinic were compared and a decrease when adipic acid is evaluated. That can be related to the different architecture in the resins. With sebacic acid, the values of crosslinks density follow the same pattern as the other acids with smaller chain. In addition, the values of crosslink density are close from those reported in literature.
References
Abdelwahab MA, Misra M, Mohanty AK (2015) Epoxidized pine oil-siloxane: crosslinking kinetic study and thermomechanical properties. J Appl Polym Sci 132:1–12. https://doi.org/10.1002/app.42451
Alarcon RT, Lamb KJ, Bannach G, North M (2021) Opportunities for the use of brazilian biomass to produce renewable chemicals and materials. Chemsuschem 14:169–188. https://doi.org/10.1002/cssc.202001726
Altuna FI, Hoppe CE, Williams RJJ (2018) Epoxy vitrimers: The effect of transesterification reactions on the network structure. Polymers (Basel). https://doi.org/10.3390/polym10010043
Bechthold I, Bretz K, Kabasci S, Kopitzky R, Springer A (2008) Succinic acid: a new platform chemical for biobased polymers from renewable resources. Chem Eng Technol. https://doi.org/10.1002/ceat.200800063
Boyer A, Cloutet E, Tassaing T, Gadenne B, Alfos C, Cramail H (2010) Solubility in CO2 and carbonation studies of epoxidized fatty acid diesters: Towards novel precursors for polyurethane synthesis. Green Chem 12:2205–2213. https://doi.org/10.1039/c0gc00371a
Chen X, Chen S, Xu Z, Zhang J, Miao M, Zhang D (2020) Degradable and recyclable bio-based thermoset epoxy resins. Green Chem 22:4187–4198. https://doi.org/10.1039/d0gc01250e
Chrissafis K, Paraskevopoulos KM, Bikiaris DN (2006) Thermal degradation kinetics of the biodegradable aliphatic polyester, poly(propylene succinate). Polym Degrad Stab 91:60–68. https://doi.org/10.1016/j.polymdegradstab.2005.04.028
Ciannamea EM, Ruseckaite RA (2018) Pressure sensitive adhesives based on epoxidized soybean oil: correlation between curing conditions and rheological properties. J Am Oil Chem Soc 95:525–532. https://doi.org/10.1002/AOCS.12046
Di Mauro C, Malburet S, Genua A, Graillot A, Mija A (2020) Sustainable series of new epoxidized vegetable oil-based thermosets with chemical recycling properties. Biomacromol 21:3923–3935. https://doi.org/10.1021/acs.biomac.0c01059
Ding C, Matharu AS (2014) Recent developments on biobased curing agents: a review of their preparation and use. ACS Sustain Chem Eng 2:2217–2236. https://doi.org/10.1021/sc500478f
Ding C, Shuttleworth PS, Makin S, Clark JH, Matharu AS (2015) New insights into the curing of epoxidized linseed oil with dicarboxylic acids. Green Chem 17:4000–4008. https://doi.org/10.1039/c5gc00912j
Falco G, Sbirrazzuoli N, Mija A (2019) Biomass derived epoxy systems: From reactivity to final properties. Mater. Today Commun. 21:100683. https://doi.org/10.1016/j.mtcomm.2019.100683
Flory PJ (1953) Principles of polymer chemistry. Cornell University Press
Frias CF, Serra AC, Ramalho A, Coelho JFJ, Fonseca AC (2017) Preparation of fully biobased epoxy resins from soybean oil based amine hardeners. Ind Crops Prod 109:434–444. https://doi.org/10.1016/j.indcrop.2017.08.041
Friedman HL (1967) Kinetics and Gaseous Products of Thermal Decomposition of Polymers. J Macromol Sci Part A - Chem 1:57–79. https://doi.org/10.1080/10601326708053917
Gobin M, Loulergue P, Audic JL, Lemiègre L (2015) Synthesis and characterisation of bio-based polyester materials from vegetable oil and short to long chain dicarboxylic acids. Ind Crops Prod 70:213–220. https://doi.org/10.1016/j.indcrop.2015.03.041
Gogoi P, Horo H, Khannam M, Dolui SK (2015) In situ synthesis of green bionanocomposites based on aqueous citric acid cured epoxidized soybean oil-carboxylic acid functionalized multiwalled carbon nanotubes. Ind Crops Prod 76:346–354. https://doi.org/10.1016/j.indcrop.2015.06.057
Hu F, La Scala JJ, Yadav SK, Throckmorton J, Palmese GR (2021) Epoxidized soybean oil modified using fatty acids as tougheners for thermosetting epoxy resins: part 2—effect of curing agent and epoxy molecular weight. J Appl Polym Sci 138:50579. https://doi.org/10.1002/app.50579
Hu F, La Scala JJ, Yadav SK, Throckmorton J, Palmese GR, La Scala JJ, Throckmorton J, Palmese GR (2021) Epoxidized soybean oil modified using fatty acids as tougheners for thermosetting epoxy resins: part 2—effect of curing agent and epoxy molecular weight. J Appl Polym Sci 138:50570. https://doi.org/10.1002/app.50579
Jansen MLA, van Gulik WM (2014) Towards large scale fermentative production of succinic acid. Curr Opin Biotechnol. https://doi.org/10.1016/j.copbio.2014.07.003
Kulkarni MV, Viswanath AK (2004) Comparative studies of chemically synthesized polyaniline and poly(o-toluidine) doped with p-toluene sulphonic acid. Eur Polym J 40:379–384. https://doi.org/10.1016/j.eurpolymj.2003.10.007
Kumar S, Krishnan S, Samal SK, Mohanty S, Nayak SK (2018) Toughening of petroleum based (DGEBA) epoxy resins with various renewable resources based flexible chains for high performance applications: a review. Ind Eng Chem Res 57:2711–2726. https://doi.org/10.1021/acs.iecr.7b04495
Lei YF, Wang XL, Liu BW, Ding XM, Chen L, Wang YZ (2020) Fully bio-based pressure-sensitive adhesives with high adhesivity derived from epoxidized soybean oil and rosin acid. ACS Sustain Chem Eng 8:13261–13270. https://doi.org/10.1021/acssuschemeng.0c03451
Li YD, Jian XY, Zhu J, Du AK, Zeng JB (2018) Fully biobased and high performance epoxy thermosets from epoxidized soybean oil and diamino terminated polyamide 1010 oligomers. Polym Test 72:140–146. https://doi.org/10.1016/j.polymertesting.2018.10.010
Liu J, Zhang L, Shun W, Dai J, Peng Y, Liu X (2021) Recent development on bio-based thermosetting resins. J Polym Sci. https://doi.org/10.1002/pol.20210328
Manthey NW (2013). Development of hemp oil based bioresins for biocomposites. Fac. Eng. Surv. Doctor of.
Mashouf Roudsari G, Mohanty AK, Misra M (2014) Study of the curing kinetics of epoxy resins with biobased hardener and epoxidized soybean oil. ACS Sustain Chem Eng 2:2111–2116. https://doi.org/10.1021/SC500176Z/ASSET/IMAGES/LARGE/SC-2014-00176Z_0008.JPEG
Omonov TS, Curtis JM (2015) Plant Oil-Based Epoxy Intermediates for Polymers, Bio-based Plant Oil Polymers and Composites. Elsevier Inc., Netherlands. https://doi.org/10.1016/B978-0-323-35833-0.00007-4
PANSUMDAENG, J., Kuntharin, S., Harnchana, V., Supanchaiyamat, N., (2020) Fully bio-based epoxidized soybean oil thermosets for high performance triboelectric nanogenerators. Green Chem 22:6912–6921. https://doi.org/10.1039/d0gc01738h
Parada Hernandez NL, Bahú JO, Schiavon MIRB, Bonon AJ, Benites CI, Jardini AL, Maciel Filho R, Wolf Maciel MRW (2019) (Epoxidized castor oil – citric acid) copolyester as a candidate polymer for biomedical applications. J Polym Res. https://doi.org/10.1007/s10965-019-1814-5
Poutrel QA, Blaker JJ, Soutis C, Tournilhac F, Gresil M (2020) Dicarboxylic acid-epoxy vitrimers: Influence of the off-stoichiometric acid content on cure reactions and thermo-mechanical properties. Polym Chem 11:5327–5338. https://doi.org/10.1039/d0py00342e
Qi M, Xu YJ, Rao WH, Luo X, Chen L, Wang YZ (2018) Epoxidized soybean oil cured with tannic acid for fully bio-based epoxy resin. RSC Adv 8:26948–26958. https://doi.org/10.1039/c8ra03874k
Sahoo SK (2018) Development of completely bio - based epoxy networks derived from epoxidized linseed and castor oil cured with citric acid. Polym Adv Technol. https://doi.org/10.1002/pat.4316
Sivanesan D, Seo BK, Lim CS, Kim S, Kim HG (2021) Trifunctional cycloaliphatic epoxy-based thermoset polymers: Synthesis, polymerization, and characterization. Polymer (Guildf). 220:123568. https://doi.org/10.1016/j.polymer.2021.123568
Song H, Lee SY (2006) Production of succinic acid by bacterial fermentation. Enzyme Microb Technol. https://doi.org/10.1016/j.enzmictec.2005.11.043
Tan SG, Chow WS (2010) Biobased epoxidized vegetable oils and its greener epoxy blends: a review. Polym - Plast Technol Eng. https://doi.org/10.1080/03602559.2010.512338
Tellers J, Jamali M, Willems P, Tjeerdsma B, Sbirrazzuoli N, Guigo N (2021) Cross-linking behavior of eutectic hardeners from natural acid mixtures. Green Chem 23:536–545. https://doi.org/10.1039/d0gc03172k
Tran TN, Di Mauro C, Graillot A, Mija A (2020) Chemical reactivity and the influence of initiators on the Epoxidized Vegetable Oil/Dicarboxylic acid system. Macromolecules 53:2526–2538. https://doi.org/10.1021/acs.macromol.9b02700
Treloar LRG (1975) The physics of rubber elasticity.
Vidil T, Tournilhac F, Musso S, Robisson A, Leibler L (2016) Control of reactions and network structures of epoxy thermosets. Prog Polym Sci 62:126–179. https://doi.org/10.1016/j.progpolymsci.2016.06.003
Vyazovkin S, Burnham AK, Criado JM, Pérez-Maqueda LA, Popescu C, Sbirrazzuoli N (2011) ICTAC Kinetics Committee recommendations for performing kinetic computations on thermal analysis data. Thermochim Acta. https://doi.org/10.1016/j.tca.2011.03.034
Waig Fang S, De Caro P, Pennarun PY, Vaca-Garcia C, Thiebaud-Roux S (2013) Synthesis and characterization of new polyesters based on renewable resources. Ind Crops Prod 43:398–404. https://doi.org/10.1016/j.indcrop.2012.07.027
Wu J, Zhao C, Li Y, Li H, Xiang D, Sun Z, Li X (2021) Properties of bio-based thermosetting composites synthesized from epoxidized soybean oil and azo-cardanol benzoxazine. J Polym Res. https://doi.org/10.1007/s10965-021-02442-z
Yadav GG, David A, Favaloro T, Yang H, Shakouri A, Caruthers J, Wu Y (2013) Synthesis and investigation of thermoelectric and electrochemical properties of porous Ca9Co12O28 nanowires. J Mater Chem A 1:11901–11908. https://doi.org/10.1039/c3ta12096a
Zeng R, Wu Y, Li Y, Wang M, Zeng J (2017) Curing behavior of epoxidized soybean oil with biobased dicarboxylic acids. Polym Test 57:281–287. https://doi.org/10.1016/j.polymertesting.2016.12.007
Zhang C, Li Y, Chen R, Kessler MR (2014) Polyurethanes from solvent-free vegetable oil-based polyols. ACS Sustain Chem Eng 2:2465–2476. https://doi.org/10.1021/SC500509H/ASSET/IMAGES/MEDIUM/SC-2014-00509H_0007.GIF
Acknowledgements
The author would thank BBC Química – São Paulo, Brazil for kindly providing the epoxidized soybean oil (ESO). Authors are gratefully to CERTBIO (Northeast Biomaterials Evaluation and Development Laboratory—Brazil) for the supported infrastructure.
Funding
The authors are grateful to CNPq (National Council for Scientific and Technological Development, Brasilia/DF, Brazil) for the financial support. Fundação de Apoio à Pesquisa do Estado da Paraíba (FAPESQ) (Concession term: 022/2023). Professor Renate Wellen is CNPq fellow (Number: 303426/2021-7).
Author information
Authors and Affiliations
Contributions
All authors contributed to the data acquisition, writing and revision of the paper
Corresponding author
Ethics declarations
Conflict of Interest
There is no conflict of interest and all authors have agreed with this submission and they are aware of the content.
Additional information
Publisher's Note
Springer Nature remains neutral with regard to jurisdictional claims in published maps and institutional affiliations.
Supplementary Information
Below is the link to the electronic supplementary material.
Rights and permissions
Springer Nature or its licensor (e.g. a society or other partner) holds exclusive rights to this article under a publishing agreement with the author(s) or other rightsholder(s); author self-archiving of the accepted manuscript version of this article is solely governed by the terms of such publishing agreement and applicable law.
About this article
Cite this article
Nepomuceno, N.C., Barreto, V. & Wellen, R.M.R. Effect of Dicarboxylic Acids’ Aliphatic Chain on the Curing of Epoxidized Soybean Oil (ESO) Resins. J Polym Environ 32, 45–56 (2024). https://doi.org/10.1007/s10924-023-02958-z
Accepted:
Published:
Issue Date:
DOI: https://doi.org/10.1007/s10924-023-02958-z