Abstract
The effects of surface roughness on the hydro-thermal performance of laminar mixed convection heat transfer of water have been investigated numerically. The geometry was a semicircular curved horizontal dimples tube with a fixed dimensionless radius of curvature (2R/D = 6.62) and dimensionless roughness height of e/D = 0.1. Under low values of Re (100,200,400) and Gr numbers (20,000.100000,400,000), a constant heat flux was imposed on the tube walls. The three-dimensional governing equations were discretized, using a finite volume method. Dimensionless temperature, convective heat transfer coefficient, axial dimensionless velocity contours, secondary flow vectors, and surface friction coefficient are presented and discussed. The results showed that for identical conditions, the dimpled tube has better thermal performance compared to a smooth tube, especially in low Re values. So that in the low Re values, the dimpled tube has 58.2% higher heat transfer coefficient in comparison with the smooth ones. However, this predominance in thermal characteristics is mitigated by increasing Re number. Additionally, it has been shown that the skin friction coefficient of a curved dimpled tube is less than that of a smooth one in low Reynolds values. Using Colburn j factor and friction coefficient (f), and presenting j/f versus Re shows that the dimpled tube is more efficient at Re < 200.
Similar content being viewed by others
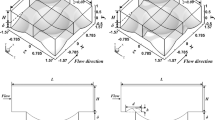
Avoid common mistakes on your manuscript.
1 Introduction
Increasing the performance is one of the most important goals in designing modern heat exchangers. The performance of heat exchangers can be improved by heat transfer enhancement techniques which are, in general, categorized into two main groups of active and passive [1]. The active techniques require external forces, e.g. electric field, acoustic, surface vibration, etc. While in passive techniques, fluid additives such as nanoparticles or special flow geometries such as rough surfaces are employed. Utilization of extended surfaces, such as dimpled surfaces, can be very useful. Dimpled surfaces simultaneously provides larger heat transfer area as well as generating local flow disturbances and resulting in higher heat transfer rate for both cooling and heating purposes. It is done by increasing the flow turbulence, intensifying the secondary flows, and by growing the thermal boundary layer infraction. Therefore, a Vipertex tube, with dimples on its outer surface, can be a good alternative for the conventional tubes in the design of high efficiency thermal equipment.
The effect of adding dimples or extending the surface on the thermal characteristics of a flow have been studied by several researchers and all of them confirmed that this modification is a useful and effective technique from thermal point of view. Among them, Bilen et al. [2] reported an experimental study on heat transfer and friction characteristics of fully developed turbulent air flow in a tubes made by different extended surfaces. They found that at the highest Reynolds number (Re = 38,000), in the tubes with circular, trapezoidal, and rectangular groove on their surfaces, the heat transfer rate is 63%, 58%, and 47% higher than that of the smooth tube, respectively. Chen et al. [3] modeled turbulent flow in a protruded-surface channel for Re values between 3000 and 6000. The results for different depth ratio of protrusions indicated that at higher ratios, due to increase in flow turbulence, friction factor and heat transfer rate became higher. Kumar et al. [4] investigated the heat transfer enhancement due to implementing the protruded surface tubes in the heat exchangers. Their outcomes revealed that for turbulent flow regime, using dentate surfaces improves the heat transfer rate and the hydro-thermal performance of the heat exchangers by 3.43 and 2.31 times, respectively. Vicente et al. [5] experimentally studied the hydro-thermal behavior of helically dimpled tubes in the low Reynolds values. Their results showed that, the skin friction coefficient of this kind of pipes is 10 to 30% more than that of the smooth ones. They also concluded that in low Rayleigh numbers these pipes are similar to the smooth tubes, while in high Rayleigh numbers, heat transfer rate is increased up to 30% due to buoyancy force increase. Solanki and Kumar [6] experimentally compared the condensation heat transfer coefficient and the frictional pressure drop of R-134a of the smooth straight tubes with the smooth helically coiled tubes, and the dimpled helically coiled ones. They showed that heat transfer coefficient and frictional pressure drop in the dimpled helically coiled tube is higher than those of the smooth helically coiled and the smooth straight tubes. Nivesrangsan et al. [7] experimentally evaluated the thermal performance of the dimpled tubes with two different dimpled-surface patterns including aligned arrangement and staggered arrangement. The results indicated that, at the lowest pitch ratio, the mean heat transfer rate of the dimpled tube with staggered arrangement is around 127 and 8% higher than those of the smooth tube and the dimpled tube with aligned arrangement, respectively. Kukulka and Smith [8] compared the thermal performance of Vipertex enhanced surface tube with and the smooth one. The results indicates that, for heating mode of the system, the heat transfer rate of the Vipertex tube, with the turbulent flow, is 100% more than that of the smooth tube. However, in laminar mixed convection, the growth of heat transfer rate due to using the dimpled tube is little. Kukukla et al. [9] experimentally evaluated the performance of Vipertex tube under fouling conditions. They showed that in the same fouling conditions, the dimpled tube leads to more heat transfer compared to the smooth tubes. Another study performed by Kukulka et al. [10] showed that the average evaporation heat transfer coefficient of R22, R32 and R410A in the Vipertextube are about two times greater compared to the smooth tubes. Mashayekhi [11] numerically investigated the effect of roughness on the forced convection heat transfer in a pipe with dimples and protrusions. Their results indicated that the thermal efficiency of the pipes in the lower Re values were higher.
An optimization of dimples in microchannel heat sink was performed by Ming et al. [12]. Their results show that the combination of dimples and impinging jets significantly improves heat transfer performance. Shui et al. [13] numerically and experimentally investigated the effects of dimples on heat transfer enhancement in a tree-like branching microchannels. Significant improvement on the averaged heat transfer performance is seen using dimples. However, its performance decreases by increasing Reynolds number.
The results indicate that the dimples can significantly improve the averaged heat transfer performance of branching microchannels. Recently Sobhani and Behzadmehr [14] investigated the effects of different dimples- protrusions pattern on the mixed convection heat transfer in a horizontal tube. They presented a modified model for which heat transfer coefficient and pressure drop is balanced.
Curved tubes as a passive technique of heat transfer enhancement could be seen in different thermal devices such as helical coil tubes in heat exchangers. Thus several theoretical studies have been done on them. Georing et al. [15] evaluated the simultaneous effects of curvature and buoyancy force on laminar flow regime in a curved tube under two different thermal boundary conditions. They presented heat transfer and pressure drop data also flow velocity and temperature contours for both constant heat flux and constant wall temperature. Wael [16] numerically investigated curvature ratio and nanoparticle volume concentrations influence on heat transfer and pressure drop characteristics of nanofluid flowing in a helically coiled heat exchanger. The results revealed that with an increase in diameter of coil, both the heat transfer coefficient and the friction factor increased. Chimres et al. [17] studied the thermal performance of semi-dimple fin in fin and tube heat exchangers numerically. They showed the existing semi-dimple fins have the highest heat transfer coefficient and pressure drop in comparison with semi-dimle pair and plain fins. However, the goodness factor of semi-dimple pair is about 33-37% greater than the existing semi-dimples and about 15-20% greater than the plain fin.
Additionally, several extensive investigations have been dedicated to the heat transfer phenomenon in the curved tubes (Li et al. [18], Akbarinia and Behzadmehr [19], Ghaffari and Behzadmehr [20], Alikhani and Behzadmehr [21]). Huminic [22] summarized newly published articles evaluating the heat transfer characteristics of conventional fluids and nanofluids in curved tubes.
The current research evaluates the laminar mixed convection in a horizontal curved dimpled tube for the low values of Re and Gr numbers. The effect of dimples on the hydro-thermal characteristics of the considered geometry, have not previously reported. To compare the curved dimpled tube with the smooth one, the axial velocity, the secondary flow and the temperature contours are considered as the criteria and these parameters are presented for different values of Re. Also the profiles of convective heat transfer coefficient and skin friction coefficient are shown and discussed.
2 Model
2.1 Physical model
It was assumed that the laminar and steady flow of a non-compressible Newtonian fluid enters into the dimpled tube at the state of fully developed (Fig. 1). The three-dimensional structure of dimpled tube is shown in Fig. 1. The r-θ plan presents the horizontal surface which means the tube is rest on the horizontal surface.
2.2 Mathematical model and governing equations
For better analysis and calculation, the following assumptions are adopted.
-
(a)
Physical properties of the fluid were assumed to be constant except for the density in the body force, which varies linearly with the temperature (Boussinesq’s hypothesis).
-
(b)
Heat losses and pressure drop were neglected.:
Therefore, the dimensional governing equations for the steady state conditions can be written as follows:
Continuity equation:
Momentum equation:
Energy equation:
It should be mentioned that the velocity and the temperature of the fluid have been become dimensionless by the following equations:
2.3 Boundary conditions
This set of nonlinear elliptical governing equations has been solved considering the following boundary conditions:
– At the tube inlet (θ = 0):
–At the fluid–solid interface (r = D/2):
– At the tube outlet (θ = π): the diffusion flux in the direction normal to the exit plan is assumed to be zero for all variables and an overall mass balance correction is also applied.
2.4 Grid independence
As shown in Fig. 2, the unstructured mesh was applied in mesh system and for more accuracy, near the wall, the grid was refined with a growth factor of 1.2. A grid independent test was carried out to find the suitable grid number. The effect of increasing the number of grid on the axial velocity profile and the dimensionless temperature profile in a horizontal direction at θ =5π/6, Re = 400 and Gr = 400,000 also were shown in Fig. 2. It can be seen when the grid number were more than 802,000, the results were independence of grid.
2.5 Model validation
In order to see the accuracy of the computational results the friction factor of the current research has been compared with the corresponding experimental results that were presented by Wojtkowiak and Popiel [23]. The results have been calculated for Den numbers between 20 and 303 for the adiabatic flows; and for Den numbers from 80 to 203 for the non-adiabatic ones. As shown in Fig. 3 there are good agreement between the experimental results and present work. In the case of adiabatic flows, the average deviation is about 5% and for the non-adiabatic flows, it is about 4%. It should be noted that the Dean number was introduced Wojtkowiak and Popiel [23] as:
Comparison the present simulation with the experimental results of Wojtkowiak and Popiel [23] for Adiabatic flow (a) and Non-adiabatic flow (b)
Furthermore, the Darcy friction factor for the adiabatic and non-adiabatic wavy pipe flows was calculated using the below formula.
3 Numerical method
In order to have a fully developed flow at the entrance, a straight pipe was employed to develop flow along the straight pipe before enters to the bend. The governing equations were discretized using the Control Volume Method and solved by steady-state implicit method. Second order upwind scheme is adopted for the convective and diffusive terms while the SIMPLEC algorithm was used for the velocity–pressure coupling and the convergence criterion is set to be 1E-06.
4 Results and discussions
Figure 4 indicates the dimensionless velocity contours, the secondary flow vectors, and the dimensionless temperature of the fluid inside the dimple and smooth curved tubes. The outcomes presented here have been achieved at the cross section of θ = 5π/6 and for Gr = 80,000, Re = 400. As it can be seen in Fig. 4a, the bumps at the inner side of the dimple tube, have directed the flow to the central axis and due to a constant mass flow rate, compared to that of the smooth tube flow, the axial dimensionless velocity increases. For the case in which Re is 400, owing to the dominant amount of centrifugal forces, the secondary flow vectors have been driven completely to the direction of the inertial forces. Therefore, the secondary flows are completely symmetric with respect to the horizontal axis (Fig. 4b). Also as previously mentioned, the cross sectional area in the rough tubes is smaller and the flow is mostly forced into the tube center.
Additionally, because of constant mass flow rate the dimensionless velocity is higher than that of the smooth tube. As a result, compared to the smooth tubes, the secondary flows’ magnitude in the rough tubes is more. In the dimensionless temperature contours (Fig. 4c), it can be seen that due to weak buoyancy forces, the contours are almost symmetry with respect to the horizontal axis.
A region with higher temperature can be observed at the inner side of the tube where the centrifugal forces are low and the fluid velocity is lower than that of the outer zone. Again because of low Grashof number, symmetry is expected to be seen with respect to the horizontal diameter. There is an interesting behavior in the dimensionless temperature contours of the fluid inside the dimpled tube. The fluid temperature tends to become more uniform because of higher heat transfer rate caused by dimples throughout the tube cross section. Subsequently, more heat transfer rate leads to higher temperature gradient close to the dimpled tube wall, compared with that of the smooth tube.
Figure 5 shows the axial evolution of mean heat transfer coefficient along the smooth and the dimple curved tubes, for different Reynolds numbers. In both tubes, for a given Gr and Re numbers, in the absence of the buoyancy force, the centrifugal force tends to improve the heat transfer coefficient. However, increasing the buoyancy forces along the tube, mitigates the positive effects of the centrifugal forces. The concurrent effects of these forces reduce the convective heat transfer coefficient and even lead to a downward trend in the chart. This is clearly shown in Fig. 6.
In the dimpled tube, at Re = 100 the buoyancy forces are dominant over the centrifugal forces. However, by increasing Re number up to 200, the simultaneous effects of the buoyancy and the centrifugal forces are almost the same order. These two secondary forces have opposite effect on the heat transfer coefficient because of reducing the generated secondary flows. On the other hand, by more increase in Re the centrifugal forces become dominant and the buoyancy forces are not able to reduce its positive effect on the heat transfer coefficient. Therefore, by increasing Re up to 400, heat transfer coefficient also augments. Comparing both tubes reveals that the dimple one has better performance in terms of heat transfer at the low Re values.
In general, comparing both tubes reveal that the dimple one shows better performance in terms of heat transfer at the low Re numbers as well as low Gr numbers. Its heat transfer coefficient can be affected by the Dean number, Re and surface roughness.
To compared the necessary pumping power between the dimple tubes and smooth tubes Table 1 is presented. Roughening a tube is believed to intend more uniform velocity profile. Thus as seen in Table 1 increasing the Re > 200 causes to see more pressure loss in the case of smooth tube than the dimple one. It is well known that in mixed convection flow in a curved tube both centrifugal and buoyancy forces induce secondary flows are important. These secondary flows alone intend to uniform the fluid flow. However, their simultaneous effects are opposite. At Re = 200 these two forces are almost at the same order and their simultaneous effect is minimum. While increasing or decreasing the Reynolds number, the centrifugal forces augments or decline (decline or augments buoyance forces) respectively. Which means by increasing or decreasing the Reynolds number (from 200) one of these forces becomes more important and thus their effects augment. This effect intends to uniform the fluid flow and thus the effect of roughening tube on the pressure drop becomes less important.
To compare the performance of the dimpled and smooth tubes for a given Gr, j/f at different Reynolds number is presented in Fig. 7. As it is seen roughening a tube improve its performance at the lower Reynolds number. Increasing the Reynolds number pressure drop becomes more important in dimple tube. In this figure f is friction factor (Eq. 10) and j is the Colburn J factor which is defined as:
5 Conclusion
In this research, a dimpled tube is numerically studied to understand its effects on the thermo-fluid behavior of a laminar mixed convection flow regime inside a curved tube. Simultaneous effects of the buoyancy forces and centrifugal forces are considered. It is shown that These forces significantly affected the fluid flow. For a given Reynolds number inlet flow velocity is slightly lower than the one in smooth tube because of dimple structure. Thus higher axial velocity and stronger secondary flow compared to a smooth tube is resulted with using dimpled tubes. It is seen that for a given Reynolds number increasing the Grashof number causes to decrease heat transfer coefficient as results of opposing effect of buoyancy and centrifugal forces. Comparisons between the dimpled tube and smooth tube shows that heat transfer coefficient augments with using dimpled tubes. While the pumping power slightly decreases where the simultaneous effects of these forces reduces (Re < 100 and Re > 500). In the case of dimpled tubes the effective solid-flow interface augments and also the near wall flow is affected by the dimples. Therefore, it can be said the dimpled tube shows better performance in terms of heat transfer at the low Re numbers as well as low Grashof number. Its heat transfer coefficient can be affected by the Dean number, Re and surface roughness.
Abbreviations
- C f :
-
Skin friction factor
- D :
-
Tube diameter (m)
- e :
-
Roughness height (m)
- E :
-
Total energy (J/kg)
- f :
-
Darcy-Weisbachfriction factor
- g :
-
Gravitational constant (9.81m/s2)
- h :
-
Heat transfer coefficient
- j :
-
Colburn J factor
- k :
-
Thermal conductivity (W/m K)
- L :
-
Tube length (m)
- P :
-
Pressure (Pa)
- q " :
-
Uniform heat flux (W/m2)
- r :
-
Radial direction
- R :
-
Curvature radius (m)
- T :
-
Temperature (K)
- V :
-
Velocity (m/s)
- \( \overrightarrow{V} \) :
-
Velocity vector (m/s)
- z :
-
Axial direction
- n:
-
New
- w:
-
Tube wall
- 0:
-
Inlet
- θ :
-
Angular coordinate
- ρ :
-
Density (kg/m3)
- μ :
-
Dynamic viscosity (N s /m2)
- τ :
-
Shear stress (Pa)
- De n :
-
New Dean number Den = Re(D/2R)
- Gr :
-
Grashof number Gr = gβq"D4/kν2
- Nu :
-
Nusselt number Nu = hD/k
- Re :
-
Reynolds number Re = ρVD/μ
References
Bergles AE (1998) Handbook of heat transfer, 3rd edn. McGraw-Hill, New York
Bilen K, Cetin M, Gul H, Balta T (2009) The investigation of groove geometry effect on heat transfer for internally grooved tubes. Appl Therm Eng 29:753–761
Chen Y, Chew YT, Khoo BC (2013) Heat transfer and flow structure in turbulent channel flow over protrusions. Int J Heat Mass Transf 66:177–191
Kumar P, Kumar A, Chamoli S, Kumar M (2016) Experimental Investigation of Heat Transfer Enhancement and Fluid Flow Characteristics in a Protruded Surface Heat Exchanger Tube. Exp Thermal Fluid Sci 71:42–51
Vicente G, Garcia AG, Viedma A (2002) Heat Transfer and pressure drop for low Reynolds turbulent flow in helically dimpled tubes. Int J Heat Mass Transf 45:543–553
Sonraki k KR (2001) Condensation of R-134a inside dimpled helically coiled tube-in-shell type heat exchanger. Appl Therm Eng 129:535–548
Nivesrangsan P, Pethkool S, Nanan K, Pimsarn R, Fuller KG (2010) Thermal performance assessment of turbulent flow through dimpled tubes. Proceedings of the 14th International Heat Transfer Conference IHTC14, pp. 1-8
Kukulka DJ, Smith R, Fuller KG (2012) Development and evaluation of vipertex enhanced heat transfer tubes for use in fouling conditions. Theor Found Chem Eng 46:27–633
Kukulka DJ, Smith R (2013) Thermal-hydraulic performance of vipertex 1EHT enhanced heat transfer tubes. Appl Therm Eng 61:60–66
Kukulka DJ, Smith R (2017) Comparison of condensation and evaporation heat transfer on the outside of smooth and enhanced 1EHT tubes. Appl Therm Eng 105:917–922
Mashayekhi M (2014) Numerical study of effect of roughness on the turbulent convective heat transfer of a nanofluid, Master thesis, University of Sistan and Baluchestan
Ming T, Cai C, Yang W, Gan T (2018) Optimization of Dimples in Microchannel Heat Sink with Impinging Jets — Part A: Mathematical Model and the Influence of Dimple Radius. J Therm Sci 27:195–202
Shui L, Sun J, Gao F, Zhang C (2018) Flow and Heat Transfer in the Tree-Like Branching Microchannel with/without Dimples. Entropy 20:379
Sobhani M, Behzadmehr A (2018) Investigation of thermo-fluid behavior of mixed convection heat transfer of different dimples-protrusions wall patterns to heat transfer enhancement. Heat Mass Transf 54:3219–3229
Goering DJ, Humphrey JAC, Greif R (1997) The dual influence of curvature and buoyancy in fully developed tube flows. Int J Heat Mass Transf 40:2187–2199
Wael AI (2014) Numerical study on turbulent heat transfer and pressure drop of nanofluid in coiled tube-in-tube heat exchangers. Energy Convers Manag 79:304–316
Chimres N, Wang CC, Wongwises S (2018) Optimal design of the semi-dimple vortex generator in the fin and tube heat exchanger. Int J Heat Mass Transf 120:1173–1186
Li LJ, Lin CX, Ebadian MA (1998) Turbulent mixed convection heat transfer in the entrance region of a curved pipe with uniform wall-temperature. Int J Heat Mass Transf 41:3793–3805
Akbarinia A, Behzadmehr A (2007) Numerical Study of Laminar Mixed Convection of a Nanofluid in a Horizontal Curved Tube. Appl Therm Eng 27:566–586
Ghaffari O, Behzadmehr A, Ajam H (2010) Turbulent mixed convection of a nanofluid in a horizontal curved tube using a two-phase approach. International Communication in Heat and Mass Transfer 37:1551–1558
Alikhani S, Behzadmehr A, Saffar-avval M (2011) Numerical study of nanofluid mixed convection in a horizontal curved tube using two-phase approach. Int J Heat Mass Transf 47:107–118
Huminic G, Huminic A (2016) Heat transfer and flow characteristics of conventional fluids and nanofluids in curved tubes. Renew Sust Energ Rev 58:1327–1347
Wojtkowiak J, Popiel CO (2000) Effect of cooling on pressure losses on U-type wavy pipe flow. International Communication in Heat and Mass Transfer 27:169–177
Author information
Authors and Affiliations
Corresponding author
Ethics declarations
Conflict of interest
There is no conflict of interest.
Additional information
Publisher’s Note
Springer Nature remains neutral with regard to jurisdictional claims in published maps and institutional affiliations.
Highlights
• Numerical study of a laminar mixed convection inside a curved dimpled tube.
• Heat transfer coefficient of a curved dimpled tube is more than that of a smooth one.
• Skin friction coefficient of a curved dimple tube, in low Reynolds number, is negligible.
• Using dimple tubes in the low Reynolds numbers are more beneficial.
Rights and permissions
About this article
Cite this article
Ganjbakhsh, N., Alikhani, S. & Behzadmehr, A. Numerical study of the effects of surface roughness on the mixed convection heat transfer of a laminar flow inside a horizontal curved dimpled tube. Heat Mass Transfer 55, 2009–2016 (2019). https://doi.org/10.1007/s00231-018-2502-4
Received:
Accepted:
Published:
Issue Date:
DOI: https://doi.org/10.1007/s00231-018-2502-4