Abstract
In this paper, a closed-loop virtual simulation system has been developed to simulate the milling process considering the interactions between manufacturing processes and machine tool dynamics. The system consists of cutting force module, machining stability module, and surface generation module. The synchronous effects of the machining parameters, tool geometry parameters, and the dynamic performance of the machine tool system are considered in the model, and the instant machine dynamic motion error is compensated in the model as a feedback to correct the cutter trajectories. Instantaneous tool-workpiece contact status is used to calculate cutting force, and the peak-to-peak cutting force plot is used to predict the machining stability in time domain under different depths of cut and cutting speeds. The envelope curve of the cutting tool is used to reconstruct the machined surface texture. Moreover, to verify the feasibility of the proposed system, micro-milling experiments are conducted with results showing that the simulation system enables the effective prediction of micro-milling process such as the cutting forces and machined surface quality. It can be potentially applied in production on processing parameter optimization and surface topography prediction.
Similar content being viewed by others
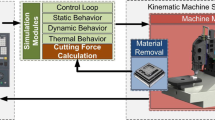
Avoid common mistakes on your manuscript.
1 Introduction
Milling, one of the most common processing methods of high machining efficiency, has been widely used in industry for mechanical equipment manufacturing and mould processing [1,2,3]. However, due to its discontinuous cutting feature, process-machine interactions (PMI) have significant effects on the machining process. For example, the cutting force often varies evidently which might cause the chattering of machining process or even the early failure of cutting tools. In-depth understanding of PMI is of significance to improve the machining efficiency and to ensure the surface quality of the machined surface.
The PMI have become a central research topic in production engineering within the last years, not only in academic research but also in industrial companies. The PMI of a machine tool system mainly depends on the selected machining parameters, and it can be evaluated by monitoring the time evolution of cutting force or testing the machining stability. Therefore, in order to improve the machining efficiency of the machine tool system and obtain high-quality machined surface, the machining parameters are required to be optimized to achieve efficient and stable machining.
Numerous researches have been carried out to understand the machining process, such as cutting force, machining stability, surface topography, and roughness. Grossi et al. [4] developed a cutting force prediction model for high-speed machining and investigated the cutting force coefficient at different spindle speeds. Considering the influence of cutter vibrations and cutter runout, Wang et al. [5] proposed a cutting force prediction algorithm, evidently reducing the prediction error of cutting force by up to 30%. Kang et al. [6] proposed an analytical mechanistic model for micro-end-milling to predict the cutting force, in which the effect of cutting-edge radius of micro-tool is considered. Bao and Tansel [7] proposed an improved cutting force model for micro-milling considering the effects of the trochoidal motion of the cutter. Montgomery and Altintas [8] studied cutting force and surface generation in peripheral milling and proposed a model to predict the cutting force and surface finish under rigid or dynamic cutting conditions. Zhang et al. [9] proposed a cutting force model which includes an algorithm for the calculation of the variable entry and exit angles caused by tool runout and tool deflection.
As one form of self-excited unstable vibration, chatter is easily generated in the machining process. Chatter vibration will lead to an increased cutting force, and thus reduce the tool life and even damage the machine tool system [10]. In order to avoid chatter vibrations, a pre-plan of the machining processes is usually performed to find the chatter-free cutting conditions with the aid of experienced stability diagram. To improve the accuracy of stability lobe diagram, several modelling methods have been developed to calculate machine tool system dynamic performance and to predict the surface generation. Altintas and Budak [11] proposed one frequency domain solution, and it could be applied in the machining processes in which the radial cutting depth is larger than a quarter of the cutter diameter. Altintas et al. [12] presented a unified frequency and discrete time domain chatter stability laws for milling. This law could be applied to reveal the dynamic process of the performance of the machine tool system with low radial cutting depth and small number of teeth. Minis and Yanushevsky [13] described the dynamics of the milling process through differential-difference equations with time-dependent periodic coefficients and examined the system stability by using the Fourier analysis and the basic properties of the parametric transfer functions of linear periodic systems. Insperger et al. [14] investigated the influence of runout on the milling chatter frequencies by using the Floquet theory. To predict the surface quality, Liu et al. [15] proposed a floor surface-generation model considering the effects of minimum chip thickness, elastic recovery, and transverse vibration. Kouravand et al. [16] developed a surface roughness model for end-milling of micro-channel by using kinematic rules and transformation operators. Ehmann and Hong [17] developed a prediction method of surface topography generation based on the general machine tool kinematics model and the generalized model with deterministic and non-deterministic cutting tool geometries. Peigne et al. [18] proposed a 2.5-dimensional geometrical model for the time domain simulation of surface generation in end milling. Ryu et al. [19] studied the effects of tool runout, tool-setting errors (such as tool tilting and eccentricity between tool centre and spindle rotation center) on the roughness, and texture generation on the end-milled surfaces, and the tool deflection caused by cutting forces was analyzed.
However, the focus of above studies is mainly on the single role of cutting force, machining stability, surface topography and roughness, or the interaction between any two factors. It is well-known that cutting force could impose external stimulation on the machine tool system during the machining process which will result in the instantaneous variation of the depth of cut and change tool cutting trajectories. This will significantly degrade the machined surface topography.
For this reason, one closed-loop virtual simulation system for milling process which consists of cutting force module, machining stability module, and surface generation module is developed in the present study. The coupled interactions among the dynamic performance of machine tool system, the dynamic cutting force, machining stability, and machined surface are considered in the proposed virtual simulation system by forming a real-time feedback between each module.
The paper is organized as follows: Section 2 briefly describes the integrated simulation system. Section 3 introduces each module of the integrated simulation system. In Section 4, a case study for micro-milling by using the proposed integrated simulation system is given, and the experimental results are compared with the simulation results. The main conclusions drawn in this paper are given in Section 5.
2 Integrated simulation system for milling
The flowchart of the virtual simulation system for milling is shown in Fig. 1. The cutting tool parameters (diameter, number of teeth, tool geometry, material parameters), spindle runout, and the machining parameters (feed per tooth, spindle speed, depth of cut) and workpiece material property parameters are used as input to predict the cutter trajectories. The initial cutting force is first calculated in the time domain by the cutting force module based on the instantaneous uncut chip thickness. The synchronous effects of the machining parameters and tool geometry parameters and the dynamic performance of the machine tool system are considered in the model when updating the cutter trajectories, and the instant machine dynamic motion error (xtw, ytw) is compensated in the model as a feedback to correct the instantaneous uncut chip thickness. The output of cutting force and machine tool dynamic motion are used as the indicators to predict machining stability and to understand the surface generation process. The envelope curve of the cutting tool is used to predict the machined surface texture. Thus, a closed-loop virtual simulation system is developed for the milling process which consists of the cutting force module, machining stability module, and surface generation module.
Considering the dynamic performance of the machine tool has significant influences on the dynamic cutting force, machining stability, and surface quality of the machined surface [20], an effective way is adopted to improve the simulation accuracy by considering the possible effects of machine tool system dynamics and multiple time delay in the machining process.
The simulation system structure is illustrated in Fig. 2. In the simulation process, the dynamic parameters of the machine system were firstly tested and pre-defined in the integrated simulation system. The dynamic performance of the machine tool system can be obtained by either machining experiments or finite element simulations [21]. The modal parameters of the machine tool system were obtained from frequency response function by the modal fitting technology. The machining parameters and cutter parameters were then input into the integrated simulation system. During the simulation process, the cutting force, dynamic tool path, and the machining stability were calculated, and the machined surface topography was generated in the dynamic surface generation programme by combining the cutter geometric parameters and dynamic tool cutting path.
2.1 Cutting force module
In most of the existing cutting force models, the calculation of the instantaneous uncut chip thickness is entirely based on input parameters, and pre-defined entrance and exit angles [22]. Cutting coefficients can be determined by either mechanistic or numerical methods; in this paper, the value of 750 N/mm2 is used for Al6061 [23]. However, in a milling process, the chip thickness and the cutting force tend to change nonlinearly, which results in dynamic fluctuations in the machining process. Moreover, the tool tooth may occasionally lose contact with workpiece in the cutting region, which could also induce the nonlinear fluctuation of cutting force [24]. For example, the cutting force could cause the deformation of the cutter and workpiece, which changes the instantaneous uncut chip thickness. The realistic cutting force of each tool tooth can also be affected by the feed per tooth, the deflection of the cutter, and even the surface topography/subsurface damage formed by previous teeth. Therefore, to accurately predict the cutting forces, the iterative approach is required, and a dynamic cutting force calculation scheme is proposed in the present cutting force module (as shown in Fig. 3).
In order to model the dynamic performance of the machine tool system, the structural loop of the machine tool is usually divided into a cutter-machine loop and a workpiece-machine loop. Since the dynamic performance of the cutter-machine loop is always worse than that of the workpiece-machine loop, therefore, only the cutter-machine loop is considered in this paper.
The cutter-machine loop can be simplified into two single degree of freedom (SDOF) systems in x (feed direction) and y (cross-feed direction). The equations of motion are depicted as:
where mx, my; cx, cy; and kx and ky are mass, damping, and stiffness of the machine tool in x- and y-directions, respectively. Fx(t) and Fy(t) represent the instantaneous cutting forces in x- and y-directions, respectively. \( x,y;\dot{x},\dot{y};\mathrm{and}\ \ddot{x},\ddot{y}\kern0.5em \) are the positions, velocities, and acceleration of the cutter in x- and y-directions.
After the solution of the Euler integration, Eq. (1) could be transformed into the following equations:
where the velocities on the right hand side of Eq. (3) are retained from the previous time step. The new velocities are then applied to determine the new displacements in Eq. (4). Again, the displacements on the right hand side of Eq. (4) are those from the previous time step. dt is the time interval set by the programme.
The relative dynamic displacement between the tool and workpiece in x- and y-directions can be given as:
Thus, the instantaneous depth of cut can be obtained by combining the tool-workpiece displacement (calculated in Eq. (5)) and the specified depth of cut. The cutting force can then be calculated. More detailed description can be found in Ref. [25].
2.2 Machining chatter module
In time domain, the gradients information of cutting forces (peak to peak (PTP) force curves) can be used to evaluate the machining stability of a machine tool system [10]. The sharp change of the PTP force curve gradient indicates the transition of machining stability from stable to unstable (chatter) [26]. However, the PTP force curves could not give a direct representation of the relationship among machining stability, axial depth-of-cut, and spindle speed. For this reason, the gradients of the PTP force is calculated using the contour plot function in MATLAB and an analytical PTP stability lobes can be generated which clearly describe the machining status.
2.3 Surface generation module
The procedure of the surface generation is illustrated in Fig. 4. The cutter geometry parameters were obtained through the SEM or AFM measurement of the tool cutting edges (step 1). In the milling process, the cutter is fed at specified machining path according to the machining programme to milling the workpiece into the designed shape, and the machined surface can be generally expressed as the envelope curve of cutting tool motion trajectories (step 2). The whole machining process could be simulated by using the homogeneous transformation matrix (HTM). The Z-map technology in the commercial software MATLAB was then used to plot minimum z position value against x and y positions in the workpiece coordinate system (step 3), and then, the final machined surface was reconstructed (step 4); the detail of the surface generation can be found in Ref. [27, 28].
It is worth to mention that the milling machine is not an ideal rigid body system, and the tool runout during the machining process could lead to the dynamic fluctuation of the relative displacement between tool and workpiece, leading to the change of the processing trajectory. To accurately simulate the milling process, those motion errors caused by the spindle runout and tool alignment error could not be neglected. In the present surface generation module, the effects of the tool runout and the dynamic response of the machining system on the surface generation were considered. The dynamic response of the machining system mainly refers to the dynamic displacement between tool and workpiece acting with the cutting force obtained from the cutting force module. The dynamic spindle runout was treated as the results of the coupled effects of tool motion errors considering the tool alignment error and spindle runout. All these effects are considered as compensations on the tool position when updating the instantaneous tool cutting path.
3 Case study: a micro-milling process
3.1 Experimental setup
To validate the feasibility of the proposed simulation system, a serial of slot milling experiments was conducted. The milling experiments were carried out on three-axis precision milling machine tool (NANOWAVE MTS5R). The machine tool is equipped with three DC servo motor-driven precision linear stages with smallest feed of 0.1 μm, and a high-speed spindle with adjustable rotation speed ranging from 5000 to 80,000 rpm; the tool runout in the whole rotation range is less than 1 μm. The practical experimental setup is illustrated in Fig. 5. A three-component piezoelectric dynamometer (Kistler 9256C2, with the sampling frequency up to 3.5 kHz) is mounted on the X-Z stage to measure the feed and cross-feed cutting forces. The workpiece material is Al6061; the workpiece is clamped on a fixture attached to the dynamometer.
3.2 Simulation parameters
The dynamic performance of the machine tool is an important input in the simulation and should be obtained beforehand. Due to the small diameter (1 mm) of the cutting tool, it is difficult to experimentally detect the dynamic response of the tool tip. Therefore, finite element simulations are adopted in this case. Figure 6a shows the finite element model for the micro-milling machine. The key input parameters of the machine tool components, such as bearing stiffness, materials properties, and damping coefficients, are extracted from relevant datasheet and/or determined from dynamic tests; the details can be found in Ref. [28]. The joint characteristics of the machine tool, such as the bolt joint and the bearing connection, have great impact on the dynamic performance. Therefore, the modelling approach of the junction directly determines the accuracy of the whole model of the machine tool. In this study, the contact elements CONTA173 and TARGE170 were applied to the contact components. The contact rolling bearings in the slides were modelled by spring elements. The Prets179 element was used to simulate the bolt joint which can exert the preload by the node K. A modal analysis was first performed to obtain the natural frequencies of machine tool and the corresponding vibration modes. As shown in Fig. 6b, the first-order natural frequency of the machine system is 478 Hz and its vibration mode is the spindle swinging around y-axis with the Y slide. By using the peak-picking fitting method, the modal dynamic parameters can be determined.
Two-flute micro-flat-end mills with the cemented carbide is adopted in the machining experiments. Table 1 lists the detailed parameters used in milling experiments, including tool geometry parameters, dynamic parameters of the machine tool, and machining parameters. Those parameters were directly used as the boundary conditions of the simulation system to stimulate the milling process. Two sets of machining parameters with different spindle speeds of 18,000 rpm and 26,000 rpm were selected to demonstrate the effectivity of the proposed simulation system (as shown in Table 2), and the feed per tooth and the depth of cut were specified as 10 μm and 0.25 mm, respectively. Although the slot milling is selected as the case study to verify the proposed system, the system is also effective for side milling.
3.3 Results and discussion
Step 1
The cutting force module was firstly run to obtain dynamic cutting forces. It will be adopted to further evaluate the machining stability of the machining system. Figure 7 compares the cutting forces predicted by the simulation system and the cutting forces measured by the dynamometer in the first set of machining experiment. It shows that the simulation results accorded well with the experimental results and both the x- and y-directions cutting forces fluctuate within a range of 4 N. As compared with the first set of machining, the amplitude of cutting force of the second set of machining increased to 20 N and 12 N in x- and y-directions, respectively (Fig. 8). High accordance between the simulation results and the experimental results were found for the second set of machining as well, which demonstrated the effectivity of the cutting force prediction module. This accordance attributes to the consideration of the PMI effects on the machining process in the proposed cutting force model. This feature has great advantage than conventional cutting force models which did not consider the dynamic performance of machine tool system. Moreover, the increase of the cutting forces for the second machining indicated that the cutting speed has significant effects on the machining process under the same depth of cut and the feed per tooth. The increase of the cutting forces might imply the alternation of the machining status from stable to unstable, which will be further analyzed by the stability module.
Step 2: machining stability module
To further demonstrate the feasibility of using the system on processing parameter optimization, a machining stability diagram was generated using the chatter module of the proposed simulation system. A large amount of simulations was running with the axial depth-of-cut changes from 0.1 to 1 mm at an interval of 0.1 mm (10 depths of cut), and the spindle speed is chosen from 8000 to 55,000 rpm with an interval of 235 rpm. The peak-to-peak (PTP) cutting force plot and the peak-to-peak stability lobes consist of the results obtained from 2000 simulation runs. As shown in the Fig. 9a, the cutting force is stable when the axial depth-of-cut is less than 0.1 mm. With the increases of the axial depth of cut, the PTP Force_y is changing with the spindle speed and the chatter occurs. In order to reflect the relationship between cutting stability, axial depth-of-cut, and spindle speed, a contour plot of the PTP Force_y is further generated as shown in Fig. 9b. This diagram reflects the machining stability under different processing conditions. It can be found that the first set of machining parameters belongs to the stable region and the second set of parameters will lead to the unstable machining.
For experimental verification, the fast Fourier-transform (FFT) analysis of the experimental cutting forces obtained in step 1 was carried out. The FFT analysis results are shown in Fig. 10. The results show that only the tooth passing frequency and its harmonic frequencies can be found for the first machining (Fig. 10a), which indicates that no chatter occurs during the first set of machining process. For the second set of machining parameters, the cutting force was found to fluctuate violently. Indeed, the cutting-in and cutting-out of the milling tool could lead to the instability of the machining process. The FFT analysis result shows that except for the tooth pass frequency and its harmonic frequencies, chatter frequencies were also observed as indicated in Fig. 10b. Thus, the chatter occurs during the second machining process. The experimental results agreed with the simulation prediction, which demonstrates the effectivity of using the machining stability module to predict the machining status.
Step 3: surface topography and roughness generation
In the surface generation module, the tool profile (expressed in a mathematical model) and the tool trajectories considering the dynamic displacement caused by the cutting force are combined and used to reconstruct the 3D surface topography. Figures 11 and 12 show the simulation of predicted surface topographies of the machined surfaces under the two sets of machining parameters, respectively. For the first machining case, it can be found that the trajectory of the tool tip exhibits evident periodicity (Fig. 11a), and clear and regular tool marks can be found on the machined surface (Fig. 11b), indicating that the machining process is stable. The surface roughness was calculated according ISO 4287:1997 standard; the predicted surface roughness (Ra) is 0.18 μm.
For the second machining case, it is observed that the periodicity of tool trajectory (Fig. 12a) is obviously worse than that of the first case, and the tool marks on the machined surface are messy (Fig. 12b). The predicted surface roughness (Ra) is 0.536 μm, much worse than that of the first cutting. The results also indicate that the machining process is instable under the second set of machining parameters.
To validate the simulation results, experiments were carried out using the same machining parameters. Figures 13 and 14 are the surface measurement results obtained by a white light interferometer (Vecco NTll00). As shown in Fig. 13, regular tool marks can be found in the machined surface when machining at the spindle speed of 18,000 rpm, indicating that a stable machining process was achieved under the first set of machining parameters. The surface roughness (Ra) is 0.190 μm, approximately consistent with the value of 0.180 μm predicted by simulation.
For the second machining, the spindle speed was increased to 26,000 rpm, and the tool marks on the machined surface are found to be orderless as shown in Fig. 14. The surface roughness (Ra) of machined surface is 0.518 μm which agreed well with the value of 0.536 μm predicted by simulation model. It is noted that the 10~20 nm difference on the surface roughness between simulation and experimental results might result from the uncertainty of the measurement equipment and the possible random machining error of the experiments.
The good agreement of the simulation and experimental results indicates the high accuracy and reliability of the proposed simulation system for micro-milling process. It is also noted that the proposed simulation system can predict the cutting force, the machining stability, and the machined surface topography in advanced with preset machining parameters, which potentially can reduce the cost and time on processing parameter selection and optimization in a production line.
4 Conclusion
The paper presents a novel simulation system to simulate the surface generation in milling process. The feasibility of the simulation system has been demonstrated by experiments. The interactions between structure and process in the machining process is established, and a basic understanding of the acting inter-relationships is achieved, which can be used to specifically influence and plan manufacturing processes in the future. The conclusions are drawn as follows:
-
1)
A forward closed-loop model for the milling process is established considering the dynamics processing-machine interactions. The proposed system can be used to predict the cutting force, machining stability, and machined surface topography under different processing parameters.
-
2)
A time domain cutting force module considering the dynamic regenerative effect has been established, and a machining chatter prediction module based on the changes of PTP force has been achieved. The proposed model successfully predicted the occurrence of chatter, and the simulation results have been verified by the experimental results.
-
3)
The fluctuation of cutting forces and the dynamic performance of the machine have significant effects on the machined surface topography. The proposed surface simulation method bridges the gap between surface topography prediction and the dynamics processing-machine interactions. The machined surface roughness can be predicted by the proposed model.
-
4)
The good consistence of simulation and experimental results indicate that the proposed system can effectively predict the typical phenomena of a milling process. This method can be potentially applied to the selection and optimization of machining parameters in production.
References
Weule H, Hüntrup V, Tritschler H (2001) Micro-cutting of steel to meet new requirements in miniaturization. CIRP Ann 50(1):61–64
Liu X, DeVor RE, Kapoor SG, Ehmann KF (2004) The mechanics of machining at the microscale: assessment of the current state of the science. J Manuf Sci Eng 126(4):666–678
Alting L, Kimura F, Hansen HN, Bissacco G (2003) Micro engineering. CIRP Ann 52(2):635–657
Grossi N, Sallese L, Scippa A, Campatelli G (2015) Speed-varying cutting force coefficient identification in milling. Precis Eng 42:321–334
Wang SB, Geng L, Zhang YF, Liu K, Ng TE (2015) Cutting force prediction for five-axis ball-end milling considering cutter vibrations and run-out. Int J Mech Sci 96:206–215
Kang IS, Kim JS, Kim JH, Kang MC, Seo YW (2007) A mechanistic model of cutting force in the micro end milling process. J Mater Process Technol 187:250–255
Bao WY, Tansel IN (2000) Modeling micro-end-milling operations. Part I: analytical cutting force model. Int J Mach Tools Manuf 40(15):2155–2173
Montgomery D, Altintas Y (1991) Mechanism of cutting force and surface generation in dynamic milling. J Eng Ind 113(2):160–168
Zhang X, Ehmann KF, Yu T, Wang W (2016) Cutting forces in micro-end-milling processes. Int J Mach Tools Manuf 107:21–40
Smith S, Tlusty J (1993) Efficient simulation programs for chatter in milling. CIRP Ann 42(1):463–466
Altintaş Y, Budak E (1995) Analytical prediction of stability lobes in milling. CIRP Ann 44(1):357–362
Altintas Y, Stépán G, Merdol D, Dombóvári Z (2008) Chatter stability of milling in frequency and discrete time domain. CIRP J Manuf Sci Technol 1(1):35–44
Minis I, Yanushevsky R (1993) A new theoretical approach for the prediction of machine tool chatter in milling. J Eng Ind 115(1):1–8
Insperger T, Mann BP, Surmann T, Stépán G (2008) On the chatter frequencies of milling processes with runout. Int J Mach Tools Manuf 48(10):1081–1089
Liu X, DeVor RE, Kapoor SG (2007) Model-based analysis of the surface generation in microendmilling—part I: model development. J Manuf Sci Eng 129(3):453–460
Kouravand S, Imani BM (2014) Developing a surface roughness model for end-milling of micro-channel. [J]. Mach Sci Technol 18(2):299–321
Ehmann KF, Hong MS (1994) A generalized model of the surface generation process in metal cutting. CIRP Ann 43(1):483–486
Peigne G, Paris H, Brissaud D (2003) A model of milled surface generation for time domain simulation of high-speed cutting. Proc Inst Mech Eng B J Eng Manuf 217(7):919–930
Ryu SH, Choi DK, Chu CN (2006) Roughness and texture generation on end milled surfaces. Int J Mach Tools Manuf 46(3-4):404–412
Huo D, Chen W, Teng X, Lin C, Yang K (2017) Modeling the influence of tool deflection on cutting force and surface generation in micro-milling. Micromachines 8(6):188
Cheng K ed. (2008) Machining dynamics: fundamentals, applications and practices. Springer Science & Business Media.
Doukas C, Pandremenos J, Stavropoulos P, Foteinopoulos P, Chryssolouris G (2012) On an empirical investigation of the structural behavior of robots. Procedia CIRP 3:501–506
Tlusty G (2000) Manufacturing equipment and processes. Prentice-Hall, Upper Saddle River
Tlusty J, Ismail F (1981) Basic non-linearity in machining chatter. CIRP Ann 30(1):299–304
Chen W, Teng X, Huo D, Wang Q (2017) An improved cutting force model for micro milling considering machining dynamics. Int J Adv Manuf Technol 93(9-12):3005–3016
Smith S, Tlusty J (1991) An overview of modeling and simulation of the milling process. J Eng Ind 113(2):169–175
Chen, W., Zheng, L., Xie, W., Yang, K. and Huo, D., 2019. Modelling and experimental investigation on textured surface generation in vibration-assisted micro-milling. Journal of Materials Processing Technology, 266, pp.339-350.
Chen, W., Xie, W., Huo, D. and Yang, K., 2018. A novel 3D surface generation model for micro milling based on homogeneous matrix transformation and dynamic regenerative effect. International Journal of Mechanical Sciences, 144, pp.146-157.
Funding
The authors gratefully acknowledge financial support of the National Natural Science Foundation of China (Grant No. 499 51505107), the UK Engineering and Physical Sciences Research Council (EP/I033424/1, EP/M020657/1), the Project (HIT.NSRIF.2017029) Supported by the Natural Scientific Research Innovation Foundation in Harbin Institute of Technology, and the European Union’s Horizon 2020 research and innovation programme under grant agreement No. 767589.
Author information
Authors and Affiliations
Corresponding author
Ethics declarations
Conflict of interest
The authors declare that they have no conflict of interest.
Additional information
Publisher’s note
Springer Nature remains neutral with regard to jurisdictional claims in published maps and institutional affiliations.
Rights and permissions
About this article
Cite this article
Chen, W., Tong, Z., Huo, D. et al. A forward closed-loop virtual simulation system for milling process considering dynamics processing-machine interactions. Int J Adv Manuf Technol 104, 2317–2328 (2019). https://doi.org/10.1007/s00170-019-04057-7
Received:
Accepted:
Published:
Issue Date:
DOI: https://doi.org/10.1007/s00170-019-04057-7