Abstract
Olive oil mill wastewater (OMW), a by-product of the olive oil industry, each year is generated millions of tons all over Mediterranean countries. Uncontrolled disposal of the OMW leads to massive environmental problems including soil and water pollution. In this experimental study, the OMW was used to partly replace clean water for getting prepared formaldehyde solution. Then, phenol and formaldehyde solutions were synthesized under alkali conditions to obtain more green phenol–formaldehyde (PF) resin. The effect of the OMW substitution level on the chemical and thermal properties of PF resin was examined by the Fourier transform infrared (FT-IR) spectral and thermogravimetric (TGA) analysis, respectively. Moreover, the bonding strength of each PF resin was evaluated under dry and wet conditions. It was found that FT-IR measurements showed that the PF resin containing various amounts of the OMW had a chemical structure very similar to the PF resin. The thermogravimetric analysis demonstrated that the low‐molecular‐weight organics in the OMW had negatively affected the thermal stability of the modified PF resins. In addition, the wood samples bonded with the PF resin containing up to 30 wt% OMW met the minimum requirements of interior and exterior bonding performance according to standard EN 12765. The OMW could be replaced by clean water up to 30 wt% for the production of green phenolic resin.
Similar content being viewed by others
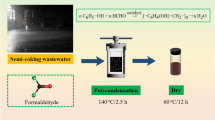
Explore related subjects
Discover the latest articles, news and stories from top researchers in related subjects.Avoid common mistakes on your manuscript.
Introduction
Olive oil production, which is common throughout the Mediterranean countries, plays an essential role in the social, economic and environmental in producing countries. Olive oil mill wastewater (OMW) is composed of olive fruit extract water and water added into the olive oil production process, which is the main waste product of the olive oil industry. The OMW is a dark, acidy, and free-flowing liquid with foul-smelling. It is consisting of water (83–92%), organic compounds, including 2-Hydroxyphenol, 4-Methyl-1,2-benzenediol, Hydroxy-tyrosol, 2-Phenylethanol, etc.) (4–16%) and minerals (1–2%). Uncontrolled disposal of the OMW leads to massive environmental problem including soil and water pollution. Environmental research has shown a strong interest in finding ways to reduce this waste. Numerous treatment techniques, including thermal, chemical, biological, and physicochemical ones, have been found to control OMW in earlier investigations. However, additional research is still required to identify easy, sustainable, and cost-effective solutions [1,2,3,4,5,6,7,8,9,10].
Phenolic resins are fundamentally classified into two categories: alkaline-catalyzed resols and acid-catalyzed novolacs. Conventionally, PF resol is a thermosetting resin derived from the addition and condensation reactions of phenol and paraformaldehyde under alkalinity conditions. Before use, paraformaldehyde is dissolved in water at 90 °C to form a formaldehyde solution of about 36–37 wt%. PF resol resins are generally used as an adhesive to produce wood-based products including particle boards, laminated boards and more, due to their high water resistance, excellent mechanical strength, outdoor durability and less volatile organic compound emissions [11, 12], [13,14,15,16].
There are many reported studies on the production of more green PF resin. Generally, they are related to the replacement of phenol by renewable resources such as bio-oil [17, 18], Kokten et al., 2018; [20], lignin products [21,22,23,24,25,26,27] and other natural materials [28,29,30,31].
In this study, the OMW was used to partly substitute clean water for getting ready formaldehyde solution. Then, phenol and formaldehyde solution were synthesized under alkali conditions to obtain green PF resin. The effect of the OMW substitution level on the chemical and thermal properties of the PF resin was examined by the Fourier transform infrared (FT-IR) spectral and thermogravimetry (TGA) analysis, respectively. Moreover, the bonding strength of each PF resin was evaluated by EN 205 standard and compared with the values specified in the EN 12765 standard.
Experimental
Materials
Olive oil mill wastewater (OMW) was collected from a local plant of olive oil in Balıkesir city, West of Turkey. It was stored at − 18 °C until use (pH 4.8; organic matter content: 7.4%). The OMW was filtered through a mesh size of 100 μm using filter paper before preparing the formaldehyde solution. The sodium hydroxide pellets were of analytical grade (NaOH, Sigma-Aldrich). Phenol (90% purity) and paraformaldehyde (98% purity) were supplied from the Gentaş Chemical Industry and Trade Marketing Inc. in Izmit city, Turkey.
Synthesis of the resin
Before the synthesis of the PF resin, a formaldehyde solution (at a concentration of 37 wt%) with different OMW/clean water substitute rates (0, 10, 20, 30, and 40 wt%) was prepared, the experimental design is given in Table 1. In a typical synthesis, the PF solution was put in the reactor, and then 0.70 of the whole NaOH solution (50 wt%) was unhurriedly incorporated at the temperature of 60 °C. The solution was warmed up to 90 °C, and it was held at a temperature of 90 °C continuously with stirring for 60 min. Then, it was cooled down to a temperature of 60 °C. Since PF resin is cured during the hot-pressing process at high pH levels, the other part of NaOH (0.30 of total weight solution) was loaded to adjust the pH (about 11.0) into the solution. Finally, at end of the synthesis, the resin was cooled up to a temperature of 25 °C. The details of the resin reactor were extensively described by [32].
Characterisation of the resin
The values of pH and viscosity of the PF resins were determined with a pH meter (TES-1380) and a digital viscometer (Brookfield, model: Dv-IPrime) at 25 °C, respectively. Free formaldehyde content was measured by the method of hydroxylamine hydrochloride based on European Standard DIN EN ISO 9397. The chemical structure of the PF resins was characterized by an Alpha FTIR spectrometer in the range of 400–4000 cm−1. The thermal behaviour of the PF resins was performed using a TG analyzer (HITACHI STA 7300) at temperatures range of 20–700 °C and the heating rates of 10 °C/min under a nitrogen atmosphere.
Bonding test
The PF resins were further evaluated as adhesives in wood lamellas samples. Beech wood (Fagus orientalis Lipsky) planks were used to investigate the bonding quality of the PF resins in accordance with standard EN 205. Beech wood samples were cut into dimensions of 20 × 50 × 100 mm and were bonded with various types of PF resin. The PF resin was applied to the surface of the lamella at a ratio of about 200 g/m2 by a hand brush. The press conditions such as pressure, temperature and duration were performed at 130 °C and 1.6 MPa for 10 min, respectively. Pressed wood samples were cut into a size of 5 × 10 × 150 mm. Before the bonding test, the treatments of the samples were determined by standard EN 12765. The wood samples from each group of the resin were divided into three subgroups for the different treatments. The treatments are summarized in Table 2.
Results and discussion
Characterization of the PF resins
The pH, viscosity values and free-formaldehyde content of all the PF resins are given in Table 3. As shown in this table, when the amount of the OMW increased from 0 to 40 wt%, the pH value of PF resin decreased from 11.90 to 10.67. The OMW contains organics, which are mainly phenolic compounds, and it has a low pH value (4.8). These compounds and the low pH value of the OMW decreased the pH value of the PF resins synthesized with the OMW. All the PF (PF10-PF40) resins synthesized with the OMW exhibited a higher viscosity than the reference PF resin. The free-formaldehyde content of the PF resins increased from 0.12 to 0.38% as the amount of the OMW substitution rate increased from 0 to 40 wt%. These results were not unexpected due to the OMW composed of high phenol and organic acid instead of clean water. These findings were well consistent with previous reports on the basic properties of green PF resins [18, 22, 33,34,35].
The FT-IR spectra of PF, PF10, PF20, PF30 and PF40 resins are illustrated in Fig. 1. It was observed that the replacement of the OMW had no distinctive effect on the resin in terms of the chemical structure. Except for the PF40, the spectrum of the PF40 resin was different from others, and mostly aromatic rings were observed. The characteristic bands at about 1600, 1500, 1250, 1150, 990 and 750 cm–1 could be attributed to the phenolics for the IR spectra of all PF resin. In addition, with the increase in the OMW substitution level the band at about 990 cm–1 became weak, and it vanished finally. FT-IR analysis results were consistent with previous reports prevıous reports on the IR analysis results of the PF resin and green PF resins [36], Zhang et al., 2013; [35, 38, 39].
The thermal behaviour of the PF and OMW containing the modified PF resins was characterised by TGA analysis (see Fig. 2). Generally, thermal degradation of phenolic resins occurred in three main steps, where the mass loss in the first stage might be caused by the release of free-phenol, formaldehyde, oligomer and water, due to the further cross-linking or condensation reaction between methyl groups (post-curing). The second stage occurred at a temperature between 350 and 450 °C. The huge mass loss in this stage might be due to the decomposition of bridged methylene (thermal reforming). Also, the phenol is further degraded into a carbonaceous structure at about 500–550 °C. The weight loss occurring in the last stage until 600 °C could be attributed to the fracture of the methylene bridge structure at high temperatures [26, 40, 41]: [42, 43]. TGA curves of reference PF resin and PF resins containing different amounts of OMW are shown in Fig. 2. As can be seen in Fig. 2, the weight losses of the PF resins containing different amounts of OMW showed a similar trend and the PF resin had higher thermal stability than that of PF resins containing OMW. The PF resins with a lower content of the OMW (PF10 and PF20) exhibited similar thermal behaviours to the reference PF resin. The weight loss of the PF resins with 30 wt% and 40 wt% OMW replacements dramatically increased at the temperature of 250 °C. This relatively low thermal stability can be explained by the presence of low molecular weight compounds in OMW. These compounds might be led to the decomposing more easily at high temperatures of the PF resins containing different amounts of the OMW.
Bonding performance of the PF resins
The data of the bonding strength of PF and PF with OMW resins are given in Table 4. The bonding strength of the wood samples bonded with the reference resin was higher than that of the samples bonded with the PF resins containing 10–40 wt% of the OMW. As the OMW substitution rate reached up to 40 wt%, the strength was dramatically decreased under dry conditions. However, the specimens bonded with PF resins containing OMW with 10 wt%, 20 wt%, and 30 wt% comply with met the minimum requirements, which was the durability class C1(≥ 10) according to standard EN 12765 under dry conditions. The highest bonding strength with a value of 8.8 N/mm2 was found in the reference resin specimens, followed by PF10 resin (8.2 N/mm2) under wet conditions (pre-treatment 2). For pre-treatment 3, a similar trend was observed with treatment 2. The bonding strength decreased dramatically after pre-treatment 3, as matched with pre-treatment 1 and pre-treatment 2. The bond quality was negatively affected by the presence of the OMW more or less. When the amount of the OMW in the PF resin was increased up to 30 wt%, the bonding strength of the samples decreased from 6.1 to 2.9 N/mm2. However, the samples bonded with the PF, PF10, PF20 and PF30 exceeded the minimum requirements for class C3 specified in EN 12765 standard. According to the bonding test results, it was recommended that the OMW can be partially replaced by clean water for the production of the green PF resin.
Conclusions
In this study, the OMW with a rich phenol content was used as the raw material to substitute clean water partially. It was synthesized with phenol and formaldehyde to produce green PF resin (Additional file 1). The effect of the OMW substitution level on the chemical and thermal properties of the PF resin was investigated by FT-IR spectral and thermogravimetric analysis respectively. Also, the bonding performance of each PF resin was evaluated by bonding tests. Based on the findings, the following conclusions can be asserted:
-
The basic properties, such as pH value, viscosity, and free formaldehyde content of the PF resins, were affected by the incorporation of the OMW. With the addition of OMW, the pH value of PF resins exhibited a decreasing trend to some extent. In contrast, the viscosity value and free formaldehyde content of the PF resin showed an increasing trend.
-
FT-IR spectra showed that the green PF resin could be successfully produced by polymerization of the OMW, phenol and formaldehyde.
-
The thermal stability of the reference resin was higher than PF30 and PF40 resins when the temperature was higher than 250 °C. The low‐molecular‐weight organics in the OMW negatively affected the thermal stability of the green PF resin.
-
Further increment in the OMW content decreased the bonding strength of the wood samples under dry conditions. Furthermore, regarding the bonding strength after pre-treatment 2 and 3 tests, the samples bonded with PF resins containing the OMW showed a lower bonding performance compared with bonded with reference PF resin. However, the PF resins containing the OMW, except for PF 40 resin, were satisfied the minimum requirements for durability classes of 1, 2, and 3 specified in EN 12765. Based on the findings of the present study, it was concluded that the OMW could be partially substituted (up to 30 wt%) to produce green phenolic resins for wood composites.
Availability of data and materials
The data used and analyzed during the current study are available from the corresponding author on reasonable request.
References
Abu-Dalo M, Abdelnabi J, Bawab AA (2021) Preparation of activated carbon derived from jordanian olive cake and functionalized with Cu/Cu2O/CuO for adsorption of phenolic compounds from olive mill wastewater. Materials 14(21):6636. https://doi.org/10.3390/ma14216636
Abu-Dalo M, Abdelnabi J, Al-Rawashdeh NA, Albiss B, Al BA (2022) Coupling coagulation-flocculation to volcanic tuff-magnetite nanoparticles adsorption for olive mill wastewater treatment. Environ Nanotechnol Monit Manag 17:100626. https://doi.org/10.1016/j.enmm.2021.100626
Cañizares P, Lobato J, Paz R, Rodrigo MA, Sáez C (2007) Advanced oxidation processes for the treatment of olive-oil mills wastewater. Chemosphere 67(4):832–838. https://doi.org/10.1016/j.chemosphere.2006.10.064
Carrara M, Kelly MT, Roso F, Larroque M, Margout D (2021) Potential of olive oil mill wastewater as a source of polyphenols for the treatment of skin disorders: a review. J Agric Food Chem 69(26):7268–7284. https://doi.org/10.1021/acs.jafc.1c00296
Fezzani B, Cheikh RB (2010) Two-phase anaerobic co-digestion of olive mill wastes in semi-continuous digesters at mesophilic temperature. Bioresource Technol 101(6):1628–1634. https://doi.org/10.1016/j.biortech.2009.09.067
Nieto LM, Hodaifa G, Rodríguez S, Giménez JA, Ochando J (2011) Degradation of organic matter in olive-oil mill wastewater through homogeneous Fenton-like reaction. Chem Eng J 173(2):503–510. https://doi.org/10.1016/j.cej.2011.08.022
Sar T, Yesilcimen Akbas M (2022) Potential use of olive oil mill wastewater for bacterial cellulose production. Bioengineered 13(3):7659–7669. https://doi.org/10.1080/21655979.2022.2050492
Sassi AB, Boularbah A, Jaouad A, Walker G, Boussaid A (2006) A comparison of Olive oil Mill Wastewaters (OMW) from three different processes in Morocco. Process Biochem 41(1):74–78. https://doi.org/10.1016/j.procbio.2005.03.074
Sierra J, Martı E, Montserrat G, Cruanas R, Garau MA (2001) Characterisation and evolution of a soil affected by olive oil mill wastewater disposal. Sci Total Environ 279(1–3):207–214. https://doi.org/10.1016/S0048-9697(01)00783-5
Türkekul B, Miran B, Canan A, Günden C (2010) Competitiveness of Mediterranean countries in the olive oil market. New Medit: Mediterranean Journal of Economics, Agriculture and Environment = Revue Méditerranéenne dʹEconomie Agriculture et Environment. 9(1):41–46
Gao Z, Lang X, Chen S, Zhao C (2021) Mini-review on the synthesis of lignin-based phenolic resin. Energy Fuels 35(22):18385–18395. https://doi.org/10.1021/acs.energyfuels.1c03177
Park BD, Riedl B, Kim YS, So WT (2002) Effect of synthesis parameters on thermal behavior of phenol–formaldehyde resol resin. J Appl Polym Sci 83(7):1415–1424
Aslan M, Özbay G, Ayrilmis N (2015) Adhesive characteristics and bonding performance of phenol formaldehyde modified with phenol-rich fraction of crude bio-oil. J Adhes Sci Technol 29(24):2679–2691. https://doi.org/10.1080/01694243.2015.1080474
Cai Z, Ros RJ (2010) Mechanical properties of wood-based composite materials. In: Centennial (ed) Wood handbook: wood as an engineering material. US Dept. of Agriculture, Forest Service, Forest Products Laboratory, Madison, p 12.1-12.12
Pizzi A (1993) Wood adhesives chemistry and technology. Marcel Dekker, New York
Wang W, Zhao Z, Gao Z, Guo M (2012) Water-resistant whey protein based wood adhesive modified by post-treated phenol-formaldehyde oligomers (PFO). BioResources 7(2):1972–1983
Sukhbaatar B, Steele PH, Ingram LI, Kim MG (2009) Use of lignin separated from bio-oil in oriented strand board binder phenol-formaldehyde resins. BioResources 4(2):789–804
Yi JP, Zhang JZ, Yao SX, Chang JM, Li B (2012) Preparation of bio-oil-phenol-formaldehyde resins from biomass pyrolysis oil. Appl Mechan Mater 174:1429–1432. https://doi.org/10.4028/www.scientific.net/AMM.174-177.1429
Kokten ES, Özbay G, Ayrilmis N (2018) Synthesis of biobased phenolic resins using catalytic pyrolysis oil and its effect on oriented strand board performance. J Adhes 96(5):475–489. https://doi.org/10.1080/00218464.2018.1481400
Jia L, Chu J, Li J, Ren J, Huang P, Li D (2020) Formaldehyde and VOC emissions from plywood panels bonded with bio-oil phenolic resins. Environ Pollut 264:114819. https://doi.org/10.1016/j.envpol.2020.114819
Cetin NS, Özmen N (2002) Use of organosolv lignin in phenol–formaldehyde resins for particleboard production: I. Organosolv lignin modified resins. Int J Adhesion Adhesives. 22(6):477–480. https://doi.org/10.1016/S0143-7496(02)00058-1
Danielson B, Simonson R (1998) Kraft lignin in phenol formaldehyde resin. Part 1. Partial replacement of phenol by kraft lignin in phenol formaldehyde adhesives for plywood. J Adhesion Sci Technol 12(9):923–939. https://doi.org/10.1163/156856198X00542
Ghorbani M, Liebner F, van Herwijnen HW, Pfungen L, Krahofer M, Budjav E, Konnerth J (2016) Lignin phenol formaldehyde resoles: the impact of lignin type on adhesive properties. BioResources 11(3):6727–6741. https://doi.org/10.15376/biores.11.3.6727-6741
Gosselink RJA, Snijder MHB, Kranenbarg A, Keijsers ERP, De Jong E, Stigsson LL (2004) Characterisation and application of NovaFiber lignin. Ind Crops Prod 20(2):191–203. https://doi.org/10.1016/j.indcrop.2004.04.021
Jin Y, Cheng X, Zheng Z (2010) Preparation and characterization of phenol–formaldehyde adhesives modified with enzymatic hydrolysis lignin. Biores Technol 101(6):2046–2048. https://doi.org/10.1016/j.biortech.2009.09.085
Wang M, Leitch M, Xu CC (2009) Synthesis of phenol–formaldehyde resol resins using organosolv pine lignins. Eur Polymer J 45(12):3380–3388. https://doi.org/10.1016/j.eurpolymj.2009.10.003
Yang W, Jiao L, Wang X, Wu W, Lian H, Dai H (2021) Formaldehyde-free self-polymerization of lignin-derived monomers for synthesis of renewable phenolic resin. Int J Biol Macromol 166:1312–1319. https://doi.org/10.1016/j.ijbiomac.2020.11.012
Mahanwar PA, Kale DD (1996) Effect of cashew nut shell liquid (CNSL) on properties of phenolic resins. J Appl Polym Sci 61(12):2107–2111. https://doi.org/10.1002/(SICI)1097-4628
Mutlu I, Alma MH, Basturk MA, Oner C (2005) Preparation and characterization of brake linings from modified tannin-phenol formaldehyde resin and asbestos-free fillers. J Mater Sci 40(11):3003–3005. https://doi.org/10.1007/s10853-005-2396-7
Papadopoulou E, Chrissafis K (2011) Thermal study of phenol–formaldehyde resin modified with cashew nut shell liquid. Thermochim Acta 512(1–2):105–109. https://doi.org/10.1016/j.tca.2010.09.008
Sanjeevi S, Shanmugam V, Kumar S, Ganesan V, Sas G, Johnson DJ, Das O (2021) Effects of water absorption on the mechanical properties of hybrid natural fibre/phenol formaldehyde composites. Sci Rep 11(1):1–11. https://doi.org/10.1038/s41598-021-92457-9
Özbay G, Kokten ES, Ozcifci A (2021) Synthesis and characterization of resol type phenol-formaldehyde resin improved by SiO2-np. Wood Res 66(1):161–170. https://doi.org/10.37763/wr.1336-4561/66.1.161170
Chen Y, Gong X, Yang G, Li Q, Zhou N (2019) Preparation and characterization of a nanolignin phenol formaldehyde resin by replacing phenol partially with lignin nanoparticles. RSC Adv 9(50):29255–29262. https://doi.org/10.1039/C9RA04827H
Mao A, Xu W, Xi E, Li Q, Wan H (2018) Evaluation of phenol-formaldehyde resins modified and blended with pyrolysis bio-oil for plywood. For Prod J 68(2):113–119. https://doi.org/10.13073/FPJ-D-17-00066
Yu Y, Xu P, Chen C, Chang J, Li L (2018) Formaldehyde emission behavior of plywood with phenol-formaldehyde resin modified by bio-oil under radiant floor heating condition. Build Environ 144:565–572. https://doi.org/10.1016/j.buildenv.2018.08.025
Poljansek I, Krajnc M (2005) Characterization of phenol-formaldehyde prepolymer resins by in line FT-IR spectroscopy. Acta Chim Slov 52(3):238–244
Zhang W, Ma Y, Wang C, Li S, Zhang M, Chu F (2013) Preparation and properties of lignin–phenol–formaldehyde resins based on different biorefinery residues of agricultural biomass. Ind Crops Products 43:326–333. https://doi.org/10.1016/j.indcrop.2012.07.037
Cui Y, Hou X, Wang W, Chang J (2017) Synthesis and characterization of bio-oil phenol formaldehyde resin used to fabricate phenolic based materials. Materials 10(6):668. https://doi.org/10.3390/ma10060668
Li B, Wang Y, Mahmood N, Yuan Z, Schmidt J, Xu CC (2017) Preparation of bio-based phenol formaldehyde foams using depolymerized hydrolysis lignin. Ind Crops Prod 97:409–416. https://doi.org/10.1016/j.indcrop.2016.12.063
Alma MH, Kelley SS (2000) Thermal stability of novolak-type thermosettings made by the condensation of bark and phenol. Polym Degrad Stab 68(3):413–418. https://doi.org/10.1016/S0141-3910(00)00029-X
Li C, Zhang J, Yi Z, Yang H, Zhao B, Zhang W, Li J (2016) Preparation and characterization of a novel environmentally friendly phenol–formaldehyde adhesive modified with tannin and urea. Int J Adhes Adhes 66:26–32. https://doi.org/10.1016/j.ijadhadh.2015.12.004
Lee WJ, Chang KC, Tseng IM (2012) Properties of phenol-formaldehyde resins prepared from phenol-liquefied lignin. J Appl Polym Sci 124(6):4782–4788
Yun J, Chen L, Zhang X, Zhao H, Wen Z, Zhu D (2018) Synthesis and structure evolution of phenolic resin/silicone hybrid composites with improved thermal stability. J Mater Sci 53(20):14185–14203. https://doi.org/10.1007/s10853-018-2384-3
Acknowledgements
The authors would like to thank the central laboratory staff of Aksaray University.
Funding
This research received no external funding.
Author information
Authors and Affiliations
Contributions
GÖ: original draft preparation, writing–reviewing & editing. NA: original draft preparation, writing—reviewing & editing. MSA, reviewing & editing. All authors read and approved the final manuscript.
Corresponding author
Ethics declarations
Consent for publication
All the authors read and approved this paper.
Competing interests
The authors declare no competing interests.
Additional information
Publisher's Note
Springer Nature remains neutral with regard to jurisdictional claims in published maps and institutional affiliations.
Supplementary Information
Additional file 1.
Materials and methods description.
Rights and permissions
Open Access This article is licensed under a Creative Commons Attribution 4.0 International License, which permits use, sharing, adaptation, distribution and reproduction in any medium or format, as long as you give appropriate credit to the original author(s) and the source, provide a link to the Creative Commons licence, and indicate if changes were made. The images or other third party material in this article are included in the article's Creative Commons licence, unless indicated otherwise in a credit line to the material. If material is not included in the article's Creative Commons licence and your intended use is not permitted by statutory regulation or exceeds the permitted use, you will need to obtain permission directly from the copyright holder. To view a copy of this licence, visit http://creativecommons.org/licenses/by/4.0/.
About this article
Cite this article
Özbay, G., Ayrilmis, N. & Ahmad, M.S. Synthesis and characterization of green phenolic resin with olive oil mill wastewater. Environ Sci Eur 35, 10 (2023). https://doi.org/10.1186/s12302-023-00719-2
Received:
Accepted:
Published:
DOI: https://doi.org/10.1186/s12302-023-00719-2