Abstract
The use of mechanochemical activation of the powder at the stage of mixing the components and consolidation by spark plasma sintering made it possible to synthesize material based on silicon carbide, which has a weight loss of less than 0.04% when tested for heat resistance at 1500°C for 100 h. A ceramic material was produced at a consolidation temperature of 1800°C, its hardness was 32 GPa and a critical stress intensity factor was 6 MPa m1/2.
Similar content being viewed by others
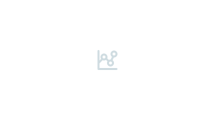
Avoid common mistakes on your manuscript.
High-temperature ceramics based on carbides and borides are promising for use in a new generation of aircraft [1–4], since the requirements for materials utilized in modern aircraft are constantly growing. The operability of currently used heat-resistant nickel alloys is limited by the operating temperature in the range of 1100–1150°С, while alloying the system with rare-earth and expensive elements, such as rhenium, ruthenium, etc., does not contribute to a significant increase in their operating temperatures, therewith increasing cost of parts [5]. In addition, the cooling of the blades of the turbine rotor, nozzle apparatus, and the flame tube of the combustion chamber leads to a significant consumption of air, which significantly reduces the completeness of fuel combustion directly in the combustion chamber of a gas turbine engine and, therefore, impairs the thrust and efficiency of the engine.
In turn, ceramic materials and composites based on them have no alternative under conditions of prolonged (from hundreds to several thousand hours) exposure to temperatures in an oxidizing medium above 1200°C, and have excellent corrosion and erosion properties [6–9]. Investigations on the integration of ceramic composite materials for the manufacture of rotor and nozzle blades of a gas turbine engine on their basis are conducted by several foreign companies (General Electric, Snecma). One of such ceramic materials is silicon carbide, which has successfully proved itself when tested under thermodynamic loads at specially designed stands simulating the operating conditions of aircraft engines [10, 11].
The most promising materials as parts for new generation aircraft are systems based on HfB2 and ZrB2, which have high heat resistance at temperatures above 1600°C [12]. However, a high degree of oxidation at temperatures above 1000°C forces these borides to be doped with silicon-containing compounds to increase the oxidative stability of the material. Silicon carbide is relevant in the temperature range of 1400–1500°С, at which a substantial part of the heat-loaded units and elements of aircraft, such as, for example, the stator parts of a high-pressure turbine, operate. A unique combination of physicomechanical characteristics of silicon carbide [13, 14] makes it possible to create ceramic materials based on it with high values of heat resistance, wear resistance, thermal conductivity, high temperature strength, radiation resistance, etc.
One of the methods for producing high-density materials based on silicon carbide is alloying it with boron, carbon, or a combination thereof [15]. The introduction of boron into silicon carbide can lead to compaction due to the formation of solid solutions of boron in silicon carbide, which, segregating on the surface of the particles, reduce the surface energy and the activation energy of the atomic diffusion process.
To introduce boron additives into silicon carbide, the method of mechanical activation is of interest, which allows the “deformational mixing” of the mixture components, that is, the mixing of the starting components at the atomic level. Mixing occurs when diffusion processes are inhibited, which allows stabilization of various metastable phases arising from mechanical stresses that manifest themselves during subsequent heat treatment [16].
For the consolidation of powder mixtures of silicon carbide and boron, it is of interest to use the method of spark plasma sintering (IPS), a high-speed technology for the formation of powders in which energy is released not only over the entire volume of the powder billet on a macroscopic scale, but also the energy is dissipated in certain areas under microscopic scale, namely, at the points of contact of the powder particles [17, 18].
The main purposes of this work was to create a technology for producing high-density ceramics based on silicon carbide without the use of additives that form the liquid phase during firing, to determine the mechanism of action of boron and carbon additives and the optimal amount of these additives.
EXPERIMENTAL
The following components were used as initial: Industrial powder α-SiC (F-1000 grade, Volzhsky abrasive plant, its parameters are listed in Tables 1, 2), crushed to a submicron size [50% of the powder has a diameter (d50) of not more than 0.22 μm], amorphous boron (MRTU 6-02-292-64), zirconium diboride manufactured by Plazmotherm. Grinding and subsequent mechanical activation were carried out at a planetary mill (PM-400, Retsch, Germany) in drums (volume 250 mL) with grinding bodies made of tungsten carbide (WC) (d = 10 mm), the grinding time was 3 h. Analysis of the material dispersion was performed on a laser particle size analyzer Analyte 22 Micro Tec/XT (Fritsch Co.). The concentration of boron introduced was 3, 6, 8, 10, and 15 wt %. A mixture of silicon carbide with a zirconium diboride content of 45, 50, and 55 wt % was used as the reference material.
Mechanical activation was carried out on a PM-400 planetary mill in drums (volume 250 mL) with grinding media from a WC (d = 10 mm), the ratio of material to grinding media was 1 : 10. The mixture was then sieved twice through a 002 sieve.
The chemical composition analysis was performed on an energy dispersive X-ray fluorescence spectrometer according to the HCAM 439-PC method (Shimadzu EDX-8000, Japan). To determine the phase composition, a D2 Phaser X-ray diffractometer (Bruker, Germany) was used. The prepared powders after mechanical activation were studied by infrared spectroscopy (IR-Fourier spectrometer, Thermo Fisher Scientific Inc., USA).
For the consolidation of powder mixtures based on silicon carbide, the FCT hybrid spark plasma sintering unit was applied. The powders obtained after mechanical activation were placed in a graphite mold. To exclude the contact of the powder with the mold and safe taking out the finished samples, the inner surface was glued with graphite foil. After installing the mold in the working chamber of the SPS-sintering unit, prepressing occurred at a pressure of 15 kN and the chamber was filled with argon to a gas pressure of 20 mbar. Sintering of the samples was carried out in the range of consolidation temperatures of 300–1750°С. The exposure time at maximum temperature was 25 min. Mixtures based on the SiC-ZrB2 system were consolidated in the temperature range of 1700–1850°С with a keeping time of 20 min.
The density of the consolidated samples was determined by hydrostatic weighing on an electronic scale GR-200 (AND, Japan). Vickers hardness of the samples was measured on an HV-1000 microhardness tester (TIME Group, China) at a load of 1 kg. The critical stress intensity factor (crack resistance) was determined by the Niihara method [19]. When indented by the Vickers pyramid, the crack resistance (K1c) of the material is determined by the formula
where Φ is a constant value (Φ ≈ 3); Hν is microhardness (Vickers hardness) (GPa); E is the elastic modulus (GPa); l is the average length of radial cracks that occur near the indenter imprint (Vickers pyramid) and measured from the imprint angle (μm); a is the half-diagonal length of the Vickers pyramid imprint (μm).
The elastic modulus was calculated based on the volume content of the initial components.
The experimental samples of the ceramic composite material were tested for heat resistance in an atmosphere of “calm air” at a temperature of T = 1500°C in a Nabertherm HT 16/18 high-temperature chamber furnace.
Grain size and other structural parameters were determined using a JSM-6490LV scanning electron microscope (Jeol, Japan).
RESULTS AND DISCUSSION
To study the effect of various modifying additives on the sintering process and the properties of silicon carbide-based ceramics, five compositions of the SiC–B system and three compositions of the SiC–ZrB2 system were selected. The mixtures were prepared in a PM400 planetary mill, and then consolidated under the above conditions in a spark plasma sintering setup. After mixing and sintering processes, the density of the samples was determined (Table 3).
The introduction of boron additives in silicon carbide leads to an intensification of sintering due to the formation of solid solutions of boron in silicon carbide and an increase in diffusion (both bulk and surface) in the material. The consolidation in the spark plasma of samples with a 3% addition of boron does not allow obtaining a material with a density higher than 92% (Table 3). An increase in boron additive to 6 wt % leads to a slight increase in density (2.92 g cm–3). This may be due to the fact that the resulting solid solution is not enough to intensify the sintering process under the given operational conditions. A noticeable increase in density values occurs when, by mechanochemical activation, 8 wt % boron is introduced into silicon carbide. In this case, it is possible to achieve a density of 3.04 g cm–3. Such a jump in the density value can be explained by the fact that a solid solution phase is formed on the surface of silicon carbide grains and in the bulk of the material, which is necessary for the main stages of the solid phase sintering process to proceed. A further increase in boron addition leads to a decrease in the rate of the density rising, which is associated with the capture of pores during intensive crystal growth. Closed intracrystalline pores are formed in the sintered material, the further removal of which is difficult due to the low coefficient of self-diffusion of the material (Fig. 1).
In the case of consolidation of the SiC–ZrB2 system, the maximum density value was reached at a ZrB2 concentration of 50 wt % (99.15% of theoretical) due to the formation of a hard-sintered skeleton of a composite material with intracrystalline porosity.
The experimental samples of the SiC–B system are characterized by a granular structure; inclusions in the form of pores are distributed over the entire volume. An increase in boron concentration leads to the removal of pores in the material; this becomes especially noticeable with introducing 8 wt % additives (Fig. 1). An increase in boron content up to 15 wt % leads to the fact that unreacted boron remains in the system (black inclusions in Fig. 1e), which makes it difficult to sinter the material to a high density.
The microstructure of sample S50Z (Fig. 1f) is fine-grained with an average particle diameter of 2–5 μm (comparable with the particle size of the initial powders), which indicates the suppression of particle growth during sintering in the case of a composite (heterophasic) structure of the material. The sample has a continuous silicon carbide matrix dispersively hardened by ZrB2 particles.
After determining the density, a heat resistance test of the samples was carried out (Table 2) at a temperature of 1500°C for 100 h (Table 4).
Samples of the silicon carbide–boron composition are superior in heat resistance to samples based on the SiC–ZrB2 system (Table 3). A large increase in the mass of samples with zirconium diboride is associated with the formation of viscous borosilicate glasses of complex variable composition, which play the role of a protective layer.
The introduction of boron into silicon carbide has a positive role in heat resistance tests (Fig. 2). An increase in the content of the additive from 3 to 8 wt % leads to a decrease in heat resistance by more than 12 times. This is most likely due to the uniform distribution of the additive over the matrix volume. Boron, segregating on the surface of silicon carbide, forms a dense crystalline layer and prevents the penetration of oxygen to intracrystalline pores. An increase in boron concentration of more than 8 wt % impairs the heat resistance of the ceramic material due to the appearance of residual unreacted boron, which, in turn, is easily oxidized and forms boron oxide on the surface of the particles. Thus, a boron concentration of 8 wt % is necessary and sufficient to achieve a minimum mass gain during the heat resistance tests.
To determine the role of carbon in the consolidation and change in the properties of ceramics based on silicon carbide, two additional experimental samples with a carbon content of 0.5 and 1 wt % were prepared. The concentration of boron was 8 wt %. After consolidation at a temperature of 300 to 1750°С with a holding time of 25 min and density measurements, the samples were also tested for heat resistance at 1500°С for 100 h (Table 5).
The tests on heat resistance of samples with additionally introduced carbon (Table 5) allow to conclude that the introduction of carbon in an amount of 1 wt % leads to the presence of free unreacted carbon in the system. This contributes to the enhanced release of gaseous products of the interaction of carbon with silicon oxides and boron, which are formed with increasing temperature in an oxidizing atmosphere. When carbon is introduced in an amount of 0.5 wt % into the silicon carbide–boron system, solid solutions of boron in silicon carbide and boron carbides of variable composition are produced, while the samples are sintered to a high density (98.04%). During oxidation, protective films of silicon oxide and borosilicate glass of complex stoichiometric composition are formed on the surface, which prevent further oxidation of the material.
It was previously shown (Table 4) that the addition of carbon in a minimum amount (0.5 wt %) has a positive effect on the change in mass during heat resistance tests (0.04% after 100 h). However, an excess of introduced carbon leads to an increase in the formation of gaseous products of its interaction with boron and silicon oxides, which negatively affects the density of the material and, consequently, the physicomechanical characteristics of the ceramic sample.
In this work, we studied the effect of the amount of carbon and the sintering completeness of the silicon carbide–boron system on such physicomechanical characteristics as hardness and crack resistance (Table 6).
The introduction of carbon into the silicon carbide–boron system in an amount of 0.5 wt % leads to the formation of solid solutions of boron in silicon carbide, and solid solutions of boron and carbon of variable composition are additionally formed in the system.
The maximum density of 3.11 g cm–3 (98.04% of theoretical) was achieved with the addition of 8 wt % boron and 0.5 wt % carbon and does not change with a further variation in the amount of additives, indicating the formation of a densely sintered skeleton. Upon transition to a high-density state of the material, the values of hardness increase due to a rise in an amount of the bridges between the pores and an increase in the hardness of the material occurs, reaching 32.92 GPa. This is explained by the growth of silicon carbide crystals and a decrease in stress concentrators at the grain boundaries in the form of micropores. Reducing stress concentrators and segregation of solid solutions at grain boundaries facilitates recrystallization at the final stage of sintering. The growth of crystals can be indicated by a decrease in the critical stress intensity factor upon the introduction of carbon using samples S8B and S8B05C as examples. With the introduction of carbon, K1c values diminish due to a change in the fracture mechanism of the material from predominantly intercrystalline, i.e., when the crack energy is spent on passing along the grain boundaries, on which stresses are concentrated, to the transcrystalline type, in which the crack passes through silicon carbide grains. With this mechanism, the crack propagation path is reduced, and the material is destroyed with less impact.
CONCLUSIONS
The introduction of boron into silicon carbide in an amount of 8 wt % is necessary to reduce the mass gain during the tests for heat resistance and sufficient for the formation of solid solutions that promote sintering using the spark plasma sintering method. An increase in boron concentration of more than 8 wt % impairs the heat resistance due to the appearance of residual unreacted boron, which in turn is easily oxidized with the formation of boron oxide, resulting in a larger increase in the sample mass due to the formation of borosilicate glass.
The introduction of carbon in an amount of more than 0.5 wt % leads to the formation of gaseous products of the interaction of the matrix components, which negatively affects the density, heat resistance, hardness, and crack resistance.
The introduction of 0.5 wt % carbon together with 8 wt % boron entails the formation of solid solutions of boron in silicon carbide and boron and carbon of variable composition, while the sintering of the system occurs to a high density, which, together with the formed compounds with a strong covalent bond, increases hardness while maintaining high values of crack resistance in comparison with the silicon carbide–boron and silicon carbide–zirconium diboride systems.
The silicon carbide–boron–carbon system turned out to be more heat resistant when tested for heat resistance at a temperature of 1500°C for 100 h due to the absence of zirconium diboride strongly reacting with oxygen. In addition, SiC with the addition of 8 wt % boron and 0.5 wt % carbon has enhanced physicomechanical properties, in particular hardness, in comparison with samples of the SiC–ZrB2 system.
REFERENCES
Kablov, E.N., Zhestkov, B.E., Grashchenkov, D.V., Sorokin, O.Yu., Lebedeva, Yu.E., and Vaganova, M.L., Teplofizika Vysokikh Temperatur, 2017, vol. 55, no. 6, pp. 704–711. https://doi.org/10.7868/S0040364417060059
Kablov, E.N., Zashchita Bezopasnost’, 2014, no. 4, pp. 28–29.
Sorokin, O.Yu., Grashchenkov, D.V., Solntsev, S.St., and Evdokimov, S.A., Tr. VIAM: Elektron. Nauch.-Tekhn. Zh., 2014, vol. 8, no. 6, p. 8. https://doi.org/10.18577/2307-6046-2014-0-6-8-8
Sorokin, O.Yu., Solntsev, S.St., and Evdokimov, S.A., Aviats. Mater. Tekhnol., 2014, no. S6, pp. 11–16. https://doi.org/10.18577/2071-9140-2014-0-s6-11-16
Lebedeva, Y.E., Prokopchenko, G.M., Modin, S.Y., Belyachenkov, I.O., and Grashchenkov, D.V., Russ. J. Appl. Chem., 2018, vol. 91, no. 5, pp. 785–792. https://doi.org/10.1134/S1070427218050099
Kablov, E.N., Aviats. Mater. Tekhnol., 2015, vol. 1, no. 1, pp. 3–33. https://doi.org/10.18577/2071-9140-2015-0-1-3-33
Chainikova, A.S., Orlova, L.A., and Popovich, N.V., Aviats. Mater. Tekhnol., 2014, no. S6, pp. 52–58. https://doi.org/10.18577/2071-9140-2014-0-s6-52-58
Chainikova, A.S., Orlova, L.A., and Popovich, N.V., Aviats. Mater. Tekhnol., 2014, no. 3, pp. 45–54.
Sorokin, O.Yu., Grashchenkov, D.V., and Solntsev, S.St., Tr. VIAM: Elektron. Nauch.-Tekhn. Zh., 2014, vol. 1, no. 6, p. 8. https://doi.org/10.18577/2307-6046-2014-0-6-8-8
Krenkel, W. and Berndt, F., Mater. Sci. Eng. A, 2005, vol. 412, no. 1–2, pp. 177–181.
Van Roode, M., Price, J., Miriyala, N., and Leroux, D., J. Eng. Gas Turbines and Power, 2007, vol. 129, no. 1, pp. 21–30. https://doi.org/10.1115/GT2005-68229
Gasch, M., Ellerby, D., and Beckman, S., J. Mater. Sci., 2004, vol. 39, pp. 5925–5937. https://doi.org/10.1023/B:JMSC.0000041689.90456.af
Kablov, E.N., Grashchenkov, D.V., and Isaeva, N.V., Ros. Khim. Zh., 2010, vol. LIV, no. 1, pp. 20–24.
Kablov, E.N., Zhestkov, B.E., Grashchenkov, D.V., Sorokin, O.Yu., Lebedeva, Yu.E., and Vaganova , M.L., High Temperature, 2017, vol. 55, no. 6, pp. 857–863. https://doi.org/10.1134/S0018151X17060086
Malinge, A., Coupe, A., Le Petitcorps, Y., and Pailler, R., J. Eur. Ceram. Soc., 2012, vol. 32, pp. 4393–4400. https://doi.org/10.1016/j.jeurceramsoc.2012.06.008
Avvakumov, E.G. and Gusev, A.A., Mekhanicheskie metody aktivatsii v pererabotke prirodnogo i tekhnogennogo syr’ya (Mechanical Activation Methods in the Processing of Natural and Industrial Raw Materials), Novosibirsk: Akad. Izd. Geo, 2009.
Barick, P., Chakravarty, D. and Saha, B.P., Ceram. Int., 2016, vol. 42, pp. 3836–3848. https://doi.org/10.1016/j.ceramint.2015.11.048
Torresil’yas San Millan, R., Solis Pinargote, N.V., Okun'kova, A.A., and Peretyagin, P.Yu. Osnovy protsessa iskrovogo plazmennogo spekaniya nanoporoshkov (Fundamentals of the Process of Spark Plasma Sintering of Nanopowders), Moscow: Tekhnosfera, 2014.
Niihara, K.A., J. Mater. Sci. Lett., 1983, vol. 2, pp. 221–223. https://doi.org/10.1007/BF00725625
Author information
Authors and Affiliations
Corresponding author
Ethics declarations
The authors declare that there is no conflict of interest requiring disclosure in this article.
Rights and permissions
About this article
Cite this article
Modin, S.Y., Popova, N.A., Chainikova, A.S. et al. Study of the Effect of Boron and Carbon Modifying Additives on Heat Resistance of a Ceramic Material Based on Silicon Carbide. Russ J Appl Chem 93, 654–660 (2020). https://doi.org/10.1134/S1070427220050055
Received:
Revised:
Accepted:
Published:
Issue Date:
DOI: https://doi.org/10.1134/S1070427220050055