Abstract
The fracture surface, the phase composition and the state of the defect substructure of the titanium VT1-0 alloy subjected to preliminary irradiation by a high intensity pulsed electron beam and failed under fatigue loading conditions have been studied. A surface layer with a nanocrystalline multiphase structure is shown to form during fatigue tests of the samples preliminarily annealed in air. The surface layer structure of the samples after irradiation is found to differ substantially from the structure of the unirradiated samples: a 5-μm-thick surface layer, in which the grain volumes have a subgrain structure, forms.
Similar content being viewed by others
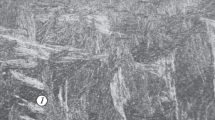
Avoid common mistakes on your manuscript.
1 INTRODUCTION
A characteristic feature of the fatigue failure of metals and alloys is the crack initiation in the surface layer [1, 2], which substantially influences the fatigue life of a material. The existence of high internal stresses, a great number of defects, significant elastic distortions of a crystal lattice near the grain boundaries lead to fast deformation localization during loading and, as a result, to the loss of plasticity of a material. To prevent undesirable changes in a surface layer, various methods of its modification are used: for example, treatment by a high-energy flux, namely, laser radiation [3, 4], electron beams [5, 6], and plasma treatment [7, 8]. These methods are characterized by pulsed and local character of action on a surface, which is their significant economic advantage as compared to stationary treatments.
The local treatment by high-energy fluxes enables the formation of new structure–phase states of surface layers with high properties. A substantial increase in the mechanical properties of a material is related to the removal of stress concentrators formed as a result of mechanical treatment, generation of compressing residual stresses in a surface layer, a dispersion of the matrix structure and minor-phase inclusions [9–16].
One of the promising methods of a purposeful modification of the structure–phase state of metallic materials is the action of an electron flux. This method differs in the possibility of controlling and varying the delivered energy, a large area of action of a high-energy flux on a treated material, low coefficients of energy reflection, and a higher energy concentration in the unit volume of a material, and, therefore, higher possibilities of forming a highly nonequilibrium state in a material to [17, 18]. The aim of this work, which continues the set of studies performed in [19, 20], is to study the fracture surface and to analyze the phase composition and the state of the defect substructure of the titanium VT1-0 alloy preliminarily subjected to high-temperature annealing in air and subsequent irradiation by high an intense pulsed electron beam and then was fractured during fatigue tests.
2 EXPERIMENTAL
We studied VT1-0 alloy samples with the following chemical composition (wt %): Ti for balance, up to 0.18 Fe, up to 0.07 C, up to 0.04 N, up to 0.1 Si, up to 0.12 O, up to 0.004 H, and 0.3% other impurities. The samples were subjected to annealing at a temperature of 1173 K for 90 min and furnace cooling.
The fatigue tests were performed by the scheme of asymmetric cantilevered bending using special-purpose installation. Samples 4 mm in thickness and 12 mm in width were prepared according to GOST 25.502–79 and had a symmetric stress concentrator in the form of semicircular notches 20 mm in radius on both sides of the sample with the minimum narrowing in the central part of 5 mm [19, 20]. The test temperature was 300 K, the bending loading frequency of the samples was 10 Hz, the stress ratio was 0.1, and the maximal cycle stress was 20 MPa. We tested 10 samples subjected to electron-beam irradiation and 10 unirradiated samples.
The sample surfaces were irradiated on a Solo installation (Institute of High Current Electronics, Siberian Branch, Russian Academy of Sciences) at the following parameters: the electron energy was 16 keV, the pulse repetition frequency was 0.3 s–1, the electron beam pulse duration was 150 μs, the electron beam energy density was 30 J/cm2, and the number of pulses was 3.
The fracture surfaces were studied with a scanning electron microscope (Tesla BS-301 microscope). The phase composition and the defect substructure state of the material were analyzed by transmission electron diffraction microscopy (JEM-2100 microscope). Foils for the studies were prepared by ion thinning of plates by electric-spark cut from a bulk sample in parallel to the fracture surface at the distance as close as possible to it. The analyzed layer thickness was ≈110 μm.
3 RESULTS AND DISCUSSION
The VT1-0 alloy samples subjected to high-temperature annealing were fractured in the unirradiated state after 267 ± 28 thousands of fatigue loading cycles. Figure 1 shows the characteristic image of the fracture surfaces of these samples. The fracture has a thin (≈2 μm) surface layer (Fig. 1b) separated on the main material by longitudinal fatigue cracks (Fig. 1c). The structure of this alloy revealed by transmission electron diffraction microscopy is shown in Fig. 2. The layer has a submicro- and nanocrystalline structure with a crystallite sizes of 80–120 nm (Fig. 2b). The minor phase inclusions, whose sizes are 12–15 nm, are located on crystallite boundaries. An analysis of the electron microscope images obtained from this layer revealed the existence of reflections of titanium oxides Ti2O and TiO2 (rutile) (Fig. 2d).
The layer adjacent to the nanostructured surface layer is α-titanium and it has a lamellar structure (Fig. 3a). The electron microscopy image obtained from this layer demonstrates an azimuth reflection diffusion, which indicates the formation of a disoriented substructure. The lamellar substructure layer thickness is ≈20 μm. At a larger distance from the sample surface, there is only a dislocation substructure in α-titanium grain bulks; the characteristic image of the substructure is given in Fig. 3b.
The irradiation by a high intense pulsed submillsecond electron beam led to an increase of the fatigue life of the alloy to 319 ± 30 thousands of loading cycles; i.e., the fatigue resource increased by 20%. Fig. 4 shows the characteristic image of the fracture of the alloy sample treated by the high intense pulsed electron beam. The fracture has a multilayer structure and consists of the surface layer (Fig. 4c, layer 1) 20–25 μm thick, the intermediate 50–55-μm-thick layer (layer 2), and the main material volume (layer 3). The surface layer has a sublayer adjacent to the irradiation surface that is characterized by the existence of micropores (layer 1–1).
The numerical solution of the problem of determining the temperature field formed in the surface layer of titanium irradiated by the high intense electron beam [19] enabled us to elucidate the cause of the formation of the fracture layered structure. The electron-beam irradiation of the alloy leads to melting of a surface layer 25.2 μm in thickness. This layer is separated into two sublayers: surface single-phase (liquid) layer 1 (16.6 μm thick) and transition two-phase (liquid + solid state) layer 2 with a thickness of 8.6 μm. The time of existence of layer 1 is 128.5 μs, and the time from the start of melting to the completion of solidification is 244.2 μs. Comparing the results shown in Fig. 4 and the results of the theoretical simulation [19], we can conclude that surface layer 1 formed as a result of melting and rapid solidification of the material and layer 2 is a heat-affected layer.
We also performed electron-microscopy studies for the failed samples in the initial (unirradiated) state along with the studies of the irradiated samples. Figure 5 shows the characteristic image of the defect substructure of the surface layer (the layer is disposed at a depth of 2–5 μm) of such samples. A polycrystalline α-titanium-based structure is observed; in the grain volume, we observed a dislocation substructure formed by chaotically distributed dislocations (Fig. 5a) or by the dislocations that form irregular networks (Fig. 5b). The scalar dislocation density determined by the linear intercept method is ≈2.8 × 1010 cm–2. Almost similar dislocation substructure is observed in the grain bulks of the layer disposed at the distance 150–200 μm from the sample surface.
The surface layer structure of the alloy irradiated by intense pulsed electric beam and fractured as a result of the fatigue tests is substantially different then the structure observed in the unirradiated alloy. In particular, as for morphology, we revealed a thin (≈5 μm) surface layer, the grain volumes in which have a subgrain structure the characteristic image of which is shown in Fig. 6a. The subgrains have a globular shape and the sizes 500–700 nm. At a larger distance from the irradiated surface, in the layer 20–25 μm in thickness, the lamellar substructure is observed in the grain bulks; the characteristic images of this substructure is shown in Figs. 6c, 6d.
The state of lamellar structure is substantially dependent on the distance from the surface irradiated by electron beam. Specifically, the transition from the mixed subgrain–lamellar structure (Fig. 6c) to the properly lamellar structure (Fig. 6d) takes place. Figure 6b shows the characteristic dislocation substructure observed in the bulks of subgrains and lamellas.
The surface layer with a lamellar structure contacts with the layer, the grain bulk of which contains the dislocation substructure that consists of dislocations, dislocation balls, and dislocation networks; the scalar dislocation density is 1.2 × 1010 cm–2 (Fig. 7). It should be noted that similar structure is also observed in the grains of the fractured samples which were not irradiated by intense electron beams previously.
Comparing the results of thermal calculations and the data obtained by the diffraction electron microscopy, we can conclude that the surface layer with the lamellar structure forms as a result of the titanium rapid solidification that takes place at the electron-beam treatment.
4 CONCLUSIONS
The studies performed using scanning and transmission electron diffraction microscopy showed that the VT1-0 alloy subjected to heat treatment in air and failed as a result of fatigue tests has a gradient structure. We observed a thin (≈2 μm) surface layer with submicro- and nanocrystalline multiphase structures, which is separated from the main sample volume by microcracks. The material volume adjacent to the surface layer has a polycrystalline structure; a lamellar structure is observed in the grain volume. The thickness of the layer with a lamellar structure is 20–25 μm. At a larger distance from the sample surface, the main element of the defect substructure in the α-titanium grain volume is represented by chaotically arranged dislocations. Irradiation by a high-energy electron beam leads to the formation of a 30-μm-thick surface layer with a lamellar substructure. The formation of the lamellar substructure as a result of rapid solidification of the surface layer favors an increase in the fatigue life of the VT1–0 alloy by ≈20% on the average.
REFERENCES
S. Kotsan’da, Fatigue Failure of Metals (Metallurgiya, Moscow, 1976).
J. Fellous, Fractography and Atlas of Fractographs (Metallurgiya, Moscow, 1982).
V. Oliveira, S. P. Sharma, M. F. S. F. de Moura, R. D. F. Moreira, and R. Vilar, “Surface treatment of CFRP composites using femtosecond laser radiation,” Optics and Lasers in Eng. 94, 37–43 (2017).
J. I. Ahuir-Torres, M. A. Arenas, W. Perrie, and J. de Damborenea, “Influence of laser parameters in surfacetexturing of Ti6Al4V and AA2024-T3 alloy,” Optics and Lasers in Eng. 103, 100–109 (2018).
D. Wei, X. Wang, R. Wang, and H. Cui, “Surface modification of 5CrMnMo steel with continuous scanning electron beam process,” Vacuum 149, 118–123 (2018).
X. Tao, Zh. Yao, Sh. Zhang, J. Liao, and J. Liang, “Investigation on microstructure, mechanical and tribological properties of in-situ (TiB + TiC)/Ti composite during the electron beam surface melting,” Surf. Coat. Techn. 337, 418–425 (2018).
M.–S. Jang, S. W. Ma, J. Song, M. Sung, and Y. Kim, “Adhesion of NCF to oxidized Si wafers after oxygen plasma treatment,” Microelectronics Reliability 78, 220–226 (2017).
O. F. Farag, “Comparison of the effect of plasma treatment and gamma ray irradiation on PS-Cu nanocomposite film surface,” Results in Physics 9, 91–99 (2018).
E. A. Erubaev, Yu. R. Kolobov, I. N. Kuz’menko, G. V. Khramov, M. B. Ivanov, and S. S. Manokhin, “Influence of nicroarc oxidation on the fatigue of the VT6 titanium alloy,” Fundanent. Issled., No. 12, 2575–2579 (2014).
V. N. Uskov, G. A. Danilin, G. A. Vorob’eva, A. V. Titov, E. Yu. Remshev, and Yu. S. Kukunya, “Influence of ATAT on the properties of deformed titanium alloys,” Metalloobrab., No 1 (73), 50–54 (2013).
V. L. Vorob’ev, P. V. Bykov, S. G. Bystrov, A. A. Kolotov, V. Ya. Bayankin, V. F. Kobziev, and T. M. Makhneva, “The change in the composition of surface layers of the titanium VT6 alloy after ion-arc mixing of aluminum and heat treatment,” Khim. Fiz. Mezoskop., No. 15 (4), 576–581 (2013).
S. V. Panin, I. V. Vlasov, V. P. Sergeev, V. V. Ovechkin, P. O. Marushchak, S. Ramasubbu, P. S. Lyubutin, and V. V. Titkov, “Fatigue life enhancement by irradiation of 12Cr1MoV steel with a Zr + ion beam. Mesoscale deformation and fracture,” Phys. Mesomech. 18 (3), 261–272 (2015).
K. N. Ramazanov, R. K. Vafin, and Yu. G. Khusainov, “Ion nitriding of tool steel KH12 in glow charge in cross electric and magnetic fields, “ Met. Sci. and Heat Treat. 6 (1, 2), 50–52 (2014).
S. V. Panin, P. O. Marushchak, I. V. Vlasov, V. P. Sergeev, B. B. Ovechkin, and V. V. Neifeld, “Impact toughness of 12 Cr1MoV steel. Part 2. Influence of high intensity ion beam irradiation on energy and deformation parameters and mechanisms of fracture,” Theor. Applied Fract. Mech. 83, 82–92 (2016).
O. V. Bashkov, Y. P. Sharkeev, S. V. Panin, V. A. Kim, T. I. Bashkova, A. A. Popkova, A. Y. Eroshenko, and A. I. Tolmachev, “Fatigue failure stages of VT1-0 titanium in different structural states. Study by acoustic emission method,” AIP Conf. Proc. 1783, 302–308 (2016).
I. Y. Timoshkin, K. V. Nikitin, V. I. Nikitin, and V. B. Deev, “Influence of treatment of melts by electromagnetic acoustic fields on the structure and properties of alloys of the Al–Si system,” Russ. J. Non-Ferous Metals 57 (4), 419–423 (2016).
J. An, X. X. Shen, Y. Lu, Y. B. Liu, R. G. Li, C. M. Chen, and M. J. Zhang, “Influence of high current pulsed electron beam treatment on the tribological properties of Al–Si–Pb alloy,” Surf. Coat. Technol. 200 (18, 19), 5590–5597 (2006).
Yu. F. Ivanov, K. V. Alsaraeva, V. E. Gromov, S. V. Konovalov, and O. A. Semina, “Evolution of Al–19.4Si alloy surface structure after electron beam treatment and high cycle fatigue,” Mater. Sci Technol. 31, 1523–1529 (2015).
S. V. Konovalov, I. A. Komissarova, D. A. Kosinov, Yu. F. Ivanov, O. V. Ivanova, and V. E. Gromov, “Structure of titanium alloy, modified by electron beams and destroyed during fatigue,” Letters on Materials 7 (3), 266–271 (2017).
S. Konovalov, I. Komissarova, D. Kosinov, Yu. Ivanov, V. Gromov, and O. Semina, “Increase of fatigue life of titanium V1-0 titanium after electron beam treatment,” Key Eng. Mater. 704, 15–19 (2016).
Funding
This study was supported by the Russian Foundation for Basic Research (project no. 16-58-00075Bel_a) and state assignment no. 3.1283.2017/4.6.
Author information
Authors and Affiliations
Corresponding author
Additional information
Translated by Yu. Ryzhkov
Rights and permissions
About this article
Cite this article
Konovalov, S.V., Komissarova, I.A., Gleser, A.M. et al. Effect of Electron-Beam Treatment on the Structure of Commercial-Purity Titanium Subjected to Fatigue Failure. Russ. Metall. 2020, 401–407 (2020). https://doi.org/10.1134/S0036029520040138
Received:
Revised:
Accepted:
Published:
Issue Date:
DOI: https://doi.org/10.1134/S0036029520040138