Abstract
Innovative composite materials ensure specific mechanical/tribological/thermal characteristics that are greater than the traditional materials from engineering polymers. The innovating epoxy/surface-treated epoxy composite is prepared through an advanced injection mold technique, and its mechanical/tribological features such as hardness, fracture toughness, and wear resistance are enhanced by the additions of 0–6 wt% of nano-silicon carbide (SiC) particles in the size of 50 nm. Mechanical properties such as hardness, fracture toughness, and wear resistance of epoxy hybrid nanocomposites are studied, and the excellence of SiC presence in epoxy matrix. Different types of epoxy composite compositions, the epoxy/20 wt% surface-treated jute fiber/6 wt% SiC identified maximum hardness of 35 ± 1HV, better fracture toughness of 1.48 ± 0.01MPa m0.5, and reduced wear rate of 0.330 ± 0.01 mg/m on 20N load at 1 m/s sliding velocity. These values are greater than the epoxy matrix without fiber and filler material. Moreover, the hybrid epoxy/20 wt% surface-treated jute/6 wt% of SiC is recommended for sports equipment applications.
Similar content being viewed by others
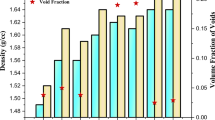
Explore related subjects
Discover the latest articles, news and stories from top researchers in related subjects.Avoid common mistakes on your manuscript.
Introduction
Particularly, the strength-to-weight ratio of poly-based composites increased in engineering sectors [1]. Different kinds of research on natural fiber-based bio-composites are extended due to their unique characteristics, including biodegradable, easy to recycle, and cost-effective [2]. According to application requirements, the poly composites are prepared with long and short fibers [3], which are synthesized by different techniques, reviewed and detailed in their processing and characteristics [4].
Amid the various techniques used in fabricating polymer composites, advanced injection molding suits complex shape production with economics [5]. The epoxy hybrid composite is synthesized with different jute and carbon fiber volume percentages for automotive interior parts applications. The epoxy composite with a higher volume of jute fiber facilitates superior mechanical properties such as tensile and flexural strength [6]. The hybrid polymer composite is developed for structural application, and its mechanical/structural behavior is studied. Its investigation revealed that the composite with higher natural fiber content has superior mechanical and structural characteristics [7]. Biodegradable hybrid polymer composite is prepared with various fiber position stacking. The impact of stacking position on basalt and ramie fiber on tensile and flexural strength of the composite is evaluated, and its evaluated result showed better improvement in mechanical behavior composite. It is greater than the conventional epoxy composite without fiber materials [8]. Sasikumar et al. [9] studied the tamarind fruit fiber incorporated epoxy-based polymer composite developed by advanced fabrication. The presence of natural fiber in the physical, mechanical, and thermal properties of prepared composites is studied through ASTM standards.
Natural fiber treated with NaOH solution offers better tensile, flexural, and impact strength and marginal improvement in hardness value related to traditional unreinforced polymer matrix [9]. In future, the development of bio-composites prepared with natural fiber is the trend for recent materials, which are eco-friendly, economical, and environmentally sustainable. For this reason, the natural fiber-blended bio-composite is attractive in automotive interior part applications [10]. Natural bast fiber incorporated HDPE composite behavior is enriched by the additions of silica nanoparticles, and better hardness and wear resistance values are recorded in unreinforced HDPE composite samples [11]. Moreover, synthetic fibers such as MWCNT and glass fiber developed epoxy composite offer better mechanical and tribological behavior. But, compared to natural fiber, it is costly [12]. The composite characteristics relate to processing and adhesive behavior [13]. The biodegradation of natural fiber processed with chemical treatment is exploited for better adhesive behavior, which results in improved physical, mechanical, and thermal characteristics. It is greater than the composite prepared without fiber or filler materials [14, 15]. Incorporating hard SiC particles in a polymer composite showed better hardness and wear resistance value [16].
The current investigation of epoxy composite developed with natural fiber-related past literature is studied, and their details are addressed in the above paragraph. The natural fiber-blended composites lacked hardness and wear resistance value. The main objectives of the current work are to synthesize the epoxy composite made with 20 wt% of surface-treated jute fiber via an advanced injection molding process and study its mechanical/wear behavior. Its specific hardness/wear resistance characteristics are featured using nano-SiC particles as 0–6 wt%. Its evaluated results showed that the epoxy hybrid nanocomposite containing 20 wt% of surface-treated jute fiber and SiC nanoparticle attained better hardness, fracture toughness, and wear resistance.
Materials and Methods
The current investigation of this paper selected epoxy resin as the matrix, jute natural fiber as the reinforcement, and nano-SiC as filler material. Epoxy is the most common resin with better chemical resistance, good strength, ease of fabricating, and cost-effective [17]. For this reason, it is selected as the matrix phase. The SiC particle offers better structural stability, improved hardness, and high thermal stability reasons [18]. It is considered a filler material for fabricating epoxy hybrid composites.
The natural jute fiber is extracted from a natural source and cleaned via water as required. Then, the fiber is dried at 100 °C with a processing time of 10min, which helps remove the moisture from the fiber. The chemical-based surface treatment approach enriches the cleaned jute fiber adhesive behavior and quality [19]. The 10% sodium hydroxide (NaOH) solution is used for jute fiber processing for 1 h. To eliminate the waste particles, the fibers are stirred manually every 10 min. After the NaOH surface treatment, it was subjected to drying at ambient temperature for 1 h and involved a drier-assisted drying process with an applied temperature of 200 °C. It supports limiting moisture content and cutting into 4–6 mm long fibers. It is used as 20 wt% for epoxy composite fabrication. As stated earlier, the 20 wt% of jute fiber facilitates better mechanical behavior than monopolymer [20].
With the suitability of high thermal stability, good hardness, and high rigidity modulus [21] reasons, the nano-SiC particle is selected as filler material as the weight percentages of 0, 2, 4, and 6 wt% are utilized to enrich the hardness and wear resistance of epoxy/surface-treated jute fiber composite. Table 1 indicates the constitutions of epoxy/jute fiber/SiC filler materials used in composite fabrication.
Epoxy Hybrid Nanocomposite Synthesis Details
Figure 1 depicts the advanced injection mold machine configured with temperature monitoring and a digital control system.
The epoxy resin is blended with hardener solution by the ratios 100:10 via a blending machine with 50–100 rpm speed; meantime, the NaOH surface-treated short jute fiber is added according to the weight percentages mentioned in Table 1. The epoxy resin mixture and surface-treated jute fiber are blended uniformly via a mechanical stirrer setup with an applied speed of 100 rpm for a processing duration of 10 min. It helps to enhance the fiber distribution that results in increased mechanical behavior of the composite [2]. During the stirrer process, the required quantity of nano-SiC is added to the epoxy/jute fiber mixture with a processing time of 10 min. The prepared epoxy resin mixture with surface-treated jute short fiber and nano-SiC is kept in an injection molding machine and heated by 200 °C to eliminate the microvoids and porosity inside the epoxy mixtures. With the support of the injector, the mixture is injected into a preheated tool steel die for the dimensions 150 mm × 150mm × 10 mm. Finally, the fabricated epoxy hybrid nanocomposites are cured by the die itself.
ASTM standards evaluate the fabricated epoxy hybrid nanocomposite characteristics. Instron tests the composite's microhardness and makes a U30 model Vickers hardness tester with a 100 g load maintained for 10s duration as per ASTM D4762 standard. Similarly, the fracture toughness and wear resistance are measured by ASTM D6110 and G99 standards. During the fracture toughness, the composite samples are notched for the Charpy impact test via the IT 30 model impact tester configured with a maximum energy absorption of 300 J. The Ducom pin-on-disk wear testing machine configured with a hardened steel counter disk is utilized for wear studies under 20N load, and 1m/sec sliding velocity at a constant sliding distance is followed. However, to find the statistical significance, the three test samples are tested with 5% test significance and the average value of three is considered as the mean value of the composite.
Results and Discussions
Hybrid Nanocomposite's Microhardness Behavior
Figure 2 bar chart indicates the microhardness of hybrid nanocomposite made by 0, 2, 4, and 6 wt% of SiC nanoparticle and 20 wt% of surface-treated jute fiber. The epoxy/20 wt% surface-treated jute fiber composite's microhardness is 19 ± 0.5HV, and 24 ± 1HV records this composite feature with 2 wt% of nano-SiC. The wide dispersion of nano-SiC particles causes improved hardness of the composite. Generally, the SiC particle has high hardness and is suitable for composite fabrication [16]. The microhardness of epoxy hybrid nanocomposite with 20wt% surface-treated jute fiber and 4wt% of nano-SiC is exposed to 29 ± 1HV. The uniform dispersion of natural fiber and SiC nanoparticles is the reason for increased hardness. Moreover, the contribution of ceramic particles in a soft polymer matrix causes a better hardness value than monopolymer [11]. The epoxy matrix/20 wt% of surface-treated jute fiber/6 wt% of nano-SiC hybrid nanocomposite showed 34 ± 1HV and 79% enhancement compared to the epoxy matrix with 20 wt% surface-treated jute fiber.
Hybrid Nanocomposite's Fracture Toughness Behavior
The fracture toughness of epoxy matrix composite with constant wt% of surface-treated jute fiber along with 0–6 wt% of nano-SiC hybrid nanocomposite is displayed in Fig. 3.
Epoxy/20 wt% of surface-treated jute fiber prepared composite's fracture toughness is 1.15 ± 0.01MPa m0.5, and this combination is prepared with 2 wt% of nano-SiC is recorded by 1.25 ± 0.02MPa m0.5. The chemical-treated natural fiber could absorb the energy and show better impact toughness [11]. The fracture toughness of epoxy/20 wt% surface-treated jute fiber/4wt% of nano-SiC is noted by the value of 1.37 ± 0.01MPa m0.5. It is higher than the other composite values of fracture toughness. The appearance of natural fiber withstanding the maximum force during fracture toughness evaluation. The multi-reinforcement combination gives a better bonding effect with the improved mechanical behavior of the composite [6]. However, the epoxy/20 wt% surface-treated jute fiber/6 wt% of nano-SiC hybrid nanocomposite is exploited by maximum fracture toughness and improved by 29% related to the fracture toughness of epoxy/20 wt% surface-treated jute fiber.
Hybrid Nanocomposite's Wear Rate
Figure 4 illustrates the wear rate of epoxy/20 wt% of surface-treated jute fiber with varied wt% of nano-SiC hybrid nanocomposite measured by 20 N load and 1 m/s sliding velocity. Epoxy/20 wt% of surface-treated jute fiber composite's wear rate is 0.403 ± 0.03 mg/m, and the inclusions of 2 wt% of nano-SiC are recorded to reduce the wear rate of 0.339 ± 0.02 mg/m. The coarse grain of SiC particles may limit the abrasive wear and withstand the maximum sliding force. The wear rate of 4wt% nano-SiC blended epoxy/20 wt% surface-treated jute fiber exhibited 0.335 ± 0.01 mg/m wear rate and is lower than the unreinforced epoxy/20 wt% of jute fiber composite. The presence of ceramic particles causes better absorption resistance value [11].
The lowest wear rate of 0.33 ± 0.01 mg/m is identified on 6 wt% nano-SiC blended by 20 wt% of surface-treated jute fiber in an epoxy matrix. Compared to epoxy/20 wt% of surface-treated jute fiber, it has reduced by 18%. The reduction in the wear rate of hybrid composite is due to the appearance and uniform dispersion of nano-SiC, making an efficient bond with jute fiber.
Conclusions
In the advanced injection molding technique, the epoxy hybrid nanocomposite is fabricated with constant weight percentages of surface-processed jute fiber, and 0–6 wt% of nano-SiC particle is made successfully. Its hardness, fracture toughness, and wear rate are investigated, and the main findings of its evaluated results are highlighted in the following key points.
-
Based on the evaluated results of the present study, the epoxy/20 wt% surface-treated jute fiber/6 wt% of nano-SiC hybrid nanocomposite’s hardness is provided with the maximum value, which is attained 79% relates to epoxy/20 wt% surface-treated jute fiber composite.
-
The fracture toughness value of the epoxy/20 wt% surface-treated jute fiber/6 wt% of nano-SiC hybrid nanocomposite is noted as higher than the other composite and obtained a 29% improvement of fracture toughness.
-
The wear rate of epoxy/20 wt% surface-treated jute fiber/6 wt% of nano-SiC hybrid nanocomposite showed an 18% reduction in wear rate compared to the epoxy/20 wt% surface-treated jute fiber composite.
-
This optimum hardness, fracture toughness and improved wear resistance is recommended for sports goods applications.
Data Availability
All the data required are available within the manuscript.
References
K. Dhanasekar et al., Influences of nanosilica particles on density, mechanical, and tribological properties of sisal/hemp hybrid nanocomposite. Adv. Polym. Technol. 1, 3684253 (2023)
R. Venkatesh et al., Evaluation of thermal adsorption and mechanical behaviour of intralaminar jute/sisal/e-glass fibre-bonded epoxy hybrid composite as an insulator. Adsorpt. Sci. Technol. (2023). https://doi.org/10.1155/2023/9222562
G. Liu et al., Additive manufacturing of continuous fiber reinforced polymer composites: design opportunities and novel applications. Composite Commun. 27, 100907 (2021)
P.P. Das et al., Emerging Trends in Green Polymer Based Composite Materials: Properties, Fabrication and Applications, in Graphene based biopolymer nanocomposites. (Springer, Singapore, 2020), pp.1–24
E. Jeong et al., Innovative injection molding process for the fabrication of woven fabric reinforced thermoplastic composites. Polymers 14(8), 1577 (2022)
M.Y. Khalid et al., Experimental and numerical characterization of tensile property of jute/carbon fabric reinforced epoxy hybrid composites. SN Appl. Sci. 2, 577 (2020)
D.K. Pokkalla et al., A novel additive manufacturing compression over molding process for hybrid metal polymer composite structures. Addit. Manuf. Lett. 5, 100128 (2023)
V. Ramesh et al., Influence of stacking sequence on mechanical properties of basalt/ramie biodegradable hybrid polymer composites. Polymers 15(4), 985 (2023)
R. Sasikumar et al., Effect of tamarind fruit fiber contribution in epoxy resin composites as biodegradable nature: characterization and property evaluation. Biomass Conv Bioref (2023). https://doi.org/10.1007/s13399-023-04465-6
S.K. Palaniappan et al., Eco-friendly Biocomposites: a step toward achieving sustainable development goals. Appl. Sci. Eng. Progr. 17(4), 7373 (2024)
W. Christraj, Performance analysis of solar water heater in multipurpose solar heating system. Appl. Mech. Mater. 592–594, 1706–1713 (2014)
P. Raja Sekaran, Adsorption and photocatalytic degradation properties of bimetallic Ag/MgO/biochar nanocomposites. Adsorpt. Sci. Technol. 2022, 3631584 (2022). https://doi.org/10.1155/2022/3631584
N. Karthi, Synthesis and adsorbent performance of modified biochar with Ag/MgO nanocomposites for heat storage application. Adsorpt. Sci. Technol. 2022, 7423102 (2022). https://doi.org/10.1155/2022/7423102
P.R. Sekaran, H. Ramakrishnan et al., Mechanical and physical characterization studies of nano ceramic reinforced Al–Mg hybrid nanocomposites. Silicon (2023). https://doi.org/10.1007/s12633-023-02473-9
W. Christraj, Experimental investigation of multipurpose solar heating system. J. Energy Eng. 141(3), 04014009 (2013)
R. Venkatesh et al., Investigation and performance study of hibiscus sabdariffa bast fiber-reinforced HDPE composite enhanced by silica nanoparticles derived from agricultural residues. Fibers Polymers 24(6), 2155–2164 (2023)
J. Venugopal et al., Effect on compression molding parameters in mechanical properties of MWCNT/glass fiber/epoxy composites. Adv. Polymer Technol. (2022). https://doi.org/10.1155/2022/9295407
H.B. Rachid et al., Effect of nanocomposites rate on the crack propagation in the adhesive of single lap joint subjected to tension. Mech. Adv. Mater. Struct. (2023). https://doi.org/10.1080/15376494.2023.2240319
L. Rajeshkumar et al., Assessment of biodegradation of lignocellulosic fiber-based composites—a systematic review. Int J Biol Macromol 253, 127237 (2023)
F. Jahan, M. Soni, Effects of chemical treatment on mechanical properties of various natural fiber reinforced composite: a review. Mater. Today Proceed. 46(15), 6708–6711 (2021)
R.S. Rana et al., Effect of SiC reinforcement on the mechanical properties of Kevlar fiber based hybid epoxy composites. Mater. Today Proceed. 44(1), 2478–2481 (2021)
Funding
The authors did not receive support from any organization for the submitted work.
Author information
Authors and Affiliations
Corresponding author
Ethics declarations
Conflict of interest
The authors declare that they have no conflict of interest.
Ethical Approval
This is an observational study. Surface-treated jute fiber-blended epoxy composite featured with SiC via injection molding process: Characteristics study: The Research Ethics Committee has confirmed that no ethical approval is required.
Additional information
Publisher's Note
Springer Nature remains neutral with regard to jurisdictional claims in published maps and institutional affiliations.
Rights and permissions
Springer Nature or its licensor (e.g. a society or other partner) holds exclusive rights to this article under a publishing agreement with the author(s) or other rightsholder(s); author self-archiving of the accepted manuscript version of this article is solely governed by the terms of such publishing agreement and applicable law.
About this article
Cite this article
Venkatesh, R. Surface-Treated Jute Fiber-Blended Epoxy Composite Featured with SiC via Injection Molding Process: Characteristics Study. J. Inst. Eng. India Ser. D (2024). https://doi.org/10.1007/s40033-024-00722-8
Received:
Accepted:
Published:
DOI: https://doi.org/10.1007/s40033-024-00722-8