The results of an experimental study of the mechanical properties of carbon fiber-reinforced plastics (CFRP) made by the “wet” winding method in the temperature range of room temperature to −196°C with different reinforcement schemes are presented. The temperature dependences of strength, plasticity and elasticity characteristics of these materials in tensile and three-point bending tests are obtained. The elastic modulus of CFRP with a longitudinal scheme of reinforcement in a given temperature range is at the level of 160 GPa. The ultimate stress of the material at room temperature is 1370 MPa. The temperature dependence of this characteristic is close to linear and practically coincides with that of bending. The low-temperature hardening, estimated by the change in the value of the ultimate stress due to cooling, reaches 39%. The mechanical characteristics of CFRP with a transverse reinforcement scheme both in tension and in bending in the considered temperature range have rather low values and are determined mainly by the matrix properties. When cooling from 20 to −196°C, the elastic modulus of CFRP with a ±45° reinforcement scheme increases by 55%, and its low-temperature hardening is 40%. At the same time, the elastic modulus and ultimate stress are six to eight and ten times, respectively, lower than the similar characteristics of CFRP with the longitudinal reinforcement scheme. Fracture of such a composite at all investigated temperatures occurs locally by shifting at an angle of 45° because of delamination of the material.
Similar content being viewed by others
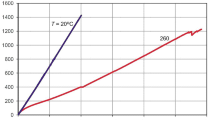
Avoid common mistakes on your manuscript.
Introduction. Composite materials reinforced with carbon fibers, harnesses, tapes, filamentary crystals are widely used in aerospace, cryogenic, transport technology, etc., due to high specific strength, stiffness, low coefficient of linear thermal expansion, the ability to manufacture one-piece large-sized parts with given mechanical properties in accordance with the type and character of the load acting on them [1, 2].
Some features of low-temperature deformation of CFRP are given in [3, 4] and other works. However, the level of mechanical characteristics of such composites depends on a range of technological and operational factors, which makes it necessary to study each specific structural material manufactured at the enterprise using the appropriate technology under conditions close to operational ones.
The aim of the work is to study the effect of temperature, textural form of reinforcing filler, and test method on the mechanical properties of CFRP used in the Yangel Yuzhnoye State Design Office.
Materials and Test Procedures. The object of research is the processes of deformation and fracture of CFRP made by “wet” winding of carbon fiber using a binder based on epoxy resin, hardener and accelerator according to unidirectional scheme or by laying of CFRP layers at an angle of ±45°.
The core of the test procedures was to obtain the stress–strain diagrams of two types of carbon fiber at tension and three-point bending in the temperature range from 20 to −196°C. The tests were performed via an Instron 1126 universal testing machine, taking into account current requirements for the reliability of standard mechanical characteristics of materials [5]. They complied with standards [6,7,8] for room conditions and those in a cryochamber, i.e., in a mixture of liquid nitrogen and ethyl alcohol (the given temperature was controlled by a thermocouple), and in liquid nitrogen [8] at temperatures of 20, −40, and −196°C, respectively.
Material’s specimens for tensile tests had the form of rectangular plates with different reinforcement directions in relation to the longitudinal axis of the specimen, namely longitudinal, transverse and ±45°-inclined directions. Nominal dimensions of specimens (mm) for tensile tests were 350 × 12 × 1 (for longitudinal and transverse reinforcement schemes) and 350 × 20 × 2 (for the reinforcement scheme at an angle of ±45°), which corresponded to type 3 according to GOST 11262-80 [6]. The aluminum alloy plates were attached to the gripping parts of the specimens. During the loading, the load–displacement diagrams were recorded, determining the following mechanical characteristics: ultimate stress σu, relative elongation at failure δ, the elastic modulus E [7]. In addition, the non-standard characteristic σc was defined as stress, which corresponded to the first load drop (jump), indicating the early stage of fracture of reinforcing fibersFootnote 1. The speed of displacement of the active capture of the machine was 1 mm/min.
The dimensions of the specimens (mm) for the three-point bending tests were as follows: 100 × 10 × 1 (longitudinal reinforcement scheme), 100 × 15 × 1 (transverse reinforcement scheme), and 100 × 20 × 2 (reinforcement scheme at an angle of ±45°). According to [8], the distance between the supports in the first two cases was 40 mm, in the third one was 80 mm. During the tests, the load–deflection diagrams were recorded, and the value of the ultimate stress at bending \( {\upsigma}_u^b \) was determined [8]. The displacement rate of the loading tip was 5 mm/min.
In all cases, three specimens were tested under identical conditions, and the results were averaged.
Results and Discussion. The character of deformation and the corresponding tensile diagrams of the specimens with different reinforcement scheme differ significantly. In CFRP with a transverse arrangement of fibers the stress σ – strain ε dependence is almost linear until the moment of failure, which occurs by mode I, whereas in the longitudinal one linear sections are interspersed with load drops (Fig. 1), corresponding to the fracture of both individual and group of fibers.
Material fracture during loading occurs gradually, that is, the rupture of fibers with delamination and cracking of the matrix. The final rupture occurs after the next local fracture accumulating a critical amount of damage. In this case, the matrix completely disintegrates, as well as part of the carbon fibers (Fig. 2).
Stress–strain relation of CFRP with the reinforcement scheme at an angle of ± 45o have an initial linear area. The diagrams show numerous shallow stress drops, which occur due to shifts and delamination (Fig. 3). After a deep drop or a few shallow ones, diagrams become nonlinear.
Fracture of specimens at all test temperatures occurs by shifting at an angle of 45° because of delamination of the material and begins, continues and ends in the same zone (Fig. 4).
Load–deflection diagrams for CFRP specimens with longitudinal and transverse schemes of fiber layout are linear and generally have no jumps. Deflection for specimens with the longitudinal scheme reaches 5 mm, while a transverse one is 2.7 mm. The character of fracture of the specimens in both reinforcement schemes is brittle. The fracture occurs at the elastic strain area; for specimens with the longitudinal arrangement of fibers during fracture, the sharp deep load drop is registered, but at a temperature of −196°C their fracture occurs with failure into two parts.
For specimens with the reinforcement scheme at an angle of ±45° the diagrams are quite extended, their deflection is higher than 25 mm. Only the lower tensile layers fracture due to delamination is observed (Fig. 5).
Temperature dependences of mechanical characteristics of CFRP with different reinforcement directions are shown in Figs. 6–9.
The elastic modulus value of the composite with longitudinal reinforcement slightly changes throughout the studied temperature range (Fig. 6), whereas the ultimate stress increases significantly (by 39%) when the material is cooled from 20 to −196°C.
The first-jump stress coincides with the fracture beginning. Low-temperature hardening, characterized by this indicator, is realized almost completely by cooling CFRP in the temperature range from 20 to −40°C.
The plasticity of CFRP as a brittle material is low; however, the value of its relative elongation during fracture increases with cooling to the temperature of liquid nitrogen (Fig. 9).
The elastic modulus of CFRP with the transverse reinforcement scheme is approximately 20 times smaller than CFRP with longitudinal one. At the same time, it increases linearly by 22% as it cools (Fig. 7).
The ultimate stress value of such a composite decreases sharply when cooling from 20 to −40°C. This is probably related to the appearance of microcracks because of thermal stresses. This is also the reason why the value of relative elongation of material during fracture decreases almost twice at cooling (Fig. 9).
As the test temperature decreases, the variation of the values of mechanical characteristics increases, except for the elastic modulus. Thus, for the ultimate stress when the test temperature decreases from 20 to −196°C, the variation coefficient increases in the range of 2–46%.
The elastic modulus of CFRP with the reinforcement scheme at an angle of ±45° is 5.5–8.3 times smaller than with the longitudinal reinforcement scheme (Fig. 8). The increase of stiffness of CFRP with the reinforcement scheme at an angle of ±45° with decreasing in temperature from 20 to −196°C reaches 55%. The strength characteristics σu and σc are 10 and 18 times, respectively, lower than CFRP with the longitudinal reinforcement scheme. The low-temperature hardening by σu characteristic is 40%. The stress σc, which characterizes the beginning of material fracture, is practically independent of temperature, but its values have the largest variation.
The value of the relative elongation at failure is small, and it decreases at cooling from 20 to −196°C (Fig. 9).
Comparison of the tensile and bending stress characteristics shows that for CFRP with longitudinal reinforcement they practically coincide in the entire temperature range. For the other two reinforcement schemes, the values σu and \( {\sigma}_u^b \) also differ several times in one direction or another. The presence of compressed layers during bending leads to the increase \( {\sigma}_u^b \) compared to σu for the material reinforced in the transverse direction. As for CFRP with the reinforcement scheme at an angle of ±45°, edge effects are important in determining its characteristics. It can be assumed that with increasing the width of the specimens of such material their strength will increase significantly.
Conclusions. Analysis of temperature dependences of mechanical characteristics of CFRP under different reinforcement schemes obtained by tensile and bending shows that in the whole investigated temperature range the highest values of the ultimate stress, elastic modulus, and low-temperature hardening has CFRP with longitudinal reinforcement, with a coincidence of its tensile and bending strength values, while for the other two reinforcement schemes, the values σu and \( {\sigma}_u^b \) differ several times in one direction or another. The values of mechanical characteristics of CFRP with the transverse reinforcement scheme are quite low, as they are determined mainly by the matrix properties, while they are much higher with the reinforcement scheme at the angle of ±45° in the considered temperature range but significantly smaller than in composite with longitudinal reinforcement.
References
A. V. Kondrat’ev and V. A. Kovalenko, “Review and analysis of world trends and problems of expanding the use of polymer composite materials in rocket and space technology,” in: Issues of Design and Manufacture of Flying Vehicles [in Russian], Issue 67, No. 3, KhAI, Kharkiv (2011), pp. 7–18.
E. Fitzer, Carbon Fibres and Their Composites, Springer-Verlag, Berlin–Heidelberg (1985).
V. A. Lototskaya, Yu. A. Pokhil, A. I. Telegon, and S. M. Dergun, “Strength and plasticity of metal and nonmetallic composites for cryogenic and aerospace purposes,” Strength Mater., 37, No. 5, 506–514 (2005), https://doi.org/10.1007/s11223-005-0061-7.
R. P. Reed and M. Golda, “Cryogenic properties of unidirectional composites,” Cryogenics, 34, No. 11, 909–928 (1994).
E. V. Vorob’ev, “On the accuracy in determination of the mechanical material characteristics at low temperatures,” Strength Mater., 50, No. 3, 487–492 (2018), https://doi.org/10.1007/s11223-018-9993-6.
GOST 11262-80. Plastics. Tensile Test Method [in Russian], Valid since December 1, 1980.
GOST 25601-80. Design Calculation and Strength Testings. Methods of Mechanical Testing of Polymeric Composite Materials. Test for Tensile Properties on Plane Specimens at Normal, Elevated, and Low Temperatures [in Russian], Valid since June 1, 1981.
GOST 25.604-82. Design Calculation and Strength Testings. Methods of Mechanical Testing of Polymeric Composite Materials. Test for Bending Properties at Normal, Elevated, and Low Temperatures [in Russian], Valid since January 1, 1984.
DSTU 7305:2013. Metals. Method for Tensile Test of Metals and Alloys at the Low and Cryogenic Temperatures [in Ukrainian], Valid since April 1, 2014.
V. A. Strizhalo, E. V. Vorob’ev, and L. S. Novogrudskii, “Effect of prior strain on serrated yielding of materials at 4.2 K,” Strength Mater., 27, No. 8, 434–440 (1995), https://doi.org/10.1007/BF02209338.
Author information
Authors and Affiliations
Corresponding author
Additional information
Translated from Problemy Prochnosti, No. 2, pp. 46 – 52, March – April, 2021.
Rights and permissions
About this article
Cite this article
Vorob’ov, E.V., Zemtsov, M.P., Novogruds’kyi, L.S. et al. Mechanical Properties of Carbon Fiber-Reinforced Plastics at Cryogenic Temperatures. Strength Mater 53, 241–246 (2021). https://doi.org/10.1007/s11223-021-00281-3
Received:
Published:
Issue Date:
DOI: https://doi.org/10.1007/s11223-021-00281-3