Abstract
This paper presents an experimental investigation on the properties of cement-coated brick aggregate concrete. Natural coarse aggregate (NA) in concrete was replaced with cement M0-coated aggregate (CCBA) for 25, 50, 75, and 100%. CCBA was tested for the physical and mechanical properties to compare with the NA. A total of 5 concrete mixes consists of one control mix M0 and four CCBA (M25–M100) concrete mixes were prepared and tested for the physical properties and mechanical strengths. The physical properties of concretes such as workability (fresh stage), hardened density, and water absorption were determined. The compressive strength of the concrete was tested at 7, 28, and 56 days. Meanwhile, splitting tensile strength was determined at 28 days only. The experimental results showed that workability of the concrete was reduced with the increasing of CCBA in concrete. Zero slump concrete was recorded for concrete containing 75 and 100% CCBA. The water absorption of the concrete was increased with the increasing amount of CCBA. There is no significant reduction of compressive strength for CCBA concrete. However, CCBA concretes gained lower splitting tensile strength compared to the normal concrete. More investigation has to be done to validate the potential usage of recycled CCBA as coarse aggregate replacement for concrete construction.
Access provided by Autonomous University of Puebla. Download conference paper PDF
Similar content being viewed by others
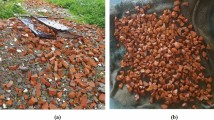
Keywords
1 Introduction
The rapid growth of construction sector leads to a high amount of consumption of construction minerals especially rock materials and sand which are the main source of construction material. The construction cost might be increased due to the shortage of these construction materials. Although the supply of natural aggregate was considered to be adequate for development in the next few years [1], but the high demand of aggregate may reduce the natural aggregate resources if no control measures are implemented [2]. To prevent the impact of shortage, a sustainable measure should be conducted. Coarse recycled brick aggregates recovered from the demolition of masonry structures can be used in the manufacture of new concrete mixtures. The utilization of masonry waste and crushed brick is an environmentally friendly measure which brings along the advantages to economy and environment. Brick aggregate as coarse aggregate in the manufacture of new concrete is adequate as brick aggregate is lightweight compare to natural aggregate. However, the compressive strength of the concrete with recycled clay brick aggregate is relatively lower compared to natural aggregate concrete [3, 4].
Brick aggregates show high porosity and low compressive strength [4,5,6]. Due to the high porosity of brick aggregates, hence, the water absorption of brick aggregate is relatively higher [4,5,6,7,8,9]. In order to reduce the water absorption of aggregates, application of cement coating on aggregate is necessary to reduce the porosity of the aggregates [10, 11]. Two-stage mixing approach was proposed which premix the recycled aggregate with proportional contents of required cement for 60 s before mixed with remaining ingredients of concrete for 120 s [12]. Two ways of cement coating were proposed which are single coat and double coat. Both of the coating techniques are the same which the cement paste with W/C ratio of 0.50 was prepared and mixed with the aggregates for 5 min [13].
Brick is known to be a high porous ceramic material which has high water absorption. Therefore, cement-coated brick aggregate is required to improve the performance of brick as a coarse aggregate in manufacture concrete. This study aimed to investigate the properties of concrete incorporating with cement-coated coarse aggregate.
2 Experimental Design
The physical and mechanical properties of cement-coated brick aggregate (CCBA) were investigated by conducting sieve analysis, water absorption, and aggregate impact value tests. In order to study the physical and mechanical properties of CCBA concrete, 45 concrete cubes (100 mm × 100 mm × 100 mm) and 14 concrete cylinders (150 mm diameter × 300 mm length) specimens were prepared. A total of 5 concrete mixes were prepared with different percentage of CCBA ranging from 0 to 100% used as the coarse aggregate in concrete.
2.1 Materials
The materials used in this study are ordinary Portland cement (OPC), natural fine and coarse aggregates, CCBA, and tap water. Clay bricks were broken manually using hammer before crushed to the smaller size using mechanical crusher into brick aggregates. The brick aggregates used were sieved passing through 20 mm sieve and retained in 5 mm sieve. The cement pastes with the water/cement ratio of 0.5 were used to treat the clay brick aggregate. The brick aggregate was submerged in the cement paste for about 5 min and let it dry naturally under ambient condition for bonding purpose. Figure 1 shows the crushed clay brick aggregate before treatment as CCBA, and Fig. 2 shows the brick aggregate after cement coating.
2.2 Properties of Coarse Aggregates and Mix Proportion
Sieve analysis was conducted for the CCBA. Besides, loose bulk density, water absorption, specific gravity, and impact value tests were carried out for both natural coarse aggregates (NA) and CCBA. Figure 3 shows the gradation of the CCBA. The properties of NA and CCBA are summarized in Table 1. CCBA used in the study is almost in the range between the upper and lower limit of the coarse aggregate size based on BS standard. The distribution curve shows CCBA has lesser aggregate in 10 mm size. As predicted, CCBA is much lighter, higher water absorption, and lower mechanical strength compared with NA.
Fives concrete mixes were prepared as given in Table 2. The mix was designed to have a 28-day target compressive strength of 30 MPa with a constant water/cement ratio of 0.55. The control mix (M0) is the normal concrete without CCBA. CCBA was used to replace NA based on the control mix for another four mixes (25, 50, 75, and 100%) The mass of the CCBA used in the mix is calculated by considering the density of the aggregates.
2.3 Specimens and Tests
The properties of concrete were determined accordance to the standard procedures. 100 mm cubes specimens were used to test the compressive strength at 7, 28, and 56 days and water absorption at 28 days. Water absorption of the hardened concrete was measured up to 120 min. 150 mm diameter × 300 mm length cylinder specimens were used to study the flexural strength at 28 days. All concrete specimens were subjected to water curing. Workability for fresh concrete, compressive, and splitting tensile strengths of hardened concrete were measured according to the procedure prescribed in BS 1881 [14, 15] and ASTM C496 [16], respectively. The reported results are the averages of the measurements for all properties.
3 Results and Discussions
3.1 Workability
Workability of the concrete mixes was determined by using slump test. Figure 4 shows the results of the slump test. The slump value of the concrete reduced with the increasing portion of CCBA in concrete. Zero slump was recorded for the concrete mix containing 75 and 100% CCBA. The reduction of workability in CCBA concrete is due to the higher water absorption of CCBA, and the irregular shape of CCBA provides more friction among the particles.
3.2 Hardened Density
Figure 5 shows the density of the hardened concrete with different portion of CCBA as coarse aggregate. The density was measured based on the 100 mm cubes before subjected to compressive strength test. The density of the hardened concrete was decreasing with the increasing of CCBA replacement as coarse aggregate in concrete. M100 achieved the lowest density with an average of 8.3% lower than M0. The reduction in density of concrete can be attributed to the aggregate density and shape [17]. Therefore, concrete containing CCBA gained lower density is due to the lightweight properties of CCBA.
3.3 Water Absorption
The results of the 28 days water absorption are shown in Fig. 6. The water absorption of the concrete was measured based on 100 mm cubes. The reading of the water absorption was taken at 10, 20, 30, 60, and 120 min. The water absorption of the concrete is gradually increase over time. The increasing of CCBA in concrete has caused the increasing of water absorption. M100 consists of 100% which CCBA shows the highest water absorption with an increment of 68% compared with M0. The result shows that the water absorption of concrete was increased as the amount of replacement of coarse aggregate using CCBA increase. Brick aggregate is generally having higher porosity and water absorption [6]. Therefore, the water absorption of concrete containing CCBA is relatively higher than the concrete with NA due to the higher capillary for concrete containing CCBA.
3.4 Compressive Strength
Figure 7 shows the compressive strengths of different concrete mix at 7, 28, and 56 days. All mixes achieved the 28-day design targeted strength of 30 MPa with the highest and lowest strengths associated with concrete M0 (38.2 MPa) and M75 (34.9 MPa), respectively.
The results show that the replacement of NA with CCBA did not show a significant reduction of the compressive strength for all ages. At 56 days, all CCBA concretes except M100 have gained higher compressive strength compared with M0. The highest compressive strength was achieved by M25 of 42.0 MPa at 56 days which is 4.74% higher than M0. M25 has showed the highest increment in compressive strength which is 96.26% at 56 days compared to its 7 days strength. While, M0 shows an increment of almost 80% in compressive strength at the age of 56 days compared to its 7 days strength. Based on the compressive strength results, all concrete mixes containing CCBA were achieved structural grade with reasonable strength.
3.5 Splitting Tensile Strength
Splitting tensile strength of the concrete was measured at the age of 28 days. Figure 8 shows the relationship between the percentage of CCBA as partial replacement in concrete and the splitting tensile strength. The splitting tensile strength of concrete is found to decrease with the increase of percentage replacement of CCBA as coarse aggregate, Concrete which containing 100% of NA (M0) shows the highest splitting tensile strength of 3.17 MPa. Inversely, concrete containing 100% of CCBA (M100) gained the lowest splitting tensile strength of 2.65 MPa. The use of CCBA in concrete has caused a reduction of splitting strength ranging between 12 and 16.4% compared to M0. The splitting tensile strength of concrete reduces when the increase of percentage of CCBA in concrete might due to the lower internal friction of the aggregate. The application of cement coating on brick aggregate reduced the internal friction of the aggregate and as a result the splitting tensile strength of the concrete decreased. This is due to the formation of a weaker interfacial transition zone (ITZ) around coated aggregate as the failure surface [13].
4 Conclusions
This study has exclusively focused on the physical and mechanical properties of cement-coated brick aggregate (CCBA) concrete. CCBA has a low density, high aggregate impact value, and high water absorption due to the high porosity of brick aggregates. The high water absorption of CCBA leads to the low workability of concrete with the same water/cement ratio compared to natural aggregate concrete. The compressive strength of concrete containing CCBA did not show a significant reduction without changing the water/cement ratio. The splitting tensile strength of the concrete decreases as the percentage of CCBA as partial coarse aggregate replacement in concrete increases. The main reason for this is attributed to the weak interfacial transition zone (ITZ) around the coated aggregate. Based on the experimental results, CCBA concrete has good advantage in weight reduction, comparable compressive strength to NA concrete, but the workability and splitting tensile strength need further investigation before practical application in concrete construction.
References
Wan Ibrahim WZ (2007) Towards a sustainable quarry industry in Malaysia. Jurutera 12:8–10
Hamid ZA, Pereira JJ, Ismail S (2006) Minerals security how vulnerable is the construction industry. Ingenieur 30:13–17
Zheng C, Lou C, Du G, Li X, Liu Z, Li L (2018) Mechanical properties of recycled concrete with demolished waste concrete aggregate and clay brick aggregate. Results Phys 9:1317–1322
Desmyter J, Van Dessel J, Blockmans S (1999) The use of recycled concrete and masonry aggregates in concrete: improving the quality and purity of the aggregates. In: Proceedings of the international congress “creating with concrete”, “Dundee, UK, Book” Exploiting wastes in concrete, pp 139–149
Khaloo AR (1994) Properties of concrete using crushed clinker brick as coarse aggregate. Mater J 91(4):401–407
Mazumder AR, Kabir A, Yazdani N (2006) Performance of overburnt distorted bricks as aggregates in pavement works. J Mater Civ Eng 18(6):777–785
Wongsa A, Sata V, Nuaklong P, Chindaprasirt P (2018) Use of crushed clay brick and pumice aggregates in lightweight geopolymer concrete. Constr Build Mater 188:1025–1034
Hansen TC (2014) Recycling of demolished concrete and masonry. CRC Press
Neville AM (1995) Properties of concrete. Longman’s, London
Katz A (2004) Treatments for the improvement of recycled aggregate. J Mater Civ Eng 16(6):597–603
Lee CH, Du JC, Shen DH (2012) Evaluation of pre-coated recycled concrete aggregate for hot mix asphalt. Constr Build Mater 28(1):66–71
Tam VWY, Gao XF, Tam CM, Tam VW (2006) Comparing performance of modified two-stage mixing approach for producing recycled aggregate concrete. Mag Concr Res
Uddin MT, Hasnat A, Awal MA, Bosunia SZ (2013) Recycling of brick aggregate concrete : an extended study on some key issues. In: 3rd international conference on sustainable construction materials and technologies, SCMT 2013. Japan
British Standard Institution (1983) Method for determination of slump. BSI, London, BS 1881: Part 102
British Standard Institution (1983) Method for determination of compressive strength of concrete cubes. BSI, London, BS 1881-116
ASTM (2004) Standard test method for splitting tensile strength of cylindrical concrete specimens. ASTM C496, annual book of American society for testing materials standards, vol C
Younis KH, Pilakoutas K (2013) Strength prediction model and methods for improving recycled aggregate concrete. Constr Build Mater 49:688–701
Author information
Authors and Affiliations
Corresponding author
Editor information
Editors and Affiliations
Rights and permissions
Copyright information
© 2023 The Author(s), under exclusive license to Springer Nature Singapore Pte Ltd.
About this paper
Cite this paper
Jung, C.T., Siang, T.C., Kwong, T.H., Boon, K.H. (2023). Properties of Cement-Coated Brick Aggregate Concrete. In: Nia, E.M., Ling, L., Awang, M., Emamian, S.S. (eds) Advances in Civil Engineering Materials. Lecture Notes in Civil Engineering, vol 310. Springer, Singapore. https://doi.org/10.1007/978-981-19-8024-4_29
Download citation
DOI: https://doi.org/10.1007/978-981-19-8024-4_29
Published:
Publisher Name: Springer, Singapore
Print ISBN: 978-981-19-8023-7
Online ISBN: 978-981-19-8024-4
eBook Packages: EngineeringEngineering (R0)