Abstract
The chapter highlights the investigations on the friction reduction capability of a pre-determined sized hemispherical dimples of 3 mm diameter, taking into consideration the fact of easy availability of the tool (ball nose end mill) for industrial applications. The dimples were created using CNC milling machines on EN 31 disc. A pin-on-disc tribometer was used to investigate the tribological behavior of the various textured density surface (7.5, 15 and 22.5%) against EN 8 steel under various loading conditions (120, 140, and 160 N) and very harsh lubricating conditions: dry, partial lubrication (lubricant supplied 54 mL dropwise at a flowrate 1 mL/s) and starved lubrication (10 mL lubricant spread over the disc before the experiment). A significant decrease of 12% reduction of coefficient of friction (COF) was observed with 15% texture density under 120 N while the COF increased by 40–60% at texture density of 22.5% and high loads. In dry condition there was no significant change in COF but the specific wear rate decreased by 64.69% in 22.5% texture density. In the present set of experiments carried out at lighter load (120 N), both 7.5 and 15% texture densities exhibited better results as compared to 22.5% texture densities (under partial lubrication). Surface characterizations by optical microscopy revealed that the friction reduction of the dimpled surface was primarily due to the lubricant retaining capability by the dimples which acted as oil reservoirs, but high texture densities intensified the friction.
Access provided by Autonomous University of Puebla. Download chapter PDF
Similar content being viewed by others
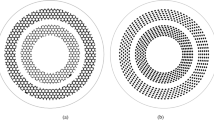
1 Introduction
Friction is energy consuming, its reduction being one of the most important tasks continuously aimed by industries. The enterprises which provide the wear and friction reduction solutions always look forward for inexpensive remedies without compromising the performance of the product. Friction reduction by surface texturing is one such methods which is very popular in different industries. Surface textures can be made using various processes, such as chemical etching (Pettersson and Jacobson 2003), laser texturing (Etsion 2005; Kovalchenko et al. 2005; Borghi et al. 2008; Etsion 2004), lithography (Stephens et al. 2002), and pellet pressing (Yan-qing et al. 2009). Zenebe Segu and Hwang (2015) discussed the effect of multi-shaped laser surface texturing on tribological properties of materials. It was found that the multi-shaped dimples gave better results than single shaped dimples. Among the different combinations of circle-ellipse, circle-triangle, and circle-square, the circle-ellipse combination gave the best results under dry and lubricated long sliding conditions. Bhaduri et al. (2017) reported results of tests on the ball-on-disc tribometer with reciprocating sliding motion, presenting the functional response of the textured surfaces with different designs that incorporate arrays of micro-dimples and grooves produced on tungsten carbide blocks by employing laser machining, which were rubbed against stainless steel. It was observed that the micro-arrays and dimples acted as traps for the asperity wear products (third body). Greco et al. (2009) discussed the potential application of vibro-mechanical texturing (VMT) for the generation of dimples on the aluminium and hardened steel on inner cylinder, outer cylinder, and flat end face geometries using a CNC lathe machine. It was found that the VMT method was much more adaptable to the process capabilities, cost effective, and a faster way to create dimples. An error of 1–11% was found on aluminium and 8–9% on hardened steel surface which was attributed to the elastic restoration of the material.
The performance of textured surfaces depends on various factors such as the shape of the textures, arrangement of the textures, materials in contact, load etc. Vilhena et al. (2010) created the surface textures using the LST (Laser Surface Texturing) technique and the tribological tests were conducted for various running parameters. It was found that the tribological behavior of the surface majorly depends upon the dimple depth, or indirectly on aspect ratio (constant diameter), local lubricating conditions, and operating parameter. At more depths and higher sliding speeds the dimpled area has proven to be most beneficial. The most significant result was obtained at a dimple depth of 16.5 microns and 0.45 m/s sliding speeds giving out a COF value as low as 0.006. Olver et al. (2016) prepared specimens of fused silica with small surface modifications in terms of creating small pocket sized micro dimpled geometries and tests were conducted to compare the difference between the textured and the non-textured samples. A reduction of 70% was observed in coefficient of friction (COF) with the textured surfaces. Furthermore, an improvement in film thickness was also observed using textured surfaces. An important result was found that, as the sum of the dimples increased along the length of the stroke, better frictional and wear properties were observed. It was also inferred that the individual dimple geometry had a very little effect on the properties as long as the overall effect remains positive. Kovalchenko et al. (2011) performed experiments on ball on disc tribometer to determine the effects of surface texturing on the disc surfaces for different oils of various viscosities, combined with different dimple densities with varying depths. The results showed that the increased dimple density caused an increase in wear rates of ball end but a decrease in COF values. The method has been suitably suggested for industrial applications. Yu et al. (2009) studied the effect of different shape dimples on the tribological properties. Different shapes like circles, ellipses, and triangles were made on the surfaces. Each shape was tested in different orientations for several loads and speeds. For example, when the pin slide against the ellipse shape perpendicular to the major axis gave the best results. Triangle is also tested with changing the orientation like sliding towards apex and sliding towards base. Optimized dimple parameters with ellipse shape orientated perpendicular to its major axis gave the best results. After ellipse, circle shape was found to give good results. Etsion and Burstein (1996) developed a model to analyze and compare the contactless seals in lubricated conditions with hemispherical pores. It was investigated if better performances can be achieved with proper selection of dimple size and aspect ratio. They found that the best and optimum dimple size depends on viscosity, contact pressure, and aspect ratio. The hydrodynamic performances were increased at the pore areas on the mechanical seals. Adjemout et al. (2017) studied the influence of real dimple shapes on the performances of the mechanical seals. Numerical solution is used to determine the optimum surface texturing and geometry, the mechanical imperfections being avoided. The real dimple shapes are analyzed and considered within the hydrodynamic lubrication model. The roughness and the bottom surface of the dimples influenced the leakage of oil through the seals. It was also found that enhanced results were obtained if the sides of the triangle were bent towards the center of the dimple. Etsion et al. (1999) developed an analytical model to investigate the performance of the mechanical seals having micro pores on its surfaces, machined using laser surface texturing. Optimization was performed for the spherical shaped pores. It was found that the effect of the pores depth over diameter ratio that is the aspect ratio was very significant. If the hydrostatic forces suppressed the hydrodynamic ones, the performances of the laser textured seals were far better than the conventional mechanical seals. Resendiz et al. (2015) studied the directional friction effects by creating asymmetrically shaped dimpled surfaces on an aluminum work piece using an inclined micro flat end milling tool. When compared with the flat surfaces, the dimpled surfaces resulted in lower friction coefficient values. Also, the asymmetrical textures gave a sliding direction dependent response in terms of measured frictional forces and the coefficient of friction. Jana et al. (2018) studied the frictional behavior and surface properties of tool under textured conditions. Different shapes of texturing were done in tetragonal and hexagonal patterns. Dimple like depressions and S shaped grooves were showing around 40% reduction in coefficient of friction. The tests were conducted in a ring test rig. Other shapes such as circular grooves and spherical dimples when oriented radially towards the sliding load gave better results in coefficient of friction. Shen and Khonsari (2015) tried to develop and adopt a numerical approximation method to find the most appropriate size of the textures or the dimples which would lead to the highest load bearing capacity of the textured surface. Numerical problems have been solved and then the method is validated and experiments were conducted creating the optimized dimples. The results were then compared with the regular shape dimples. The optimized shape was a chevron shape for unidirectional sliding and trapezoidal shaped dimples for the bi-directional sliding motion. Amini et al. (2016) studied the tribological behaviors of two micro textured surfaces and compared it with that of smooth surface. Pin on disc reciprocating set up is used for testing. Two surfaces that is micro surface textured (MST) and micro furrowed surface (MFS) was tested under load conditions from 20 to 160 N and under boundary lubricated condition. Here both MST and MFT showed better results than the smooth surface. The complex cutting movement is caused by ultrasonic vibrations. The results indicate that proper micro texture by Ultrasonic vibration-assisted milling (UAVM) can improve the load bearing capacity. Li et al. (2014) studied the frictional behavior and wear rates of a textured surface made by laser peen texturing. Texture densities with 5, 13 and 35% are tested by pin-on-disc tribometer and compared with the untextured surface under the load condition from 20 to 400 N. In this case, 13% texture density samples demonstrate better results in friction performance and wear rate. Schneider et al. (2017) studied the influence of aspect ratio, texture pattern, and dimple parameters under mixed lubrication regimes. The texture density was varied from 5 to 30% in different patterns like cubic, hexagonal and random arrangement. The depth to diameter ratio was also varied from 0.1 to 0.2. The lubricant used was POA. Results illustrate that those patterns arranged in hexagonal arrays performed well under the texture density of 10% with aspect ratio of 0.2. Around 80% reduction in friction coefficient was observed in this condition. Varenburg et al. (2002) studied the role of oxide wear debris in fretting wear. The wear rate varies according to the roughness of the material. Here micro dimples act as traps for debris. As the pin is sliding, wear debris gets deposited on the dimples which helps in further reduction in wear rate. They also found that 84% reduction is there due to the dimples acting as pores. Multi dimples with different patterns were created and tribological properties were evaluated and tested to collect data for wear and coefficient of friction values by Tang et al. (2013). The results show that surface texturing is essential and an important method for reducing friction and wear. Amendments in the area fractions and the aspect ratios can significantly improve the tribological characteristics, COF and the wear rates. A significant reduction of 38% in COF and 72% in wear rates were observed under the area fraction of 5% which was increased due to hydrodynamic pressure in the interfacial contacts between the surfaces. Podgornik et al. (2012) investigated the tribological effects of surface texturing under starved, boundary and mixed lubrication regimes. The experiments were conducted with LST technique on pin on disc apparatus and compared the results with varying lubricant viscosity, normal load, sliding speed, dimple/groove size, dimple/groove density, dimple depth and different lubrication regimes. The results show that LST surfaces with lower dimple/groove size and density has less friction under boundary lubricated conditions. Further the largest dimple depth under full film lubricated conditions gives the lowest friction. Hua et al. (2017) studied the frictional behavior of the contact surfaces lubricated with grease by using disc on ring tribometer. Various parameters like texture density, load, sliding speed and sliding time were varied. The lubrication regime was mixed lubricated regime. The results show that influence of texture density is a significant factor in controlling the tribological properties. Here a texture density of 15% is found to give the best results. Also, the major reason for control of friction is the hydrodynamic effect of the lubricant. Ogawa et al. (2010) investigated the tribological properties of slideways by laser texturing method. Different types of dimples and grooves were made for testing. The dimple width varied from 50 μm to 1 mm. The optimum dimple parameters were found after the test. The textured surface was found to give less friction coefficient as lubricant reservoirs were created inside the dimples. Jahanmir (1985) experimented and observed that the process of wear particle formation is greatly affected by the tangential stresses. Keeping the normal stresses constant and varying the tangential stresses with the COF, it was observed that the wear particles are formed due to deformation of the surface asperities significantly due to plowing and delamination process. It was also concluded that friction modifiers can influence the wear rate and its mechanism. Wear rate can be reduced by reducing the COF value below the threshold limit. Plowing and delamination are one of the causes that influence the wear rate. Under starved lubricating conditions the adhesive wear is predominant. Wang et al. (2017) investigated about the wear and friction performance of three different types of polymer on steel surface using ring on plane device. Texturing of different density values was done on steel surfaces. Polymers of various composition are tested under diverse texture densities and depths. The best results were obtained in dimples with depth of 5 μm rather than dimples with a depth of 10 μm. The wear debris found for non-textured surface were smooth and at higher wear the nature of debris was lumpy and at lower wear rate the nature was like twisted. Zhang et al. (2012) studied and conducted experiments on textured and untextured surfaces of UHMWPE under water lubrication using ring-on-disc tester. The textured surfaces shows a reduction in the COF as much as 66.7–85.7% on different load and speed conditions. The textured UHMWPE with an area density of 29.9%, diameter 50 mm, and depth 15 mm presents a significant effect of wear resistance, being reported as optimized result. It was observed that the micro-scaled surface textures show a greater wear resistance and lower COF values. Chowdhury et al. (2011) investigated the behavior of friction and wear under varying sliding speed, normal load and relative humidity. The experiments were conducted on pin-on-disc tribometer, where disc was made of aluminum and pin was of stainless steel. The results show that as the sliding speed increased, friction decreased and wear rate increased, as aluminum has the property of reacting with air and forming oxides. It forms a layer on the surface reducing metal to metal contact, hence reducing friction. From the above cited works, it can be seen that surface texturing has been used since a long time in various fields to control the friction. The recent work reported by Chen et al. (2019) showed that the load bearing capacity of a separator plate enhanced after texturing. In this case the cylindrical and cuboidal textures performed better than hemispherical textures at low speed. They also reported that the geometrical features of the dimples played a major role in enhancing the load bearing capacity. A decrease of over 20% wear rate in textured samples made of Ti alloys was reported by Yuan et al. (2019). In another work involving the investigation of tribological properties of Ti alloy reported by Kummel et al. (2019), it was observed that the melt bulges formed around the sides of the channels created using laser were active sites for solid solution of interstitial elements such as oxygen and nitrogen which helped in enhancing the tribological properties of Ti6Al4V.
Thus, it can be seen that surface engineering is an established field in controlling friction and wear and many works have been reported but very few systematic work has been done on dimples created using milling machines. Almost no work has been reported involving extreme harsh conditions of lubrication of dimpled surface. This chapter focuses on the performance of the dimpled surface in highly sparse lubricant condition where very minimal quantity of lubricant with discontinuous flow has been used. Milling machines (vertical) which are very common in any manufacturing unit were used to create the dimples. The cost of creating dimpled surfaces by milling is less expensive and easy to make for any industry. The size of the dimple was also chosen in such a way that the tool necessary for making the dimple is not expensive and easily available in the local market. Thus, the present work will be helpful for process industries in combating wear using dimpled surfaces created by milling process.
2 Texturing on Tribo Surface Using Milling Operation
A disc of EN 31 steel with 165 mm diameter, thickness 8 mm and hardness 38 HRC was used. Circular dimples were created on the disc surface with a ball end mill cutter in a CNC milling machine (Make: Lakshmi Machine Works, Model: LV45) at a constant feed rate of 120 mm\rev. The dimples on the surface of the specimen were uniformly arranged in a circular orientation as shown in Fig. 12.1. Hua et al. (2017) studied the frictional behavior of the contact surface lubricated with grease by using disc on ring tribometer and reported that the texture density of 15% exhibits least coefficient of friction. Thus, for the present work three dimple densities, namely 7.5, 15 and 22.5% were considered. The design texture density (Td) was calculated using Eq. 12.1 (Hua et al. 2017)
where
- Td:
-
is the texture area ratio (texture density);
- Ad:
-
is the area of the dimple (Ad = πD2/4)
- As:
-
is the sector area between the dimple \(A_{s} = \frac{{\theta (r_{1}^{2} - r_{2}^{2} )}}{2}\)
- r1:
-
is radius of the bigger sector
- r2:
-
is radius of the smaller sector
- D:
-
is dimple diameter.
The bulges or burrs which formed around the dimple during the machining process were removed by polishing. This reduces the negative effect on the tribological performance of contacting surfaces (Etsion 2004). A cylindrical EN 8 pin (diameter 10 mm, length 30 mm and hardness 31HRC) was used against the EN 31 disc.
In this work circular dimples were developed keeping in mind the following:
-
i.
Ease of availability of the 3 mm diameter ball nose milling tool in local markets.
-
ii.
Ellipse and circular dimples exhibited better tribological properties (Yu et al. 2009).
-
iii.
Textured surfaces with curved bottom were found to show better tribological properties than flat bottom surfaces, sharp angles and straight edges (Qiu et al. 2013).
3 Investigating the Tribological Properties Using Pin-on-Disc Tribometer
Pin-on-disc tribometer was used to investigate the tribological properties of the textured surface (disc of EN 31). The counter part was the EN 8 pin. SAE 10W30 lubricant was used during the tests and three different loads were considered (120, 140, and 160 N) at a constant speed of 4.2 m/s under the influence of the following lubrication condition:
-
i.
Dry condition: no lubricant was used.
-
ii.
Partial lubrication condition: lubricant was supplied between the interface of the pin and disc in a drop wise manner (amount of lubricant used: 54 mL with a flow rate of 1 mL/s).
-
iii.
Starved lubrication condition: about 10 mL of the SAE 10W30 lubricant was poured over the textured surfaces before the start of the experiment. It was ensured that the lubricant fully covers the disc. The test was started after five minutes ensuring the lubricant to settle in the dimples. No further lubricant was added during the entire duration of the tribo experiment.
Each combination of trials was repeated thrice and an average of the friction coefficient and wear rate has been reported in the work. The experimental parameters are shown in Table 12.1.
The average coefficient of friction for all the experiments are shown in Fig. 12.2a. Here the same chronology is maintained as shown in Table 12.1.
Dry condition: From Fig. 12.2a it can be seen that the COF in dry condition is more than the lubricated conditions. When it comes to partial and starved lubrication condition, a decrease in COF is observed. The highest COF is experienced in experiment number 4 (i.e. load 120 N, texture density 22.5% and dry lubrication condition) while the least value is obtained in experiment number 27 (i.e. 120 N, texture density 15% and partial lubrication condition). But in higher loading conditions such as 140 and 160 N performed under partial lubrication the least coefficient of friction is observed in texture density of 7.5%. Figure 12.2b depicts the variations of the wear rates under different testing. It can be seen that the wear rate decreases with the increase in texture density. Same goes with the next 2 sets of intervals (Experiment 5 to Experiment 8; Experiment 9 to Experiment 10). A slight increase in the last experiment (Experiment 8 and Experiment 12) of each set corresponding to the highest texture density in that set.
Lubricated condition: Fig. 12.2c shows the trend and variation of wear rates with changes in the experiment conditions which includes changes in loads, lubricating conditions and texture densities. Experiment 13–24 correspond to the starved lubrication under different texture densities and Experiments 25–36 corresponds to the partial lubricating condition. The highest wear rate can be seen in experiment number 36 (160 N, texture density 22.5% and partial lubrication condition) while the least wear rate is observed in experiment number 15 (load 120 N, texture density 15% and starved lubrication condition). In starved lubrication, a decreasing trend for the first 3 experiments in 1st set (Experiment No. 13–15) and increasing trend for the last 3 experiment in the 3rd set (Experiment No. 22–24) are obtained. This goes for all the intervals (Experiment 29 to Experiment 36). But a nonlinear variation for all experiments in the 2nd set (Experiment No. 17–20) and 7th set (Experiment No. 25–28) is observed. The 4th experiment on each set is always seen to be increasing in each interval similar to dry condition.
From Fig. 12.2, it can be seen that at 140 and 160 N load, the COF and wear rates increased with an increase in texture densities. The lowest COF and wear rate were obtained at 120 N load conditions. The wear rates were high at 140 and 160 N as compared to 120 N of applied load. Figure 12.3 shows the COF and wear rates plotted against texture density at 120 N load conditions performed under various lubricated conditions. A decreasing trend in COF with increasing texture density under partial lubricating regime can be seen in Fig. 12.3a whereas, in starved lubrication the coefficient of friction decreases till 7.5% texture density and then increases. Furthermore, 7.5% texture density exhibited lowest COF (15 and 18% decrease in 0 and 15% texture densities under starved lubricating regime respectively) while in partial lubrication the 15% dimple density have shown beneficiary results as the COF was 13% less than 0% and 3.6% less than 7.5% texture densities. Thus, a decreasing trend of COF in lubricating conditions indicates the advantage of the presence of dimples on the surface. Figure 12.3b shows the variations between the wear rates and texture density with constant loading conditions and different lubrication regimes (starved and partial lubrication). It can be seen that during starved lubrication condition, there was no significant change in the wear rates at 0 and 7.5% textured density while a significant decrease in wear rate by 64–65% was observed at 15% texture density as compared to the wear rates of 0 and 7.5% texture densities. In partial lubrication, a slight decrease of 9% wear rate was observed at 7.5% as compared to untextured but it increased at 15% texture density. Unlike the COF variations, the least wear rate is found in the texture density of 15% under starved lubrication condition. Figure 12.3c shows the trend of COF with varying texturing density in dry environment and under 120 N loading conditions which exhibited that the COF in non-dimpled and dimpled surface were almost equal, however a significant 61% decrease in wear rate in case of textured surface can be observed as seen in Fig. 12.3d.
From above discussions it can be seen that the COF is less in the case of partial lubrication as compared to dry and starved lubrication conditions. Figure 12.4 shows the COF against texture densities at different load conditions (120, 140 and 160 N) performed under partial lubricated condition. In case of 120 N with partial lubricated condition (Fig. 12.4a), a gradual decrease in the COF was observed till 15% texture density but there was a 60% decrease in COF at 15% as compared to 22.5% texture density while in 140 and 160 N with partial lubricated conditions (Fig. 12.4b, c), a slight decrease in friction coefficient was observed at a texture density of 7.5% as compared to texture density of 0% and further increasing the texture density the COF increased. It is to be noted that for all loads, an increasing trend of COF was observed with increase in texture density.
4 Understanding the Mechanisms Involved During Tribo Tests
4.1 Lubricant Reservoirs Leading to Friction Reduction
Figure 12.5 shows the arrangement of the pin and the dimple in a lubricated condition. During the test, the pin surface fully covered the dimple region at an instantaneous moment while sliding. The dimple served as the lubricant reservoir while running in starved lubricating conditions, but in dry sliding condition the dimples behaved as the wear debris storage and prevented the wear debris to affect the overall surface morphology, thus making the surface more wear resistant (Varenberg et al. 2002; Yamakiri et al. 2011). Friction between tribo pairs are less when the lubricating film is thicker than the average surface roughness value or the average height of the asperities but under high loading conditions, the lubricant oozes out of the rubbing track or the frictional zone, leading to the reduction in the film thickness to less than the average asperity height causing greater asperity contacts and ultimately leading to higher frictional force and wear (Bart et al. 2013). In case of textured surfaces, the region where the pin comes in complete contact with the dimple, the thickness of the lubricant film increases due to the presence of lubricant in the dimple. The depth of the dimple helps in retaining the lubricant which in turn increases the thickness of lubricant film leading to an increased hydrodynamic pressure exerted by the lubricant. This results in the increase of load bearing capacity, which ultimately reduces wear (Kovalchenko et al. 2005). It has been reported that increased dimple depths have beneficial effects on the reduction of friction and wear (Ogawa et al. 2010). Furthermore, in hydrodynamic lubricating conditions the effects of surface texturing have also contributed in improving the tribological characteristics (Mo et al. 2017; Qu et al. 2013).
The three-dimensional image of the dimples, shown in Fig. 12.6, clearly depicts that there was no contact between the pin and the base of the dimples, as no major deterioration of the surface can be observed, thus indicating the presence of lubricants in the dimples as shown in Fig. 12.6b.
4.2 Presence of Third Bodies in the Dimples (Dry Condition)
In 120, 140 and 160 N dry condition no significant difference in friction coefficient is observed but the wear rate was less in textured surfaces as compared to the non-textured surface. This may be due to the debris entrapment in the dimples which helped in preventing the direct contact of the tribo pairs and thus reducing the wear (Bhaduri et al. 2017; Varenberg et al. 2002; Fukagai et al. 2019; Yamakiri et al. 2011).
4.3 Increase in COF with the Increase in Load and Texture Density
As discussed in Sect. 12.3, in partial lubricated conditions COF gradually decreased as the texture density increased, but over 15% the COF increased again. In dry conditions, surface texturing in general will lead to increased friction (Fig. 12.2a), with every dimple acting as obstacle to the sliding motion (Podgornik et al. 2012). The increase in the texture density to 22.5% exhibited an increase in wear rate as compared with texture density of 7.5 and 15%. In the case of 22.5% texture density, the presence of large dimples made the surface less uniform which affected the uniform asperity peaks (Hua et al. 2017) increasing the COF. Furthermore, the heat generated led to localized welding of the small wear debris on the wear track (Elsevier 1987). This continuous welding and accumulation of the wear particles at a high load contributed to an increased frictional property.
At 120 N and partial lubricating conditions, as the texture density was increased the coefficient of friction decreases until texture density of 15%. The dimples acted as a lubricant reservoir and enhance the hydrodynamic action (Ogawa et al. 2010; Yamakiri et al. 2011). Further increasing the texture density to 22.5%, drastic increase in COF was observed. The space between each dimple acted like peaks, which affected the film distribution, thus resulting in higher friction (Hua et al. 2017). Also at higher dimple densities, the surface becomes highly non-linear leading to a turbulent lubricant flow on the surface affecting the shear properties of the interface (Qu et al. 2013). In case of starved lubrication condition as the texture density was increased the COF decreased until texture density of 7.5% and then increased with the increase in texture density. The change of lubrication regime from a partially hydrodynamic condition to very localized boundary conditions resulted in high asperity contacts (Li et al. 2014) during starved lubrication condition which resulted in gradual decrease in film over a period thereby, increasing the COF.
In 140 and 160 N under partial lubricated condition, the COF was less in textured surface as compared to un-textured surface but the increase in COF was similar to that of 120 N, as texture density increased the COF also increased. This is because at higher loads there is always a portion of area coming in contact and as a result, the edge of the dimple perpendicular to sliding direction lead to high stress generation at the edge of dimple (Zhang et al. 2012), thus affecting friction and wear. In 140 N, starved lubricated condition, in un-textured surface the lubricant after certain time drains out and thus, favoring high asperity-asperity contact increase the COF. Furthermore, in case of 7.5% texture density, the number of dimples were less as compared to 15% texture density and hence, more lubricant was retained in 15% texture density as compared to 7.5% texture density. Thus, COF for 7.5% was slightly more than texture density of 15% but further increasing the texture density to 22.5% conducted to augmentation of COF. The increase in COF and wear in high density textured surfaces were primarily due to the ploughing action exhibited by the dimples (Jahanmir 1985). Therefore, the exact number of dimples which is required to control wear and friction also depends on the amount of load applied.
4.4 Understanding the Severity of the Wear on the Counter Surface Against the Textured Surface
The scanning electron microscope images of the counter body (pin) after the tribo test has been shown in Fig. 12.7 which clearly identifies the severity of the wear during the process. As seen from Fig. 12.7a, b, the surface for dry conditions is more damaged than those of the lubricated condition as seen in Fig. 12.7c (non-textured) and Fig. 12.7d (15% texture density). High abrasive wear can be seen in both cases of dry condition in Fig. 12.7a, b, thus indicating that texturing may not be a good idea in dry condition but as seen in Fig. 12.7c, d, the surfaces are less damaged as compared to Fig. 12.7a, b. Close observation of Fig. 12.7c revealed the formation of grooves in several places and depression were also found as indicated. The formation of such deep grooves and depressed surfaces are due to the film breakage which resulted in high metal to metal contact. Moreover, it is to be noted that the lubrication condition considered for the present work was discontinuous and was supplied in drop wise condition making the situation quite severe, thus the possibility of film breakage is quite certain but looking into Fig. 12.7d (the surface of the pin whose counter body i.e. the disc was having dimples showed almost negligible damage) as compared to those of dry condition and lubricated condition (without dimples, Fig. 12.7c).
5 Conclusion
The chapter initially discusses the work which was reported by various researchers and then focused on the tribological properties of micro dimpled surfaces. The results showed that texturing may not be effective in dry condition in reducing coefficient of friction but significant decrease in wear rate can be achieved using the correct textured density (in this case 7.5%). The friction and wear reduction capability of textured surfaces primarily depends on the regime of lubrication, applied load and texture densities. However, the creation of micro sized dimples with CNC end mill ball nose cutters is an easy process and is quite capable of reducing the friction under severe conditions. This solution can be adopted by industries as an economical process to control friction and wear.
References
Adjemout M, Andrieux A, Bouyer J, Brunetière N, Marcos G, Czerwiec T (2017) Influence of the real dimple shape on the performance of a textured mechanical seal. Tribol Int 115:409–416
Amini S, Hosseinabadi HN, Sajjady SA (2016) Experimental study on effect of micro textured surfaces generated by ultrasonic vibration assisted face turning on friction and wear performance. Appl Surf Sci 390:633–648
Bart JCJ, Gucciardi E, Cavallaro S (2013) Principles of lubrication. Biolubricants 2:10–23
Bhaduri D, Batal A, Dimov SS, Zhang Z, Dong H, Fallqvist M, M’Saoubi R (2017) On design and tribological behavior of laser textured surfaces. Proced CIRP 60:20–25
Borghi A, Gualtieri E, Marchetto D, Moretti L, Valeri S (2008) Tribological effects of surface texturing on nitriding steel for high-performance engine applications. Wear 265:1046–1051
Chen LY, Li R, Xie F, Wang Y (2019) Load-bearing capacity research in wet clutches with surface texture. Measurements 142:96–104
Chowdhury MA, Khalil MK, Nuruzzaman DM, Rahaman ML (2011) The effect of sliding speed and normal load on friction and wear property of aluminum. IJMME 11:45–49
Elsevier BV (1987) Sliding wear. Tribol Ser 6:351–495
Etsion I (2004) Improving tribological performance of mechanical components by laser surface texturing. Tribol Lett 17:733–737
Etsion I (2005) State of the art in laser surface texturing. J Tribol 127:248–253
Etsion I, Burstein L (1996) A model for mechanical seals with regular micro surface structure. Tribol T 39:677–683
Etsion I, Kligerman Y, Halperin G (1999) Analytical and experimental investigation of laser-textured mechanical seal faces. Tribol T 42:511–516
Fukagai S, Ma L, Lewis R (2019) tribological aspects to optimize traction coefficient during running-in period using surface texture. Wear
Greco A, Raphaelson S, Ehmann K, Wang QJ, Lin C (2009) Surface texturing of tribological interfaces using the vibromechanical texturing method. J Manuf Sci E-T ASME 131:061005
Hua X, Puoza J, Zhang P, Xie X, Yin B (2017) Experimental analysis of grease friction properties on sliding textured surfaces. Lubricants 5:42
Jahanmir S (1985) The relationship of tangential stress to wear particle formation mechanisms. Wear 103:233–252
Jana S, Peter S, Martin F, Martin N, Jana M, Martin K (2018) The influence of the tool surface texture on friction and the surface layers properties of formed component. Adv Sci Technol Res J 12:181–193
Kovalchenko A, Ajayi O, Erdemir A, Fenske G, Etsion I (2005) The effect of laser surface texturing on transitions in lubrication regimes during unidirectional sliding contact. Tribol Int 38:219–225
Kovalchenko A, Ajayi O, Erdemir A, Fenske G (2011) Friction and wear behavior of laser textured surface under lubricated initial point contact. Wear 271:1719–1725
Kummel D, Hamann-Schroer M, Hetzner H, Schneider J (2019) Tribological behavior of nanosecond-laser textured Ti6Al4V. Wear 422:261–268
Li K, Yao Z, Hu Y, Gu W (2014) Friction and wear performance of laser peen textured surface under starved lubrication. Tribo Int 77:97–105
Mo F, Shen C, Zhou J, Khonsari MM (2017) Statistical analysis of surface texture performance with provisions with uncertainty in texture dimensions. IEEE Access 5:5388–5398
Ogawa H, Sasaki S, Korenaga A, Miyake K, Nakano M, Murakami T (2010) Effects of surface texture size on the tribological properties of slideways, proceedings of the institution of mechanical engineers. J Eng Tribol 224:885–890
Pettersson U, Jacobson S (2003) Influence of surface texture on boundary lubricated sliding contacts. Tribol Int 36:857–864
Podgornik B, Vilhena LM, Sedlaček M, Rek Z, Žun I (2012) Effectiveness and design of surface texturing for different lubrication regimes. Meccanica 47:1613–1622
Qiu M, Minson BR, Raeymaekers B (2013) The effect of texture shape on the friction coefficient and stiffness of gas-lubricated parallel slider bearings. Tribol Int 67:278–288
Qu H, Shen Z, Xie Y (2013) Numerical investigation of flow and heat transfer in a dimpled channel among transitional reynolds numbers. Mathem Prob Eng 2013:1–10
Resendiz J, Graham E, Egberts P, Park SS (2015) Directional friction surfaces through asymmetrically shaped dimpled surfaces patterned using inclined flat end milling. Tribol Int 91:67–73
Schneider J, Braun D, Greiner C (2017) Laser textured surfaces for mixed lubrication: influence of aspect ratio. Textur Area Dimple Arrange Lubric 5:32
Shen C, Khonsari MM (2015) Numerical optimization of texture shape for parallel surfaces under unidirectional and bidirectional sliding. Tribol Int 82:1–11
Stephens LS, Siripuram R, Hayden M, McCartt B (2002) Deterministic micro asperities on bearings and seals using a modified LIGA process. Turbo Expo, 4
Tang W, Zhou Y, Zhu H, Yang H (2013) The effect of surface texturing on reducing the friction and wear of steel under lubricated sliding contact. Appl Surf Sci 273:199–204
Varenberg M, Halperin G, Etsion I (2002) Different aspects of the role of wear debris in fretting wear. Wear 252:902–910
Vilhena LM, Podgornik B, Vižintin J, Možina J (2010) Influence of texturing parameters and contact conditions on tribological behaviour of laser textured surfaces. Meccanica 46:567–575
Vlădescu S-C, Olver AV, Pegg IG, Reddyhoff T (2016) Combined friction and wear reduction in a reciprocating contact through laser surface texturing. Wear 358–359:51–61
Wang M, Zhang C, Wang X (2017) The wear behavior of textured steel sliding against polymers. Materials 10:330
Yamakiri H, Sasaki S, Kurita T, Kasashima N (2011) Effects of laser surface texturing on friction behavior of silicon nitride under lubrication with water. Tribol Int 44:579–584
Yan-qing W, Gao-feng W, Qing-gong H, Liang F, Shi-rong G (2009) Tribological properties of surface dimple-textured by pellet-pressing. Proced Earth Planet Sci 1:1513–1518
Yu H, Wang X, Zhou F (2009) Geometric shape effects of surface texture on the generation of hydrodynamic pressure between conformal contacting surfaces. Tribol Lett 37:123–130
Yuan S, Lin N, Zhou J, Liu Z, Wang Z, Tian L, Qin L, Zhang H, Wang Z, Tang B, Wu Y (2019) Effect of laser surface texturing (LST) on tribological behavior of double glow plasma surface zirconizing coating on Ti6Al4V alloy. Surf Coat Technol 368:97–109
Zenebe Segu D, Hwang P (2015) Friction control by multi-shape textured surface under pin-on-disc test. Tribol Int 91:111–117
Zhang B, Huang W, Wang X (2012) Biomimetic surface design for ultrahigh molecular weight polyethylene to improve the tribological properties. Proc Inst Mech Eng J Eng Tribol 226:705–713
Acknowledgements
The authors are grateful for the financial grant received from Tata Steel Jamshedpur, India for carrying out the work. The authors are grateful to Tata Steel for allowing to publish the work.
Author information
Authors and Affiliations
Corresponding author
Editor information
Editors and Affiliations
Rights and permissions
Copyright information
© 2019 Springer Nature Singapore Pte Ltd.
About this chapter
Cite this chapter
Bhaumik, S. et al. (2019). Influence of Surface Texturing on Friction and Wear. In: Katiyar, J., Bhattacharya, S., Patel, V., Kumar, V. (eds) Automotive Tribology. Energy, Environment, and Sustainability. Springer, Singapore. https://doi.org/10.1007/978-981-15-0434-1_12
Download citation
DOI: https://doi.org/10.1007/978-981-15-0434-1_12
Published:
Publisher Name: Springer, Singapore
Print ISBN: 978-981-15-0433-4
Online ISBN: 978-981-15-0434-1
eBook Packages: Chemistry and Materials ScienceChemistry and Material Science (R0)