Abstract
Composite sandwich panels provide an increase in buckling resistance to thin composite plates and shells, leading to widespread use in a variety of applications such as boat hulls, rotor blades, and rocket casings. Past research has shown that delamination between the face sheets and core of composite sandwich panels occurs under a variety of both dynamic and quasi-static load conditions. While this failure mechanism has been identified and observed, existing research has not fully investigated the mechanisms behind this adhesive failure. In this study, a carbon fiber bar was adhered using JB Weld epoxy to a variety of substrates. Bulk polymer substrates included polycarbonate, ultra-high molecular weight polyethylene, and Delrin®, while two PMI foam substrates were used: Rohacell® WF200 and Rohacell® HERO200-HT. Experiment samples were impacted using a Kolsky bar apparatus to impart simple shear on the adhesive joint. The adhesive joint was observed in-situ using a synchrotron X-ray source in phase contrast imaging mode. The X-ray source was used in tandem with the Kolsky bar and high-speed camera. In order to introduce simple shear in the adhesive joint, the Kolsky bar was used to impact the carbon fiber bar with an impact velocity of ~7 m/s. Adhesive failure was observed in each of the bulk polymer samples, but no failure was seen in the PMI foam samples.
Access provided by Autonomous University of Puebla. Download conference paper PDF
Similar content being viewed by others
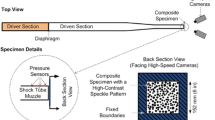
Keywords
Introduction
Fiber-reinforced composite materials have been seeing increased use over the past several years in a wide variety of applications including boat hulls, rotor blades, rocket casings, and aircraft wings. Due to the high strength-to-weight ratio of composite materials, these parts are often crafted as thin plates and shells. In order to increase the buckling resistance of these thin structures, composite sandwich materials were introduced to provide increased rigidity. The core material of these composite sandwich materials was initially composed of a honeycomb structure, often made of aluminum. Previous research has led to the use of polymer foams as a replacement for honeycomb cores as a cheaper and more effective core material.
All sandwich panels are composed of polymeric constituents, which can include the adhesive layer, the composite matrix and fibers, and the core layer of a panel. Due to the viscoelastic nature of polymeric materials, it follows that sandwich panels will display some inherent rate effects in their mechanical behavior. As a result, several studies have been done to examine the effects of impact and blast loads on composite sandwich panels. Experiments conducted by Rolfe et al. [1] and Dear et al. [2] showed that when subjected to blast loads, sandwich panels suffer failure both by core crushing and layer delamination. Another study examined the behavior of sandwich beams and panels under impact loading and found that delamination occurred between panel layers. These panels and beams were also tested after impact and showed reduced strength when compared to un-damage samples [3]. Other authors have expanded on this research and have stated that the adhesive layer between the face sheet and core layers is critical to the behavior of sandwich panels under dynamic load conditions [4].
Experiments
In order to examine the behavior of an adhesive joint between a composite layer and core layer, samples were subjected to simple shear by a modified Kolsky bar. Five different core materials were selected; monolithic Delrin®, monolithic polycarbonate, monolithic ultra-high molecular weight polyethylene, Rohacell® 200WF, and Rohacell® 200HERO-HT. In order to reduce the number of varied parameters, the face-sheet layer and adhesive remained constant. Samples were constructed using 0.25″ thick sections of core material with a 0.19″ thick layer of carbon fiber adhered with JB Weld steel-reinforced epoxy. The layer of carbon fiber was shifted slightly to overhang from the core layer. This geometry was chosen in order to isolate the impact load to the face sheet layer. Each sample was loaded by the incident bar at approximately 7 m/s and restrained with a rigid backstop. A schematic of the sample and its load configuration is show in in Fig. 34.1.
In order to visualize the behavior of the adhesive layer, the experiments were conducted at beam line 32-ID at the Advanced Photon Source, Argonne National Laboratory. Using a remote control and triggering system, X-rays were transmitted through the sample at an energy of 25.0 keV during the event. After passing through the sample, the X-rays were transmitted through a single crystal Lu3Al5O12:Ce scintillator, which converted the X-rays into visible light. Images were then recorded at a frame rate of 2,000,000 frames/second using a Shimadzu Hyper Vision HPV-X2 high-speed camera.
Results
The use of high-speed phase contrast imaging allowed for good observation of an adhesive joint between two dissimilar substrates. Of the configurations examined, apparent failure of adhesion was observed in each of the samples constructed with a monolithic polymer core material. In contrast, the samples composed of rigid foam cores showed no apparent failure. The damage seen in a Delrin® core sample is shown in Fig. 34.2. While the polymer of the two foam core materials is different from those in the monolithic cores, the results suggest a relation between surface porosity of the core material and adhesive strength of the adhesive layer in a sandwich panel.
References
Rolfe, E., Kelly, M., Arora, H., Hooper, P.A., Dear, J.P.: Procedia Eng. 167, 176–181 (2016)
Dear, J.P., Rolfe, E., Kelly, M., Arora, H., Hooper, P.A.: Procedia Eng. 173, 471–478 (2017)
Daniel, I.M., Abot, J.L., Schubel, P.M., Luo, J.J.: Exp. Mech. 52, 37–47 (2012)
Mostafa, A., Shankar, K., Morozov, E.V.: Mater. Des. 50, 92–101 (2013)
Author information
Authors and Affiliations
Corresponding author
Editor information
Editors and Affiliations
Rights and permissions
Copyright information
© 2020 Society for Experimental Mechanics, Inc.
About this paper
Cite this paper
Paulson, S., Kedir, N., Sun, T., Fezzaa, K., Chen, W. (2020). Observation of Dynamic Adhesive Behavior Using High-Speed Phase Contrast Imaging. In: Lamberson, L. (eds) Dynamic Behavior of Materials, Volume 1. Conference Proceedings of the Society for Experimental Mechanics Series. Springer, Cham. https://doi.org/10.1007/978-3-030-30021-0_34
Download citation
DOI: https://doi.org/10.1007/978-3-030-30021-0_34
Published:
Publisher Name: Springer, Cham
Print ISBN: 978-3-030-30020-3
Online ISBN: 978-3-030-30021-0
eBook Packages: EngineeringEngineering (R0)