Abstract
A rapid method for the quantitative determination of the hydroxyl value (OHV) of hydroxylated soybean oils by HATR/FTIR spectroscopy is described. Calibration standards were prepared by the formic acid/hydrogen peroxide method and OH values were determined by the official method of AOCS Tx 1a-66, covering an analytical range of 3.5–125 mg of KOH/g of sample. A partial least squares (PLS) calibration model for the prediction of the hydroxyl value (OHV) was developed based on eight different spectral subregions between 3,150 and 990 cm−1 and combinations of them. On average, 36 samples were used for the modeling and 17 were used for external validation. The resulting calibration was linear over the analytical range and had a standard deviation of 2.334. Validation of the method was carried out by comparing the OHV of a series of hydroxylated soybean oils predicted by the PLS model to the values obtained by the AOCS standard method. A correlation coefficient of R 2 = 0.9843 and RMSEC and RMSEP values of, respectively, 3.393 and 3.643 were obtained. After the calibration of the spectrometer, the OHV could be obtained in 2–3 min per sample, a major improvement over conventional wet chemical methods. The advantages of these methodologies are that they do not destroy the sample, have a lower cost, expedite the analysis and do not produce residues. Therefore, they may yield excellent results when used to quantify OHV of soybean polyols obtained by hydroxylation reaction.
Similar content being viewed by others
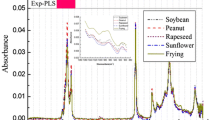
Avoid common mistakes on your manuscript.
Introduction
The environmental and sustainability aspects of using oleochemical polyols are of great importance to the polyurethane industry, considering the broad range of applications of these materials. Oleochemical polyols can be used in the production of VOC-free, two-component polyurethane coatings and floorings, adhesives, and thermoplastic polyurethanes [ 1–3 ].
In order to use natural oils as raw materials for polyurethane production, multiple hydroxyl functionality is required. Hydroxyl functionality occurs in some in natura oils, such as castor oil, or can be introduced in other oils, such as soybean and linseed oil, by epoxidation of the double bonds followed by ring opening with alcohols, amino alcohols or acids [4].
Our research group has been working on the development of soybean polyols, which have been prepared by the “one-step” hydroxylation of soybean oil with the formic acid/hydrogen peroxide system [5]. Depending on the reaction conditions, two different types of reaction products can be obtained: (a) polyols with high OH functionality by complete reaction of oxirane groups and (b) epoxy polyol ethers or epoxy polyol esters containing OH groups and remaining epoxy groups by incomplete reaction of the oxirane groups. Therefore, by controlling the reaction conditions, it is possible to obtain soybean polyols with different levels of hydroxyl functionality, which can be used to prepare polyurethanes with different properties.
For polyurethane preparation, it is important to know the final hydroxyl value (OHV) of the soybean polyol. Usually, the OHV is determined by titration methods such as the American Oil Chemists’ Society (AOCS) hydroxyl value determination (AOCS Cd 13–60) used in this work. The hydroxyl value is expressed in mg of KOH per g of oil. This method is reliable and reproducible if carried out under standardized conditions, but it is time-consuming, labor-intensive, reasonably sensitive, largely dependent on the skills of the analyst and uses large amounts of sample and reagents, some of which (pyridine, acetic anhydride) are hazardous and difficult to dispose of.
Similar problems have also been observed in other chemical analyses of fats and oils based on titration methods. Therefore, spectroscopic methods are being increasingly used to replace wet chemical procedures. Infrared spectroscopy is one that has found increased use due to its low cost, shorter analysis time, non-destructiveness and small sample quantities, in addition to accuracy and reliability when associated with chemometric methods [6–12].
FTIR coupled with horizontal attenuated total reflectance (HATR) simplifies many of the sample handling problems commonly associated with infrared analysis and is readily amenable to routine quality control applications [13]. The HATR procedure is rapid because it requires no weighing or quantitative dilution of test materials in any solvent and little or no preparation of the test sample [14].
Interferences usually take place when oil analysis is done in the mid-infrared spectral region. In such situations one of the most powerful chemometric approaches available is the PLS method [15, 16], which is capable of accounting for interactions, underlying absorptions, overlapping bands and other factors that may affect the spectra as the concentration of all components changes.
In this paper, we describe the development of a practical and rapid HATR/FTIR method to determine the OHV by the partial least squares (PLS) technique for multivariate analysis of FTIR data using synthesized soybean polyols as a basis for calibration and validation.
Materials and Methods
Chemicals
Refined soybean oil was purchased from CBM Ind Com Distrib Ltd (Cachoeirinha, RS, Brazil). Formic acid, ethyl ether were purchased from Synth. Hydrogen peroxide solution 30%, sodium chloride, sodium carbonate, sodium hydrogen sulfite, sodium sulfate anhydrous were purchased from Nuclear. All chemicals are analytical grade and were used without further purification.
Calibration Standards
Soybean polyols were synthesized following the method described below and were used as calibration standards. Depending on the time of reaction, soybean polyols with different OH functionality were obtained. The acid number (AN) and the OHV of the soybean polyols were determined by AOCS standard methods Cd 3a–63 [17] and Cd 13–60 [18], respectively. The 1H-NMR spectra were obtained using a Varian Inova 300, 300 MHz, using CDCl3 as solvent and TMS as standard.
1H-NMR spectra of the calibration standards showed the absence of double bonds and the presence of hydroxyl, epoxy and formate groups. The OHV cover a range of 3.5–125 mg of KOH/g.
Synthesis of Soybean Polyols
Refined soybean oil (70 g, 0.37 mol of double bonds) was mixed with 43 ml (1.11 mol) of formic acid. A solution of H2O2, 32% (50.5 ml, 0.56 mol) was slowly added dropwise to the mixture at room temperature over 30 min, under strong mechanical stirring. When the H2O2 addition was completed, the mixture was heated up to 65 °C, and strongly stirred for different times depending on the hydroxylation level to be reached. After the required time, the product was washed firstly with a sodium bisulfite 10% w/v solution, followed by a sodium carbonate 10% w/v solution until neutralization had occurred. Afterwards, ethyl ether was added and the organic phase was separated and dried overnight with sodium sulfate. The solvent was removed in vacuum, with a yield of 90% w/w.
Instrumentation
A Nicolet Magna 550 FTIR spectrophotometer with 4 cm−1 resolution and 16 scans was used for the measurement of soybean polyols. The duplicate spectra were recorded by applying the soybean polyol sample on the surface of a Pike horizontal attenuated total reflectance (HATR) sample-handling accessory with ZnSe crystal.
Calibration
A partial least squares (PLS) regression analysis for the HATR/FTIR spectra of the 36 soybean polyol samples was carried out using Pirouette software (Infometrix). The PLS models were developed using HATR/FTIR absorption data in four different regions (3,150–2,800; 1,490–1,400; 1,400–1,200 and 1,090–990 cm−1). These had been constructed with auto-scaled data (mean centered and variance scaled methods were applied) and/or multiplicative scattering correction (MSC). The samples presenting extreme OHV values were included in the calibration set.
Cross-validation following the leave-one-out procedure was performed during the validation step in order to define the optimum number of factors that should be kept in the model and to detect any outliers.
Validation
Seventeen soybean polyol spectra were used in duplicate for the validation of the PLS regression model. The best model was selected considering the minimal error, that is, lowest RMSEC (root mean square error of calibration) and lowest RMSEP (root mean square error of prediction) described in Eq. 1,
where n is the number of spectra, y i and ŷ i are the values determined by AOCS standard method and those predicted by HATR/FTIR/PLS, respectively, in the calibration set or external validation set.
Results and Discussion
Low-molecular-weight liquid epoxy polyol esters or ethers from vegetable oils can be employed as polyols in polyurethane formulation. Usually, hydroxyl groups have been introduced through a two-step synthesis involving firstly the epoxidation of the unsaturated sites with formic acid and hydrogen peroxide, followed by epoxy ring opening with mono or polyfunctional alcohols, amino alcohols, or acids. Depending on the reaction conditions, polyols with high OH functionality (complete reaction) or epoxy polyol esters with remaining epoxy groups (partial conversion) are obtained.
In this work, epoxy polyol esters were prepared by “one-step” synthesis using the formic acid/H2O2 system. The hydroxylation reaction was carried out at constant temperature, 65 °C, and by increasing the reaction time it was possible to prepare soy polyols with different OH functionality, which were used as calibration standards and for external validation samples [5].
Figure 1 shows the FTIR and 1H-NMR spectra of the soy polyol with an OH value of 66.3 mg of KOH/g. In the FTIR spectrum, besides the appearance of a large band at 3,450 cm−1 assigned to the OH stretching band and two small bands at 875 and 920 cm−1 assigned to the epoxy groups, the disappearance of the 3,010 cm−1 band corresponding to the C–H stretching band of the C=C–H group indicates the formation of epoxy polyol esters.
In the 1H-NMR spectrum, the major changes were the appearance of hydrogen signals assigned to the formate group (8.15 ppm), to epoxy groups (2.8–3.2 ppm) and to hydroxyl groups (3.8–4.2 ppm). In the characteristic region of unsaturated bonds (5.2–5.5 ppm) only the signal corresponding to the hydrogen of the glycerol –CH2(R)–CH(R)–CH2(R)– group remains, which provides evidence for the absence of double bonds in the triacylglyceride molecule.
It is important to point out that there is not a homogeneous distribution of OH groups in epoxy polyol esters from vegetable oils. In fact, the OHV determined for each sample is an average distribution of OH groups present in the triacylglycerides, which are composed of glycerol triesters of different saturated and unsaturated fatty acids. This non-homogeneous distribution is responsible for the different properties and characteristics of vegetable polyols compared with petrochemical ones.
In this work, a total of 53 samples of soybean polyols were prepared, covering an analytical range of 3.5–125 mg of KOH/g. For chemometric evaluation, 36 samples were used for the modeling and 17 for external validation.
Figure 2 shows some HATR-FTIR absorption spectra of prepared samples. The spectra were quite homogeneous, and no outliers were identified in the PLS models developed.
Generally, noise and systematic behavior are undesirable features in the spectra. To minimize the noise of the calibration and validation spectra sets in PLS calibration models, the spectra were treated using multiplicative scattering correction (MSC) and compared with the original spectra set [19]. All models using MSC presented a decrease in the RMSECV (root mean square error of cross-validation) values.
Different calibration models were investigated to find the optimum model. The quality of these models was evaluated using the root mean square errors of calibration (RMSEC) and prediction (RMSEP). The first PLS model was developed using spectral ranges of 3,600–2,800, 1,800–1,680, 1,490–1,200 and 1,170–990 cm−1, auto-scaling, and MSC. Despite the excellent correlation coefficient (R 2 = 0.9998) obtained by the 16 latent variables, the minimal RMSEP was 6.511, which is very large by comparison with RMSEC = 0.5339, indicating over fitting.
To identify the best region of the spectrum where a good calibration model can be obtained, the RMSECV was determined for eight different sub regions using 1–15 latent variables, as shown in Fig. 3. The lowest RMSECV was found for the region between 1,400 and 1,200 cm−1, using 7, 8 or 9 latent variables. In the next step, the best region (1,400–1,200 cm−1) was combined with the other regions resulting in seven new calibration models. It was verified that an improvement of the RMSECV value occurred when more than one region was used. The process was repeated using 3 and 4 combined regions [20].
Table 1 shows four types of calibration model with different spectral regions and numbers of latent variables. The table contains the values for the correlation coefficient (R 2), the RMSEC and RMSEP values, and the number of latent variables (LV) used. The results show that very good correlation coefficients were obtained for all models.
We compared RMSEC and RMSEP values to further evaluate the quality of the models. If they were similar, i.e., RMSEC/RMSEP ratio close to 1.0, the model was considered to have good prediction capability [14]. Considering the correlation coefficients and the RMSEC/RMSEP ratio obtained, the model with the best predictive ability was model 3a, using 8 latent variables and the combined regions from 1,490 to 1,200 cm−1 and from 1,090 to 990 cm−1. Figure 4 shows the measured versus predicted plots for the calibration and external validation set, using eight latent variables (model 3a) in the PLS regression.
In conclusion, we have demonstrated that good calibration models for OHV determination in soybean polyols can be constructed using spectra obtained by HATR-FTIR and PLS regression. The best model, based on the correlation coefficient values (R 2, RMSEC, and RMSEV), was constructed with 53 samples (36 for calibration and 17 for external validation) covering a range of OHV values from 3.5 to 125.0 mg of KOH/g and using the ATR signal corrected by MSC. OHV determination was carried out in 2–3 min per sample, which is a major improvement over conventional wet chemical methods.
References
Guo A, Javni I, Petrovic ZS (2000) Rigid polyurethane foams based on soybean oil. J Appl Polym Sci 77:467–473
Petrovic ZS, Guo A, Zhang W (2000) Structure and properties of polyurethanes based on halogenated and nonhalogenated soy-polyols. J Polym Sci: Part A: Polym Chem 38:4062–4069
Huy H, Gao Y, Wang DN, Hu CP, Zu S, Vanoverloop L, Randall D (2002) Rigid polyurethane foam prepared from a rape seed oil based polyol. J Appl Polym Sci 84:591–597
Guo A, Cho YJ, Petrovic ZS (2000) Structure and properties of halogenated and nonhalogenated soy-based polyols. J Polym Sci: Part A: Polym Chem 38:3900–3910
Monteavaro LL, Da Silva EO, Costa APO, Samios D, Gerbase AE (2005) Polyurethane networks from formiated soy polyols: synthesis and mechanical characterization. J Am Oil Chem Soc 82:365–371
Parreira TF, Ferreira MMC, Sales HJS, Almeida WB (2002) Quantitative determination of epoxidized soybean oil using near-infrared spectroscopy and multivariate calibration. Appl Spectrosc 56:1607–1614
Al-Alawi A, van de Voort FR, Sedman J (2004) New FTIR method for the determination of FFA in oils. J Am Oil Chem Soc 81:441–446
Seedman J, Van de Voort FR, Ismail AA, Maes P (1998) Industrial validation of Fourier transform infrared trans and iodine value analyses of fats and oils. J Am Oil Chem Soc 75:33–39
Moh MH, Man YBC, van de Voort FR, Abdullah WJW (1999) Determination of peroxide value in thermally oxidized crude palm oil by near infrared spectroscopy. J Am Oil Chem Soc 76:19–23
Seedman J, Van de Voort FR, Ismail AA (1997) Upgrading the AOCS infrared trans method for analysis of neat fats and oil by Fourier transform infrared spectroscopy. J Am Oil Chem Soc 74:907–913
Russin TA, van de Voort FR, Sedman J (2004) Rapid Determination of oxidative stability of edible oils by FTIR spectroscopy using disposable IR cards. J Am Oil Chem Soc 81:111–116
Ratnayake WMN, Pelletier G (1996) Methyl esters from a partially hydrogenated vegetable oil is a better infrared external standard than methyl elaidate from the measurement of total trans content. J Am Oil Chem Soc 73:1165–1169
Borin A, Poppi RJ (2004) Multivariate quality control of lubricating oils using Fourier transform infrared spectroscopy. J Braz Chem Soc 15:570–576
Ferrão MF, Davanzo CU (2005) Horizontal attenuated total reflection applied to simultaneous determination of ash and protein contents in commercial wheat flour. Anal Chim Acta 540:411–415
Geladi P, Kowalski BR (1986) Partial least-squares regression: a tutorial. Anal Chim Acta 185:1–17
Brereton RG (2000) Introduction to multivariate calibration in analytical chemistry. Analyst 125:2125–2154
Official Methods and recommended practices of the Am Oil Chem Soc, 4th edn, Am Oil Chem Soc, Champaign, 1980
Official Methods and recommended practices of The Am Oil Chem Soc, 4th edn, Am Oil Chem Soc, Champaign, 1993, revised (1997)
Ferrão MF, Carvalho CW, Muller EI, Davanzo CU (2004) Simultaneous determination of ash content and protein in wheat flour using infrared reflection techniques and partial least-squares regression (PLS). Ciênc Tecnol Aliment 24:333–340
Sutter JM, Kalivas JH (1993) Comparison of forward selection, backward elimination, and generalized simulated annealing of variable selection. Microchem J 47:60–66
Acknowledgments
The authors are grateful to the Conselho Nacional de Desenvolvimento Científico e Tecnológico (CNPq) for financial support.
Author information
Authors and Affiliations
Corresponding author
About this article
Cite this article
Godoy, S.C., Ferrão, M.F. & Gerbase, A.E. Determination of the Hydroxyl Value of Soybean Polyol by Attenuated Total Reflectance/Fourier Transform Infrared Spectroscopy. J Amer Oil Chem Soc 84, 503–508 (2007). https://doi.org/10.1007/s11746-007-1067-z
Received:
Revised:
Accepted:
Published:
Issue Date:
DOI: https://doi.org/10.1007/s11746-007-1067-z