Abstract
It has been shown that the oxygen and nitrogen within the atmosphere of a double oxide film defect can be consumed by the surrounding Al melt. Experimentally determined reaction rates were used to construct a semi-empirical model to predict the change in volume with time of a bubble of air trapped in an Al melt, with the model including the diffusion of H from the metal into the bubble. Comparison with experimental results showed that the model predicted the change in volume well. The model was then used to estimate the duration of the internal atmosphere within double oxide film defects, which suggested that these would be consumed in a time of up to 3 minutes, depending upon assumptions made about the initial defect size.
Similar content being viewed by others
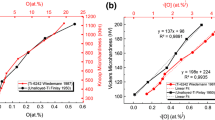
Avoid common mistakes on your manuscript.
Introduction
Aluminum alloy castings are increasingly commonplace in automotive and aerospace applications, and it is therefore essential that defects and potential failure mechanisms are fully understood if reliable castings are to be produced consistently. One such defect is the entrained double oxide film, identified by Campbell.[1] During the casting process, the oxidized surface of the liquid metal can fold over onto itself and become entrained in the bulk liquid metal, forming a doubled-over oxide film defect in which the internal surfaces are not bonded, but have a layer of gas trapped between them. This gas would have the composition of the mold atmosphere, but may be predominantly air. The formation and effects of these defects has been further discussed by Campbell in Reference 1.
In Nyahumwa et al.,[2] it was suggested that the air inside a double oxide film defect floating within an Al melt might be consumed gradually by reaction with the surrounding liquid metal (after an incubation period associated with the transformation from γ- to α-alumina), perhaps eventually leading to the internal oxide surfaces of the defect bonding together in some way. An analogue experiment to study this behavior was carried out, in which a silicon-nitride rod with a hole in one end was plunged into a melt of pure liquid Al, resulting in the trapping of an air bubble of known volume.[3,4] The change in the volume of the air bubble with time, as its contents reacted with the surrounding melt, was recorded using real-time X-ray radiography.
The results from this experiment showed that the O and N of the air bubble reacted with the surrounding melt to form Al2O3 and AlN, respectively. The rates of reaction were extracted from the change in air bubble volume with time obtained from digital video recordings of the X-ray image. It was also observed that, if the initial H content of the Al melt was greater than the equilibrium amount associated with the ambient atmosphere, H initially diffused into the trapped air bubble and caused its expansion, and extended the time taken for the volume of the air bubble to decrease.
A semi-empirical mathematical model has been developed to predict the behavior of this trapped air bubble in the liquid Al. The model has been used to estimate what effect changes in the ratio of the volume-to-surface area of a bubble would have on its lifetime, and then used to estimate the duration of the atmosphere within a double oxide film defect of an assumed initial size. The effect of different initial H contents of the melt has also been examined.
Mathematical Model of the Change in Bubble Volume
Discretization
A semi-empirical mathematical model of a cylindrical volume of air, undergoing reaction with a surrounding melt of liquid Al, was constructed, which included the diffusion of hydrogen within the metal and into and out from the cylindrical bubble. The model used an explicit finite difference solution to the diffusion equation in a cylindrical axisymmetric coordinate system as follows:[5]
where C is the concentration of hydrogen; D is the diffusion coefficient of hydrogen in liquid Al; t is time; and r and z are radial distance and height, respectively.
To derive discretization equations in a cylindrical coordinate system, the model was divided into several cylindrical finite difference elements with dimensions Δr, Δz, and 1 in directions r, z, and θ, respectively (Figure 1). The discretized equation for each element was then derived from Eq. [1] by an explicit finite difference method:
Finite difference control volume in axisymmetric cylindrical coordinates.[5]
Here, C p and C 0 p are the concentration of species in the element at present and previous time-steps, respectively. The terms C 0 E , C 0 W , C 0 N , and C 0 S are concentrations of species at neighboring grid points, east, west, north, and south of the element at the previous time-step, respectively, and a E , a W , a N , a S , and a P are given by
where r is the radial distance and D is the diffusion coefficient at the east, west, north, and south sides of the element, respectively.
Boundary Conditions
The boundary condition at the melt/air interface of the trapped bubble and the liquid Al was determined as follows. The relationship between the concentration of hydrogen in pure liquid aluminum, ([pctH]Al), and the partial pressure of hydrogen in the ambient atmosphere, P H, was determined by Ransley and Neufeld[6] to be
where T metal is the liquid metal temperature. Because the equilibrium constant of the reaction of Al with water vapor at 700 °C is very high (1.46 × 1042, calculated using data from Reference 7), each mole of water vapor in contact with an aluminum melt should turn to 1 mole of hydrogen; therefore, the boundary condition of the diffusion equation at the melt/air interface of the cylindrical bubble and the liquid Al can be obtained by substituting P H in Eq. [4] with P ws × H R , where P ws is the saturated water vapor pressure for the ambient atmosphere, and H R is the relative humidity.
To allow for the diffusion of hydrogen into the internal atmosphere of the cylindrical bubble, the hydrogen concentration of each air element in the model was converted to a partial pressure using Eq. [4], and the mean hydrogen partial pressure of the air elements in the bubble were taken to represent the overall hydrogen partial pressure of the entire cylindrical bubble, P HB .
The consumption rates of the oxygen and nitrogen in the trapped atmosphere were described by Eqs. [5] and [6], derived from experimental data obtained by studying the reduction in bubble volume with time in an Al melt with a low hydrogen content of about 0.1 mL/100 g.[3]
where R O and R N are the consumption rates of oxygen and nitrogen by reaction with liquid Al (in mole s−1 m−2); and f O and f N are the fraction of oxygen and nitrogen moles present in the atmosphere, respectively. The explicit finite difference model of the diffusion of hydrogen in aluminum was then coupled with these equations to model the rate of change of the oxygen, nitrogen, and hydrogen content in the atmosphere of the bubble.
Oxygen consumption rates reported in the literature are shown in Table I.[8–10] These were measured in an environment with an unlimited supply of oxygen, i.e., a constant fraction of oxygen equal to 0.2. The measurement of the initial oxygen consumption rate (when f O = 0.2) in the experiment was not possible due to the small delay in operating the equipment,[3] but extrapolation of Eq. [5] to f O = 0.2 produced an estimated initial consumption rate of oxygen of 8.45 × 10−6 mole s−1 m−2, comparable to the experimentally determined rates reported in Table I. No nitrogen consumption rates were found in the literature for comparison with the consumption rates used in the model.
Model
Initially, the volume and surface area in contact with the liquid metal, V air and S air, of the cylindrical air bubble were calculated. The initial partial pressure of hydrogen in the bubble atmosphere, P 0 HB, was calculated using Eq. [4] for a defined value of the initial hydrogen content of the aluminum, and (neglecting metallostatic pressure) the number of oxygen and nitrogen moles present in the bubble, n O and n N, respectively, were calculated using the following simple equations. (The temperature T air was assumed to be constant and equal to T metal, and the pressure P atm was assumed to be 1 bar):
where V M is the molar volume of air at temperature T air and pressure P atm, n air is the number of moles of air, and R is the universal gas constant. The presence of any argon in the atmosphere was neglected. The thermophysical data and other parameters used in the model are reported in Table II.
The discretized Eq. [2] was then used to calculate, at each time-step, the change in the concentration of hydrogen atoms in each element throughout the model and the amount of hydrogen entering or leaving the bubble. In addition, the amount of oxygen and nitrogen consumed in the trapped air bubble in each time-step was calculated using Eqs. [5] and [6].
From thermodynamic considerations, it was expected that the consumption of nitrogen by the liquid aluminum could only begin when almost all of the oxygen molecules in the atmosphere were consumed, but when this criterion was applied in the model, it led to unrealistically low oxygen consumption rates, because the oxygen content of the gas in the cylindrical bubble declined, and delayed the beginning of any reaction with nitrogen for unrealistically long times in the model. The experimental results suggested that nitrogen consumption began when the volume of the trapped air bubble was about 85 pct of its initial value. A molar fraction of oxygen of 3.8 pct was therefore chosen as a criterion after which consumption of nitrogen in the model began.
Based on the calculated n O, n N, and P HB, the internal pressure of the trapped air bubble was calculated using the following equation:
If P B were greater than P atm (1 bar), then the bubble was expanded to compensate for this increased pressure. This expansion was accounted for by adding one layer of air elements around the air bubble, although this meant that the least possible expansion that could be taken into account was determined by the dimensions of the elements. A premature expansion of the bubble caused the internal pressure to drop below the atmospheric pressure, and in this case, the program became unstable. The expansion step, therefore, was carried out only if the internal pressure of the bubble, after the calculated expansion, remained above atmospheric pressure, which caused the shape of the calculated curves to become stepped. The same algorithm was used to shrink the bubble when P B was less than P atm. After any expansion, P HB, P B , V air, and S air were recalculated.
To check the accuracy of the mathematical model, the predicted change in the volume of a trapped air bubble with time was compared to the volume change curves obtained from the experimental work (Reference 3). These curves are shown in Figures 2 and 3, for low and high initial hydrogen contents of 0.1 and 0.3 mL/100 g, respectively.
Figure 2 shows that the modeled curves for the experiments with low initial hydrogen contents were in good agreement with the experimental results, for bubbles of two different sizes. However, Figure 3 shows that, for experiments with high initial hydrogen contents, although the initial expansion of the bubble was predicted well, the modeled duration of the air bubble was less than the actual duration in the liquid aluminum by 25 pct for a cylindrical bubble with an initial height of 40 mm. The comparison for the experiment with high initial hydrogen content and an initial bubble height of 10 mm produced a smaller error in the estimation of the duration of the trapped air bubble, although the expansion of the bubble was not modeled well. However, considering the simplicity of the mathematical model and the many simplifying assumptions made, the model predicted the duration of a bubble of air in liquid aluminum, containing low and high initial hydrogen contents, with an error of 30 pct at most.
Results
Rate of Consumption of the Interior Atmosphere of a Double Oxide Film Defect
The experimental consumption rates for O and N (Eqs. [5] and [6]) were for a known volume of air undergoing reaction through a known interfacial area. In order to use these values to predict the lifetime of the volume of air assumed to be trapped in a double oxide film defect, it was necessary to relate the rate of reaction of the cylindrical bubbles to their volume and their surface area. The ratio of the volume of the atmosphere to the surface area over which reaction occurred is defined here as the modulus, M. By relating the modulus of the cylindrical air bubbles with the duration of their atmosphere, it was possible to extrapolate the model to the case of a double oxide film defect, with its much smaller volume of internal atmosphere, comparatively larger interfacial area, and hence smaller modulus.
Figure 4 shows the predicted effect of changing the modulus of the cylindrical air bubble on the duration of its atmosphere, estimated by the model, with an assumed initial hydrogen content of 0.1 mL/100 g. This showed that, as expected, the duration of the bubble atmosphere decreased as the initial size of the bubble decreased, with the data being fitted by a cubic equation:
where M is the modulus of the bubble in millimeters, calculated from its initial dimensions, and t d is the duration of the bubble in hours.
Modeled curves of the change in the volume of the trapped air bubble with time for bubbles with different initial moduli and an initial hydrogen content, H0, of 0.1 mL/100 g. This illustrates the stepwise change in the predicted bubble volume owing to the construction of the model. This graph also shows modeling of a bubble with a modulus (M) of 1.4 mm with two different element sizes, which showed no change in the predicted duration
Figure 5 shows the predicted duration of the atmosphere within air bubbles with different moduli and with different initial hydrogen contents of 0.1 and 0.3 mL/100 g. These results showed that the increase in the initial hydrogen content increased the duration of the bubble atmosphere in the liquid aluminum by about 180 pct. Equation [13] was derived from the data shown in Figure 5 and describes the duration of the atmosphere within a cylindrical air bubble of different moduli, in an Al melt, with an initial hydrogen content of 0.3 mL/100 g:
By the assumption that the rate of consumption of the oxygen and nitrogen in the air bubble in the experiments was similar to that in a double oxide film defect, and that this was controlled by the same mechanism (reasoned to be crack formation in the oxide film separating the atmosphere from the melt), Eqs. [12] and [13] can be used to estimate the lifetime of the interior atmosphere of a double oxide film defect. The initial dimensions of double oxide film defects in Al castings are not known, but one estimate[1] suggested dimensions of about 10 × 5 mm and a thickness of the internal trapped atmosphere of 5 μm. This corresponds to a volume-to-surface area ratio, or modulus, of 2.5 × 10−6 mm. If a much wider range of possible double oxide film thicknesses is taken, say, from between 5 nm and 40 μm, a range of possible times in which double oxide film defects can lose their interior atmosphere can be obtained.
Equation 12 suggests that the duration of the atmosphere within a double oxide film defect, with these assumed dimensions, with a low initial hydrogen in the melt (0.1 mL/100 g), would be from 7 to 77 seconds, respectively. If the melt had an initial hydrogen content of 0.3 mL/100 g, Eq. [13] suggested that these times would be increased to 13 to 144 seconds, respectively.
Effect of Rejected Hydrogen during Solidification
Excess hydrogen is rejected at an advancing solidification front, and the overall concentration of hydrogen in the liquid Al can be increased, to possibly more than the theoretical maximum solubility (0.69 mL/100 g at 660 °C[7]). Zou et al.[11] suggested that a local concentration as high as 1.2 mL/100 g could occur. To find the influence of very high hydrogen concentrations on double oxide film defects, the behavior of a cylindrical bubble of air with a diameter of 5 mm and a height of 2.5 mm was modeled with hydrogen concentrations of between 0.1 and 1.05 mL/100 g. (The modeling of bubbles with smaller dimensions would have taken an excessively long time.) The result of this modeling is shown in Figure 6.
Each curve ended when all of the oxygen and nitrogen in the air bubble were consumed by reaction with the surrounding liquid aluminum. It can be seen that when the hydrogen concentration in the melt was 0.5 to 0.75 mL/100 g in the model, the diffusion of hydrogen into the bubble compensated for the decrease in bubble pressure caused by the consumption of oxygen and nitrogen, and therefore it was predicted that the volume of the bubble did not change with time. When the hydrogen content of the liquid metal was 0.8 mL/100 g or more, the diffusion of hydrogen into the bubble overcame the decrease in pressure caused by the oxidation and nitridation reactions and the predicted bubble size quickly expanded; consequently, the oxygen and nitrogen contents of the air bubble were consumed more quickly, due to the increase in the bubble surface area, leading to a greater interfacial area for reaction.
It is possible that, in the presence of very high hydrogen contents, real oxidation and nitridation reaction rates are different from the values that were used in the mathematical model, but Figure 6 suggests that the influence of very high hydrogen contents on the modeled behavior of the air bubble is so strong that variations in reaction rates would not have a great effect on the modeled behavior of the bubble. The model estimated a 10,000 and 100,000 fold increase in the volume of the bubble before the oxygen and nitrogen within it were consumed, if the initial hydrogen contents were 0.8 and 1.05 mL/100 g, respectively.
Figure 7 shows an estimation from the model of the change in volume of a double oxide film defect with time, if it were maintained in a 50 g melt of pure aluminum with initial hydrogen contents of between 0.8 to 1.05 mL/100 g. The initial dimensions of the modeled double oxide film were 5 mm × 5 mm × 40 nm, giving an initial volume of 0.001 mm3 (and modulus of 2 × 10−5 mm). It was estimated that the atmosphere within the double oxide film defect would expand to a sphere with a diameter of about 1 to 4 mm with initial hydrogen contents of 0.8 to 1.05 mL/100 g, respectively, over 60 seconds. These hydrogen contents correspond to the high values that might locally occur during solidification, and, interestingly, the lowest part of the range of the estimated diameters is comparable to the diameters of pores in Al castings, identified as being caused by hydrogen gas precipitation.
Discussion
To summarize, the model of the consumption of the air in a trapped bubble in liquid Al suggested that the oxygen and nitrogen trapped in a double oxide film defect should be consumed quickly, within about 3 minutes, and only the residual argon from the air (about 1 vol pct) would remain in the defect after this time. The two oxide layers should then be in contact with each other, at least at several points, and if the metal is held in the liquid state long enough, it is possible that partial bonding can take place between the internal oxidized surfaces, as was suggested by Nyahumwa et al.[12]
Consideration of the estimated durations of the double oxide film defect atmosphere and typical solidification times of castings suggest that double oxide films may still be in the process of having their interior atmosphere consumed as the castings are solidifying. It would therefore be expected that any oxide film defects would have a significant effect on mechanical properties. Once the internal atmosphere was consumed, the behavior of the oxide film defect may change, for example, the surfaces may be joined together in some way, perhaps reducing the effect of the oxide film defect on mechanical properties. However, the rejection of excess hydrogen from the melt during solidification would cause the double oxide film defect to expand, and the defects would still cause variable and reduced mechanical properties.
Conclusions
-
1.
A semi-empirical mathematical model of the reaction of the atmosphere of a trapped air bubble with liquid aluminum, which included the diffusion of hydrogen, has been constructed.
-
2.
The model suggested that the oxygen and nitrogen in the atmosphere of a double oxide film defect in an aluminum melt may be consumed in less than about 3 minutes, depending on its dimensions, specifically, volume and surface area.
-
3.
The model produced additional supporting evidence that a double oxide film defect could act as an initiation site for the growth of hydrogen gas pores during solidification of Al castings.
References
J. Campbell: Castings, 2nd ed., Butterworth-Heinemann, Oxford, United Kingdom, 2003, pp. 20–69
C. Nyahumwa, N.R. Green, J. Campbell: Metall. Mater. Trans. A, 2001, vol. 32A, pp. 349–58
R. Raiszadeh, W.D. Griffiths: Metall. Mater. Trans. B, 2006, vol. 37B, pp. 865–71
R. Raiszadeh, W.D. Griffiths: World Foundry Congress, Harrogate International Centre, Harrogate, United Kingdom, 2006, pp. 26/1–26/10
J. Crank: The Mathematics of Diffusion, 2nd ed., Oxford Clarendon Press, Oxford, United Kingdom, 1979, pp. 69–88
C.E. Ransley, H. Neufeld: J. Inst. Met., 1948, vol. 74, pp. 599–621
E.A. Brandes, G.B. Brook: Smithells Metals Reference Book, 7th ed., Butterworth-Heinemann, Oxford, United Kingdom, 1999, p. 12-2
W.C. Sleppy: J. Electrochem. Soc., 1961, vol. 108 (12), pp. 1097–1102
W. Thiele: Aluminium, 1962, vol. 38, pp. 707–15
S. Impey, D.J. Stephenson, J.R. Nicholls: Int. Conf. on the Microscopy of Oxidation, Institute of Materials, Selwyn College, University of Cambridge, Cambridge, United Kingdom, 1993, pp. 323–37
J. Zou, S. Shivkumar, D. Apelian: AFS Trans., 1990, vol. 178, pp. 871–78
C. Nyahumwa, N.R. Green, J. Campbell: AFS Trans., 1998, vol. 58, pp. 215–23
Acknowledgments
The authors thank Professor J. Campbell for helpful discussions in connection with the work; Mr. A. Caden for his technical support; and the Ministry of Science, Research and Technology of the Islamic Republic of Iran for its financial support.
Author information
Authors and Affiliations
Corresponding author
Additional information
Manuscript submitted May 4, 2007.
Rights and permissions
About this article
Cite this article
Raiszadeh, R., Griffiths, W. A Semi-empirical Mathematical Model to Estimate the Duration of the Atmosphere within a Double Oxide Film Defect in Pure Aluminum Alloy. Metall Mater Trans B 39, 298–303 (2008). https://doi.org/10.1007/s11663-008-9142-x
Published:
Issue Date:
DOI: https://doi.org/10.1007/s11663-008-9142-x