Abstract
Next generation of advanced hard coatings for tribological applications should combine the advantages of hard wear resistant coatings with low-friction films. In this study, the tribological behaviour of vanadium pentoxide (V2O5) single-layer as well as VN–V2O5 bi-layer coatings was investigated in the temperature ranging between 25 and 600 °C. For VN–V2O5 bi-layer coatings, the V2O5 top-layers were deposited by dc and bipolar-pulsed dc reactive magnetron sputtering, where the V2O5 phase shows preferred growth orientation in (200) and (110), respectively. The V2O5 single-layer coatings were prepared by dc reactive magnetron sputtering with a substrate bias of −80 V which leads to a preferred (200) growth orientation. Tribological properties were evaluated using a ball-on-disc configuration in ambient air with alumina balls as counterpart. The structure of the as-deposited films and eventual changes after tribometer testing were identified using X-ray diffraction, Raman spectroscopy and scanning electron microscopy. The friction coefficient of VN–V2O5 bi-layer coatings deposited in dc and pulsed dc mode decreases from room temperature to 600 °C, where the pulsed dc VN–V2O5 coatings have a significantly lower coefficient of friction over the whole testing temperatures reaching a value of 0.28 at 600 °C. Up to 400 °C, V2O5 single-layer coatings showed almost the same coefficient of friction as pulsed dc VN–V2O5 bi-layer coatings but reached a value of 0.15 at 600 °C. It seems that thermal activation of crystallographic slip systems is necessary for V2O5 films to show a low-friction effect.
Similar content being viewed by others
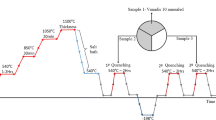
Avoid common mistakes on your manuscript.
1 Introduction
Over the last few years, oxides and their combinations have attracted interest for tribological applications due to their potential as low-friction coatings in the high-temperature range [1–9]. In an earlier study [9], we reported on the beneficial effect of vanadium oxide formation on tribological properties of V and VN coatings. It could also be demonstrated that, to achieve a low-friction effect and at the same time sufficient wear resistance, an oxide layer of overcritical thickness has to be formed on the coating surface, which seems to be stable and efficient after reaching certain oxidation temperature.
Recently, we have studied in detail the structure and surface morphology of V2O5 thin films deposited by reactive magnetron sputtering at different deposition temperatures [10]. Investigations on amorphous and polycrystalline V2O5 coatings deposited by dc and bipolar-pulsed dc magnetron sputtering showed the role of deposition method as well as substrate temperature on structure, preferential orientation of the V2O5 phase and mechanical properties [11]. In the literature, several investigations on structural and optical properties of V2O5 films prepared by various deposition techniques and under varying deposition conditions can be found [10–18]. However, with the exception of a few investigations [5, 19], the tribological properties of V2O5 films, particularly at elevated temperatures, have not yet been reported in detail. Therefore, the purpose of the present study was to prepare VN–V2O5 bi-layer coatings by dc and bipolar-pulsed dc reactive magnetron sputtering with V2O5 top-layers having a sufficient thickness and to study their tribological properties. We also characterized the tribological behaviour of V2O5 single-layer films during high-temperature tests to verify their suitability as low-friction coatings.
2 Experimental Details
The coatings investigated in this study were deposited by means of reactive magnetron sputtering on high-speed steel discs (DIN 1.3343, AISI M2), which were quenched and tempered to a hardness of 65 HRC. After evacuating the vacuum chamber down to a pressure of 8 × 10−4 Pa, the ground and polished substrates were ultrasonically pre-cleaned with acetone and ethanol and ion etched within the deposition chamber prior to deposition. The films were deposited from three V targets (ø 50.8 × 6.35 mm2) mounted to a cluster of three unbalanced magnetrons (AJA cluster with A320-XP magnetrons), focused to the substrate holder (AJA SHQ400). Depending on the investigations foreseen, dc and bipolar-pulsed dc magnetron sputtering were applied in a gas mixture of Ar + O2 or Ar + N2, respectively. The target current was set to 0.35 A at each magnetron for all experiments. The substrates were positioned parallel to the magnetron cluster in a distance of 7 cm and were rotated at ∼10 rpm during deposition to obtain uniform films. In all deposition runs, the total gas pressure was kept constant at 0.28 Pa, whereas for VN and V2O5 coatings the N2 and O2 partial pressure was 15 and 21% of the total pressure, respectively. In the case of the VN–V2O5 bi-layer coatings, the VN layer was deposited in dc mode at 500 °C while the V2O5 top-layer was grown in dc and pulsed dc (MKS RPG-50 bipolar-pulsed dc power supplies, 100 kHz pulsing frequency and 16% duty cycle) modes, respectively, at 300 °C and floating potential. These two different modes for depositing V2O5 top-layer were used in order to elucidate the dependency between friction coefficient and frequency-stimulated structural differences of the films. The V2O5 single-layer was prepared by dc reactive magnetron sputtering at 300 °C with a substrate bias potential of −80 V. The average thickness of the VN–V2O5 bi-layer coatings was 4 μm (2 μm VN/2 μm V2O5), while the V2O5 single-layer coating had an average thickness of 2 μm.
The film structure was determined by X-ray diffraction (XRD) analysis using a Siemens D500 diffractometer in Bragg-Brentano configuration and Cu–Kα radiation. Dry sliding experiments were conducted using coated high-speed steel discs in ambient air starting from room temperature (RT, ∼25 °C) up to 600 °C using a CSM THT high-temperature ball-on-disc tribometer and alumina balls of 6 mm diameter as counterpart. For all coating systems, the sliding speed was kept constant at 0.1 m/s and the wear track radius at 7 mm, while the sliding distance was 50 m. A load of 1 N was used for all experiments. After tribometer testing, the wear tracks on the coatings were characterized using an optical 3-D white light profiling system (Wyko NT 1000). Wear tracks and surfaces of the samples were examined using XRD, Raman spectroscopy (Horiba Jobin-Yvon LabRAM Raman Microscope, He–Ne laser, λ = 632.8 nm) and scanning electron microscopy (SEM, Zeiss EVO 50) to characterize the changes in surface structure and composition after ball-on-disc testing at different temperatures.
3 Results and Discussion
Figure 1 presents XRD patterns of the investigated coatings in the as-deposited state. The patterns are presented in a diffraction angle range between 12 and 33° to show the preferential orientation of the V2O5 phase formed. The XRD pattern of the V2O5 single-layer deposited in dc mode at −80 V substrate bias (Fig. 1a) indicates the presence of polycrystalline α-V2O5 with a preferred (200) orientation (cf. JCPDS file 01-077-2418). The VN–V2O5 bi-layer coating deposited in dc mode (see Fig. 1b) shows no significant differences in the XRD pattern compared to the V2O5 single-layer, while the growth orientation of the pulsed dc VN–V2O5 coating (Fig. 1c) changes due to its different deposition condition. In this case, the peak at 2θ = 26.153° dominates, indicating that the pulsed dc VN–V2O5 coating grows in a preferred (110) orientation. More details on the effect of deposition conditions on structural characteristics of dc and pulsed dc sputtered V2O5 single-layer films can be found in our previous publication [11]. There, it was shown that V2O5 films deposited in pulsed dc mode grow with preferred (110) and (001) orientation. Here, it seems that the VN base-layer favours the growth of the V2O5 phase in (110) direction. XRD single-line profile analysis employing the Pseudo–Voight method [20] yields a mean coherently diffracting domain size of the V2O5 phase of 21 nm for the V2O5 single-layer, 40 nm for the dc sputtered VN–V2O5 and 13 nm for the pulsed dc VN–V2O5 bi-layer along (200). Applying the Pseudo–Voight method for the (110) orientation indicates a mean domain size of 21 nm for the V2O5 single-layer, 15 nm for the dc VN–V2O5 and 37 nm for the pulsed dc VN–V2O5 bi-layer coatings. Structural investigations by XRD and Raman spectroscopy of the films after tribometer testing up to 600 °C reveal no detectable structural changes compared to the as-deposited state. The results suggest that all single- and bi-layer coatings are stable and remain unchanged also after exposure in ambient air up to 600 °C.
Figure 2 shows the average friction coefficient investigated by ball-on-disc tests against alumina at different temperatures. It is obvious that the changes in structure and different preferential growth orientation of the coatings depending on the deposition mode influence the value of the friction coefficient. The results show that the pulsed dc VN–V2O5 coatings to have a significantly lower friction coefficient over the whole temperature range compared to the dc sputtered VN–V2O5 coatings. In the case of dc sputtered VN–V2O5 coatings, the coefficient of friction increases from ∼0.57 at RT to ∼0.63 at 300 °C and decreases again with further increase in test temperature. As no significant structural changes could be observed by XRD and Raman measurements after tribometer testing up to 600 °C, the increased friction coefficient at 300 °C can be attributed to changes occurring at the contacting sliding surfaces, presumably due to the interaction of wear particles with both surfaces in contact. The pulsed dc bi-layer coatings show a continuous decrease of the friction coefficient to a low value of ∼0.28 at 600 °C (see Fig. 2). The considerable reduction of the friction coefficient to ∼0.39 at 300 °C compared to RT indicates presumably the earlier onset of thermal activation of slip processes along easy shearable crystallographic planes compared to those deposited in dc mode. This might be related to the (110) preferred growth orientation of the pulsed dc VN–V2O5 films. As reported in our previous work, there is a transition from amorphous to polycrystalline growth for V2O5 films deposited by dc magnetron sputtering with increasing deposition temperature [10]. In order to illuminate the friction coefficient further, dry sliding tests of the dc sputtered VN–V2O5 coatings with an amorphous V2O5 top-layer (deposited at RT [10]) were also investigated. It is worth mentioning that no remarkable changes in the friction coefficient compared to dc sputtered VN–V2O5 coatings with polycrystalline V2O5 top-layer (deposited at 300 °C) could be observed. In the case of the V2O5 single-layer deposited in dc mode, the friction coefficient observed at RT is almost identical to the dc sputtered VN–V2O5 bi-layer. However, the friction values of the V2O5 single-layer above 300 °C are clearly lower compared to the VN–V2O5 bi-layer deposited by dc sputtering. As the preferred orientation in both coating systems is (200), the decrease in friction coefficient might be attributed to the different structure of single-layer V2O5 films due to the applied substrate bias [21]. The friction coefficient decreases from ∼0.55 at RT to ∼0.39 at 300 °C and reaches its lowest value of 0.15 at 600 °C.
An interpretation of the low-friction coefficient appearing at 600 °C requires further investigations. According to the XRD patterns of all coatings after testing at 600 °C, grain coarsening occurs during the test. Applying the Pseudo–Voight method for the (200) orientation for both dc sputtered films reveals that the mean domain size of the V2O5 single-layer increases to 500 nm while that of the bi-layer increases to 262 nm. In the case of the pulsed dc sputtered bi-layer film, the mean domain size increases to 211 nm along (110) orientation.
Local melting of the V2O5 phase due to high flash temperatures in the sliding contact and thus liquid lubrication could also contribute to the low-friction effect. However, SEM investigations did not give any evidence for the dendritic structure observed on oxidized vanadium containing nitrides [7, 8]. We also investigated the surface morphology of the single-layer V2O5 and VN–V2O5 bi-layer coatings after dry sliding tests at different temperatures by SEM. The results indicate a modification of the surface morphology of all investigated coatings after testing at 600 °C. Figure 3 illustrates the top-view SEM micrographs of V2O5 single-layer coatings after dry sliding tests at RT, 300 and 600 °C outside of the wear track. Single-layer V2O5 coatings show after testing at 300 °C a granular structure similar to the as-deposited state indicated in Fig. 3a, while the surface morphology of the coating changes to a plate-like structure as the test temperature is increased to 600 °C. According to cross-sectional SEM analysis, this phenomenon only occurs on the surface of the coatings and does not apply for the total coating thickness. The change in the surface morphology might be another reason for the reduction of the friction coefficient for all investigated coatings with increasing testing temperature. However, since the coefficient of friction of the single-layer and bi-layer coatings after the dry sliding tests at 600 °C is different, this can obviously not be the only factor determining the resulting friction coefficient.
It has been mentioned before that grain coarsening takes place at elevated temperatures. Assuming that deformation of the film plays a role in determining the resulting friction coefficient (in accordance with the theory of velocity accommodation of Berthier et al. [22]), it is plausible that a coarsened structure, which deforms easier, e.g. by shearing of crystallographic planes, yields a lower friction coefficient. Also the orientation of the films should be related to the deformation mechanism, since the slip systems that might be activated depend on the orientation. Both bi-layer coatings investigated (sputtered in pulsed dc and dc mode, respectively) show comparable grain sizes after thermal exposure to 600 °C. The difference in the friction coefficient should thus mainly be related to the different orientation of the films. In case of the V2O5 single-layer, the resulting friction coefficient might be determined not only by the orientation (which is similar to the dc sputtered bi-layer film) but also by the coarsened structure of the film. This mechanism might also be effective at lower temperatures since testing at 300 °C already represents a homologous temperature of ∼0.6 for V2O5. It is also worth mentioning that, according to XRD single-line profile analysis, the biased single-layer V2O5 film shows a more pronounced coarsening than the bi-layer coatings with increasing test temperature. Employing the Pseudo–Voight method revealed an increase in the mean domain size of the single-layer V2O5 from 21 nm at RT to ∼39 nm at 300 °C, while the mean domain size in the case of the bi-layer coatings changes only slightly. Summing up, grain size, surface morphology and growth orientation might be determinant for the friction coefficient of sputtered V2O5 films.
Two-dimensional surface profiles of the wear tracks of the coatings after tribometer testing at RT and 600 °C are shown in Fig. 4. For the dc and pulsed dc sputtered VN–V2O5 bi-layers, the predominant wear mechanism at RT is abrasion as evidenced by the deep grooves with a wear track depth of ∼2.2 μm. In this case, the V2O5 layer is completely worn trough while the hard VN layer remains intact after ball-on-disc testing. The V2O5 single-layer failed during the test at RT. The wear mechanism in this case is the same, and the depth of the wear track is ∼2 μm, as shown in Fig. 4a. At a testing temperature of 300 °C, all investigated coatings failed. After increasing the temperature to 400 °C, most areas of the wear tracks of all investigated coatings show no significant material removal. However, in some small regions grooves with 1.3–2.4 μm depth could be observed. Figure 5 presents a SEM micrograph of the wear track of the dc sputtered VN–V2O5 bi-layer after dry sliding at 400 °C as an example for the above-mentioned behaviour. Figure 4b shows the 2-D profiles of the wear tracks of the V2O5 single-layer and the VN–V2O5 bi-layers deposited in dc and pulsed dc mode, respectively, after dry sliding tests at 600 °C. This further increase in testing temperature leads to a reduction of the depth of the wear track and to transfer of wear particles, as evidenced by the positive wear shown in Fig. 4b. As clearly shown in Fig. 4b, the VN–V2O5 bi-layer deposited by pulsed-dc magnetron sputtering has a better wear performance compared to both, the dc sputtered VN–V2O5 bi-layer and V2O5 single-layer coatings. It is assumed that the better friction and wear performance of the pulsed dc V2O5 coating is attributed to its (110) growth orientation.
4 Conclusions
VN–V2O5 bi-layer coatings grown by dc and pulsed dc reactive magnetron sputtering and V2O5 single-layers synthesized by dc reactive magnetron sputtering have been investigated in the temperature ranging between 25 and 600 °C to characterize the influence of sputtering mode, structure and growth orientation of the films on their tribological performance. Structural investigations using XRD revealed that the V2O5 single-layer and the V2O5 top-layer of dc sputtered VN–V2O5 coatings have preferred (200) orientation, while the V2O5 top-layer of pulsed dc VN–V2O5 coatings shows preferred (110) growth. According to XRD and Raman analysis, all single- and bi-layer coatings investigated in this study are stable and remain unchanged during high-temperature dry sliding tests in ambient air up to 600 °C. However, coarsening of the V2O5 phase occurs as temperature rises, where the V2O5 single-layer shows the most pronounced coarsening. Furthermore, a considerable change in the surface morphology of all investigated coatings from granular to plate-like structure after dry sliding test at 600 °C could be observed. Ball-on-disc experiments against alumina show that the friction coefficient of all investigated coatings decreases with increasing temperature, where thermally activated processes seem to be necessary to promote low friction due to easy shearing of lattice planes. Growth orientation and film structure seem to determine this onset temperature, and both together with surface morphology determine the frictional behaviour. Furthermore, also the wear resistance is improved with increasing testing temperature. Finally, it can be concluded that a combination of a well-adherent VN base-layer with a V2O5 top-layer is a promising candidate for coating systems providing low friction with sufficient wear resistance over a wide temperature range.
References
Erdemir, A.: A crystal-chemical approach to lubrication by solid oxides. Trib. Lett. 8, 97–102 (2000)
Greenwood, O.D., Moulzolf, S.C., Blau, P.J., Lad, R.J.: The influence of microstructure on tribological properties of WO3 thin films. Wear 232, 84–90 (1999)
Gardos, M.N.: Magnéli phases of anion-deficient rutile as lubricious oxides. Part I. Tribological behaviour of single-crystal and polycrystalline rutile (TinO2n-1). Trib. Lett. 8, 65–78 (2000)
Lugscheider, E., Knotek, O., Bärwulf, S., Bobzin, K.: Characteristic curves of voltage and current, phase generation and properties of tungsten- and vanadium-oxides deposited by reactive d.c.-MSIP-PVD-process for self-lubricating applications. Surf. Coat. Technol. 142–144, 137–142 (2001)
Lugscheider, E., Knotek, O., Bobzin, K., Bärwulf, S.: Tribological properties, phase generation and high temperature phase stability of tungsten- and vanadium-oxides deposited by reactive MSIP-PVD process for innovative lubrication applications. Surf. Coat. Technol. 133–134, 362–368 (2000)
Gassner, G., Mayrhofer, P.H., Kutschej, K., Mitterer, C., Kathrein, M.: A new low friction concept for high temperatures: Lubricious oxide formation on sputtered VN coatings. Tribol. Lett. 17(4), 751–756 (2004)
Franz, R., Neidhardt, J., Sartory, B., Kaindl, R., Tessadri, R., Polcik, P., Derflinger, V.H., Mitterer, C.: High-temperature low-friction properties of vanadium-alloyed AlCrN coatings. Tribol. Lett. 23(2), 101–107 (2006)
Fateh, N., Fontalvo, G.A., Gassner, G., Mitterer, C.: Influence of high-temperature oxide formation on the tribological behaviour of TiN and VN coatings. Wear 262, 1152–1158 (2007)
Fateh, N., Fontalvo, G.A., Gassner, G., Mitterer, C.: The beneficial effect of high-temperature oxidation on the tribological behaviour of V and VN coatings. Tribol. Lett. 28, 1–7 (2007)
Fateh, N., Fontalvo, G.A., Cha, L., Klünsner, T., Hlawacek, G., Teichert, C., Mitterer, C.: Synthesis-structure relations for reactive magnetron sputtered V2O5 films. Surf. Coat. Technol. 202, 1551–1555 (2008)
Fateh, N., Fontalvo, G.A., Mitterer, C.: Structural and mechanical properties of dc and pulsed dc reactive magnetron sputtered V2O5 films. J. Phys. D: Appl. Phys. 40, 7716–7719 (2007)
Ramana, C.V., Hussain, O.M., Srinivasulu Naidu, B., Reddy, P.J.: Spectroscopic characterization of electron-beam evaporated V2O5 thin films. Thin Solid Films 305, 219–226 (1997)
Julien, C., Guesdon, J.P., Gorenstein, A., Khelfa, A., Ivanov, I.: The influence of substrate material on the growth of V2O5 flash-evaporated films. Appl. Surf. Sci. 90, 389–391 (1995)
Gies, A., Pecquenard, B., Benayad, A., Martinez, H., Gobeau, D., Fuess, H., Levasseur, A.: Effect of total gas and oxygen partial pressure during deposition on the properties of sputtered V2O5 thin films. Solid State Ionics 176, 1627–1634 (2005)
Lee, S.H., Cheong, H.M., Seong, M.J., Liu, P., Tracy, C.E., Mascarenhas, A., Pitts, J.R., Deb, S.K.: Raman spectroscopic studies of amorphous vanadium oxide thin films. Solid State Ionics 165, 111–116 (2003)
Meng, L.J., Silva, R.A., Cui, H.N., Teixeira, V., dos Santos, M.P., Xu, Z.: Optical and structural properties of vanadium pentoxide films prepared by d.c. reactive magnetron sputtering. Thin Solid Films 515, 195–200 (2006)
Lim, S.P., Long, J.D., Xu, S., Ostrikov, K.: Nanocrystalline vanadium oxide films synthesized by plasma-assisted reactive rf sputtering deposition. J. Phys. D: Appl. Phys. 40, 1085–1090 (2007)
Fang, G.J., Liu, Z.L., Wang, Y., Liu, Y.H., Yao, K.L.: Synthesis and structural, electrochromic characterization of pulsed laser deposited vanadium oxide thin films. J. Vac. Sci. Technol. A 19, 887–892 (2001)
Gulbińnki, W., Suszko, T., Sienicki, W., Warcholiński, B.: Tribological properties of silver-and copper-doped transition metal oxide coatings. Wear 254, 129–135 (2003)
De Keijser, T.H., Langford, J.I., Mittemeijer, E.J., Vogels, A.B.P.: Use of the Voigt function in a single-line method for the analysis of X-ray diffraction line broadening. J. Appl. Crystallogr. 15, 308–314 (1982)
Petrov, I., Barna, P.B., Hultman, L., Greene, J.E.: Microstructural evolution during film growth. J. Vac. Sci. Technol. A 21, 117–128 (2003)
Berthier, Y., Godet, M., Brendle, M.: Velocity accommodation in friction. Tribol. Trans. 32, 490–496 (1989)
Acknowledgements
This work was supported by the Austrian NANO Initiative via a grant from the Austrian Science Fund FWF within the project “LowFrictionCoatings”. The assistance of Daniel Kiener for SEM investigations is kindly appreciated.
Author information
Authors and Affiliations
Corresponding author
Rights and permissions
About this article
Cite this article
Fateh, N., Fontalvo, G.A. & Mitterer, C. Tribological Properties of Reactive Magnetron Sputtered V2O5 and VN–V2O5 Coatings. Tribol Lett 30, 21–26 (2008). https://doi.org/10.1007/s11249-008-9307-4
Received:
Accepted:
Published:
Issue Date:
DOI: https://doi.org/10.1007/s11249-008-9307-4