Abstract
Efficient lubrication is essential for synovial joint mobility in both health and disease. It is well known that extremely low friction is required for proper functioning of synovial joints. In several medical treatments, bio-lubricants are injected into human joints to maintain their proper functioning. In the course of developing and screening such bio-lubricants, it is important to measure their effect under conditions similar to the ones in vivo. To this end, a first attempt was made to test the friction of two slices of human articular cartilage sliding over each other under various working conditions in the presence of different lubricating fluids. The results can be used for future research in the field of joint lubrication.
Similar content being viewed by others
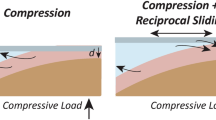
Avoid common mistakes on your manuscript.
Introduction
The human body has 143 different joints that connect bones of the skeleton to one another. Of the majority of joints are the synovial ones, which usually allow free and sometimes extensive movement between the bones involved [1]. Human synovial joints have to withstand complex, varied and often harsh loading regimes, been subjected to both dynamic and static loads under conditions of sliding and rolling [2]. Peak resultant forces across human hip may reach seven times body weight during normal walking and the maximum contact pressure in normal hip can reach 3 MPa [3].
The human joint is a self-acting and dynamically load-bearing structure that uses a porous and elastic biomaterial (e.g. articular cartilage) as well as a highly non-Newtonian lubricant (e.g. synovial fluid) for its functioning. Relative motion between two surfaces in contact is characterized by frictional forces and wear of one surface or both [4]. The friction coefficient is affected by the mechanical properties of the materials in contact, the operating conditions and the type of lubricant (if any) in the contact interface [5].
It is well known that human synovial joints function with an extremely low friction coefficient (∼0.02) [6]. Degradation of either part of the synovial fluid–articular cartilage system leads to increased friction, wear [3] and reduction of mobility [5]; degeneration of cartilage is characterized by softening and fibrillation [7] that may lead to joint pain. In the course of developing new nano-particles (liposomes) lubricant additives that may reduce joint friction and prevent or even cure joint diseases it became necessary to evaluate various bio-lubricants as potential carriers for the nano-particles. To this end a rational human joint friction test was developed using a human cartilage-on-cartilage setup.
Many investigators [2,8–17] have measured the friction coefficient of articular cartilage (from animal models) against different surfaces under different operating conditions in order to study the lubrication mechanism in joints. They found that sliding velocity, level and duration of load, as well as the type of lubricant affect the friction coefficient. Experiments measuring the frictional forces on the entire joint are very cumbersome; therefore most experiments were carried out on small and flat specimens since it is difficult to calculate the friction coefficient for a non-flat shaped area [6]. Most of the work concerning joint lubrication uses cartilage-on-metal, cartilage-on-ceramic and recently animal cartilage-on-cartilage setups (table 1); however, except for a few pendulum machine tests of an entire human joint e.g. [3,18,19], no fundamental work has been done yet using human cartilage-on-cartilage specimens.
Friction of animal cartilage surfaces was studied, for example, by sliding a cartilage of an adult rat femur against a stainless steel plate in the presence or absence of synovial fluid [2]. It was found that the surface layer on the cartilage, though small in dimension (less than 1 μm in depth), [2] is responsible for the lubrication; in the absence of synovial fluid, this effect is limited in duration. Cartilage beneath the surface layer has poor lubrication properties. Synovial fluid can act synergistically with a cartilage surface to achieve extremely low friction coefficient (∼0.02), [6]; lubrication provided by the cartilage surface becomes less effective at loads higher than the body weight; lubrication by the cartilage surface is impaired by low temperatures.
Murakami et al., [8], using a pig cartilage-on-metal model, showed that the lubrication mode changes from a full fluid film to mixed or boundary lubrication depending on the severity of the operating conditions. They also found that the friction coefficient is affected by the concentration and viscosity of the lubricants used. Friction of bovine articular cartilage-on-cartilage and cartilage-on-metal was measured by Forster and Fisher [10] using synovial fluid and Ringer’s solution as lubricating fluids. Synovial fluid significantly reduced the friction compared to Ringer’s solution in the bovine cartilage-on-cartilage model and was not as effective for the bovine cartilage-on-metal model. For the cartilage-on-metal model, the friction coefficient rose with increasing dwell time (time under which stationary loading is exerted on the tissue prior to sliding). They also observed [11] higher static friction coefficient upon un-loading re-loading the cartilage compared to continuous loading. Static friction coefficient of femoral condyle in canine stifles was measured at different dwell times [12]. It was found that the mean value of the static friction coefficient increased sharply from 0.012 at zero dwell time to 0.313 at a dwell time of 30 min. For comparison, the friction coefficient of femoral condyles on-glass plate measured for the same dwell times were 0.005 and 0.457, respectively.
Malcom [14] tested plugs from bovine humeral head against a glenoid surface under a continuously rotating articulation. He found that friction coefficient in the presence of synovial fluid increased with dwell time and magnitude of load. Malcom also observed similar effects using saline, however, the friction coefficient was higher than with synovial fluid. For example, the friction coefficient with saline was 0.006 compared to 0.0025 in synovial fluid under low load, and 0.03 compared to 0.01 at a high load.
Obviously, the use of cartilage-on-cartilage is most realistic and challenging as well. Fewer studies were carried out using animal models, mainly due to problems of acquiring suitable specimens and controlling such experiments [5]. Pendulum machine tests of human joints as in Refs. [3] and [18] do not provide direct measurement of the friction force which has to be calculated based on some simplified mathematical model. The pendulum machine test described in [19] does provide a direct friction measurement of a human joint however, like with the former pendulum machines, the friction is varying with time during each cycle and this, as well as the static friction issue are not considered in Ref. [19]. The present study is a first attempt to measure accurately friction coefficient (static and dynamic) on a human cartilage-on-cartilage setup. Here, we test the influence of many parameters on the friction coefficient. Amongst these parameters are: (i) loads (from 1 to 30 N); (ii) temperature (24 and 37 °C); (iii) dwell time (from 5 to 300 s) and, (iv) different lubricating fluids.
Materials and methods
Lubricating fluids
Distilled water, 15 mM NaCl and 150 mM NaCl (saline), histidine buffer (l-histidinemonohydrochloride) at 5, 15, and 150 mM, which is considered as a potential carrier for nano-particles liposome additives, and inflamed synovial fluid (obtained from Rheumatology Department at the Rambam Hospital, Haifa, Israel) were used as lubricating fluids.
Tissue sampling and preparation
Human articular cartilage was obtained from total hip replacement operations of six patients (ages: 72–86 years) at the Rambam Hospital. Tissue was classified as normal or pathological according to the clinical diagnosis, and frozen at −20 °C until analyzed in order to keep its properties close to live tissue [20]. Only normal cartilage with a completely intact and smooth surface was tested.
Full depth plugs (approximately 1.5–2 mm), preferably from the same region of the joint, were removed from the bone (figure 1) using a cork borer and a scalpel, and trimmed on the bone side using a freezing Leica 1320 microtome (Leica, Germany) in order to allow good attachment to the holders. Up to 15 pairs of cartilage discs, comprising 4 mm and 8 mm in diameter for each pair, were harvested from each of the six patients. These discs were refrozen at −20 °C until used. The cartilage discs were then glued to holders on their trimmed side (close to the bone side) prior to measurements, using a cyanoacrylate-based adhesive glue. Friction tests were carried out on the untrimmed, i.e. the exposed side of the cartilage samples.
Description of the test rig and test procedure
The apparatus shown schematically in figure 2 is designed to measure the friction between two discs of cartilage soaked in a given lubricating fluid and subjected to a range of normal loads, sliding velocities as well as dwell times. The cartilage discs are allowed to slide over each other under applied normal load N, while immersed in different lubricants (one at the time). The sliding velocity is controlled by a special mechanism that allows the horizontal motion of the bath while the friction force, F, is continuously measured.
The upper, 4 mm diameter, cartilage disc holder (figure 3a) is attached to a loading mechanism via a ball and socket joint to provide self alignment between the two cartilage discs. The lower, 8 mm diameter, cartilage disc holder (figure 3b) is fixed in the bath (figure 3c). Both holders and bath are made of Perspex.
The tested lubricating fluids are placed in the bath and cover both the lower and upper specimens to ensure lubricant presence in the contact interface. For experiments carried out above room temperature, a heat source is used to warm up the lubricating fluid; the temperature is measured by UIL 6681 infrared thermometer (UIL, Israel). In order to distinguish between the effects of the different parameters under investigation a dedicated specimen pair was tested with only one lubricating fluid. Tests were performed in increasing normal load order. The same practice of dedicated specimen pair was also used for studying the effect of dwell time, temperature and sliding velocity. For each tested pair of cartilage discs, only one parameter was changed, while all other parameters were kept constant.
Tested parameters
Various parameters were studied for their impact on the friction; these parameters are: (i) sliding velocity; (ii) temperature; (iii) different loads; (iv) dwell time; and (v) different lubricating fluids.
(i) The sliding velocity, controlled by a computer program, can be pre-selected as needed. Several velocities were tested: 0.5, 1 and 2 mm/s.; (ii) the temperatures used in our experiments were 24 and 37 °C; (iii) different loads equivalent to physiological loads in joints were used, i.e. 5, 10 and 30 N (equivalent to pressures of 0.4, 0.8 and 2.4 MPa, respectively). The nominal contact pressure was obtained by dividing the normal load by the area of the smaller (upper) disc; (iv) the dwell time measured by a chronometer varied between 5, 20, 60 and 300 s. The sliding time changed according to the sliding velocity. The recovery time between successive tests without application of any load was at least equal to the dwell time; (v) different lubricating fluids: saline, histidine buffer and inflamed synovial fluid were used for the friction coefficient measurements.
Statistical analysis
The statistical significance of the differences in static or dynamic friction coefficient for: (i) the range of applied loads; (ii) same lubricant at different temperatures; (iii) different concentrations of lubricating fluids; and (iv) same lubricant and load at different dwell times, were determined using ANOVA two-factor with replication. Significance was set at p-value of 0.05 for all tests. Each friction test was repeated at least 10 times on the same specimen, from which the mean and standard deviation were calculated.
Results and discussion
Measurement of the static and dynamic friction coefficient
A typical diagram of friction coefficient as a function of test time is shown in figure 4. The case shown in the figure corresponds to saline lubricant, 10 N load, sliding speed of 1 mm/s, dwell time of 5 s, and temperature of 24 °C. The static friction coefficient, corresponding to sliding inception, is obtained at point (1) in the graph. The dynamic friction coefficient was calculated as the mean of the values obtained during the rest of the test time following sliding inception.
For all tests and under all conditions used, the dynamic friction coefficient was statistically different from the static one (p < 0.022).
Effect of applied load on friction coefficient
Measurements of the friction coefficient that were performed under loads of 1, 5, 10 and 30 N, (equivalent to pressures of 0.08, 0.4, 0.8 and 2.4 MPa, respectively) in the presence of saline, at 24 °C, 5 s dwell time and 1 mm/s sliding velocity, are presented in figure 5. In all cases studied, application of higher load resulted in a significant decrease of friction coefficient (p < 3.9E-13).
Static friction coefficient obtained under a load of 1 N was 4.2 times higher than that obtained under 30 N (0.42 compare to 0.1); similar behavior was observed for the dynamic friction coefficient under the same loads (0.34 and 0.055, respectively). Similar reduction in friction coefficient with increasing load is reported in a review [4] of previously published literature. The static friction coefficient in unlubricated bovine cartilage-on-cartilage tests decreased by approximately 3 times as load increased by a factor of approximately 8.
Forster and Fisher [10] measured static friction coefficient of 0.033 under a pressure of 4 MPa for bovine cartilage-on-cartilage in the presence of Ringer’s solution having the same viscosity as that of the saline that we used in our human cartilage-on-cartilage model. Extrapolation of our data (R² = 0.9) up to a pressure of 4 MPa (50 N) resulted in static friction coefficient of 0.081. In another paper by Stachowiak and coworkers [2], a dynamic friction coefficient of 0.07 was obtained in the presence of saline under 1.8 MPa for a rat cartilage-on-metal model. This is comparable to our interpolated value of 0.065 shown in figure 5.
The behavior of the dynamic friction coefficient as shown in figure 5 in the presence of saline under constant viscosity and constant sliding speed is typical of a hydrodynamic (fluid film) lubrication regime according to the Stribeck curve. It should be noted though that the exact mode of lubrication of an entire joint is an unsettled issue yet (see for example Unsworth et al. [19]) and even on tests with small specimens, as in our case, there is still no consensus among different researchers.
Effect of temperature on the friction coefficient
Several lubricants were tested and compared at 37 and 24 °C, under loads of 10 and 30 N, at a sliding velocity of 1 mm/s, and a dwell time of 5 s. The results are shown in figures 6 and 7. The following abbreviations are used in the figures: H.B.—histidine buffer (5 mM), I.F.S.—inflamed synovial fluid.
We found that a decrease in temperature (from 37 to 24 °C) had almost no effect on the friction coefficient in the presence of saline; static and dynamic friction coefficient were found to vary insignificantly (p > 0.077) with temperature at both 10 and 30 N. Our data is not consistent with that of Stachowiak et al. [2] who found, in a rat cartilage against stainless steel model, that static friction coefficient obtained in the presence of saline at 15–17 °C is lowered at 38 °C. Unlike saline, a significant difference between friction coefficient at 24 and 37 °C in the presence of inflamed synovial fluid was found (p < 1.09E-11). The static friction coefficient decreased (as the temperature increased from 24 to 37 °C) from 0.127 to 0.095 under a 10 N and from 0.1 to 0.06 under a 30 N load. Our results are in accordance with previously published literature claiming that synovial fluid becomes less viscous with elevation of temperature and hence, performs as a better lubricating fluid for low friction [3]. However, Seller and coworkers [21] show that viscosity of synovial fluid has little effect on the frictional forces in joint. Similar to the synovial fluid, friction coefficient (static and dynamic) in the presence of histidine buffer (5 mM) were found to be significantly influenced (p < 0.0036) by the temperature.
Effect of concentration of lubricating fluids on the friction coefficient
Friction tests were carried out in the presence of different lubricating fluids under the same operating conditions (10 and 30 N loads, at 37 °C, sliding velocity of 1 mm/s and dwell time of 5 s). Distilled water, 15 and 150 mM NaCl and histidine solutions at 5, 15 and 150 mM were tested. In general, for each of the solutions tested, an increase in the concentration led to a significant increase in the friction coefficient (p < 0.012) both under 10 and 30 N as shown in figures 8 and 9, respectively.
Increase in salinity, from none to 150 mM, resulted in increase of static and dynamic friction coefficient by about 50 and 40% under load of 10 and 30 N, respectively. Stachowiak [2] found a fourfold increase in static friction coefficient, from 0.02 to 0.08, with increase in salinity, from 75 to 300 mM NaCl, using rat cartilage-on-metal model at 38 °C under 1 MPa.
The same behavior was observed for histidine buffer; as the histidine concentration increased, from 5 to 150 mM, the static and dynamic friction coefficient increased by about 50 and 40% under load of 10 and 30 N respectively.
Effect of dwell time on the friction coefficient
Most joints are subjected to high loads of short duration as well as to low loads of longer duration prior to sliding; these time durations are termed as dwell time.
Dwell time in the range from 5 s to 5 min was tested to mimic natural processes in synovial joints. The recovery time, i.e. the time without any load between successive repetitions was at least as long as the corresponding dwell time. The results are shown in figures 10 and 11 for loads of 10 and 30 N, respectively.
It was found that an increase in dwell time resulted in a significant increase in friction coefficient (static and dynamic), both for saline (p < 1.5E-06) and for 5 mM histidine buffer (p < 4.2E-06) under loads of 10 and 30 N. In the presence of saline, a drastic and non-linear increase in the friction coefficient, between 70 and 100%, was observed for dwell times of 20 and 60 s. After a dwell time of 60 s, no significant change (p > 0.05) in the friction coefficient with saline was observed under the 10 N load (figure 10) while an increase by 40–50% was observed under the 30 N load (figure 11). In the presence of histidine buffer, the increase in both static and dynamic friction coefficient under the two loads of 10 and 30 N was almost linear (R² = 0.91) with the dwell time. In general, for any given dwell time, the friction coefficient with histidine buffer was lower compared to this with saline. It can be concluded that histidine buffer has a better resistance to load and dwell times than saline. Similar effect of dwell time on friction coefficient was observed by Forster and Fisher [10], using a bovine cartilage plug on cartilage surface in a sliding-friction machine. They reported that the static friction coefficient sharply increased with increasing dwell times and exceeded 0.25 after 45 min. In our tests a maximum value of 0.24 was obtained already after 5 min.). Mabuchi et al. [12] found a similar increase in the static friction in canine cartilage-on-cartilage model. The static friction coefficient increased from 0.012 at zero dwell time to 0.31 at 30 min dwell time. They concluded that the increase in friction can be caused by a decrease in lubricant film thickness and a transition from hydrodynamic to boundary lubrication regime. A recent study [17] using a pig cartilage-on-glass model showed similar dependence of friction coefficient on dwell time. The friction coefficient increased from 0.037 to 0.5 as the dwell time increased from at 10 to 600 s.
Conclusion
A first attempt to accurately measure static and dynamic friction coefficient using a human cartilage-on-cartilage setup was made. The influence of many parameters on the friction coefficient was tested and found to be reproducible. Amongst these parameters are: loads from 1 to 30 N, temperature of 24 and 37 °C, dwell time from 5 to 300 s, and different lubricating fluids that are potential candidates for carrying nano-particle liposome additives.
In all studied cases, higher loads resulted in lower friction coefficient, in agreement with previous studies with animal cartilage-on-cartilage and cartilage-on-metal setups.
Lubrication of the cartilage surface by synovial fluid, unlike histidine buffer and saline, was impaired at low temperatures.
An increase in dwell time resulted in higher friction coefficient similar to previous studies with animal cartilage. In the presence of saline under 10 N load, the friction coefficient leveled up above dwell time of 60 s. In all other cases (i.e. saline under 30 N and histidine buffer under both 10 and 30 N), the friction coefficient increased monotonically.
In conclusion, under all tested operating conditions, the presence of synovial fluid, even though obtained from inflamed joints, in the contact interface of two cartilage discs is advantageous and enables lower friction coefficient compared to saline, water and histidine buffer. These results, obtained using human cartilage-on-cartilage, can be used for future research of joint lubrication.
References
J.A. Gaudin, in: Encyclopedia of Human Biology, Vol. 1, eds. R. Dulbecco (Academic press, INC. San Diego, 1991) 371
G.W. Stachowiack, A.W. Batchelor, L.J. Griffiths (1994) Wear 171:135
T. Little, M. Freeman, and S.A.V. Swanson, in: Lubrication and Wear in Joints, eds. V. Wright (Sector, London, 1969) 110
V.C. Mow and G.A. Ateshian, in: Basic Orthopedic Biomechanics, eds. V.C. Mow and C. Wilson (Lippincott-Raven, Philadelphia, 1997) 275
M. Furey, in: The Biomedical Engineering Handbook, eds. J. D. Bronzino (CRC Press, Boca Raton, 2000)
S.A.V. Swanson, in: Adult Articular Cartilage, eds. M. A. R. Freeman (Pitman Medical, London, 1979) 415
G. Grushko, M.Sc. Thesis Technion, Israel Institute of Technology, Haifa, Israel (1987)
T. Murakami, H. Higaki, Y. Sawae, N. Ohtsuki, S. Moriyama, Y. Nakanishi (1998) Proc. Instn. Mech. Engrs. Part H, J. Eng. Med. 212:337
T.W. Walker, J.D. Graham, R.H. Mills (1976) J. Biomech. 9:615
H. Forster, J. Fisher (1996) Proc. Instn. Mech. Engrs. Part H, J. Eng. Med. 210:109
H. Forster, J. Fisher (1999) Proc. Instn. Mech. Engrs. Part H, J. Eng. Med. 213:329
K. Mabuchi, M. Ujihira, T. Sasada (1998) Clin. Biomech. 13:492
M. Kobayashi, J. Toguchida, M. Oka (2001) J. Biomed. Mater. Res. 55:645
L.L. Malcom, Ph.D. thesis, University of California, San Diego (1976)
C.W. McCutchen (1962) Wear 5:1
D. Dowson, M.D. Longfield, P.S. Walker, V. Wright (1968) Proc. Instn. Mech. Engrs. 182:68
M.H. Naka, K. Hattori, T. Ohashi, K. Ikeuchi (2005) Clin. Biomech. 20:1111
J. Charnley, (1959) Symposium on Biomechanics, Instn. Mech. Engrs. London, 12
A. Unsworth, D. Dowson, V. Wright (1975) J. Lub. Technol. 3:369
A. Maroudas, R. Schneiderman and O. Popper, in: Articular Cartilage and Osteoarthritis, eds. K. E. Kuettner, R. Schleyrbach, J. G. Peyron and V. C. Hascall (Raven Press, New York, 1992) 355
P. Seller, D. Dowson, M. Longfield, and V. Wright, in: Lubrication and Wear in Joints, eds. V. Wright (Sector, London, 1969) 142
Author information
Authors and Affiliations
Corresponding author
Rights and permissions
About this article
Cite this article
Merkher, Y., Sivan, S., Etsion, I. et al. A rational human joint friction test using a human cartilage-on-cartilage arrangement. Tribol Lett 22, 29–36 (2006). https://doi.org/10.1007/s11249-006-9069-9
Received:
Accepted:
Published:
Issue Date:
DOI: https://doi.org/10.1007/s11249-006-9069-9