Abstract
Temperature stable Li2ZnTi3O8 dielectric ceramics with Li2O–B2O3–SiO2 (LBS) glass additive and TiO2 dopant have been prepared by the conventional solid-state ceramic route. The sintering temperature of Li2ZnTi3O8 ceramics can be reduced from 1,050 to 875 °C by doping LBS glass additive. The 1 wt% LBS-added Li2ZnTi3O8 sintered at 875 °C/4 h has ε r = 23.9, Q × f = 40,503 GHz, and τ f = −13.4 ppm/°C. Adding appropriate amount of TiO2 can effectively adjust the temperature coefficient of resonant frequency (τ f ) and improve the dielectric properties. Typically, the Li2ZnTi3O8 + 1 wt% LBS + 3.5 wt% TiO2 sintered at 875 °C shows excellent dielectric properties of εr = 26, Q × f = 44,023 GHz, τ f = −4.4 ppm/°C. Compatibility with Ag electrode indicates this material may be applied to low temperature co-fired ceramic devices.
Similar content being viewed by others
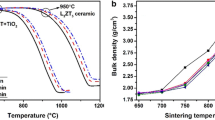
Avoid common mistakes on your manuscript.
1 Introduction
To meet the demands of the miniaturization of microwave components for wireless communication, low-temperature co-fired ceramic (LTCC) technology becomes an important approach owing to its predominance in enabling the fabrication of three-dimensional ceramic modules with low dielectric loss and co-fired metal electrodes. As a metallic electrode, Ag has been widely used in LTCC technology because of its high conductivity and comparatively low cost. The melting temperature of Ag is low, about 961 °C. Therefore, the microwave dielectric ceramics must have a low sintering temperature lower than 950 °C and chemical compatibility with Ag [1, 2] in order to use the most common electrode silver.
Unfortunately, Most of the known commercial dielectric materials for the high frequency applications have good microwave dielectric properties, but they cannot be co-fired with Ag electrode because of high sintering temperatures above 1,000 °C [3–5]. The addition of sintering aids, such as low-melting glasses and oxides, is the most often used method to lower the sintering temperatures [6–12]. Besides this, considerable attention has been paid to developing new microwave dielectrics with low cost of raw materials and low sintering temperature [13–15]. Currently, the search for new kinds of low-temperature firing materials that have good microwave dielectric properties is still continuing.
More recently, George and colleagues [16] reported that Li2ZnTi3O8 ceramics exhibited good microwave dielectric properties (εr = 25.6, Q × f = 72,000 GHz, τ f = −11.2 ppm/°C) and low cost of raw materials. Unfortunately, the ceramics can not be co-fired with Ag electrode due to high sintering temperatures (~1,075 °C). Subsequently, the firing temperature can be reduced to 900 °C by adding the lithium magnesium zinc borosilicate (LMZBS) glass or BaCu(B2O5) compound into the LZT [17, 18]. For example, the 3 wt% LMZBS glass doped- LZT ceramic sintered at 900 °C/4 h has ε r = 23.2, Q × f value = 31,300 GHz, and τ f = −15.6 ppm/°C. Unfortunately, the prepared ceramic still possesses a large positive τ f value which precludes its further applications in practice. Hence, it is better to adjust excessively high τ f to near zero while maintaining high permittivity, Q × f value and low sintering temperature of ~900 °C.
It is well known that TiO2 with a large positive τ f is commonly used to tune the temperature coefficient of resonant frequency of microwave dielectric ceramics which have a negative τ f [19, 20]. In the present work, we have attempted to lower the sintering temperature below 950 °C by adding Li2O–B2O3–SiO2 (LBS) glass and to tune the temperature coefficient of resonant frequency (τ f ) to near zero by doping TiO2 in the LBS glass-added LZT ceramics. The effects of LBS glass additive and TiO2 doping on the sintering behavior, phase purity, microstructure, and microwave dielectric properties have been investigated. Meanwhile, the compatibility of the ceramic with an Ag electrode in the LZT + 1 wt% LBS + y wt% TiO2 (0 ≤ y ≤ 4.5) system has also been studied.
2 Experimental procedure
The Li2ZnTi3O8 (LZT) ceramic samples were prepared by the conventional solid-state ceramic route. High-purity Li2CO3 (+97.5%), H3BO3 (+99%), ZnO (+99%), and TiO2 (+99%) (Guo-Yao Co. Ltd., Shanghai, China) powders were used as the starting materials. Stoichiometric amounts of the powder samples were mixed and ball milled using zirconia balls in ethanol medium for 24 h. The resultant slurry was then dried. The LZT ceramic powders were calcined at 900 °C/4 h. The LBS (48.7Li2O:36.4B2O3:14.9SiO2) glass powders were prepared from the above-mentioned high purity oxide chemicals of Li2CO3, H3BO3 and SiO2. These oxides were weighed stoichiometrically and mixed for 12 h using distilled water as medium. They were dried, melted in a corundum crucible at 900 °C/1 h, then quenched and powdered. The medium grain size of LBS glass powder was about 5 μm. The calcined LZT powders were remilled together with different weight percentages LBS glass additives (0–5 wt%) and TiO2 (0–4.5 wt%) in alcohol medium for 24 h. After drying, mixing with 5 wt% polyvinyl alcohol solution, the granulated powders were pressed uniaxially into pellets of 12 mm in diameter and 6–7 mm in thickness under a pressure of 100 MPa. The pellets were then fired at 600 °C/1 h to expel the binder before sintering at temperatures in the range of 850–950 °C/4 h in air at a heating rate of 2 °C/min. The pure LZT pellets were sintered at different temperatures in the range of 1,025–1,150 °C/4 h in air.
The bulk density was measured by the Archimedes method. The theoretical density (D) of the glass added LZT specimens was calculated using the equation
where W1 and W2 are the weight percentage of LZT and glass with densities D1 and D2 respectively. The crystal structure and phase purity of the powdered samples were analyzed using X-ray diffraction (XRD, D8-ADVANCE, Bruker, Germany) with CuKα radiation. The microstructure observation of the samples was performed using scanning electron microscopy (SEM, JEOL JSM-5610LV, Tokyo, Japan). The microwave dielectric properties were measured by a Vector Network Analyzer (N5230C, Agilent Technologies). The temperature coefficient of resonant frequency (τ f ) was measured in the temperature range of 25–75 °C using the equation,
where f 75 and f 25 are the resonant frequencies at 75 and 25 °C, respectively.
To check the chemical compatibility of the ceramic with the silver powder, 20 wt% powdered silver was mixed and homogenized with the ceramic powder, and then the mixture was pressed into pellets and fired at 875 °C/4 h to achieve equilibrium. In addition to the XRD analysis, micro-structural study was conducted via scanning electron microscopy (SEM, JSM-5610, JEOL, Tokyo, Japan) coupled with energy-dispersive X-ray spectroscopy (EDS).
3 Results and discussion
Figure 1 shows the XRD patterns of the LZT ceramic sintered at 1,050 °C/4 h and the LZT + x wt% LBS ceramics (0.5 ≤ x ≤ 5.0) sintered at 875 °C/4 h. All the peaks are indexed based on JCPDS file number 86-1512 for Li2ZnTi3O8 with cubic crystal symmetry belonging to the P4332 (212) space group. There are no peaks for secondary phases, as shown in Fig. 2. It is possible that the LBS liquid phase is not crystallized and retains its amorphous nature. Hence, LBS glass exists as a liquid phase during sintering and assists the densification of LZT ceramics.
Figure 2 depicts the SEM micrographs of pure LZT sintered at 1,050 °C/4 h and the LZT + x wt% LBS ceramics sintered at 875 °C/4 h. It is observed that the pure LZT ceramic exhibits a dense microstructure with majority of the grains average size of 100–150 μm. However, a different microstructure is observed for the LBS glass-doped LZT ceramics shown in Fig. 2b–d. Moreover, it can be seen that the porosity increases with increasing LBS glass contents, and the grain sizes are smaller than those of pure LZT ceramic. Figure 2c is a typical example of liquid-phase sintering in which the glass melts and wets the grains and flows between the grains of LZT ceramics. It is well known that the liquid phase sintering decreases the grain size of dielectric ceramics [21]. The increase in porosity may be due to the evaporation of glass components.
Figure 3a shows the variation of sintering temperature and relative density of the LZT + x wt% LBS ceramics-glass composites (0 ≤ x ≤ 5) as a function of LBS glass fluxing. The sintering temperature is optimized for best density and dielectric properties. As the amount of glass increases, a gradual decrease in the sintering temperature of the LZT + LBS ceramics glass composites is observed. Addition of 1 wt% LBS decreases the sintering temperature of LZT from 1,050 to 875 °C. However, higher wt% of glass fluxing does not decrease the sintering temperature further. The relative density of LZT ceramics is found to decrease with glass fluxing. It may be noted that the density of LBS glass (~2.4 g/cm3) [22] is slightly lower than the density of LZT ceramics. It is believed that the sintering characteristics are strongly correlated with the formation temperature of the eutectic liquid phase. The decrease in densification of glass-added ceramics could be due to the inhomogeneous evaporation of the liquid phase from the grain boundary causing incomplete wetting, formation of pores, and suppressed grain growth [23]. Maximum densification of 92.5% is observed for 1 wt% LBS glass-added LZT ceramics. Trapped porosity associated with grain growth and formations of pores by the evaporation of excess glass components are the reasons for the reduction of density for higher wt% of glass fluxing, which is well in agreement with the research results reported by George et al. [17].
The effect of glass addition on the microwave dielectric properties depends strongly on the glass composition, the phase change during sintering, and the final density [1, 23]. In general, the Q value (Q = 1/tanδ) of the ceramic–glass composite decreased with the increasing glass content despite the increase in the densification. The relative permittivity and quality factor of LZT ceramics as a function of LBS glass addition is also shown in Fig. 3b. It is noteworthy that the relative permittivity changes in a manner similar to that of densification (relative density). As the LBS glass content increases from 0 to 5 wt%, the relative permittivity of LZT decreases from 25.4 to 23.0, which may be attributed to the lower densification and low relative permittivity of LBS glass (ε r ~ 7) [22]. It is found that the Q × f values decrease from 56,777 to 26,193 GHz as the amount of LBS glass increases from 0 to 5 wt%. The added glass not only acted as the sintering aid but also as an impurity phase with low quality factor and low ε r that can adversely affect the microwave dielectric properties. It has been reported that the microwave dielectric loss is mainly caused not only by the lattice vibrations but also by the pores, the grain morphology, and the second phase [2, 23]. It can be evidenced by comparing the SEM images that the LBS glass is mainly concentrated at the grain boundaries. It is reported that during sintering the impurities are trapped at the grain-boundary intersections and this accumulation of impurities increases with an increase in the grain boundary intersections [2, 6, 17]. In addition, the dielectric loss of glasses is much higher than that of LZT ceramics. The relatively higher dielectric loss of the glass could be the reason for the decrease in the quality factor (Q × f) of LZT + LBS ceramic–glass composite with glass additions. Addition of 1 wt% LBS glass in LZT shows the Q × f value of 40,503 GHz when sintered at 875 °C/4 h. Figure 3c also illustrates the variation of the temperature coefficient of resonant frequency (τ f ) of LZT ceramic with different wt% of LBS glass. It is observed that the τ f varies from −9.2 to −16.5 ppm/°C when the glass content increases from 0 to 5 wt%. The decrease in the τ f is due to the relatively high negative τ f of LBS glass compared with LZT ceramics. On the whole, the promising microwave dielectric properties of ε r = 23.9, Q × f = 40,503 GHz, and τ f = −13.4 ppm/°C can be obtained in the LZT + 1 wt% LBS ceramic-glass composite sintered at 875 °C/4 h. Although the LZT + 1 wt% LBS ceramic shows good dielectric properties, the τ f of −14.3 ppm/°C is still large. Hence, it is essential to lower the τ f close to near zero for applications in LTCC based devices while keeping excellent dielectric properties.
Figure 4 shows the XRD patterns of LZT + 1 wt% LBS + y wt% TiO2 ceramics (0 ≤ y ≤ 4.5) and LZT + 1 wt% LBS + 2.5 wt% TiO2 + 20 wt% Ag sintered at 875 °C/4 h. It can be observed there is no additional phase other than metallic silver (JCPDS file number 03-0921), LZT (JCPDS file number 86-1512) phases and TiO2 (JCPDS file 82-0514). Because the formation of secondary phase is not observed in the pattern, it may be possible to use Ag as the electrode material for these ceramic–glass composites. This observation is also verified by the SEM and EDS profile shown in Fig. 5. The silver did not react with the ceramic–glass composites and are distributed randomly. This micrograph strongly supports the results of non-reactivity of silver with ceramic–glass system as evidenced from the X-ray diffraction pattern shown in Fig. 4.
Figure 6 shows the SEM micrographs of the LZT + 1 wt% LBS + y wt% TiO2 ceramics (1 ≤ y ≤ 4.5) sintered at 875 °C/4 h. When y = 1, there is no significant change in the grain size compared with 1 wt% LBS glass doped-LZT sample shown in Fig. 2b. However, the others exhibits an obvious difference in microstructure when y ≥ 2. Namely, both of large grains and fine grains coexist, as shown in Fig. 6b–d. All the ceramic samples have dense microstructures. It is interesting that the volume fraction of large grains decreases with an increase in the concentration of TiO2. The detail work is under study.
Figure 7 shows the variation of ε r , Q × f and τ f values of the 1 wt% LBS glass-added LZT ceramics as a function of TiO2 contents sintered at 875 °C/4 h. From Fig. 7a, it is observed that the ε r increases from 23.9 to 27.1 with increasing TiO2 content from 0 to 4.5 wt%. In general, the ε r has been reported to significantly depends on the percentage densification and secondary phases at microwave frequencies for the composite ceramics [24]. Because all the samples have dense microstructure, the high permittivity of TiO2 (ε r > 100) [25] is suggested to dominate the ε r values of LBS glass-added LZT ceramics. The Q × f values of LBS glass-added LZT ceramics show first decrease and then increase with an increase in TiO2 content, as shown in Fig. 7b. A maximum Q × f value is 44,023 GHz at y = 3.5. There are several factors that contribute to the dielectric loss at microwave frequencies, such as density, porosity, second phases, grain boundaries, and inclusions in real homogeneous ceramics [24]. The increase in the Q × f value with increasing TiO2 can be attributed to the decrease in the volume fraction of the LBS glass having high dielectric loss and the increase of TiO2 possessing high quality factor (>20,000 GHz) [25].
Figure 7c also illustrates the variations of the temperature coefficient of resonant frequency (τ f ) value as a function of TiO2 content. The τ f is found to increase from −13.4 to +8.7 ppm/°C as the amount of TiO2 increases from 0 to 4.5 wt%. As we know, the τ f is governed by the composition in the composite ceramics [26]. Because the τ f values of the 1 wt% LBS-added LZT and TiO2 are about −13.4 and +400 ppm/°C [25], increasing TiO2 content makes the τ f value become more positive. It implies that zero τ f can be easily achieved by adjusting the amount of TiO2 content. In fact, it can be expected that the reasonable dielectric properties can be obtained. Typically, the 1 wt% LBS-added LZT with 3.5 wt% TiO2 sintered at 875 °C/4 h has better microwave dielectric properties of ε r = 26, Q × f = 44,023 GHz, τ f = −4.4 ppm/°C. Therefore, it provides a wide process window, which would benefit commercial applications in LTCC field.
4 Conclusions
The Li2ZnTi3O8 + LBS and the Li2ZnTi3O8 + LBS + TiO2 system ceramic materials have been synthesized by the conventional solid-state ceramic route and the phase purity, microstructure, microwave dielectric properties are also investigated. The Li2ZnTi3O8 + 1 wt% LBS glass sintered at 875 ppm/°C/4 h has ε r = 23.9, Q × f = 40,503 GHz, and τ f = −13.4 ppm/°C. The temperature coefficient of resonant frequency (τ f ) can be easily modified to near zero ppm/°C by doping TiO2 in the Li2ZnTi3O8 + 1 wt% LBS glass system. Typically, the LZT + 1 wt% LBS + 3.5 wt% TiO2 sintered at 875 °C/4 h shows excellent dielectric properties of ε r = 26, Q × f = 44,023 GHz, τ f = −4.4 ppm/°C, Compatibility with Ag electrode indicates this material can be applied to low temperature co-fired ceramic devices.
References
B.K. Kim, D.W. Lee, S.H. Key, T.J. Jo, S.M. Jeong, K.J. Kim, M.S. Jeon, J.K. Song, Y.S. Cho, J. Am. Ceram. Soc. 93(8), 2334 (2010)
M. Guo, S.P. Gong, G. Dou, D.X. Zhou, J. Alloys. Compd. 509, 5988 (2011)
K.P. Surendran, M.T. Sebastian, J. Mater. Res. 20(11), 2919 (2005)
H. Hughes, D.M. Iddles, I.M. Reaney, Appl. Phys. Lett. 79(18), 2952 (2001)
E.A. Nenasheva, L.P. Mudroliubova, N.F. Kartenko, J. Eur. Ceram. Soc. 23(14), 2443 (2003)
Q.L. Zhang, H. Yang, J.L. Zou, H.P. Wang, Mater. Lett. 59(8–9), 880 (2005)
B. Li, Z.X. Yue, L.T. Li, J. Zhou, Z.L. Gui, J. Mater. Sci. 13(7), 415 (2002)
S.H. Wee, D.W. Kim, S.I. Yoo, J. Am. Ceram. Soc. 87(5), 871 (2004)
G.H. Chen, L.J. Tang, J. Cheng, M.H. Jiang, J. Alloys. Compd. 478(1–2), 856 (2009)
T.S. Sasikala, C. Pavithran, M.T. Sebastian, J. Mater. Sci. 21(2), 141 (2010)
C.S. Hsi, Y.R. Chen, H.I. Hsiang, J. Mater. Sci. 46(13), 4695 (2011)
Z. Wang, X. Zeng, B. Yan, R. Xu, W. Lin, J. Electromagnet. Wave. 24(1), 71 (2010)
L.X. Pang, D. Zhou, Mater. Lett. 64(22), 2413 (2010)
J. Liang, W.Z. Lv, J. Am. Ceram. Soc. 92(4), 952 (2009)
A. Feteira, D.C. Sinclair, J. Am. Ceram. Soc. 91(4), 1338 (2008)
S. George, M.T. Sebastian, J. Am. Ceram. Soc. 93, 2164 (2010)
S. George, M.T. Sebastian, Int. J. Appl. Ceram. Technol. 8(6), 1400 (2011)
H.F. Zhou, X.L. Chen, L. Fang, D.J. Chu, J. Mater. Res. 25(7), 1235 (2010)
S.-H. Yoon, G.-K. Choi, D.-W. Kimb, S.-Y. Cho, K.-S. Hong, J. Eur. Ceram. Soc. 27(8–9), 308 (2007)
Y.-C. Liou, Y.-T. Chen, W.-C. Tsai, J. Alloys. Compd. 477(1–2), 537 (2009)
D.L. Corker, R.W. Whatmore, E. Ringgaard, W.W. Wolny, J. Eur. Ceram. Soc. 20, 2039 (2000)
S.N. Renjini, S. Thomas, M.T. Sebastian, Int. J. Appl. Ceram. Technol. 6(2), 286 (2009)
P.V. Bijumon, M.T. Sebastian, Mater. Sci. Eng. B 123, 31 (2005)
C.H. Hsu, H.A. Ho, Mater. Lett. 64, 396 (2010)
D.G. Lim, B.H. Kim, T.G. Kim, H.J. Jung, Mater. Res. Bull. 34(10–11), 1577 (1999)
K.C. Li, H. Wang, H.F. Zhou, M.H. Zhang, X. Yao, Int. J. Appl. Ceram. Technol. 7(S1), E144 (2010)
Acknowledgments
This work was supported by the National Undergraduate’s Innovation Experiment Program (101059529), Ministry of Education of the People’s Republic of China.
Author information
Authors and Affiliations
Corresponding author
Rights and permissions
About this article
Cite this article
Hou, Mz., Chen, Gh., Bao, Y. et al. Low-temperature firing and microwave dielectric properties of LBS glass-added Li2ZnTi3O8 ceramics with TiO2 . J Mater Sci: Mater Electron 23, 1722–1727 (2012). https://doi.org/10.1007/s10854-012-0653-5
Received:
Accepted:
Published:
Issue Date:
DOI: https://doi.org/10.1007/s10854-012-0653-5