The article describes the calculations and design of a steam jet vacuum system for the column of a hydrocracking unit. Based on calculation results (considering specific operating conditions of the production), several variants of pressure distribution through the pump stages were calculated, and the optimal schematic of the vacuum system was defined, yielding a 20% reduction in energy consumption and a 15% reduction in capital costs.
Similar content being viewed by others
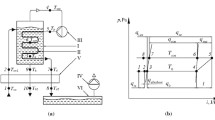
Avoid common mistakes on your manuscript.
Evaluation of the effectiveness of the possible design solutions should be carried out using economic criteria (energy and operation criteria, reduced costs, contingent income, etc.). For refineries, as a rule, electricity is an external power source, and steam and circulating water are internal sources of energy. The relative operating costs of different energy sources, expressed in comparable terms (in kWh), taking into account the efficiency of energy conversion cycles, in the first approximation can be expressed by the ratio energy of oil fuel consumption : energy of steam : electricity = 0.5:0.6:1.0 [1]. In reality, the existing prices of discussed energy sources at different refineries vary widely and are not always consistent with the specified ratio.
Vacuum-creating systems (VCS) in units for separation of heavy oil products in industrial practice are typically systems of vacuum pumps of several types: steam jet ejector pumps (SEP), hydro-circulating VCS based on liquid single-stage ejectors (LE), and based on liquid ring vacuum pumps (LRVP). LRVP systems for deepening the vacuum can be used in conjunction with gas or steam ejectors (SE). A previously conducted comparison of different types of VCS showed [1] that in order to maintain a sufficiently deep technical vacuum (25 mmHg) in the column, a combined hydro-compression system (SE + LRVP) greatly outperforms other possibilities. However, on a number of refineries internal conditions unfold (availability of excess steam, high temperature circulating water, etc.) that justify the use of SEP.
Thus, a customer decided to use SEP to create a vacuum in the column in the section of heavy hydrocarbon feedstock hydrocracking. According to the order, the VCS should be a three-stage SEP comprised of three ejectors and three intercondensers of the surface type. Condenser cooling is implemented using water from the water-circulating system of the plant. The goal of design calculations is to determine the optimum working parameters of operating a VCS (Fig. 1) at which the use of energy resources (motive steam and circulating water) is minimal.
In agreement with the initial data (Table 1), the pumped steam–gas mixture (SGM) is significantly different in composition from, for example, the SGM from vacuum columns of atmospheric vacuum pipe heater (AVPH) systems [2–4]: a relatively small amount of decomposition gases and leakage gases (atmospheric air that is drawn into the apparatus through leaks in the structure) is present in the SGM, the main component in the SGM is steam (93.5 wt.%) that is introduced into the evacuated object due to technological considerations.
In these conditions, selecting a SEP according to the current regulatory documents [5] is ineffective: normalized SEP are designed for pumping SGM containing no more than 40% of saturated water vapor, so their use leads to unreasonably high consumption of the working fluid. Also, in this case the surface of the condensing apparatus may be insufficient. Furthermore, in this case the steam in the SGM at the outlet from the process unit is in a superheated state (pre-condensation is not possible at the given parameters of the cooling water). Therefore, for unloading the 2nd and 3rd stages of the SEP it is advisable to ensure maximum condensation of both the working steam injected into the 1st stage of the pump, and the process steam in the intermediate condenser of the 1st stage of the SEP. At the same time, increase in pressure after the 1st step enhances the effectiveness of the condensation process and reduces the required heat transfer surface and cooling water consumption, but also increases the working steam flow at this stage. The total energy consumption of the VCS will be determined by the distribution of compression ratios ε at all the stages of the pump:
where εt is the total compression ratio; ε1, ε2, and ε3 represent the compression ratio in the respective stages of the SEP.
The selection of the compression ratio at each stage of the SEP in this case becomes the subject of optimization calculations. Obviously, a limitation is to be imposed on the value of ε1 – the condensation temperature of water vapor contained in the SGM at the outlet from the 1st stage must exceed the minimum achievable water vapor condensation temperature in the condenser at this stage (in accordance with a predetermined initial water temperature, it can be taken to equal 32°C). A feeding circuit for the entire amount of cooling water to the condenser of the 1st stage of the pump was adopted. In this case, the cooling water temperature at the outlet of the stage 1 condenser will be determined by the flow rate of the working steam supplied to the ejector J-401. After this, circulating water is sequentially (fully or partially) fed into the intercondensers of the 2nd and 3rd stages, respectively.
Pointwise study of this complex system is inefficient because the specific values of the characteristics of all the system elements can only be established within the integrative characteristics of the combined chemical-technological system (CCTS) [2, 3]. Therefore, the VCS under consideration was conditionally divided into three elements of the upper hierarchical level: 1st compression stage – devices J-401 and E-423; 2nd compression stage – devices J-402 and E-424; 3rd compression stage – devices J-403 and E-425. Each top-level element consists of two elements of the second level. The achievable condensation temperature at all levels of the SEP is determined by the initial temperature, the flow rate of the cooling water, and the adopted heat transfer surface.
According to the catalog of Giproneftemash company [5], the optimum injection pressure after the 1st stage of the pump p inj1 = 80 mmHg. However, the data in [5] must be corrected to calculate a specific installation. According to the calculations, a satisfactory condensation of SGM water vapor from J-401 (about 90%) is achieved at 33–36°C in the pressure range of 65–75 mmHg.
Steam ejectors were calculated according to the gas dynamics theory [6].
Generally, ejector operation is considered according to the theory of one-dimensional motion of gas, which uses several dimensionless parameters: the ejection coefficient n is the ratio of the flow rate of compressed gas to the flow rate of the working fluid; the degree of expansion E is the ratio of the total pressures of the working and compressed gases; compression ratio ε is the ratio of the pressure after the ejector to the pressure of the pumped medium; ejector geometrical parameter α is area ratio of the working and compressible gas flows entering the mixing chamber; and θ is the ratio of the temperatures of the compressible and the working gases.
The ejection coefficient and compression ratio determining the required flow of water vapor are calculated from the equations
The index A is calculated according to the formula
where k is the adiabatic index.
The gas-dynamic function [6] q(λ) is determined by the equation
where λ is the reduced flow rate.
In Eqs. (2) and (3), \( {\overline{c}}_{p2}/{c}_{p1} \) is the ratio of specific heats of the pumped mixture and the working steam; subscripts 1, 2, and 3 refer to the parameters of the working, pumped, and mixed flows, respectively.
The amount of steam required for compressing the pumped mixture to an intermediate pressure, as well as the intermediate pressure of the mixture after the steam ejector, were determined by formulas (2)–(4). The phenomenon of condensation of the working body after flowing through the active nozzle of the ejector was accounted for in accordance with [7].
With decreasing discharge pressure, steam consumption decreases (Fig. 2), but at pressures below 50 mmHg water vapor does not condense completely, resulting in increased load on the 2nd stage of the SEP. Simultaneously, an increase in the proportion of condensation (the ratio of the amount of condensate formed to the initial amount of the mixture) in the 1st stage of the pump is accompanied by an increase in the flow of circulating water and the required heat transfer surface of the E-423 condenser.
Using condensation temperature of 36°C adopted in [5] and an approximate value of the heat transfer coefficient k ap = 150 kcal/(m2·h·°C), the approximate heat transfer area at different discharge pressures after the 1st stage was estimated (see Fig. 3).
To satisfy the requirements of technical specifications, intermediate coolers-condensers are type AE(X, J)S TEMA Class R or the like, with a vertical cut in the partitions on the annulus. From a normal series of condensers according to [8], the most suitable is KP-1.6-2.5-M1/20G-6-T-2-U-I with a heat transfer surface area of 609.7 m2.
The obtained data allowed to determine the compression ratio ε1 for the 1st stage of the SEP corresponding to the minimum energy consumption at this stage, and to select the size for the intercondenser out of a series [8].
Similar calculations were made for two other compression ratios.
At the next step, more accurate calculations of all the elements of the SEP were made considering the actually achievable coefficients of heat transfer and hydraulic resistance of the condensers (Table 2).
Thus, designing an individual steam ejector pump in comparison with selecting a normalized structure yields a 20% reduction in energy and a 15% reduction in capital costs of the process implementation.
References
E. V. Osipov, E. Sh. Telyakov, S. I. Ponikarov, and K. S. Sadykov, “World of petroleum products,” Vest. Neft. Komp., 31–35 (2011).
E. V. Osipov, Kh. S. Shoipov, and E. Sh. Telyakov, Vest. Kazan. Technol. Univ., No. 3, 209–212 (2014).
E. V. Osipov, Kh. S. Shoipov, and E. Sh. Telyakov, Vest. Kazan. Technol. Univ., No. 21, 283–286 (2013).
E. V. Osipov, E. A. Efremov, D. I. Kashifrazov, and L. E. Osipova, Vest. Kazan. Technol. Univ., No. 20, 259–261 (2014).
Steam Jet Vacuum Pumps, Giproneftemash, Moscow (1965).
G. N. Abramovich, Applied Gas Dynamics, Nauka, Moscow (1969).
E. V. Osipov, E. Sh. Telyakov, T. S. Kozyreva, and E. B. Mats, Vest. Kazan. Technol. Univ., 15, No. 19, 101–104 (2012).
TU 3612-023-00220302-01, Floating-Head Shell Heat Exchangers, U-Tube Shell Heat Exchangers.
Author information
Authors and Affiliations
Corresponding author
Additional information
Translated from Khimicheskoe i Neftegazovoe Mashinostroenie, No. 5, pp. 30–32, May, 2016.
Rights and permissions
About this article
Cite this article
Osipov, E.V., Telyakov, E.S. & Sadуkov, K.S. Optimal Design Process of a Steam Jet Vacuum System for a Hydrocracking Unit. Chem Petrol Eng 52, 339–343 (2016). https://doi.org/10.1007/s10556-016-0196-3
Published:
Issue Date:
DOI: https://doi.org/10.1007/s10556-016-0196-3