Abstract
The present study uses ultrasonic vibration energy as an energy source in thermoforming of a microspeaker diaphragm. Microspeaker diaphragms have many applications in mobile media, and are generally manufactured from a thin polymer film using the thermoforming process. Thermoforming is a polymer processing method in which a polymer film is heated and softened to be formed into a desired shape. This process requires long cycle time because the polymer film should be heated enough to be softened before forming, and should be cooled sufficiently to be solidified after forming. In this study, ultrasonic vibration is applied to a thermoforming plug from which thin polymer films are shaped. For this purpose, an ultrasonic plug is designed to resonate at the excitation frequency of ultrasonic waves, and is applied to the thermoforming of a microspeaker diaphragm that incorporates a number of micro-corrugations. Considering that the cycle time of the proposed ultrasonic-assisted thermoforming process is <20 s owing to its localized heating capability, it can be concluded that the proposed process is superior to the conventional thermoforming process, the cycle time of which was as long as 160 s.
Similar content being viewed by others
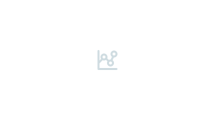
Explore related subjects
Discover the latest articles, news and stories from top researchers in related subjects.Avoid common mistakes on your manuscript.
1 Introduction
Recently, an explosive use of mobile devices has driven the development of microspeakers with high sound power and quality. Considering the trend of mobile phones with increasingly large screens and reduced thicknesses, microspeakers are being developed with compact sizes; usually as small as 10 mm in diameter (Shahosseini et al. 2013; Kim and Jeong 2015). To meet the requirement for size reduction, polymer diaphragms are generally used instead of the traditional pulp diaphragms (Hwang et al. 2005). The polymer diaphragms are fabricated by the thermoforming process, in which a thin polymer film is shaped into the desired geometry (Kim and Park 2013).
In the thermoforming process, a thin polymer film is heated above its softening temperature, and the softened film is deformed into the desired shape over a mold, by applying adequate pressure (Throne 1996). This pressure can be applied in a direct manner by using hot compressed air or mechanical plugs (Collins et al. 2002), as well as an in indirect way by using a vacuum (Hosseini et al. 2006). In either way, the thermoforming process requires long cycle time as long as several minutes, in order to control the mold temperature effectively; the mold surface should be heated higher than the polymer softening temperature before the forming stage, and should be cooled below the demolding temperature after the forming stage (Li et al. 2009).
In recent years, ultrasonic vibration energy has been used to reduce thermal energy consumption in various polymer processing methods. Ultrasonic energy was used in hot embossing as an auxiliary heat source (Mekaru et al. 2007; Khuntontong et al. 2009), and in micro-injection molding to plasticize a small amount of polymer (Michaeli et al. 2011; Sacristan et al. 2014). It has also been used as a direct energy source to imprint micropatterns on thermoplastic polymers (Mekaru and Takahashi 2008; Seo and Park 2012). This ultrasonic imprinting was further applied to develop functional micropatterns by means of selective micropattern replication (Jung and Park 2014; Jung et al. 2015) and repetitive micropattern replication (Lee and Park 2014).
In this study, ultrasonic vibration energy is applied to a plug-assisted thermoforming process of a microspeaker diaphragm, in order to reduce the cycle time by heating the polymer film locally and rapidly. For this purpose, a thermoforming plug was developed to resonate at the given ultrasonic excitation frequency, and used as an ultrasonic horn. To improve the transmission capability of ultrasonic waves, thermoforming molds were developed using a soft material, with both flat and curved shapes. The effects of the mold shapes and the relevant processing conditions were then investigated in terms of the heating capability and formability, and the results show that the proposed ultrasonic-assisted thermoforming could be successfully applied to manufacture microspeaker diaphragms with short cycle time.
2 Thermoforming of a microspeaker diaphragm
2.1 Overview of the microspeaker diaphragm
Microspeaker diaphragms play an important role in generating desired sound responses by vibrating within the audible frequency range. To enable adequate flexibility at its vibration, a polymer diaphragm is designed to have a thin membrane shape, <100 μm in thickness in general. This diaphragm is assembled with a voice coil, from which it vibrates due to the electromagnetic interaction between the voice coil and magnets in the speaker module (Hwang et al. 2005). Because the generated sound of the speaker module depends on the vibration of the diaphragm, the diaphragm should be designed to obtain desired vibration characteristics (Pillai and Deenadayalan 2014).
Figure 1 shows the dimensional configuration of the microspeaker diaphragm developed in this study; the basic dimensions are 13.8 mm in length, 9.8 mm in width, and 32 μm in thickness. Three rectangular bands were designed: one large band in the outer region, and two small bands in the inner region. The outer band is the most important part of the diaphragm, as it determines the vibration characteristics. A number of micro-corrugations were designed at the four corner regions of the outer band, in order to improve the sound quality and uniformity (Kwon et al. 2007). These micro-corrugations are 350 μm in width and 70 μm in depth. On the contrary, the two inner bands are designed to control the material flow inside the outer band during thermoforming, and these regions will be trimmed out after thermoforming. Thus, the formability of the outer band including the micro-corrugation is the main concern of the present study.
The polymer film was manufactured by laminating three thermoplastic polymer films; the base film is a thermoplastic poly-urethane (TPU) film with 20 μm thickness, and two thin Polyetheretherketones (PEEK) films with 6 μm thickness are laminated on both sides of the base film. Detailed material properties for the TPU and PEEK films are listed in Table 1.
2.2 Plug-assisted thermoforming using a heated mold
The thermoforming process is a polymer processing method that shapes a thin polymer film into the desired geometry. The microspeaker diaphragm shown in Fig. 1 was manufactured by the conventional thermoforming process: the polymer film was heated to its softening temperature (156 °C), shaped over a mold by applying air pressure (7.5 MPa), and cooled for demolding by circulating coolant (50 °C) in the heated mold. This process requires long cycle time, 160 s, in order to heat the mold before forming and to cool the mold after forming.
In this study, plug-assisted thermoforming is used to form the microspeaker diaphragm, where a mechanical plug is used to press a softened polymer film instead of air pressure. Additionally, the plug is used not only to press the softened film but also to transfer the ultrasonic wave to the film for appropriate heating and softening. The plug thus should be designed to play a role as an ultrasonic horn: it should resonate at the specified excitation frequency at its longitudinal vibration mode (Seo and Park 2012). The plug was then designed to have the same geometry as the optimally designed horn that was determined by a finite element analysis in a previous work of the authors (Bae and Park 2015). Figure 2 shows the fabricated ultrasonic plug with its dimensions, where three rectangular bands and micro-corrugations were engraved. The plug material was AA7075-T61, considering its high ultrasonic transmission capability and mechanical strength.
The plug-assisted thermoforming was performed first without the use of ultrasonic excitation, in order to compare the formability of the microspeaker diaphragm in terms of whether ultrasonic vibration energy is used or not. The thermoforming mold was fabricated using an AISI-1045 steel block, and the negative shapes of the diaphragm features were engraved on its surface. The mold temperature was maintained at 165 °C using two cartridge heaters. Air pressure was not imposed in this case, in order to investigate the effect of ultrasonic vibration in isolation.
Thermoforming experiments were performed with variation in the forming time; from 1.0 to 4.0 min, with an increment of 1.0 min. Figure 3a–d are enlarged photographs of the thermoformed films for each case, showing that micro-corrugations were not developed even in the 4.0 min case.
For quantitative comparison of the formability, the forming ratio was defined by the relative height of the thermoformed feature to its design value (0.47 mm). The forming ratio was evaluated for the results of four thermoforming cases, by measuring the formed band heights at four different locations for three thermoformed samples, as marked in Fig. 4a. These forming ratios are compared in Fig. 4b, showing a range between 54 and 61 %. Although the increase in forming time led to slightly improved forming ratio, the amount of improvement was not significant enough to fulfill the satisfactory level. Therefore, it can be concluded that additional efforts are required for further improvement of formability.
3 Ultrasonic-assisted thermoforming
3.1 Process overview
To improve the formability of the microspeaker diaphragm, an ultrasonic-assisted thermoforming system was developed by modifying the aforementioned plug-assisted thermoforming process. Figure 4 shows the configuration of the developed ultrasonic-assisted thermoforming system, which is mainly composed of an ultrasonic excitation unit, a pressing unit, and a thermoforming section. In the thermoforming section, a polymer film is placed between an ultrasonic plug and a lower mold. Ultrasonic waves are transferred from the plug to the polymer film, by generating repetitive deformation energy of the polymer film and frictional heat between the plug and polymer surfaces. The deformation energy and frictional heat raise the film temperature above its softening temperature. The plug then presses the softened film during a certain amount of holding time such that the polymer film is deformed into the desired shape.
The ultrasonic excitation unit delivers ultrasonic waves with a frequency of 27 kHz and a power of 700 W. The ultrasonic plug was fabricated according to the design parameters to resonate at 27 kHz, as shown in Fig. 2. The fabricated plug was attached to the ultrasonic forming equipment, and its vibration amplitude was measured as 4.35 μm at the outlet. The pressing unit uses hydraulic pressure to impose imprinting pressure, up to 0.6 MPa. In the thermoforming section, a polymer film was installed in the mold where two cartridge heaters were inserted. A sensor hole was placed between these two heater holes, in which a thermal sensor was installed to measure the mold temperature for feedback temperature control.
3.2 Ultrasonic thermoforming using a soft mold
In ultrasonic imprinting, the lower molds are usually prepared using hard metal (Liao et al. 2015). These metal molds have are typically used in ultrasonic imprinting, where the target polymer films are thicker than 100 μm. Hence, ultrasonic vibration with amplitude of several micrometers is well absorbed in the target film. However, in the case of the present thermoforming, the film thickness is only 32 μm, which is too thin to absorb the given ultrasonic vibration; electrical short-circuits frequently occurred when the contact force of the ultrasonic plug exceeded the critical value of the developed system (Fig. 5).
To overcome this problem, a soft mold was used instead of the hard metal mold. Dow Corning® 184 silicone elastomer was used as the soft mold material, the Shore hardness and elongation of which are 44 and 120 %, respectively. Soft mold cores were fabricated using this material, and were inserted into a metal mold base (AISI-1045 steel). Figure 6 illustrates the configuration of two soft molds, a flat soft mold (Fig. 6a) and a curved soft mold (Fig. 6b). The curved mold was fabricated to have a negative shape of the microspeaker diaphragm, by molding from its positive shape.
To investigate the heating characteristics of these two soft molds, ultrasonic thermoforming experiments were performed with temperature measurement. The temperature distribution of the polymer film was measured using a thermal imaging system (FLIR E50, FLIR Systems Inc., USA). Ultrasonic vibration was imposed for 0.5 s with a pressure of 0.3 MPa. The forming experiments were performed at room temperature without mold heating. Figure 7a, b show the temperature distributions for both molds, at three intermediate stages: (1) before vibration, (2) during vibration, and (3) after vibration. It can be seen that the maximum temperatures after vibration were 91.1 °C for the flat mold and 101.3 °C for the curved mold, respectively. This indicates that the curved mold provides better heating capability than the flat mold because the ultrasonic-induced deformation and friction were more focused in the curved regions than the flat region.
Figure 7c compares the temperature profiles for each case, at the maximum temperature locations. It can be seen that the maximum temperature increased rapidly during the vibration stage, and fell below 50 °C after 20 s without additional mold cooling. This rapid heating and cooling capability is due to the localized heating characteristics of the repetitive friction between the plug and polymer film, where the locally generated heat is dissipated through heat conduction to the horn and mold. Therefore, the ultrasonic-assisted thermoforming does not require additional mold cooling unlike the conventional thermoforming process, where the entire mold is heated by a number of embedded heaters.
Figure 8a, b show the changes of the maximum temperature for the flat and curved mold cases, with an increase of the vibration time. Overall, the maximum temperature increased as the vibration time and imprinting pressure increased while the imprinting pressure shows a more sensitive effect than the vibration time. Among these four pressure cases, the case of 0.6 MPa pressure shows a remarkable temperature increase compared to other cases. Based on these results, the imprinting pressure was set to 0.6 MPa.
Ultrasonic thermoforming experiments were then performed under conditions of 0.6 MPa pressure, 0.1 s vibration time and 9.0 s holding time. Figure 9a, b show photographs of the thermoformed diaphragm for the flat and curved mold cases, enlarged in the corner region where micro-corrugations were developed. It can be seen that the curved mold case shows better replication of the micro-corrugations than the flat mold case. This is in good agreement with the result in Fig. 8, showing that the curved mold presents a higher temperature increase than the flat mold. The curved mold has another advantage that the negative features on the mold surface facilitate pressure transmission during the thermoforming process, by increasing the contact area between the mold and the polymer film.
3.3 Effects of processing conditions
3.3.1 Effects of the vibration time
In this section, the effects of the processing parameters including the vibration time, holding time, and mold temperature are discussed. The imprinting pressure was set to 0.6 MPa according to the results of Sect. 3.2. First, ultrasonic thermoforming experiments were performed with variation of the vibration time from 0.05 to 0.20 s. The holding time was set to 9.0 s, and the experiments were performed at room temperature.
The forming ratio for the outer band was evaluated for each condition, and compared in Fig. 10. It can be seen that the flat mold case shows a forming ratio between 68 to 74 %, which is higher than those of the plug-assisted thermoforming cases in Fig. 4, between 54 and 61 %. Considering that the proposed ultrasonic thermoforming took only 9.2 s at most including its vibration and holding time, it is noted that the proposed ultrasonic-assisted thermoforming is superior to the plug-assisted thermoforming in terms of productivity and quality. Furthermore, the curved mold case shows superior results; the forming ratio exceeded 90 % when the vibration time was longer than 0.1 s. However, in the case of the curved mold, forming fractures occurred when the vibration time was 0.2 s, as shown in Fig. 11. These fractures were expected to occur when excessive vibration was imposed. Thus, the vibration time was set to 0.1 s, with which the forming ratio was as high as 94 % without any forming fracture.
3.3.2 Effects of the holding time
Additional experiments were performed with variation of the holding time from 3.0 to 9.0 s, with an increment of 2.0 s. In these experiments, the imprinting pressure and vibration time were set to 0.6 MPa and 0.1 s. The experiments were performed at room temperature. The resulting forming ratios are compared in Fig. 12. The overall trend, where the curved mold case shows a higher forming ratio than the flat mold case, was similar with that of the previous result in Fig. 10. In the case of the curved mold, high forming ratios >90 % could be obtained when the holding time was longer than 5.0 s. Based on this result, the holding time was set to 5.0 s in order to reduce the processing time as well as to maintain a high forming ratio.
3.3.3 Effects of the mold temperature
Further experiments were performed with variation of the mold temperature from 25 to 100 °C, with an increment of 25 °C. The imprinting pressure, vibration time and holding time were set to 0.6 MPa, 0.1 and 5.0 s, respectively. Figure 13 shows the measured forming ratio at four mold temperatures for the flat and curved mold cases. It can be seen that the mold temperature did not exert a significant effect on the forming ratio, unlike the other processing parameters. This can be explained by the low thermal conductivity of the soft mold (1.30 W/m-K) such that the mold heating by the cartridge heaters does not affect the mold surface temperature significantly. Instead, mold heating affects only the outer region of the polymer film where it contacts the metal mold base. The outer region is then locally softened so that ultrasonic excitation is absorbed in that region, which can act as a negative effect on formability. Based on these results, the mold temperature was set to 25 °C (room temperature) without additional mold heating, as a way of minimizing energy consumption.
3.4 Results and discussion
Based on the results of the previous section, the best forming conditions were determined as 0.6 MPa imprinting pressure, 0.1 s vibration time, 5.0 s holding time, and 25 °C mold temperature. Ultrasonic-assisted thermoforming experiments were performed under these conditions, in which the forming ratios for the flat and curved molds were 68 and 95 %. To compare these results with the conventional thermoforming process, thermoforming experiments were also performed without the aid of ultrasonic excitation. In the thermoforming process, the mold was heated from the initial temperature (50 °C) to the target temperature (160 °C) for 100 s. The mold was then cooled by circulating cold water for 60 s, until the mold temperature reached 50 °C.
To investigate the forming characteristics of micro-corrugations, their surface profiles were measured using a laser microscope (VK-X200, KEYENCE Co., Japan). Figure 14a, b show the measured surface profiles of the micro-corrugations, in the cases of the flat and curved molds, respectively. The surface profile measurement was also performed for a thermoformed sample, as shown in Fig. 14c. It can be clearly seen that the curved mold sample (Fig. 14b) has better replication quality than the flat mold sample (Fig. 14a), but shows slightly lower replication quality than the thermoformed sample (Fig. 14c).
Figure 15 compares the measured sectional profiles of the micro-corrugations for the three cases. It can be seen that the curved mold case (452.4 ± 24.7 μm) shows similar forming height with that of the conventional thermoforming case (462.6 ± 34.2 μm), while the flat mold case shows much lower forming height (293.3 ± 6.2 μm). This indicates that the proposed ultrasonic-assisted thermoforming using the curved mold ensures high forming quality comparable to that of the conventional thermoforming process, while a small deviation existed due to the use of the soft mold and ultrasonic vibration.
Table 2 compares the cycle time for each forming method. The cooling time was determined by measuring the elapsed time when the mold temperature reached 50 °C after the forming stage. It can be seen that the ultrasonic-assisted thermoforming required only 19.5 s cycle time, when the curved mold was used. Considering that this cycle time corresponds to only 1/8th of the conventional thermoforming process case (160 s), the proposed ultrasonic-assisted thermoforming process can replace the conventional thermoforming process of microspeaker diaphragms, as a rapid and energy-efficient fabrication method.
4 Conclusion
In this study, an ultrasonic-assisted thermoforming process was developed to manufacture a microspeaker diaphragm in a short cycle time. In this process, ultrasonic vibration energy was used to soften the polymer film instead of the conventional thermal energy, by imposing repetitive deformation and friction. A thermoforming plug was designed to act as an ultrasonic horn, which was designed to resonate at a frequency of 27 kHz with a longitudinal vibration mode. Microfeatures as a positive shape of the microspeaker diaphragm were engraved on its outlet. To transfer ultrasonic vibration to a thin polymer film effectively, soft molds were used instead of typical metal molds. Two types of soft molds, a flat mold and a curved mold with the negative shape of the diaphragm, were investigated in terms of their heating characteristics and formability.
An experimental comparison revealed that the curved mold showed better heating characteristics and formability than the flat mold, because the negative features on the mold surface improved the transmission characteristics of the ultrasonic vibration and pressure. The best forming conditions were determined to be as follows: 0.6 MPa imprinting pressure, 0.1 s vibration time, 5.0 s holding time, and 25 °C mold temperature. Under these conditions and with the use of the curved mold, high forming ratio could be obtained: 97 % for the outer band and 72 % for the micro-corrugations, in comparison with those of the thermoformed sample.
Considering that the cycle time of the ultrasonic-assisted thermoforming was as short as 19.5 s, the proposed process is expected to replace the traditional thermoforming process, which required more than 160 s per cycle. Further studies are required to improve the forming ratio of the micro-corrugations in order to obtain better sound quality of microspeaker diaphragms.
References
Bae HJ, Park K (2015) Design and analysis of ultrasonic horn for polymer sheet forming. Int J Precis Eng Manuf Green Technol 3(1). doi:10.1007/s40684-016-0007-5
Collins P, Harkin-Jones EMA, Martin PJ (2002) The role of tool/sheet contact in plug-assisted thermoforming. Int Polym Process 17(4):361–369
Hosseini H, Vasilivich BB, Mehrabani-Zeinabad A (2006) Modeling of deformation processes in vacuum thermoforming of a pre-stretched sheet. Polym Plast Technol Eng 45(12):1357–1362
Hwang SM, Lee HJ, Hong KS, Kang BS, Hwang GY (2005) New development of combined permanent-magnet type microspeakers used for cellular phones. IEEE Trans Magn 41(5):2000–2003
Jung W, Park K (2014) Selective ultrasonic imprinting for micropattern replication on predefined area. Ultrasonics 54(6):1495–1503
Jung W, Lee HJ, Park K (2015) Micropattern replication characteristics in selective ultrasonic imprinting using negative masks. Int J Precis Eng Manuf 16(9):1999–2004
Khuntontong P, Blaser T, Schomburg WK (2009) Fabrication of molded interconnection devices by ultrasonic hot embossing on thin polymer films. IEEE Trans Electron Packag Manuf 32(3):152–156
Kim DC, Jeong HY (2015) An optimal design of the internal space in a micro-speaker module. Int J Precis Eng Manuf 16(6):1141–1147
Kim KM, Park K (2013) Numerical investigation on vibration characteristics of a micro-speaker diaphragm considering thermoforming effects. J Mech Sci Technol 27(10):2923–2928
Kwon JH, Hwang SM, School KSK (2007) Development of slim rectangular microspeaker used for minimultimedia phones. IEEE Trans Magn 43(6):2704–2706
Lee HJ, Park K (2014) Development of composite micro-patterns on polymer film using repetitive ultrasonic imprinting. Int J Precis Eng Manuf Green Technol 1(4):341–345
Li ZZ, Heo KS, Xuan DJ, Seol SY (2009) A study on cooling efficiency using 1-d analysis code suitable for cooling system of thermoforming. J Mech Sci Technol 23(3):607–613
Liao S, Gerhardy C, Sackmann J, Schomburg WK (2015) Tools for ultrasonic hot embossing. Microsyst Technol 21:1533–1541
Mekaru H, Takahashi M (2008) Ultrasonic nanoimprint on poly(ethylene terephthalate) at room temperature. Jan J Appl Phys 47:5178–5184
Mekaru H, Goto H, Takahashi M (2007) Development of ultrasonic micro hot embossing technology. Microelectron Eng 84(5–8):1282–1287
Michaeli W, Kamps T, Hopmann C (2011) Manufacturing of polymer micro parts by ultrasonic plasticization and direct injection. Microsyst Technol 17(2):243–249
Pillai MA, Deenadayalan E (2014) A review of acoustic energy harvesting. Int J Precis Eng Manuf 15(5):949–965
Sacristan M, Planta X, Morell M, Puiggali J (2014) Effects of ultrasonic vibration on the micro-molding processing of polylactide. Ultrason Sonochemistry 21(1):376–386
Seo YS, Park K (2012) Direct patterning of micro-features on a polymer substrate using ultrasonic vibration. Microsyst Technol 18(12):2053–2061
Shahosseini I, Lefeuvre E, Moulin J, Woytasik M, Martincic E, Pillonnet G, Lemarquand G (2013) Electromagnetic MEMS microspeaker for portable electronic devices. Microsyst Technol 19(6):879–886
Throne JL (1996) Technology of thermoforming. Hanser Verlag GmbH & Co, Munich
Acknowledgements
This research was financially supported by National Research Foundation of Korea (NRF) Grants funded by the Ministry of Education (Grant No. NRF-2013R1A1A2A10004709) and by a Technological Innovation R&D Program grant funded by the Small and Medium Business Administration (Grant No. S2166762), Republic of Korea.
Author information
Authors and Affiliations
Corresponding author
Rights and permissions
About this article
Cite this article
Bae, HJ., Lee, HJ. & Park, K. Ultrasonic assisted thermoforming for rapid fabrication of a microspeaker diaphragm. Microsyst Technol 23, 1677–1686 (2017). https://doi.org/10.1007/s00542-015-2740-z
Received:
Accepted:
Published:
Issue Date:
DOI: https://doi.org/10.1007/s00542-015-2740-z