Abstract
There are some problems in drilling Ti-6Al-4V/Al2024-T351 materials by traditional twist drill, such as big thrust force, big burr at outlet, and poor surface morphology. To solve these problems or reduce damage, low amplitude and high frequency vibrations are usually added in the direction of feed motion. This paper focuses on the study of geometric tool conventional drilling (CD) and ultrasonic-assisted drilling (UAD). Under ideal experimental conditions, through the combination of experiment and simulation, the drilling of laminated materials was investigated. The experimental results show that the UAD reduces the thrust force, burr height, torque, and temperature of laminated materials by 28.6%, 54.5%, 28.6%, and 13.2% respectively.
Similar content being viewed by others
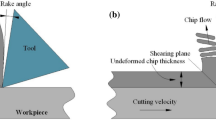
Avoid common mistakes on your manuscript.
1 Introduction
Drilling techniques are particularly important in the manufacture of composite laminates and are used in the joining of composites and other materials [1]. Drilling can approximately 40% of aerospace materials [2]. Along with the widespread applications of composite laminates, the machining accuracy has been required more and more strict. Due to the heterogeneity and anisotropy of composite laminates, delamination, shrinkage, and other damage will occur in the traditional drilling process [3, 4], which could not only directly reduce the surface finish and assembly tolerance, but also affect the fatigue strength of the hole, thus eventually hinder the service performance of the assembly parts [5,6,7]. Drilling is one of the main methods of material processing. In aerospace material manufacturing, the drilling process accounts for approximately 40% of the material removal process [8]. In practical applications, single-engine aircraft and large transport aircraft require 100,000 and 1 million fixed holes, respectively [9]. With the increasing requirements of material processing accuracy, more and more researches have been done on drilling. Many excellent researchers have studied drilling. Some researchers believe that using a drill with a larger apex angle can reduce tool wear and better remove chips when drilling CFRP/Ti [10]. Some researchers believe that increasing the spindle speed and reducing the feed rate can improve the quality of CFRP hole processing [11]. Some researchers have added texture to the edge and edge of the tool to reduce the drilling power and torque of titanium drilling [12]. Some researchers have conducted in-depth research on the formation of borehole burrs at the exit surface angle of the workpiece [13]. Some people have done in-depth research on how to reduce the problem of aluminum alloy drilling burrs [14]. The experimental study was analyzed by the Taguchi method. The influence of processing parameters on the burr was discussed from the aspect of variance. Through the design of cutting speed and feed rate parameters and the experiment of water cooling, the influence of the angle of the workpiece exit surface on the burr is discussed. It is difficult to meet the processing requirements of difficult materials by traditional processing methods [15]. Recently, a new technology has been used as an alternative to traditional drilling. Ultrasonic vibration is added to the ultrasonic-assisted drilling process. In this technique, the vibration of high frequency and low amplitude is superimposed on the movement of tool or working material [16,17,18]. In drilling, the addition of ultrasound can effectively reduce the cutting force during cutting, but as the frequency and amplitude increase, the reduction of cutting force decreases [19]. In the drilling process, the addition of ultrasonic vibration can promote the segmentation of the chips and improve the processing quality [20]. Adding ultrasonic vibration to the AL/SIC metal matrix drilling plays a role in reducing burrs [21]. With the continuous advancement of computer technology, many scholars use simulation combined with experimental methods to conduct research [22, 23].
Considering the above situation, this paper will study from two aspects. The first aspect is to study the drilling performance of geometric tools different from ordinary twist drills. The second aspect is to add ultrasonic vibration to the CD drilling process to explore its processing performance. First of all, two kinds of geometric cutters are modeled and compared in detail, and subsequently, the CD and UAD models are also established for numerical simulation by the use of DEFORM-3D finite element software. Secondly, the principle of UAD is simply analyzed. Last but not least, the experiments with different parameters (burr, thrust force, torque temperature) produced by different tools in CD and UAD were carried out and compared, and the results were analyzed.
2 Finite element modeling
Figure 1 shows the two tools used in this article. The first step and the second step cutting edge of the step drill are 0.667 mm, and h is 0.1212 mm. The lengths of the first and second cutting edges of the double-cone drill are 1.2 mm and 1 mm, respectively. UAD is a new processing method different from CD, which adds a certain frequency and amplitude to the original CD. Due to the frequency and amplitude, the drilling has changed from the original continuous cutting process to continuous stage cutting, and the mechanism of machining has changed dramatically. The rotational speed, feed rate, frequency, and amplitude of drilling have a significant influence on the machining effect of drilling. Reasonable parameter optimization can improve the machining quality of the workpiece and reduce tool wear. Changing the geometry of different twist drills can also greatly improve drilling performance.
The workpiece is a laminate composed of a titanium alloy and an aluminum alloy, and the material parameters of the titanium alloy and the aluminum alloy are shown in Table 1. Both the titanium alloy and the aluminum alloy have a thickness of 1.5 mm and a total of 3 mm. The radius of the workpiece is 6 mm and the diameter of the tool is 3.6 mm.
In this paper, finite element modeling is used to build a laminated material drilling model to dynamically simulate CD and UAD of laminated materials. The workpiece Al2024-T351/Ti-6Al-4V laminate is set as a molding material and is divided into 25,000 grids according to the relative grid size. The two-layer material adds side boundary conditions, and the workpiece has a zero velocity on the Z-axis so that the workpiece cannot move during the drilling process and imposes constraints on the two-layer material contact interface. The drill bit is set to a rigid body for better finite element simulation. The operation step is set to 3000, the time step is set to 0.0002 s, and the system will be stored once every 50 steps. Drilling in finite element simulation is traditional machining. Ultrasonic-assisted drilling requires MATLAB software to calculate the speed of each time period. The numerical values are imported into the finite element simulation to add ultrasonic-assisted vibration to ordinary drilling.
Tables 2 and 3 show the experimental parameters and the geometric parameters of the two drill bits, respectively, to facilitate the analysis of the experimental results. Table 4 shows the chemical composition of the workpiece titanium alloy and aluminum alloy.
3 Principle analysis of CD process and thrust force model
It is necessary to study the cutting edge force in drilling engineering. The cutting edge force can be regarded as the sum of several components. As shown in Fig. 2, an orthogonal cutting model is established to analyze the cutting edge force. Ignore the power of the blade.
where the average primary cutting edge thrust force is expressed as Fth (N), the correction factor is expressed as ζ, the primary cutting edge elemental thrust force is expressed as ΔFth (N), the point angle is expressed as 2 p, the dynamic feed angle is expressed as ηd, the material shear strength is expressed as ks (Mpa), the dynamic uncut chip thickness of primary cutting edge element is expressed as hd (mm), the width of each element is expressed as ΔL (mm), the dynamic friction angle is expressed as λn, the dynamic friction angle is expressed as λnd, the normal rake angle is expressed as γn, the dynamic normal rake angle is expressed as γnd, the dynamic shear angle is expressed as ϕnd, the effective radius of the ith element is expressed as ri (mm) (see Fig. 2), the drill radius is expressed as R, the chisel edge angle is expressed as ψ, the drill web thickness is expressed as 2T (mm), and the drill helix angle is expressed as β0.
4 Experimental work
This section studies the thrust forces generated by the Ti/Al laminated material during drilling with two different drill bits (step drill, double cone drill). The effects of cutting speed and frequency on the thrust force of two kinds of cutting tools were investigated experimentally and the instrument is shown in Fig. 3 [24]. The maximum spindle speed of the experimental device is 10000 RPM and the rated power is 15kw.The Al/Ti laminated material is clamped onto a piezoelectric dynamometer to accurately measure thrust during drilling. The height of the burr was measured by a 3D laser scanning microscope after drilling. The macroscopic morphology and microstructure of drilling were observed by optical scanning electron microscope. The experiment was designed with multiple cutting speed factors, and each experiment was repeated 3 times for the accuracy of the experiment.
Figure 4 clearly shows the axial forces under different processing conditions (50 m/min, 70 m/min, 90 m/min) and analyzes and discusses the results. The errors of experimental data and simulation data in titanium alloy drilling are 4.3%, 4.8%, and 5%, respectively. The errors of experimental data and simulation data in aluminum alloy drilling are 5.1%, 4.4%, and 5.7%, respectively. The reliability of the simulation results is verified and it is worthy of trust. The thrust force increases as the rotational speed increases. When the drill bit is drilled at a relatively high speed, the high temperature is generated and the tool wear is aggravated, so that the tool cannot be processed normally and the thrust force is also increased. The right speed is the key factor in ensuring material processing.
5 Explore the influence of thrust force on exit burr
During the drilling process, the material at the edge of the hole is not cut by the cutting edge, and after being deformed, it is bonded to the exit to form a burr. The entry burr, exit burr, and delamination gap will appear in CD of workpiece, as shown in Fig. 5. The following is a detailed description of the formation process of the exit burr.
5.1 Material deformation model
It is a common sense that the material’s resistance to deformation decreases along with the thinning of workpiece during the drilling and the existence of cutting heat could further aggravate the plastic deformation. Due to the abovementioned phenomenon, part of the material at the bottom of the hole will remain around the edge when the drill bit penetrates the workpiece, thus eventually forms burrs.
The formation of burr is a continuous process, which can be simply divided into three main stages [25]. Figure 6 is a schematic diagram of the plastic deformation of the material, which can clearly show the forming process of burrs. The initial stage of burr formation is material extension deformation (□ABCD to □HBCK), In the middle of the burr formation, the material is bent and deformed to form a burr (□HBCK to □EJBH). At the end of the burr formation, the material is bent and deformed to form the final burr (□EJBH to □MNJL).
5.2 The mechanism of thrust force
The study of thrust in the drilling of laminated materials is very important. Too much thrust will reduce the accuracy of the workpiece, so it is necessary to reduce the thrust. In this paper, the thrust of two kinds of drill bit drilling materials is explored, and CD and UAD are discussed.
As shown in Figs. 7 and 8, the experimental results of the thrust force can be clearly observed. When the cutting speed of step drill and double cone drill is 50 m/min, the mean thrust force of the UAD (20 KHz) Ti-6Al-4V laminate is 24.8% and 25.0% lower than that of CD, respectively. When the cutting speed of step drill and double cone drill is 50 m/min, the mean thrust force of the UAD (20 KHz) Al2024-T351 laminate is 10.4% and 10.2% lower than that of CD, respectively. At the same time, the related researchers used the ultrasonic-assisted drilling UAD to reduce the thrust force generated by CD by 20% [26]. As the speed increases, the drilling force also increases. The thermal conductivity of the titanium alloy is small, and as the rotational speed increases, the cutting temperature also increases, thereby increasing the thrust. The aluminum alloy has good thermal conductivity, and the cutting heat energy is effectively dissipated, so the thrust is only slightly increased when the rotational speed is increased. Compared to CD, UAD can greatly reduce the thrust. The vibration in the UCD process accelerates the chip breakage, and the chip takes away a lot of cutting heat, which causes the thrust to drop accordingly. In addition, the double cone drill produces a lower thrust than a step drill.
5.3 The mechanism of burr
During the drilling process, the material at the edge of the hole is not cut by the cutting edge, and after being deformed, it is bonded to the exit to form a burr. Export burrs can affect the assembly accuracy of parts, so the study of burrs is of great significance. This section studies the burrs generated by the Ti/Al laminated material during drilling with two different drill bits (step drill, double cone drill). The burrs produced by CD and UAD are compared and analyzed by simulation experiments. In order to more clearly observe the burr of the laminated material drilling, the cylindrical workpiece is cut through the center of the circle. The height of the workpiece burr can be clearly seen to facilitate analysis of the experimental results.
Figure 9 is the drilling simulation diagram at cutting speed of 50 m /min, feed rate of 1 mm/r and vibration frequency of 40 Khz. The burr height produced by CD and UAD can be clearly seen. As shown in Fig. 10, the burr height produced by step drilling in UAD (40 Khz) reduced by 54.5% compared with CD (0 Khz) and the one produced by double cone drilling decreased by 65%. The burr height becomes lower and lower with the increase of frequency. The stepping drill produces more thrust than the double-cone drill. The excessively high drilling temperature softens the material and increases the material’s extensibility, so it is easier to produce larger burrs. The thrust force has a certain influence on the exit burr and the plastic deformation has a positive correlation with the thrust force, which makes it easier for the bottom material of the workpiece to be remained on the edge of the hole wall. UAD the form of motion of the drill bit, and the axial vibration of the tool causes the chisel edge to drill the workpiece earlier than CD. After the chisel is drilled, the residual thickness of the outlet is larger than that of CD, the rigidity of the outlet residual material is strong, and the deformation along the feeding direction is reduced, so the burr height is lowered. In UAD, the regular contact of the workpiece on the surface to be machined is beneficial for the dissipation of cutting heat and the diminution of deformation of the hole at the bottom material, which makes a great contribution to the inhibition of burr.
6 The analysis of torque
The study of torque in the drilling of laminated materials is necessary. Excessive torque will cause great wear to the cutter; thus, the reduction of torque and cutting tool wear has become a hot research topic of many experts. This paper presents a comparative study of the torques produced in CD and UAD.
As shown in Fig. 11, the torque of the two types of drill bits for drilling the laminate material in the case of CD (90 m/min, 1 mm/r, and 0 Khz) and UAD (90 m/min, 1 mm/r, and 40 Khz) is compared. When the tool first enters the titanium alloy, the torque increases sharply due to the contact area between the tool and the workpiece. When the cutting edge is fully engaged with the workpiece, the torque reaches a maximum and remains stable. As the drill bit drills into the aluminum alloy, the torque begins to drop and then remains stable. When the tool passes through the workpiece, the torque is reduced to zero. Where the titanium alloy and aluminum alloy are excessive, the stepping drill produces a sharp drop in torque and the torque produced by the double cone drill is slowly reduced. This is related to the two tool configurations, and there is no connection between the second step of the stepping drill and the first step. The second step drills the titanium layer when the first step drills the aluminum layer. The double cone drill has two cutting edges that make the torque gradient relatively small. The greater hardness of titanium alloy than that of aluminum alloy produced a greater torque during drilling. The torque produced by step drilling in UAD of titanium alloy layer is 28.6% lower than that of CD, while the one by using aluminum alloy layer is only slightly lower. The torque produced by double cone drilling in UAD of titanium alloy layer is 35.7% lower than that of CD, while the one by using aluminum alloy layer is only slightly lower. As a consequence, UAD machining can effectively reduce the torque, reduce tool wear and improve tool life.
7 The mechanism of temperature
Drilling temperature has a certain impact on tool wear and too high temperature will accelerate tool wear; thus, the temperature generated by two types of drilling tools was studied in this chapter. As shown in Fig. 12, the temperature simulation of the drilling of the laminate material in the case of CD (50 m/min, 1 mm/r, and 0 Khz) and UAD (50 m/min, 1 mm/r, and 20 Khz) is compared between the two drill bits. The highest temperature in the step drilling process occurs on three parallel blades. The highest temperature in the process of double cone drilling is generated on the secondary cutting edge. In the research on the drilling temperature of the workpiece, the workpiece is divided in order to better study and analyze the workpiece temperature. The workpiece and tool temperature distribution can be clearly seen to facilitate analysis of the experimental results. Initial stage: due to the extrusion of the drill bit, the workpiece begins to gradually deform and form chips. As the chips are discharged as the drill rotates, the cutting force and temperature rise sharply. In-depth stage: The cutting process is a process of extrusion deformation and cutting, undergoing four stages of elastic deformation, plastic deformation, cracking, and cutting. At this stage, the cutting force and temperature tend to be stable. At the end stage: the drill bit is drilled through the bottom surface of the workpiece, and the cutting force and temperature are decreasing.
As shown in Figs. 13 and 14, the temperature produced by drilling the laminate material with different parameters is clearly shown. The drilling process has a great influence on the machining quality of the workpiece and the wear of the tool, so more and more people have conducted in-depth research on the drilling temperature. Different methods of drilling temperature measurement will produce different results. How to measure accurately is a topic worthy of further study [27,28,29,30,31]. Under the same conditions, the temperature produced by step drilling is higher than that of by double cone drilling. When the cutting speed of step drill and double cone drill is 50 m/min, the temperature of the UAD (20 KHz) Ti-6Al-4V laminate is 4.0% and 3.6% lower than that of CD, respectively. When the cutting speed of step drill and double cone drill is 50 m/min, the temperature of the UAD (20 KHz) Al2024-T351 laminate is 10.1% and 9.1% lower than that of CD, respectively. UAD is a discontinuous process in which the cutting heat changes in pulse form. During extremely short chip formation, heat does not have time to travel deeper into the metal, so the average cutting temperature is lower. UAD makes chips more prone to fracture, which takes away a lot of heat, so the temperature of UAD is lower than that of ordinary drilling. Drilling temperature increases with the increase of cutting speed and decreases with the increase of frequency.
8 The mechanism of effective stress
As shown in Fig. 15, the effective stress simulation of the drilling of the laminate material in the case of CD (50 m/min, 1 mm/r, and 0 Khz) and UAD (50 m/min, 1 mm/r, and 20 Khz) is compared between the two drill bits. Comparing the effective stresses produced by drilling two different tools. It is obviously that the distribution of the effective stress in each position of the workpiece in the process of machining can be seen. In order to more clearly observe the distribution of the equivalent stress during the drilling of the laminated material, the cylindrical workpiece is cut through the center of the circle. The equivalent stress distribution of the upper and lower layers of the laminate can be clearly seen to facilitate analysis of the experimental results.
The effective stress is mainly distributed in the contact area between the tool tip and the workpiece and the contact area of the two layers of the workpiece. During the UAD process, the cutter and the chip are a continuous contact separation process. The tool and the chip are in a separated state for a long time, and the equivalent stress generated is relatively small. As shown in Figs. 16 and 17, the effective stress produced by drilling the laminate material with different parameters is clearly shown. When the cutting speed of step drill and double cone drill is 50 m/min, the effective stresses of the UAD (20 KHz) Ti-6Al-4V laminate is 6.2% and 6.1% lower than that of CD, respectively. When the cutting speed of step drill and double cone drill is 50 m/min, the effective stresses of the UAD (20 KHz) Al2024-T351 laminate is 9.7% and 8.1% lower than that of CD, respectively.
9 Conclusion
In this paper, CD and UAD studies of Ti-Al-4V/Al2024-T351 laminated materials are carried out, and the experimental results of two kinds of geometric bit (step drill and double cone drill) processing are compared.
- (1)
The mean thrust force of step drilling and double cone drilling in titanium UAD is 24.8% and 25.0% lower than that of CD, respectively. The results of aluminum layer were 10.4% and 10.2%, respectively. When compared with CD, step drill and double cone drill could produce 54.5% and 65% lower exit burrs in laminated UAD. In CD, the burr becomes higher as the thrust increases, and the UAD process can greatly reduce the height of the burr.
- (2)
Step drilling and double cone drilling reduced the torque in UAD by 28.6% and 35.7% when compared with CD. As a consequence, UAD machining can effectively reduce the torque, reduce tool wear and improve tool life.
- (3)
The temperature and equivalent stress generated by the UAD in the titanium layer using stepped and double cone drills were 13.2%, 11.9%, and 6.6%, respectively, lower than the use of CD. The temperature and equivalent stress generated by the UAD in the aluminum layer using stepped and double cone drills were 13.2%, 11.9% and 6.6%, respectively, lower than the use of CD. UAD is a discontinuous process in which the cutting heat changes in pulse form. During extremely short chip formation, heat does not have time to travel deeper into the metal, so the average cutting temperature is lower.
References
Geng D, Liu Y, Shao Z, Lu Z, Cai J, Li X, Jiang X, Zhang D (2019) Delamination formation, evaluation and suppression during drilling of composite laminates: a review. Compos Struct 216:168–186
Subramanian K, Cook NH (1997) Sensing of drill wear and prediction of drill life. Trans ASME J Eng Indus 99:295–301
Liu D, Tang Y, Cong WL (2012) A review of mechanical drilling for composite laminates. Compos Struct 94:1265–1279
Uhlmann E, Mullany B, Biermann D, Rajurkar KP, Hausotte T, Brinksmeier E (2016) Process chains for high-precision components with micro-scale features. CIRP AnnManuf Technol 65:549–572
Caprino G, Tagilaferri V (1995) Damage developments in drilling glass fiber reinforced plastics. Int J Mach Tools Manuf 35:817–829
Mishra R, Malik J, Singh I, Davim JP (2010) Neural network approach for estimate the residual tensile strength after drilling in uni-directional glass fiber reinforced plastic laminates. Mater Des 31:2790–2795
Geng D, Zhang D, Li Z, Liu D (2017) Feasibility study of ultrasonic elliptical vibrationassisted reaming of carbon fiber reinforced plastics/titanium alloy stacks. Ultrasonics 75:80–90
Tsao C (2008) Experimental study of drilling composite materials with step-core drill. Mater. Des 29:1740–1744
Krishnaraj V, Vijayarangan S, Suresh G (2005) An investigation on high speed drilling of glass fibre reinforced plastic (GFRP). Indian J. Eng. Mater. Sci 12:189–195
SenthilKumar M, Prabukarthi A, Krishnaraj V (2013) Study on tool wear and chip formation during drilling carbon fiber reinforced polymer (CFRP)/Titanium alloy (Ti6Al4V) stack. Proce. Eng 64:582–592
Isbilir O, Ghassemieh E (2013) Numerical investigation of the effects of drill geometry on drilling induced delamination of carbon fiber reinforced composites. Compos. Struct 105:126–133
Niketh S, Samuel GL (2016) Surface texturing for tribology enhancement and its application on drill tool for the sustainable machining of titanium alloy. J. Clean. Prod 167:253–270
Min S, Dornfeld DA, Nakao Y (2003) Influence of exit surface angle on drilling Burr formation. J Manuf Sci Eng 125(4):637–644
Kundu S, Das S, Saha PP (2014) Optimization of drilling parameters to minimize burr by providing back-up support on aluminium alloy. Procedia Engineering 97:230–240
Ni CB, Zhu LD, Liu CF, Yang ZC (2018) Analytical modeling of tool-workpiece contact rate and experimental study in ultrasonic vibration-assisted milling of Ti–6Al–4 V. Int J Mech Sci 142–143:97–111
Barani A, Amini S, Paktinat H, Tehrani AF (2014) Built-up edge investigation in vibration drilling of Al2024-T6. Ultrasonics 54(5):1300–1310
Amini S, Khosrojerdi M, Nosouhi R, Behbahani S (2014) An Experimental investigation on the machinability of Al2O3 in vibration-assisted turning using PCD tool. Mater. Manuf. Processes 29(3):331–336
Amini S, Paktinat H, Barani A, Tehran AF (2013) Vibration drilling of Al2024-T6. Mater. Manuf. Processes 28(4):476–480
Kong C, Wang DZ (2018) Numerical investigation of the performance of elliptical vibration cutting in machining of AISI 1045 steel. Int J Adv Manuf Technol 98(1–4):715–727
Chang SS, Bone GM (2005) Burr size reduction in drilling by ultrasonic assistance. Robot Comput Integr Manuf 21(4):442–450
Kadivar M et al (2012) Burr size reduction in drilling of Al/SiC metal matrix composite by ultrasonic assistance. Adv Mater Res 410:279–282
Wang YS, Sui LN, Yin ZY, Wang XL, Liu NN, Guo H (2017) A hybrid prediction for wind buffeting noises of vehicle rear window based on LES-LAA method. Appl Math Model 47:160–173
Paktinat HP, Amini S (2017) Ultrasonic assistance in drilling: FEM analysis and experimental approaches. Int J Adv Manuf Technol 92(5–8):2653–2665
Zhu ZJ, Guo K, Sun J, Li JF, Liu Y, Zheng YH, Chen L (2018) Evaluation of novel tool geometries in dry drilling aluminium 2024-T351/titanium Ti6AL4V stack. J Mater Process Tech 259:270–281
Kim J, Dornfeld DA (2002) Development of an analytical model for drilling burr formation in ductile materials. J Eng Mater Technol 124(2):192
Pujana J, Rivero A, Celaya A, Lo’pez de Lacalle LN (2009) Analysis of ultrasonic-assisted drilling of Ti6Al4V. Int J Mach Tools Manuf 49(6):500–508
Li R, Shih AJ (2007) Spiral point drill temperature and stress in high-throughput drilling of titanium. Int J Mach Tools Manuf 47(12-13):2005–2017
Bono M, Jun N (2002) A model for predicting the heat flow into the workpiece in dry drilling. J Manuf Sci Eng 124(4):773–777
Kalidas S, Kapoor SG, DeVor RE (2002) Influence of thermal effects on hole quality in dry drilling, Part 1: A thermal model of workpiece temperatures. J Manuf Sci Eng 124(2):258–266
Ueda T, Nozaki R, Hosokawa A (2007) Temperature measurement of cutting edge in drilling-effect of oil mist. CIRP Annals 56(1):93–96
Wei L, Wang D (2019) Comparative study on drilling effect between conventional drilling and ultrasonic-assisted drilling of Ti-6Al-4V/Al2024-T351 laminated material. Int J Adv Manuf Technol 103(1-4):141–152
Author information
Authors and Affiliations
Corresponding author
Additional information
Publisher’s note
Springer Nature remains neutral with regard to jurisdictional claims in published maps and institutional affiliations.
Rights and permissions
About this article
Cite this article
Wei, L., Wang, D. Effect of ultrasound-assisted vibration on Ti-6Al-4V/Al2024-T351 laminated material processing with geometric tools. Int J Adv Manuf Technol 106, 219–232 (2020). https://doi.org/10.1007/s00170-019-04637-7
Received:
Accepted:
Published:
Issue Date:
DOI: https://doi.org/10.1007/s00170-019-04637-7