Abstract
Low-density sandwich panels consisting of an oil palm wood core overlaid with a rubberwood veneer face were manufactured. Effects of two types of grain orientation of the oil palm wood core (parallel and perpendicular to board surface) and three different veneer thicknesses (0.7, 1.8 and 2.7 mm) and core densities (223 ± 14, 301 ± 35 and 418 ± 33 kg/m3) on some physical and mechanical properties of the boards were investigated. Results showed that higher core density increased the values of thermal conductivity, screw withdrawal resistance, modulus of rupture and modulus of elasticity but decreased the value of water absorption without effect on thickness swelling of the boards. Boards with the core grain direction oriented perpendicular to panel’s surface possessed lower value of thickness swelling but higher values of thermal conductivity and strain at fracture when the board failed in a mode of core shear under bending test than those of the others. Finally, the relationship between board density and the measured physical and mechanical properties of the oil palm wood core sandwich panels overlaid with a rubberwood veneer expressed as mathematical equations could be used to predict and design the expected properties of this type of sandwich board.
Similar content being viewed by others
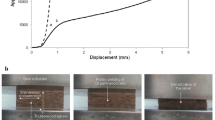
Avoid common mistakes on your manuscript.
1 Introduction
For years, sandwich structures consisting of two thin, stiff and strong skins separated by a thick, light and weaker core have been utilized in many applications such as aeronautical structures, high speed marine crafts and building construction (Allen 1969; Ashby et al. 2000; Barala et al. 2010; Crump and Dulieu-Barton 2010; Panjehpour et al. 2013). The advantage of this structure is that the flexural and shear stiffness can be easily achieved by increasing the core thickness to increase the second moment of inertia with little increase in weight. It provides an efficient structure with a high strength to weight ratio for resisting bending and buckling loads (Zenkert 1997; Hoo et al. 2010). In addition, an energy-efficient structure can also be achieved due to the insulation property of the low density core (Ashby et al. 2000). Thus, these structures are widely used in residential construction as structural insulated panels (SIPs) in walls, floors and roofs (Ashby et al. 2000; Borjesson and Gustavsson 2000). Traditional SIPs consist of either a plywood or oriented strand board (OSB) face sheet and a light weight plastic foam core (Terentiuk and Memari 2012; Vaidya et al. 2010; Mousa and Uddin 2011; Mullens and Arif 2006). The insulation capability can be adapted by varying the foam type and thickness (Tracy 2000).
The oil palm tree is one of the economic crops found in tropical regions. Generally, oil palm trees are cut down for replanting at the age of 25–30 years when the oil palm fruit yield is uneconomical (Sulaiman et al. 2012; Lim and Khoo 1986). Most oil palm biomass is left over the plantation area as waste material. It is usually burned to dispose of it, causing air pollution (Abdul Khalil et al. 2010; Suhaily et al. 2012). This effect can be reduced if there is use for biomass. The oil palm trunk is of interest for use as an alternative raw material for the core section of SIP production because it has a relatively low density with an average value of 235 kg/m3 (Lim and Khoo 1986).
An oil palm trunk is comprised of primary vascular bundles embedded in soft parenchymatous tissue. Each vascular bundle consists of a fibrous sheath with phloem, xylem and parenchyma cells. The number of vascular bundles gradually decreases from the peripheral region to the center of the cross section and increases from the butt end to the top of the oil palm trunk (Lim and Khoo 1986). Oil palm wood density, directly related to the number and thickening of the vascular bundles (Lim and Khoo 1986), varies both radially and vertically. The density in the peripheral region at the bottom part of the stem is as high as 575 kg/m3 and gradually decreases to 190 kg/m3 at the center of the cross section (Lim and Gan 2005). Physical and mechanical property values also vary as a result of the variation of the density (Lim and Khoo 1986; Haslett 1990). With its low density around the central region of the cross section, it is possible for oil palm wood to be used as a SIP core section.
The main objective of this study was to evaluate the feasibility of using oil palm wood as a core for SIP production. A thin rubberwood veneer was used to overlay the core. The effects of veneer thickness, core density and core grain direction on the physical (board density, thickness swelling, water absorption and thermal conductivity) and mechanical properties (screw withdrawal resistance, modulus of rupture and modulus of elasticity) of the boards obtained were investigated.
2 Materials and methods
2.1 Raw material preparation
Commercial rubberwood veneers with three different thicknesses (0.7, 1.8 and 2.7 mm) were supplied by Phang-Nga Timber Industries Co., Ltd. from Phang-Nga, Thailand. They were used as the face of the sandwich panels. For 1 month, these veneers were placed in a conditioning room at a temperature of 20 °C with humidity of 65 %. The final moisture content before taken for panel production was 12 %.
The oil palm trees at about 25 years of age were from a plantation in Surat Thani, Thailand. They were cut down and transported to dry to the final moisture content of 12 % in the laboratory kiln (Eurasia, Singapore) at the Wood Science and Engineering Research Unit of Walailak University, Nakhon Si Thammarat, Thailand. Two types of oil palm wood specimens were prepared with respect to the grain direction of the flat plane: parallel (PR specimen) and perpendicular (PP specimen). The dimensions of each piece were 13 cm × 13 cm (cross-section) × 2 cm (thickness) as shown in Fig. 1. These specimens were abraded on both flat plane sides by using a planar plate with 40 grit rough sandpaper to achieve the required thickness of 14.6, 16.4 and 18.6 mm for the PR specimens and 14.6 mm for the PP specimens. These oil palm wood pieces were then kept in a conditioning room at a temperature of 20° C and humidity of 65 % to make the final moisture content of 12 % at the time of board manufacturing. At this moisture content, the PR specimens were classified into three different densities ranging from 200 to 250 kg/m3 (ρ central ), 300–350 g/m3 (ρ middle ) and 400–450 g/m3 (ρ outer ), respectively. The PP specimens were selected only at the density range of 300–350 kg/m3 (ρ middle ) to produce the core.
Melamine urea formaldehyde (MUF) adhesive supplied by Dynea Krabi Co., Ltd. from Songkla, Thailand was used for bonding face and core layer in this experiment. The MUF adhesive at 30 °C has a viscosity of 190 cps, solid content of 55.2 %, pH level of 9.36, density of 1.212 and gel time of 43 s.
2.2 Board manufacturing
Eight pieces of oil palm wood specimens with the same grain direction and density range were bonded side to side with polyvinyl acetate (PVAc) adhesive to form a rectangular core with dimensions of 260 mm (width) × 520 mm (length). MUF resin was spread onto the rough surface of the rubberwood veneer with a hand brush. The resin content used in this experiment was 250 kg/m2 (solid basis) (Srivaro et al. 2014). The glued veneers were then placed on the top and bottom surfaces of the prepared core so that the grain of the veneer was oriented parallel to the panel length. Two types of panels, having the grain direction of oil palm core aligned parallel (PR boards) and perpendicular (PP boards) to the surface (Fig. 2a, b, respectively), were manufactured. The assembled mats were then put into the placing space of a single-opening hydraulic lab hot press (60 × 60 cm2 Wabash MPI, USA). Two 20 mm thick steel stoppers were placed on both sides of the assembled mat to control the final thickness of the board during pressing. The assembled mats were then pressed with the platen heated to 160 °C at 2 MPa for 5 min.
The PR boards were produced at three different veneer thicknesses (0.7, 1.8 and 2.7 mm) and three different core densities (ρ central , ρ middle and ρ outer ). Both faces of the sandwich boards had the same veneer thickness. The thickness of the core (18.6, 16.4 and 14.6 mm) was chosen such that the thickness of the boards produced was 20 mm. The PP boards were produced using the 2.7 mm thick rubberwood veneer as faces and the 14.6 mm thick oil palm wood with density of ρ middle as cores. Three replications were performed in each treatment, so a total of 27 PR boards and 3 PP boards were manufactured.
2.3 Property testing of the boards
The obtained boards were cut into test specimens and kept in the conditioning room at a temperature of 20 °C and humidity of 65 % for at least 1 month until constant weight was attained. The following properties were then determined:
-
Board density (ρ B ) evaluation was conducted on specimens with the dimensions of 50 mm (width) × 50 mm (length) × 20 mm (thickness) according to EN 323 (1993).
-
Thickness swelling (TS) and water absorption (WA) were determined using specimens with the dimensions of 50 mm (width) × 50 mm (length) × 20 mm (thickness) by water immersion at 20 °C for 24 h in accordance with EN 317 (1993) and ASTM D 1037-12 (2012), respectively.
-
Thermal conductivity (λ) was determined on specimens with the dimensions of 190 mm (width) × 190 mm (length) × 20 mm (thickness) in accordance with ASTM C177 (2010). This test method was used to measure the steady-state heat flux through flat specimens using a thermal conductivity analyzer (Anacon model 88, USA).
-
Screw withdrawal resistance (SWR) was determined for both the face and edge sides of specimens with the dimensions of 75 mm (width) × 75 mm (length) × 20 mm (thickness) in accordance with EN 320 (2011) using a 150 kN universal testing machine (Lloyd, UK).
-
Modulus of elasticity (MOE) and modulus of rupture (MOR) were determined by three-point static bending test on specimens with the dimensions of 50 mm (width, b) × 500 mm (length parallel to the veneer grain direction) × 20 mm (thickness, d) in accordance with EN 310 (1993) using a 150 kN universal testing machine (Lloyd, UK). The test span length (L) was 400 mm. During this test, the beam was also recorded on a video recorder to pursue its progressive failure.
Duncan’s range tests were conducted to determine significant differences between mean values.
3 Results and discussions
The average values of the physical and mechanical properties of the sandwich boards are shown in Table 1. Each property is now discussed.
3.1 Board density
The obtained board densities are below 500 kg/m3 (Table 1), therefore these boards may be classified as lightweight materials (Youngquist 1999). According to a rule of mixtures, the sandwich board density is a combination of densities of rubberwood veneer face (ρ f ) and oil palm wood core (ρ c ). In addition, since the amount of adhesive used is large in the core, an apparent core density (\( \rho_{c}^{*} \)) should also account for weight of the adhesive (1.25 g for the test specimen with 50 mm × 50 mm cross-section with MUF equivalent to a 250 g/m2 solid basis). The board density (ρ B ) value can then be expressed as
where V f is volume fraction occupied by the face (which is equal to 2t/d where t is the face thickness and d is the board thickness). By substituting the values of apparent core densities (\( \rho_{c}^{*} \)) to be 248 ± 14, 326 ± 35 and 443 ± 33 kg/m3, calculated for three different oil palm wood densities (ρ central , ρ middle and ρ outer , respectively) and the rubberwood veneer density (ρ f ) of 633 ± 56 kg/m3 into Eq. 1, the board densities as a function of volume fraction of veneer face are obtained for each oil palm wood core density. These predicted values agree well with the ones obtained by the experiments as shown in Fig. 3.
3.2 Thickness swelling and water absorption
The thickness swelling (TS) percentages of the sandwich panels after being soaked in water at 20 °C for 24 h are shown in Table 1. Statistical analysis reveals that different thicknesses of the veneers and different densities of the oil palm wood core within the ranges studied have no significant effect on TS of the PR board (average value of 3.8 ± 0.4 %). The TS value of the PP boards (average value of 2.0 ± 0.3 %) was about half of the PR boards with respect to the board having the same core density of ρ middle . Most of the parenchyma cells within oil palm wood, roughly spherical in shape with extremely thin walls and a large lumen (Lim and Khoo 1986), contribute more or less to the approximate similarity of the shrinkage/swelling values in both radial and tangential directions (Sulaiman et al. 2012). As a result, the alignment of microfibril orientations in fiber cell walls which are aligned nearly parallel to the longitudinal axis (Shinoj et al. 2011) of the oil palm wood should be responsible for the different TS of the PR and PP boards. It is noted that the TS value of this type of sandwich panel is much lower than a requirement of OSB type 2 (EN 300 1997) of 20 % and of typical southern pine plywood of 8.3 % (Biblis and Lee 1984), which are mostly used as a face for structural insulated panels.
The corresponding water absorption (WA) values of the boards after being soaked in water for 24 h are also shown in Table 1. Both the veneer thickness and core grain direction have no significant effect on the WA value of the boards. The WA value is, however, very dependent on core density and overall board density (ρ B ). The WA value, ranging from 51 to 172 %, decreases with increasing board density from 275 to 512 kg/m3 (Table 1). It is well known that saturated moisture content in wood has an inverse relation to specific gravity (Skaar 1972; Glass and Zelinka 2010). It is worth therefore to plot the WA value against the reciprocal of board density. Indeed, the WA value is inversely proportional to the board density as shown in Fig. 4 according to the following equation:
This result can be explained by the distribution of vascular bundles containing thick-walled fibrous sheath and thin-walled parenchyma cells in the oil palm wood core. More parenchyma cells are in the lower core density from the inner zone which can absorb more of the water than those of the higher density core from the outer zone where there are less parenchyma cells. Because of lower density (higher porosity) than those of other wood composites, sandwich panels made from oil palm wood overlaid with rubberwood veneers show greater WA values than those of other wood composites such as rice husk particleboard overlaid with European ash strands (Kwon et al. 2012) and medium density fiberboard laminated with European beech veneer (Büyüksari et al. 2012). However, the WA value of the sandwich panels produced is comparable to that of the oil palm plywood (Abdul Khalil et al. 2010).
3.3 Thermal conductivity
The average thermal conductivity value of the PP sandwich panels (0.111 W/m K) is about 44 % higher than that of the PR board (0.077 W/m K) of the same core density of ρ middle and veneer thickness of 2.7 mm (Table 1). Since parenchyma cells within the oil palm wood core are almost isotropic in shape, the elongated fiber cells which are aligned parallel and perpendicular to the surfaces of PR and PP sandwich boards, respectively, are responsible for the different thermal conductivities observed. The elongated fiber cells having relatively thick cell walls (Abdul Khalil et al. 2008) should act as shortcuts for heat conduction through thickness of the PP board. In addition, thermal conductivity of the PR sandwich boards (0.063–0.087 W/m K) appears to depend on density of the oil palm wood core and therefore the sandwich board density (360–539 kg/m3) as shown in Table 1. Thermal conductivity across grain of wood was reported to be proportional to wood density (Glass and Zelinka 2010). By plotting thermal conductivity data of all PR sandwich boards examined against their densities (Fig. 5), a linear relationship between thermal conductivity (λ) and board density (ρ B ) is obtained according to the equation:
It is interesting to note that by extrapolating this equation to the vertical axis (Fig. 5), where the value of board density is zero (roughly corresponding to air density), the value of thermal conductivity obtained is 0.025 W/m K. This coincides with thermal conductivity of air at 27 °C (0.026 W/m K) reported in literature (Lide 1998).
Thermal conductivity of the oil palm sandwich panel (0.06–0.11 W/m K) is much lower than that of traditional building materials such as red clay brick (0.93 W/m K), hollow concrete block (0.68 W/m K), lightweight concrete brick panel walls (0.54 W/m K) (Alavez-Ramirez et al. 2012) and gypsum board (0.17 W/m K) (Ashby 1992). In addition, when compared to other developed structural insulated panels for housing such as low density fiberboard core overlaid with red meranti veneer (0.07 W/m K) (Kawasaki and Kawai 2006) and coconut fibre filled ferrocement sandwich panels (0.22 W/m K) (Alavez-Ramirez et al. 2012), the oil palm sandwich panel has good potential as structural insulated panel for use in building construction.
3.4 Screw withdrawal resistance
According to screw withdrawal resistance (SWR) data shown in Table 1, the screw withdrawal resistance on the face side (SWR f ) of the sandwich panels is higher than that on the edge side both in transverse direction (SWR et ) and in longitudinal direction (SWR el ) of oil palm wood core. When the screw was inserted in the edge side, it passed only the low density oil palm wood core. While embedding it into the face of the sandwich panel, the screw thread contacted both the rubberwood veneer face and oil palm wood core. The SWR f value appeared to be very dependent on board density (ρ B ), a combination of rubberwood veneer face and oil palm wood core densities. It is well established that SWR is wood density dependent (Taj et al. 2009; Cai and Ross 2010). By plotting the SWR f data of all PR sandwich panels examined against their densities (Fig. 6a), a linear relationship between SWR f and ρ B is obtained according to the equation:
Plots of a face-screw withdrawal resistance (SWR f ) against board density and edge-screw withdrawal resistance, b in transverse direction (SWR et ) and c in longitudinal direction of oil palm core (SWR el ) against oil palm wood core density. Solid lines represent the best fit to the experimental data
In the same manner, the edge-screw withdrawal resistance in transverse direction (SWR et ) and in longitudinal direction (SWR el ) of the oil palm wood core are proportional to density of the oil palm wood core section (ρ c ) (Fig. 6b, c, respectively) according to the equations:
It should be noted that, the constant in Eq. 4 (1.691), describing SWR f as a function of average board density of rubberwood veneer face and oil palm wood core (ρ B ), is close to that in Eq. 5 (1.659) describing SWR et as a function of oil palm core density (ρ c ) alone. This implies that SWR on side grain face depends mainly on average density of the wood section that the screw thread makes contact with regardless of the wood type. On the edge side, the SWR el in longitudinal direction is about 10 % lower than the SWR et in transverse direction at the same oil palm wood core density. Grain orientation of the oil palm wood core also affected the SWR f value. The average SWR f value of the PP sandwich panels (577 ± 45 N) is about 19 % lower than that of the PR board (713 ± 55 N) of the same core density of ρ middle and veneer thickness of 2.7 mm (Table 1). SWR in longitudinal direction has been reported to be lower than that in transverse direction of wood grain (Aytekin 2008; Cai and Ross 2010). Finally, the maximum SWR value of the oil palm wood core sandwich panels obtained within this work of 908 N is higher than that of minimum requirement of fiberboard specifications according to EN 622-3 (2004) of 450 N and JIS A 5905 (1994) of 300 N, respectively.
3.5 Bending performance
The static bending properties of the sandwich panels according to EN 310 (1993) are illustrated in Table 1. Modulus of elasticity (MOE) ranging from 5.5 to 9.3 GPa (Fig. 7a) and modulus of rupture (MOR) ranging from 16 to 46 MPa (Fig. 7b) of the sandwich panels (20 mm thick) were obtained using veneer face thickness of 0.7–2.7 mm and oil palm wood core density of 200–450 kg/m3. It should be noted that the MOE and MOR values of the sandwich panels produced are higher than those values of OSB type 2 with a density of 600 kg/m3 as required by EN 300 (1997) of 3.5 GPa and 18 MPa, respectively. Both MOE and MOR values increased with increasing veneer thickness and oil palm wood core density. Changes in the face thickness appeared to have a stronger effect on the values of MOE and MOR than changes in the oil palm wood core density.
Bending performance of oil palm sandwich panel a modulus of elasticity (MOE) and specific modulus of elasticity (MOE/ρB) and b modulus of rupture (MOR) and specific modulus of rupture (MOR/ρB) of sandwich panels at various oil palm core grain orientations, face thicknesses, oil palm wood core densities and span-depth ratios
All of the specimens (except the PR board with Vf = 0.27 and density of oil palm wood core of ρcentral) tested at span-depth ratio of 20 (L/d = 20) according to EN 310 (1993) failed with face yielding. Face yielding occurs when the tensile stress in the bottom face exceeded the allowable tensile stress of the rubberwood veneer (Hibberler 1997). The bending strength of the PR and PP boards having different core grain orientation with similar board density (ρmiddle) and veneer thickness (Vf = 0.27) is largely governed by the strength of rubberwood veneer in the bottom face. As a result, the core grain orientation appeared to have little influence on the MOR value. The MOR values of the PR and PP boards were similar (Table 1; Fig. 7b) and the load–deflection curves obtained from those boards were almost identical (data not shown).
It is worth to explore the effect of core grain orientation on the sandwich panel’s bending performance when failure mode of the panel is core shear. Mode of failure could change from face yielding to core shear on a shorter span length or higher thickness of the sandwich panel. Additional bending test was performed on the sandwich panel specimens with a shorter span length (L/d = 7). Obviously, the PR and PP boards tested at this span-depth ratio failed in the mode of core shear. Although the values of MOE and MOR of the PR and PP boards were similar (Fig. 7a, b), the load–deflection curves of those boards were quite different (Fig. 8). After reaching a point of maximum (points A and A′ in Fig. 8 used to evaluate the values of MOR for the PR and PP boards, respectively), an applied load of both boards gradually decreased with increasing displacement of the beam. While the PR board failed at a relatively short displacement of 5.86 mm, the PP board failed at a displacement of about four times longer (Fig. 8). Cracks were initiated at an angle of around 45° to the horizontal axis at half distance between the points of applied load and support commonly observed in the three-point bending test (Hibberler 1997). In addition, examination of fracture surfaces revealed that cracks were generated and propagated in weak parenchyma cells. Since parenchyma cells are spherical in shape and have relatively thin walls (Sulaiman et al. 2012), shear strength of the parenchyma cells should be isotropic. As a result, grain orientation of the oil palm wood core appeared to have no significant effect on the MOR value. On the other hand, crack propagation in the oil palm wood core of the PR and PP boards was different. Since cracks easily propagated parallel to the core grain orientation (along direction of the fiber cells) (B in Fig. 8), the PR board failed at a relatively short displacement when cracks reached the beam end (C in Fig. 8). Within the core section of the PP board, however, crack propagation in the horizontal direction was rather difficult. Thick-walled fiber cells aligned vertically in the PP board act as crack stoppers and are very effective to resist horizontal shear stress. It appeared that during the increment of displacement, new cracks were generated in the vertical channel of parenchyma cells located between the vertical fiber cells (B′ in Fig. 8). Alignment of the fiber cells at this point appeared to slightly deviate from the vertical direction as a result of the horizontal shear stress (B′ in Fig. 8). The final failure of the PP board occurred when the vertical shear stress component exceeded the vertical shear strength of the PP board, which continuously decreased as a result of generation of cracks in the vertical channel, to cause delamination of the face and core layers (C′ in Fig. 8). This mechanism increased plastic strain to failure and therefore toughness of the PP board by four times with respect to those of the PR board.
Finally, from the viewpoint of structural light weight panel, the MOE and MOR to density ratio should be considered. Specific MOR increased with increasing veneer thickness (Fig. 7b), while specific MOE remained roughly the same (Fig. 7a). On the other hand, increasing oil palm wood core density decreased the values of specific MOE and MOR, even though it slightly increased the MOE and MOR values. Therefore, increasing veneer thickness was more efficient in enhancing bending performance of the sandwich panel than increasing oil palm wood core density. In addition, the maximum values of specific MOE and MOR of the oil palm sandwich panels produced (22 and 0.10 MN m/kg, respectively) are higher than those of the oil palm plywood (3.5 and 0.04 MN m/kg, respectively) (Abdul Khalil et al. 2010).
4 Conclusion
The following conclusions can be drawn from this work.
-
1.
The oil palm wood core sandwich panel overlaid with a rubberwood veneer face was successfully manufactured with a density of less than 500 kg/m3, classified as lightweight materials.
-
2.
Thickness swelling of the sandwich panels was solely affected by core grain orientation (3.8 and 2.0 % for the core grain oriented parallel and perpendicular, respectively, to the panel’s surface), while water absorption (51–172 %) was inversely proportional to density of the panels.
-
3.
Thermal conductivity of the sandwich panels (0.06–0.11 W/m.K) was linearly increased with board density. The panels with the core grain oriented perpendicular to the panel’s surface showed higher thermal conductivity than those with the core grain oriented parallel to the panel’s surface.
-
4.
Screw withdrawal resistance of the sandwich panels both on the face side and the edge side was proportional to density of the wood section that the screw thread made contact with. On the edge side, screw withdrawal resistance in the transverse direction of the oil palm wood core was higher than that in the longitudinal direction.
-
5.
Modulus of rupture (16–46 MPa) and modulus of elasticity (5.5–9.3 GPa) of the sandwich panels were dependent on veneer thickness and oil palm wood core density. When the panels failed in a mode of core shear, core grain oriented perpendicular to the panel’s surface increased strain at fracture by about four times with respect to the one oriented perpendicular to the panel’s surface.
-
6.
The mathematical equations describing physical and mechanical properties of the sandwich panels as a function of board density could be used in the design of the oil palm wood core sandwich panels overlaid with rubberwood veneer face according to the properties required by various applications.
References
Abdul Khalil HPS, Siti Alwani M, Ridzuan R, Kamarudin S, Khairul A (2008) Chemical composition, morphological characteristics, and cell wall structure of malaysian oil palm fibers. Polym Plast Technol Eng 47(3):273–280
Abdul Khalil HPS, Nurul Fazita MR, Bhat AH, Jawaid M, Nik Fuad NA (2010) Development and material properties of new hybrid plywood from oil palm biomass. Mater Des 31:417–424
Alavez-Ramirez R, Chiñas-Castillo F, Morales-Dominguez VJ, Ortiz-Guzmana M (2012) Thermal conductivity of coconut fibre filled ferrocement sandwich panels. Constr Build Mater 37:425–431
Allen HG (1969) Analysis and design of structural sandwich panels. Pergamon press, London
Ashby MF (1992) Materials selection in mechanical design. Pergamon Press, Oxford
Ashby FM, Evans AG, Fleck NA, Gibson LJ, Hutchinson JW, Wadley HGN (2000) Metal foams: a design guide. Butterworth-Heinemann, Boston
ASTM D1037-12 (2012) Standard test methods for evaluating properties of wood-based fiber and particle panel materials. ASTM Annual Book of Standards. ASTM International, West Conshohocken
ASTM C177-10 (2010) Standard test method for steady-state heat flux measurements and thermal transmission properties by means of the guarded-hot-plate apparatus. Annual Book of Standards. American Society for Testing and Materials, ASTM International, West Conshohocken
Aytekin A (2008) Determination of screw and nail withdrawal resistance of some important wood species. Int J Mol Sci 9:626–637
Barala N, Cartiéb DDR, Partridgeb IK, Baleyc C, Daviesd P (2010) Improved impact performance of marine sandwich panels using through thickness reinforcement: experimental results. Compos B Eng 41(2):117–123
Biblis EJ, Lee WC (1984) Properties of sheathing-grade plywood made from sweetgum and southern pine. Wood Fiber Sci 16(1):86–92
Borjesson P, Gustavsson L (2000) Greenhouse gas balances in building construction: wood versus concrete from life-cycle and forest land-use perspectives. Energy Policy 28(9):575–588
Büyüksari Ü, Hiziroglu S, Akkiliç H, Ayrılmış N (2012) Mechanical and physical properties of medium density fibreboard panels laminated with thermally compressed veneer. Composites (Part B) 43:110–114
Cai Z, Ross RJ (2010) Mechanical properties of wood based composite materials. In: Ross RJ (ed) Wood handbook—wood as an engineering material, General Technical Report, FPL-GTR-190. USDA Forest Service, Forest Products Laboratory, Madison, Wisconsin, pp 12-1–12-12
Crump DA, Dulieu-Barton JM (2010) Performance assessment of aerospace sandwich secondary structure panels using thermoelastic stress analysis. Plast Rubber Compos 39(3–5):137–147
EN 300 (1997) Oriented strand boards (OSB)—definitions, classification and specifications. European Committee for Standardization (CEN), Brussels
EN 310 (1993) Particleboards and fibreboards—determination of modulus of elasticity in bending and of bending strength. European Committee for Standardization (CEN), Brussels
EN 317 (1993) Particleboards and fibreboards—determination of swelling in thickness after immersion in water. European Committee for Standardization (CEN), Brussels
EN 320 (2011) Particleboards and fibreboards—determination of resistance to axial withdrawal of screws. European Committee for Standardization (CEN), Brussels
EN 323 (1993) Wood-based panels—determination of density. European Committee for Standardization (CEN), Brussels
EN 622-3 (2004) Fibreboards specifications– Requirements for medium boards. European Committee for Standardization (CEN), Brussels
Glass SV, Zelinka SL (2010) Moisture relations and physical properties of wood. In: Wood handbook—wood as an engineering material, General Technical Report, FPL-GTR-190. USDA Forest Service, Forest Products Laboratory, Madison, Wisconsin, pp 4-1–4-19
Haslett AN (1990) Suitability of oil palm trunk for timber uses. J Trop For Sci 2(3):243–251
Hibberler RC (1997) Mechanics of materials, 3rd edn. Prentice-Hall, New Jersey
Hoo F, Michelle S, Sirivolu D (2010) A wave propagation model for the high velocity impact response of a composite sandwich panel. Int J Impact Eng 37:117–130
JIS A 5905 (1994) Fibreboards. Japanese Industrial Standard, Tokyo
Kawasaki T, Kawai S (2006) Thermal insulation properties of wood-based sandwich panel for use as structural insulated walls and floors. Jpn Wood Res Soc 52:75–83
Kwon JH, Ayrilmis N, Han TH (2012) Enhancement of flexural properties and dimensional stability of rice husk particleboard using wood strands in face layers. Composites (Part B) 44:728–732
Lide DR (1998) CRC handbook of chemistry and physics, 79th edn. CRC Press, Boca Raton
Lim SC, Gan KS (2005) Timber Technology Bulletin, Forest Research Institute Malaysia: Selangor, Malaysia, pp 1-11
Lim SC, Khoo KC (1986) Characteristics of oil palm trunk and its potential utilisation. Malays For 49(1):3–21
Mousa MA, Uddin N (2011) Flexural behavior of full-scale composite structural insulated floor panels. Adv Compos Mater 20:547–567
Mullens M, Arif M (2006) Structural insulated panels: impact on the residential construction process. J Constr Eng Manage 132(7):786–794
Panjehpour M, Abang Ali AA, Voo YL (2013) Structural insulated panels: past, present, and future. J Eng Proj Prod Manag 3(1):2–8
Shinoj S, Visvanathanb R, Panigrahic S, Kochubabu M (2011) Oil palm fiber (OPF) and its composites: a review. Ind Crops Prod 33(1):7–22
Skaar C (1972) Water in Wood. Syracuse University Press, Syracuse
Srivaro S, Chaowana P, Matan N, Kyokong B (2014) Lightweight sandwich panel from oil palm wood core and rubberwood veneer face. J Trop For Sci 26(1):50–57
Suhaily SS, Jawaid M, Abdul Khalil HPS, Mohamed AR, Ibrahim F (2012) A review of oil palm biocomposites for furniture design and applications: potential and challenges. Bioresource 7(3):4400–4423
Sulaiman O, Salim N, Nordin NA, Hashim R, Ibrahim M, Sato M (2012) The potential of oil palm trunk biomass as an alternative source for compressed wood. Bioresource 7(2):2688–2706
Taj MA, Najafi SK, Ebrahimi G (2009) Withdrawal and lateral resistance of wood screw in beech, hornbeam and poplar. Eur J Wood Prod 67:135–140
Terentiuk S, Memari A (2012) In-plane monotonic and cyclic racking load testing of structural insulated panels. J Archit Eng 18(4):261–275
Tracy J (2000) SIPs: overcoming the elements. For Prod J 50(3):12–18
Vaidya A, Uddin U, Vaidya U (2010) Structural characterization of composite structural insulated panels for exterior wall applications. J Compos Constr 14(4):464–469
Youngquist JA (1999) Wood-based composites and panel products. In: Wood handbook—wood as an engineering material, General Technical Report, FPL-GTR-113. USDA Forest Service, Forest Products Laboratory, Madison, Wisconsin
Zenkert D (1997) An introduction to sandwich construction. EMAS, London
Acknowledgments
The authors gratefully acknowledge the Thailand Research Fund through the Royal Golden Jubilee Ph.D. Program (Grant No.PHD/0065/2552) for the financial support, Phang-Nga Timber Industries Co., Ltd., Phang-Nga, Thailand for providing the raw materials and facilities for the experimental work and Dynea Krabi Co., Ltd., Songkhla, Thailand for providing MUF adhesives used in this work.
Author information
Authors and Affiliations
Corresponding author
Rights and permissions
About this article
Cite this article
Srivaro, S., Matan, N., Chaowana, P. et al. Investigation of physical and mechanical properties of oil palm wood core sandwich panels overlaid with a rubberwood veneer face. Eur. J. Wood Prod. 72, 571–581 (2014). https://doi.org/10.1007/s00107-014-0817-5
Received:
Published:
Issue Date:
DOI: https://doi.org/10.1007/s00107-014-0817-5