Abstract
Carbonation is one of the factors that can reduce the service life of reinforced concrete structures, especially in urban environments where carbon dioxide (CO2) concentrations are elevated. While concrete is generally considered to be resistant to carbonation under normal atmospheric conditions, in polluted urban environments and accelerated laboratory conditions, carbonation can occur at accelerated rates. Concentration of carbon dioxide (CO2) can have a significant impact on the rate at which carbonation occurs. There are no current guidelines for determining the carbonation rate in reinforced concrete as a function of CO2 concentrations. This work presents a risk-based framework that can be used to quantify carbonation depths and rates for various levels of CO2. This paper also identifies the key variables that affect the service life of reinforced concrete structures, from the point of view of carbonation and the resulting corrosion. These variables include the quantities of the various hydrated/anhydrous phases and the effective diffusion coefficient of the cementitious system. Monte-Carlo simulations are also performed to identify the change in time to carbonation with change in both CO2 concentration exposure and the concentrations of the hydrated and anhydrous phases of concrete.
Access provided by Autonomous University of Puebla. Download conference paper PDF
Similar content being viewed by others
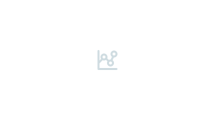
Keywords
1 Introduction
Corrosion of the reinforcement embedded in concrete structures is responsible for around 95% of the durability related issues of concrete. The steel reinforcement bar is passive in nature due to the high pH environment created by the concrete pore solution. Corrosion is considered to be initiated when the passive layer on the surface of the steel reinforcement bar is disrupted due to the reduction of pH of the concrete pore solution. The penetration of atmospheric carbon dioxide (CO2) and its subsequent reactions with hydrated and anhydrous phases of cement contributes to this reduction of pH. This process is termed as carbonation and it is quantified using the RILEM CPC-18 method (Measurement of hardened concrete carbonation depth) [1].
The three environmental factors that have a significant impact on concrete carbonation are: (1) relative humidity, (2) ambient temperature, and (3) CO2 concentration. The effect of relative humidity and temperature have been thoroughly discussed in past literature [2]. There is consensus, among these studies, that 40–90% RH and higher temperatures are conducive to concrete carbonation [3,4,5]. Although, plenty of literature capture the effect of CO2 concentration on concrete carbonation, there is no decision-making model available to the decision makers that quantify the time and rate of carbonation based on the ambient CO2 levels. Such a tool will be valuable for decision makers to compute the service life of the structure, especially when carbonation-induced corrosion is of utmost concern. The average atmospheric concentration of CO2, 390 parts per million by volume (ppmv), is still relatively low from the perspective of carbonation of concrete [6]. However, local concentrations of CO2 sampled in urban environments can be as high as 700 ppmv [2]. Figure 1 illustrates the CO2 concentration of the various states in the US based on the information provided by the US Energy Information Administration (EIA) [7]. Note here that CO2 concentration values specified for each state is an average value for the state and on-site measurements are recommended to obtain more accurate values. Ambient CO2 concentration influences the carbonation process in two ways: – (1) higher concentration gradient of CO2 increases the diffusion of CO2 into the concrete and (2) higher CO2 concentration leads to a faster rate of reaction.
1.1 Carbonation Depth Modeling
Most of the models developed to predict the carbonation depth and rate have been either empirical or statistical in nature [8, 9]. However, equations based on the theoretical science governing the process and the stoichiometry of the reactions involved are generally more accurate than the empirical models. The following equation was determined by Papadakis et al. (1991) in a seminal paper on fundamental modeling of concrete carbonation [10].
where xc is the carbonation depth in m, De,CO2 is the effective diffusivity of CO2 through the concrete (m2/s), and [CO2]0, [Ca(OH)2]0, [C-S-H]0, [C3S]0, and [C2S]0 are the concentrations of the respective compounds at the end of moist curing and the onset of CO2 exposure. The molar concentration of the hydrated and anhydrous phases in Eq. (1) are represented as moles per unit volume of concrete (mol/m3). It can be noted that Eq. 1 has the same form as the common empirical function that is generally used to model the carbonation front [10].
To identify the time to carbonation, Eq. 1 can be rewritten as:
Here t is the time to carbonate the depth of concrete xc and it can be seen in Eq. (3) that it depends upon the CO2 concentration, diffusivity of CO2, and the concentration of the hydrated and unhydrated phases. However, this equation can be simplified further. The concentration of the unhydrated phases (C3S, C2S) becomes small when compared to the concentration of the hydrated phases (Ca(OH)2, CSH) as the hydration reaction proceeds over time. So, as the degree of hydration (DoH) approaches 100%, the concentrations of the unhydrated phases are negligible when compared to the concentrations of the hydrated phases [11]. This is especially valid for the timeframe that is observed in the outcome of this study. So, Eq. (3) simplifies to Eq. (4) as follows:
It can be observed in this equation that [C-S-H]0 and [Ca(OH)2]0 have stoichiometric coefficients of 3 and 1 respectively. This implies that the time to carbonation is thrice as sensitive to CSH concentration when compared to the Ca(OH)2 concentration. The authors would like to note that this could be a potential drawback of the model as the concrete carbonation process primarily involves the reaction of Ca(OH)2 with atmospheric CO2. Table 1 shows a typical sample concrete mixture that will be used to assess the time to carbonation.
Table 2 shows the parameters, based on the mixture proportions in Table 1, which can be used to compute the time to carbonation. The molar concentrations of the hydrated and anhydrous phases were calculated, based on the mixture design, using an online calculator developed by the Swiss Federal Laboratories for Materials Science and Technology [12]. This calculator is based on the principles of thermodynamic modeling and serves as a powerful tool to estimate the concentrations of hydrated phases of a cementitious system.
Using Eq. (4), a sensitivity plot for time to carbonation is created and is shown in Fig. 2. The values shown in Table 2 were used to calculate the baseline value for time to carbonation. Percentage change in the variables is represented in the abscissa and the percent changes in the time to carbonation are shown on the ordinate. The slope of the lines indicates the sensitivity of time to carbonation with respect to each parameter. The steeper the slope, the higher the sensitivity associated with that parameter.
It can be observed in Fig. 2 that De,CO2 and CO2 are inversely related to the time to carbonation. For a 10% increase in these two parameters, the time to carbonation decreases by approximately 9%. It can also be seen that concrete cover is the most effective way to extend the time to carbonation. A 20% increase in cover depth can lead to almost a 44% increase in the time to carbonation (Assuming the increase in cover does not result in cracking). Another item of note in this figure is the sensitivity due to changes in Ca(OH)2. It can be seen that for a 100% decrease in the value of Ca(OH)2, the time to carbonation decreases by only 23.7%. Research shows that time to carbonation is very likely more sensitive to Ca(OH)2 content than what is indicated in this figure [14].
2 Methodology
2.1 Monte-Carlo Simulation
The outcome of the simulations shown in this paper can assist users and decision makers to better understand the effects of ambient CO2 concentration on the time to carbonation of reinforced concrete structures and the associated corrosion risks. This model, as noted earlier, depends primarily on the concrete cover depth, effective diffusivity, and concentrations of hydrated and anhydrous phases. Similar works on chloride-induced corrosion are available, but at the time of this writing no analogous works are available for carbonation-induced corrosion [15]. To generate a dataset large enough to develop such a model, Monte-Carlo simulation was used [16]. This simulation method uses random sampling and statistical modeling to estimate mathematical functions and can simulate the operations of complex systems. This method relies on probability density functions (PDFs) and random number generators (RNGs) to introduce the element of randomness, to what would be otherwise, a deterministic approach. In this work, a large dataset is generated by identifying the probabilistic distributions for all the parameters shown in Eq. 4, except for the CO2 concentration. A normal distribution was assumed for the parameters for the sake of simplicity and ease of interpretation. In this work, CO2 concentration will be treated as a deterministic parameter with values ranging from 300 to 800 ppm incrementally. Using CO2 concentration as a deterministic parameter enables the understanding of its effect on the time to carbonation on a case-by-case basis.
2.2 Kaplan Meier Reliability Analysis
The Kaplan-Meier method is a non-parametric survival analysis technique that is used to estimate survival and hazard functions for a given application [17]. Equation 4 can be used to carry out reliability analysis by constructing survival and hazard curves. These plots can help inform decision-makers about the service life of the structure based on the ambient carbon dioxide concentration. In this scenario, where it is intended to compute the time to carbonation of a reinforced concrete structure, the survival curve can be established using the following Eq. (5):
In Eq. (5), S is the survival function at for a duration of time t, in years and CO2 is the ambient CO2 concentration in ppm. F is the cumulative density function. The survival function S(t) gives the probability that the structure does not undergo complete concrete cover carbonation up to a specified time, t. In other words, S(t) gives the probability that the random variable T exceeds the specified time, t. The survival function is a crucial aspect of the survival analysis because it provides survival probabilities of structures for different values of t.
The hazard function, denoted by H(t), gives the instantaneous potential per unit time for the event to occur, i.e., that the structure has undergone complete concrete cover carbonation at time t. The hazard function is computed by calculating the ratio of the probability density function to the survival function. This function is then summed up until the required duration to determine the cumulative hazard function. In this study, cumulative hazard curves were constructed using the following Eq. (6):
These curves are widely used because they can be easily interpreted. These plots can be utilized by stakeholders and decision-makers to determine the effects of CO2 concentration on the time to carbonation, and hence the service life of the structure.
3 Results and Discussion
The results from the Monte-Carlo simulations are summarized in Fig. 4. Ten thousand simulations were performed and 6 cases are illustrated, one for each ambient CO2 concentration. For example, Fig. 3a shows the histogram of time to carbonation at a CO2 ambient concentration of 300 ppm. A normal distribution was superimposed on the histogram and it can be seen that the mean time to carbonation is 169 years. This indicates that, at low CO2 concentrations, such as 300 ppm, the structure will be safe from carbonation-induced corrosion over its service life. Figure 3b–f illustrate the time to carbonation histograms at CO2 concentrations of 400 ppm, 500 ppm, 600 ppm, 700 ppm, and 800 ppm respectively. Overall, it can be observed that, as the CO2 concentrations increase, the spread of the histograms are reduced and the mean time to carbonation decreases. For the highest CO2 concentration investigated in this study (800 ppm), the mean time to carbonation is 63 years. This indicates that a CO2 concentration of 800 ppm poses a challenge to structures that were intended to have a service life longer than 63 years.
Figures 4 and 5 illustrate the survival and hazard curves for various ambient CO2 concentrations. In Fig. 4, the survival duration is presented in the abscissa and the cumulative survival probability is presented in the ordinate. Overall, it can be seen that as CO2 concentrations increase the probability of survival up to a specified time decreases. For example, at a duration of 200 years, the cumulative survival probability at 300 ppm is around 0.45. At the same duration, the cumulative survival probability is around zero at 800 ppm. A closer inspection of the 800-ppm curve clearly indicates that the survival probability is approximately zero beyond 100 years of service life. This corroborates with the sensitivity plot shown in Fig. 2. Another important piece of information that can be gathered from the survival plots is the risk associated with each case. For example, the 700-ppm case curve reaches a cumulative survival probability of 0.5 around 82 years. This implies that there is a 50% chance of survival up to that duration and hence, 50% risk associated with it.
Figure 5 shows the cumulative hazard plots. The cumulative hazard plot consists of a plot of the cumulative hazard H(t) versus time t of the ith failure. In the context of this study, failure refers to the complete carbonation of concrete cover. For a structure exposed to 300 ppm of CO2, the probability of failure is approximately zero for the first 25 years, implying no hazards in that time frame. For the same case, at 300 years, the cumulative hazard is slightly higher than 2. This indicates that 2 out of 100 structures will be subjected to the hazard (complete carbonation) within that duration. At any duration, it can be seen that, low CO2 concentrations have the least cumulative hazard. It can also be noticed that the slopes are steeper for higher ambient CO2 concentrations indicating a higher rate of failure with respect to time.
3.1 Case Study
In this section, an example is presented that synthesizes all the findings presented in the work. In Fig. 1, it was shown earlier that California and Texas are the top-two states in the US for ambient CO2 concentrations. Texas has an average CO2 concentration of 657 ppm and California has an average CO2 concentration of 363 ppm. The information presented in Fig. 3, along with linear interpolation, can be used to predict the time to carbonation for both cases. Therefore, it can be estimated that reinforced concrete structures at Texas, which were built with the sample mixture proportions shown in Table 1, are expected to have a time to carbonation of 78 years. Similarly, structures in California are expected to have a time to carbonation of around 148 years. At a duration of 100 years, the cumulative survival probabilities for structures in Texas and California are around 0.4 and 0.8 respectively. If the design service life is set at 100 years, it can be seen that most of the structures in the US are relatively immune to carbonation-induced corrosion caused by ambient CO2. However, in cases of elevated local CO2 concentrations, there would be a higher risk of carbonation-induced corrosion. Industrial chimneys are a structure that could be at risk of higher rates of carbonation due to continuous elevated CO2 levels.
4 Conclusion
Time to carbonation was calculated in this work, based on a fundamental model developed by Papadakis et al. [10], using statistical techniques. Results from the sensitivity analysis showed the sensitivity and influence of ambient CO2 concentration, effective diffusion coefficient, concentration of hydrated and unhydrated phases, and concrete cover depth. The outcomes from the Monte-Carlo simulation showed that mean time to carbonation reduces as the ambient CO2 concentration increases. At concentrations below 600-ppm, the mean values of time to carbonation were greater than 100 years. This indicates that carbonation-induced corrosion is likely not a major factor affecting the service life of reinforced concrete structures when lower ambient CO2 concentrations are present.
The survival and hazard plots that were created as part of the reliability analysis can be used by decision makers to better understand the risk associated with the service life of their structure. The results from the reliability analysis showed that ambient CO2 concentrations are capable of significantly affecting the risk associated with the survival of the structure. Beyond 200 years, the cumulative probability of survival is approximately zero for CO2 concentrations of 600, 700, and 800 ppm. This clearly indicates that, at elevated CO2 concentrations, carbonation-induced corrosion must be considered while estimating the expected service life of the structure.
References
De La Rilem Recommendations: CPC-18. Measurement of hardened concrete carbonation depth. Mater. Struct. 21, 453–455 (1988)
Richardson, M.G.: Fundamentals of Durable Reinforced Concrete, 273 pp. CRC Press (2002)
Bunte, D.: Zum Karbonatisierungsbedingten Verlust der Dauerhaftigkeit vonAußenbauteilen aus Stahlbeton. Ph.D. thesis, TU Braunschweig, 346 pp (1994)
Wierig, H.J.: Longtime studies on the carbonation on concrete under normal outdoor exposure. RILEM seminar durability of concrete structures under normal outdoor exposure, pp. 239–249 (1984)
Miller, L.B., Witt, J.C.: Solubility of calcium hydroxide. J. Phys. Chem. 33(2), 285–289 (2002)
Dyer, T.: Concrete Durability, 420 pp. CRC Press (2014)
US EPA webpage. https://www.eia.gov/environment/emissions/state/analysis/. Accessed 20 June 2021
Silva, A., Neves, R., De Brito, J.: Statistical modelling of carbonation in reinforced concrete. Cement Concr. Compos. 50, 73–81 (2014)
Te Liang, M., Qu, W., Liang, C.H.: Mathematical modeling and prediction method of concrete carbonation and its applications. J. Mar. Sci. Technol. 10(2), 128–135 (2002)
Papadakis, G., Costas, G., Michael, N.: Experimental investigation and mathematical modeling of the concrete carbonation problem. Chem. Eng. Sci. 46, 1333–1338 (1991)
Scrivener, K., Snellings, R., Lothenbach, B.: A Practical Guide to Microstructural Analysis of Cementitious Materials. Crc Press (2018)
EMPA webpage. https://www.empa.ch/web/s308/ternary-diagram. Accessed 20 June 2021
Jung, S.H., Lee, M.K., Oh, B.H.: Measurement device and characteristics of diffusion coefficient of carbon dioxide in concrete. ACI Mater. J. 108(6), 589 (2011)
Sisomphon, K., Franke, L.: Evaluation of calcium hydroxide contents in pozzolanic cement pastes by a chemical extraction method. Constr. Build. Mater. 25(1), 190–194 (2011)
Shakouri, M., Trejo, D., Gardoni, P.: A risk-based model for determining allowable admixed chloride limits in concrete. In: International RILEM Conference on Materials, Systems and Structures in Civil Engineering, pp. 631–640 (2016)
Mooney, C.Z.: Monte Carlo Simulation, no. 116. Sage (1997)
Kleinbaum, D.G., Klein, M.: Survival Analysis. Springer (2010)
Author information
Authors and Affiliations
Corresponding author
Editor information
Editors and Affiliations
Rights and permissions
Copyright information
© 2023 The Author(s), under exclusive license to Springer Nature Switzerland AG
About this paper
Cite this paper
Vasudevan, G.D., Trejo, D. (2023). Reliability Analysis for Service Life of Concrete Structures Subject to Various Carbon Dioxide Concentrations. In: Escalante-Garcia, J.I., Castro Borges, P., Duran-Herrera, A. (eds) Proceedings of the 75th RILEM Annual Week 2021. RW 2021. RILEM Bookseries, vol 40. Springer, Cham. https://doi.org/10.1007/978-3-031-21735-7_27
Download citation
DOI: https://doi.org/10.1007/978-3-031-21735-7_27
Published:
Publisher Name: Springer, Cham
Print ISBN: 978-3-031-21734-0
Online ISBN: 978-3-031-21735-7
eBook Packages: EngineeringEngineering (R0)