Abstract
The elevation of photovoltaic (PV) cells temperature reduce its electrical conversion efficiency (above to characterization temperature usually 25 ℃). The use of a phase change material (PCM) layer linked to a PV cells panel can decrease its temperature rise. This paper based on a numerical study of the effect of the tilt angle of curved PV panel with 100 mm of curvature radius (Technology so-called PV-mirror) on its thermal performance. For this raison a 2D model of heat transfer conjugated with a solid-liquid phase change was developed and validated with an experimental data for two PV/PCM systems with and without fins, where a good agreement was obtained. The Results reveal that the tilt angle (more than 45°) allows a good thermal regulation, a noticeable decrease in PV cell temperature more than 20 ℃ compared with a single curved PV which maintain its efficiency et 14%. In addition the heat transfer was dominated by conduction for tilt angle less than 45º, which increase the front temperature of PV/PCM system. However, the convection dominates in the other system, where the cold liquid PCM flow absorbs more heat, which decreases the PV cells temperature.
Access provided by Autonomous University of Puebla. Download conference paper PDF
Similar content being viewed by others
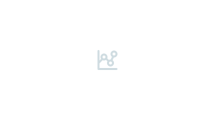
Keywords
1 Introduction
The photovoltaic cell temperature elevation reduces its electrical efficiency. In fact, only 15–20% of the sunlight converted to electricity. While the rest of sunlight dissipated into heat [1], that causes the increase of the PV operating temperature. As a result, the electrical conversion efficiency dropped by 0.5% per 1 ℃; and affected the solar cell lifetime Norton et al. [2]. Therefore, maintaining the temperature of PV cells at adequate level can improve their efficiency. Several researches try to decrease the PV cells temperature rise. Overall, the use of a thin layer of Phase Change Material (hereafter PCM) behind PV panel has been an effective solution widely used for passive cooling of PV cells [3,4,5,6,7], which can absorb a large quantity of heat during its melting process at constant temperature. The experimental and numerical studies of Huang et al. [8,9,10,11,12,13] was conducted under the thermal regulation of building integrated photovoltaic panel BIPV by using PCM. Starting by the first research [12] which, they have succeed to maintain the temperature of the PV cells under 40 ℃ for 80 min, with a PCM RT25 that have a melt temperature of 32 ℃, then considering the low thermal conductivity of RT25 0.18 W m−1 K−1, an internal fins in Aluminum used to transport the thermal load into the PCM in order to reduce the temperature rise on PV. In other hand Huang et al. [8,9,10,11] investigated the use of inner fins in BIPV to enhance the heat transfer in PCM losing the excess heat in PCM. They have studied the effect of internal fins spacing on BIPV thermal regulation and PCM behavior, they found that the use of fins improve thermal distribution of PV/PCM system and reduce its temperature significantly. Recently, a novel technology of solar photovoltaic panel was introduced in world of solar energy, so-called PV-mirror, which combined by two types of panel: a plate one placed at the focal point of reflector mirror and the second (curved PV) behind the curved mirror [14], or several PV panels arranged rear the mirror to take the curvature form [15]. This system made with special mirror that concentrates the large part of the sunlight into a flat PV panel positioned at the reflector’s focal point. On the other hand, the rest part of the sunlight is converted to electric power via curved one. Nehari et al. [16] studied the impact of the fins length [5, 10, 15, 20, 25, 30, 35 mm] on the heat transfer improvement through the PCM layer. Results confirmed that the internal fins reduce significantly the increase of the temperature compared to the case configuration without inner fins. Furthermore, the configurations of L = 25, 30 and 35 mm allow better cooling of the PV panel. Benlekkam et al. [17] numerically evaluated the impact of fins tilt angle and its orientation on the thermal cooling of PV/PCM system. They found that the best results were obtained with diverged configuration that maintained the temperature about 34 ℃ for 170 min. In addition the fins tilt angle with diverged configuration less than 30° allows a good thermal cooling rate, and maintained the PV cell efficiency at average value of 14% for more than 3 h compared with PV system without PCM. Moreover the fins tilt angle 25° provides the best performances. Furthermore the PCM “RT25” was more useful for thermal regulation of PV/PCM system under medium and low insolations intensities for the same thermal operating conditions. Elarga et al. [18] developed a physical model to study the incorporation of PCM layer on a double-facade of PV panel for three different climates, they have found that this technique can improve the conversion of solar energy into electricity independently of the climate. Also they concluded that the use of PCM can increase the cooling of the building more than 20% per month. An experimental study was carried out by Nikolaos et al. [19] to evaluate the efficacy of PCM to mitigate the influence of temperature on photovoltaic module performance. The PV/PCM system was tested under Mediterranean climatic conditions. They found that the chosen PCM “RT27” succeeded in reducing the PV module temperature by an average of 11 ℃ compared to a system without PCM, furthermore the conversion efficiency of the PV module increases by about 8.6%. Since the phase change materials are pure and combined, Farouk et al. [20] studied their influence on the performance improvement of the PV modules. They found that the use of pure PCM can reduce the PV temperature by more than 6.5 ℃ by an average of 2.7 ℃, and increase the electrical efficiency by an average of 3%. On the other hand, the combined PCM can reduce the PV temperature by an average of 5.6 ℃ and improves the efficiency of the PV module by about 5.8%. The present study carried out to evaluate the effect of tilt angle of curved PV panel in the range of 15° to 90° in an interval of 15° on its thermal regulation and the heat transfer mode inside the PCM.
2 Numerical Model and Validation
The studied domain of curved PV/PCM considered in the present paper is illustrated in Fig. 1-a, as shown the PV/PCM system is composed by a curved PV panel attached on a curved container filled by PCM. The PCM used is Rubitherm RT25 [17, 21] and its thermophysical properties are assumed to be constant during the melting process. Natural convection was adopted over the PV panel and the back wall of the container of PCM. The PCM is in perfect contact with the PV panel and the back wall. The incident energy IT is absorbed and dissipated into heat inside the PV/PCM system. In our case, we use the same initial and thermal boundary condition considered by Huang et al. [12] which are:
-
(i)
the initial temperature of the system PV/PCM is TPV;
-
(ii)
the front and rear surfaces of the system have respectively the values h1 and h2;
-
(iii)
concerning the top and bottom boundaries, the adiabatic conditions are used.
The 2D unsteady governing equations of energy and momentum heat transfer are solved by using the implicit finite volume method with the ANSYS FLUENT 17. In addition, the Boussineq approximation was adopted to take account the change in density of the PCM in liquid phase as a function of temperature.
For the numerical solution, the pressure-velocity coupling is accounted for by using SIMPLE algorithm [22], whereas the Quick scheme was adopted for convective discrimination. The grid size adopted in present simulation was 48 × 132 and a variable time step with a minimum value of 0.01 s are used for all the simulations, and the convergence was confirmed at each time step, with the convergence criterion of 10−6 for all variables.
3 Validation
All the simulations were conducted using the heat transfer coefficients on the front and rear surfaces are respectively 12.5 W m−2 K−1 and 7.5 W m−2 K−1 and the insolation was 750 W/m−2.
The present model Benlekkam et al. [17, 21] was validated successfully with numerical and experimental data of [12] for two PV/PCM system with and without fins. Our validation was performed with a same initial and boundary conditions, material properties and geometry, then we compared our results with the predicted and experimental temperature evolution of front and rear surface of PV/PCM system with fins Fig. 2-b, and for the PV/PCM system without fins Fig. 2-c In addition we compared the isothermal contours of temperature in Fig. 2-a, where a good agreement was obtained.
Model validation with Huang et al. [12] (PV/PCM system with fins)
4 Results and Discussion
For all performed simulations the tilt angle was varied from the vertical (α) to 15º in an interval of 15°. All numerical simulations were performed along 200 min until the PCM will be completely melted. Initially the PCM starts to melt close to the front face, where the heat transfer was dominated by conduction but once enough PCM is melted, natural convection in the liquid melt starts to dominate.
Figure 3-a and b shows the distribution of the isothermal contours of the curved PV/PCM system at the 50th and 100th min. It is clear that the temperature increase to reaches its mean value of 39 ℃ and 40 ℃ for the PV/PCM system with tilt angle 45° to 90° at 50 and 100 min respectively. While rising to its maximum value 46 ℃ and 68 ℃ for tilt angle of 15°. This behavior due to the heat transfer mode domination. From the inclination 0º to 45º, we observed the increase of the melted PCM quantity which allows the domination of convection. Therefore, it can maintain the temperature of the PV due to the convective flow of the cold PCM. On the other hand, the inclination lower than 45° reduces the heat transfer via convection until the case of pure conduction for the horizontal system.
The Fig. 4-a and b, shows the isothermal contours at the 150th and 200th min for all tilt angle, we can see always the same behavior of the PV/PCM temperature and an increase of the melted PCM volume compared to the precedent cases. In the other hand, we notice also the increase of convection phenomena with the decrease of tilt angle until 45°. However, for the lower ones than 45°, we can confirm the domination of conduction phenomena as mentioned in the precedent time of simulation. We can observe also a kind of stratification of the temperature due to the strong domination of the conduction.
When the tilt angle of curved PV/PCM system decreases, the velocity of melted PCM decreases, which reduces the convective heat transfer inside the PCM enclosure. Therefore, reduces the heat transfer from the PV to the PCM (cases lower than 45°). Besides, there is no convection for horizontal panel and the heat transfer by convection is the maximum for a vertical tilt angle.
The Fig. 5-a shows the temperature evolution along the time for all tilt angle investigated. It is clear that the temperature increase similarly for all cases up to 30 min due to the conduction heat transfer in the solid PCM. Then the PCM starts to melt and the liquid PCM quantity increase absorbing more heat from the PV panel as latent heat, therefore maintain the system temperature. As we explained above the tilt angle higher than 45º allows a good thermal regulation due to the natural convection in liquid PCM, as shown in Fig. 6-b we can see that the thermal enhancement it’s about 20 ℃ for vertical PV/PCM system compared with the PV panel without PCM. However the lower tilt angle than 45º reduce the velocity in the melted PCM to allow the domination of the pure conduction as shown in Fig. 5-a for the PV panel tilted by 15°.
From the Fig. 6-a, it’s clear that the use of PCM can maintain the efficiency of PV cells at an average value greater than 14% more than 3 h; a drop of 1% from the maximum efficiency of the PV cells considered (15%). However, the curved PV cells efficiency without PCM layer at the same conditions fall of 2%.
In addition, the PV/PCM system tilted with 15° drop to 12.3% because of the high temperature due to the conduction domination.
The electrical output power is presented in Fig. 6-b, it’s clear that the use of PCM can improve the power generation of PV cells due to the passive cooling that maintain the PV cell temperature at lower values. We can see that the PV cells power generation decrease with respect to the tilt angle from 15.3 W to 13,3 W, due to the heat transfer mode domination which the conduction allows the higher temperature presented in PV/PCM system because of the low thermal conductivity of PCM.
5 Conclusion
In the current work, a numerical model was presented to investigate the effect of the tilt angle of curved PV/PCM system. The developed numerical model was compared with numerical and experimental data of literature for both: Average temperature of PV cells versus time and the isothermal contours for 50th and 100th min, where a good agreement was found. The obtained results indicate that the heat transfer mode in the PV/PCM system plays a substantial role for its thermal regulation and the cooling rate of PV cells. In fact, the tilt angle of PV/PCM system controls the heat transfer inside the PCM. We found that the convection dominate for a tilt angle higher than 45°. Whereas, the small tilt angle lower than 45° allows the domination of the conduction where the natural convection completely disappears. In addition, the results reveal that the temperature of the PV panel increases with the decrease of the inclination, and the inclinations higher than 45° can maintain the curved PV panel temperature under 50 ℃ for 170 min comparing with other tilted by 15°, where its temperature increased up to 102 ℃. Moreover, the vertical PV/PCM system improves the conversion efficiency and the power generation by 2% and 1.3 W respectively for more than three hours.
References
Emery, K.B., Caiyem, J., Dunlavy, Y., Field, D., Kroposki, H., Moriarty, B., Ottoson, T., Rummel, L., Strand, S.: Temperature dependence of photovoltaic cells, modules and systems. In: Conference Record of the Twenty Fifth IEEE Photovoltaic Specialists Conference, pp. 1275–1278 (1996)
Norton, B., Eames, P.C., Mallick, T.K., Huang, M.J., McCormack, S.J., Mondol, J.D., Yohanis, Y.G.: Enhancing the performance of building integrated photovoltaics. Sol. Energy 85(8), 1629–1664 (2011)
Ho, C., Tanuwijava, A., Lai, C.-M.: Thermal and electrical performance of a BIPV integrated with a microencapsulated phase change material layer. Energy Build. 50, 331–338 (2012)
Hasan, A., McCormack, S.J., Huang, M.J., Norton, B.: Characterization of phase change materials for thermal control of photovoltaics using differential scanning calorimetry and temperature history method. Energy Convers. Manag. 81, 322–329 (2014)
Atkin, P., Farid, M.M.: Improving the efficiency of photovoltaic cells using PCM infused graphite and aluminium fins. Sol. Energy 114, 217–228 (2015)
Ma, T., Yang, H., Zhang, Y., Lu, L., Wang, X.: Using phase change materials in photovoltaic systems for thermal regulation and electrical efficiency improvement: a review and outlook. Renew. Sustain. Energy Rev. 43, 1273–1284 (2015)
Browne, M.C., Norton, B., McCormack, S.J.: Heat retention of a photovoltaic/thermal collector with PCM. Sol. Energy 2(133), 533–548 (2016)
Huang, M.J.: Two phase change material with different closed shape fins in building integrated photovoltaic system temperature regulation. In: World Renewable Energy Congress-Sweden, pp. 2938–2945. Linköping University Electronic Press, Sweden (2011)
Huang, M.J., Eames, P.C., Norton, B.: Thermal regulation of building-integrated photovoltaics using phase change materials. Int. J. Heat Mass Transf. 47(12), 2715–2733 (2004)
Huang, M.J., Eames, P.C., Norton, B.: Phase change materials for limiting temperature rise in building integrated photovoltaics. Sol. Energy 80(9), 1121–1130 (2006)
Huang, M.J., Eames, P.C., Norton, B., Hewitt, N.J.: Natural convection in an internally finned phase change material heat sink for the thermal management of photovoltaics. Sol. Energy Mater. Sol. Cells 95(7), 1598–1603 (2011)
Huang, M.J., Eames, P.C., Norton, B., Hewitt, N.J.: The effect of phase change material crystalline segregation on the building integrated photovoltaic system thermal performance. In: World Renewable Energy Congress (WRECX), pp. 1338–1343 (2008)
Huang, M.J.: The effect of using two PCMs on the thermal regulation performance of BIPV systems. Sol. Energy Mater. Sol. Cells 95(3), 957–963 (2011)
Holman, Z., Yu, Z.J.: Solar and alternative energy high-efficiency solar power with integrated storage (2015)
Zhengshan, J.Y., Fisher, K.C., Wheelwright, B.M., Angel, R.P., Holman, Z.C.: PVMirror: a new concept for tandem solar cells and hybrid solar converters. IEEE J. Photovolt. 5(6), 1791–1799 (2015)
Nehari, T., Benlakam, M., Nehari, D.: Effect of the fins length for the passive cooling of the photovoltaic panels. Periodica Polytech. Eng. Mech. Eng. 60(2), 89–95 (2016)
Benlekkam, M.L., Nehari, D., Madani, H.I.: The thermal impact of the fin tilt angle and its orientation on performance of PV cell using PCM. Int. J. Heat Technol. 36(3), 919–926 (2018)
Elarga, H., Goia, F., Zarrella, A., Dal Monte, A., Benini, E.: Thermal and electrical performance of an integrated PV-PCM system in double skin façades: a numerical study. Sol. Energy 136, 112–124 (2016)
Savvakis ,N., Tsoutsos, T.: Phase change materials in photovoltaics: the assessment of system performance in the present mediterranean climate conditions (2016)
Hachem, F., Abdulhay, B., Ramadan, M., El Hage, H., El Rab, M.G., Khaled, M.: Improving the performance of photovoltaic cells using pure and combined phase change materials–experiments and transient energy balance. Renew. Energy 107, 567–575 (2017)
Benlekkam, M.L., Nehari, D., Madani, H.Y.: Numerical performances study of curved photovoltaic panel integrated with phase change material. Mech. Mech. Eng. 22(4), 1439–1451 (2018)
Patankar, S.: Numerical Heat Transfer and Fluid Flow. CRC Press, Boca Raton (1980)
Author information
Authors and Affiliations
Corresponding author
Editor information
Editors and Affiliations
Rights and permissions
Copyright information
© 2020 Springer Nature Switzerland AG
About this paper
Cite this paper
Benlekkam, M.L., Nehari, D. (2020). Numerical Investigation of Thermal Regulation Improvement of Curved PV Panel Using PCM. In: Hatti, M. (eds) Smart Energy Empowerment in Smart and Resilient Cities. ICAIRES 2019. Lecture Notes in Networks and Systems, vol 102. Springer, Cham. https://doi.org/10.1007/978-3-030-37207-1_46
Download citation
DOI: https://doi.org/10.1007/978-3-030-37207-1_46
Published:
Publisher Name: Springer, Cham
Print ISBN: 978-3-030-37206-4
Online ISBN: 978-3-030-37207-1
eBook Packages: EngineeringEngineering (R0)